Исследование процесса лазерной сварки стали У10А
Автор: Горяинов Дмитрий Сергеевич, Балакиров Сергей Николаевич, Гусев Александр Алексеевич
Журнал: Известия Самарского научного центра Российской академии наук @izvestiya-ssc
Рубрика: Машиностроение и машиноведение
Статья в выпуске: 4-2 т.18, 2016 года.
Бесплатный доступ
В статье приведены результаты исследования лазерной точечной сварки образцовиз высокоуглеродистой стали У10А. Установлено, что максимальная прочность сварного соединения достигается при принудительном охлаждении сварного шва газово-аэрозольной смесью Ar2+H2O.Прочность сварного шва образцов из стали Ст3 не зависит от коэффициента теплоотвода.
Конечно-элементное моделирование, сварной шов, остаточные напряжения, микротвёрдость
Короткий адрес: https://sciup.org/148204675
IDR: 148204675
Текст научной статьи Исследование процесса лазерной сварки стали У10А
Был проведен анализ различных способов образования неразъемных соединений высокоуглеродистых сталей. Из рассмотренных методов чаще всего используют электронно-лучевую, электрошлаковую, плазменную, газовую, лазерную и контактные способы сварки. По итогу проведенного анализа наиболее универсальным, производительным, перспективным из этих способов оказалась лазерная сварка.
Для решения проблемы была выдвинута теория, предполагающая создание в поверхностном слое остаточных напряжений сжатия, которые будут препятствовать образованию холодных трещин. За основу взят метод лазерного термопластического упрочнения (ЛТПУ) с принудительным охлаждением. В качестве образцов использовалась сталь У10А.
Основные положения теории заключаются в следующем: для обеспечения близкой к максимальной степени сжимающих остаточных напряжений в поверхностном слое необходимы условия, при которых на поверхности металл застынет и охладился быстрее, чем в нижних слоях шва. Это осложняется тем, что теплоотвод в основной материал детали идет быстрее, чем через поверхность (охлаждающую среду). Для создания высоких градиентов нагрева и охлаждения обработку следует вести импульсным методом с принудительным охлаждением с достаточным коэффициентом теплоотдачи. Для достижения глубокого проплавления с минимальным количеством энергии для импульса и уменьшения зоны термического влияния необходимо изменить форму импульса.
Для оценки состоятельности теории использовались методы компьютерного исследования конечно-элементных моделей в среде ANSYS Workbench. Задача рассматривается в осесимметричной постановке. Моделируется один лазерный импульс с последующим охлаждением. Для этого строится прямоугольник с размерами по длине – 10 мм, по высоте – 4,5 мм, что соответствует полубесконечному телу. Проводится два анализа Transient Thermal и Static Structural. Для моделирования глубокого проплавления в центре цилиндра вырезается пустотелый канал, который выжигается и испаряется при лазерном импульсе высокой мощности. Размеры канала определены экспериментально при пробном импульсе.
Физические, механические и тепловые свойства стали У10А, в том числе и зависящие от температуры были взяты из литературных источников.
Размер элементов в основном теле материала равен 0,1 мм. В месте сгущения сетки, ее размер изменяется от 0,002 до 0,020 мм. Измельчение сетки КЭ распространяется на глубину 0,2 мм от поверхности канала и области воздействия энергии лазерного луча.
При проведении теплового анализа на поверхность в зоне воздействия лазерного излучения, на дно и стенки канала накладывается плотность потока энергии (Heat Flux) зависящая от времени, а также на поверхность накладывается коэффициент конвективной теплоотдачи (Convection).
Закрепление модели проводилось вдоль оси Y по нижней горизонтальной линии.Энергия импульса 15 Дж. Импульс длился 15 миллисекунд. С помощью предварительных экспериментов была найдена оптимальная форма распределения энергии импульса по времени для глубокого проплавления: в первые 12 миллисекунд на излучение тратилось 20% всей энергии импульса, а в последующие 3 миллисекунды 80% энергии.
Процесс остывания сварного шва моделировался с тремя вариантами коэффициентов конвекции: 1,2 . 10-2 Вт/м2К (атмосферный воздух), 2,1 Вт/м2К (средний для струи аргона Ar2, под давлением Р=2 атм.) и 4,0 . 104 (средний для газово-аэрозольной смеси Ar2+Н2О под давлением Р=2 атм.).
Для определения остаточных напряжений данные температурных полей передаются из анализа Transient Thermal в Static Structural.
Решение модели показало, что наивысшее значение сжимающих остаточных напряжений в поверхностном слое получается при газовоаэрозольном охлаждении. На рис. 1. приведены изолинии температур при остывании образца при газово-аэрозольном охлаждении(Ar2+Н2О).
На рис. 2 изображена диаграмма зависимости температуры от времени охлаждения в самой нагретой точке образца при принудительном охлаждении спреем Ar2+Н2О.
Изолинии остаточных напряжений образца из стали У10А, охлаждаемого газово-аэрозольной смесью приведены на рис. 3.
Анализ полученных результатов позволяет судить о наличии в поверхностном слое сжи-
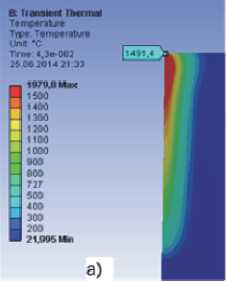
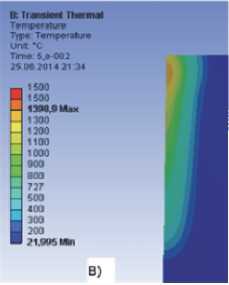
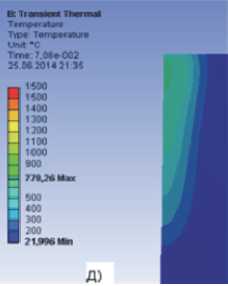
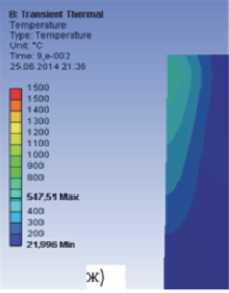
Рис. 1. Изменение положения изолиний температур в процессе охлаждения по времени: а – t=0,043 с, б – t=0,045 с, в – t=0,050 с, г – t=0,060 с, д – t=0,070 с, е – t=0,080 с, ж – t=0,090 с, з – t=0,100 с мающих остаточных напряжений величиной до 111,8МПа. Также анализ данных позволяет определить в первом приближении глубину и радиус залегания напряжений сжатия, которые составляют 50-60 мкм и 800 мкм соответственно.
Также проведены физические экспериментальные исследования образцов из стали У10А с применением охлаждения на спокойном атмосферном воздухе, в струе аргона Ar2, под давлени-
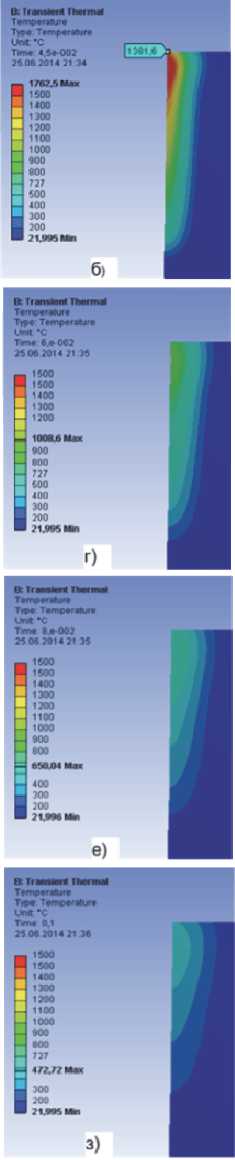
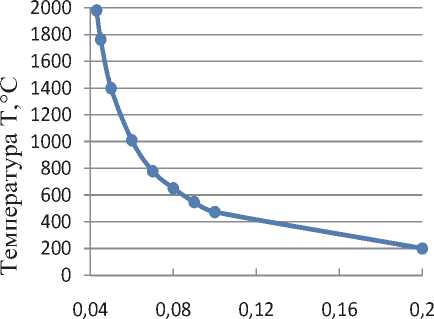
Время от начала имульса t, сек
Рис. 2. Диаграмма охлаждения самой нагретой точки образца
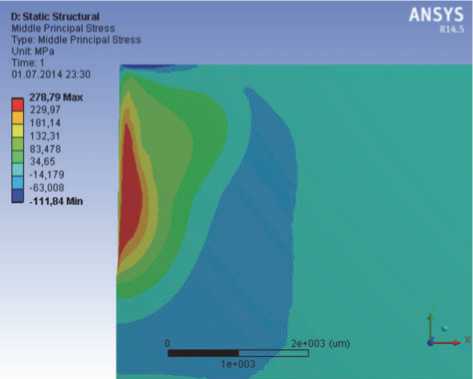
Рис. 3. Изолинии остаточных напряжений образца из У10А, охлаждаемого газово-аэрозольной смесью
ем 2 атм. и в газово-аэрозольной смеси Ar2+Н2О под давлением 2 атм. Для сравнения влияния микротвёрдости сварного шва на его прочность были поставлены дополнительные эксперименты по сварке образцов из стали Ст3.
В ходе проведения исследования были проведены расчёт, конструирование и апробация установки для импульсной лазерной сварки с применением принудительного охлаждения поверхности металла струей газа или газово-аэрозольной смесью (рис. 4).
Для обеспечения доверительного интервала 0,95 на основании теории малых выборок берется по 7 пар образцов сталей У10А и Ст3 размерами 20х10х4,5 мм.
Образцы разрезаются ручной ножовкой по металлу. Затем для обеспечения шероховатости не менее Ra 2,5 шлифуются на шлифовальной шкурке зернистостью 50 и 25.
Исследования проводятся на модернизированной лазерной установке «КВАНТ-15». Перед проведением эксперимента на пробном образце производится лазерный импульс с параметрами энергии, времени и формы, соответствующими тем, что были описаны выше и использовались при решении КЭ модели. Процесс лазерного импульса и последующего охлаждения фиксируется на высокоскоростную видеокамеру V-500 с частотой съемки 1000 кадров в секунду. По материалам видеосъемки определяется время от начала импульса до момента образования на поверхности сварной ванны корки застывшего металла.
Для проведения эксперимента по лазерной сварке образцы из одноименных материалов ставятся торцом друг к другу на столе лазерной установки. Чтобы избежать колебания и перемещения образцы во время сварки закрепляются на столе прижимами. С помощью регулировочных винтов стола лазерной установки происходит наведение лазера на центр стыка свариваемых образцов. Лазерный пучок фокусируется до диаметра ø1 мм. Поверхность образцов располагается за фокальной плоскостью. Затем происходит выставление энергии, длительности и формы импульса. Изменение формы импульса возможно за счет многомодовой системы накачки.
Перед началом эксперимента включается все необходимое оборудование, открываются краны и вентили, заливается чистая дистиллированная вода в бачок охлаждающей жидкости. После заряда системы накачки лазерной установки происходит импульс в соответствии с заданными параметрами. Затем наступает период выдержки, когда воздействие лазера прекратилось, а охлаждение не началось. На 43 миллисекунде, когда на поверхности образовалась корка застывшего металла, подается сигнал с блока задержки электрического сигнала 8 (рис. 4) на блок управления ЭПК 7 (при охлаждении на свободном воздухе сигнал на открытие ЭПК не подается). Открыва-
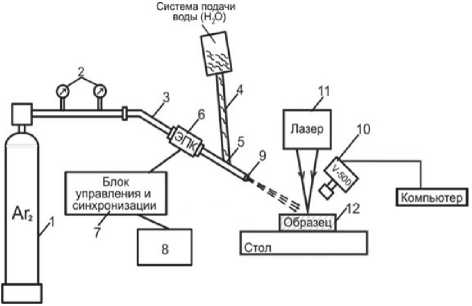
Рис. 4. Схема установки для лазерной сварки: 1 – баллон сжатого газа (Ar2); 2 – манометр; 3 – магистраль подачи газа высокого давления; 4 – магистраль подачи охлаждающей жидкости (Н2О); 5 – инжектор; 6 - электропневматический клапан (ЭПК); 7 – блок управления ЭПК; 8 – блок задержки электрического сигнала; 9 – сопло; 10 – скоростная видеокамера V-500; 11 – лазерная установка; 12 – образец ется ЭПК 6 и в магистраль подачи газа высокого давления 3 поступает аргон под давлением Р=2 атм. Продвигаясь по магистрали подачи газа высокого давления 3 аргон смешивается с водой, поступает к соплу 9 и подается к образцу в виде спрея (в случае охлаждения в среде аргона вода не подается). Весь цикл импульса и охлаждения занимает 1 секунду. За это время металл в сварном шве успевает расплавиться, смешаться, закристаллизоваться и остыть.
Сваренные образцы исследуются на сопротивление разрыву на разрывной машине РМ-50М.
Для определения микротвердости и микроструктуры места сварки изготавливаются микрошлифы образцов разорванных по месту сварки. Исследование микроструктуры сварных соединений проводится с использованием оптического микроскопа NEOPHOT-30. Микротвердость металла сварного шва измеряется с помощью микротвердомера ПМТ-3. При данном исследовании алмазная пирамидка вдавливается с усилием 0,490 Н. Микротвердость измеряется на линии оси сварного канала, начиная от поверхности и заканчивая самой нижней точкой канала.
Фотографии микрошлифов образцов из стали У10А приведены на рис. 5.
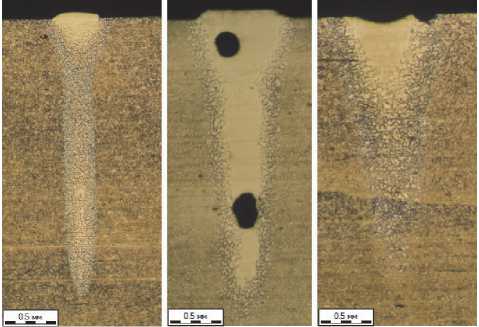
а) б) в)
Рис. 5. Фотографии микрошлифов образцов из стали У10А:
а - при охлаждении на спокойном воздухе; б - при охлаждении струей аргона, в - при газово-аэрозольном охлаждении
Фотографии микрошлифов образцов из Ст3 показаны на рис. 6.
Сравнение фотографии микрошлифа образца из стали У10А, полученного лазерной сваркой с последующим газово-аэрозольным охлаждением смесью Ar2+Н2О и фотографии изолиний температур численной модели для этого же варианта перед началом принудительного охлаждения (рис. 7) позволяет сделать вывод об адекватности численной модели.
Диаграмма охлаждения стали У10А при принудительном охлаждении (рис. 2) позволяет прогнозировать образование в сварном шве закалочных структур преимущественно мартенсита, особенно
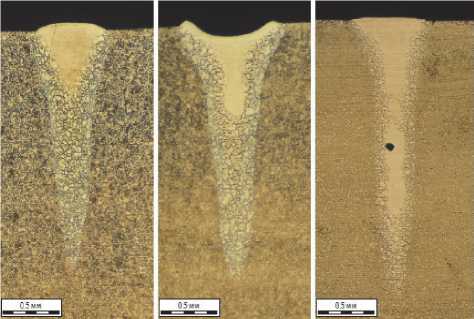
а) б) в)
Рис. 6. Фотографии микрошлифов образцов из Ст3: а - при охлаждении на спокойном воздухе, б - при охлаждении струей аргона, в - при газово-аэрозольном охлаждении
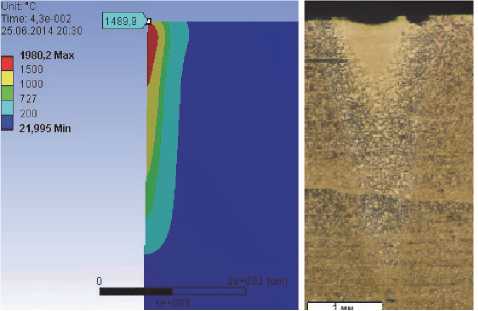
а) б)
Рис. 7. Сравнение ЗТВ при лазерной сварке с глубоким проплавлением стали У10А:
а – численная модель на стадии начала охлаждения, б – физический эксперимент у поверхности образца. Исследования микроструктуры сварных швов на микрошлифах из стали У10А на оптическом микроскопе NEOPHOT-30 подтвердили данное предположение.
Также исследование микроструктуры сварных швов микрошлифов образцов из стали Ст3 показало, что при равных скоростях охлаждения у образцов из сталей У10А иСт3 образуются преимущественно одинаковые фазовые структуры.
На микрошлифах образцов измерена микротвердость. По усредненным данным были построены графики зависимости микротвердости от глубины залегания для У10А и для Ст3 (рис. 8 и рис. 9 соответственно).
Как видно из графиков, при сварке У10А микротвердость на поверхности практически одинаковая для всех трех случаев охлаждения. С увеличением глубины при охлаждении в струе аргона микротвердость почти не изменилась. При охлаждении на спокойном воздухе она снижается незначительно. При аэрозольном охлаждении наблюдается значительное снижение микротвердости по мере удаления от поверхности.
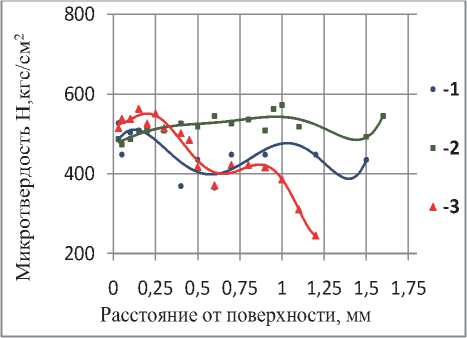
Рис. 8. Сравнительный график микротвердости стали У10А:
1 – охлаждение на воздухе;
2 – при охлаждении струей аргона;
3 – при газово-аэрозольном охлаждении
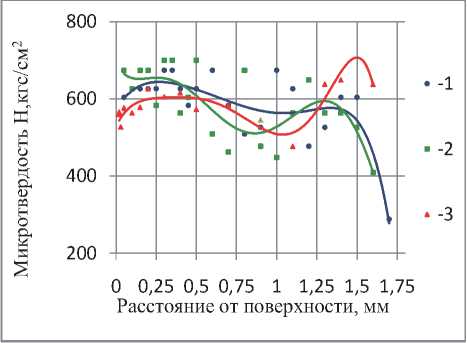
Рис. 9. Сравнительный график микротвердости стали Ст3:
1 – охлаждение на воздухе;
2 – при охлаждении струей аргона;
3 – при газово-аэрозольном охлаждении
При сваривании стали Ст3 наибольшая микротвердость в поверхностном слое достигается при охлаждении сжатым аргоном. Близко к ней проходит линия значений микротвердости для случая сварки с охлаждением на воздухе. Ниже глубины 1,4 мм микротвердостьобразцов, полученных при охлаждении на спокойном воздухе и струей аргона,значительно снижается. При аэрозольном охлаждении микротвердость сварного шва на поверхности ниже, чем в двух других вариантах, но ниже 1,3 мм увеличивается. В целом микротвердость образцов из Ст3 для всех трех вариантов охлаждения имеет сходные графики.
В результате проведения испытаний на разрывной машине РМ-50 построен график зависимости средних усилий разрыва точечных сварных соединений от коэффициента теплоотдачи охлаждающей среды (рис. 10). Как видно из рис. 10 прочность сварного шва стали Ст3 не зависит от способа охлаждения. Прочность сварного соединения стали У10А при использовании аэрозольного охлаждения увеличилась от 1,57 кг до 3,63 кг, т.е. в 2,3 раза.
Анализ и сопоставление сравнительных графиков микротвердости (рис. 8 и рис. 9) с графиком зависимости среднего усилия разрыва от коэффициента теплоотдачи показывает, что ста-
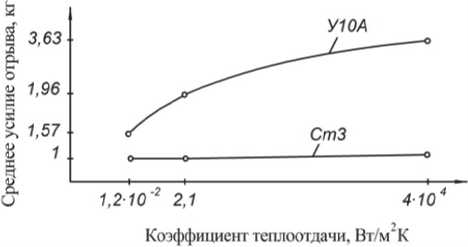
Рис. 10. График зависимости среднего усилия разрыва от коэффициента теплоотдачи тическая прочность сварного соединения на разрыв не сильно зависит от микротвердости и, как следствие, фазовых структур шва. В значительно большей степени прочность шва определяется наличием горячих и предрасположенностью к образованию холодных трещин. Сталь Ст3 не предрасположена к образованию трещин, поэтому прочность шва на разрыв практически не менялась в зависимости от коэффициента теплоотдачи охлаждающей среды.
При применении принудительного охлаждения сварного шва в поверхностном слое образуются сжимающие остаточные напряжения (рис. 3). Именно они препятствуют образованию горячих и развитию холодных трещин в сварном шве. Величина сжимающих остаточных напряжений возрастает при увеличении скорости охлаждения поверхности образца. Это объясняет рост среднего усилия разрыва сварного соединения образцов из У10А при увеличении коэффициента теплоотдачи охлаждающей среды.
Анализ полученных результатов позволил сделать следующие выводы.
Микротвердость образцов не сильно зависит от способа охлаждения. Это свидетельствует об образовании одинаковых фазовых структур.
Технологическая прочность сварного соединения деталей из У10А увеличивается в 2,3 раза при использовании принудительного охлаждения газово-аэрозольной смесью. Причина повышения прочности сварного шва – сжимающие остаточные напряжения в поверхностном слое.
Список литературы Исследование процесса лазерной сварки стали У10А
- Васильев А.А., Ерофеев В.А., Судник В.А. Анализ явлений испарения и конденсации металла при лучевых способах сварки.//Сб. докл. Шестой межд. конф. «Математическое моделирование и информационные технологии в сварке и родственных процессах», 29 мая -1 июня 2012 г., пос. Кацивели, Большая Ялта, Крым, Украина . Киев: Международная ассоциация «Сварка», 2012. C. 21-26.
- Стали и сплавы. Марочник/В.Г. Сорокин, М.А. Гервасьев, П.С. Палеев, И.В. Гервасьева, С.Я. Палеева. М.: Интермет Инжиниринг, 2001. 608 с.