Creation of a composite material based on plant-based components. Nanotechnologies in construction
Автор: Cherkashina N.I., Pavlenko Z.V., Domarev S.N., Ruchiy A.Yu., Solgalov V.V.
Журнал: Nanotechnologies in Construction: A Scientific Internet-Journal @nanobuild-en
Рубрика: Application of nanomaterials and nanotechnologies in construction
Статья в выпуске: 1 Vol.16, 2024 года.
Бесплатный доступ
Introduction. The study is aimed at analyzing the possibility of creating a building composite material based on amylose and amylopectin with the introduction of crushed walnut shells as a filler. Materials and methods of research. To obtain the composite, the following components were used: distilled water, potato starch (NevaReaktiv, St. Petersburg, Russia), acetic acid 70% (NevaReaktiv, St. Petersburg, Russia), highly dispersed walnut shell powder. For this research, we used walnut shells of the Chandler variety (engrafted) collected form the Belgorod region. The composite was produced in several stages. At the first stage, a mixture of starch and walnut shells was added to distilled water, followed by a pre-prepared 9% acetic acid solution. The resulting mixture was thoroughly mixed, after which it was transferred to a stainless-steel bowl and subjected to heat treatment. The resulting mixture was then pressed with solid-phase compaction method at a pressure of 72 MPa. We studied the physical and mechanical characteristic of the resulting composite, its thermal properties, as well as the hydrophobic-hydrophilic balance of the surface. Results and discussion. The resulting composite has good strength characteristics. Flexural strength at break is σf = 25.85±2.51 MPa and σf = 28.44±5.71 MPa for filling 50% weight and 75% weight. Accordingly, they put it on a par with similar composites made from more conventional thermo- and thermoset polymers. The temperature limit for the composite material exploitation has been established, the upper of which can be considered the temperature at which the polymer matrix begins to soften – 103.1 °C. Conclusion. The results obtained are crucial for understanding the mechanisms involved in creating composite materials made entirely from plant components, utilizing, among other factors, agro-industrial waste.
Botanical raw materials, highly dispersed walnut shell powder, composite material, starch, contact angle of wetting, thermal properties, flexural strength
Короткий адрес: https://sciup.org/142240528
IDR: 142240528 | DOI: 10.15828/2075-8545-2024-16-1-67-76
Текст научной статьи Creation of a composite material based on plant-based components. Nanotechnologies in construction
Original article
Several years ago, the development of high-tech industries began to be marked by the active integration of composite materials and exploration into their potential applications. Through the identification of necessary compositions, it became possible to create materials with specific technological specifications. Certain metals have lost competitiveness under extreme operating conditions due to the exceptional properties of composite materials, including corrosion resistance, high strength, and heat resistance. Another benefit of composite ma- terials is their ease of production without the need for additional processing, thereby lowering the economic costs associated with prolonged, multi-step material preproduction [1–3]. This aspect makes them particularly attractive especially + particularly for autonomous application in the construction industry, the industry of creating advanced spacecraft [4], as well as for strengthening building structures through high-strength connections [5, 6]. Operational parameters are defined during the material creation process, considering = taking into account the thermal, chemical, mechanical properties, and anisotropic behavior of the final product [7].
APPLICATION OF NANOMATERIALS AND NANOTECHNOLOGIES IN CONSTRUCTION
With the development of the composite materials sector, they have become high-demand resources for high-tech industries. Scientists began to study the possibility of introducing various reinforcing substances into the polymer matrix to improve physical and mechanical characteristics. Unreinforced polymers can be used for cladding buildings and as finishing materials [8]. Fiber-reinforced polymers are high-strength, lightweight, corrosion-resistant materials that can be used to create allcomposite structures, to strengthen bridges and buildings, and the provision of thermal and sound insulation for buildings [9, 10]. During the creation of these materials, the matrix substance encases and anchors the reinforcing fibers in specific + certain positions, fostering a robust material interaction at the intercellular level [8].
In the process of widening the scope of application of composite materials, the operational requirements for the final products have been changing, which generated the search for new solutions – modification with chemicals. Due to the introduction of new components, the properties and characteristics of the substance with additives have changed. Modifiers in some cases+ In certain instances facilitate the process of processing products, and also enhance resistance to various forms of degradation, as well as increasing resistance to combustion. Fillers can be organic or inorganic in nature [11, 12].
In turn, they are divided into three groups upon their physical state: dispersed (powdery), fibrous and leafy. The activity of fillers is determined by the following factors: the energy of adhesion of the polymer to the filler, particle dispersion, and the ratio of filler to polymer. For better interaction, the surface of the filler can be further modified. Accordingly, any filler can be made active if necessary [13]. The resource-saving technologies research has become popular in the further development of science. Composite materials are now created with fillers from various waste materials: wood waste [14], metallurgical industry waste [15], waste from the production of cement bonded particle boards [16] and produced with environmentally friendly agricultural wastes fillers [17–20].
Each filler contributed to the improvement of certain strength, decorative, heat-resistant, and corrosion-resistant characteristics of the material. Utilized resourcesaving technologies has effectively solved the problem of reusing raw materials and reclamation of unrecyclable wastes. The production of composites from natural fibers will reduce the use of non-degradable materials.
Modified organic fillers in the matrix of thermoplastic polymers will significantly reduce the cost of the product. Filler modification can generally improve the physical and mechanical properties of the finished material [21, 22]. Polymer composites modified with organic fillers are a competitive alternative to conventional wooden construction materials.
Lignified parts of agricultural wastes are of particular interest: husks, shells, stems and shells of various plants. They are not commonly used in other fields and are a waste of resources. Therefore, it is an inexpensive raw material that can be re-used and effectively applied. [23]. Walnut shells contain a large amount of lignocellulose. Its introduction into the polymer matrix as filler improves the properties of the material, giving it a lower density, physical and mechanical stability due to the creation of strong bonds. To replace the synthetic component in the polymer matrix, a mixture based on amylose and aminopectin will be used. The main benefits of replacing synthetic, inorganic fillers include their natural origin, their high physical and mechanical strength, and their good thermal insulating properties.
The final product will be environmentally friendly and durable, with resistance to external influences. As the components interact, the beneficial qualities of each individual component will have a positive impact on the properties of the final material. Safety for organisms and the environment will be the main criterion for this material [24]. The high physical and mechanical properties of composite materials, including their reliability, resistance to external influences, and durability during operation, ensure their use in a variety of industries, not just in the construction sector. These materials are suitable for use in all high-tech sector that require a durable and reliable product.
The purpose of this research is to study the unique properties of the composite material based on amylose and amylopectin with the introduction of crushed walnut shells as a filler.
MATERIALS AND METHODS OF THE RESEARCH
To obtain the polymer composite, the following components were used: distilled water, potato starch (NevaReaktiv, St. Petersburg, Russia), acetic acid 70% (NevaReaktiv, St. Petersburg, Russia), walnut shell powder (size no more than 160 microns). For the research, we used walnut shells of the Chandler variety (grafted) collected in the Belgorod region. To use the shells as fillers for polymer composites, they were ground into a powder form. Before grinding, the shells were thoroughly washed in running water and dried at 110 оС for 3 hours in order to completely remove any remaining water.
Grinding was performed in two stages. At the first stage, large shell fragments were crushed in a vibration mill. After that, the material was ground to a particle size less than 160 micron in a laboratory batch planetary mill, Tencan XQM-1a (manufactured by Tencan, China). The grinding was done in steel cups made from ShKh-1 steel, steel balls with a diameter of 8 to 10 mm were used as the grinding media. The obtained walnut shell powder
APPLICATION OF NANOMATERIALS AND NANOTECHNOLOGIES IN CONSTRUCTION from the Chandler variety (grafted) was studied by scanning electron microscopy (SEM) on a TESCAN MIRA 3LMU device with the recording of energy-dispersive X-ray spectra (EDS) at several points (microregions) with a built-in spectrometer X-MAX 50 Oxford Instruments (manufactured by TESCAN ORSAY HOLDING, Czech Republic).
The granulometric composition of the resulting walnut shell powder was studied on the Analysette 22 NanoTec plus laser diffraction particle size analyzer with the laser diffraction method in suspension. For this purpose, a small amount of the powder was diluted with 96% isopropyl alcohol. This is done to avoid excessive swelling of the particles and to obtain more accurate results.
The preparation of the polymeric composite was carried out in several stages. At the first stage, a mixture of starch and walnut shells was added to distilled water, then a pre-prepared 9% solution of acetic acid was added. The formulation for the polymeric matrix is based on a modified version of the composition presented in the study [1], the modification consists of a twofold reduction in the water-solid ratio. The resulting mixture was thoroughly mixed and then transferred to a stainless-steel bowl.
The mixture was heated in the bowl on a laboratory electric heating plate. With continuous stirring, the mixture was brought to the boiling point and kept hot for the next 15 minutes. After that, it was allowed to cool to a temperature between 25–30 оС within half an hour. Unlike the initial suspension of starch particles and walnut shells, the resulting mixture has obtained increased viscosity, which indirectly indicates an increase in polymerization degree for the main components of starch.
To obtain a composite press material, the above mixture was dried. For drying, a NuWav-Pro laboratory microwave unit (manufacturer Nutech Analytical, Kolkata, India) was used. Drying schedule: power – 800 W, magnetron frequency – 2450 MHz. Drying the material in a microwave oven has a number of benefits over drying in a convection oven: among them are reduced drying time (~ 5 minutes), heating the liquid throughout the entire volume simultaneously, and a softer mode of heating. Drying was carried out until the moisture completely evaporated.
The formation of material samples was conducted on a tensile testing machine, REM-100 (manufacturer “Metrotest”, Russia), in compression pressing mode. After the resulting press composition had been loaded into a preheated mold at 120 оС, it was manually compacted using a punch and placed in a preheated 120 оС convection oven for 30 minutes. Heating the material is a necessary step in molding the polymer composition, as the polymer matrix in the final press products has thermoplastic qualities. The optimal mode for pressing the samples was selected based on the change in sample density depending on the pressing pressure and is 72 MPa with holding under pressure for 1 min.
The density study of the of the resulting composition and powder materials was conducted by direct measurements of the parameters of a tableted sample with a diameter of 30 mm. The density of the composite was calculated as the ratio of the volume of the resulting sample to its mass.
For studying the tensile strength on the three-point static bending, samples were produced in the form of beams 80 mm long, 10 mm width and 4 mm thick. The test conducted at a constant speed of traverse movement of 2 mm/min, support span was 64 mm. The absolute values of sample deformation and applied force obtained as a result of testing were reduced to the relative value of displacement and flexural strain, respectively. To convert the absolute value of the sample deformation (s, mm) into units of relative deformation (εf, %) the following formula was used:
600$ 左

where s is the deflection of the sample, mm; h – sample height, mm; L – support span, mm. To convert the absolute bending strain (F, N) into units of flexural stress (σf, MPa), the following formula was used:
3FL where F – bending strain, N; L – support span, mm; b – sample width, mm; h – sample height, mm.
The study of wettability, as well as the free energy of the surface, was conducted by the “sessile drop” method, with the measurement the contact angle of wetting (WCA) using the tangential method. The “sessile drop” method involves applying drops of a liquid with a volume of 10 microliters (µl) to the surface of a sample using a glass pipette. To calculate the surface free energy of the composite material using the OWRK method (Owens, Wendt, Rabel, and Kaelble), we studied the wettability of its surface using two liquids with known dispersive and polar surface tension components. The surface free energy was calculated using the OWRK model:

where σ l – the surface tension of the liquid, mJ/m2; θ – contact angle of wetting; σ l D – dispersion component of the surface tension, mJ/m2; σ l P – polar component of the surface tension, mJ/m2; σ sol P – polar component of the free surface energy, mJ/m2; σ sol D – dispersion component of the free surface energy, mJ/m2.
APPLICATION OF NANOMATERIALS AND NANOTECHNOLOGIES IN CONSTRUCTION
RESULTS AND DISCUSSION
Study of highly dispersed walnut shell powder
The study used a previously sifted walnut shell powder, which had been passed through a C12/38 sieve with a mesh size of 160 µm to remove larger particles. The results of the granulometric analysis are shown in Figure 1.
Based on the granulometric analysis data, it can be noted that the granulometric composition is typical for systems obtained by dispersing the initial product in planetary ball mills. The resulting system can be well described by a unimodal distribution with a peak at 49 µm, with most particles falling within the range of 1 to 49 µm.
The resulting particle size is well suited for obtaining maximum strength of the resulting composition with minimal energy consumption, since as the particle size decreases, their specific surface area increases, in the case of the system presented above, a component of the order of ~ 8500 cm2/cm3, and the homogeneity of the resulting mixture increases. The density of the resulting powder is within the range of 1.07±0.01 g/cm3.
Figure 2 shows images of walnut shell powder obtained using a fourth generation scanning electron microscope (SEM) with a TESCAN MIRA 3 Schottky cathode. The data presented in Figure 2 indicate a complex surface morphology of the powder. Walnut shell powder particles have an irregular shape in the form of plates. The crosssectional (largest) particle size varies from 1 to 20 µm.
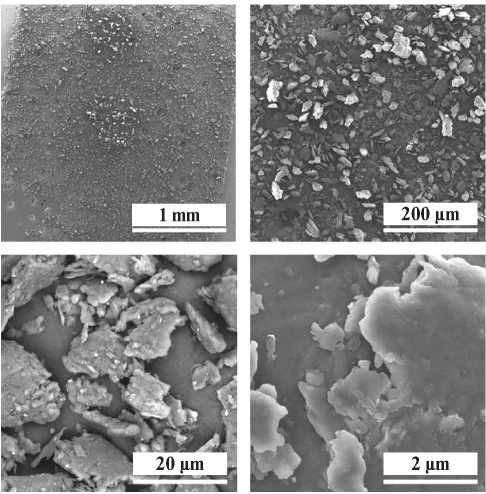
Fig. 2. SEM images of the resulting walnut shell powder
The curves of the combined TG–DSC analysis of walnut powder (Fig. 3) show the presence of several regions associated with various thermal effects.
The thermogravimetric curve contains several sections of mass loss, which occurs due to a number of processes. Thus, in the temperature range from 23.0 to 131.0 oC, a decrease in the mass of the sample to 95.44% is being
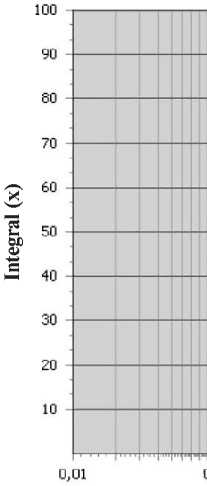
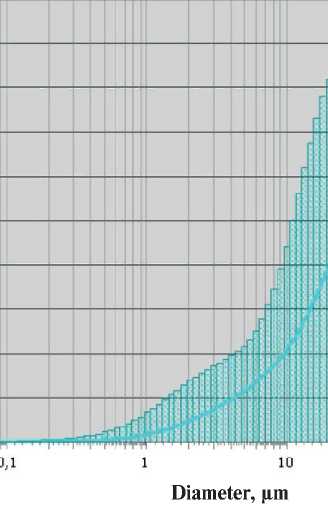
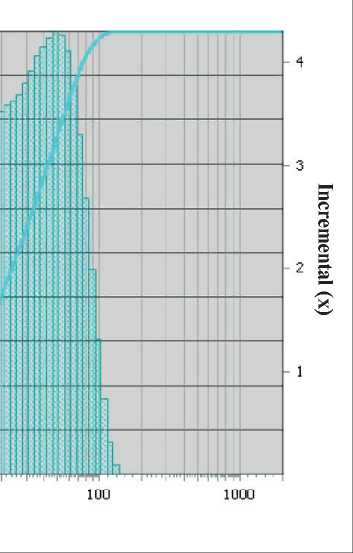
Fig. 1. Particle size distribution of grinding walnut shell powder
APPLICATION OF NANOMATERIALS AND NANOTECHNOLOGIES IN CONSTRUCTION
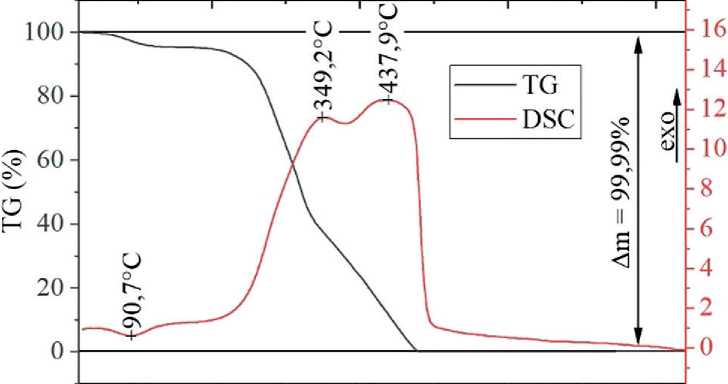
(m/мш) usd
200 400 600 800
Temperature (℃)
Fig. 3. TG–DSC curves of walnut shells recorded. In this case, the DSC curve for this temperature range shows one endothermic peak with a minimum at 90.7 oC. The nature of this peak indicates that the process under this temperature range has been involving energy consumption, and the presence of a subsequent plateau on the TG curve indicates stability of the resulting residue in the temperature range from 131.0 to 207.2 oC. Due to the significant specific surface area of the shell powder (8500 cm2/cm3) and its hydrophilicity, the considered mass loss and the associated endothermic peak are most likely associated with the removal of adsorbed water.
In the next section of the TG curve, in the range from 131.0 to 207.2 oC, there is a plateau, where device does not detect significant mass loss. There are also no thermal effects within the interval; the DSC curve is being within the zero mark.
In the temperature range from 207.2 to 323.7 oC, the device records a significant (about 50%) weight loss of the sample on the TG curve, with an associated exo thermic peak at 349.2 oC. Total mass loss occurs between 349.2 and 476.8 oC, with an associated exothermic peak at 437.9 oC. For organic mixtures, in general, pyrolytic processes occur predominantly in this temperature range. Thus, the peak at 349.2 oC belongs to the pyrolytic decomposition of lignin, noted by the authors in the article [25]. In turn, the peak at 437.9 oC predominantly belongs to the exothermic effect that occurs during the pyrolytic decomposition of cellulose [26].
Study of physical and mechanical parameters of the resulting composition
The polymer press compositions considered in this study are presented in Table 1. The result presented in the table was calculated as the arithmetic mean of three parallel measurements.
The density of the resulting composite largely depends on the amount of filler, which is explained by the lower
Table 1
Studied formulations of the composite
Serial number of the composition |
Composite formulation |
Auxiliary components |
|||
Starch, wt.% |
Walnut shell powder, wt.% |
Composition density, g/cm3 |
Water, ml/100 g composite |
9% acetic acid solution, ml/100 g composite |
|
Compound 1 |
75 |
25 |
1.42±0.01 |
625 |
5 |
Compound 2 |
50 |
50 |
1.43±0.01 |
||
Compound 3 |
25 |
75 |
1.34±0.01 |
APPLICATION OF NANOMATERIALS AND NANOTECHNOLOGIES IN CONSTRUCTION
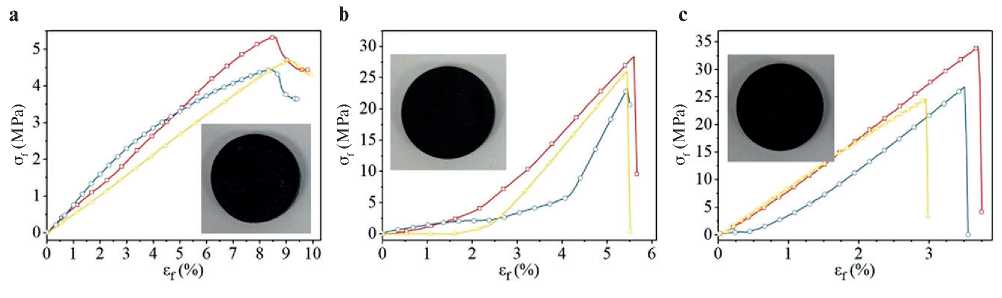
Fig. 4. The “Flexural stress/relative deformation” curves for samples (the insets show the outer appearance of the composition being tested): a – filling 25 wt.%. (σf= 4.81±0.52 MPa); b – filling 50% wt. (σf = 25.85±2.51 MPa); a – filling 75% wt. (σf = 28.44±5.71 MPa)
density of walnut shell powder (1.07±0.01 g/cm3) compared to the polymer matrix (1.40±0.01 g/cm3).
The core strength indicator studied for the resulting polymer composite is the flexural strength at break. Figure 4 shows “the flexural stress/relative deformation” curves obtained as a result of the conducted tests.
Based on the data from the curves presented in Figure 4, the flexural strength at break for compositions with a filling of 25, 50 and 75% wt. are equal to 4.81±0.52 MPa, 25.85±2.51 MPa and 28.44±5.71 MPa, respectively. In this case, the values of the relative deformation index at the flexural strength at break of the samples are in the range of 8.70±0.47% for a composite with a filling of 25 wt.%, 5.51±0.10% for a composite with a filling of 50 wt.%., and 3.39±0.32% for a composite with a filling of 75% wt.
The introduction of a significant amount of walnut powder (over 50% by weight) into the polymer composition provides a beneficial effect on the flexural strength at break of the resulting composite. In the case of this particular composition, there is a nearly five-fold increase in the hardness of the highly filled composite. It is worth noting the change in the shape of the graph “Flexural stress/relative deformation”, in which there is no tensile yield for a highly filled polymer; the test curve in this case is well described by a linear polynomial. In turn, for a composite with a filling of 25% wt. the presence of flow behavior is noted after reaching the flexural strength at break, which is associated with the properties of the polymer matrix.
Wettability study of the resulting composition
The wettability study of the polymer composite was conducted using two solvents - water (σDl = 22.6 mJ/m2; σPl = 50.2 mJ/m2) and isopropyl alcohol (σDl = 3.5 mJ/m2; σPl = 19.5 mJ/ m2). Statistically processed data of contact angle of wetting are presented in Table 2.
When measuring the contact angle of wetting for the surface with isopropyl alcohol, no significant deviations in the WCA value were recorded, however, for water, its significant decrease had been determined with an increase in the filler content in the composite from 25 wt.%. up to 50% wt., followed by a growth with increasing filler content from 50% wt. up to 75% wt. Pictures of the “sessile drops” and the corresponding WCA values are presented in Figure 5.
It is worth noting that the contact angle of wetting for the polymer matrix with water is also in the range of 60– 70o. The untreated walnut shell is completely wetted.
Table 2
The obtained values of the contact angle of wetting for the composite with the solvents
Composite filling, wt.% |
Contact angle of wetting |
Surface free energy |
|||
Water |
Isopropanol |
σDl, mJ/m2 |
σPl, mJ/m2 |
General, mJ/m2 |
|
25% |
76,74±5,75 |
15,21±4,18 |
11,53±0,01 |
16,27±0,57 |
27,8±0,58 |
50% |
62,19±4,31 |
17,01±3,04 |
7,25±0,01 |
32,1±0,16 |
39,35±0,17 |
75% |
98,13±2,05 |
14,23±2,18 |
20,73±0,01 |
1,84±0,08 |
22,57±0,09 |
APPLICATION OF NANOMATERIALS AND NANOTECHNOLOGIES IN CONSTRUCTION
Filling 25% wt.
76.74±5.75 。
Filling 50% wt
62J9±4,31 。
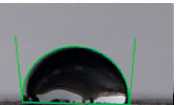
|Filling 75% wt.
98J3±2,05 。
Fig. 5. Representative pictures of “sessile water” drops on a polymer composite
Thermogravimetric and DSC analysis of the resulting composition
For thermogravimetric analysis of the resulting composition with the combined thermogravimetry method (TG) and differential scanning calorimetry (DSC) of the resulting composition, a sample with 50 wt.%. filler content (walnut shell) was selected.
The sample’s thermogram (Fig. 6) is represented by a complex multi-stage decomposition curve, consisting of 3 main sections. In the first section, in the temperature range from 20.0 to 122.1 oC, a decrease in the mass of the sample to 95.11% is noted. On the DSC curve, one endothermic peak is associated with this region, the center of which is at 86.1 oC. Due to the fact that there is no mass loss recorded by the device in the subsequent sec-
20-
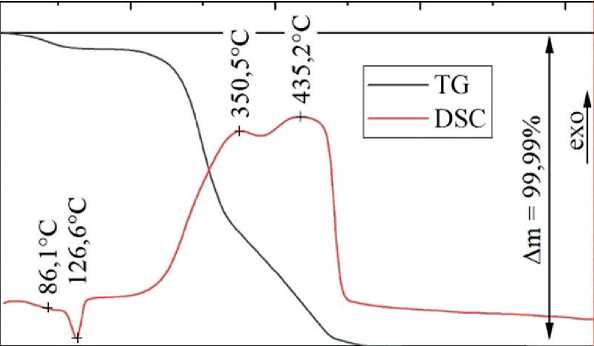
(m/MW) OS 4 2 0 11186420

Fig. 6. TG–DSC curves of the composite with filling of 50% wt. walnut shells
APPLICATION OF NANOMATERIALS AND NANOTECHNOLOGIES IN CONSTRUCTION tion of the curve, and also based on the endothermic nature of the associated peak, it is most likely that the mass loss that occurred in the temperature range from 20.0 to 122.1 oC is associated with the removal of the water adsorbed by polymer composite.
As noted earlier, in the second section of the ther-mogravimetric curve in the range from 122.1 to 130.5 oC, the device has not detected significant mass loss, however, the DSC curve shows the presence of an endothermic peak with a minimum at 126.6 oC. Based on the available academic literature data [22, 27] the above peak refers to the softening of the starch thermoplastic polymer. Thus, it can be judged that the optimal temperature regime for molding the resulting composition is in the range from 122.0 to 130.5 oC (overall width peak at half maximum). The temperature of the composite is softening within 103.1±0.1 oC.
The thermogravimetric curve of the third section of the thermogram is characterized by a multi-step decomposition curve without the formation of intermediate fixed constituent. The range from 250.4 to 329.2 oC accounts for about 50% of the total mass loss of the material. In this temperature range, thermal destruction of cellulose occurs, primarily expressed in dehydration, due to the large-scale representation of thermolabile hydroxyl groups in the structure of cellulose. In the temperature range from 329.2 to 480.6 oC (section 4), almost complete combustion of the organic components of the filler and polymer matrix occurs, after which the thermogravimetric curve passes to section 5.
It is worth noting that sections 3–5 exhibit their own rates of mass loss (which is reflected by the slope of the curve in the thermogram). The DSC curve shows two exothermic peaks associated with these areas at 350.5 oC and 435.2 oC, most likely belonging to the pyrolytic decomposition of lignin and cellulose, respectively [25, 26].
CONCLUSION
Discussed in the article the resulting polymer composition based on a thermoplastic starch polymer has a number of remarkable properties. Compared to untreated walnut shell powder and polymer matrix, the composite has obtained hydrophobic properties, which significantly expands the possibilities of its application.
The resulting composition has showed good strength characteristics. Flexural strength at break is σf = 25.85±2.51 MPa and σf = 28.44±5.71 MPa for filling 50% of wt. and 75% wt. accordingly. We can put it on a par with similar composites made from more conventional thermo- and thermoset polymers. The thermograms study of the resulting composition provides more accurate establishment of the operating temperature limits for the polymer composite, the upper of which can be considered the temperature at which the polymer matrix begins to soften – 103.1 oC, as well as to determine the optimal modes for molding products from a thermoplastic composite.
The resulting polymer composite, particularly compositions with a filling of 50% wt. and 75 wt.%, due to their properties, can rightfully be considered promising materials for several products and consumer goods manufacturing, for which the most appropriate is the use of completely biodegradable material.
Список литературы Creation of a composite material based on plant-based components. Nanotechnologies in construction
- Kablov E.N. Composites: Today and Tomorrow. Metals of Eurasia. 2015; 1: 36–39. (in Russian)
- Lesovik V.S. Stroitel’nye materialy [Construction materials]. Present and future. Vestnik MGSU. 2017; 1: 9–16. https://doi.org/10.22227/1997-0935.2017.1.9-16. (in Russian)
- Klyuev A.V., Kashapov N.F., Klyuev S.V., Zolotareva S.V., Shchekina N.A., Shorstova E.S., Lesovik R.V., Ayubov N.A. Experimental studies of the processes of structure formation of composite mixtures with technogenic mechanoactivated silica component. Construction Materials and Products. 2023; 6 (2): 5 – 18. https://doi.org/10.58224/2618-7183-2023-6-2-5-18
- Cherkashina N.I., Pavlenko V.I., Noskov A.V., Shkaplerov A.N., Kuritsyn A.A., Popova E.V., Zaitsev S.V., Kuprieva O.V., Kashibadze N.V. Synthesis of PI/POSS nanocomposite films based on track nuclear membranes and assessment of their resistance to oxygen plasma flow. Polymer. 2021; 212: 123192. https://doi.org/10.1016/j.polymer.2020.123192
- Kuzina E., Cherkas A., Rimshin V. Technical aspects of using composite materials for strengthening constructions. IOP Conference Series: Materials Science and Engineering. 2018; 365: 032053. https://doi.org/10.1088/1757-899X/365/3/032053
- Volodchenko A.A. Efficient Silicate Composites of Dense Structure using hollow microspheres and Unconventional Aluminosilicate Raw Materials. Construction Materials and Products. 2023. 6 (2): 19 – 34. https://doi.org/10.58224/2618-7183-2023-6-2-19-34
- Shishakina O.A., Palamarchuk A.A. Polymer composite materials in construction. International Journal of Applied and Basic Research. 2019; 12-2:234–238. (in Russian)
- Buzaeva M.V., Ageeva O.V., Antipova I.A. Polymeric basalt fiber composites in construction. Vestnik Moskovskogo informatsionno-tekhnologicheskogo universiteta – Moskovskogo arkhitelno-stroitel’nogo instituta [Bulletin of the Moscow Information and Technological University – Moscow Institute of Architecture]. 2022; 4: 49–54. (in Russian)
- Osnos S.P., Rozhkov A.I., Fedotov A.A. Basalt Continuous Fibers: Characteristics and Advantages. Raw materials, technologies and equipment. Creation of factories and materials. Composite world. 2022; 2:1 8–27. (in Russian)
- Abdul Khalil H.P.S., Chong E.W.N., Owolabi F.A.T., Asniza M., Tye Y.Y., Rizal S., Nurul Fazita M.R., Mohamad Haafiz M.K., Nurmiati Z., Paridah M.T. Enhancement of basic properties of polysaccharide‐based composites with organic and inorganic fillers: A review. Journal of Applied Polymer Science. 2019; 136, 12: 47251. https://doi.org/10.1002/app.47251
- Hayajneh M.T., AL-Oqla F.M., Al-Shrida M.M. Hybrid green organic/inorganic filler polypropylene composites: Morphological study and mechanical performance investigations. e-Polymers. 2021; 1, 1: 710-721. https://doi.org/10.1515/epoly-2021-0074
- Cherkashina N. I., Pavlenko V. I., Sidelnikov R. V., Besedin P. Study of the Resistance of a Polymer Composite with Crystalline Silicon Dioxide to the Effect of the Flow of Oxygen Plasma. Bulletin of the Belgorod State Technological University named after V.G. Shukhov. 2018; 10: 110-118. (in Russian) https://doi.org/10.12737/article_5bd95a78957a23.58646223
- Kolosova A.S., Sokolskaya M.K., Vitkalova I.A. Fillers for modification of modern polymer composite materials. Basic research. 2017; 10-3: 459–465. (in Russian)
- Paskar V.S., Rubleva O.A. Directions of application of eco-friendly products from wood-composite materials based on woodworking waste. Advanced science. 2019; 2(13): 67-71. (in Russian)
- 44-48. Klimenko N.N., Kolokolchikov I.Yu., Mikhailenko N.Yu., Orlova L.A., Sigaev V.N. New building materials with increased strength based on metallurgy waste. Glass and ceramics. 2018; 5: 44-48. (in Russian)
- Kuznetsova N.V., Barinova O.S. Physical and Mechanical Properties of Cement Composite Building Materials with the Use of CBPB Production Waste. Building materials. 2017; 6: 7-9. (in Russian)
- Treshalin Y.M. Design of technological modes for the production of innovative nonwoven composite materials using flax and hemp processing waste. Young Scientists for the Development of the National Technology Initiative (POISK). 2021; 1: 399-400. (in Russian)
- Cherkashina N.I., Pavlenko Z.V., Matveenko D.S., Domarev S.N., Pushkarskaya D.V., Ryzhikh D.A. Synthesis and Characteristics of Composite Material with a Plant-Based Filler. ChemEngineering. 2023; 7 (2): 38. https://doi.org/10.3390/chemengineering7020038
- Zolotarev A.S. Development of modern eco-friendly ones. Heat-insulating materials based on the processing of crop waste. Scientific Journal of Young Scientists. 2022; 5(30): 45–50. (in Russian)
- Paskar V.S., Rubleva O.A. Experimental Justification of Technological Possibilities of the Method of Manufacturing Eco-Friendly Decorative Products from Crushed Wood. Polzunovskiy Almanac. 2020; 1: 59-64. (in Russian)
- Barczewski M., Sałasińska K., Szulc J. Application of sunflower husk, hazelnut shell and walnut shell as waste agricultural fillers for epoxy-based composites: A study into mechanical behavior related to structural and rheological properties. Polymer Testing. 2019; 75: 1-11. https://doi.org/10.1016/j.polymertesting.2019.01.017
- Zuo Y., He X., Li P., Li W., Wu Y. Preparation and Characterization of Hydrophobically Grafted Starches by In Situ Solid Phase Polymerization. Polymers. 2019; 11 (1): 72. https://doi.org/10.3390/polym11010072
- Salasinska K., Barczewski M., Górny R., Kloziński A. Evaluation of highly filled epoxy composites modified with walnut shell waste filler. Polymer Bulletin. 2018; 75 (6): 2511-2528. https://doi.org/10.1007/s00289-017-2163-3
- Jiang T., Duan Q., Zhu J., Liu H., Yu L. Starch-based biodegradable materials: Challenges and opportunities. Advanced Industrial and Engineering Polymer Research. 2020; 3(1): 8-18. https://doi.org/10.1016/j.aiepr.2019.11.003
- Li J., Bai X., Fang Y., Chen Y., Wang X., Chen H., Yang H. Comprehensive mechanism of initial stage for lignin pyrolysis. Combustion and Flame. 2020; 215: P. 1-9. https://doi.org/10.1016/j.combustflame.2020.01.016
- Wang Q., Song H., Pan S., Dong N., Wang X., Sun S. Initial pyrolysis mechanism and product formation of cellulose: An Experimental and Density functional theory(DFT) study. Scientific Reports, 2020; 10 (1): 3626. https://doi.org/10.1038/s41598-020-60095-2
- Sherif M. A. S. Keshk, Abdullah G. Al-Sehemi, New Composite Based on Starch and Mercerized Cellulose. American Journal of Polymer Science. 2013; 3(3): 46-51. https://doi.org/10.5923/j.ajps.20130303.02