Effective use of dry foaming agents in the manufacture of foam gypsum thermal insulation nanocompositions
Автор: Ruslan I. Shigapov, Dmitry A. Sinitsin, Rauf M. Khalikov, Elena A. Solovyeva, Igor V. Nedoseko
Журнал: Nanotechnologies in Construction: A Scientific Internet-Journal @nanobuild-en
Рубрика: Application of nanomaterials and nanotechnologies in construction
Статья в выпуске: 4 Vol.14, 2022 года.
Бесплатный доступ
Introduction. The elaboration of foamed eco-friendly gypsum nanocomposites with low specific gravity, high thermal insulation, operational and technical and economic characteristics remains an urgent task. Controlled hardening of gypsum foam nanoassemblers using dry foaming agents is a promising direction in the technology of production of heat-insulating building materials. Methods and materials. The production of a foam gypsum composition was carried out in an ejector-turbulent mixer by mixing a gypsum nanobinder with functional foaming nanoadditives. Building gypsum G5 BII was used as a binder in the work; porization of gypsum compositions was carried out using an adsorbed foaming agent PBNS. Results. The transformation of liquid-phase foaming agents into solid-phase ones by binding water allows the production of gypsum foam compositions from dry mixtures, which gives high dosing accuracy, a good degree of homogenization of components and stable characteristics of foamed gypsum nanocompositions. In production conditions, a one-storey small-sized pavilion was built using a pilot 3D printer AMT S1160, in which vertical enclosing structures are filled with foamed heat-insulating nanostructured foam gypsum. Monolithic foam gypsum nanomaterial with a density of 300–400 kg/m3 was used for insulation and sound insulation of attic floors during the overhaul of the historic building of the Veterans Hospital in Ufa. Discussion. The elaboration of technology for obtaining foam gypsum from dry mixtures is based on the advantage of manufacturing and using thermal insulation nanocompositions, which allows for significant punctuality of dosing and stable characteristics of foam gypsum building materials. Surfactants have a significant effect on the kinetics of the structure formation of the foam gypsum nanocomposition and slow down the coalescence of air bubbles. Conclusions. Nanoporous foam gypsum concrete, obtained as a result of controlled hardening, with a density of 400 kg/m3 has a thermal conductivity of 0.12 W/(m•ºС) and a compressive strength of 1.4 MPa. The compressive strength of foamed foam gypsum using a dry foaming agent on sorbents is 17% higher than the strength of a heat-insulating nanomaterial prepared using traditional technology.
Foam gypsum nanomaterials, foaming agents, structure formation of foam gypsum, hardening of nanocomposite
Короткий адрес: https://sciup.org/142234627
IDR: 142234627 | DOI: 10.15828/2075-8545-2022-14-4-274-281
Текст научной статьи Effective use of dry foaming agents in the manufacture of foam gypsum thermal insulation nanocompositions
Original article
As part of the implementation of the national project of the Russian Federation “Housing and urban environment”, modern building materials of nanoporous structure are widely used for the construction of individual residential low-rise buildings [1–5]. The elaboration of foamed nanocomposite eco-friendly gypsum binders with sufficiently significant strength, low specific gravity, high thermal insulation and frost-resistant properties, ensuring the production of 3D structures with demanded operational and technical and economic characteristics, remains an urgent task.
The purpose of this article is to study the production of foam gypsum nanomaterials using effective foaming agents based on the raw materials of Bashkortostan for the construction of low–rise buildings.
METHODS AND MATERIALS
The preparation of a foamed gypsum nanocomposition was carried out by mixing a gypsum binder with the introduced functional nanoadditives, including a dry
APPLICATION OF NANOMATERIALS AND NANOTECHNOLOGIES IN CONSTRUCTION
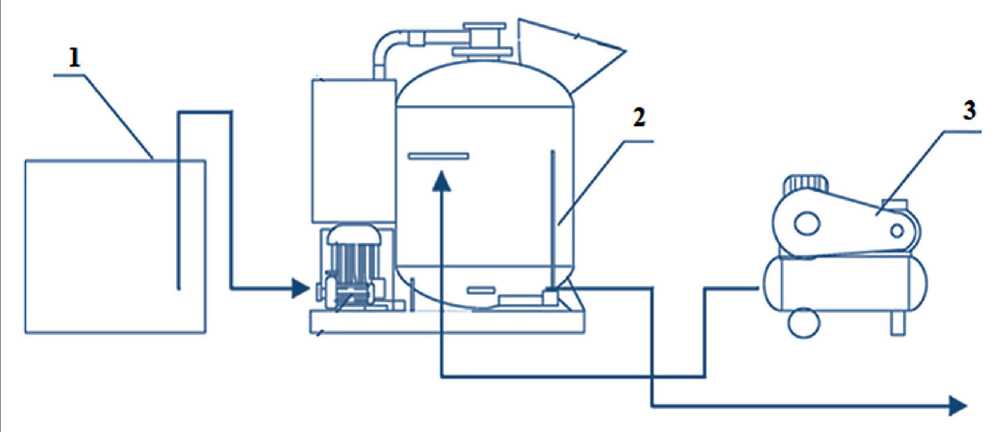
Fig. 1. Technological scheme of production of foam gypsum nanocomposition: 1 – storage reservoir;
2 – ejector-turbulent mixer; 3 – ejector compressor
foaming agent and water at the installation – ejector-turbulent mixer ETS-0.5 (Weft company) (Fig. 1).
The method of production of heat-insulating foam gypsum is based on one-stage mixing for 6-8 minutes of a dosed amount of gypsum composite nano-binder and water from a storage reservoir. The mixer ETS-0.5 is equipped with a flow-through electronic sensor for monitoring the water level of the closure and a time relay for monitoring the phase of active porization of the nanogypsum composition. Metered volumes of air, which are supplied by the compressor through an ejector built into the mixer, provides bubbling and intensive foaming, cavitation of gypsum nanocomposition. The capacity of the ETS mixer is 0.5 to 5 m3/hour, with the supply of nanocomposite foam gypsum through hoses at a pressure of 0.2–2.5 MPa up to 30 meters horizontally and up to 15 meters vertically.
To measure the thermal conductivity coefficient of foam gypsum samples with dimensions of 250 • 250 • 50 mm, the ITP-MG4 “100” device was used: the test range is 0.03–1 W / (m • оC), the limit of the relative error in determining the thermal conductivity coefficient is ± 7. The determination of the thermal conductivity of a foam gypsum sample provides for the creation of a constant heat flow through the sample at a fixed temperature difference on its surfaces [6].
Building gypsum G-5BII (Ufa Gypsum Company) was used as a nano-binder in the work. To regulate the kinetics of hardening (slowing down the setting time) of the gypsum foam mixture, nano–additives – setting retarders were used: Plast Retard PE (firm “Retardan”, Italy) 0.05% by weight of the gypsum binder. Various hardening retarders provide a controlled decrease in the dissolution rate of gypsum semihydrate, therefore, reduce the concentration of calcium sulfate dihydrate crystallohydrates precipitating into an undesirable precipitate [7, 8].
Foaming porization of gypsum compositions was carried out using a dry (adsorbed with expanded clay sand) PBNS foaming agent with stabilizing nanoadditives (“Plant Technochemsynhtes”, Ufa), which provides the necessary air extraction (foam multiplicity of at least 5) and the viability of three-phase foam. The PBNS foaming agent has the following chemical structure: a hydrocarbon chain C10–19 (hydrophobic fragment) and a hydrophilic functional group.
Concentrated aqueous solutions of the PBNS foaming agent were converted into a dry solid-phase state by the method of joint mixing with expanded clay sand. The stability of the dry foaming agent on the adsorbent is explained by the fact that the microparticles of the expanded clay sorbent are positively charged, and the hydrophilic part of the foaming agent molecule is negatively charged. The adsorbed foaming agent with the sorbent was dried at a temperature of 20–150оC to a humidity of 5%; then the dried PBNS foaming agent was crushed and added (the optimal concentration of 0.25%) to a dry building gypsum mixture. The elaboration of technology for obtaining foam gypsum from dry mixes is based on the advantage of manufacturing and using dry mixes: high dosing accuracy, a good degree of homogenization of components and stable characteristics of foam gypsum nanomaterials [9, 10].
During adsorption on the surface of air bubbles (Fig. 2), the hydrophobic hydrocarbon part of the foaming agent molecules are arranged in a monomolecular layer in the gas phase, forming a 2.5–3 nm diffinyl layer.
APPLICATION OF NANOMATERIALS AND NANOTECHNOLOGIES IN CONSTRUCTION
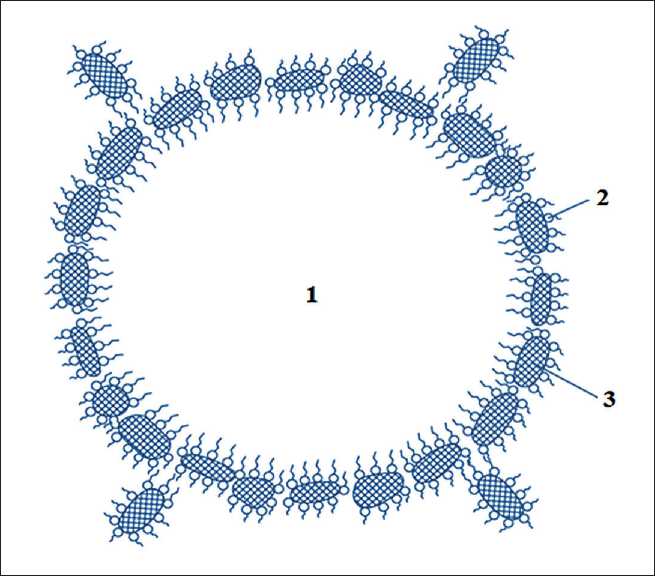
Fig. 2. Scheme of adsorption of foaming agent molecules on the surface of foam gypsum air bubbles: 1 – gas phase;
2 – monomolecular layer of foaming agent; 3 – gypsum crystallohydrates
Local micro-heterogeneities and germinal calcium sulfate dihydrate nanoclusters crystallohydrates with sizes of ≈ 20–70 nm [11] lead to variations in the thickness of the molecular layer of the foaming agent in the nanogypsum foam composition. Further strengthening of the primary nanostructure occurs due to an increase in the number of nanocontacts between unrelated growing gypsum microcrystals.
The consumption of dry foaming agent in the manufacture of foam gypsum thermal insulation nanocompositions is 1.7–2.8 kg per 1 m3 of foamed mixtures, which is proportional to the consumption of liquid-phase foaming agent. Foam multiplicity is not less than 7.0; foam stability is not less than 360 seconds. The optimal formation of a foamed gypsum structure also depends on the ratio of water and gypsum nano-binder; in addition, the hydrochemical quality of the water component should be noted. Increased water hardness leads to overspending of the foaming agent, therefore reliable quality management of the functioning of the technological water supply line is necessary.
The density and compressive strength of foam gypsum samples were determined according to GOST 17177-94 “Materials and products for building thermal insulation. Test methods”, GOST EN 1602-2011 “Thermal insulation products used in construction. Method for determining apparent density”, GOST 125-2018 “Gypsum binders. Technical conditions”. A stereoscopic method for studying the shapes and sizes of micropores of foam gypsum samples was performed using a Nicon SMZ 1500 optical microscope.
RESULTS
Optimal porization of gypsum nanocompositional materials is associated with significant difficulties due to the short setting time of the nano-binder; the introduction of a modified PBNS foaming agent optimizes the kinetics of hardening. In the process of foaming, the hydrophilic-oriented molecules of the foaming agent create an adsorption layer on the hydrated layers of gypsum nanoassemblers, sharply slow down the fusion (coalescence) of air bubbles, preserve the nanosuspension for a sufficiently long time in a colloidal state. The use of surface-active molecules of the PBNS foaming agent ensures the involvement of the necessary volume of micro-bubbles of air in the production of foam gypsum nanosuspension .
The addition of a gypsum binder foam agent PBNS concentration of 0.1–0.2% leads to a decrease in the water gypsum ratio. The study of the technological parameters of foaming made it possible to determine the conditions of the kinetic stability of the foam: a decrease in the angular velocity of mixing the foam causes thinning of the interstitial partitions of the foam gypsum with the formation of through porosity. The set of structural strength with foam gypsum concrete takes from two to three hours. The com-
APPLICATION OF NANOMATERIALS AND NANOTECHNOLOGIES IN CONSTRUCTION pressive strength of foamed foam gypsum with a density of 400 kg/m3, prepared using a dry foaming agent PBNS (on sorbent), is 17% greater than the strength of the thermal insulation material made using classical technology with the same foaming agent in the form of an aqueous solution. It is established that the optimal production of closed porosity of nanostructured foam gypsum (Fig. 3) is provided under the condition that the foam dispersion rate and the mixing rate do not change.
It should be noted that the use of only prefabricated blocks and slabs based on light, cellular concrete or foam ceramics with the best thermal efficiency indicators for objective reasons cannot satisfy all the needs of the construction industry in structural and thermal insulation building materials. In particular, in the conditions of major repairs and restoration of architectural heritage objects, only monolithic methods of construction work are possible. The choice of structural and thermal insulation materials for monolithic technologies presented on the construction market is in reality small and is practically limited only to the use of expanded clay backfills and expanded clay concrete of various densities in screeds under floors and for the deconstruction of flat low-slope roofs.
Nanostructured foam gypsum is the most popular and promising building material for the monolithic method of production of construction and installation works and the use of structural and thermal insulation composites. Comprehensive studies of thermal insulation and sound insulation characteristics of nanostructured foam gypsum obtained using monolithic technology (Table 1) have confirmed its sufficiently high technological characteristics.
Monolithic foam gypsum nanomaterial was used to insulate attic floors during the overhaul of the Veterans Hospital building in Ufa to replace the slag filling that had become unusable, as well as a sound-proofing and fire-retardant building material of the interstory floor. The practical effectiveness of using nanostructured monolithic foam gypsum in attic and interstory floors is as follows: – nanocomposite foam gypsum (density 300– 400 kg/m3) is much lighter than slag backfill (density
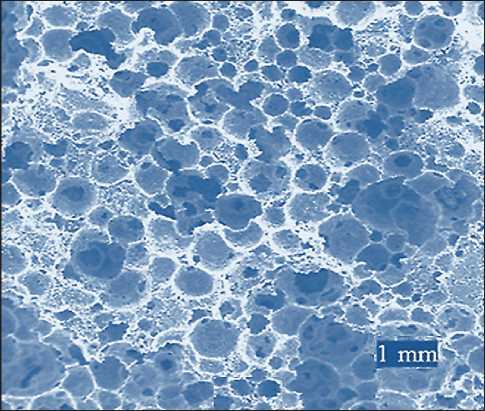
Fig. 3. Microstructure of nanostructured foam gypsum with a density of 400 kg/m3
900–1100 kg/m3), and its use in floors has significantly lightened the weight of the floor and reduced the load on the main load-bearing structures of the historic building (walls and foundations), which for almost 1.5 centuries of operation have received significant physical wear;
– monolithic nanofoam gypsum provides both sufficient sound insulation of interstory floors and fire protection of existing steel beams without additional treatment with very expensive flame retardant swelling paint compositions;
– it is especially important in the production of repair and restoration works to fill with monolithic nanocomposite foam gypsum, which allows you to meet almost any requirements for geometric characteristics; in particular, during the overhaul of the building of the Hospital of War Veterans after the dismantling of old building structures: boardwalk, wooden beams and slag filling, it turned out that the steel main beams of
Table 1
Physico-mechanical and thermal characteristics of nanocomposite foam gypsum
No. |
The name of the indicator |
Average values of the indicator |
|
1 |
Density, kg/m3 |
300 |
400 |
2 |
Thermal conductivity in the dry state at t = 25оC, W/(m • оC) |
0.10 |
0.12 |
3 |
Calculated characteristics of thermal conductivity, W/(m • оC): – under operating conditions of construction “A”, – under operating conditions of construction “B” |
0.14 0.23 |
0.17 0.26 |
4 |
Vapor permeability, mg/(m • h • Pa) |
0.28 |
0.25 |
5 |
Compressive strength, MPa |
1.1 |
1.4 |
APPLICATION OF NANOMATERIALS AND NANOTECHNOLOGIES IN CONSTRUCTION the floor-to-floor overlap have different heights and accordingly, the thickness of the foam gypsum layer varied from 25 to 40 cm;
– at the restored facility, internal repair work due to production necessity was carried out in the autumnwinter period with the heating system not working; at the same time, the fast setting time (20–30 minutes, even taking into account the introduction of a moderator) made it possible to pour nanogypsum at negative temperatures (there was a need to heat the sealing water).
The use of monolithic nanocomposite foam gypsum has made it possible to reduce the cost of major repairs of the historical object (compared with semi-rigid mineral wool slabs, the cost of foam gypsum is several times lower) and accelerate construction work. The technology of preparation of foam gypsum concrete directly at the construction site and the possibility of supplying foam gypsum nanocomposition using flexible hoses under pressure of 0.2–2.5 MPa can significantly reduce the cost of lifting mechanisms.
3D printing technology has made it possible to construct a two-storey residential building in which the interior space of the exterior walls is filled with monolithic foam gypsum. In production conditions, the employees of the Ufa Gypsum Company and USPTU using the 3D printer AMT S1160 (“SPETSAVIA” Yaroslavl) printed fragments of vertical enclosing structures of a one-story
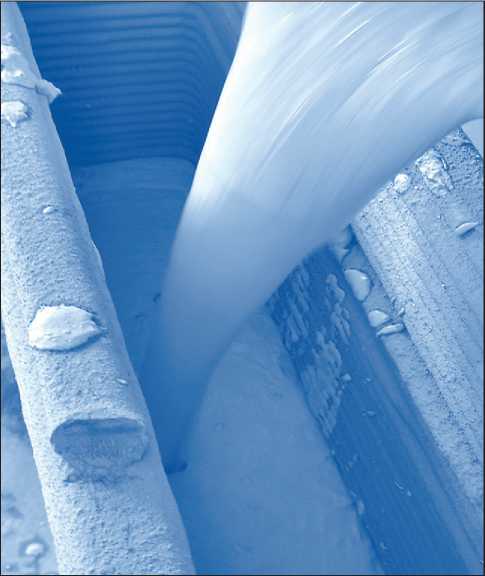
Fig. 4. Filling with foam gypsum nanocomposition of vertical enclosing 3D constructions small-sized pavilion; then filled with foamed thermal insulation nanocomposite foam gypsum (Fig. 4).
Technological filling of nanocomposite thermal insulation foam gypsum should be carried out preferably in the warm season for natural drying to a humidity of 12% and strengthening of building constructions. In case of industrial necessity, accelerated drying with heat guns (infrared emitters) can be used until the foam gypsum nanocomposite is completely dry.
DISCUSSION
The molecules of the PBNS foaming agent participate in the formation of the microcellular structure of the foam gypsum and determine the most important characteristics of the thermal insulation nanocomposite: density, thermal conductivity, strength and durability. The supramolecular mechanism of action of the foaming agent consists in the formation of stable air bubbles (gas phase) in a gypsum suspension with a diameter of several tens of micrometers to several millimeters. On the physico-chemical characteristics of three-phase foam in nanocompositional foam gypsum: multiplicity, stability, etc. many variable factors influence – variations in the values of surface tension, pH of the medium, temperature [12]; the intensity of mixing and bubbling on the installation of an ejector-turbulent mixer.
It should be noted that the formation of the nanostructure of gypsum foam compositions in the process of synergetic self-assembly [13] of gypsum crystallohydrates proceeds quite quickly in parallel with the hydration of CaSO4 • 0,5H2O semihydrate. The colloidal solution CaSO4 • 2H2O crystallizes fairly quickly, and the growing microcrystals of gypsum form a coagulation nanoset; gypsum crystallohydrates are fractal and have sizes from 47 nm to 138 nm.
Difficulties in pore formation gypsum nanosystems represent a technological problem of designing cellular building materials with an average density of 300– 400 kg/m3, characterized by optimal microstructure and providing functional purpose: sound absorption, thermal resistance and other indicators. It is necessary to strive for the creation of a finely porous structure with a uniform distribution of micropores [14] in the volume of foam gypsum thermal insulation material; and in the case when the formation of a porous microstructure in foam gypsum is achieved by traditional methods of introducing gas-forming agents into the molding mixture (aluminum powder, hydrogen peroxide, etc.), due to the rapid kinetics of the reaction with water of the gypsum binder, the mixture turns into a monolith in a short time, not allowing the gas-forming agents to fully pore formation the molding composition. In some cases, to increase the porosity of gypsum, a method is used consisting in the direct addition of pre-made foam to gypsum suspensions.
APPLICATION OF NANOMATERIALS AND NANOTECHNOLOGIES IN CONSTRUCTION
For the technological production of stable foam in the liquid-phase component, in addition to water, a special surface-active component (foaming agent) must be present able to be adsorbed on the interfacial surface. The effectiveness of foaming agents is determined by the ability of the foam to retain fine mineral particles of gypsum nanowires on its surface for a long time. The transformation of liquid-phase foaming agents into a dry state is based on the binding of water molecules: by the physicochemical (sorption) method – by mixing the foaming agent with a powdered or granular porous sorbent; by the hydration method – by mixing the foaming agent with semi-hydrated gypsum of the G-2 brand, quicklime and Portland cement PC 500.
The study of the mechanism of regulation of microstructural characteristics of nanocomposite foam gypsum obtained by the method of dry mineralization of foam has established that the kinetic stability of foam is a reliable way of regulating porosity. The main technological indicators of foam gypsum: average density, pore size, strength are determined by the characteristics of the nano-binder and foaming agent. Analysis of the microstructure of structural and thermal insulation foam gypsum samples showed that in foam gypsum with a density of 300 kg/m3, the average diameter of micropores is 0.47 mm, the pore size distribution is dimodal, the pores have a spherical shape. With an increase in the average density to 400 kg/m3, the size of micropores of foam gypsum decreases and is about 0.38 mm.
To obtain a highly porous foam gypsum with a total porosity of 65–70% and a uniform bimodal pore size distribution, the authors [15] used 1.7 wt. % of nonionic surfactant. Based on the changes in viscosity and temperature in the solidifying foam gypsum, it was found that the nonionic surfactant slows down the crystallization of the gypsum nanocomposition. The increase in viscosity during the crystallization of gypsum stabilizes the micropores formed during foaming. Gypsum foams with a submicron pore size of the matrix and a relatively uniform micropore size of ≈ 92–100 microns were obtained due to a shorter coalescence time of air bubbles.
The use of the PBNS foaming agent reduces the water-gypsum ratio, therefore increases the strength and improves other technological characteristics of the foam gypsum product; ensures the formation of air bubbles uniform in diameter; reduces the viscosity of the foam gypsum composition; slightly slows down hardening, which reduces the time to stripping by 20–25%. The reduced water resistance of foam gypsum products, which manifests itself in a decrease in strength in humid environmental conditions, can be compensated by modifying the gypsum nano-binder by introducing mechano-activated cement and siliceous fillers.
Surfactants have a significant effect on the kinetics of the structure formation of the foam gypsum nanocom- position; the first stage of foaming was the appearance of adsorption layers on the interfacial surface-films of molecules of foaming agents. It should be noted that the regulation of the hardening of gypsum foam binders is considered promising in the design of the initial components of 3D technologies [16–18]; and the determining factor of the aggregate stability of the suspension is the electrostatic barrier of interaction of microparticles. An effective approach to enhance the performance characteristics of building nanocomposites for 3D additive technologies based on gypsum binders is the implementation of controlled hardening with mineral nanoadditives.
The pumpability of foamed gypsum nanocompositions in 3D printing can be enhanced by the addition of 0.8% highly effective superplasticizers based on comb-like polycarboxylate esters, which can significantly increase the consistency retention time [19]. The advantage of 3D printing technology in the construction of buildings using dry foaming agents is: robotization of the construction process, reduction of labor costs for the production of works.
The most popular in the innovative construction industry are cellular wall blocks with a density mark in the range of 300–800 kg/m3: 300...500 kg/m3 – thermal insulation foam gypsum, 500...800 kg/m3 are used as structural and thermal insulation building materials. The elaboration of chemical additives that improve water-repellent characteristics allows the use of porous wall blocks on gypsum binders for the construction of load-bearing internal walls. The volume of cellular porosity of nanostructured foam gypsum is determined by the pore size distribution, the maximum and average size of micropores, their shape, and the thickness of the interpore partitions. The characteristic of micropores in size, which vary from tens of nanometers to millimeter, is a significant factor that determines the compressive strength, thermal conductivity and water permeability of the gypsum foam material.
Positive characteristics of foam gypsum composite nanomaterials (low cost, environmental cleanliness, rapid strength gain, good heat and sound insulation properties, absence of shrinkage deformations, good thermal insulation and sound-absorbing ability, fire resistance, etc.) [20–23] increase the operational qualities of residential buildings. It should also be noted that the use of monolithic gypsum composite nanofoam makes it possible to increase by three times the distance between the racks of thin-walled steel structures of the frame. Reducing the consumption of construction steel is especially in demand in the current aggravated interstate relations and the most difficult conditions for the functioning of the Russian building industry.
CONCLUSION
Technological advantages of using dry mixes: high dosing accuracy, a good degree of homogenization of the
APPLICATION OF NANOMATERIALS AND NANOTECHNOLOGIES IN CONSTRUCTION components and stable characteristics of gypsum foam nanomaterials necessitated the elaboration of dry foaming agents. Metered volumes of air, which are supplied through an ejector built into the mixer, provide intensive foaming of the gypsum nanocomposition, in addition, additional cavitation. The compressive strength of foamed foam gypsum with a density of 400 kg/m3, prepared using dry foaming agent PNBS with a concentration of 0.1–0.2%, is 17% greater than the strength of the thermal insulation building material manufactured according to classical technology by foaming agents in the form of an aqueous solution.
Список литературы Effective use of dry foaming agents in the manufacture of foam gypsum thermal insulation nanocompositions
- Ferronskaya AV, Korovyakov VF, Baranov IM, Buryanov AF, Losev YuG, Poplavsky VV, Shishkin AV. Gypsum in low-rise building. Moscow: Publishing House of the ABU; 2008.
- Petropavlovskaya VB, Belov VV, Novichenkova TB. Low-energy gypsum building composites. Tver: TSTU; 2014.
- Chernysheva NV, Lesovik VS, Glagolev ES, Volodchenko AA. Effective composites employing fast-hardening gypsum cement binders for additive manufacturing. Advances in Engineering Research. 2017; 133: 135–141. Available from: https://dx.doi.org/10.2991/aime-17.2017.23.
- Kuzmina VP. Mechanisms of nanoadditives influence on gypsum products. Nanotechnologies in construction. 2012; 4(3): 98–106.
- Bessonov IV, Shigapov RI, Babkov VV. Thermal insulation foam gypsum in low-rise construction. Building materials. 2014; 7: 9–13.
- Sinitsin DA, Shayakhmetov USh, Rakhimova ON, Khalikov RM, Nedoseko IV. Nanostructured foam ceramics for building purposes: production technology and applications. Nanotechnologies in Construction. 2021; 13(4): 213–221. Available from: https://doi.org/10.15828/2075-8545-2021-13-4-213-221.
- Kosenko NF, Blinova OV, Veselkova EA. Foam gypsum composition. Patent No. 2280627 C1 Russian Federation. Publ. 27.07.2006. Bulletin 21.
- Gabitova AR, Akhmadullina II, Pechenkina TV, Pudovkin AN, Nedoseko IV. Nanostructural aspects of hydration and hardening of gypsum and gypsum slag compositions based on two-water gypsum. Building materials. 2014:(1-2): 46–51.
- Capasso I, Pappalardo L, Romano RA, Iucolano F. Foamed gypsum for multipurpose applications in building. Construction and Building Materials. 2021; 307: 124948. Available from: https://doi.org/10.1016/j.conbuildmat.2021.124948.
- Kulikov VG. Physicochemical aspects of the disperse SAM systems foaming process. Nanotechnologies in construction. 2010; 2(1): 72–90.
- Khalikov RM, Sinitsyna EA, Silantieva EI, Pudovkin AN, Nedoseko IV. Modifying intensification of the hardening of extruded construction gypsum nanocomposites. Nanotechnologies in construction. 2019; 11(5): 549–560. Available from: https://doi.org/10.15828/2075-8545-2019-11-5-549-560.
- Kruglyakov PM, Exerova DR. Foam and foam films. Moscow: Chemistry; 1990.
- Khalikov RM, Mashukov N.I. Features of stabilization of natural and synthetic molecular structures. Nalchik: Publishing House of the RPK; 2010.
- Morozova NN, Maisuradze NV, Galiev TF, Potapova LI. Efficiency of air-entrapping additives in gypsum materials. Bulletin of the Technological University. 2016; 19(2): 31–33.
- Roch IE, Messing GL. Direct foaming and seeding of highly porous, lightweight gypsum. Journal of Materials Research. 2016; 31: 2244–2251. Available from: https://doi.org/10.1557/jmr.2016.246.
- Ivanova OV, Khalikov RM, Salov AS, Nizamutdinov MKh, Zinnatullin VV. Technological equipment management for 3D additive printing of building nanocomposites. Nanotechnologies in Construction. 2021; 13(2): 117–123. Available from: https://doi.org/10.15828/2075-8545-2021-13-2-117-123.
- Frolova MA. Aspects of determining the aggregative stability of water suspensions of mineral powders for building composites. Nanotechnologies in Construction. 2022; 14(1): 5–10. Available from: https://doi.org/10.15828/2075-8545-2022-14-1-5-10.
- Chernysheva N, Shatalova S. Compounding features of composite gypsum binders for porous composites in construction printing technologies. IOP Conference Series: Materials Science and Engineering. 2020; 945: 012007. Available from: https://doi.org/10.1088/1757-899X/945/1/012007.
- Khalikov RM, Ivanova OV, Korotkova LN, Sinitsin DA. Supramolecular impactmechanism of polycarboxylate superplasticizers on controlled hardening building nanocomposites. Nanotechnologies in Construction. 2020; 12(5): 250–255. Available from: https://doi.org/10.15828/2075-8545-2020-12-5-250-255.
- Shakhova LD. The role of foaming agents in foam concrete technology. Building materials. 2007. No. 4. P. 16–19.
- Bessonov IV, Nikolaev MA, Alekseev AL. Method of obtaining foam gypsum mass by vacuuming in a cavitation activator-disintegrator. Patent No. 2421424 C1 Russian Federation. Publ. 20.06.2011. Bulletin 17.
- Bagdasarov AS, Nesterenko AI, Pupkova AYu. Foam gypsum products based on local binders. Herald of Dagestan State Technical University. 2018; 45(4): 153–161. Available from: https://doi.org/10.21822/2073-6185-2018-45-4-153-161.
- Matyeva AK, Asanalieva ZhD, Azizova AE. Modified dry concrete mix (foam gypsum concrete). Science and innovative technologies. 2019; 2(11): 58–63. Available from: https://doi.org/10.33942/sit11.13.