Construction heat and sound insulating composite materials with high tensile strength
Автор: Kozhevnikova O.V., Bokova E.S., Dedov A.V., Nazarov V.G., Ivanov L.A.
Журнал: Nanotechnologies in Construction: A Scientific Internet-Journal @nanobuild-en
Рубрика: Manufacturing technology for building materials and products
Статья в выпуске: 1 Vol.16, 2024 года.
Бесплатный доступ
Introduction. The objective of this study is to examine the impact of the impregnation (with the aliphatic polyurethane water dispersion) degree on the deformation properties of the polyacetal, polyethylene terephthalate and polypropylene fibers based nonwoven needle-punched composite fabrics. Materials and methods. We investigated the deformation properties of the nonwoven fabrics manufactured from the 0.33 tex linear density fibers of: polyethyleneterephthalate (diameter 20–25 microns, according to TU 6-13- 0204077-95-91), polypropylene (diameter 27–30 microns, according to TU 2272-007-5766624-93) and the original polyacetal ones (diameter 18–22 microns). The nonwoven fabrics were obtained by the mechanical formation technique. The needlepunching surface density was 180 cm–2. The water dispersion of anionic stabilized aliphatic polyethyruretane (IMPRANIL DL 1380 (China)) with a dry residue of 40% was used for the impregnation. The experimental samples’ linear dimensions were determined in accordance with the requirements of GOST 15902.2-2003. The sample’s thickness was determined by a thickness gauge with a pressure of 10 kPa and an instrumental error ~ 0.01 mm according to GOST 11358-70. The samples’ mechanical properties were determined in accordance with the requirements of GOST 15902.3-79. Results and discussion. The fiber filler composition influence on the ob-tained (by the impregnation of polyethyleneterephthalate, polypropylene and polyacetal fibers based non-woven needle-punched fabrics with polyurethane aqueous dispersion) composite materials tensile resistance has been established. We found the impregnation degree (depending on the chemical nature of the fibers and on the direction of nonwoven fabrics formation) at which the tensile resistance of the composite materials reaches the maximum value. It is demonstrated that, in the construction of buildings and structures, it is advisable to utilize materials based on composite polyacetal fibers. These materials exhibit higher tensile resistance compared to those based on polypropylene and polyethylene terephthalate at equivalent impregnation levels. Conclusion. The obtained optimal impregnation degree (at which the maximum tensile resistance of polyacetal fiber based composite materials was achieved) depends on the direction of the non-woven fabric formation. The maximum tensile resistance was observed: in the transverse direction – at 0.44 and in the longitudinal direction – at 0.35 impregnation degree values.
Non-woven needle-punched fabrics, polyurethane aqueous dis-persion, impregnation, composite material, stretching
Короткий адрес: https://sciup.org/142240523
IDR: 142240523 | DOI: 10.15828/2075-8545-2024-16-1-22-31
Текст научной статьи Construction heat and sound insulating composite materials with high tensile strength
Original article
Introduction. The objective of this study is to examine the impact of the impregnation (with the aliphatic polyurethane water dispersion) degree on the deformation properties of the polyacetal, polyethylene terephthalate and polypropylene fibers based nonwoven needle-punched composite fabrics. Materials and methods. We investigated the deformation properties of the nonwoven fabrics manufactured from the 0.33 tex linear density fibers of: polyethyleneterephthalate (diameter 20–25 microns, according to TU 6-130204077-95-91), polypropylene (diameter 27–30 microns, according to TU 2272-007-5766624-93) and the original polyacetal ones (diameter 18–22 microns). The nonwoven fabrics were obtained by the mechanical formation technique. The needlepunching surface density was 180 cm–2. The water dispersion of anionic stabilized aliphatic polyethyruretane (IMPRANIL DL 1380 (China)) with a dry residue of 40% was used for the impregnation. The experimental samples’ linear dimensions were determined in accordance with the requirements of GOST 15902.2-2003. The sample’s thickness was determined by a thickness gauge with a pressure of 10 kPa and an instrumental error ~ 0.01 mm according to GOST 11358-70. The samples’ mechanical properties were determined in accordance with the requirements of GOST 15902.3-79. Results and discussion. The fiber filler composition influence on the ob-tained (by the impregnation of polyethyleneterephthalate, polypropylene and polyacetal fibers based non-woven needle-punched fabrics with polyurethane aqueous dispersion) composite materials tensile resistance has been established. We found the impregnation degree (depending on the chemical nature of the fibers and on the direction of nonwoven fabrics formation) at which the tensile resistance of the composite materials reaches the maximum value. It is demonstrated that, in the construction of buildings and structures, it is advisable to utilize materials based on composite polyacetal fibers. These materials exhibit higher tensile resistance compared to those based on polypropylene and polyethylene terephthalate at equivalent impregnation levels. Conclusion. The obtained optimal impregnation degree (at which the maximum tensile resistance of polyacetal fiber based composite materials was achieved) depends on the direction of the non-woven fabric formation. The maximum tensile resistance was observed: in the transverse direction – at 0.44 and in the longitudinal direction – at 0.35 impregnation degree values.
INTRODUCTION synthetic fibers based nonwoven fabrics [1–9] highly voidness materials with a porosity coeffi

cient of more than 0.8. Such materials are often used for heat- [10–12] and sound- insulation [13–15] of buildings and constructions. Their main disadvantage is the low tensile resistance [16–22]. The fabrics stretching during the transportation, installation and operation leads to an increase in porosity and a decrease in the specified exploitation characteristics. When impregnating the nonwoven fabrics with the polymer solutions and dispersions, the voidness composite materials with the increased tensile resistance were obtained [23, 24].
The mechanical properties set of the composite materials is mainly de-termined by the interaction at the
MANUFACTURING TECHNOLOGY FOR BUILDING MATERIALS AND PRODUCTS interface “fiber–polymer binder” [25–30]. The highly voidness materials with the sufficiently useable tensile resistance were obtained by wetting with the polymer solutions and dispersions as the result of nanoscale polymer bridges between the fibers formation that limited their mobility in the mechanical force field.
The synthetic fibers are well wetted with the polymer solutions in different organic solvents. High wetting of polyethyleneterephthalate fibers with a binder is achieved by the nonwoven fabrics impregnating with the polyurethane in dimethylphoramide solution [31, 32]. In addition, when using polymer solutions in organic solvents, a predominant sorption of the binder occurs on the surface of the fibers while preserving the porous structure of the impregnated fabric. A significant volume and the toxicity of containing various organic solvents liquid effluents limit the industrial use of impregnated nonwoven fabrics.
The negative environmental impact is significantly reduced when using polymers’ aqueous dispersions for the nonwoven fabrics impregnating [25–30, 32–34]. But their wetting of the synthetic fibers is less then polymer solutions in organic solvents ones [32–34]. The interaction in the “fiber–polymer dispersion” system is, as a rule, regulated by changing the chemical nature of the polymer or by introducing the surfactants and other ingredients into the material composition [25–30]. The approach associated with varying the chemical nature of the reinforcing fabric fiber filler is practically not used [32–34]. When obtaining the composite materials, the polyethyleneterephthalate fibers based nonwoven needle-punched fabrics (and, less often, polypropylene ones) are mainly used as a fibrous reinforcing element.
The primary objective of this study is to investigate the influence of the impregnation degree on polyacetal, polyethyleneterephthalate and polypropylene fibers with aliphatic polyurethane water dispersion onto the deformation properties of the composite materials under consideration.
MATERIALS AND METHODS
The subjects of examination were needle-punched nonwoven fabrics composed of fibers with a linear density of 0.33 tex: polyethyleneterephthalate (with a diameter of 20–25 µm, TU 6-13-0204077-95-91), polypropylene (with a diameter of 27–30 µm, TU 2272-007-5766624-93) and experimental polyacetal fibers with a diameter of 18– 22 µm. The nonwoven fabrics were manufactured with the mechanical molding technique. The surface density of the main needle punching was 180 cm–2.
The linear dimensions of the experimental samples (Table 1) were determined in accordance with the requirements of GOST 15902.2-2003. The nonwoven fabric’s thickness was determined using a thickness gauge with an instrumental error ~0.01 mm under the 10 kPa pressure according to GOST 11358-70. The relative measurement error of the sample’s sizes was ~2%. The mechanical properties of the nonwoven fabrics were established in accordance with the requirements of GOST 15902.3-79 (the relative error ~12%).
The anionic stabilized aliphatic polyethiruretane (IMPRANIL DL 1380, China) water dispersion was used for the impregnation of the nonwoven fabrics. The concentration of the polyurethane in water was ~42%. A 50 by 200 mm sample was immersed in a 500 ml container filled with the dispersion and was flattened with a roller for 3–5 minutes at a room temperature. Removed from the container sample was kept until the dispersion completely drained and was flattened between the rolls with a gap equal to half of the nonwoven fabric thickness. The laboratory technique of sample’s impregnation simulated the industrial one.
The heat treatment of the impregnated nonwoven fabric was carried out at a temperature of 70оС. The impregnation degree of the sample was varied by diluting the polyurethane aqueous dispersion with the distilled water.
The impregnation degree ( CM , rel. units) was calculated from the equation:
Table 1
The characteristics of the initial nonwoven fabrics used for the composite material creation with the polyurethane water dispersion impregnation technique
Fiber |
рf , kg/ m3 |
F , kg/ m2 |
d ×103, m |
р , kg/m3 |
δ, rel.un. |
polyacetal |
1410 |
0,28 |
2,1 |
130 |
0,91 |
polyethyleneterephthalate |
1370 |
0,26 |
3,0 |
120 |
0,91 |
polypropylene |
920 |
0,33 |
2,1 |
110 |
0,89 |
Here: pf – the density of the fiber-forming polymer; d – the thickness, F – the surface density (the mass of the sample with an area of 1 m2) and p – the (bulk) density of the initial nonwoven fabric; δ – the porosity coefficient of the initial material.
MANUFACTURING TECHNOLOGY FOR BUILDING MATERIALS AND PRODUCTS
C M
m i - m
=--------,
m
where m1 and m are the mass (kg) of the samples after and before feeding respectively.
The porosity coefficients of the initial (Table 1) and the impreginated nonwoven fabrics were calculated from equations 2 and 3:

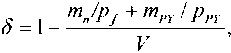
where δ is the porosity coefficient, rel. units; р, рf and рРY are the densities of the fabric, fiber and polyurethane, kg/m3; mn and mРY are the mass of the fabric and polyurethane in the composite material sample after heat treatment, kg.
RESULTS AND DISCUSSION
The specification of the parameter determining the tensile resistance of chemically different fibers based composite materials
The parameter determining the tensile resistance of the nonwoven fabrics and corresponding composite materials was established from the analysis of the dependences of the conditional mechanical stress (σ, MPa) on the relative elongation (ε, %). The dependences of σ on ε in the longitudinal and transverse directions of the samples made of various chemical nature fibers are shown in Fig. 1.
The stretching in the longitudinal and in the transverse directions of the samples occurs in two stages each of which is described by almost linear sections of σ on ε dependencies. These sections’ slope angles analysis shows that the stretching at the second stage occurs at a higher conditional stress (Fig. 1).
The stretching of the non-woven needle-punched fabrics
The two-stage stretching of the nonwoven needle-punched fabrics is a consequence of the specific polymer materials’ bulk structure with an uneven distribution of fiber packing density (Fig. 2).
When punching, the fibers are captured by needle notches with the formation of bundles oriented perpendicular to the surface of the fabric (Fig. 2a). The mechanical stress during the stretching direction is distributed to the bundle’s fibers at various stages of the process uniformly. The fiber packing density and the fiber contact area in the bundle are significantly higher than similar characteristics in the interbundle space [17–23].
The nonwoven fabrics stretching at the first stage of the process is a consequence of straightening and changing the configuration of the fibers between the the bundles. After the straightening and reorientation of the fibers between the bundles in the direction of the mechanical stress (Fig. 2b), the latter is redistributed to the fibers in the bundles (Fig. 2b) which packing density and significant cross-fiber contact area leads to an increase in the probability of relative movement of the fibers. In the extreme case, the rupture of such fibers or their slipping out of the bundles leads to the destruction of the needle-punched nonwoven fabrics [19, 20].
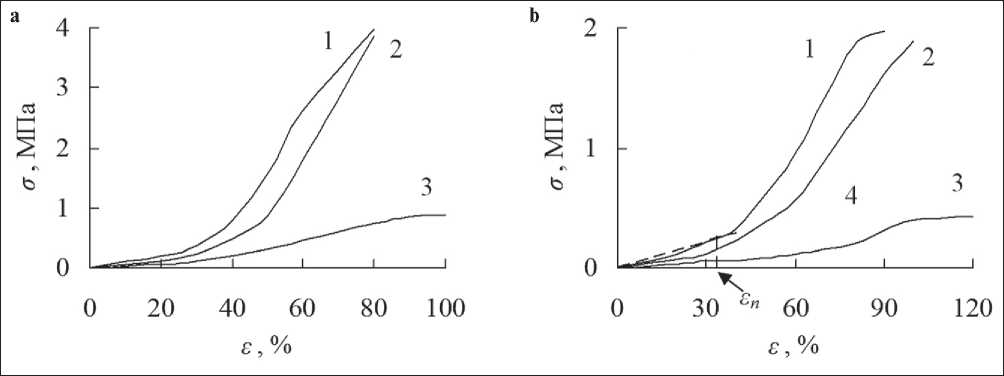
Fig. 1. The dependences of the conditional stress on the elongation during stretching of the nonwoven fabrics made of polyacetal (1), polyethyleneterephthalate (2) and polypropylene (3) fibers in the transverse (a) and longitudinal (b) directions (dotted line 4 is a segment of the dependence σ on ε, showing the stretching at first stage of the process; the arrow shows the relative elongation at which the transition from the first to the second stage of stretching occurs)
MANUFACTURING TECHNOLOGY FOR BUILDING MATERIALS AND PRODUCTS
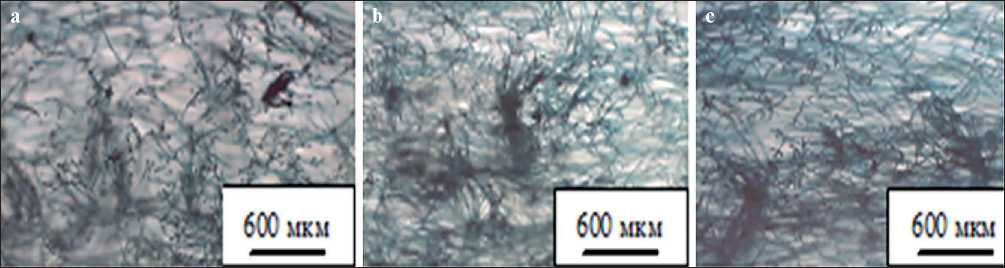
Fig.2. The micrographs of the cuts of the initial (a), 10 (b) and 80 (c) % elongated polyethyleneterephthalate fibers based nonwoven fabrics
The nonwoven fabrics of various compositions are deformed in the longitudinal direction less than in the transverse one (Fig. 1) under the equal mechanical impact. The various degrees of stretching are the consequence of the predominant orientation of the fibers in the transverse direction that is achieved by using a mechanical technique of the nonwoven fabric forming. A high degree of orientation of the fibers in the transverse direction leads to the connection of the bundles with a large number of fibers during the punching process. The bundles are connected by a smaller number of the fibers in the longitudinal direction which leads to a redistribution of the mechanical load on individual fibers and the mutual movement of the fibers even with the relatively small efforts [19, 20].
The dependences of σ on ε of the polyacetal or polyethyleneterephthalate fibers based nonwoven fabrics practically coincide with each other (Fig. 1, curve 1 and 2). It indicates the equal resistance of the samples to the stretching at first and second stages of the process. As it follows from σ on ε dependences (Fig. 1, curve 3) the polypropylene fibers based nonwoven fabrics stretching at first and second stages occurs at a lower conditional stress determined by the less friction coefficient of the polypropylene fibers [35, 36]. The lower ability of the polypropylene fibers to be held in the needle notches limits the formation of the bundles [19, 20]. As a result, the mechanical stress is distributed to a smaller number of polypropylene fibers connecting the bundles.
The stretching of the non-woven needle-punched composite materials reinforced with a polyacetal fibers
The σ on ε dependences of the polyacetal fibers based composite materials are shown in Fig. 3. Their types correspond to similar dependences for polyethyleneterephthalate and polypropylene fibers based nonwoven fabrics.
The stretching of these composite materials occurs in two stages too. However, the conditional stress required
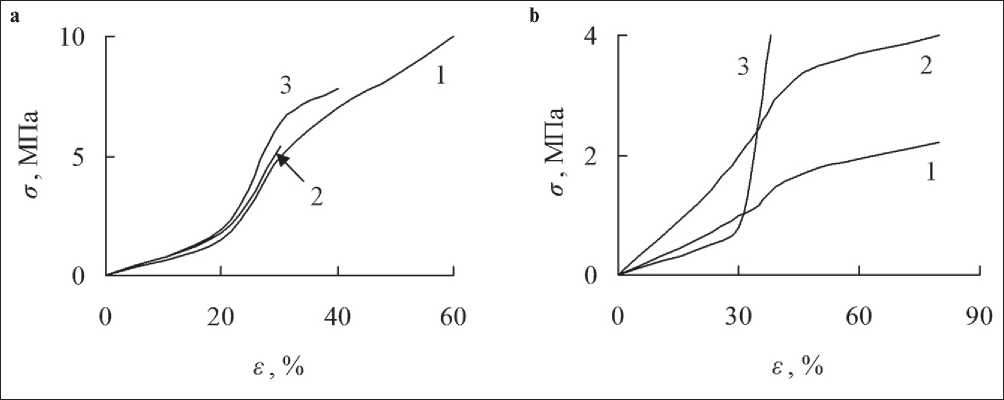
Fig. 3. The dependences of the conditional stress on the relative elongation of polyacetal fibers based composite materials with a degree of impregnation of 0.1 (1), 0.24 (2) and 0.52 (3) MPa in the transverse (a) and longitudinal (b) directions
MANUFACTURING TECHNOLOGY FOR BUILDING MATERIALS AND PRODUCTS for stretching at the first and second stages increases. It is most pronounced in the longitudinal direction of the materials (Fig. 3b). An increase of the impregnation degree from 0 to 0.52 slightly affects the stretching of the composite materials in the transverse direction at first stage of the process. In addition, there is a decrease in the conditional stress required for deformation at first stage of the longitudinal stretching for the material with 0.52 impregnation degree (Fig. 3b, curve 3).
The parametric describing of the tensile resistance for various chemical nature fibers made composite materials reinforced with the fillers
It is of practical interest to determine the tensile resistance of the materials at first stage of stretching due to it leads to the significant increase in porosity and the decrease in the specified functional properties of the nonwoven composite materials with various compositions. The linear section of σ on ε dependencies of the nonwoven composite materials are described by general equation:
ь = Е 。急, ε < ε n ,
where Е 0 – is the effective tensile modulus, MPa; εn – is the relative elongation that shows the transition from first to second stages of stretching.
The effective modulus corresponds to the Young’s ones (designed to assess the elastic/reversible deformation of solids under tension) according to the determination technique. However, the nonwoven’ deformation is not elastic at first stage of stretching. For composite materials, the irreversible movement of fibers is a con- sequence of intermolecular interaction between polyurethane particles, the elongation of the gap between them is significantly less than the tensile elongation at the first stage of the process of stretching composite materials of varying degrees of impregnation. It is due to the consequence of the friction bond between the fibers which rupture leads to the irreversible movement of the fibers in the inter-bundle space. In addition, the Young’s modulus describes the processes occurring with a reversible change in the distance between the molecules or atoms that significantly differs from the macroscopic fibers movement. Therefore, the “effective module» parameter has been introduced to assess the tensile resistance of the nonwoven fabrics and the cooresponding impregnated materials.
The Е 0 and εn parameters are used to determine the effect of the impregnation degree on the tensile strength of the composite materials based on fibrous fillers of various chemical compositions. The technique of εn value specification is shown in Fig. 1b with the dotted line.
The impregnation degree influence on the tensile resistance of chemically different fibers based composite materials
The Е0 on СM dependences in the longitudinal and transverse deformation directions for the discussed nonwoven composite materials are shown in Fig.4.
The Е0 on СМ dependences in the transverse and longitudinal deformation directions for the composite materials with different chemical structure have an extreme appearance. The impregnation degree at which the effective tensile modules have the maximum values depends on the nonwoven fabric composition. The maximum
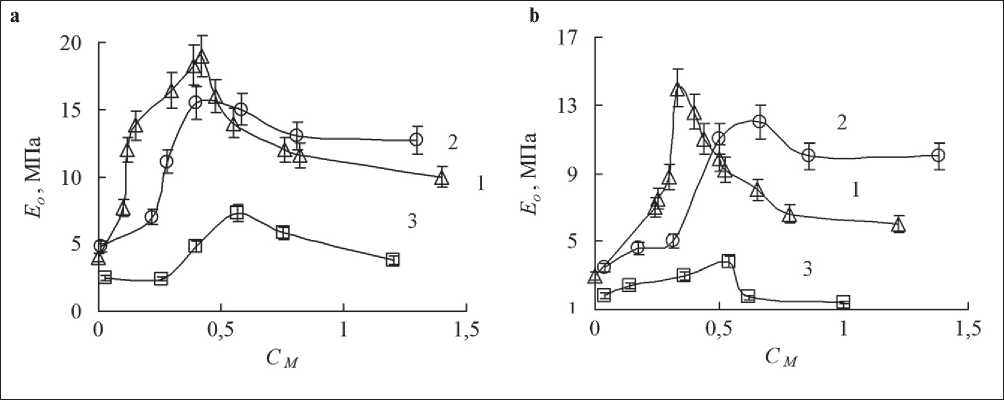
Fig. 4. The effective tensile modulus ( E 0, MPa) (in the transverse (a) and longitudinal (b) directions) on the impregnation degree dependences for the polyacetal (1), polyethyleneterephthalate (2) and polypropylene (3) fibers composite materials
MANUFACTURING TECHNOLOGY FOR BUILDING MATERIALS AND PRODUCTS values of the effective modulus of the polyacetal fiber based composite material is respectively 25% and three times higher than ones of the polyethylene terephthalate and polypropylene fibers based composite materials. The effective tensile modulus of different chemical structure composite materials suddenly decreases (Fig. 4a, b) when the impregnation degree is greater than the optimal.
The maximum value of the effective tensile modulus for the polyacetal fibers based composite materials in the transverse deformation direction is achieved at an impregnation degree of about 0.45 and in the longitudinal direction – about 0.35 (Fig. 4b, curve 1). When using the polyethylene terephthalate and the polypropylene fibers based nonwoven fabrics, the maximum values of the effective tensile modulus in the transverse and longitudinal directions are observed at an impregnation degree of approximately 0.5–0.6 (Fig. 4b, curves 2 and 3).
In addition, it follows from the Е 0 on СМ dependences that the effective longitudinal and transverse tensile modulus begins to increase with a degree of impregnation greater than 0.25 (Fig. 4a, b, curvees 2 and 3) (for the polyethylene terephthalate and polypropylene fibers based materials). The monotonic increase in the effective tensile modulus is observed with an increase of the impregnation degree from 0 to 0.4 in the longitudinal direction and from 0 to 0.5 in the transverse direction (Fig. 4a, b, curve 1) of the experimental samples deformation.
The maximum values of the effective tensile modulus for the polyacetal fibers based composite material with an optimal impregnation degree, as well as an increase in the effective tensile modulus with a change in the impregnation degree from 0 to the optimal value can be explained by the specific wettability of the polyacetal (compared to polyethylene terephthalate and polypropylene) fibers with the polyurethane water dispersion. This concept is confirmed by the studies of the distilled water wetting edge angles for the polyethylene terephthalate, polypropylene and polyacetal films (the relative analogues of fibers’ surfaces). The wetting angle for the polyethylene terephthalate films was 68о, for the polypropylene films – 87о, and for the polyacetal films – 62о [37–39].
The influence of the impregnation degree on the porosity of chemically different fibers based composite materials
It is necessary to explain the decrease in the effective tensile modulus of the composite materials when the degree of impregnation is greater than the optimal value (Fig. 3a, b). We’ve studied the dependence of the porosity coefficient on the impregnation degree for the composite materials based on various chemical compositions fibers (Fig. 5).
At the maximum impregnation degree of 1.22, the porosity coefficient of the considered composite materials
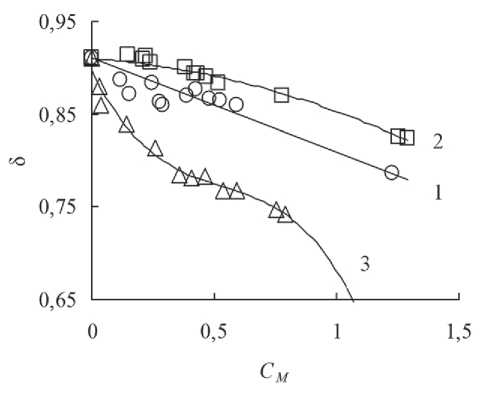
Fig. 5. Dependences of the porosity coefficient on the impregnation degree for the composite materials based on polyacetal (1), polyethylene terephthalate (2) and polypropylene (3) fibers (at CM = 0 – the average porosity coefficient of various compositions fabrics, assumed to be 0.9)
was 0.84 and 0.80, respectively (Fig. 5, curves 1 and 2). We’ve found the porosity coefficient of the polypropylene fibers based composite material equal to 0.6 (at the impregnation degree of 1.22) by the curve 3 (Fig. 4) extrapolation. The lower value of the porosity coefficient for the composite materials based on the polypropylene fibers is a consequence of the worse (compared to polyethylene terephthalate and polyacetal fibers) wettability with the polyurethane water dispersion [37–39] and with the concentration of binder particles in the space between the fibers leading to a decrease in pore volume. When impregnating the nonwoven fabrics made of polyethyleneterephthalate and polyacetal fibers, the binder particles are deposited directly onto the fibers’ surface, which leads to an insignificant change in porosity with a relatively high degree of the impregnation.
The chemically different fiber based composite materials with a degree of impregnation greater than 0.35–0.50 (or greater than the optimal value at which the maximum effective tensile modulus is achieved (Fig. 3)) have the relatively high values of the porosity coefficient, which indicate that the pores of the materials are not filled with particles of binder.
The structure of polyacetal fibers based composite materials when the impregnation degree varying
We studied the cross sections micrographs of the polyacetal fiber based composite materials with the impregnation degrees of 0.17, 0.44 and 0.81 (Fig. 6). With
MANUFACTURING TECHNOLOGY FOR BUILDING MATERIALS AND PRODUCTS
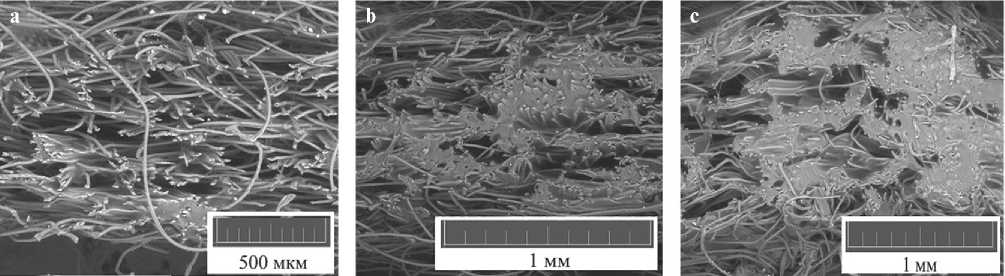
Fig. 6. Micrographs of cross sections of the composite materials reinforced with a polyacetal fibers cloth, with the impregnation degrees of 0.17 (a), 0.44 (b) and 0.81 (c)
a degree of impregnation of 0.44, the effective tensile modulus in the transverse direction has the maximum value (Fig. 3).
The polyacetal fibers based composite materials microphotographs analysis shows that the distribution of the binder in the volume of the fibrous filler is local and depends on the impregnation degree. At the minimum impregnation degree ( CM = 0.17), the binder is concentrated in separate areas along the thickness of the sample (Fig. 5a). Increasing the impregnation degree to 0.44 leads to an increase in the area of the fabric sections filled with the binder (Fig. 5c). At the impregnation degree of 0.81, a relatively uniform distribution throughout the thickness of the composite material is observed (Fig. 5b).
The formation of bonds between the polyacetal fibers at different impregnation degrees is shown in Fig. 7.
Figure 7a shows that at the impregnation degree of 0.17, binder particles are deposited at the points of contact between polyacetal fibers, and the surface of the fibers remains free. As the impregnation degree increases to 0.44, at which the polyacetal fibers based composite material has a maximum effective modulus in the trans- verse direction, nanoscale “bridges” of binder particles are formed between the fibers. The bridges are located at a considerable distance from each other and connect several fibers together.
At the impregnation degree of 0.17, local deposition of binder particles on the fibers’ surface is observed. Bridges are formed between two adjacent fibers located at a short distance less than the diameter of the fibers. The space between the fibers (pores) is not filled with binder particles (Fig. 7b).
The bridges between the fibers of the composite material with the impregnation degree of 0.17 and 0.44 fit tightly to the surface of the fibers, which indicates the significant strength of the bonds between the fibers at the fiber-binder interface. The limitation of the fibers’ mobility in a force field is reflected by an increase in the effective tensile modulus (Fig. 3).
A micrograph of a composite material based on a polyacetal fibers with an impregnation degree of 0.81 is shown in Fig. 8.
The peeling of the binder shell from polyacetal fibers (Fig. 8) is a consequence of polyurethane shrinkage during heat treatment [33, 34]. During heat treatment of the
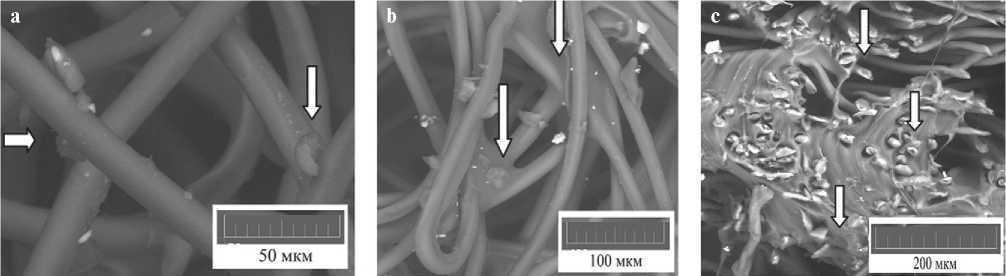
Fig.7. Micrographs of fiber-to-fiber contacts in a composite material based on a polyacetal fibers with the impregnation degrees of 0.17 (a), 0.44 (b) and 0.81 (c) (in Fig. 7a, the arrows point to the contacts between fibers connected by binder particles; in Fig. 7b, the arrows mark the places where nanoscale “bridges” are located between the fibers; in Fig. 7c, the arrows mark the interface between the fibers and binder)
MANUFACTURING TECHNOLOGY FOR BUILDING MATERIALS AND PRODUCTS
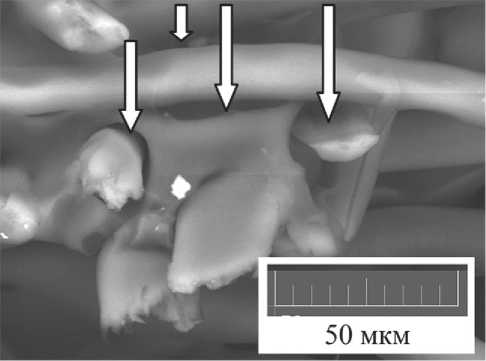
Fig. 8. Micrograph of the contact between polyacetal fibers of a composite material with an impregnation degree of 0.81 (the arrows point to the separation of the binder shell from the fibers)
impregnated fabric, as a result of [volatilization (evaporation)] evaporation of water, the volume of dispersion in the space between the fibers decreases, which leads to the convergence of polyurethane particles and an increase in intermolecular interaction.The relationship between the physical interaction at the polyurethane-polyacetal fiber interface and the intermolecular interaction between polyurethane macromolecules in the volume of the particles depends on the thickness of the adsorption shell of the binder on the surface of the fibers. At a certain thickness of the shell, the intermolecular interaction in the volume of polyurethane particles begins to prevail over the interaction at the interface of the polyurethane-fiber phases, which leads to the delamination of the shell from the fiber surface (Fig. 8).
In addition, the peeling of the polyurethane shell from the polyacetal fiber surface may be the result of the parallel adsorption of both binder particles and water molecules (which is a dispersed medium) on the fibers’ surface. The relatively high content of oxygen atoms in polyacetal macromolecules determines the increased adsorption of water molecules compared to the polyurethane particles. The formation of water molecules shell on the fibers’ surface reduces the bond strength between the binder particles and the fiber surface. This leads to the polymer shell peeling during the heat treatment contributes.
CONCLUSION
– when impregnating the nonwoven fabrics from the polyacetal fibers, the composite materials with a large effective modulus (and tensile strength resistance) were obtained (in comparison with the fabrics made of polyethylene terephthalate and polypropylene fibers);
– the maximum values of the effective tensile modulus for the polyacetal fibers based composite materials are observed in the transverse direction at the impregnation degree of 0.44 and in the longitudinal direction at the impregnation degree of 0.35;
– when the effective tensile modulus maximum is achieved with the optimal value of the impregina-tion degree, the binder particles are concentrated on the polyethyleneterephthalate and polyacetal fibers surfaces, which makes it possible to produce the composite materials for the construction purposes with the porosity of near nonwoven fabrics used.
The work was carried out with the financial support of the Ministry of Science and Higher Education of Russian Federation (State Task No. FZRR-2023-0003)
Список литературы Construction heat and sound insulating composite materials with high tensile strength
- Diabat A., Kannan D., Mathiyazhagan K. Analysis of enablers for implementation of sustainable supply chain management – a textile case. J.Cleaner Production. 2014; 83(4):391–403.
- Datta M. Geotechnology for Environmental Control at Waste Disposal Sites. Indian Geotechnical J. 2012; 42(1): 1–36.
- Neznakomova М., Boteva S., Tzankov L., Elhag М. Non-woven Textile Materials from Waste Fibers for Cleanup of Waters Polluted with Petroleum and Oil Products. Earth Systems and Environment. 2018; 2(3): 413–420.
- Baley C., Gomina M., Breard J., Bourmaud A. Specific features of flax fibres used to manufacture composite materialsr. Inter. J. Material Forming 2019; 12(6): 1023-1059.
- Yakovleva O. I., Sashina E. S., Osipov M. I., Smirnov G. P. Non-Woven Needle Punched Material with Silver Nanoparticles from Natural Silk Fiber Waste. Fiber Chem. 2020; 52(2): 263-268.
- Easwaran P., Lehmann M.J., Wirjadi O. Fiber thickness measurement in scanning electron microscopy images validated using synthetic data. Chem. Eng. Technol. 2016; 39(3): 395–402.
- Shirvan А.R., Hemmatinejad N., Bashari А. PET-Cell Fibers: Synthetic with Natural Effects, Surface Modification of PET Fibers with Luffa Nanowhiskers. J. Polym. Environment. 2017; 25(8): 453–464.
- Azimian M., Kühnle C., Wiegmann A. Design and optimization of fibrous filter media using lifetime multipass simulations. Chem. Eng. Technol. 2018; 41(5): 928–935.
- Pan Z., Liang Y., Tang , M., Sun Z., Hu J., Wang J. Simulation of performance of fibrous filter media composed of cellulose and synthetic fibers. Cellulose. 2019; 26(5): 7051–7065.
- Shabaridharan G., Das А. Study on heat and moisture vapour transmission characteristics through multilayered fabric ensembles. Fibers Polym. 2012; 13(4): 522–528.
- Venkataraman M., Mishra R., Subramaniam V., Gnanamani A., Kotresh T. M., Militky J. Dynamic heat flux measurement for advanced insulation materials. Fibers Polym. 2016; 17(6): 925–931.
- Zimina E. L., Skobova N. V., Sokolov L. E., Grishanova S. S. Technologies for Processing Chemical Fiber Waste of Carpet Production. Fibre Chem. 2019; 51(2): 23–25.
- Gao В., Zoo L., Zuo В. Sound absorption properties of spiral vane electrospun PVA/nano particle nanofiber membrane and non-woven composite material. Fibers Polym. 2016; 17(7): 1090–1096.
- Kalauni K., Pawar S. J. A review on the taxonomy, factors associated with sound absorption and theoretical modeling of porous sound absorbing materials. J. Porous Materials. 2019; 26(3): 1795–1819.
- Thirumurugan V., Kumar M. Design of an Instrument to Determine the Acoustic Characteristics of Non Wovens Made from Recycled Polyester, Jute and Flax. Fibers Polym. 2020; 21(12): 3009–3015.
- Dedov, A.V., Babushkin, S.V., Platonov, A.V., Nazarov, V.G. Heterocapillarity of non-woven canvases at various stages of their production. Fibre Chem. 2001; 33(1): 33-36.
- Bokova, E.S., Dedov, A.V. Mechanical characteristical of needlepunch materials theated with heated air. Fibre Chem. 2012; 44(1): 32–34.
- Dedov A.V., Nazarov V. G. Mechanical Properties of Composite Materials Based on Latex-Impregnated Needle-Punched Nonwoven Fabrics from Fibers of Different Nature. Inorganic Materials: Appl. Research. 2018; 9(1):47–51
- Dedov A. V., Roev B. A., Bobrov V. I., Kulikov G. B., Nazarov V. G. Mechanism of Stretching and Breaking of Needle-Punched Nonwovens. Fibre Chem. 2018; 49(5): 334–337.
- Nazarov V.G., Doronin F.A., Evdokimov A.G., Dedov A.V. Regulation of the wettability of nonwoven cloth by oxyfluorination to improve its impregnation by latex. Fibre Chem. 2020; 52(2): 109-111.
- Dedov A.V., Babushkin S.V., Platonov A.V., Kondratov A.P., Nazarov V.G. Sorptive properties of nonwoven materials. Fibre Chem. 2001; 33(5): 56–58.
- Dedov A.V., Nazarov V.G. Processed Nonwoven Needlepunched Materials with Increased Strength. Fibre Chem. 2015; 47(2): 121–125.
- Dedov A.V., Nazarov V. G. Mechanical Properties of Composite Materials Based on Latex-Impregnated Needle-Punched Nonwoven Fabrics from Fibers of Different Nature. Inorganic Materials: Appl. Resear. 2018; 9(1): 47–51.
- Dedov A. V., Nazarov V. G., Kondratov A. P., Kuznetsov V. A. Abrasion of Impregnated Nonwoven Needle- Punched Fabrics. Fibre Chem. 2020; 51(6): 444–448.
- Wang L., Xu F., Li H., Liu Y., Liu Y. Preparation and stability of aqueous acrylic polyol dispersions for twocomponent waterborne polyurethane. J.Coatings Technol. Res. 2017; 14(1): 215–223.
- Arshad N., Zia K. М., Hussain М. Т., Zuber М., Arshad М.М. Synthesis of novel curcumin-based aqueous polyurethane dispersions for medical textile diligences with potential of antibacterial activities. Polym. Bulletin. 2022; 79(10): 7711–7727.
- Moiz A., Vijayan A., Padhye R., Wang X. Chemical and Water Protective Surface on Cotton Fabric by Pad-Knife-Pad Coating of WPU-PDMS-TMS. Cellulose. 2016; 23(5): 3377–3388.
- Moiz A., Padhye R., Wang X. Coating of TPU-PDMS-TMS on Polycotton Fabrics for Versatile Protection. Polym. 2017; 9(12): 660–668.
- Sikdar P., Islam S., Dhar A., Bhat G., Hinchliffe D., Condon B. Barrier and mechanical properties of waterbased polyurethane-coated hydroentangled cotton nonwovens. J. Coatings Technol. Res. 2022; 19(9): 1255–1267.
- Amid Н., Mazé В., Flickinger M. C., Pourdeyhimi В. Hybrid adsorbent nonwoven structures: a review of current technologies. J. Mater. Sci. 2016; 51(9): 4173–4200.
- Liu R., Chen Y., Fan Н. Design, characterization, dyeing properties, and application of acid-dyeable polyurethane in the manufacture of microfiber synthetic leather. Fibers Polym. 2015; 16(9): 1970–1980.
- Nazarov V.G., Doronin F.A., Evdokimov A.G., Dedov A.V. Regulation of the wettability of nonwoven cloth by oxyfluorination to improve its impregnation by latex. Fibre Chem. 2020; 52(2): 109–111.
- Ahmad N., Khan M B., Ma X., Ul-Haq N. The Influence of Cross- Linking/Chain Extension Structures on Mechanical Properties of HTPB-Based Polyurethane Elastomers. Arab. J. Sci. Eng. 2014; 39(1): 43–51.
- Szołyga M., Dutkiewicz M., Marciniec B. Polyurethane composites based on silsesquioxane derivatives of different structures. J. Thermal Analysis Calorimetry. 2018; 132(9): 1693–1706.
- Hao S, Wenquan F, Lei Z, Fuquan M, Yulong H, Chunpeng H. Experimental study on the mechanical properties of different types of fiber reinforced soil. J. Chin Foreign Highw. 2017; 37(3): 237–241.
- Lu Y., Liu X., Lu K., Li Y., Liu F., Liu P. Properties and Fracture Surface Features of Plaster Mold Reinforced with Short Polypropylene Fibers for Investment Casting. Inter. J.Metalcasting. 2021; 15(4): 700–709.
- Nazarov, V.G., Stolyarov, V.P., Gagarin, M.V. Simulation of chemical modification of polymer surface. J. Fluorine Chem. 2014; 161: 120–127.
- Nazarov, V.G., Stolyarov, V.P. Modified polymer substrates for the formation of submicron particle ensembles from colloidal solution. Colloid J. 2016; 78(1): 75–82.
- Nazarov, V.G., Doronin, F.A., Evdokimov, A.G., Rytikov, G.O., Stolyarov, V.P. Oxyfluorination-Controlled Variations in the Wettability of Polymer Film Surfaces. Colloid J. 2019; 81(2): 146–157.