High velocity compaction of carbon compositions
Автор: Samodurova M.N., Barkov L.A., Latfulina Yu.S.
Журнал: Вестник Южно-Уральского государственного университета. Серия: Металлургия @vestnik-susu-metallurgy
Рубрика: Порошковая металлургия, композиционные материалы и покрытия
Статья в выпуске: 3 т.17, 2017 года.
Бесплатный доступ
High velocity compaction of metal, ceramic and other powders have no widespread industrial application at the present time. Carrying out a large number of experiments with processes of high velocity compaction with powders of non-ferrous, ferrous metals, ceramics and polymers - showed that formation with speeds of the ram tester more than 1-2 m/s, causes the following adverse effects: pressing of gases and vapors of the liquids containing in initial powders and destruction of the specimens. In Chelyabinsk there are several large-scale enterprises (“Electrode Plant”, “Electrometallurgical Integraыted Plant”, Plant “Grafitoplast”, branch of “Doncarb Graphite”, “Uglegraphite”, “Carbon Material Plant” and others), which produce a brand range of products from carbon compositions. Scientists from Resource Centre of Special Metallurgy of South Ural State University (RCSM of SUSU) carried out the theoretic, technologic and experimental investigations for these enterprises. This article is devoted to the analysis of the experimental studies on devices of the Swedish company HY-DROPULSOR and the American company Instron. Foreign researchers established values of devices striker pin kinetic energy at which density of specimens comes nearly to theoretical, but, unfortunately, without indication of powder compositions, kind of specimens pressing and also strikers and specimens masses, their density at various values of speed and mass of strikers. Therefore the aim of the article is studying processes of High Velocity Compaction providing different indications of powder compositions containing graphite and optimized strikers and specimens masses, strikers speed.
High velocity compaction, carbon compositions, granulo-morphological research, hydropulsor press, прессы hydropulsor
Короткий адрес: https://sciup.org/147157096
IDR: 147157096 | DOI: 10.14529/met170314
Текст научной статьи High velocity compaction of carbon compositions
Granulo-morphological research
For granulometric and morphological analysis of the powder composites together with the standard procedure [1–8], were used the methods providing usage of a granulo-morphometer ALPAGA 500 NANO and Electron Microscope Tescan VEGA-II. The granulo-morphometer ALPAGA 500 NANO has an exclusive software Callisto product of the company OCCHIO (Belgium) allows to measure the diameter of the mesh aperture, roundness, elongation and other parameters of the particles with the dimensions from 0.5 to 2500 μm. The specimen preparation is done by placing the particles on the slide through the aperture in the vacuum chamber by making a slight (within 0.1 bar) change of pressure. The diameter of the mesh aperture is a minimum diameter of its hole through which a particle can pass. Roundness is a parameter characterizing departure of the particle form from a perfectly round one. Elongation of the powder particles is a normalized ratio of ellipsoid semi-axis of Lagrange inertia.
Compositions of powder mixtures studied are given in Table 1.
Graphite was obtained from electrode scrap of Chelyabinsk Electrode Plant by ball milling, the particle size is from 1 μm to 5 mm.
The binder is powdered phenolformaldehyde novolac type resin that has 6–9 % of urotropine mass fraction according to Specification Requirements.
Copper electrolytic powder used in composition No. 3, has a bulk density of 1.25–2.00 g/cm3. In compositions No. 4 and 5 a petroleum coke with the ash content is not more than 0.5 %, was used as an additive.
Powder of zinc stearate, zinc mass fraction does not exceed 4 %, was used in Composition No. 5 as a lubricant between graphite and binding particles.
Table 1
Compositions of powder mixtures
Mixture Number |
Graphite, % |
Binding, % |
Copper, % |
Coke, % |
Zinc stearete, % |
1 |
100 |
– |
– |
– |
– |
2 |
86 |
14 |
– |
– |
– |
3 |
76 |
14 |
10 |
– |
– |
4 |
71 |
14 |
– |
15 |
– |
5 |
71 |
14 |
– |
10 |
5 |
Results of granulo-morphological research
Results of the granulometric and morphological analyses are given in Tables 2, 3 and 4. Cumulative particle size distribution in powder composites to the mesh aperture diameter is given in Table 2. Thus, for example, for composi- tion No. l the minimum mesh aperture diameter is 0.96 μm, and maximum one is 95 μm. The part of the particles with mesh aperture diameter up to 13 μm is 5 %, with mesh aperture diameter up to 18 μm – 10 %, up to 21 μm – 16 %, up to 26 μm – 25 %, up to 40 μm – 50 % etc, up to 94 μm – 95 %.
Mesh aperture diameter, μm
Table 2
о 00 СО |
S 1 § |
1П сц |
о |
40 |
in сц |
о in сц |
in сц |
сц |
о 04 сц |
in 04 сц |
1 X |
|
1 |
47 |
0,96 |
13 |
18 |
21 |
26 |
40 |
65 |
77 |
85 |
94 |
95 |
2 |
32 |
0,96 |
8 |
10 |
12 |
15 |
22 |
40 |
57 |
72 |
86 |
99,8 |
3 |
34 |
0,96 |
9 |
11 |
14 |
17 |
26 |
46 |
56 |
72 |
81 |
87 |
4 |
33 |
0,48 |
9 |
12 |
15 |
20 |
31 |
44 |
48 |
54 |
64 |
78 |
5 |
33 |
0,48 |
9 |
12 |
15 |
18 |
28 |
45 |
53 |
59 |
75 |
76 |
Тablе 3
Roundness, %
СО |
1 § |
in сц |
о |
40 |
in сц |
о in сц |
in сц |
сц |
о 04 сц |
in 04 сц |
1 X |
|
1 |
49 |
15 |
28 |
31 |
35 |
38 |
45 |
59 |
66 |
70 |
77 |
100 |
2 |
53 |
10 |
25 |
32 |
33 |
40 |
52 |
65 |
71 |
75 |
80 |
100 |
3 |
50 |
15 |
24 |
32 |
35 |
39 |
49 |
60 |
65 |
71 |
77 |
100 |
4 |
35 |
10 |
13 |
13 |
16 |
19 |
30 |
45 |
52 |
60 |
69 |
100 |
5 |
31 |
13 |
13 |
15 |
16 |
17 |
27 |
39 |
46 |
53 |
65 |
100 |
Table 4
Powder particles elongation, %
00 СО |
1 § |
in сц |
о |
40 |
in сц |
о in сц |
in сц |
сц |
о 04 сц |
in 04 сц |
1 X |
|
1 |
33 |
0,01 |
11 |
14 |
17 |
22 |
32 |
45 |
50 |
51 |
54 |
91 |
2 |
34 |
0,01 |
10 |
14 |
17 |
21 |
32 |
44 |
49 |
54 |
59 |
91 |
3 |
39 |
0,01 |
12 |
15 |
21 |
26 |
40 |
49 |
55 |
59 |
64 |
92 |
4 |
39 |
0,01 |
10 |
16 |
22 |
29 |
38 |
51 |
57 |
61 |
64 |
97 |
5 |
38 |
0,01 |
12 |
16 |
20 |
27 |
37 |
51 |
53 |
58 |
65 |
93 |
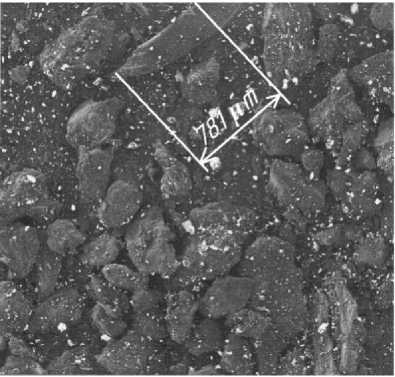
Fig. 1. Micrograph from microscope TESCAN VEGAII.
Mixture No. 2, extension 100 x
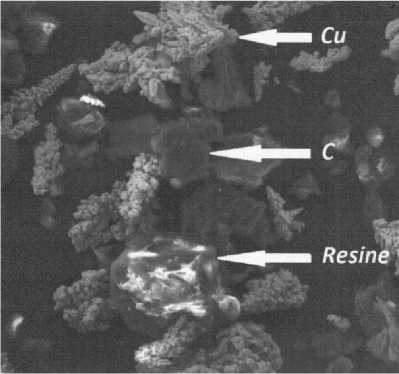
Fig. 2. Micrograph from microscope TESCAN VEGAII.
Mixture No. 3, extension 1000 x
Comparison of average values of the mesh aperture diameter allows analyzing the ratio of dimensions of the compositions’ particles. Adding binding, copper powder, coke, zinc stearate was done with simultaneous decrease of the graphite part in the composite and in the large decreased the average size of the composition particles. More than 50 % of particles in composition No. l have diameter less than 40 μm, when adding only 14 % of binding to the composition No. 2, there are more than 75 % of particles with the diameter less than 40 μm, thus, average diameter of the binding particles should be considerably less than 40 μm. Minimum and maximum values of the particles' diameter are not typical as minimum size is close to the granulо-morpho-meter sensitivity; the upper value is determined by the peculiarities of preparation of specimens for research.
Particles distribution by roundness is given in Table 3, by elongation – in Table 4. Roundness and elongation characterize the shape of particles of mixture components.
The photographs from the electron microscope (Fig. 1, 2), allow visually value the typical sizes and shape of the particles as well as the mixture homogeneity.
High Velocity Compaction research
The processes of High Velocity Compaction (HVC) carbon compositions were researched first of all scientists from ICSM of SUSU (Russia) in cooperation with scientists from National Engineering School in Saint-Etienne (France) [9–11] on the gas-hydraulic press HYP35–181 (Fig. 3).
Maximal striking energy of this press in 18 kJ, the strike speed can be changed within the range of 1–11 m/s. During experiments the striking energy varied within the range of 212–2247 J, this corresponds to the change of the punch speed which varied within the range of 1.10– 3.58 m/s. Falling mass of the striker is equal to 350 kg.
Besides that, the processes of HVC were researched in Russia scientists from ICSM of SUSU on the CEAST 9350 produced by American Instron Engineering Corp.2 in Italy with features: energy range 0.59–1800 J, impact speed 0.77–24 m/s, drop mass 2.0–70 kg. General view of the CEAST 9350 is given in Fig. 4. The CEAST 9350 is equipped wide range interchangeable falling masses available from 2.0 to 70 kg.
Fig. 5 presents a general view of the pressing block of high-speed gas-hydraulic press HYP 35-18, and Fig. 6 illustrates its principle of operation. The block works as follows. Powder is poured into the cavity of the press-mold and the punch is moved to its working position. High-speed pressing is begun by the action of a pulsator (indicated by the arrow) on the top punch. The pulsator in turn receives an energy pulse equal to 18 kNm by the discharge of an accumulator with high fluid pressure. The energy pulses can be changed within a range of 10–100 % of the maximum energy and the speed of the pulsator can be varied from 1 to 11 m/s. During operation in the pulsative forming regime, the shortest time between pulses is 450 ms.
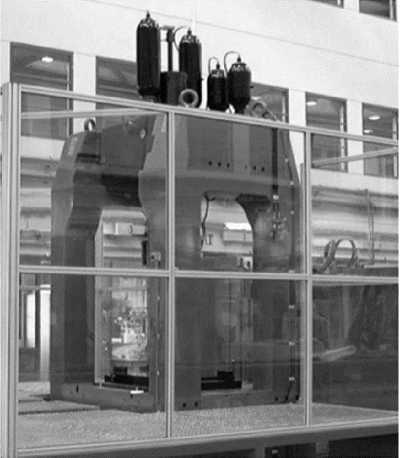
Fig. 3. Press HYP 35-18 for HVC

Fig. 4. The CEAST 9350
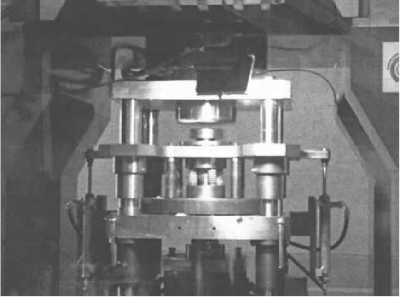
Fig. 5. Pressing block of gas-hydraulic press HYP 35-18
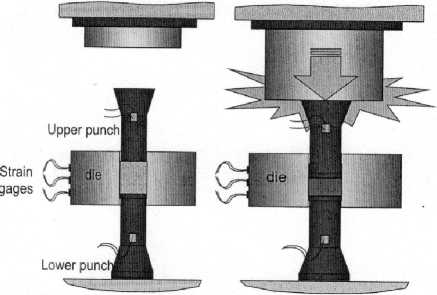
Fig. 6. Diagram showing the action of the forces during the forming operation
Results of HVC research
Results of the research compacting from the graphite powder of cylindrical specimens are given in Table 5. Compacting energy values are from 212 to 1892 J and punch stroking speed values are from 1.10 to 3.29 m/s. After compacting specimens 1 and 2 destroyed specimens 3 and 4 had defects in the form of delamination.
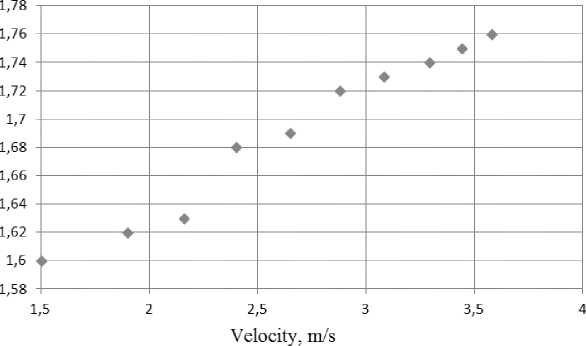
Fig. 7. Dependence density from velocity
Table 5
Specimens compaction from the graphite powder and composition
6 й о CO |
8 Q s z |
fl
CO |
So
|
CO |
"5 |
1 M) 5 |
Q |
Compaction from graphite powder |
|||||||
1 |
1 |
1 |
212 |
1,10 |
The specimen destroyed |
||
2 |
1 |
1 |
394 |
1,50 |
The specimen destroyed |
||
3 |
1 |
1 |
1450 |
2,88 |
51,2 |
12,24 |
1,63 |
4 |
1 |
1 |
1892 |
3,29 |
51,1 |
11,95 |
1,68 |
Compa ction fr om mixtur e g r a phit e + r e s in |
|||||||
5 |
2 |
2 |
394 |
1,50 |
50,35 |
12,93 |
1,60 |
6 |
2 |
1 |
632 |
1,90 |
50,34 |
12,75 |
1,62 |
7 |
2 |
1 |
816 |
2,16 |
50,30 |
12,68 |
1,63 |
8 |
2 |
1 |
1008 |
2,40 |
50,26 |
12,38 |
1,68 |
9 |
2 |
1 |
1230 |
2,65 |
50,24 |
12,26 |
1,69 |
10 |
2 |
1 |
1450 |
2,88 |
50,18 |
12,15 |
1,72 |
11 |
2 |
1 |
1657 |
3,08 |
50,16 |
12,08 |
1,73 |
12 |
2 |
1 |
1892 |
3,29 |
50,15 |
11,99 |
1,74 |
13 |
2 |
2 |
2074 |
3,44 |
50,15 |
11,97 |
1,75 |
14 |
2 |
5 |
2247 |
3,58 |
50,14 |
11,84 |
1,76 |
C ompa ction fr om mixtur e g r a phit e + resin + copper |
|||||||
15 |
3 |
1 |
1450 |
2,88 |
50,13 |
7,97 |
2,62 |
16 |
3 |
1 |
1892 |
3,29 |
50,10 |
7,90 |
2,64 |
17 |
3 |
1 |
2074 |
3,44 |
50,08 |
7,87 |
2,66 |
18 |
3 |
3 |
2247 |
3,58 |
50,07 |
7,83 |
2,67 |
After c ompa cting sp e c ime ns № 5–14 from compositions graphite+r e s in w i t h th e e ner g y a nd s pe e d v a lues i ndi c a t e d in Ta ble 5 no d e f ec t s wer e found. W hen in c r ea s ing t he c ompa c t ion ene r g y and th e punc h st r ok e spe ed it is ob se r v e d st a b le re g ula rity of incr e asing densi ty of the specime ns from 1.60 to 1.76 g/cm3 (Fig. 7).
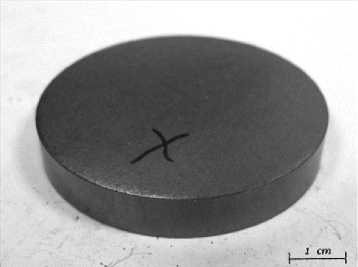
Fig. 8. Specimen from graphite + resin + copper powders
Compacting of the specimens from compositions graphite+resin+copper powders went without problems. The quality of the obtained specimens was high (Fig. 8).
Partial replacement of the graphite with coke powder did not lead to successful results. All 9 specimens obtained at formation energy 1892, 2074 and 2247 J and speed of 3.29, 3.44 and 3.58 m/s had some defects. Adding zinc stearate as a lubricant to the composite did not eliminate the defects.
Conclusions
Implementation of HVC will allow increasing the density, which in turn ensure the improved mechanical properties and decrease resistibility of such electrical products as trolleybuses current collectors, strips in pantograph collectors in trams, commuter rails, electric locomotives and brushes for electrical machines.
The increased velocity of formation leads to the increase of technical process operating efficiency at the given products formation.
The increase of work materials density after compaction makes it possible to reduce the part of the binding in the composition.
The work was supported by Act 211 Government of the Russian Federation, contract № 02.A03.21.0011.
Список литературы High velocity compaction of carbon compositions
- Edser, C. Höganäs promotes potential of high velocity compaction/C. Edser//Metal Powder Report. -2001. -Vol. 56, iss. 9. -P. 6 DOI: 10.1016/S0026-0657(01)80505-1
- Skoglung, P. High density PM parts by high velocity compaction/P. Skoglung//Powder metallurgy. -2001. -Vol. 44, no. 3. -P. 199-202.
- Skoglung, P. HVC punches PM to new mass production limits/P. Skoglung, М. Keizelman, J. Hauer//Metal Powder Report. -2002. -No. 57. -P. 26-31.
- Berglund, Т. High velocity compaction and sintering of satellite 12 powders/Т. Berglund, M. Olsson. -www.triplesteelix.se/project2008-11-28_103.
- Comparison of conventional and HVC of alumina powders/D. Souriou, P. Goeuriot, O. Bonnefoy et al.//Extended abstracts. 11th International Ceramics Congress and 4th Forum on New Materials, Acireale (Sicily, Italy), 2006.
- High velocity compaction of electro-lytic copper powder/J.Z. Wang, X.H. Qu, H.Y. Yin et al.//The Chinese journal of nonferrous metals. -2008. -Vol. 18, iss. 8. -P. 1498-1503.
- Effect of multiple impacts on high velocity pressed iron powder/J.Z. Wang, H.Q. Yin, X.H. Qu et al.//Powder Technology. -2009. -Vol. 195, no. 3. -P. 184-189.
- High velocity compaction of ferrous powder/J.Z. Wang, H.Q. Yin, X.H. Qu et al.//Powder Technology. -2009. -No. 192. -P. 131-136.
- Static and high-energy shaping of carbon-based powder composites/M.N. Samodurova, L.A. Barkov, V.A. Ivanov et al.//Metallurgist. -2012. -Vol. 55, no. 11-12. -P. 848-853.
- Пат. 2176590 Российская Федерация, МПК B 24 D 18/00, B 29 C 43/36. Пресс-форма для формования заготовок/В.Н. Дятлов, Л.А. Барков, В.И. Трусковский и др. -2000107551/02; заявл. 27.03.2000; опубл. 10.12.2001, Бюл. № 34. -4 с.
- Оборудование для обработки давлением порошков и порошковых заготовок/Л. А. Барков . -Челябинск: Металл, 1992. -296 c.