Использование высокотемпературных порошковых никелевых припоев в качестве износостойких наплавок на торец пера лопатки турбины
Автор: Климов Вадим Геннадьевич, Жаткин Сергей Сергеевич, Баранов Дмитрий Александрович, Дяговцов Игорь Анатольевич, Хакимов Алексей Мунирович
Журнал: Известия Самарского научного центра Российской академии наук @izvestiya-ssc
Рубрика: Машиностроение и машиноведение
Статья в выпуске: 1-2 т.18, 2016 года.
Бесплатный доступ
В статье рассматривается возможность использования высокотемпературных порошковых припоев в качестве износостойких слоев, наносимых лазерной импульсной наплавкой, как альтернатива классическим износостойким композитам с примесью карбида вольфрама. Данные материалы апробируются для последующего восстановления высоты пера лопатки турбостартера турбовинтового авиационного двигателя НК-12МП и придания торцевой кромке износостойких свойств. На основе проведенных сравнительных испытаний на локальный абразивный износ и анализа различных порошковых материалов (ВПр11-40Н, ВПр24, ВПр27, Рок-Дюр 6740) при импульсной лазерной порошковой наплавке подтверждена пригодность некоторых порошковых припоев в качестве износостойких наплавок.
Лазерная наплавка, самофлюсующиеся припой, порошковая ванна, микротвердость, электронная микроскопия, абразивный износ
Короткий адрес: https://sciup.org/148204371
IDR: 148204371
Текст научной статьи Использование высокотемпературных порошковых никелевых припоев в качестве износостойких наплавок на торец пера лопатки турбины
Наплавка как метод нанесения покрытий с определенными физико-механическими свойствами остается наиболее актуальным и распространенным методом для повышения ресурса работы деталей машин. На данный момент существуют различные способы восстановления геометрии лопаток газотурбинных двигателей (ГТД). Весьма распространен метод дуговой наплавки, описанный ещё в 1976 г. в работах И.А. Перми-ловского (ИЭС им. Е.О. Патона.) , в 2000 г. в патенте В.И. Колосова (ОАО «Пермский моторный завод»), в работе 2004 г. Л.И. Сорокина (ФГУП «ВИАМ») [2-5]. Несмотря на доступность данного метода, он не лишен ряда недостатков, таких как большая зона термического влияния и сложность при наплавке краевых элементов. Вследствие этого дуговая наплавка в среде защитного газа не получила широкое распространение при восстановлении дефектных мест жаропрочных лопаток из литейных сплавов типа ЖС. По причине перегрева лопатки от электрической дуги в зоне термического влияния образуется область обильной коагуляции и растворения упрочняющей γ'-фазы, что приводит к разупрочнению материала подложки и образованию трещин, как в процессе наплавки, так и при последующей работе [1]. Способы борьбы с данной проблемой были описаны в работе Л.И. Сорокина (ФГУП «ВИАМ»), но также даже самим автором отмечается сложность применения подобной технологии, что ограничивает её использование на производстве [6].
Альтернативным способом борьбы с износом деталей газовой турбины стала пайка высокотемпературными припоями в среде защитных газов или вакуума, что позволяет исключить образование трещин в области исправления дефекта [7, 8]. Объясняется это
Дяговцов Игорь Анатольевич, инженер бюро пайки Хакимов Алексей Мунирович, студент тем, что пайка происходит при температуре ниже структурных преобразований жаропрочных никелевых литейных сплавов. На сегодняшний момент большинство крупных зарубежных компаний и отечественных производств успешно используют высокотемпературную пайку в защитных средах для ремонта узлов газовых турбин таких как рабочие лопатки, сопловые аппараты и других детали горячего тракта [9, 10].
Процесс пайки с общим нагревом происходит следующим образом: производят разделку дефектного места и подготовку поверхности основного материала под пайку. В разделку помещают порошок припоя на никелевой основе или смесь с порошком основного материала в виде пасты, замешанной с использованием 5%-ного раствора акриловой смолы БМК-5 на ацетоне. Затем осуществляется нагрев в печи с защитной атмосферой до температуры плавления припоя и определенной выдержкой. Стоит также обратить внимание, что при диффузионной пайке в вакууме из-за длительного термического цикла жаропрочность и пластичность поверхностного слоя основного материала детали горячего тракта снижаются, что, в свою очередь, снижает срок ее эксплуатации [10].
В настоящее время в промышленность внедряются технологии восстановительной на-плавки, ранее не имевшие широкого распространения. Одной из таковых является лазерная наплавка, для которой характерна наименьшая зона термического воздействия среди всех остальных способов восстановления рабочих поверхностей деталей машин. В этой работе в исследованиях использовались лопатки, полученные методом литья в керамические оболочковые формы с равноосной кристаллизацией из сплава ЖС6-К (ТУ 1809-1025-98, табл. 1).
Износ лопатки турбостартера (ТС) происходит по торцу пера лопатки и имеет абразивный характер, согласно ранее опубликованным материалам [11]. На основании вышесказанного при восстановлении геометрии пера была поставлена задача повышения стойкости его верхней кромки к абразивному изнашиванию. На входе в турбину стартера турбовинтового двигателя НК-12МП температура составляет около 900оС. Поэтому, учитывая невысокие температурные нагрузки на торец пера лопатки ТС, в качестве материала для его восстановления были выбраны порошковые высокотемпературные никелевые припои типа ВПр, разработанных ФГУП «ВИАМ» (г. Москва), и композитный порошковый материал из серии «Сфекорд Рок-Дюр» производства ООО «СП Техникорд» (г. Москва). В работе рассмотрена возможность использования высокотемпературных никелевых припоев в качестве материала для износостойких наплавок, как альтернатива классическим композитам с примесью карбида вольфрама.
Методика исследований. В работе описана наплавка следующих порошковых материалов:
-
- ВПр11-40Н (ТУ 1-809-108-91). Самофлюсующийся композитный порошковый литой высокотемпературный припой на основе никеля, дисперсностью 100-250 мкм (табл. 1). Припой ВПр11-40Н является механической смесью припоя ВПр11 (60%) и наполнителя (40%) на никелевой основе с незначительными добавками других элементов. Температура плавления 980-1020оС. Обладает высоким уровнем самофлюсации.
-
- ВПр24 (ТУ 1-595-4-1218-2011). Самофлюсующийся порошковый литой высокотемпературный припой на основе никеля, дисперсностью 100-315 мкм (табл. 1). Температура плавления 1150-1190оС.
-
- ВПр27 (ТУ 1-595-4-1218-2011). Самофлюсующийся порошковый литой высокотемпературный припой на основе никеля, дисперсностью 100-315 мкм (табл. 1). Температура плавления 1030-1080ºС.
-
- Рок-Дюр 6740 (ТУ 1526-001-86297481-2008). Композиционный материал на основе сплава Ni с литым карбидом вольфрама (WC-W 2 C), плакированного сплавом на основе Ni. Температура плавления 980-1050 ºС. По утверждению производителя обладает высокой абразивной износостойкостью в сочетании с сопротивлением давлению, механическим и тепловым ударам, коррозии и кавитации.
Морфология используемых в наплавке порошков представлена на рис. 1.
Таблица 1. Классификация и рабочая температура материалов
Материал |
ГОСТ, ТУ |
Классификация |
Основные компоненты |
Рабочая температура, оС |
ЖС6-К |
ТУ 1-809-1025-98 |
жаропрочный литейный сплав |
Ni-Cr-Al-W-Mo-Co-Ti-Si-C |
до 1000 |
ВПр11-40Н |
ТУ 1-809-108-91 |
высокотемпературный порошковый припой |
60% (Ni-Cr-Al-Fe-Co-B-Si-C) + 40% (Ni-B-Si) |
до 900 |
ВПр24 |
ТУ 1-809-838-89 |
высокотемпературный порошковый припой |
Ni-Co-Cr-Nb-W-Al-Mo-Ti-Si-B-C |
до 1050 |
ВПр27 |
ТУ 1-595-4-1021 2007 |
высокотемпературный порошковый припой |
Ni-Co-Cr-W-Si-Mo-Al-Nb-B-C |
До 1000 |
Рок-Дюр 6740 |
ТУ 1526-00186297481-2008 |
композиционный материал на основе сплава Ni с литым карбидом вольфрама. |
60% (Ni-Cr-B-Si-C) + 40% [88(WC-W 2 C) + 12% (Ni-Cr-B-Si-C)] |
До 700 |
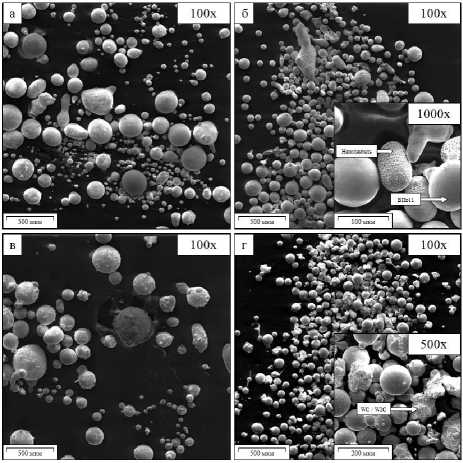
Рис.1. Морфология порошков: а – ВПр27; б – ВПр11-40Н; в – ВПр24; г – Рок-Дюр 6740
Импульсная лазерная наплавка производилась на установке ALFA-300 (производство ООО «Лазер-Форм», г. Зеленоград, Россия). Наплавка проводилась помещением пера лопатки в ванну с наплавляемым порошком. Лопатка размещалась в порошковой насыпи так, чтобы ее перо и поверхность порошковой насыпи находились на одном уровне [11].
Восстановленные зоны и сам порошковый материал исследовались на электронном микроскопе Tescan (Чехия) VEGA3 LM c модулем Oxford instruments X-Max, а измерения твердости проводились на микротвердомере «EMCO-TEST PrufmaSchinen GmbH» (Австрия) DuraScan-10 на базе центральной заводской лаборатории (ЦЗЛ) предприятия ПАО «Кузнецов». Испытания на абразивный износ были проведены в лаборатории «Наноструктурированных покрытий» СамГТУ на установке Универсал-1А, собранной на базе сверлильного станка СС-13/350, обеспечивающей через систему датчиков и средств регистрации непрерывный контроль нормальной нагрузки и момента трения.
Результаты исследований. На рис. 2 представлена лопатка ТС двигателя НК-12МП, восстановленная лазерной порошковой наплавкой после эксплуатации и механического износа по торцу пера (а), а также восстановленная лопатка после механической обработки и травления для выделения наплавленного слоя (б).
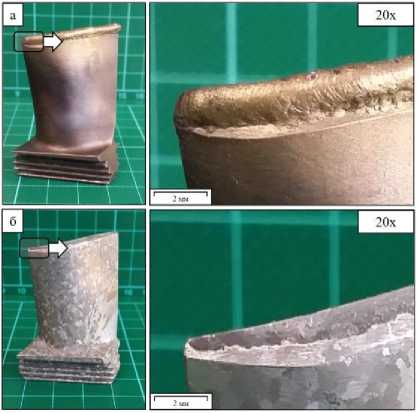
Рис. 2. Лопатка ТС двигателя НК-12МП: а – восстановленная лазерной порошковой наплавкой после эксплуатации и механического износа по торцу пера; б – восстановленная лопатка после механической обработки и травления для выделения наплавленного слоя
Важным элементом конструкции турбостартера является металлокерамическая вставка как ответная часть к перу лопатки и имеющая твердость 46-94 HV по Викерсу. Вставку получают методом порошкового спекания с использованием графитового и никелевого порошка, а также кремния. При сборке зазор между лопаткой и вставкой выдерживается на уровне 0,6-0,8 мм. Однако при выходе на рабочую температуру (900оС) за счет теплового расширения и центробежной силы зазор между лопаткой и вставкой уменьшается практически до нуля.
Кроме того, при длительном воздействии температуры твердость вставки многократно возрастает -в отработанной металлокерамике твердость отдельных участков возрастает до 58 HRC (690-720 Hv). Как показал анализ отработанных лопаток, перо лопатки имеет механический абразивный износ, о чем свидетельствуют явно выраженные острые края изношенных областей. На рис. 2 представлена микроструктура образцов восстановленных лопаток ТС.
Зоны наплавки припоев ВПр11-40Н и ВПр24 имеют схожую структуру, представляющую сеть мелких аустенитных зерен на основе никеля размерами не более 10 мкм (рис. 3а, 3б), по границам которых распределяются мелкодисперсные интерметаллиды на основе Cr, W и Nb. При наплавке ВПр27 формируется ещё более мелкая структура, также схожая со структурой материалов, описанных выше. Из анализа микроструктуры можно сделать вывод, что лазерное излучение как метод нанесения покрытия, формирует мелкодисперсную структуру наплавляемого порошкового материала припоев с предположительно интерметал-лидной и карбидной сеткой и минимальным влиянием на структуру основного материала подложки (лопатки ТС). Наплавка композитного порошка Рок-Дюр 6740 формирует структуру с более выделенными в размере карбидами (WC / W 2 C) размером порядка 20-80 мкм и равнораспределенной эвтектикой W по Ni-Co матрице, образовавшийся в результате распада карбида. В табл. 2 приведены результаты измерения микротвердости подготовленных шлифов наплавок на лопатки ТС.
Зоны наплавки припоев ВПр11-40Н и ВПр24 имеют схожую структуру, представляющую сеть мелких аустенитных зерен на основе никеля размерами не более 10 мкм (рис. 3а, 3б), по границам которых распределяются мелкодисперсные интерметаллиды на основе Cr, W и Nb. При наплавке ВПр27 формируется ещё более мелкая структура, также схожая со структурой материалов, описанных выше. Из анализа микроструктуры можно сделать вывод, что лазерное излучение как метод нанесения покрытия, формирует мелкодисперсную структуру наплавляемого порошкового материала припоев с предположительно интерметал-лидной и карбидной сеткой и минимальным влиянием на структуру основного материала подложки (лопатки ТС). Наплавка композитного порошка Рок-Дюр 6740 формирует структуру с более выделенными в размере карбидами (WC / W 2 C) размером порядка 20-80 мкм и равнораспределенной эвтектикой W по Ni-Co матрице, образовавшийся в результате распада карбида. В табл. 2 приведены результаты измерения микротвердости подготовленных шлифов наплавок на лопатки ТС.
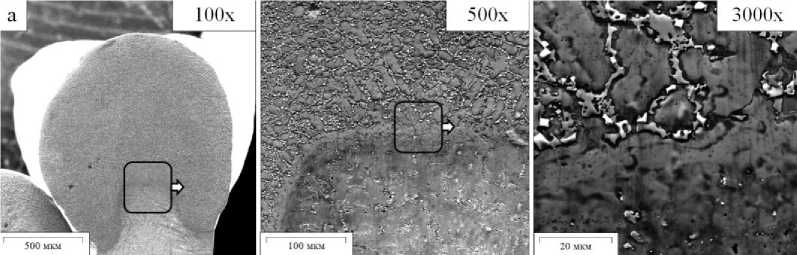
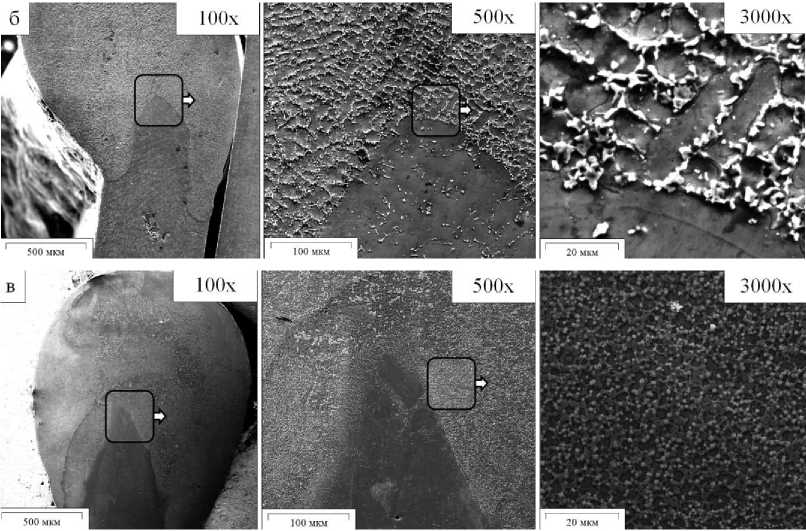
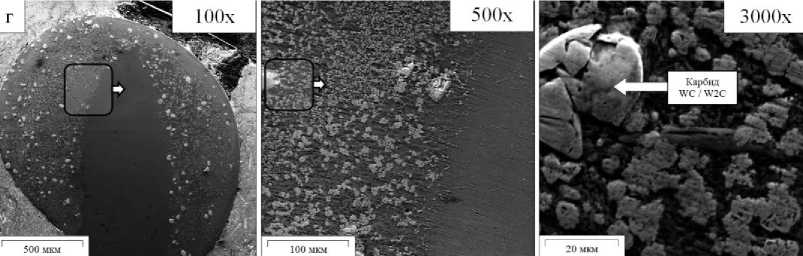
Рис.3. Микроструктура зон лазерной импульсной наплавки при восстановлении лопатки ТС: а – наплавка порошка ВПр11-40Н; б – наплавка порошка ВПр24; в – наплавка порошка ВПр27; г – наплавка порошка Рок-Дюр 6740
Таблица 2. Показания твердости порошковой наплавки
Материал |
ВПр11-40Н |
ВПр24 |
ВПр27 |
Рок-Дюр 6740 |
средняя твердость по площади наплавки, HV |
490 – 510 |
690 – 740 |
400 – 690 |
330 – 390 |
тип упрочняющей фазы |
интерметаллиды и карбиды на основе Сr |
интерметаллиды на основе Cr, W и Nb |
интерметаллиды на основе Cr и W |
карбид вольфрама (WC / W 2 C) |
твердость упрочняющей фазы, HV |
невозможно точно определить ввиду малого размера фазы |
1500 – 2300 |
После наплавки высокотемпературных порошковых припоев наблюдался существенно меньший разброс в распределении твердости по всей толщине наплавки по сравнению с износостойким материалом Рок-Дюр 6740, что обусловлено образованием в наплавленной зоне мелкодисперсной структуры, содержащей интерметаллиды и мелкие карбиды.
Восстановленные лазерной наплавкой лопатки подвергались механической обработке для придания ей первоначального профиля. По результатам рентгеновского и люминесцентного контроля восстановленных лопаток, проведенных в лаборатории НМК предприятия ПАО «Кузнецов» не было выявлено ни внешних (трещины), ни внутренних дефектов (поры, несплавления). Испытания на абразивный износ проводились локально в участке зоны наплавки, материал контртела – трубка из стали 40Х (закалка до HRC 46-48) с внешним диаметром 6 мм и толщиной стенки 1 мм. Испытания проводились при нормальной нагрузке в 30 кгс в течение 15 минут с частотой вращения шпинделя 600 об/мин. При испытаниях использовалась алмазная паста АСМ-3/2-НОМГ, соответственно износ образца осуществлялся алмазным порошком дисперсностью 2-3 мкм. Площадь трения составляла 1,57*10-5м2.
На основании проведенных испытаний установлено (табл. 3), что приемлемой износостойкостью обладают порошковые припои ВПр11-40Н и ВПр27, сравнимой со стойкостью карбидосодержащего материала Рок-Дюр 6740. Стоит также учесть, что после обработки шлифованием припуска наплавки остается относительно небольшая зона износостойкого слоя. В случае использования для реставрации геометрии тела лопатки материала Рок-Дюр 6740 его неравномерно распределенная карбидная фаза (WC / W2C) может оказаться в малом количестве в износостойком слое, что снизит общую стойкость восстановленной кромки. Формируемая мелкодисперсная структура и равнорас-пределённая по площади наплавки упрочняющая фаза в жаропрочных никелевых припоях позволяет сохранить общую стойкость к износу кромки пера лопатки ТС после шлифования.
Таблица 3. Скорость локального абразивного изнашивания материалов
Материал |
Скорость износа, мкм/час |
Время проведения испытаний, мин |
ЖС6-К (основной материал лопатки ТС) |
323,5 ± 31 |
15 |
ВПр11-40Н |
114,5 ± 11 |
|
ВПр24 |
473,5 ± 32 |
|
ВПр27 |
236 ± 50 |
|
Рок-Дюр 6740 |
161,5 ± 15 |
Выводы:
-
1. Формируемая структура жаропрочных никелевых припоев при лазерной импульсной наплавке обладает равнораспределенной твердостью по площади всего нанесенного слоя.
-
2. По результатам проведенных испытаний на локальный абразивный износ установлено, что припои ВПр11-40Н и ВПр27 обладают приемлемой износостойкостью, сравнимой со свойствами классического износостойкого материала Рок-Дюр 6740 с включениями карбида вольфрама (WC / W 2 C).
-
3. Формируемая мелкодисперсная структура и рав-нораспределённая по площади восстановленного слоя
упрочняющая фаза в жаропрочных никелевых припоях ВПр11-40Н и ВПр27 предположительно позволит сохранить общую стойкость к износу кромки пера лопатки в работе, даже при небольшом объеме наплавки после удаления припуска.
Список литературы Использование высокотемпературных порошковых никелевых припоев в качестве износостойких наплавок на торец пера лопатки турбины
- Петрушин, Н.В. Структура и свойства монокристаллов жаропрочного никелевого сплава, содержащего рений и рутений/Н.В. Петрушин, Е.С. Елютин, P.M. Назаркин и др.//Металлургия машиностроения. 2013. №1. С. 12-18.
- Пермиловский, И.А. Восстановление наплавкой турбинных лопаток авиационных двигателей/И.А. Пермиловский, В.С. Гейченко, И.И. Фруман//Автоматическая сварка. 1976. №5. С. 54-56.
- Пермиловский, И.А. Физико-механические свойства наплавленных карбидохромовых сплавов/И.А. Пермиловский, Н.А. Казанцева//Автоматическая сварка. 1976. №4. С. 52-54.
- Пат. 2153965 РФ. Способ восстановления длины пера лопаток компрессора газотурбинного двигателя и устройство для его осуществления/Колосов В.И. Бюл. 2000. №1.
- Сорокин, Л.И. Аргонодуговая наплавка бандажных полок рабочих лопаток из высокожаропрочных никелевых сплавов//Сварочное производство. 2004. № 7. С. 20-26.
- Сорокин, Л.И. Свариваемость жаропрочных никелевых сплавов типа ЖС6/Л.И. Сорокин, В.И. Лукин, Ю.С. Багдасаров//Сварочное производство. 1997. № 6. С. 12-17.
- Корниенко, А.Н. Состояние и проблемы внедрения пайки для ремонта лопаток газотурбинных двигателей/А.Н. Корниенко, А.М. Жадкевич//Заготовительные производства в машиностроении. 2005. № 10. С. 9-12.
- Квасницкий, В.Ф. Сварка и пайка жаропрочных сплавов в судостроении. -Л.: Судостроение, 1986. 224 с.
- Ключников, И.П. Ремонт высоконагруженных деталей и узлов горячего тракта ГТД методом высокотемпературной пайки/И.П. Ключников, В.А. Гейкин/Пайка. Современные технологии, материалы, конструкции. -М.: ЦРДЗ, 2001. Т. 2. С. 19-24.
- Орлов А.В. Ремонт деталей газовых турбин методами пайки/А.В. Орлов, Ю.Н. Березников, Т.С. Самсонова//Энергомашиностроение. 1984. № 2. С. 33-34.
- Климов, В.Г. Особенности восстановления геометрии пера газотурбинного двигателя методом лазерной порошковой наплавки/В.Г. Климов, С.С. Жаткин, Е.Ю. Щедрин, А.В. Когтева//Известия Самарского научного центра Российской академии наук. 2015. Т. 17, №2(4). С. 782-788.