Influence of the technological conditions of detonation coatings application on their phase composition
Автор: Sirota V.V., Savotchenko S.E., Strokova V.V., Bondarenko D.O., Podgorny D.S.
Журнал: Nanotechnologies in Construction: A Scientific Internet-Journal @nanobuild-en
Рубрика: The study of the properties of nanomaterials
Статья в выпуске: 5 Vol.16, 2024 года.
Бесплатный доступ
Introduction. Detonation spraying is an effective method for applying high-quality coatings to various materials, widely used in industry to improve wear resistance and corrosion resistance of surfaces. This article examines the influence of key process parameters, such as gun-to-substrate distance and nozzle velocity, on the structure and properties of the resulting coatings. Materials and methods of research. The Ti–TiO2 coatings on hot-rolled carbon steel are studied. The spray distance and the speed of nozzle passage are varied while the rest spraying parameters are fixed. The obtained coatings were studied using scanning electron microscopy, X-ray diffraction, and energy-dispersive X-ray spectroscopy. Results and discussion. It is found that the phase composition of the coating changes depending on the detonation spray conditions. The fraction of rutile exceeds the fraction of anatase in the obtained samples except for the samples obtained with the fastest nozzle passage. The rutile fraction monotonically decreases with an increase in the spray distance with fixed values of the rest parameters of spraying process. It is found a nonmonotonic changing the rutile fraction with an increase in the speed of nozzle passage and found its optimal values. Two new theoretical models for the spray process based on differential equations are proposed, the solutions of which sufficiently describe the dependencies of the rutile fraction on the distance and speed of the nozzle, respectively. Conclusion. It has been demonstrated that the theoretical values of the parameters, calculated using the formulated equations, are in good agreement with the experimentally measured values.
Ti–TiO2, composite coatings, detonation spray coating process, phase composition, anatase, rutile, X-ray diffraction analysis, spray distance, the speed of nozzle passage
Короткий адрес: https://sciup.org/142242274
IDR: 142242274 | DOI: 10.15828/2075-8545-2024-16-5-404-414
Текст научной статьи Influence of the technological conditions of detonation coatings application on their phase composition
Original article
O ptimizing the technological parameters of coating deposition to achieve the desired characteristics is an important practical challenge [1]. One of the widely used methods for applying ceramic coatings is the of detonation spraying method [2–4], including those based on titanium dioxide [5–7].
Detonation spraying is a process in which coatings are formed by accelerating the sprayed powder by a blast wave generated by the combustion of flammable gas with a frequency of 1 to 100 times per second. The flammable gas enters the gun barrel, where the sprayed powder is fed, the powder accelerates and forms a continuous coating when it hits the substrate. The coatings obtained by this method are characterized by low porosity, high density
THE STUDY OF THE PROPERTIES OF NANOMATERIALS and adhesive strength. In this case, mineral (from silicate, aluminate and other rocks), oxides (including synthetic) and metal powders can be used as raw materials. Various metals and alloys, ceramics, building materials (based on Portland cement and magnesia cement), glass, various plastics and polymer glasses can be used as substrates. Separately, it is worth noting the higher economic efficiency of this method compared to HVOF [8].
The key parameters in the process of detonation spraying that influence the characteristics of the resulting coating are: the speed of passage of the gun nozzle along the substrate, the spraying distance, the used combustible gases, the morphology and thermophysical properties of the initial powder used.
Many authors investigate the influence various parameters of detonation spray process on the properties of the coatings [9–11]. In particular, the authors of [12] study the effects of oxygen fuel rate on microstructure of detonation sprayed coatings. Effects of plasma spray parameters on TiO2-coated mild steel are reported in [13]. Effects of substrate temperature and precursor amount on the properties including microstructure of TiO2 thin films are presented in [14, 15].
Phase composition of formed coatings can be controlled by the condition of spray process [16]. An important characteristic is the ratio of anatase and rutile phases for coatings based on titanium dioxide [17].
In our recent paper [18], composite coatings based on titanium oxides were successfully obtained by detonation spraying and their microstructure, phase composition and photocatalytic activity were investigated. The coating based on Ti–TiO2 is photocatalytic coatings which includes the nanosized particles abling to decompose the molecules of many pollutants due to the formation of H+, O2–, OH–, decomposing organic matter into CO2 and H2O killing algae, fungi and bacteria under the action of radiation, ultraviolet or visible spectrum [19, 20].
In this paper, we investigate the effect of detonation spray technology condition of Ti–TiO2 composite coating on metal substrate. The detonation spray coating technology we use makes it easy to vary such parameters as the distance from the nozzle to the surface (spray distance) and the speed of nozzle passage. Finding the optimal values of the technological parameters of detonation spraying make it possible to obtain coatings with the given phase fractions of rutile and anatase necessary to ensure the required photocatalytic properties.
METHODS AND MATERIALS
The hot-rolled carbon steel St3 (National Standard 380-2005, Russia) was chosen as the substrate for the coating because the metal products made from St3 take the leading place in terms of the volume of all consumed ferrous metal. Note that steel grade A57036 (ASTM/ ASME, USA) is closest in composition to St3 steel. A comparison of the elemental compositions of these steels is given in Table 1.
Steel samples 40×40 mm were made. The target surface was degreased and sandblasted before spray processing. The samples were processed in an air environment. We form the coatings with the thickness about of 100–150 µm.
The titanium powder of PTS-1 grade (JSC Polema, Russia) is used for spraying. A fraction of 40–60 µm was preliminarily selected by the sieve method. The results of studying the granulometric composition of the titanium powder of PTS-1 grade (particle size integral (dot line) and differential (solid line) distributions) are shown in Figure 1. The results of X-ray phase analysis of the titanium powder are given in your previous paper [18].
Formation of the Ti–TiO2 composite coating was carried out using a robotic complex for detonation spraying of coatings (IntelMashin LLC, Moscow, Russia) equipped with a multi-chamber detonation accelerator (MCDS) [21].
The fixed values of parameters of the coating deposition by a robotic complex for detonation spraying of coatings are following: barrel length is 300 mm, barrel diameter is 18 mm, powder feed rate is 300 g/h. Flow rates of fuel mixture components are following: air – 1.37 m3/h, oxygen – 2.48 m3/h, propane (30 %) + butane (70 %) – 0.59 m3/h, (cylindrical form combustion chamber).
The spray distance and speed of nozzle passage are varied parameters from 40 to 80, mm, and from 600 to 2000 mm/min, respectively. Five samples are sprayed under each condition. The average values of 5 tests are taken as the measurement results.
We control the microstructure of obtained coatings by scanning electron microscopy (SEM) and energy-dispersive X-ray spectroscopy (EDS) using Tescan MIRA3 LMU (Czech Republic).
The study of the phase composition of the coating was carried out using the ARL 9900 series X-ray fluorescence spectrometer (Thermo Fisher Scientific, Basel, Switzer-
Table 1
The elemental compositions of St3 and A57036 steels
Si |
C |
Mn |
S |
P |
Ni |
Cr |
Cu |
N |
As |
Fe |
|
St3 |
0.15–0,3 |
0.14–0.22 |
0.4–0.65 |
0.05 |
0.04 |
0.3 |
0.3 |
0.3 |
0.008 |
0.08 |
rest |
A57036 |
– |
0.25 |
0.9 |
0.05 |
0.04 |
– |
– |
0,2 |
– |
– |
rest |
THE STUDY OF THE PROPERTIES OF NANOMATERIALS
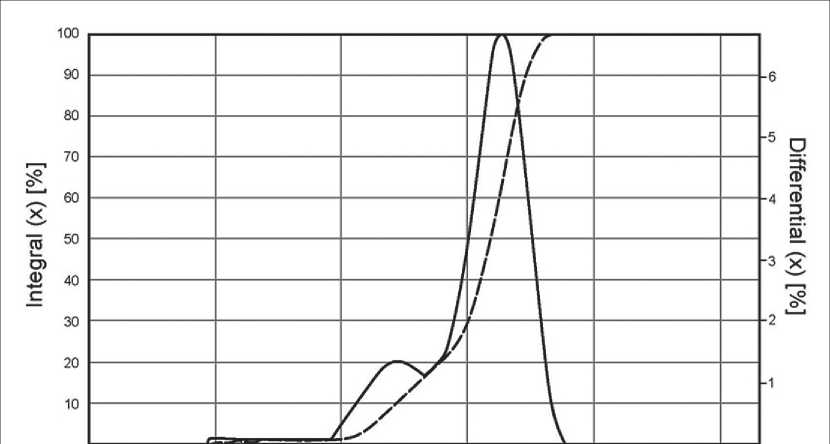
0,01

1 10 100
Diameter, pm
Fig. 1. The granulometric composition of the titanium powder of PTS-1 grade (particle size integral (dot line) and differential (solid line) distributions)
land). Quantitative analysis of the proportion of identified phases in X-ray diffraction studies was carried out using the Rietveld method using Siroquantv.3 software.
RESULTS AND DISCUSSION
There are several mechanisms that characterize changes in the phase fraction depending on the spray distance and deposition rate in coatings. First of all, as the spray distance increases, the temperature of the flow that hits the substrate decreases. Also, the kinetic energy of the powder particles decreases with an increase in the spray distance. This reduces the temperature when the kinetic energy of the powder transforms into thermal energy.
The speed of passage of the gun nozzle is also important. As the speed increases, the exposure time of the flow to the substrate surface decreases. During these processes, phase transitions Ti → TiOx occur less intensely or do not occur at all due to a decrease in temperature during coating formation.
The results of EDS and SEM analysis of the Ti–TiO2 composite coatings are presented in Figures 2–5. SEM images with a visible field of 1000 and 5000 µm (Figures 2–5, c, d) show a developed surface represented mainly by titanium oxides with spherical titanium inclusions 5–25 µm in size. When increasing to a visible field of 100 µm (Figures 2–5, b), a uniform distribution of various phases (Ti–TiOx) with smooth transitions is observed. At the same time, the surface structure is more developed than in macro photographs, which is due to the scattering of titanium particles when they hit the surface.
The resulting “titanium splashes” tend to intensify oxidation with the formation of higher titanium oxides (TiO2, Ti2O3, Ti3O5...). At the same time, at the points of impact, films in the form of metallic titanium and its lower oxides (Ti6O, Ti3O...) are often visible, which is evident from the smooth change in image shades between metallic titanium and the higher oxide (TiO2).
This fact is also confirmed by EDS images presented in Figures 2–5, a . These images show a chaotic distribution of both titanium and oxygen. At the same time, 3 main shades are visually distinguishable in the images, which are represented by: metallic titanium, titanium dioxides (anatase, rutile, brookite) and the transition phase TiO , where x = 0.7–1.3.
x ,
Results of SEM analysis allow obtaining the averaged elemental composition of coatings from a visible field of 1000 microns sprayed under different regimes. In particular, the average fraction of titanium increased by 1.8% (from 39.3 to 37.5%), and the average fraction of oxygen decreased by 1.7% (from 62.3 to 60.6%) when the deposition distance increased from 40 to 80 mm, at a constant speed of passage of the detonation nozzle of 1500 mm/min. Consequently, doubling the spraying distance leads to an increase in the average fraction of titanium by approximately 2% and a decrease in the average fraction of oxygen by approximately the same amount.
The average fraction of titanium decreased by 4.7% (from 48.0 to 43.3%), and the average fraction of oxy-
THE STUDY OF THE PROPERTIES OF NANOMATERIALS
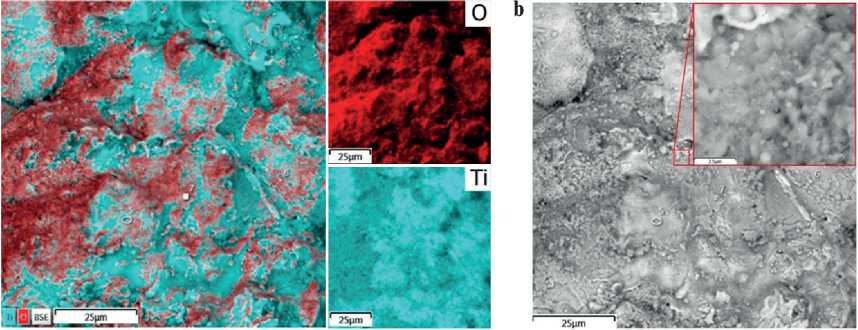
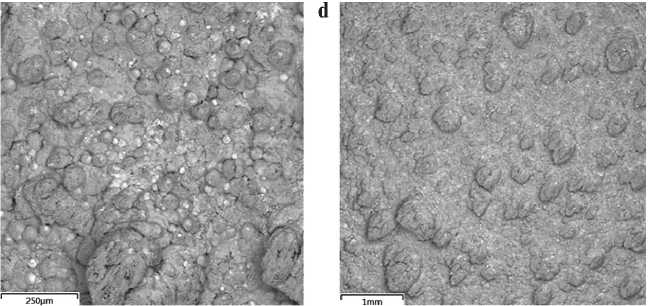
Fig. 2. EDS (a) and SEM images with visible field of 100 µm (b), 1000 µm (c), 5000 µm (d) of coatings obtained with the speed of nozzle passage of 1500 mm/min, and the spray distance of 40 mm
а
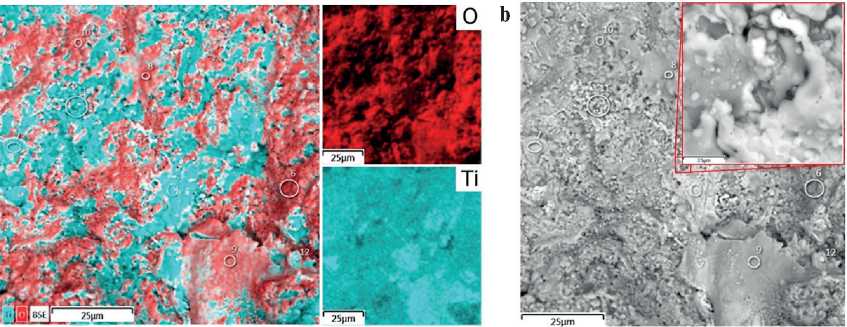
c
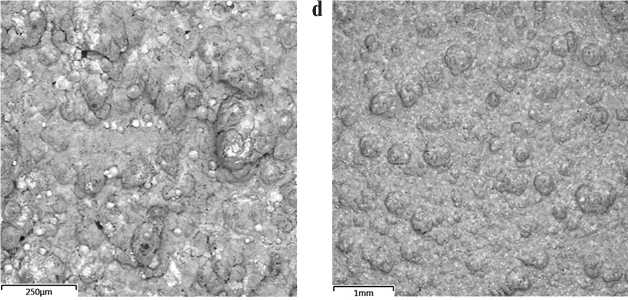
Fig. 3. EDS (a) and SEM images with visible field of 100 µm (b), 1000 µm (c), 5000 µm (d) of coatings obtained with the speed of nozzle passage of 1500 mm/min, and the spray distance of 80 mm
THE STUDY OF THE PROPERTIES OF NANOMATERIALS
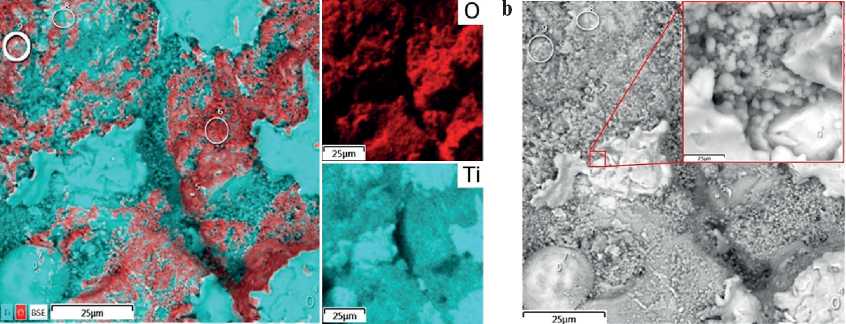
c
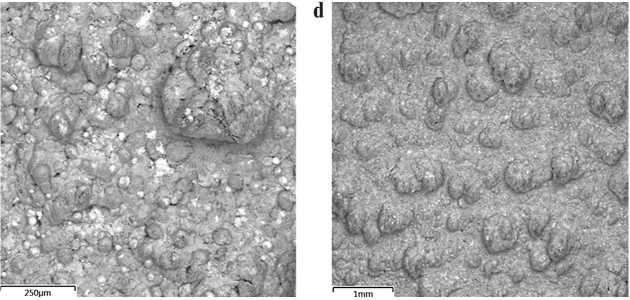
Fig. 4. EDS (a) and SEM images with visible field of 100 µm (b), 1000 µm (c), 5000 µm (d) of coatings obtained with the speed of nozzle passage of 600 mm/min, and the spray distance of 60 mm
а
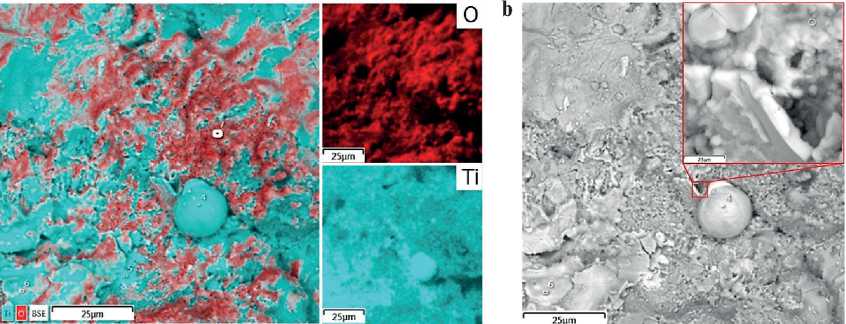
c
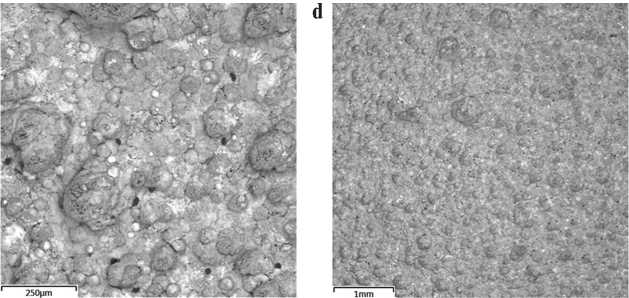
Fig. 5. EDS (a) and SEM images with visible field of 100 µm (b), 1000 µm (c), 5000 µm (d) of coatings obtained with the speed of nozzle passage of 2000 mm/min, and the spray distance of 60 mm
THE STUDY OF THE PROPERTIES OF NANOMATERIALS gen increased by 3.8% (from 51.8 to 55.6%) when the speed of passage of the detonation nozzle increased from 600 to 2000 mm/min, at a constant deposition distance of 60 mm. Consequently, an increase in the speed of passage of the detonation nozzle by more than 3.3 times leads to a decrease in the average fraction of titanium and an increase in the average fraction of oxygen by approximately 4–5%.
Such conclusions suggest the existence of a linear dependence of the average fractions of titanium and oxygen in the resulting coatings on such technological spraying parameters as the spray distance and speed of the nozzle.
The results of X-ray diffraction (XRD) analysis of the coatings are presented in Figures 6 and 7. We take into account the main phase composition of formed coating:
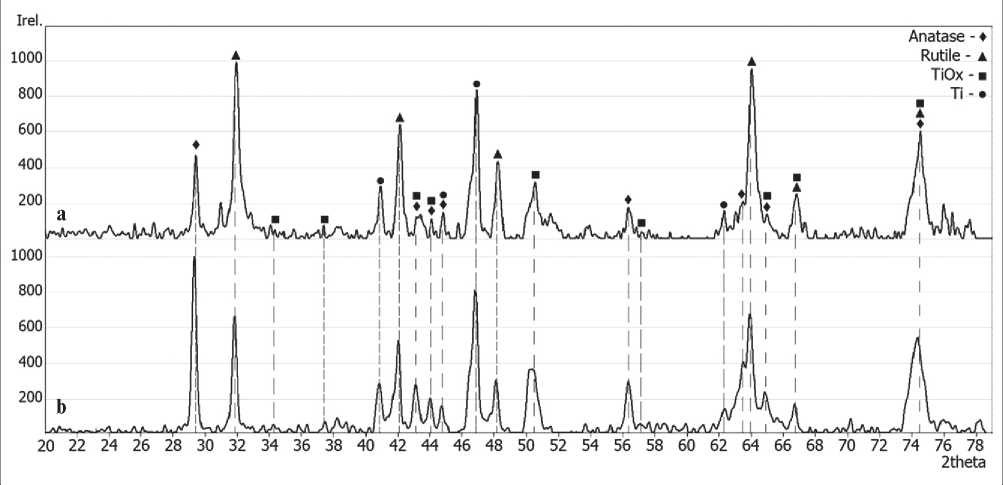
Fig. 6. XRD patterns (intensity, a.u., versus 2Θ,°) of coatings obtained with fixed speed of nozzle passage 1500, mm/min and different spray distance: a) 40 mm; b) 80 mm. Phase composition is presented in Table 2
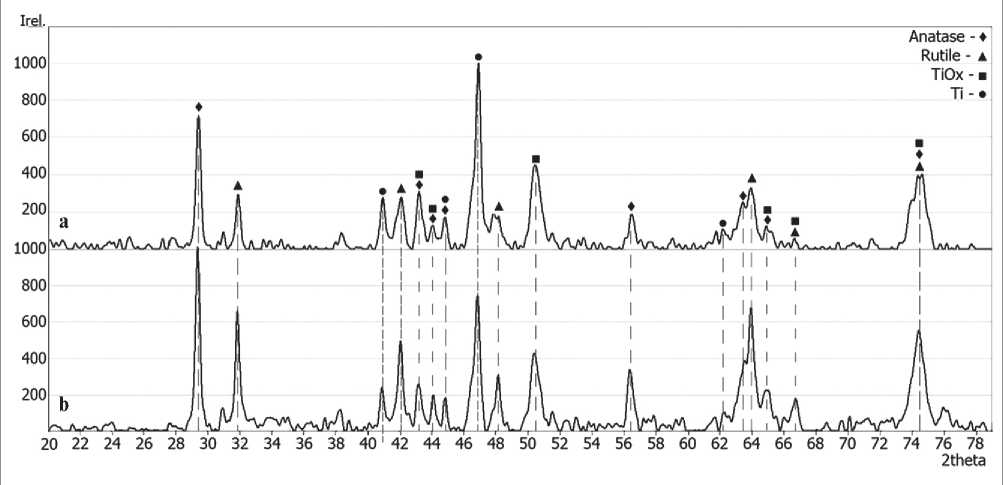
Fig. 7. XRD patterns (intensity, a.u., versus 2Θ,°) of coatings obtained with fixed spray distance 60 mm, and different values of speed of nozzle passage: a) 2000 mm/min; b) 600 mm/min. Phase composition is presented in Table 2
THE STUDY OF THE PROPERTIES OF NANOMATERIALS rutile (TiO2), anatase (TiO2), titanium oxide (TiO), and titanium (Ti) (see Table 2).
Figure 6 shows diffractograms of two coatings, which formed with fixed speed of nozzle passage 1500 m/min, and different spray distances 40 and 80 mm, respectively. Figure 3 shows diffractograms of two coatings, which formed with fixed spray distance 20, mm, and different values of speed of nozzle passage 600 and 2000 mm/min, respectively.
The results of XRD analysis of the coatings showed that the relative intensity of the peaks changes significantly the phase composition changes. This allows us to conclude that the phase composition of the coating changes depending on the detonation spray conditions. The fraction of rutile exceeds the fraction of anatase in the obtained samples except for the samples obtained with the fastest nozzle passage.
Table 3 shows the material characteristics of the al- lotropic species of titanium dioxide, in particular the lattice parameters of the unit cell, as well as the types and arrangements of atoms in the unit cell.
Figure 7 shows change in the phase composition of the coatings formed under different values of the spray distance and fixed the rest values of the spray process parameters (including fixed value of the speed of the nozzle passage 1500 mm/min). We focus below on change in the rutile fraction due to its importance in the composition of photocatalytic titanium coatings [22, 23].
We find that the rutile fraction ( YR , %) monotonically decreases from 44.97 to 30.87% with an increase in the spray distance ( d , mm) from 40 to 80 mm. Three segments of this dependence can be distinguished. The rate of decrease in the rutile fraction is greatest at small spray distances (segment 1 in Figure 8). Then, a slowdown is observed in the middle of the dependence, when the rutile fraction decreases slightly (segment 2 in Figure 8). The decrease in the rutile fraction accelerates with a further increase in the spray distance (segment 3 in Figure 8).
We calculate the linear approximations of dependence of the phase fractions Y ( w = R for rutile fraction, w = A for anatase fraction, w = O for titanium oxide fraction, w = T for titanium fraction) on the spray distance (mm):
Y w ( d ) = k w • d + Y w 0 , (1)
where the values of parameter kw and Y 0 of Eq. (1) are presented in Table 4. We plot Eq. (1) in Figure 8 (solid straight lines) for each phase fraction. Here kw (%/mm) is the average rate of the w-phase fraction changing with the spray distance; Y у 0 (%) is the conventional value of the w-phase fraction at zero spray distance.
Table 2
The phase compositions of coatings obtained in different spray regimes corresponding to the Figures 6 and 7
Phase compositions, % |
Speed of nozzle passage, mm/min |
Spraying distance, mm |
Fig. no |
|||
Anatase |
Rutile |
TiO |
Ti |
|||
11.01 |
50.82 |
23.15 |
15.02 |
1500 |
40 |
6, a |
29.69 |
33.25 |
18.43 |
18.62 |
1500 |
80 |
6, b |
23.11 |
20.82 |
27.4 |
28.63 |
2000 |
60 |
7, a |
28.25 |
33.93 |
19.78 |
18.04 |
600 |
60 |
7, b |
Table 3
The material characteristics of the allotropic species of titanium dioxide
Anatase |
Rutile |
Ti |
TiO |
|
COD number |
96-900-8215 |
96-900-4142 |
96-900-8518 |
96-110-0043 |
Space group |
I41/amd(#141-1) |
P42/mnm(#136-1) |
P63/mmc(#194-1) |
A2/m(#12-4) |
a, Å |
3.78920 |
4.59300 |
2.95000 |
5.85500 |
b, Å |
3.78920 |
4.59300 |
2.95000 |
9.34000 |
c, Å |
9.53700 |
2.95900 |
4.68600 |
4.14200 |
Volume, Å3 |
136.9326 |
62.4220 |
35.3164 |
215.9890 |
α, ° |
90.0000 |
90.0000 |
90.0000 |
90.0000 |
β, ° |
90.0000 |
90.0000 |
90.0000 |
90.0000 |
γ, ° |
90.0000 |
90.0000 |
120.0000 |
107.5300 |
THE STUDY OF THE PROPERTIES OF NANOMATERIALS
---------30 050505050 544332211 %=£зи«asvqd
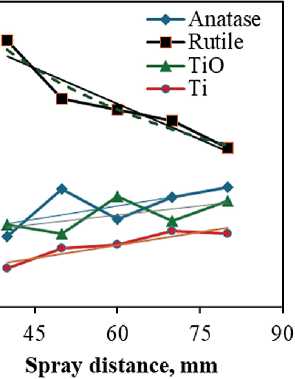
Fig. 8. Dependencies of the phase composition of the coatings formed under different values of the spray distance and fixed the rest values of the spray process parameters (including fixed value of the speed of the nozzle passage 1500 mm/min; see main text for details)
Dependence of the rutile fraction YR ( d ) allows obtaining that the average rate of the rutile fraction decreasing with the changing spray distance is about of 0.31 %/mm (coefficient of determination R 2 = 0.887).
We observe that the anatase fraction does not change significantly. It slightly increases with an increase in the spray distance, within about of 5% from 19.21 to 25.65% (see Figure 8). The average rate of anatase fraction increasing with the changing spray distance is about of 0.118 %/mm ( R 2 = 0.45). The rest observed fraction show a similar trend. They are slightly increases with an increase in the spray distance too with average rates are about of 0.079 %/mm (TiO, R 2 = 0.36), and 0.112 %/mm (Ti, R 2 = 0.85). Thus, the growth of the remaining fractions is insignificant and amounts to about 5% with the same growth rate about of 0.1 %/mm.
It is interesting to note that the sum of the all average rates of the phase fraction changing is zero (see Table 4): kR + kA + kO + kT = 0. Therefore, we can write relationship between the average rates of the phase fraction changing as follows: | kR | = kA + kO + kT .
In addition, we note that the straight lines corresponding to the dependences of the titanium and titanium oxide fractions are almost parallel (see Figure 8), since kO ≈ kT. This means that the increase in the fractions of titanium and titanium oxide is almost the same.
We find that the best fit of experimental data of rutile fraction dependence on the spray distance (markers in Figure 8) is given by the inverse power law YR ( d ) = 264.1/ d 0.28 (dash line in Figure 8) with the coefficient of determination R 2 = 0.94. This dependence approximates the experimental data better than the linear equation, for which R 2 = 0.887 (see Table 4, w = R ).
In order to describe this equation, we suppose that the rate of rutile fraction decreasing Y´R (the prime indicates the derivative of YR with respect to the spray distance d ) with the changing spray distance is proportional to YR and inverse proportional to the spray distance. Therefore, we can write following differential equation
YR (d)= - bYR, (2) d where b is the proportion coefficient.
The solution to Eq. (1) is given by
YR (d) = db, ⑶ where a is the integration constant.
We indicated above found using least square method the values of a = 264.1 mm•% and b = 0.48. The value of coefficient of determination is close to one ( R 2 = 0.94). This indicates that solution (3) of the formulated equation (2) is adequately described by experimental data. Thus, we propose the model of spray process sufficiently describing dependence of the rutile fraction with the changing spray distance.
Figure 9 shows change in the phase composition of the coatings formed under different values of the speed of nozzle passage and fixed the rest values of the spray process parameters (including fixed spray distance d = 60 mm).
We observe a nonmonotonic changing the rutile fraction with an increase in the speed of nozzle passage ( s , mm/min). The maximum of rutile fraction is about 34.16% at s = 800 mm/min.
Two main segments of the experimental dependence can be distinguished. The first segment is characterized
Table 4
The values of parameters k and Yw0 of Eq. (1)
Phase |
w |
kw , %/mm |
Yw 0, % |
R2 |
Rutile |
R |
– |
55.31 |
0.887 |
Anatase |
A |
0.118 |
16.14 |
0.449 |
TiO |
O |
0.079 |
17.21 |
0.363 |
Ti |
T |
0.112 |
11.33 |
0.852 |
THE STUDY OF THE PROPERTIES OF NANOMATERIALS
貫 яОІЗиа3svqd
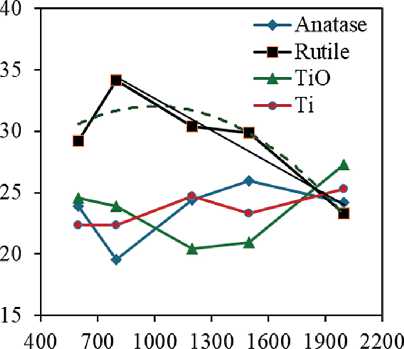
Speed of nozzle passag, mm/min
Fig. 9. Dependencies of the phase composition of the coatings formed under different values of the speed of the nozzle passage and fixed the rest values of the spray process parameters (including fixed value of the spray distance 60 mm; see main text for details)
by the growth of the rutile fraction to it maximum value at small values of s (segment 1 in Figure 9). Then, a decrease in the rutile fraction from the maximum to 23.29% is observed with a further increase in the speed of nozzle passage from 800 to 2000 (segment 2 in Figure 9).
The second segment can be sufficiently approximated by linear equation (solid straight line in Figure 9) YR ( s )= 41.39 — 0.01 ・ s ( R 2 = 0.84), from which we obtain that the average rate of rutile fraction decreasing is about of 0.01 %•min/m with the changing speed of nozzle passage from 800 to 2000 mm/min.
We find the parabolic equation (dash line in Figure 9) Y r ( s ) = 23.08 + 0.017 ・ s - 9 ・ 10-6 ・ s 2 ( R = 0.84), which can be used to fit of the experimental data (markers in Figure 9) over all range of the speed of nozzle passage varying.
In order to describe this parabolic equation, we suppose that the changing of rutile fraction occurs with negative constant acceleration Y'R (two primes indicate the second order derivative of Y r with respect to the speed of nozzle passage s) with the changing spray distance. Therefore, we can write following second order differential equation
Y,R (s) = -2А, ⑷ where A is the acceleration constant.
The solution to Eq. (4) is given by
Y r = 工 — A •( s — s j, (5)
where 工 is the rutile fraction maximum at optimal value of the speed of nozzle passage sm .
Using calculated above parabolic equation, we find the following values of parameters of Eq. (5): A = 9 ・ 10-6% • (min/mm)2, Ym = 34.19%, sm = 1110 mm/min. The theoretical values of the maximum of the rutile fraction and corresponding the speed of nozzle passage calculated using Eq. (5) are in satisfactory agreement with the experimentally observed values (34.16%, s . = 800 mm/min). Thus, we propose the model of spray process sufficiently describing dependence of the rutile fraction with the changing speed of nozzle passage.
CONCLUSION
We investigated experimentally the influence of the technology conditions of detonation spraying of coatings on its phase composition. We form the Ti–TiO2 composite coating on hot-rolled carbon steel St3 substrate. We varied the spray distance and the speed of nozzle passage while the rest spraying parameters were fixed.
We found basing on obtained results of XRD analysis that the phase composition of the coating changes depending on the detonation spray conditions. We observed that the fraction of rutile exceeds the fraction of anatase in the obtained samples except for the samples obtained with the fastest nozzle passage. Results showed that changing the spray distance and speed nozzle passage did not significantly affect the anatase fraction.
We found that the rutile fraction monotonically decreases with an increase in the spray distance with fixed values of the rest parameters of spraying process. We obtained that the inverse power law fits of experimental dependence of the rutile fraction on the spray distance.
We observed a nonmonotonic changing the rutile fraction with an increase in the speed of nozzle passage and found its optimal values. We obtained that the parabolic equation fits of experimental dependence of the rutile fraction on the speed nozzle passage.
We proposed two new theoretical models of spray process based on differential equations, the solutions to which sufficiently describe dependencies of the rutile fraction on the spray distance and the speed of nozzle passage respectively. We showed that the theoretical values of the parameters calculated using the formulated equations are in satisfactory agreement with the experimentally observed values. We found relationship between the average rates of the phase fraction changing.
We believe that our results can be useful for optimization of detonation spray technology to obtain the Ti–TiO2 based coatings with the given phase fractions of rutile and anatase necessary to ensure the required photocatalytic properties.
THE STUDY OF THE PROPERTIES OF NANOMATERIALS
Список литературы Influence of the technological conditions of detonation coatings application on their phase composition
- Ramaiah K., Bettahalli Eswaregowda N., Tambrallimath V., Kuppahalli P. Optimization of deposition parameters in plasma spray coatings. Modeling and Optimization in Manufacturing. 2021; 217–235.
- Haridasan V., Velayudham A., Krishnamurthy R. Response surface modeling and parameter optimization of detonation spraying with enhanced coating performance. Materials Today: Proceedings. 2021; 46: 3474–3481.
- Ulianitsky V., Rybin D., Sova A., Ostovari Moghaddam A., Samodurova M., Doubenskaia M., Trofimov E. Formation of metal composites by detonation spray of powder mixtures. The International Journal of Advanced Manufacturing Technology. 2021; 117 (1–2): 81–95.
- Moghaddam A.O., Samodurova M., Mikhailov D., Trofimov E. High entropy intermetallic coatings fabricated by detonation spraying. Materials Letters. 2022; 311. Article number 131560.
- Dudina D., Zlobin S., Bulina N., Bychkov A., Korolyuk V., Ulianitsky V., Lomovsky O. Detonation spraying of TiO2–2.5vol.% Ag powders in a reducing atmosphere. Journal of the European Ceramic Society. 2012; 32 (4): 815–821.
- Sirota V.V, Savotchenko S.E., Strokova V.V, Vashchilin V.S., Podgornyi D.S., Prokhorenkov D.S., Zaitsev S.V., Kovaleva M.G. Effect of detonation spray regimes on photocatalytic activity of Ti–TiO2 coatings. Journal of Photochemistry and Photobiology A: Chemistry. 2024; 452. Article number 115626.
- Sirota V.V., Savotchenko S.E., Strokova V.V., Vashchilin V.S., Podgornyi D.S., Limarenko M.V., Kovaleva M.G. Effect of irradiation intensity on the rate of photocatalysis of TiO2 coatings obtained by detonation spraying. International Journal of Applied Ceramic Technology. 2024; 21(5): 3335–3345.
- Tyurin Y., Kolisnichenko O., Jia J., Vasilik N., Kovaleva M., Prozorova M., Arseenko M., Sirota V. Performance and economic characteristics of multi-chamber detonation sprayer used in thermal spray technology. International Thermal Spray Conference. 2016; 83768: 630–634.
- Sreekumar Rajesh T., Venkata Rao R. Experimental investigation and parameter optimization of Al2O3–40% TiO2 atmospheric plasma spray coating on SS316 steel substrate. Materials Today: Proceedings. 2018; 5 (2): 5012–5020.
- Kumar N., Choubey V. Comparative evaluation of oxidation resistance of detonation gun-sprayed Al2O3–40%TiO2 coating on nickel-based superalloys at 800 °C and 900 °C. High Temperature Corrosion of Materials. 2023; 99 (5–6): 359–373.
- Kantay N., Rakhadilov B., Kurbanbekov S., Yeskermessov D., Yerbolatova G., Apsezhanova A. Influence of detonation-spraying parameters on the phase composition and tribological properties of Al2O3 coatings. Coatings. 2021; 11 (7). Article number 793.
- Xie L., Wang Y., Xiong X., Chen Z., Wang Y. Effects of oxygen fuel rate on microstructure and wear properties of detonation sprayed iron-based amorphous coatings. Materials Transactions. 2018; 59 (12): 1867–1871.
- Forghani S., Ghazali M., Muchtar A., Daud A., Yusoff N., Azhari C. Effects of plasma spray parameters on TiO2-coated mild steel using design of experiment (DoE) approach. Ceramics International. 2013; 39 (3): 3121–3127.
- Astinchap B., Laelabadi K. Effects of substrate temperature and precursor amount on optical properties and microstructure of CVD deposited amorphous TiO2 thin films. Journal of Physics and Chemistry of Solids. 2019; 129: 217–226.
- Astinchap B., Ghanbaripour H., Amuzgar R. Multifractal study of TiO2 thin films deposited by MO-CVD method: The role of precursor amount and substrate temperature. Optik. 2020; 222. Article number 165384.
- Ulianitsky V., Dudina D., Batraev I., Kovalenko A., Bulina N., Bokhonov B. Detonation spraying of titanium and formation of coatings with spraying atmosphere-dependent phase composition. Surface and Coatings Technology. 2015; 261: 174–180.
- Dey B., Bulou S., Gaulain T., Ravisy W., Richard-Plouet M., Goullet A., Granier A., Choquet P. Anatase TiO2 deposited at low temperature by pulsing an electron cyclotron wave resonance plasma source. Scientific Reports. 2020; 10 (1). Article number 21952.
- Sirota V., Vashchilin V., Ogurtsova Y., Gubareva E., Podgornyi D., Kovaleva M. Structure and photocatalytic properties of the composite coating fabricated by detonation sprayed Ti powders. Ceramics International. 2024; 50 (1): 739–749.
- Liu Y., Huang J., Feng X., Li H. Thermal-Sprayed photocatalytic coatings for biocidal applications: A Review. Journal of Thermal Spray Technology. 2021; 30 (1–2): 1–24.
- Atacan K., Güy N., Özacar M. Recent advances in photocatalytic coatings for antimicrobial surfaces. Current Opinion in Chemical Engineering. 2022; 36. Article number 100777.
- Sirota V., Pavlenko V., Cherkashina N., Kovaleva M., Tyurin Y., Kolisnichenko O. Preparation of aluminum oxide coating on carbon/carbon composites using a new detonation sprayer. International Journal of Applied Ceramic Technology. 2021; 18 (2): 483–489.
- Iesalnieks M., Eglītis R., Juhna T., Šmits K., Šutka A. Photocatalytic activity of TiO2 coatings obtained at room temperature on a polymethyl methacrylate substrate. International Journal of Molecular Sciences. 2022; 23 (21). Article number 12936.
- Bersch J., Flores-Colen I., Masuero A., D. Dal Molin Photocatalytic TiO2-based coatings for mortars on facades: A Review of Efficiency, Durability, and Sustainability. Buildings. 2023; 13 (1). Article number 186.