Интенсификация процесса разделения газов каталитического крекинга
Автор: Шаймарданов М.И., Валеев М.Р., Ханнанова Г.Д., Фасхутдинов Р.Р.
Журнал: Международный журнал гуманитарных и естественных наук @intjournal
Рубрика: Технические науки
Статья в выпуске: 12-5 (87), 2023 года.
Бесплатный доступ
Проведены анализ работы и цифровое моделирование блока газофракционирования установки каталитического крекинга 1-А/1М завода ПАО АНК «Башнефть» «Башнефть-Уфанефтехим». В результате проведенного анализа определены пути совершенствования процесса выделения пропан-пропиленовых, бутан-бутиленовых фракций. В рамках процесса моделирования были рассмотрены различные сценарии повышения эффективности процесса газоразделения. В результате работы выявлены оптимальные технологические параметры колонны.
Каталитический крекинг, газофракционирование, пропан-пропиленовая фракция, бутан-бутиленовая фракция, фракционирующий абсорбер, жирный газ, моделирование
Короткий адрес: https://sciup.org/170201683
IDR: 170201683 | DOI: 10.24412/2500-1000-2023-12-5-72-78
Текст научной статьи Интенсификация процесса разделения газов каталитического крекинга
В данный момент наблюдается кризис сырьевой базы нефтехимической промышленности. Основное назначение нефтехимических предприятий состоит в использовании продуктов нефтеперерабатывающих заводов для производства синтетических материалов и изделий.
Основным сырьем для нефтехимических предприятий выступают продукты нефти и газопереработки, в том числе непредельные углеводородые газы, такие как пропан-пропиленовая фракция (ППФ), бутан-бутиленовая фракция (ББФ), которые вырабатываются в процессе каталитического крекинга. ППФ применяется в качестве сырья процессов полимеризации и алкилирования, ББФ является сырьем процесса алкилирования, также используется в производстве метилэтилкетона, полиизобутилена, синтетического каучука и т.д. [4; 5]
Каталитический крекинг (КК) является одним из основных крупнотонажных процессов углубленной переработки нефти. Установка КК состоит из следующих блоков: гидроочистки вакуумного газойля (сырьё процесса), реакторно-регенераторного, нагревательно
- фракционирующего и газофракционирования.
Разделение газов осуществляется на блоке газофракционирования. Типичная схема блока газофракционирования состоит из фракционирующего абсорбера, компрессора, сепараторов, циркуляционных насосов и откачки продуктов [2].
В рамках данной работы рассмотрим методы интенсификации процесса разделение газов, полученных в процессе каталитического крекинга. Конкретизируем задачу на примере газофракционирующего блока установки КК 1-А/1М Филиала ПАО АНК «Башнефть» «Башнефть-Уфанефтехим», где существует проблема потерь ППФ, ББФ в результате уноса с сухим газом КК.
Предложенный метод позволяет повысить качество разделения газофракционирующего блока установки с минимальными капитальными затратами. Проведен анализ работы текущей технологической схемы газофракционирующего блока установки КК 1-А/1М ПАО АНК «Башнефть» «Башнефть-Уфанефтехим», на основе которого были определены основные возможные направления модернизации, показано влияние основных технологиче- ских параметров процесса на выход и качество получаемых продуктов.
Фракционирующий абсорбер представляет собой аппарат колонного типа с ребойлером.
Необходимая четкость отбора сухих и жирных газов может быть достигнута следующими методами:
-
1. Изменение технологических
параметров процесса:
-
- Увеличение давления в колонне;
-
- Уменьшение температуры в кубовой части фракционирующего абсорбера;
-
- Увеличение кратности циркуляции абсорбента [3].
-
2. Изменение конструктивных
особенностей газофракционирующего блока:
-
- Увеличение числа контактных устройств фракционирующего абсорбера.
-
- Модернизация внутренних
контактных устройств фракционирующего абсорбера на более эффективные без изменения их количества.
-
- Регулирование количества
циркуляционных орошений, их температуры, а также изменения тарелок их отбора и возврата [1].
Эффективность процесса разделения зависит от таких технологических параметров, как температура, давление, количество контактных устройств, а также соотношение величины потоков пара и жидкости по высоте колонны. В контексте работы фракционирующего абсорбера К51 необходимо выделение сухого газа, не содержащего в своем составе ППФ, ББФ. ППФ и ББФ выводятся с куба колонны вместе с бензином КК, и направляются на дальнейшее разделение [6].
Сформированная модель газофракционирующего блока в системе моделирования Aspen Hysys позволила оценить эффективность работы абсорбера и разработать мероприятия по корректировке режима его работы для повышения качества продуктов и увеличения выхода целевых компонентов в кубовом продукте. На базе модели были рассмотрены различные сценарии работы фракционирующего абсорбера К-51, с целью нахождения оптимальных значений давления верха и низа колонны, при которых удалось достигнуть повышения качества газоразделения.
Модель была построена на основе уравнения состояния Пенга-Робинсона.
Уравнение имеет следующий вид:
RT a(T)
Vm-b у2_^2Ь.ут-№ где p – давление газа, кПа;
R – универсальная газовая постоянная, Дж/(моль·К);
V m – молярный объём, м3/моль;
Т – температура газа, К.
Достоинством уравнения является то, что свойства чистого газа описываются этим уравнением с помощью только трёх индивидуальных свойств: температуры и давления критической точки газа, а также ацентрического фактора Питцера. Эти параметры определены для широкого круга веществ [8].
При расчёте смесь рассматривается как некоторый гипотетический газ, параметры критической точки которого являются известной функцией концентраций исход- ных компонентов и термодинамических параметров их критических точек [8].
На установке 1-А/1М Филиала ПАО АНК «Башнефть» «Башнефть-Уфанефтехим» в настоящее время есть проблема потери жирных газов в составе сухого газа, выводимого с верха фракционирующего абсорбера К-51. Для анализа пути интенсификации процесса выделения газов жирных газов из сухого газа КК была сформирована модель абсорбера К-51 в среде Aspen Hysys.
Для сравнительного анализа вариантов работы фракционирующего абсорбера К51 была воспроизведена технологическая схема, представленная на рисунке 1. Со- став сырья и технологические параметры фракционирующего абсорбера установки 1-А/1М представлены в таблицах 1 и 2.
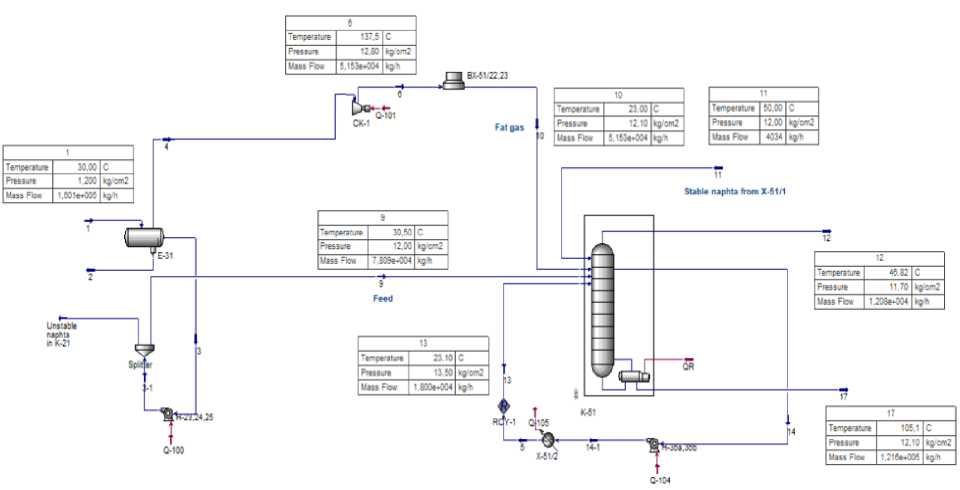
К-51 - фракционирующий абсорбер; Е-31 - газосепаратор; СК-1 - газовый компрессор; Н-23, 24, 25, 36а, 36в - насос; ВХ-51/22,23 - аппарат воздушного охлаждения; Х-51 - теплообменник
Рис. 1. Схема газофракционирующего блока установки 1-А/1М
Для достижения необходимой степени отбора сухих и жирных газов, методы, связанные с изменением конструкций газофракционирующего блока, не рассматриваются в рамках решения производственной задачи, что связанно с высокими капитальными затратами и длительными сроками реализации проекта модернизации.
Увеличение кратности циркуляции абсорбента не позволит должным образом выделить сухой газ в качестве верхнего продукта без увеличения диаметра колонны, что обусловленно повышенным расходом жидкого потока над паровым на контактных устройствах в верхней части фракционирующего абсорбера и физическим уносом жидкой фазы с сухим газом [7].
Уменьшение температуры в кубе фракционирующего абсорбера уменьшает отпаривание легких компонентов, и повышают концентрацию компонентов сухого газа С 1 -С 2 в кубовом продукте.
Таблица 1. Исходный состав сырья колонны К-51
Наименование компонента |
Состав, % масс. |
Метан |
1,57 |
Этан-этиленовая фракция |
2,35 |
Пропан-пропиленовая фракция |
7,11 |
Бутан-бутиленовая фракция |
11,59 |
H 2 S |
0,11 |
O 2 |
0,10 |
H 2 |
0,05 |
N 2 |
1,23 |
CO |
0,10 |
CO 2 |
0,30 |
H 2 O |
6,32 |
фр. н.к. - 50 ℃ |
22,82 |
фр. н.к. - 50-78 ℃ |
11, 7 |
фр. н.к. - 78-106 ℃ |
7,31 |
фр. н.к. - 106-134 ℃ |
5,47 |
фр. н.к. - 134-162 ℃ |
12,6 |
фр. н.к. - 162-190 ℃ |
5,09 |
фр. н.к. - 190-218 ℃ |
1,72 |
фр. н.к. - 218-246 ℃ |
1,14 |
фр. н.к. - 246-274 ℃ |
1,32 |
Итого: |
100 |
Таблица 2. Нормы технологического режима фракционирующего абсорбера К-51
Наименование параметра |
Единицы измерения |
Рабочие значения |
Расчетные значения |
Давление верха колонны |
кгс/см2 |
10,72 |
15,0 |
Давление низа колонны |
кгс/см2 |
11,11 |
|
Температура верха колонны |
°Ⅽ |
42,0 |
150,0 |
Температура низа колонны |
°Ⅽ |
96,3 |
Наиболее предпочтительным является регулирование давления фракционирующего абсорбера.
Полученная модель позволила оценить эффективность процесса разделения газов фракционирующего абсорбера К-51. Зафиксированные значения массовых расходов С 3 -С 4 , при различных сценариях изменений давления в колонне К-51, представлены в таблицах 3-4 (* в таблицах отмечены оптимальные значения параметров).
В таблице 3 представлены результаты расчета программы по значениям массового выхода жирного газа и изменение массовых расходов с укрепляющей (12 поток) и кубовой (17 поток) части фракционирующего абсорбера при изменении дав- лении на 1 кгс/см2 с постоянным перепадом давления. Исходя из полученных результатов следует, что увеличение давления приводит к уменьшению содержания смеси ППФ и
ББФ в сухом газе.
Исходя из значений таблицы 4 можно сделать вывод, что увеличение давления приводит к повышению концентрации целевых компонентов в кубе колонны и уменьшению массового расхода верхнего продукта колонны, что коррелирует со снижением потерь целевых компонентов. Прослеживается динамика увеличения массового расхода с куба колонны по жирному газу и другим компонентам.
Таблица 3. Зависимость массового выхода и расхода С 3 -С 4 от давления в К-51
Параметр |
Вариант № |
||||
1 |
2 |
3* |
4 |
5 |
|
Давление верха, кгс/см2 |
11,7 |
12,7 |
13,7 |
14,7 |
15,7 |
Давление низа, кгс/см2 |
12,1 |
13,1 |
14,1 |
15,1 |
16,1 |
Массовый выход С 3 -С 4 с верха, % |
21,80 |
14,54 |
8,08 |
7,44 |
6,90 |
Массовый выход С 3 -С 4 с низа, % |
20,57 |
21,23 |
21,66 |
21,63 |
21,60 |
Массовый расход с верха, кг/ч |
12052,32 |
10658,5 |
9472,49 |
8812,55 |
8208,09 |
Массовый расход с низа, кг/ч |
121596,4 |
122988,17 |
124174,44 |
124834,67 |
125439,03 |
Таблица 4. Зависимость массового выхода и расхода С 3 -С 4 от давления в К-51
Параметр |
Вариант № |
||||
1 |
2 |
3* |
4 |
5 |
|
Давление верха, кгс/см2 |
11,7 |
12,7 |
13,7 |
14,7 |
15,7 |
Давление низа, кгс/см2 |
12,1 |
13,1 |
14,1 |
15,1 |
16,1 |
Массовый выход С 3 -С 4 в потоке 12, % |
21,80 |
14,54 |
8,08 |
7,44 |
6,90 |
Массовый выход других компонентов в потоке 12, % |
78,20 |
85,46 |
91,92 |
92,56 |
93,10 |
Массовый расход С 3 -С 4 в потоке 12 , кг/ч |
2627,41 |
1549,26 |
765,42 |
655,51 |
566,28 |
Массовый расход других компонентов в потоке 12, кг/ч |
9424,91 |
9109,25 |
8707,07 |
8157,03 |
7641,81 |
Массовый расход С 3 -С 4 в потоке 17, кг/ч |
25016,38 |
26116,01 |
26894,71 |
27000,88 |
27091,67 |
Массовый расход других компонентов в потоке 17, кг/ч |
96580,01 |
96872,16 |
97279,73 |
97833,80 |
98347,37 |
После моделирования был проанализирован количественный и качественный состав газа, уходящего с верха газофракционирующего абсорбера. Как видно из рисунка 2 и таблиц, представленных выше, изменение давления с укрепляющей и от- гонной части колонны К-51, при неизменном градиенте давлений, позволяет улучшить абсорбцию жирных компонентов газа, в следствии чего уменьшить потери С3-С4 вместе с сухим газом.
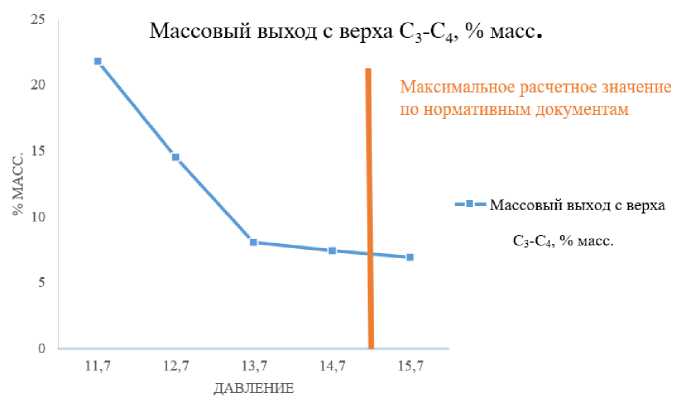
Рис. 2. График зависимости изменения процентного содержания выхода С 3 -С 4 с верха колонны от давления
Таким образом, можно утверждать, что оптимальное разделение без увеличения диаметра фракционирующего абсорбера достигается при давлении 13,7 кгс/см2, и входит в интервал расчетных технологических параметров данной колонны согласно допустимым нормам по проекту. Массовый выход С3-С4 с верха колонны при уве- личении давления до 13,7 кгс/см2 уменьшается на 13,72% масс., а расход кубового продукта – на 2579,83 кг/ч, одновременно с этим, выход С3-С4 с куба абсорбера увеличится на 1% масс., а расход соответственно на 2578,04 кг/ч. Данное давление можно считать оптимальным, так как при дальнейшем повышении давления наблю- дается незначительное повышение качества разделения, однако нагрузка на оборудование и энергозатраты значительно увеличиваются.
«Башнефть-Уфанефтехим» позволяет создавать давление в колонне К-51 11,2 кгс/см2, поэтому необходима его замена. Затраты при этом будут на порядок ниже замены самого фракционирующего абсорбера на установке.
Действующий компрессор на установке 1-А/1М Филиала ПАО АНК «Башнефть»
Список литературы Интенсификация процесса разделения газов каталитического крекинга
- Анищук Е.А. Модернизация газофракционирующего блока установки каталитического крекинга / Е.А. Анищук, А.В. Ганцев // Новые технологии - нефтегазовому региону: материалы Международной научно-технической конференции: в 2 т. - Тюмень: ТИУ, 2016. 2 т. - С. 148-150. EDN: VYCMJL
- Ахметов С.А. и др. Технология и оборудование процессов переработки нефти и газа: Учебное пособие / С.А. Ахметов, Т.П. Сериков, И.Р. Кузеев, М.И. Баязитов; Под ред. С.А. Ахметова. - CПб.: Недра, 2006. - 868 с.
- Задегбейджи Р. Каталитический крекинг в псевдоожиженном слое катализатора. Справочник по эксплуатации, проектированию и оптимизации установок ККФ: пер. с англ. яз. 3-го изд; под ред. О.Ф. Глаголевой. - СПб.: ЦОП "Профессия", 2014. - 384 с.
- Информационно-технический справочник по наилучшим доступным технологиям ИТС 30-2017 "Переработка нефти". - [Электронный ресурс]. - Режим доступа: https://www.rst.gov.ru/portal/gost/home/activity/NDT/sprav_NDT_2017 (дата обращения 09.10.2023).
- ЛакПром. Нефтехимический комплекс. - [Электронный ресурс]. - Режим доступа: http://lkmprom.ru/analitika/neftekhimicheskiy-kompleks-zadachi-i-perspektivy/ (дата обращения 09.10.2023).
- Мейерс Р.А. Основные процессы нефтепереработки. Справочник: пер. с англ. 3-го изд. / Р.А. Мейерс и др.; под ред. О.Ф. Глаголевой, О.П. Лыкова. - СПб.: ЦОП "Профессия", 2011. - 944 с. EDN: QNFIGB
- Мясин Я.О., Мясина Е.А., Ганцев А.В., Мустафин И.А. Повышение эффективности разделения продуктов каталитического крекинга в результате моделирования и анализа работы газофракционирующих блоков // Башкирский химический журнал. - 2017. - Том 24. № 3. - С. 77-84. EDN: ZJSCPZ
- Рид Р., Праусниц Дж., Шервуд Т. Свойства газов и жидкостей: Справочное пособие / Пер. с англ. под ред. Б.И. Соколова. - Л.: Химия, 1982. - 592 с.