Creation of polymer composites with mineral fillers
Автор: Chimchikova M.K., Rysbaeva I.A., Aidaraliev Z.K., Talgatbekova A.Zh., Mamytov A.B.
Журнал: Nanotechnologies in Construction: A Scientific Internet-Journal @nanobuild-en
Рубрика: The results of the specialists’ and scientists’ researches
Статья в выпуске: 1 Vol.17, 2025 года.
Бесплатный доступ
Introduction. Currently, the development of science and technology requires the creation of new polymer composites with high technical characteristics for various industries. One of the primary methods to improve the physical and technical characteristics of polymer composites based on thermoplastic elastomers is by incorporation of natural fillers. In the Kyrgyz Republic, there is particular interest in using fine mineral fillers extracted from local natural resources. The minerals and rocks found in the region are characterized by high availability, extensive reserves, and a variety of properties. The accumulated experience in research and practical application opens up prospects for using these materials to create polymer composites with unique characteristics. This opens up new possibilities for using the cavitation process in various industrial applications, including the grinding of materials. Methods and materials. An experimental hydrocavitation mill has been developed to produce fine powders from minerals and rocks intended for use as fillers in polymer composites. The physicochemical properties of polymer composites and their raw materials were studied using modern instruments and equipment. The fractional composition and physical and technical characteristics of some minerals and rocks used to obtain active fillers for polymer composites are given. Results and Discussion. The fractional composition of crushed fillers with a particle size of less than 0.31 mm is distributed as follows: finely ground basalt – 7.3%, wollastonite – 44.6%, marble dust – 50.26%, brown coal powder – 47.56%. The analysis shows that among the studied fillers, finely ground basalt contains the smallest amount of fine fractions, which is due to its high hardness compared to other minerals such as wollastonite, marble, and coal. Physical and mechanical studies of the resulting polymer composites showed that when finely ground basalt is added, an uneven distribution of basalt powder in the polymer matrix is observed, which leads to a decrease in the strength characteristics of the composite. Therefore, to obtain a more durable material, it is necessary to grind minerals and rocks to the level of microparticles using the cavitation effect. For this purpose, a laboratory mill was created that operates based on the cavitation effect. Fillers at the level of micro- and nanoparticles were obtained using the developed hydro cavitation mill. The physical and technical characteristics of polymer composites with additives of the resulting nanofillers have been determined. The compressive strength of composites with mineral fillers (fraction less than 0.31 mm, content of wollastonite filler in the composite – 25.2%) was 5.47 MPa, with basalt filler – 5.2 MPa, and with leather powder (dust) – 4.25 MPa. Fillers at the level of micro- and nanoparticles were obtained using the developed hydro cavitation mill. The physical and technical characteristics of polymer composites with additives of the resulting nanofillers have been determined. The compressive strength of composites with mineral fillers (fraction less than 0.31 mm, content of wollastonite filler in the composite – 25.2%) was 5.47 MPa, with basalt filler – 5.2 MPa, and with leather powder (dust) – 4.25 MPa. The compressive strength of the composite with the addition of carbon filler (13.2%) was 4.2 MPa. The introduction of up to 14.2% of mineral fillers into the composition of the composite increases its heat resistance: when adding basalt filler – up to 106 °C, and wollastonite – up to 114 °C. Conclusion. The fractional composition of mineral fillers based on inorganic raw materials studied for their use in creating polymer composites. A hydro cavitation mill was made and a method for processing fillers from minerals and rocks was developed. New polymer composites were obtained with the addition of basalt, wollastonite, marble, and leather industry waste. Studies have been carried out on the physical and technical characteristics of these polymer composites depending on the content of fillers, such as basalt, wollastonite, marble and leather industry waste.
Polymer composites, fine powders, basalt filler, micro- and nanoparticles, composite
Короткий адрес: https://sciup.org/142243358
IDR: 142243358 | DOI: 10.15828/2075-8545-2025-17-1-59-73
Текст научной статьи Creation of polymer composites with mineral fillers
Original article
In modern conditions, polymer composites are widely used in various industries. This is due to the available technology for processing polymers, their relatively low cost, as well as the ability to create durable and lightweight products for various purposes.
Composites based on polymers and mineral fillers are systems consisting of two or more components with different chemical compositions and structures. Reinforcing elements improve the physical and technical characteristics of the material, and matrix components form a frame that provides a connection between the reinforcing elements [1–3].
Nanocomposite materials are composite materials with nanoscale components that are used in architectural construction, surface coating, automotive industry, space industry and high technology [4–9].
Adding fillers from various natural sources is one of the effective methods for improving polymer composite materials based on thermoplastic elastomers [10–16]. In the Kyrgyz Republic, the use of fine mineral fillers extracted from local natural resources is of particular interest. The minerals and rocks available in the Kyrgyz Republic are characterized by availability, extensive reserves and a variety of properties. The experience of their processing and application, accumulated through scientific and practical means, opens up opportunities for the use of these materials in the creation of polymer composite materials for various purposes with improved properties [17–20]. The physical and technical characteristics of polymer composites can be enhanced by reinforcement using various fillers, depending on their fractional composition. Unlike other types of fillers, mineral fillers do not form a homogeneous material with the polymer. Instead, they are distributed in the polymer in the form of separate particles constituting a separate phase, which requires preliminary preparation and processing of fillers by certain requirements [1–20].
Fillers in polymers, whether in powder, fiber, or sheet form, can change the flow and viscosity of the material, affecting flow rates. Their presence can also modify the conditions of cavitation, which occurs when a certain flow velocity is reached when the pressure becomes equal to the saturated vapor pressure. This critical speed corresponds to the moment the cavitation begins. Modern technologies actively use the cavitation process for various purposes, including the creation of installations for grinding materials [21–23].
METHODS AND MATERIALS
The granulometric method has been used to determine the fractional composition of finely ground material in various ways. Fine powder of basalt, wollastonite, marble and coal from local mineral raw materials is distributed in a ball mill using a set of sieves ranging in size from 0.14 to 10 mm.
Previously, finely ground natural basalt from the Suluu-Terek deposit was used to create composites [11].
The physical and mechanical characteristics of polymer composites created based on mineral fillers were studied using an RT-250 M tensile testing machine. Thermoplastic elastomer was chosen as the polymer, while the percentage and size of filler fractions varied. Fillers included finely ground basalt stone, wollastonite, marble, coal and leather dust.
The particle sizes of finely ground minerals and rocks after the cavitation process as fillers were determined using a Quanta 200i 3D scanning electron microscope [24]. Studies were also carried out on the chemical resistance of the resulting polymer composites to water, ethyl alcohol, gasoline, acetic acid and industrial oil. Fine powdered fillers were used to create polymer composites. Table 1 contains data on such inorganic-based fillers available in the Kyrgyz Republic.
Table 1 shows various ranges of filler particle sizes, ranging from more than 10 mm to less than 0.31 mm.
Table 1. Finely ground fillers on an inorganic basis
Sample No. |
Sieve diameter, mm |
Fine fillers, % |
|||
Basalt powder (Kashka-Suu) |
Wollastonite powder |
Marble powder |
Brown coal powder |
||
1 |
More than 10 mm |
36.2 |
0.4 |
0.2 |
0.7 |
2 |
10–5 |
23.1 |
12.7 |
3.4 |
10.2 |
3 |
5–2.5 |
16.5 |
7.6 |
5.8 |
6.3 |
4 |
2.5–1.25 |
8.5 |
14.1 |
15.8 |
16.3 |
5 |
1.25–0.31 |
8.6 |
21.2 |
24.6 |
19.5 |
6 |
Below 0.31 |
7.1 |
44 |
50.2 |
47 |
THE RESULTS OF THE SPECIALISTS’ AND SCIENTISTS’ RESEARCHES
Particular attention should be paid to the last range, where the percentage of fine fillers is quite high. Wollastonite powder, dolomite marble powder and brown coal powder in the range of less than 0.31 mm have a high percentage of 44÷50.2%, indicating the need for processing to reduce particle sizes and ensure more uniform distribution.
Having considered the sizes of filler fractions and their insufficient performance properties, it is proposed to use the cavitation method in a liquid medium to reduce the size of filler particles. For this purpose, the use of a hydrocavitator, shown in Figure 1, is considered.
Finely ground mineral fillers in a hydro cavitation mill analyzed, taking into account the processing time carried out every 4 hours.
RESULTS AND DISCUSSION
Obtained results after study of fillers influence on physical and mechanical characteristics of the polymer composite shown in the table 2.
Analysis of the table data allows us to conclude that the type and size of filler particles have a significant influence on the characteristics of the composite. The high strength of the composite (3.5–5.2 MPa) is ensured by an increase in the content of finely ground basalt to 40.0% and wollastonite powder to 40.0% with a fraction of less than 0.31 mm, which indicates increased adhesion between the filler and the polymer matrix. Other fillers, such as
marble dust, coal dust and leather dust, do not show such high physical and technical values. Thus, coal dust has the minimum strength (2.91 MPa), as well as the lowest density (1.05 g/cm³) and hardness (59.1 conventional units). Marble dust and leather dust also do not have sufficient physical and technical characteristics compared to finely ground basalt and wollastonite.
Fillers for polymer composites with a fraction below 0.31 mm have higher hardness and density, which is associated with their uniform distribution in the composite matrix.
A graph of changes in the density of polymer composites depending on the content of fillers is shown in Fig. 2. From Figure 2 it can be seen that at a low content of fillers (curves 2 and 3), the density is almost the same. However, with an increase in the percentage of basalt fibers and powder, a decrease in density is observed (curve 2). Averaged graphs show linear behavior composite.
Averaged graphs show linear behavior. However, when finely ground basalt is added in an amount of 3–4%, the density change graph becomes nonlinear (the line takes the shape of a parabola), which indicates a significant effect on the properties of the composite.
It is observed that increasing the percentage of mineral filler in the composite leads to an increase in the density of the material. For example, introducing up to 14% fillers causes an increase in density by 10% and 15% for finely
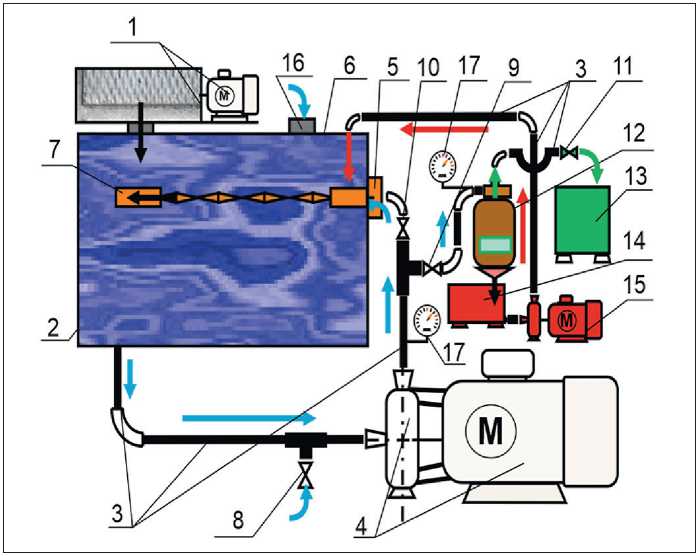
Fig. 1. Hydrocavitation mill: 1 – grinder; 2 – capacity; 3 – pipes; 4, 15 – pumps; 5 – vortex; 6 – cavitation chamber; 7 – vortex brake; 8÷11 – valves; 12 – hydraulic separator; 13 – container for processing field; 14 – tank (large filler fraction); 16 – water fills; 17 – pressure gauge for measuring pressure
THE RESULTS OF THE SPECIALISTS’ AND SCIENTISTS’ RESEARCHES
Д 1
Table 2. Physical and technical characteristics of polymer composites
Content and fraction of filler |
δ stretching, МPа |
εrel., % |
ε perm. , % |
ρ, g/cm3 |
Hardness, a.u. |
|
Filler |
Fraction, mm |
|||||
Thermoplastic elastomer |
– |
3.75 |
265.2 |
20.2 |
1.07 |
57.2 |
Finely ground basalt (25.0%) |
0.31÷2.5 |
3.62 |
256.3 |
21.1 |
1.15 |
64.1 |
2.5÷1.25 |
3.54 |
254.2 |
24.3 |
1.16 |
66.2 |
|
1.25÷0.31 |
3.61 |
258.1 |
21.2 |
1.14 |
63.1 |
|
< 0.315 |
4.82 |
289.3 |
18.1 |
1.13 |
62.3 |
|
Finely ground basalt (40.0%) |
0.31÷2.5 |
3.51 |
251.4 |
23.2 |
1.18 |
67.4 |
2.5÷1.25 |
3.36 |
240.5 |
28.1 |
1.25 |
69.1 |
|
1.25÷0.31 |
3.52 |
252.3 |
23.2 |
1.16 |
66.3 |
|
< 0.31 |
5.21 |
315.2 |
22.3 |
1.13 |
65.2 |
|
Finely ground wollastonite (25.0%) |
0.31÷2.5 |
4.0 |
280.1 |
21.2 |
1.14 |
63.2 |
2.5÷1.25 |
3.6 |
25.2 |
24.2 |
1.21 |
67.3 |
|
1.25÷0.31 |
4.1 |
302.1 |
20.1 |
1.12 |
61.2 |
|
< 0.31 |
5.45 |
341.2 |
17.2 |
1.09 |
60.2 |
|
Finely ground wollastonite (40.0%) |
0.31÷2.5 |
4.2 |
301.3 |
22.2 |
1.31 |
68.3 |
2.5÷1.25 |
3.4 |
250.2 |
25.2 |
1.33 |
70.4 |
|
1.25÷0.31 |
4.6 |
286.3 |
21.1 |
1.28 |
69.4 |
|
< 0.315 |
5.6 |
342.1 |
20.4 |
1.25 |
63.3 |
|
Marble dust (25.0%) |
< 0.31 |
3.9 |
278.5 |
20.3 |
1.15 |
61.2 |
Carbon dust (25.0%) |
< 0.31 |
2.91 |
175.3 |
20.5 |
1.05 |
59.1 |
Leather dust (25.0%) |
< 0.31 |
4.2 |
282.2 |
24.5 |
1.03 |
60.3 |
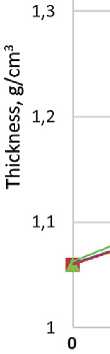

♦ Compositions with bazalt fibers
I I Compositions with bazalt powder
△ Compositions with wollastonite powder
Fig. 2. Changes in the density of polymer composites depending on the percentage of mineral fillers
THE RESULTS OF THE SPECIALISTS’ AND SCIENTISTS’ RESEARCHES ground basalt and by 17% for finely ground wollastonite. Increasing the percentage of filler also increases the viscosity of the composite material, making it more difficult to process.
Table 3 presents the obtained results of the physical and technical characteristics of composites with mineral fillers.
Finely ground wollastonite has proven to be an active filler for thermoplastics, increasing the tensile strength of the composite by 22% in the content range up to 14%. This effect is explained by a mathematical relationship in the form of a third-order polynomial.
Finely ground basalt stone did not prove to be an active filler for the divinylstyrene matrix of thermoplastic elastomer. The decrease in tensile strength with increasing filler content is described by linear equations for both powder and short fibers. The decrease in the tensile strength of composites with short basalt fibers is associated
with their uneven distribution in the volume of the polymer: coefficient –0.088φ for powder compared to coefficient –0.062φ for fibrous filler. The formation of large aggregates of short basalt fibers makes it difficult to distribute them evenly, which in turn leads to a greater reduction in tensile strength than would be expected based on a linear relationship.
From Table 3 and Figure 3, it can be seen that the addition of finely ground basalt to the composite led to an increase in residual stress and a decrease in elongation.
The degree of swelling of composites based on mineral fillers in technical oil and acetic acid is presented in Table 4, and the kinetics of their swelling is shown in Figures 4–8. However, further swelling of samples containing wollastonite and basalt with a fraction of 2.5–1.25 mm as fillers occurs faster than for samples with fraction sizes of less than 0.31 mm. The highest degree of swelling in technical oil is observed in samples
Table 3. Physicomechanical characteristics of composites with mineral fillers
Composite |
Filler content, % (mass.) |
δ stretching, МPа |
εrel., % |
ε perm. , % |
Composite with finely ground basalt |
4.7 |
3.7 |
266 |
20 |
9 |
3.67 |
263 |
20.1 |
|
13 |
3.65 |
260 |
20.4 |
|
16.7 |
3.62 |
258 |
20.8 |
|
20 |
3.6 |
256 |
21 |
|
23 |
3.58 |
254 |
21.6 |
|
25.9 |
3.53 |
253 |
22.2 |
|
28.6 |
3,5 |
251 |
23 |
|
Composite with basalt fibers |
4.7 |
3.68 |
265 |
20 |
9 |
3.65 |
261 |
20 |
|
13 |
3.63 |
260 |
21 |
|
16.7 |
3.58 |
256 |
23 |
|
20 |
3.53 |
254 |
24 |
|
23 |
3.5 |
251 |
25 |
|
25.9 |
3.43 |
245 |
27 |
|
28.6 |
3.35 |
240 |
28 |
|
Composite with finely ground wollastonite |
4.7 |
3.72 |
268 |
20 |
9 |
3.8 |
270 |
20.1 |
|
13 |
3.84 |
273 |
20.3 |
|
16.7 |
3.9 |
277 |
20.7 |
|
20 |
4.0 |
280 |
21 |
|
23 |
4.02 |
287 |
21.2 |
|
25.9 |
4.05 |
295 |
21.7 |
|
28.6 |
4.1 |
301 |
22 |
THE RESULTS OF THE SPECIALISTS’ AND SCIENTISTS’ RESEARCHES
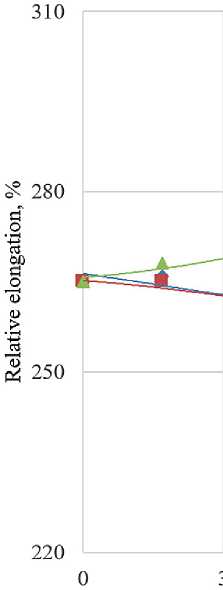
у = 0,1427x2 + о,6147х + 265,74
у = 0,0045x2 - 1,1966х + 266,39
у = -0,0889х2 - 0,581х + 265,19
6 9
♦ Composition with bazalt powder
■ Composition with bazalt fiber
Filler composition, proccessed %
Fig. 3. Relative elongation of composites with mineral fillers at break, % of composites containing leather dust and coal powder as fillers.
An analysis of the swelling kinetics curves of the resulting polymer composites with mineral fillers in technical oil showed that all composite samples remained stable upon contact for up to 24 hours (Fig. 4–8). However, further swelling of samples containing wollastonite and basalt with a fraction of 2.5–1.25 mm as fillers occurs faster than for samples with fraction sizes of less than 0.31 mm.
The highest degree of swelling in technical oil is observed in samples of composites containing leather dust and coal powder as fillers.
Results of the analysis of Fig. 4–8 indicate that all composite compositions were resistant to acetic acid. A composite with finely ground wollastonite as a filler showed a particularly high degree of resistance to acetic acid, while composites with carbon powder turned out to be less stable.
When exposed to gasoline, the resulting polymer composites demonstrated relative stability after short contact (2–4 hours). The most stable were composites with finely ground wollastonite with fraction sizes of 2.5– 1.25 mm. However, with prolonged contact (4–8 hours), the composites became sticky, lost their shape and began to swell.
After immersing the composites in water for 48 hours, no changes in their size and weight were observed.
Next, the fractional composition of finely ground materials obtained in a laboratory hydrocavitator mill was analyzed (Fig. 1).
Electron microscopy of the surfaces of mineral fillers was obtained using a Quanta 200i 3D scanning electron microscope, the image is shown in Fig. 9.
After further grinding of finely ground basalt using a hydrocavitation mill, its particle sizes sharply decreased from the micron range to the nanorange (Fig. 9). Particle sizes range from 77 to 751 nm. During grinding using a hydrocavitation mill, an increase in the content of fine fractions is observed due to the destruction of large fractions of minerals. Figure 10 shows the dynamics of changes in powder sizes.
After completion of hydrocavitation grinding, the composition of the fractions becomes heterogeneous. Large fractions predominate: 500÷700 and above 700 nm. Small fractions: 50÷100 and from 100÷300 nm make up 30.0% of the volume (Fig. 10).
The results of energy dispersive spectroscopy of finely ground basalt after the cavitation grinding process are presented in Fig. 11a and b.
Comparing the spectra of finely ground basalt before and after the grinding process in a hydrocavitation mill,
THE RESULTS OF THE SPECIALISTS’ AND SCIENTISTS’ RESEARCHES we observe an increase in the oxygen and carbon content by 1.5–2 times. This fact indicates that cavitation is not only a physical, but also a physicochemical process.
The cavitation process occurs at different temperatures and with strong hydraulic shock of the finely ground powder under study. The combination of these two factors leads not only to the mechanical process of grinding,
but also to the occurrence of physical and chemical processes of processing the surface of powdered materials. Table 5 shows the physical and mechanical characteristics of polymer composites with basalt powder after the cavitation process.
As can be seen from Table 5 and Figure 12, the tensile strength of the composite containing finely ground basalt
Table 4. Swelling capacity of polymer composites at different contents and fractions of fillers, %
Content and fraction of filler |
Swelling, % |
||||||||
Filler content, % |
Fractions, mm |
In technical oil |
In acetic acid |
||||||
8 h |
24 h |
48 h |
72 h |
96 h |
2 h |
8 h |
24 h |
||
Without filler |
0.00 |
6.4 |
12.6 |
22 |
28.4 |
28.3 |
2.6 |
5.2 |
8. 0 |
Finely ground basalt at 25.0 % |
Components of fraction |
4.2 |
10.3 |
19.6 |
24.6 |
25.4 |
1.7 |
4.3 |
7.7 |
2.5–1.25 |
3.3 |
9.2 |
19.7 |
24.8 |
27 |
3.7 |
7.2 |
7.7 |
|
1.25–0.31 |
5.0 |
9.5 |
19.4 |
24.1 |
26.3 |
2.2 |
4.0 |
6.9 |
|
Less than 0.31 |
6.2 |
9.7 |
17.4 |
23 |
24.2 |
2 |
3.3 |
6.4 |
|
Finely ground basalt at 40.0% |
Components of fraction |
4.3 |
8.0 |
16.0 |
21.0 |
24.4 |
2.0 |
3.2 |
6.2 |
2.5–1.25 |
2.8 |
8.4 |
16.7 |
22.4 |
25.1 |
2.0 |
3.5 |
6.4 |
|
1.25–0.31 |
3.6 |
8.1 |
16.4 |
22.1 |
24.7 |
1.7 |
3.3 |
6.0 |
|
Less than 0.31 |
5.2 |
7.7 |
15.6 |
20.4 |
23.0 |
1.5 |
3.0 |
5.7 |
|
Finely ground wollastonite at 25.0% |
Components of fraction |
5.3 |
9.6 |
16.5 |
21.0 |
26,8 |
0.8 |
3.3 |
5.7 |
2.5–1.25 |
7.2 |
14.3 |
25.1 |
32.2 |
32.3 |
1.0 |
3.3 |
9.7 |
|
1.25–0.31 |
5.8 |
11.2 |
23.5 |
26.8 |
27.0 |
0.7 |
3.2 |
4.6 |
|
Less than 0.31 |
3.5 |
8.8 |
17.0 |
22.5 |
23.4 |
0.7 |
3.0 |
3.1 |
|
Finely ground wollastonite at 40.0% |
Components of fraction |
2.7 |
9.2 |
15.3 |
20.5 |
21.0 |
0.2 |
3.2 |
3.3 |
2.5–1.25 |
2.7 |
7.9 |
15.8 |
21.0 |
22.1 |
0.1 |
3.1 |
3.5 |
|
1.25–0.31 |
2.8 |
8.3 |
15.5 |
21.1 |
22.0 |
0.1 |
3.0 |
3.1 |
|
Less than 0.31 |
3.3 |
7.7 |
14.4 |
20.0 |
20.1 |
0.2 |
2.8 |
2.9 |
|
Carbon dust at 25.0% |
Components of fraction |
13.8 |
19.0 |
31.1 |
41.5 |
41.6 |
6.7 |
10.1 |
20.1 |
Мarble dust at 25.0% |
Less than 0.31 |
4.6 |
9.1 |
21.3 |
27.4 |
28.0 |
3.4 |
6.7 |
16.7 |
Leather dust at 25.0% |
Components of fraction |
7.5 |
18.6 |
26.0 |
29.7 |
37.1 |
3.5 |
6.9 |
17.3 |
THE RESULTS OF THE SPECIALISTS’ AND SCIENTISTS’ RESEARCHES
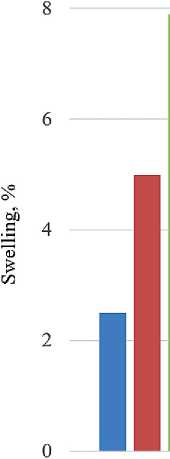
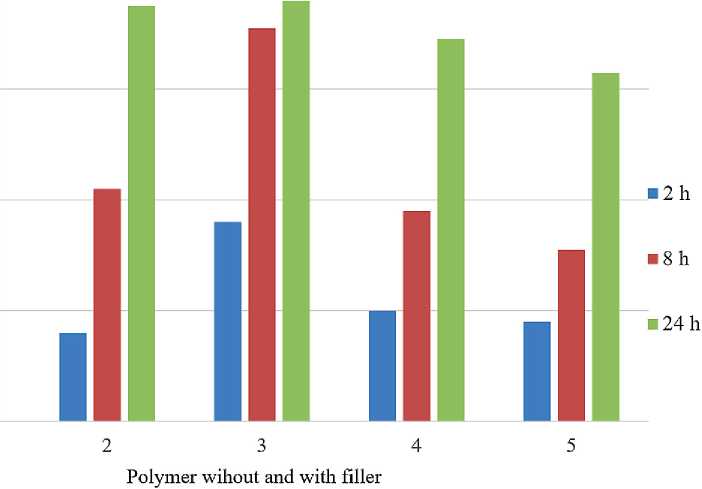
Fig. 4. Swelling diagram of polymer composite without filler and with filler (finely ground basalt of various fractions – 25%) in acetic acid, %: 1 – without filler; 2 – fraction composition; 3 – fraction at 2.5–1.25 mm;
4 – fractions at 1.25–0.31 mm; 5 – filler fraction less than 0.31 mm
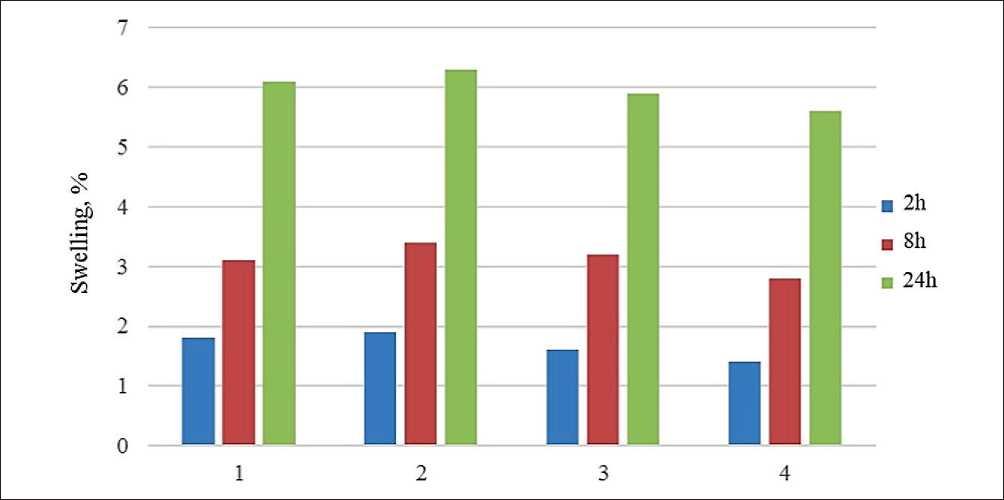
Fig. 5. Diagram of swelling of a polymer composite from finely ground basalt (40%) with different fractions in acetic acid, %: 1 – composition of fractions; 2 – filler fraction size 2.5–1.25 mm; 3 – filler fraction size 1.25–0.31 mm; 4 – filler fraction size at less than 0.31 mm
THE RESULTS OF THE SPECIALISTS’ AND SCIENTISTS’ RESEARCHES
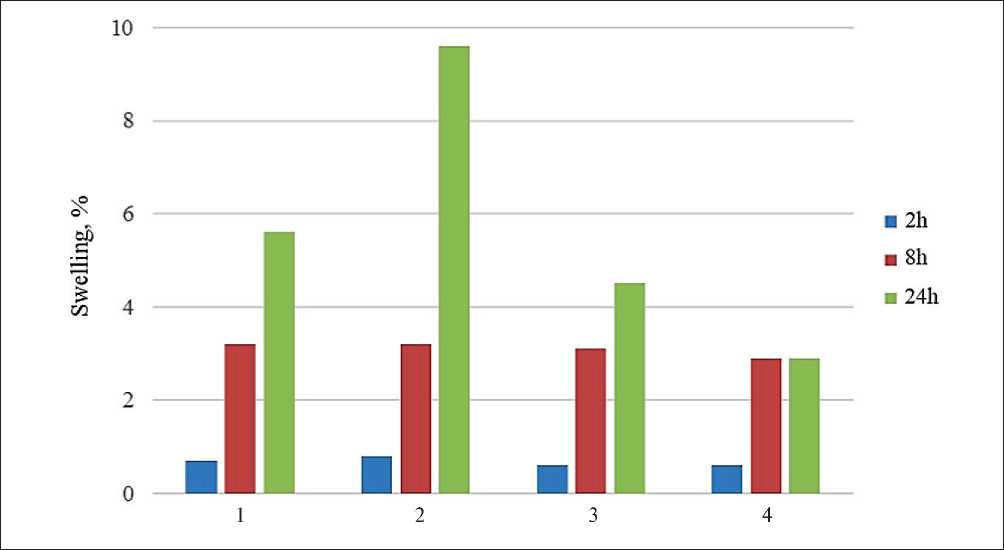
Fig. 6. Diagram of swelling of a polymer composite with finely ground wollastonite (25.0%) with different fractions in acetic acid, %: 1 – composition of fractions; 2 – filler fraction at 2.5–1.25 mm; 3 – filler fraction at 1.25–0.31 mm; 4 – filler fraction at less than 0.31 mm
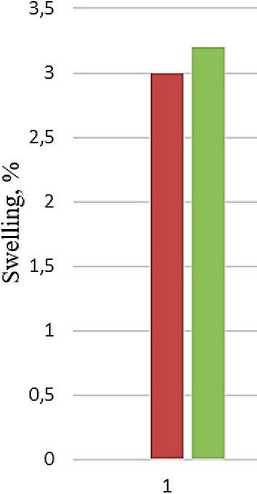
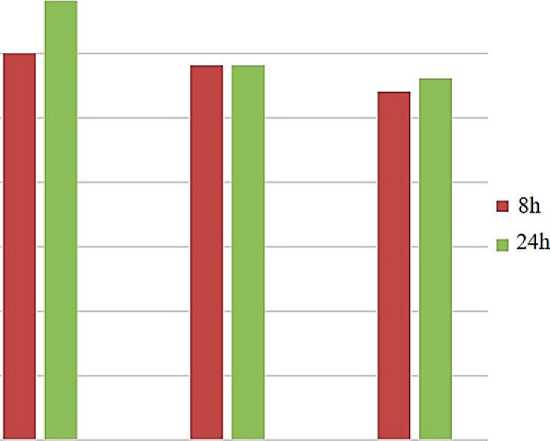
2 3 4
Fig. 7. Diagram of swelling of a polymer composite with finely ground wollastonite (40.0%) of various fraction sizes in acetic acid, %: 1 – mixture of fractions; 2 – filler fraction size 2.5–1.25 mm; 3 – filler fraction size 1.25–0.31 mm; 4 – filler fraction size less than 0.31
THE RESULTS OF THE SPECIALISTS’ AND SCIENTISTS’ RESEARCHES
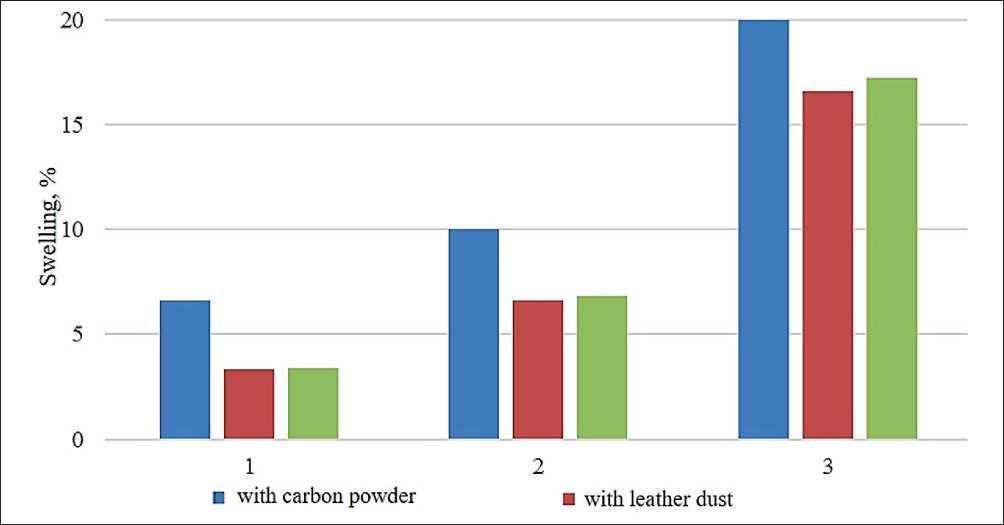
Fig. 8. Diagram of swelling in acetic acid of a polymer composite with the addition of various fillers (25.0%), %: 1 – after 2 hours; 2 – after 8 hours; 3 – after 24 hours
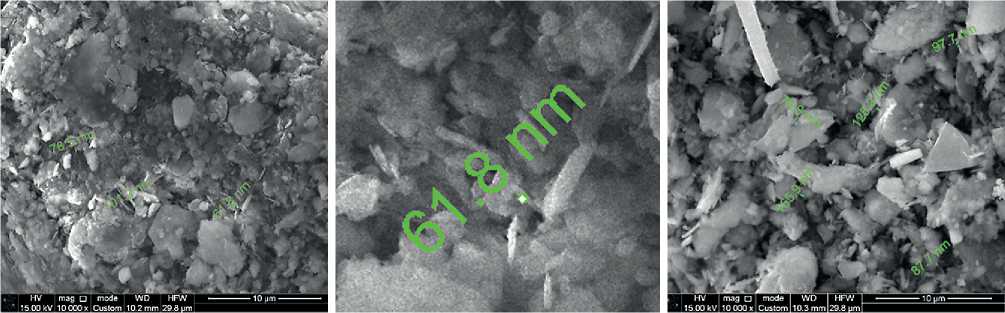
Fig. 9. Electron microscopy of mineral filler surfaces
虫 ^со^с^о ф£з-о>
20• ,
10-
1 2345
而 3
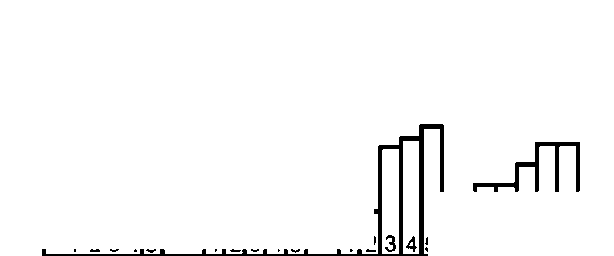
Fig. 10. Finely ground basalt stone after cavitation:
1 – fraction from 50 to 100 nm;
2 – fraction 100÷300 nm;
3 – fraction 300÷500 nm;
4 – fraction 500÷700 nm;
5 – fraction above 700 nm
5 12345
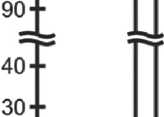
0 4 8 12
Time, hours
THE RESULTS OF THE SPECIALISTS’ AND SCIENTISTS’ RESEARCHES
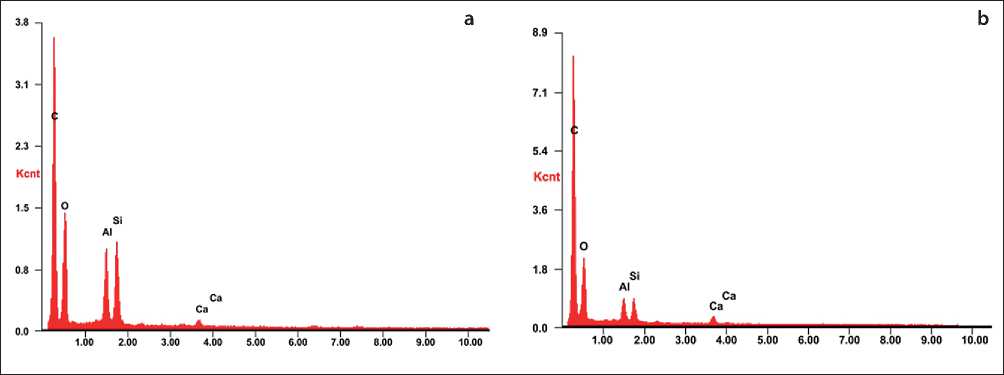
Fig. 11. Comparative EDS spectra of finely ground basalt: a – after mechanical grinding; b – after cavitation grinding
Table 5. Physico-mechanical characteristics of polymer composites with finely ground basalt after a cavitation mill
Content of finely ground basalt, in % |
δ stretching, МPа |
εrel., % |
ε perm. , % |
4.9 |
3.9 |
271 |
19.7 |
9.5 |
3.95 |
276.8 |
19.6 |
13. 4 |
4.6 |
282.5 |
19.3 |
16.9 |
4.7 |
287.6 |
20.8 |
20.6 |
4.9 |
289.7 |
20.9 |
23.5 |
4.97 |
295.6 |
21.4 |
26 |
5.4 |
303.5 |
22.4 |
28.7 |
5.3 |
315.4 |
22.5 |

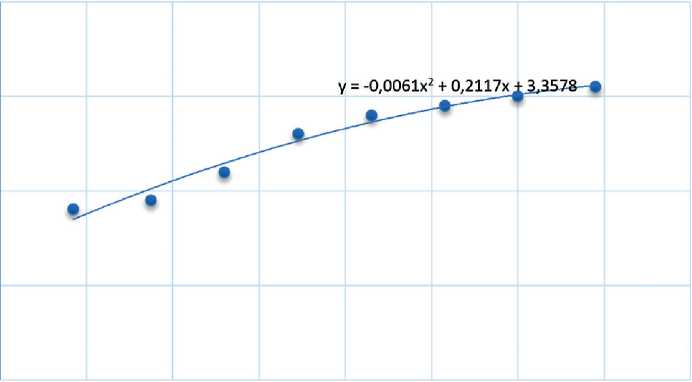
14 16
2 4 6 8 10 12
Filler content, %
. Row 1
The polynomial (Row 1)
Fig. 12. Tensile strength of the composite after cavitation mill
THE RESULTS OF THE SPECIALISTS’ AND SCIENTISTS’ RESEARCHES increased after cavitation treatment. Table 6 shows the physical and technical characteristics of the resulting polymer composite with mineral fillers.
As can be seen from the Table 6 physical and technical characteristics of the resulting polymer composites using inorganic fillers meet the requirements of the Government Standard.
CONCLUSION
According to the obtained research results, the following conclusions were made:
1. Finely ground fillers on an inorganic basis were studied: basalt and wollastonite stone, marble and coal dust. The research results showed that the use of inorganic fillers from minerals and rocks of the Kyrgyz Republic in the composition of polymer composites improves their physical and technical characteristics, and also allows for reducing the cost of the polymer composite material.
-
2. A hydro cavitation mill has been created for processing finely ground inorganic fillers intended for the production of organic polymer composites with inorganic additives. Using this mill, fillers with particle sizes of 50– 100 nm – 15%, 100–300 nm – 15%, 300–500 nm – 20%, 500–700 nm – 25% and more than 700 nm – 25% were obtained.
-
3. It has been established that the use of finely ground and processed filler powders after cavitation treatment makes it possible to increase the tensile strength to 5.1 MPa, and the heat resistance of polymer composites based on thermoplastic elastomers to 100–110 °C. In addition, it improves water resistance and resistance to aggressive media such as industrial oil, acetic acid and gasoline.
-
4. The physical and mechanical characteristics of composites with inorganic fillers have been studied. It was revealed that the developed polymer composites with inorganic fillers (basalt, wollastonite, marble, coal dust) have a set of physical and mechanical characteristics that meet the requirements of the standards.
Table 6. Physical and technical characteristics of polymer composites with inorganic fillers
No. |
Characteristics |
Polymer comosite with inorganic fillers |
||
Basalt |
Wollastonite |
Carbon |
||
1 |
Thickness, g/cm3 |
1.14 |
1.12 |
0.98 |
2 |
Shore hardness, arb. units |
63-65 |
59-62 |
60-63 |
3 |
Tensile strength, MPa |
4.9 |
5.50 |
4.1 |
4 |
Elongation at break, % |
290 |
342 |
246 |
5 |
Residual elongation, % |
19 |
18 |
22 |
6 |
Heat resistance, °С |
79 |
87 |
76 |
Список литературы Creation of polymer composites with mineral fillers
- Bazhenov S.L., Berlin A.A., Kulkov A.A., Oshmyan V.G. Polymer Composite Materials. Dolgoprudny. Intellect. 2010; 352.
- Kolosova A.S. Modern Polymer Composite Materials and Their Application. International Journal of Applied and Fundamental Research. 2018; 5(1): 245-256.
- Kolosova A.S., Sokolskaya M.K., Vitkalova I.A., Torlova A.S. Fillers for the Modification of Modern Polymer Composite Materials. Fundamental Research. 2017; 10(3): 459-465.4. Rogov V.A., Shkarupa M.I., Velis A.K. Classification of composite materials and their role in modern mechanical engineering. Bulletin of RUDN University, series Engineering Research. 2012; 2:41-49. (In Russ.)
- Li XuHui., Zhao Yi. Nanocomposite Building Materials in Modern Architectural Design. Journal of Nanomaterials. 2022;1169911,8. https://doi.org/10.1155/2022/1169911
- Rathod V.T., Kumar J.S., Jain A. Polymer and ceramic nanocomposites for aerospace applications. Appl Nanosci. 2017;7:519–548. https://doi.org/10.1007/s13204-017-0592-9
- Lukuttsova N., Pykin A., Kleymenicheva Y., Suglobov A., Efremochkin R. Nano-additives for composite building materials and their environmental safety. International Journal of Applied Engineering Research. 2016;11(11):7561–7565.
- Rashid A.B., Haque M., Islam S.M.M., Uddin Labib K.M.R. Nanotechnology-enhanced fiber-reinforced polymer composites: Recent advancements on processing techniques and applications. Heliyon. 2024;10(2):e24692. https://doi.org/10.1016/j.heliyon.2024.e24692
- Abdullaeva Z. Nanomaterials for Building and Protection. In: Nanomaterials in Daily Life. Publishing: Springer, Cham. 2017; 91-110. https://doi.org/10.1007/978-3-319-57216-1_5
- Rogov V.A., Shkarupa M.I., Velis A.K. Classification of Composite Materials and Their Role in Modern Mechanical Engineering. Bulletin of RUDN, Series: Engineering Research. 2012; 2: 41-49.
- Ershova O.V., Ivanovsky S.K., Chuprova L.V., Bakhaeva A.N. Modern Composite Materials Based on a Polymeric Matrix. International Journal of Applied and Fundamental Research. 2015; 4: 14-18.
- Melnichenko M.A., Ershova O.V., Chuprova L.V. Effect of Filler Composition on the Properties of Polymer Composite Materials. Young Scientist. 2015; 16(96): 199-202.
- Zavyalova N.B., Stroganov V.F., Stroganov I.V., Akhmetshin A.S. Study of the Influence of Filler Nature on the Strength Properties of Heterophase Polymer Compositions. Bulletin of KazGASU. 2007; 1(7): 63-66.
- Lipatov Yu.S. Physicochemistry of Filled Polymers. Kyiv: Naukovа Dumka Publishing, 1967.
- Mumtaz N., Li Y., Artiaga R., Farooq Z., Mumtaz A., Guo Q., Nisa F.U. Fillers and methods to improve the effective (out-plane) thermal conductivity of polymeric thermal interface materials – A review. Heliyon. 2024;10(3):e25381. https://doi.org/10.1016/j.heliyon.2024.e25381
- Lasrado D., Ahankari S., Kar K. Nanocellulose‐based polymer composites for energy applications – a review. J Appl Polym Sci. 2020;137:48959. https://doi.org/10.1002/app.48959
- Kwon Y.J., Park J.B., Jeon Y.P., Hong J.Y., Park H.S., Lee J.U. A Review of Polymer Composites Based on Carbon Fillers for Thermal Management Applications: Design, Preparation, and Properties. Polymers (Basel). 2021;13(8):1312. https://doi:org/10.3390/polym13081312
- Akunova M., Imankulova A.S., Chimchikova M.K. Study of Various Types of Fillers for Their Application in Polymer-Based Composite Materials. Proceedings of the Scientific and Technical Conference of Young Scientists, Postgraduates, and Students “Youth – The Driving Force of Science,” I. Razzakov KSTU, Part 2. Bishkek. 2017; 116-120.
- Abdykalykov A.A., Aydaraliev Zh.K., Kainazarov A.T., Abdiev M.S. Determination of the Fractional Composition of Basalt Production Waste for Obtaining a Composite Composition. Bulletin of KSUSTA. Bishkek. 2019; 1(63): 137-144.
- Aidaraliev Z., Rysbaeva I., Atyrova R., Abdykalykov A., Bekbolot kyzy B., Zholdoshova C., Sopubekov N., Kuduev A., Dubinin I., Abdullaeva Z. Suitability of Suluu-Terek Basalt Deposits for Stone Casting. Journal of Minerals and Materials Characterization and Engineering. 2022;10:1-14. https://doi:org/10.4236/jmmce.2022.101001
- Abdykalykov A., Aydaraliev Zh.K., Abdykalyk kyzy Zh., Kuduev A.Zh., Rashid kyzy B. Suitability of Basalt Raw Materials from the Kyrgyz Republic for the Production of Superfine and Continuous Fibers. Nanotechnology in Construction. 2023; 15(6): 574–582. https://doi.org/10.15828/2075-8545-2023-15-6-574-582
- Aydaraliev Zh.K., Rysbaeva I.A., Bekbolot kyzy B., Chimchikova M.K., Rashid kyzy B. Production of Polycrystalline Silicon by Chlorination from Rice Husk and Purification of Chlorine-Containing Gases by Adsorption Method. Nanotechnology in Construction. 2023; 15(6): 592–601. https://doi.org/10.15828/2075-8545-2023-15-6-592-601
- Makavetskas A.R., Bashlykova T.V., Pakhomova G.A., Filippov V.I., Lebedev N.M. Influence of Cavitation on the Technological Properties of Ore and Non-Ore Mineral Raw Materials. Nonferrous Metals. 2007; 3: 87–92.
- Ershov V.A., Kondratyev V.V., Afanasyev A.D. Sonochemical Dispersion of Quartz Using Cavitation Effects. Bulletin of Irkutsk State Technical University. 2011; 11(58): 159-164.
- Chimchikova M.K. Development of Composite Materials Based on Thermoplastic Elastomers and Mineral Fillers. PhD Dissertation in Technical Sciences. Kyrgyzstan, Osh State University. 2023; 148.
- Chimchikova M.K., Karpukhin A.A. Effect of Mineral Fillers on the Heat Resistance of Polymeric Composite Materials. Bulletin of Science and Practice. 2022; 8(8): 403-408. (in Russian). https://doi.org/10.33619/2414-2948/81/40