Экспериментальное исследование жесткости технологической системы на базе промышленного робота Kuka KR 300 R2500 Ultra
Автор: Нуркенов Антон Халилевич, Гузеев Виктор Иванович, Батуев Виктор Викторович, Нестерюк Егор Владимирович, Павлов Семен Александрович
Рубрика: Контроль и испытания
Статья в выпуске: 1 т.22, 2022 года.
Бесплатный доступ
В современном машиностроительном производстве существует множество деталей, имеющих как значительные габаритные размеры, так и сложные труднодоступные поверхности для обработки. Изготовление таких деталей производится на специализированном оборудовании, которое имеет такие же значительные габаритные размеры. Однако сложность конструкции ряда деталей, таких как корпус ракетного двигателя, емкости большого объема, неразборные металлоконструкции и т. д., а также их труднодоступность, нивелирует технологические возможности данного оборудования. В настоящее время для обработки таких деталей используют промышленных роботов, оснащенных инструментальными шпинделями. Наличие большого количества степеней свободы данного оборудования, сравнительно небольшие габаритные размеры и обширность рабочей зоны позволяют их эффективно использовать в данной сфере машиностроения. Однако недостаточно изученная жесткость данного оборудования, отсутствие конкретных рекомендаций по их применению значительно ограничивают сферу их применения. Таким образом, вопросы, связанные с взаимным влиянием жесткости технологической системы, силой резания и режимами резания при изготовлении крупногабаритных деталей при помощи промышленных роботов, актуальны и требуют всестороннего исследования. С целью исследования динамических процессов при изготовлении крупногабаритных деталей с использованием промышленного робота проведены эксперименты по определению амплитудно-частотных характеристик вибраций, возникающих в процессе обработки. Экспериментальное исследование позволило установить, что жесткость технологической системы изменяется в широком диапазоне. При этом жесткость детали при импульсной нагрузке отличается от жесткости при фрезеровании не менее чем на порядок, а жесткость шпинделя при фрезеровании отличается от жесткости детали не менее чем на 2 порядка. Исходя из этого в процессе проектирования механической обработки крупногабаритных нежестких деталей при помощи промышленных роботов необходимо учитывать наихудшие условия по жесткости. Целесообразно дальнейшие рекомендации по назначению режимов резания при изменяющихся условиях обработки основывать на учете математического моделирования жесткости элементов технологической системы. Также для автоматизации процесса съема параметров жесткости технологической системы актуальной задачей ставится определение путем тестового определения вибраций на шпинделе промышленного робота и косвенной оценкой микроперемещений на детали.
Жесткость технологической системы, вибрация, промышленный робот, микроперемещения, обработка крупногабаритных деталей
Короткий адрес: https://sciup.org/147237466
IDR: 147237466
Текст научной статьи Экспериментальное исследование жесткости технологической системы на базе промышленного робота Kuka KR 300 R2500 Ultra
В современном машиностроительном производстве существует множество деталей, имеющих как значительные габаритные размеры (до нескольких десятков метров), так и сложные труднодоступные поверхности для обработки. Изготовление таких деталей производится на спе-
Нуркенов А.Х., Гузеев В.И., Экспериментальное исследование жесткости Батуев В.В. и др. технологической системы на базе промышленного робота… циализированном оборудовании, которое имеют такие же значительные габаритные размеры. Однако сложность конструкции ряда деталей, таких как корпус ракетного двигателя, емкость большого объема, неразборные металлоконструкции и т. д., а также их труднодоступность, нивелирует технологические возможности данного оборудования.
В настоящее время для обработки таких деталей используют промышленных роботов, оснащенных инструментальными шпинделями [1–9]. Наличие большого количества степеней свободы данного оборудования (более 6), сравнительно небольшие габаритные размеры и обширность рабочей зоны позволяют их эффективно использовать в данной сфере машиностроения. Однако недостаточно изученная жесткость данного оборудования, отсутствие конкретных рекомендаций по их применению значительно ограничивают сферу их применения.
В процессе проектирования операций технологического процесса изготовления деталей при помощи промышленных роботов возникают трудности при назначении режимов резания и припусков на различные стадии механической обработки [10–14]. Поскольку данный вид обработки относительно новый, то отсутствуют научно-обоснованные методы и методики определения и назначения рациональных режимов резания, которые учитывают множество переменных таких факторов, к ним относится и жесткость технологической системы, зависящая от положения, занимаемого промышленным роботом, вылетом и положением его исполнительных органов, относительно положения заготовки и т. д. Зачастую режимы резания назначаются в соответствии с рекомендациями справочников, которые не подходят для данного метода обработки и в последующем подвергаются значительной коррекции уже на основе субъективного опыта технолога, что сказывается на производительности операции и качестве изготавливаемой продукции.
На промышленных предприятиях технологи из-за отсутствия возможности учесть все возможные факторы, влияющие на обработку, занижают режимы резания для снижения вероятности поломки режущего инструмента, увеличения ресурса его работы и обеспечения требований к точности обработки. Отсюда возникают проблемы снижения производительности и качества обработки, связанные с неполной реализацией потенциала промышленных роботов, используемых для изготовления деталей.
Экономически приемлемый выбор режимов обработки основан на соотношении показателей точности и производительности. Эти показатели находятся во взаимосвязи друг с другом и зависят от множества различных факторов, влияющих на точность и качество обработки, но при этом одним из основных являются силы резания, возникающие в процессе обработки, которые позволят в дальнейшем построить корреляцию этой зависимости.
Таким образом, вопросы, связанные с взаимным влиянием жесткости технологической системы, силами резания и режимами резания при изготовлении крупногабаритных деталей при помощи промышленных роботов, актуальны и требуют всестороннего исследования [15–19].
Цель исследования: исследование динамических процессов при изготовлении крупногабаритных деталей с использованием промышленного робота, а также проведение экспериментов по определению амплитудно-частотных характеристик вибраций, возникающих в процессе обработки.
Экспериментальное исследование вибраций в технологической системе
Целью эксперимента являлось исследование амплитудно-частотной характеристики (АЧХ) промышленного робота и заготовки с последующим определением микроперемещений и параметров жёсткости технологической системы.
Для достижения поставленной цели в работе решались следующие задачи:
-
- экспериментальная обработка изделия с измерением АЧХ;
-
- обработка результатов измерений для определения собственных частот элементов технологической системы;
-
- расчёт приведённой жёсткости технологической системы.
Для проведения эксперимента были смоделированы реальные условия обработки, используемые на производстве, что позволило производить анализ и оценку полученных результатов с учётом их практической применимости.
В качестве обрабатываемой детали выбрана приборная панель кабины машиниста электропоезда «Ласточка» представленная на рис. 1. Габаритные размеры детали составляют
Контроль и испытания
3000x800x400 мм, толщина стенки – 6 мм. Заготовка изготавливается путём напыления смеси, состоящей из коротких стекловолоконных нитей и связующего полиэфирного наполнителя на заранее подготовленную форму (матрицу). Далее после отверждения материала, полученную заготовку подвергают механической обработке: сверлению, фрезерованию и шлифованию.
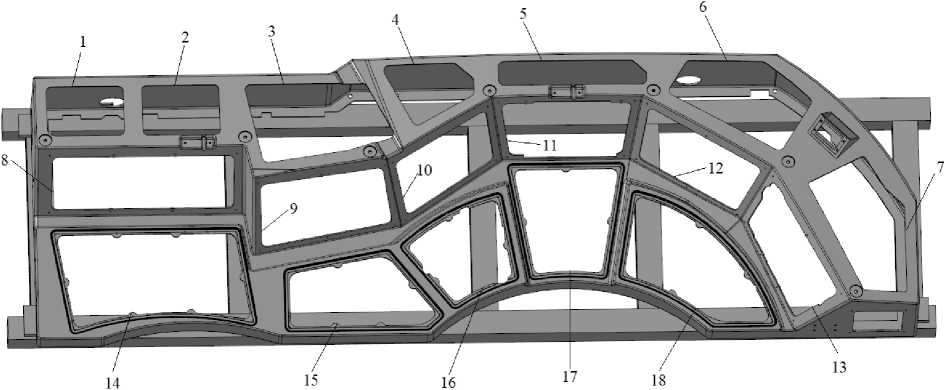
Рис. 1. Приборная панель кабины машиниста электропоезда «Ласточка»
Обработка производилась на промышленном роботе модели KUKA KR 300 R2500 Ultra.
Требуемая точность обрабатываемых элементов лежит в пределах 12–15 квалитета точности, что при размерах от 56 до 580 мм допуск составляет 0,3–2,8 мм. При этом точность обработки на промышленном роботе KUKA KR 300 R2500 Ultra в соответствии с паспортными данными также может изменяться в широком диапазоне (0,1–1 мм) и зависеть от вылета своих рабочих органов.
Поскольку отсутствуют типовые методики по определению параметров технологической системы по вибрациям и микроперемещениям для промышленных роботов, используя известные методы определения АЧХ и методики измерений, предлагается разработать тестовую методику на основе модального анализа.
Для последующей обработки при помощи промышленного робота деталь устанавливалась в специальное станочное приспособление (рис. 2) на поворотном столе.
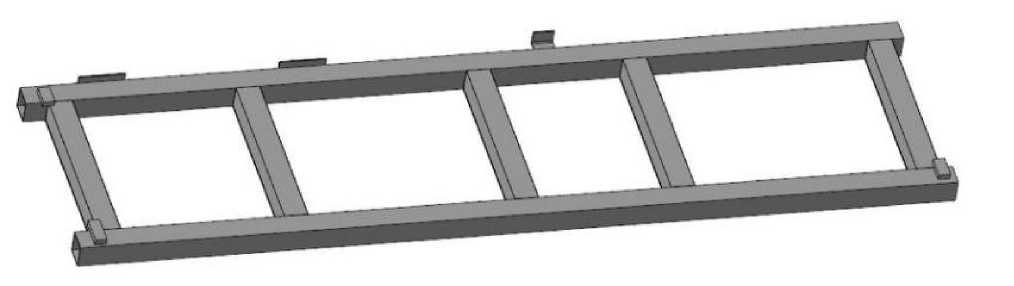
Рис. 2. Специальное приспособление
Данное приспособление состоит из пустотелых профилей квадратного и прямоугольного сечения, соединённого между собой методом электродуговой сварки. Данное приспособление устанавливается на поворотный стол при помощи трёх разъёмных соединений, состоящих из Т-образных пазов, шпилек, шайб и гаек. Базирование обрабатываемой детали в приспособлении происходит по нижней плоскости и боковым поверхностям. Закрепляется деталь при помощи трёх винтов, шайб и гаек по верхним поверхностям. Деталь, установленная в приспособлении, представлена на рис. 3.
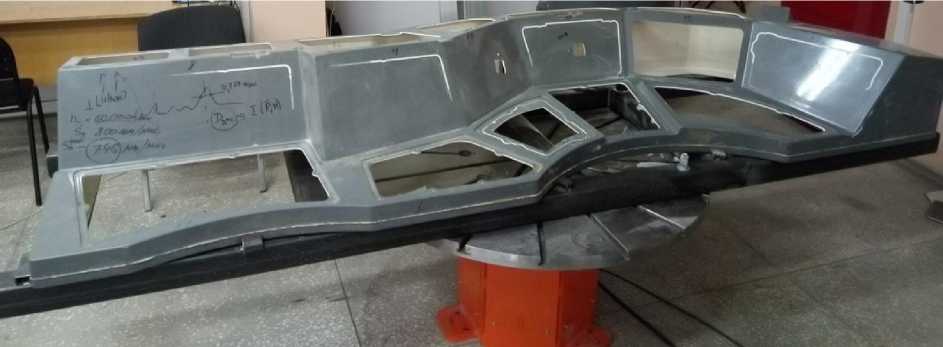
Рис. 3. Деталь, установленная в приспособлении
Для определения собственных форм и амплитуд колебаний технологической системы были определены места и установлены акселерометры (рис. 4). С целью исключения дополнительных источников вибраций производилась запись фоновых шумов без нагрузки ТС продолжительностью 30 с.
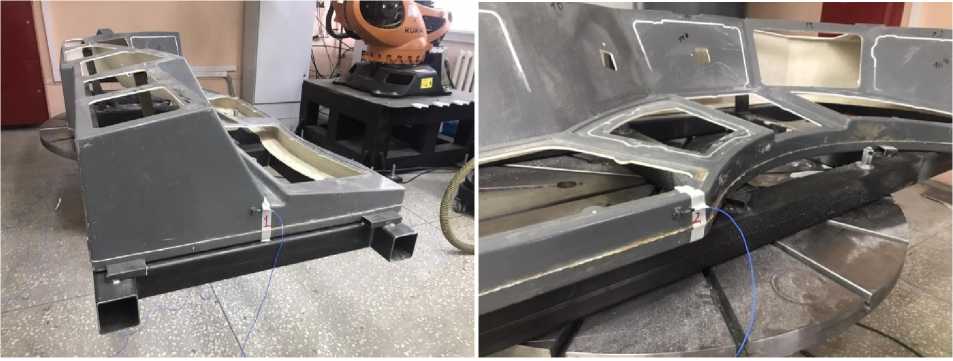
Рис. 4. Места установки акселерометров
Для получения АЧХ осуществлялась импульсная нагрузка динамометрическим молотком в местах крепления датчиков. Импульс ударной силы составил порядка 120–210 Нˑс. В результате измерения вибраций получены графики затухающих колебаний по осям Х и Y с четырёх источников (рис. 5). Частота опроса с датчика составляет 1000 измерений в секунду.
Для дальнейшей работы исходный сигнал преобразовывался при помощи метода Фурье. Данный метод позволил визуально оценить собственные колебания в виде спектра колебаний (рис. 6).
Анализ графиков по осям Х и Y показал повторяющиеся пиковые амплитуды, которые являются собственной частотой детали.
В дальнейшем производились исследования вибраций технологической системы в процессе механической обработки детали. Для сложной и нежёсткой конструкции, обрабатываемой детали, была определена последовательность обработки окон с технологической точки зрения и с точки зрения крепления датчиков.
С целью фиксирования колебаний в направлениях X, Y как с заготовки, так и со шпинделя промышленного робота, применялись два акселерометра. Первый закреплялся на заготовке, второй на шпинделе промышленного робота.
Контроль и испытания
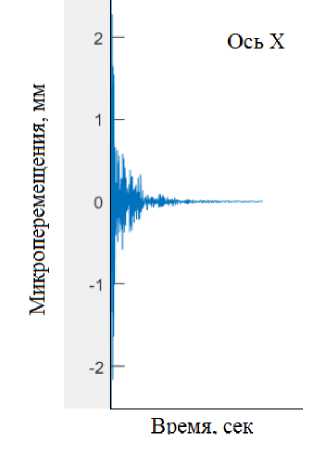
Рис. 5. Графики затухающих колебаний по осям Х и Y при ударе
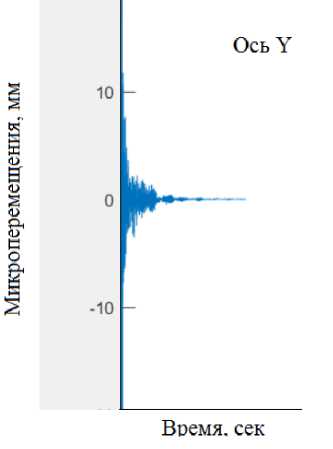
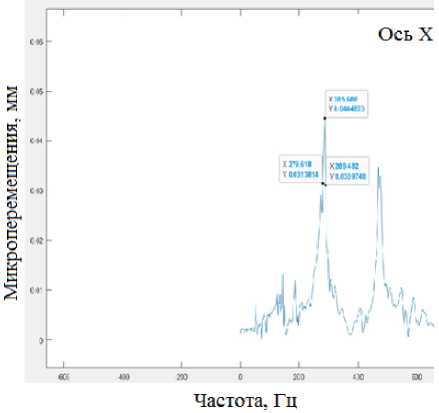
Рис. 6. Преобразования Фурье по осям X и Y
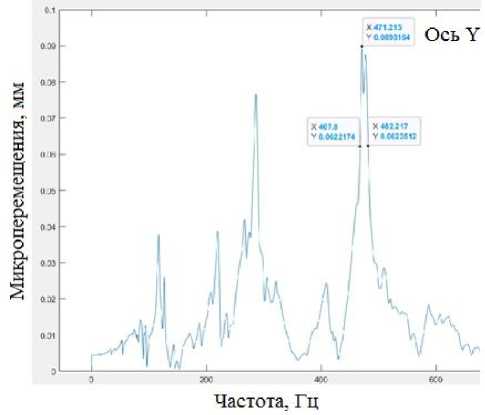
Режимы резания назначались в соответствии со справочными данными производителя инструмента Cerlin (табл. 1).
Таблица 1
Режимы резанья согласны нормативам
№ п/п |
Наименование параметра обработки |
Величина параметра обработки |
1 |
Скорость резания – V c |
160 м/мин |
2 |
Подача – F |
800 мм/мин |
3 |
Глубина резания – t |
3 мм |
Фрезерование и измерение вибраций осуществлялись при последовательной обработке различных элементов детали. Графики измеренных вибраций представлены на рис. 7.
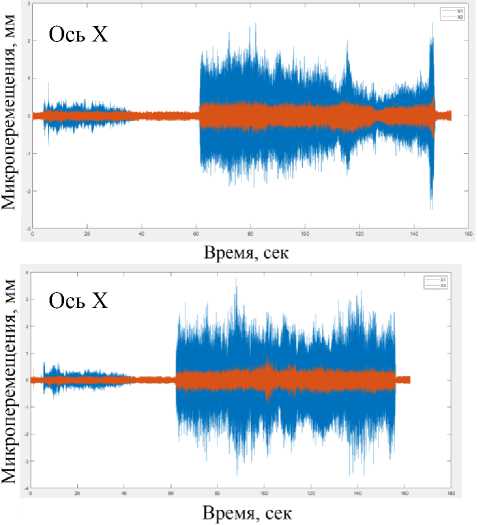
Рис. 7. – измерение вибраций на разных участках, обрабатываемой детали
– показания датчиков на шпинделе; – показания датчиков на заготовке
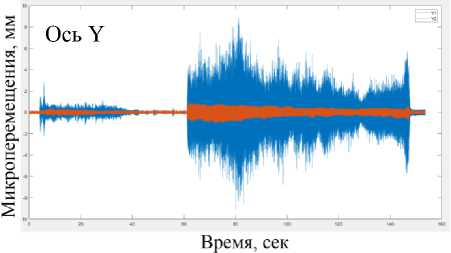
'о » w w е ио ио не ш
Время, сек
Ось Y
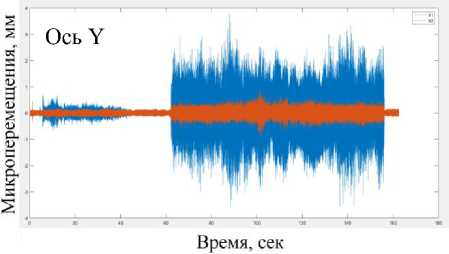
Ось Y s ■ 2
« Я «О ® Ю НО IM
Время, сек
По результатам измерения установлено существенное отличие виброускорений шпинделя в процессе фрезерования от виброускорений детали. При этом визуально при наложении графиков АХЧ на шпиндель и деталь можно сделать вывод о возможности выявления корреляции между значениями микроперемещений на детали и шпиндели.
С целью выявления корреляции между значениями микроперемещений на детали и шпинделе было произведено быстрое преобразование Фурье и получен порядок значений АЧХ на детали и шпиндели (рис. 8).
Для дальнейшего расчета жесткости по полученным параметрам АЧХ была применена методика В.А. Кудинова, ссылка которой позволила на основе экспериментальных характеристик рассчитать значения постоянных, характеризующих жесткость технологической системы. Расчет значения постоянных, характеризующих жесткость технологической системы, осуществлялся при помощи программы MathCAD с применением метода интерполяции сплайнов для аппроксимации экспериментальных амплитуд.
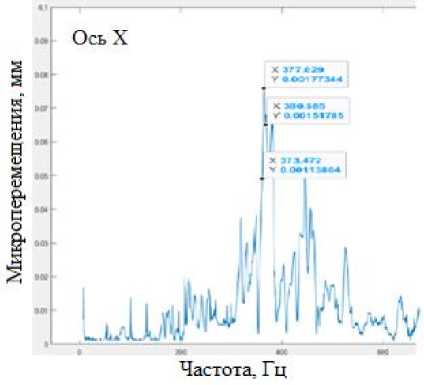
Рис. 8. Амплитудно-частотные характеристики ТС, полученные со шпинделя
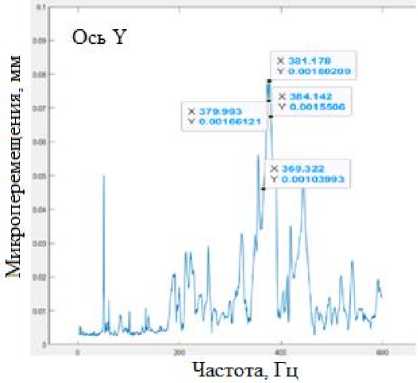
Контроль и испытания
Для дальнейшего расчета параметров для определения жесткости применялась методика, предложенная А.Х. Нуркеновым [20], заключающаяся в определении микроперемещений в зоне резания на основе определения приведенной жесткости технологической системы через определения ее собственной частоты колебаний. Результаты расчета приведены в табл. 2 и 3.
Таблица 2
Расчеты импульсной нагрузки молотком по заготовке
Номер датчика |
Направление удара |
Резонансная амплитуда Амах, мм |
Декремент затухания λ |
Амплитуда колебаний силы P 0, H |
Приведенная жесткость С, H/m |
1 |
по оси X |
0,0444 |
0,32 |
164,339 |
3,61·107 |
2 |
по оси Y |
0,0652 |
0,58 |
172,506 |
1,44·107 |
3 |
по оси X |
0,0057 |
0,57 |
136,815 |
1,33·107 |
4 |
по оси Y |
0,0268 |
0,26 |
172,506 |
7,84·107 |
Из таблицы установлено, что жесткость при импульсной нагрузке изменяется более чем в 5 раз на разных местах обрабатываемой заготовки.
Таблица 3
Расчеты при фрезеровании заготовки
Расположение датчика |
Номер окна |
Ось |
Резонансная амплитуда Амах, мм |
Декремент затухания λ |
Амплитуда колебаний силы P 0, H |
Приведенная жесткость С, H/m |
деталь |
7 |
X |
0,070 |
0,85 |
14 |
0,79·106 |
Y |
0,039 |
1,12 |
14 |
0,99·106 |
||
13 |
X |
0,045 |
0,87 |
14 |
1,13·106 |
|
Y |
0,036 |
0,94 |
14 |
1,28·106 |
||
шпиндель |
7 |
X |
0,035 |
0,08 |
14 |
5,57·108 |
Y |
0,015 |
0,01 |
14 |
3,92·108 |
||
13 |
X |
0,09 |
0,01 |
14 |
0,88·108 |
|
Y |
0,05 |
0,03 |
14 |
2,37·108 |
Из таблицы установлено, что жесткость при фрезеровании изменяется: на детали в 1,62 раза; на шпинделе более чем в 6 раз.
Выводы
Экспериментальное исследование позволило установить, что жесткость технологической системы изменяется в широком диапазоне. При этом жесткость детали при импульсной нагрузке отличается от жесткости при фрезеровании не менее чем на порядок, а жесткость шпинделя при фрезеровании отличается от жесткости детали не менее чем на 2 порядка.
Исходя из этого в процессе проектирования механической обработки крупногабаритных нежестких деталей при помощи промышленных роботов необходимо учитывать наихудшие условия по жесткости. Таким образом, целесообразно дальнейшие рекомендации по назначению режимов резания при изменяющихся условиях обработки основывать на учете математического моделирования жесткости элементов технологической системы. Также для автоматизации процесса съема параметров жесткости технологической системы актуальной задачей ставится определение путем тестового определения вибраций на шпинделе РТК и косвенной оценкой микроперемещений на детали.
Исследование выполнено при финансовой поддержке Министерства науки и высшего образования Российской Федерации (грант № FENU-2020-0020)
Список литературы Экспериментальное исследование жесткости технологической системы на базе промышленного робота Kuka KR 300 R2500 Ultra
- Кучина, О.Б. Проектирование машиностроительного производства: учебное пособие к практическим занятиям / О.Б. Кучина; под ред. Ю.Г. Микова. - Челябинск: Изд-во ЮУрГУ, 2007. - 63 с.
- Проектирование механосборочных цехов: учебник / Г.Н. Мельников, В.П. Вороненко; под ред. А.М. Дальского. - М.: Машиностроение, 1990. - 352 с.
- Проектирование машиностроительных заводов и цехов: справочник: в 6 т / под ред. Е.С. Ямпольского. -М.: Машиностроение, 1974. - Т. 4.
- Машиностроительное производство: учебник / В.П. Вороненко, А.Г. Схиртладзе, B.Н. Брюханов; под ред. Ю.М. Соломенцева. - М. : Высш. школа, 2001. - 304 с.
- Huynh, H.N. Direct method for updating flexible multibody systems applied to a milling robot / H.N. Huynh, H. Assadi, V. Dambly et al. // Robotics and Computer-Integrated Manu-facturing. -2021. - Vol. 63.
- Экспериментальные исследования жёсткости станка-робота /Б.А. Еникеев, А.Р. Сайду-ганов, О.К. Акмаев и др. // Станкостроение и инновационное машиностроение: материалы всероссийской научно-технической конференции. - Уфа: Изд-во УГАТУ, 2019. - С. 273-276.
- Бутенко, В.И. Влияние динамической жёсткости технологического робота на качество обработанной поверхности детали /В.И.Бутенко, И.В. Давыдова, Т.В Атоян //Вестник БГТУ. -2019. - № 2(75). - С. 21-27.
- Дударев, А.С. Инновационное применение роботов для производства изделий из полимерных композиционных материалов /А.С. Дударев // СТИН. - 2018. - № 10. - С. 2-6.
- Иванова, А.В. Робототехнический комплекс удаления заусенцев после фрезерования деталей / А.В. Иванова, Б.Б. Пономарёва, А.В. Савилов и др. // Вестник ИРНИТУ. - 2013. -№ 11 (82). - С. 49-53.
- Кудояров, Р.Г. Методика измерений виброустойчивости станка-робота / Р.Г. Кудояров, C.И. Фецак, Р.Р. Башаров // Станкостроение и инновационное машиностроение: материалы всероссийской научно-технической конференции. - Уфа: Изд-во УГАТУ, 2019. - С. 292-296.
- Nubiola, A. Absolute calibration of an ABB IRB 1600 robot using a laser tracker / A. Nubiola, I.A. Bonev // Robotics and Computer-Integrated Manufacturing. - 2013. - Vol. 29, № 1. - P. 236-245.
- Nguyen, V. Active vibration suppression in robotic milling using optimal control./ V. Nguyen, J. Johnson, S. Melkote // International Journal of Machine Tools and Manufacture. - 2020. - Vol. 152.
- He, F.-X. A chatter-free path optimization algorithm based on stiffness orientation method for robotic milling / F.X. He, Y. Liu, K. Liu // International Journal of Advanced Manufacturing Technology. - 2019. - Vol. 101, № 9-12. - P. 2739 -2750.
- Increasing Machining Accuracy of Industrial Manipulators Using Reduced Elastostatic Model / S. Mamedov, D. Popov, S. Mikhel et al. // Lecture Notes in Electrical Engineering. - 2020. - Vol. 613. -P. 384-406.
- Klimchik, А. MSA-technique for stiffness modeling of manipulators with complex and hybrid structures / A. Klimchik, A. Pashkevich, D. Chablat //IFAC-PapersOnLine. - 2018. - Vol. 51, № 22. -P. 37-43.
- Guo, Y Stiffness-oriented posture optimization in robotic machining applications / Y. Guo, H. Dong, Y. Ke // Robotics and Computer-Integrated Manufacturing. - 2015. - Vol. 35. - P. 69 -76.
- Габитов, А.А. Анализ обеспечения точности позиционирования промышленных роботов / А.А. Габитов, А.В. Каляшина // Вестник казанского государственного технического университета им. А.Н. Туполева. - 2018. - № 4. - С. 49-54.
- Сравнительный анализ качества обработанной поверхности по параметру шероховатости на станке-роботе и станке классической компоновки / Б.А. Еникеев, Р.Р, Баниров, А.Р. Сайдуганов и др. // Станкостроение и инновационное машиностроение: материалы всероссийской научно-технической конференции. - Уфа: Изд-во УГАТУ, 2019. - С. 266-272.
- Измерение собственных и вынужденных частот робота-станка и станка мод. 500V/5 / А.Ф. Гаймалов, Б.А. Еникеев, А.Н. Типеев и др. // Станкостроение и инновационное машиностроение: материалы всероссийской научно-технической конференции. - Уфа: Изд-во УГАТУ, 2019. - С. 318-224.
- Нуркенов, А.Х. Методика моделирования круглого врезного шлифования с учетом фактической жесткости технологической системы / А.Х. Нуркенов, А.В. Геренштейн, Н.М. Машрабов // Материалы LIV международной научно-технической конференции «Достижения науки - агропромышленному производству». Челябинск: ЧГАА. - 2015. - № 3. - С. 92-98.