Исследование износостойких электрометаллизационных покрытий из порошковых проволок с минеральными модифицирующими добавками
Автор: Лебедев М.П., Винокуров Г.Г., Кычкин А.К., Стручков Н.Ф., Лебедев Д.И.
Журнал: Известия Самарского научного центра Российской академии наук @izvestiya-ssc
Рубрика: Недра и их использование
Статья в выпуске: 1-2 т.11, 2009 года.
Бесплатный доступ
Проведены сравнительные исследования химического и фазового состава, структуры и микротвердости газотермических покрытий из экспериментальных порошковых проволок с модифицирующими минеральными добавками. Изученные закономерности изнашивания покрытий из порошковых проволок при трении скольжения показали возможность использования минеральных ассоциаций из месторождений Республики Саха (Якутия) в качестве добавок в износостойкие порошковые материалы для получения покрытий с повышенными эксплутационными свойствами.
Минеральные добавки, порошковые материалы, эксплуатационные свойства
Короткий адрес: https://sciup.org/148198296
IDR: 148198296
Текст научной статьи Исследование износостойких электрометаллизационных покрытий из порошковых проволок с минеральными модифицирующими добавками
Разработка и применение высокоинтенсивных технологических процессов обеспечивают использование сложных комплексных руд и многообразных отходов горнодобывающего производства для создания материалов многоцелевого назначения. Поэтому актуальными являются новые подходы к переработке и применению минерального сырья для получения материалов и покрытий, основанные на воздействии на минералы концентрированных потоков энергии (наплавка, элек-трошлаковый переплав, плазменно-дуговая обработка и др.), позволяющих в одном цикле восстанавливать природные оксиды и синтезировать новые соединения.
Целью данной работы является установление особенностей формирования состава, структуры и свойств износостойких
электрометаллизационных покрытий из порошковых проволок с минеральными модифицирующими добавками, выявление закономерностей процессов их изнашивания при трении скольжения.
В работе проведено комплексное исследование основных факторов, определяющих износостойкость электроме-таллизационных покрытий с минеральными модифицирующими добавками: химического и фазового состава, микротвердости и структуры покрытия; выявлены закономерности процессов изнашивания поверхности трения. Основным материалом шихты порошковой проволоки был выбран промышленный порошок ПГ-СР4, который широко применяется для получения износостойких порошковых покрытий. В качестве модификаторов износостойкого порошкового покрытия были использованы комплексные концентраты Нижне-Куранахского (содержание: оксиды TiO 2 – 20%, Nb 2 O 5 – 4,1% и триоксиды редкоземельных металлов от 4% до 8% масс.) и редкоземельного Томтор-ского (содержание: Nb 2 O 5 от 5,03% до 13,56%, триоксиды редкоземельных металлов от 15,45% до 31,03% масс.) месторождений Республики Саха (Якутия).
Порошковая шихта с минеральными модифицирующими добавками измельчалась и просеивалась на фракцию с дисперсностью от 40 мкм до 200 мкм на пробоподготовительном комплексе. Были подготовлены порошковые шихты с добавками ильменитового концентрата от 8% до 20% по массе (составы №2 – 4), с добавками редкоземельного концентрата от 3% до 9% по массе (составы №5 – 7) и контрольный состав порошковой шихты без минерального сырья (состав №1). Перед изготовлением порошковой проволоки подготовленные шихты смешивались в установке типа «пьяная бочка» в течение 1 часа до получения однородной смеси. В качестве оболочки порошковой проволоки использовалась лента листовой стали Ст 08 кп (ГОСТ 1050-88) толщиной 0,4 мм и шириной 9 мм. Изготовление порошковой проволоки диаметром 1,8 мм проведено на промышленном стане по технологическим режимам, учитывающим скорость подачи шихты в стальную ленту оболочки для обеспечения требуемого коэффициента порошковой набивки.
В качестве подложек покрытий использовались образцы для испытания на износ из конструкционной стали Ст3, которые проходили предварительную подготовку дробеструйной обработкой и обезжириванием. Покрытия были нанесены электродуговой металлизацией поверхности образцов порошковыми проволоками на промышленной установке ЭДУ-500С. Для исследования состава, структуры, свойств были изготовлены поперечные металлографические шлифы покрытий. Средние значения химического состава покрытий определены по данным спектрального анализа на установке «WAS Foundry-Master»; металлографические исследования структуры проведены на микроскопе «Neophot-32»; микротвердость покрытий измерена на приборе «ПМТ-3М». Рентгеноструктурные исследования фаз покрытия проведены на установке ДРОН-3 с использованием монохроматического CuKα-излучения. Испытания на износ покрытий проводились на машине трения СМЦ-2; на основе анализа работ и методик испытаний на износ была выбрана схема трения «диск-колодка»; износ определялся весовым способом. Режимы испытаний на износ: нагрузка – 38 кГ; частота вращения вала – 5 об/сек; трение сухое. Для измерения шероховатости поверхности трения на каждом образце были промаркированы четыре диаметрально противоположных участка покрытия. Шероховатость поверхности трения определялась с помощью профилометра SJ-201P фирмы «Mitutoyo» (Япония). Измерение шероховатости проводилось на каждом из 4-х участков, затем данные усреднялись по всей поверхности трения.
Для формирования упрочняющих фаз определяющее значение имеет химический состав порошкового покрытия. При добавлении минеральных ассоциаций в состав проволок среднее содержание углерода в покрытиях повышается от 0,22% до 0,57%. В покрытиях из порошковых проволок содержание углерода определяет склонность к образованию карбидов железа, хрома, вольфрама, кремния – упрочняющих фаз с высокой твердостью. Высокое содержание никеля (≈ 20% и более) в покрытиях из порошковых проволок указывает на более высокий температурный запас вязкости и меньшую склонность к хрупкому разрушению. Все карбидные фазы покрытий обладают высокой температурой плавления и высокой твердостью. Следует отметить, что фазы внедрения покрытий трудно растворимы; даже при очень высоком нагреве они могут не перейти в твердый раствор. Силициды обеспечивают защиту от окисления и жаропрочность; интерметаллиды, найденные во всех покрытиях, также обеспечивают их упрочнение. С целью выявления особенностей структуры покрытий из порошковых проволок проведен их металлографический анализ. При электродуговой металлизации формирование покрытия происходит наложением расплавленных частиц, состоящих из фаз оболочки и порошковой набивки. Тугоплавкие компоненты порошкового материала выделяются в виде отдельных нерасплавленных частиц, все покрытия из проволок характеризуются неоднородной микроструктурой и состоят из множества отдельных фаз.
Установлено, что в отличие от технологий напыления порошкообразного материала, электродуговая металлизация порошковых проволок приводит к более сложным формам частиц покрытия, отклоняющимся от сферической и эллипсоидальной; сечения частиц имеют преимущественно лентообразный изогнутый вид. Составы покрытий имеют сложную внутреннюю структуру, состоящую из изогнутых лентообразных прослоек различных оттенков; также наблюдаются круглые фазовые включения разного диаметра и оттенка. Отмеченные особенности микроструктуры отражаются на значениях микротвердости покрытий, зависящих от количества, состава, распределения фаз, особенностей внутреннего микростроения слоев, образованных расплавленными и кристаллизовавшимися частицами. Как показал анализ структуры покрытий, для более полного расплавления модифицирующей добавки из ильменитового концентрата при электродуго-вой металлизации необходимо уменьшить дисперсность фракционного состава (ниже 100 мкм).
Испытаниями на износ установлено, что на стадии приработки контактных поверхностей, до ≈ 150000 - 20000 циклов машины трения (по выбранной схеме трения один цикл соответствует пути трения, равному 1,96×10-2 м), интенсивность изнашивания нестабильна, что объясняется изменением фактической площади контакта, увеличение и стабилизация которой определяют наступление режима установившегося износа. Поэтому по тангенсу угла наклона прямой установившегося массового износа для всех покрытий с минеральными модифицирующими добавками были определены интенсивности установившегося изнашивания (рис. 1). Как видно из графика, для получения износостойких покрытий наиболее перспективными являются ильменитовые и редкоземельные минеральные модифицирующие добавки с малой концентрацией (менее 8% и 3% по массе соответственно).
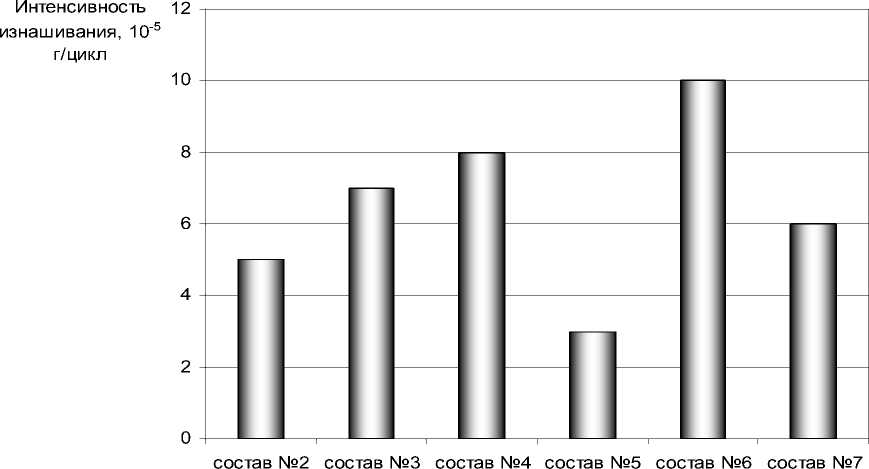
Рис. 1. Интенсивности изнашивания покрытий из порошковых проволок с минеральными добавками
Профилометрическими измерениями выявлено, что механизм процесса истирания покрытий из порошковых проволок с модифицирующими минеральными добавками состоит в постепенном уменьшении размера выемок на поверхности трения с ее сглаживанием, что приводит к колебаниям средней шероховатости поверхности трения.
Выводы:
-
1. Электродуговой металлизацией получены износостойкие покрытия из экспериментальных порошковых проволок с модифицирующими минеральными добавками. Химический состав порошковых проволок с минеральными модифицирующими добавками способствует формированию многофазных покрытий, содержащих бориды, карбиды, силициды, интер-металлиды и др.; анализом фаз обнаружено дисперсионное упрочнение покрытий в результате образования карбидов.
-
2. Минеральные модифицирующие добавки значительно сужают интервал распределения микротвердости покрытий из порошковых проволок и не приводят к большей неоднородности микроструктуры покрытий. По результатам анализа структуры покрытий, для более полного расплавления модифицирующей добавки из ильменитового концентрата при электро-дуговой металлизации необходимо умень-
- шение дисперсности фракционного состава (ниже 100 мкм).
-
3. Испытания в условиях трения скольжения показали, что для всех покрытий наблюдаются практически одинаковые характерные участки приработки и установившегося износа. Механизм процесса истирания покрытий из порошковых проволок с модифицирующими минеральными добавками состоит в чередовании процессов появления все мелких выемок на поверхности трения и их сглаживания, что приводит к колебаниям средней шероховатости поверхности трения. Для получения износостойких покрытий наиболее перспективными являются ильменитовые и редкоземельные минеральные модифицирующие добавки с малой концентрацией (менее 8% и 3% по массе соответственно).
Работа выполнена при поддержке инновационного проекта № 6781 Фонда содействия развитию малых форм предприятий в научно-технической сфере в рамках программы СТАРТ.
RESEARCH THE WEARPROOF ELECTROMETALICCOATINGS FROM POWDER WIRES WITH MINERALMODIFYING ADDITIVES