Development and applications of MEMS components
Автор: Levitskiy Alexey A., Marinushkin Pavel S.
Журнал: Журнал Сибирского федерального университета. Серия: Техника и технологии @technologies-sfu
Статья в выпуске: 3 т.8, 2015 года.
Бесплатный доступ
This article provides the results of the MEMS (MicroElectroMechanical Systems) components studies. The design considerations and manufacturing techniques of the silicon-based MEMS components are considered. Results of the experimental characterization of the fabricated prototypes are provided. Furthermore, discussion related to the future development of the MEMS components is also presented.
Microelectromechanical systems (mems), microelectromechanical resonators, scream technology, microgyroscopes, inertial navigation, pedestrian navigation, scream-технология
Короткий адрес: https://sciup.org/146114953
IDR: 146114953
Текст научной статьи Development and applications of MEMS components
Nowadays one of the most rapidly developing trends of microelectronics is a microelectromechanical systems (MEMS) technology which enables production of signal-processing electronics, microsensors and actuators in the single manufacturing cycle. MEMS devices used in variety of applications: sensors and actuators, RF components and micromirrors, inkjet-printer
Problems of MEMS modeling and development
Modeling of MEMS components may present significant difficulties. This is due to the fact that in order to create models of MEMS components it is necessary to take several physical domains into account during the simulation process: mechanics, electronics, fluid mechanics, optics, and electrostatics. In addition, the modeling of microdevices requires consideration of effects which are not usually taken into account when analyzing the devices at the macro level: air damping and gravity force in electrostatic devices, surface tension of the liquid in the microfluidic devices.
In recent years, the problem of computer simulation of MEMS attained much attention. Developers of CAE-systems include special modules for the analysis of MEMS in their packages, constantly expand range of simulated physical phenomena. In addition, software tools are created to simulate MEMS together with signal processing circuits at the system level. The advantage of these software from the developer’s perspective MEMS certainly is their specialization, focus on the problem area. However, on the other hand, a detailed study of the physical processes in MEMS components and, especially, the development of new variants are virtually impossible without the involvement of universal computational modeling packages. Such packages typically involve numerical methods including finite element method (FEM), finite volume method (FVM), and the boundary element method (BEM). The most popular is the FEM (ANSYS, COMSOL, Algor, Abaqus).
Typical problems that arise in the simulation of MEMS are following: eigenvalue problems, stressstrain analysis; transient analysis and so on. These problems can be solved by most universal finite element analysis packages. However, despite the advantages of numerical methods, the modeling of MEMS components still remains a difficult and challenging problem due to their multidomain nature. In this work results of the researches connected with creation of MEMS components are presented and ways of their further development are considered.
Experience in the development of microsystem devices
Microfluidic systems. Among the MEMS devices of the most interesting and challenging for the analysis are components of microfluidic systems. For the last few years there has been significant growth of research in the field of microfluidic components. Different microfluidic devices such as active valves, pumps, filters and mixers have been designed and fabricated. Various microfluidic components are combined in microfluidic systems. The main examples of microfluidic systems are lab-on-chip devices, DNA systems, drug delivery systems.
For the controlled transport of liquids in microfluidic systems on-chip micropumps are desired. When considering mechanical pumps, piezoelectric valveless micropumps (fixed valve pumps) seem to be more advantageous due to their higher reliability and higher flow rate. Fig. 1 shows the FEM model and the experimental model of such valveless micropump [1]. It consists of a liquid-filled chamber (depth of the working chamber is 25 microns) sealed with a movable membrane with attached piezoelectric disk and two diffuser/nozzle elements.
RF Microresonators. Advances in technology of semiconductor microstructures stimulate research and development aimed at the creation of components of electromechanical systems, which – 291 –
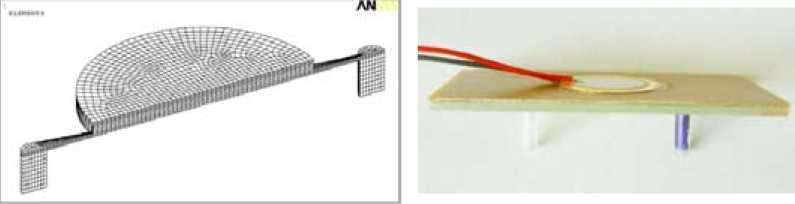
b
a
Fig. 1. Valveless micropump: a – finite element model; b – experimental model [1]
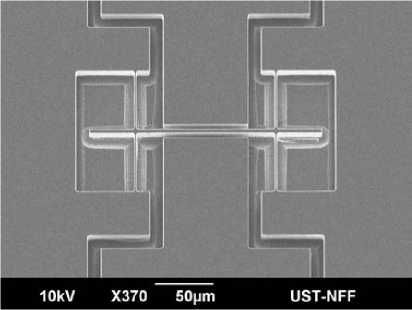
Fig. 2. SEM images of micromechanical resonator [2]

include micromechanical resonators. Fig. 2 shows the SEM images of such micromechanical resonator fabricated using SCREAM (Single Crystal Reactive Etch and Metallization) process [2]. This method is relatively simple as the bulk silicon serves as both the structural and sacrificial material.
The analysis of FEM simulation results and research of fabricated samples lead to the conclusion that on the basis of a considered micromechanical resonator design elements with resonant frequencies, at least from hundreds of kilohertz to tens of megahertz can be produced. High repeatability of sample sizes indicates the small effect of uncontrollable factors when using the SCREAM-technology. Processing methods similar to those used in this study allow forming of more complex RF 3D microstructures. The main applications are expected to be in filters and reference oscillators.
Miniature piezoelectric gyroscopes. In recent years areas related to the development of compact, reliable and cost-effective navigation and control systems for moving objects have been actively developing [3,4]. These are: spatial orientation control of wells; orientation, navigation and control systems for unmanned aerial vehicles, autonomous underwater vehicles and mobile robots; stabilization systems for railroad transport. These systems use angular rate sensors (gyroscopes) to measure angular displacements of objects.
Analysis of publications and research work on the subject has shown that despite of the fact that integrated silicon gyroscopes receive more and more wide application in the systems of – 292 –
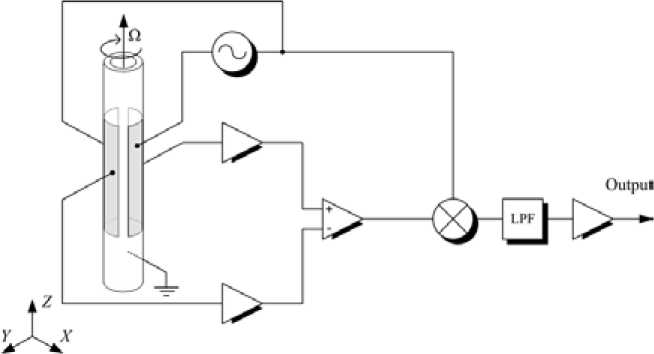
Fig. 3. Tubular piezoelectric angular rate sensor [3]
navigation, stabilization and orientation of various objects, the problems concerning research and design of piezoelectric angular rate sensors are still actual. On a number of parameters (cost, power consumption) piezoelectric vibrating gyroscopes overcome micromechanical gyroscopes that make them more suitable for mobile, autonomous instrumentation. Thus it is of great relevance to research and develop reliable and efficient modeling and design methods of the piezoelectric gyroscopes. As well as development of adequate models, providing a detailed study of the physical processes occurring in piezoelectric gyroscopes, and search for new design solutions.
Design of such vibratory angular rate sensor containing thin-walled cylinder (resonator) made of piezoelectric ceramics is presented on Fig. 3.
Resonator has two pairs of electrodes on external surface, and a common electrode on inner surface. The principle of action of the piezoelectric vibratory gyroscope is based on transformation of energy of the primary vibrations excitated by means of the first pair of electrodes in plane XZ to energy of secondary vibrations in YZ -plane under action of Coriolis forces exerted by rotation of a gyroscope around Z -axis. The second pair of electrodes serves for detecting of vibrations in YZ -plane. An oscillator is connected between the driving electrodes for self-oscillating driving of resonator. When the excitation signal is applied to driving electrodes, resonator makes bending vibrations in XZ -plane. The signal due to the Coriolis force is synchronously detected by the synchronous detection circuit, low-pass filtered and then amplified by DC amplifier.
One of the main problems of vibratory gyroscopes development is increasing of the gyroscope sensitivity to angular velocity. It is known, that the highest sensitivity of a vibratory gyroscope is achieved at coincidence of resonance frequencies of primary and secondary vibrations. That is why designs of piezoelectric vibratory gyroscopes based on axisymmetrical resonators look promising since rotational symmetry allows to achieve equality of frequencies of primary and secondary vibrations. Another important advantage of such gyroscopes is monolithic design of their resonators. Monolithic design of the resonator allows to minimize using of diverse materials and thus to increase stability of gyroscope characteristics in comparison with the gyroscopes based on conventional prismatic and bimorph resonators.
Perspectives of MEMS-based devices
Development of high sensitive accelerometers. High sensitivity accelerometers are of great importance for aerospace industry. Currently, there is need to solve a number of problems for the aerospace industry involving the measurement of low-frequency microaccelerations onboard of spacecraft. It is known that a significant impact on the results of scientific research and technological experiments done in microgravity have low-frequency accelerations due to the operation of onboard systems, the influence of the satellite aerodynamic forces, the inhomogeneity of the gravitational field within the spacecraft and spacecraft oscillations around the center of mass. Therefore, information on the level, spectral and spatial distribution of the residual quasi-static acceleration is one of the main characteristics of the spacecraft, and the problem of its determination is of great scientific interest.
The available traditional (macro) accelerometers are bulky, expensive, and high power consuming. The existing serially produced integrated MEMS accelerometers are also do not meet a number of requirements for measuring low frequency accelerations such as sensitivity, dynamic range, frequency bandwidth. Therefore, the most important is the problem of the development of comprehensive design methodologies of a new generation of highly sensitive accelerometers on the basis of new microsystem technologies. Solving these problems requires theoretical studies of the dynamics of microaccelerometers based on a strict account of the factors affecting their characteristics. The key to realizing high-sensitivity feature in MEMS-accelerometers relies on the increasing of the seismic mass and reduction of the gap sizes (Fig. 4).
The majorities of publications in the field of designing of integrated accelerometers are very heterogeneous and consider only specific implementations. Thus, a systematic approach to analysis and design of highly sensitive MEMS accelerometers to measure low-frequency accelerations are currently not yet formed. In this regard, the development of theory and methods of calculation and design of highly sensitive micromechanical accelerometers based on new technical solutions that provide increased sensitivity, decreased weight and size, power consumption and cost of instruments for the measurement of micro-accelerations, is an important task.
Pedestrian inertial navigation systems. Since the 80s years to present, there has been increasing interest in research and development of compact, reliable and cost-effective inertial systems for motion
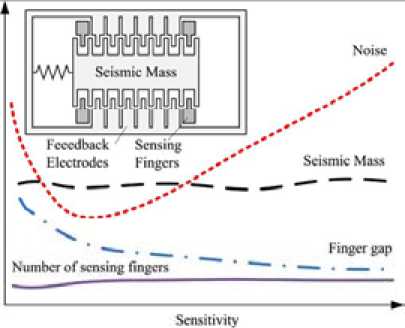
Fig. 4. Accelerometer sensitivity vs. noise trade-off analysis
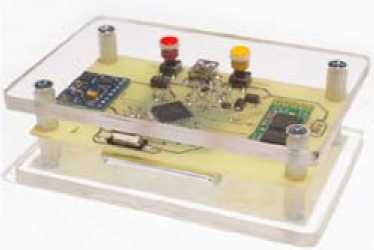
Fig. 5. Foot-mounted MEMS inertial measurement unit (IMU) [5]
parameters control. Besides such traditional applications as strapdown inertial system (SINS) of small robots and unmanned aerial vehicles, MEMS inertial sensors becoming very attractive for personal navigation applications [5, 6]. Potential users of personal navigation systems (PNS) are firefighters, emergency and security services. Civil users (pedestrians) also need such position estimation systems. Moreover of great interest is using of personal navigation equipment for military purposes. Personal navigation equipment enables to carry out continuous monitoring of personnel actions in absence of satellite communications, as well as performing “friend or foe” identification function. Solving these tasks requires the use of appropriate sensors meeting the requirements for size, weight and power consumption. Development of special navigation algorithms that will take into account features of human motion is also required.
MEMS inertial sensors used in personal navigation systems, meet the size, weight and power consumption requirements. In addition, inertial sensors are the only sources providing position and heading information when GPS signal is not available (buildings, urban canyons, dense forests). However, MEMS inertial sensors cannot provide high position accuracy since the position errors grow over time after integration and double integration operations. Due to this MEMS inertial sensors are usually combined with other sources of navigation information. That’s why current research efforts have focused on development and simulation of algorithms for the joint processing of heterogeneous information (inertial and magnetic measurements) to improve the quality of navigation information.
Conclusion
The future work on MEMS technologies promises to offer substantial performance improvements for MEMS devices as well as increasing of their functionality. Further progress in the field of MEMS will provide opportunities for miniaturized medical and biological systems, communication technology and wearable personal navigation systems. However, MEMS packaging and integration still will be a challenge and will require cost efficient and reliable solutions.
This work was financially supported by Russian Foundation for Basic Research (RFBR), grant № 14-38-50162, and by the Russian Federation Ministry of Education and Science in Siberian Federal University (contract № 02.G25.31.0041).
Список литературы Development and applications of MEMS components
- Kolovskiy Y.V., Levitskiy A.A., Marinushkin P.S.//Problems of perspective micro and nanoelectronic systems development: The Proceedings of the Third Conference, Moscow, 2008. P. 398-401.
- Levitskiy A., Marinushkin P.//Russian Physics Journal. 2013. № 8/3. P. 159-161.
- Marinushkin P.S.//Nanotechnologies and Electron Devices EDM’2010: Conference Proceedings. Novosibirsk, 2010. P. 168-171.
- Levitskiy A., Marinushkin P.//Achievements of Modern Radioelectronics. 2012. № 9. P. 34-38.
- Marinushkin P.S., Podshivalov I.A.//International Siberian Conference on Control and Communications SIBCON 2013: Proceedings. Krasnoyarsk, 2013. P. 19-21.
- Fischer C., Talkad S.P., Hazas M.//Pervasive Computing, IEEE, 2013. Vol. 12. № 2. P. 17-27.