К вопросу размещения термопар при контроле температурного режима восстановления режущей способности дисковых почвообрабатывающих орудий методом электромеханического деформирования
Автор: Селиверстов М.В.
Журнал: Международный журнал гуманитарных и естественных наук @intjournal
Рубрика: Технические науки
Статья в выпуске: 5-1 (56), 2021 года.
Бесплатный доступ
В статье указана значимость контроля теплофизических характеристик при восстановлении режущей способности кромки дисковых почвообрабатывающих орудий электромеханическим деформированием металла режущей кромки, приведена схема размещения термопар, а также обоснования материала для их изготовления. Опознана методика их размещения. Так как проведение опытов предполагает два этапа исследований, статического и динамического, то приведены обе методики контроля температуры.
Электромеханическое деформирование, режущая кромка, температура, термопара, измерительный блок
Короткий адрес: https://sciup.org/170188858
IDR: 170188858 | DOI: 10.24412/2500-1000-2021-5-1-68-71
Текст научной статьи К вопросу размещения термопар при контроле температурного режима восстановления режущей способности дисковых почвообрабатывающих орудий методом электромеханического деформирования
Для полного и качественного определения влияния энергетических параметров процесса, а так же теплофизических характеристик в данной работе согласно теоретическим исследованиям необходимо измерить температуру в трех точках выделенного стержня системы «электрод - деталь - теплоотводящая масса», а именно в точке контакта электрода с деталью (х=0), в точке находящейся на противоположной стороне режущей кромки (х=l2), а также в точке находящейся в теле теплоотводящей массы [1].
В связи с чем, температуру в выше приведенных точках решено измерять посредством трех хромель - алюмелевых термопар (ТХА), расположенных следующим образом: (рис. 1).
Рис. 1. Схема размещения термопар при проведении натурных экспериментов в исследуемом образце и теплоотводящей массе
Учитывая, что при контактном способе измерения температуры происходит нарушение первичного температурного поля исследуемого объекта, обусловленное монтажом термочувствительного элемента. Вследствие чего при приготовлении контактных датчиков температуры необходимо было свести к минимуму наруше- ние теплового баланса, вносимого термочувствительными элементами [2; 3].
Закрепление термопары измеряющей температуру поверхности восстанавливаемой режущей кромки (7К) проводилось следующим образом: на поверхности режущей кромки на расстоянии 2,6 мм (срединная точка режущей кромки с учетом максимально допустимого износа 0,8 мм) делалось углубление равное 0,25 мм (половина диаметра спая термопары); далее это углубление с целью лучшего приваривания термопары обезжиривалось и подсушивалось в течении 10…15 мин. Затем с использованием конденсаторной сварки производилась приварка термопары в углубление. После чего с целью дополнительной изоляции и снижения токовых наводок спай обрабатывался клеевым составом на основе эпоксидной смолы и подсушивался до момента полимеризации состава [5].
Закрепление термопары находящейся на противоположной стороне режущей кромки (6К) осуществлялась на расстоянии 3,2 мм от края режущей кромки (расстояния в обоих случаях вымерялось с использованием штангензубомера). Остальные операции производились аналогично.
Для обеспечения большей информативности измерения температуры в теплоотводящей массе было решено производить на глубине 5 мм от поверхности теплоотводящей массы. Для этого с тыльной стороны теплоотводящей массы было сделано сверление диаметром 5 мм на глубину 10 мм. Для снижения влияния токовых наводок на термопару расположенную в теле теплоотводящей массы было решено произвести дополнительную изоляцию. Для этого в сверление был залит эпоксидный состав. После отверждения состава (24 часа) по центру делалось еще одно сверление на ту же глубину, но уже диаметром 3 мм. С использованием конденсаторной сварки производилась приварка термопары. Окончательной операцией по заделке термопары (8К) была повторная заливка сверления эпоксидным составом и сушка.
В связи с тем, что в данной работе необходимо определить параметры энер- говложения сначала для статического режима, а затем с использованием полученных данных для динамического режима начальной стадии процесса восстановления, то и теплофизические эксперименты необходимо проводить в два этапа [5].
Методика термометрирования образцов в статическом режиме
Замер температур производился следующим образом: теплоотводящую массу с закрепленной на ней термопарой (8К) устанавливали в трехкулачковый патрон установки, затем производился монтаж на теплоотводящую массу восстанавливаемой детали с закрепленными на ней термопарами (6К, 7К), при этом необходимо совместить теплоотводящую массу и образец таким образом, чтобы все термопары находились в одной плоскости по радиусу. Далее устанавливали систему «диск - теплоотводящая масса» таким образом, чтобы термопары оказались напротив электрода. Путем перемещения суппорта станка создаем усилие поджатия ролика электрода равное 800 Н и угол его воздействия 200. Изменением ступеней трансформатора устанавливалось напряжение равное 1,8 В. После выполнения этих операций производилось включение контрольно - измерительной аппаратуры и осуществлялся процесс ЭМД. По завершении деформирования режущей кромки выключался трансформатор и АЦП, затем формующий электрод отводился от детали [6; 7].
Для интерпретации экспериментальных данных выбиралось такое время процесса, в течение которого начинается и заканчивается процесс формирования режущей кромки. Таким образом, регистрация температур при проведении процесса начиналась с момента начала процесса и заканчивалась после его завершения.
Методика термометрирования образцов в динамическом режиме
В части закрепления термопар в образце методика термометрирования в динамическом режиме не отличается от статического режима. В данной методике присутствуют отличия от предыдущей начальным размещением контролируемого «стержня» относительно электрода [5] (рис. 2).
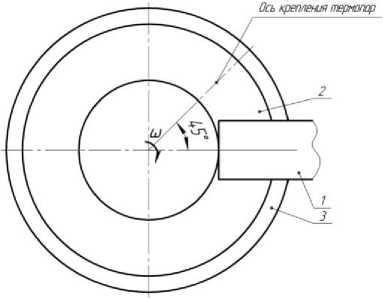
Рис. 2. Схема размещения оси крепления термопар относительно электрода в динамическом режиме1 – электрод; 2 – деталь; 3 – теплоотводящая масса.
В данном случае необходимо было определить вторую стадию термической обработки (рис. 2). Для этого необходимо чтобы измерения температур в точках системы «электрод – деталь – теплоотводящая масс» проводилось на достаточном для этого участке. В связи, с чем было решено отвести место крепления термопар относительно электрода на угол равный 450 в сторону противоположную вращению диска, кроме того, такое расположе- ние термопар позволяет снизить токовые наводки, идущие от электродвигателя привода станка [7; 8]. При этом линейная скорость движения режущей кромки диска относительно формующего электрода составляла 5,6 м/мин. Остальные параметры
Процесс термометрирования системы также начинался с момента начала процесса восстановления. Процесс завершался после того как ось крепления термопар пройдет под электродом и удалится на угол 40…450. По завершении процесса одновременно выключался силовой трансформатор и привод шпинделя, затем выключался аналогово - цифровой преобразователь и электродный узел отводился от детали. Следовательно, регистрация тем- ператур системы производилась в течении всего опыта. В качестве начальной точки интерпретации процесса выбиралась точка момента включения силового трансформатора, а заканчивалась в точке достижения температур максимального значения.
процесса оставались аналогичными.
Список литературы К вопросу размещения термопар при контроле температурного режима восстановления режущей способности дисковых почвообрабатывающих орудий методом электромеханического деформирования
- Чижов В.Н. Контроль температуры контактной поверхности "Электрод-деталь" при восстановлении режущей кромки дисков почвообрабатывающих машин / В.Н. Чижов, А.А. Болтенков, О.Г. Бельчикова, М.В. Селиверстов // Вестник Алтайского государственного аграрного университета. - 2018. - №5 (163). - С. 155-163.
- Нубарян С.М. Контрольно-измерительные приборы в теплотехнических измерениях. Курс лекций. - Харьков: ХНАГХ, 2006. - 283 с.
- Линевег Ф. Измерение температур в технике. Справочник. Пер. с нем. под ред. Чариховой Л.А. - М.: Металлургия. 1980. - 544 с.
- Овчинников В. В. Технология и оборудование контактной сварки: Лабораторно-практические работы: учеб. пособие для студ. учреждений сред. проф. образования. - 5-е изд., стер. - М.: Издательский центр "Академия", 2016. - 160 с.
- Вопросы моделирования тепловых процессов при восстановлении режущей способности дисковых рабочих органов почвообрабатывающих машин методом электромеханического деформирования / Болтенков А.А., Селиверстов М.В. // Вестник Алтайского государственного аграрного университета. - 2018. - №9 (167). - С. 159-164.
- Селиверстов М.В. Описание экспериментальной установки для восстановления режущей способности дисковых почвообрабатывающих орудий методом электромеханического деформирования // Международный журнал гуманитарных и естественных наук. - 2020. - №12-1 (51). - С. 165-167.
- Катаев Р.Ф. Теория и технология контактной сварки: учебное пособие / Р.Ф. Катаев, В.С. Милютин, М.Г. Близник. - Екатеринбург: Изд-во Урал. ун-та, 2015. - 144 с.
- Романов Д.И. Электроконтактный нагрев металлов. - М.: Машиностроение, 1981. - 168 с.