Компьютерная подготовка производства конических авиационных передач
Автор: Волков Андрей Эрикович, Медведев Владимир Иванович
Журнал: Известия Самарского научного центра Российской академии наук @izvestiya-ssc
Рубрика: Механика и машиностроение
Статья в выпуске: 4-2 т.14, 2012 года.
Бесплатный доступ
Описан программный комплекс «Эксперт», предназначенный для решения задач синтеза и анализа конических передач с круговыми зубьями. Представлены программные модули, которые дают возможность проводить расчет наладок зубообрабатывающих станков, определять пятно контакта и кривую неравномерности передачи вращения без нагрузки и под нагрузкой, находить распределение контактных давлений и напряжений изгиба на каждой фазе зацепления, рассчитывать подналадки станков на основе проведенных измерений боковых поверхностей зубьев колес. Все расчеты могут быть проведены с учетом технологических погрешностей.
Конические передачи с круговыми зубьями, наладки, пятно контакта, контактные давления, главные нормальные растягивающие напряжения
Короткий адрес: https://sciup.org/148201268
IDR: 148201268
Текст научной статьи Компьютерная подготовка производства конических авиационных передач
Конические передачи с круговыми зубьями обладают высокой нагрузочной способностью в сочетании со слабой чувствительностью к монтажным погрешностям. Такие передачи широко используются в трансмиссиях вертолетов и в редукторах различных машин. Степень неравномерности передачи вращения зависит от формы поверхностей контактирующих зубьев, которая, в свою очередь, зависит от наладок зубообрабатывающего оборудования. Под наладками понимаются величины, определяющие исходное положение инструмента и закон его движения относительно заготовки, а также величины, характеризующие геометрию зубообрабатывающего инструмента. От значений наладок зависит не только ошибка в законе передачи равномерного вращения, но и многие другие факторы, определяющие работу зубчатой пары, например, благоприятное (без ударов) или неблагоприятное (с ударами) пересопряжение зубьев; размеры, форма и положение пятна контакта на поверхностях контактирующих зубьев, и как следствие – нагрузочная способность передачи.
Исследованием конических передач с круговыми зубьями занимались многие российские и зарубежные ученые, в том числе M.L. Baxter [8], Ф.Л. Литвин [9], В.Н. Кедринский [3], К.М. Пис-маник [5], М.Г. Сегаль [4], Н.Ф. Хлебалин [6], Г.И-. Шевелева [7], V. Simon [10] и многие другие.
На кафедре “Теоретическая механика” МГТУ «Станкин» на протяжении нескольких десятилетий ведется научная работа по моделированию технологических процессов формообразования поверхностей зубьев конических колес и процессов работы этих колес в передаче. Организатором и руководителем этой работы была д.т.н., проф. Галина Ивановна Шевелева. Результатом работы является программный комплекс (ПК) «Эксперт», позволяющий сократить сроки подготовки производства конических передач с круговыми зубьями и повысить их нагрузочную способность.
Повышение нагрузочной способности может быть достигнуто за счет применения комплексного подхода к конструированию зубчатых передач с использованием методов компьютерного моделирования. Для этого уже на стадии проектирования передачи определяются значения основных параметров процессов зубообработки, а проверочный расчет проводят с учетом той реальной формы зубьев, которая получается на зубообрабатывающем оборудовании. Такой комплексный подход может быть реализован с использованием программного комплекса «Эксперт».
ОПИСАНИЕ ПК «ЭКСПЕРТ»
ПК «Эксперт» дает возможность инженеру не самой высокой квалификации принимать грамотное решение при подготовке производства конических зубчатых колес благодаря надежному компьютерному расчету наладок и их оценке, основанной на результатах компьютерного анализа работы будущей зубчатой передачи в условиях, близких к эксплуатационным. ПК «Эксперт» состоит из шести блоков программ- ных модулей. Алгоритмы, на которых основаны программные модули ПК «Эксперт», опубликованы в работах [1, 2, 7].
Программные модули первого блока «Синтез» предназначены для расчета наладок зубообрабатывающих станков как при отсутствии каких-либо технологических ограничений на изготовление колес, так и при наличии технологических ограничений. К технологическому ограничению относится, например, требование изготовить пару зубчатых колес для передачи с малым межосевым углом с использованием инструмента, диаметр которого значительно меньше длины образующей делительного конуса. Расчет наладок осуществляется из условия обеспечения локализованного контакта.
Исходными данными являются геометрические характеристики зубчатой пары и ее элементов, сведения об инструменте для обработки колеса и условия синтеза, т.е. требования к зацеплению, которые задают с помощью параметров синтеза. К числу последних относятся положение расчетной точки (центра будущего пятна контакта); отношение p длины мгновенной контактной площадки в расчетной точке к ширине зубчатого венца; направление движения точки контакта по поверхности зуба; величина зазора dtmax между боковыми поверхностями зубьев в расчетном положении колес при принудительно равномерном вращении колеса; коэффициент Кm модификации обкаточного движения. Результатами работы модулей является карта наладок для наиболее распространенных моделей саратовских станков, американских станков фирмы Gleason и станков немецкой фирмы Modul.
Во второй блок «Формообразование» входят программные модули, которые дают возможность точно определять всю боковую поверхность зуба, включая переходную поверхность, диагностиро- вать заострение зубьев и недопустимое сужение зубьев еще до изготовления колес в металле, определять величину снимаемого припуска при чистовой обработке после выполненной черновой.
Третий блок «Компенсация погрешностей» составляют программные модули, предназначенные для расчета наладок с целью воспроизведения требуемой расчетной поверхности на конкретном зубообрабатывающем оборудовании для компенсации его погрешностей.
При расчете наладок с использованием модулей «Синтез» невозможно учесть неизвестные погрешности конкретного станка. По этой причине боковые поверхности зубьев, полученные при обработке на станке, отличаются от расчетных непредсказуемым образом. Для определения поля отклонений между рассчитанными и нарезанными поверхностями проводится измерение боковых поверхностей нарезанных зубьев в нескольких точках (обычно 45-ти) с помощью координатно-измерительной машина (КИМ).
Набор скорректированных значений наладок для повторения расчетных боковых поверхностей зубьев на конкретном зубообрабатывающем станке осуществляется путем минимизации отклонений методом наименьших квадратов. Скорректированные значения наладок позволят на конкретном станке с погрешностями получить конические колеса с такими же боковыми поверхностями, которые были смоделированы с использованием ПК «Эксперт».
На рис. 1 даны некоторые результаты расчета с использованием программных модулей третьего блока. На рис.1а показано поле отклонений расчетной поверхности и боковой поверхности зуба, нарезанного по расчетным наладкам и измеренного с помощью КИМ. Максимальное отклонение вследствие погрешностей станка составило 0,29 мм. На рис.1б показано поле откло-
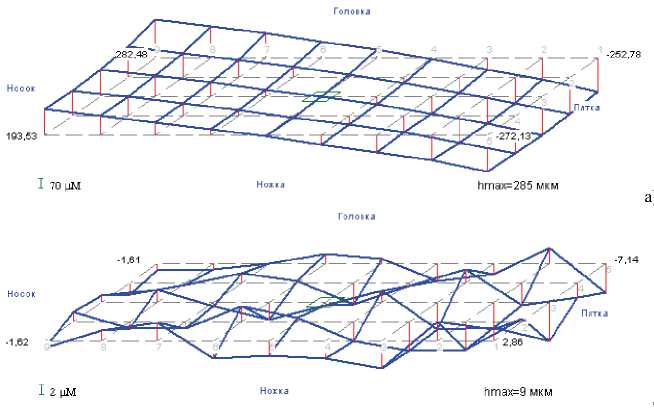
Рис. 1. Примеры полей отклонений, построенные для боковых поверхностей зубьев, нарезанных: а – по расчетным наладкам; б – по скорректированным наладкам
б)
нений боковой поверхности зуба, нарезанного по скорректированным наладкам и измеренного с помощью КИМ, от той же расчетной поверхности. Максимальное отклонение оказалось равным 0,009 мм.
Программные модули четвертого блока «Анализ без нагрузки» предназначены для моделирования проверки зубчатой пары на контрольно-обкатном станке. Исходными данными служат: таблично заданные на сетках боковые поверхности зубьев шестерни и колеса; векторы, характеризующие положение осей вращения зубчатых колес; толщина слоя краски. Результатами являются пятна контакта и кривая неравномерности передачи вращения. Все результаты могут быть получены с учетом погрешностей окружного шага или с учетом монтажных погрешностей: осевые смещения колеса и шестерни, гипоидное смещение колеса и ошибка в межосевом угле передачи.
В пятый блок «Анализ под нагрузкой» входят программные модули, предназначенные для анализа работы нагруженной передачи. Основу анализа составляют контактные давления. Входной информацией служат таблично заданные на сетках поверхности контактирующих зубьев, положение осей вращения колес, передаваемый крутящий момент и физические свойства материалов: коэффициенты n Пуассона и модули E упругости контактирующих зубьев. В результате на каждой фазе зацепления зубьев определяется форма мгновенной контактной площадки, суммарное пятно контакта, распределение по нему контактных давлений, значение максимального контактного давления. Алгоритм учи- тывает двухпарность контакта. Предусмотрена возможность учета влияния погрешностей окружного шага, а также технологических и монтажных погрешностей.
Шестой блок «Напряженное состояние» составляют программные модули, которые позволяют рассчитывать напряженное состояние зубьев в районе галтели с учетом их реальной формы и реальной нагрузки, действующей на зубья. Рассчитываются компоненты матрицы влияния нагрузки на напряженное состояние зуба.
С помощью модулей «Напряженное состояние» определяется максимальное растягивающее напряжение в районе галтели в любом сечении зуба на каждой фазе зацепления. В результате находится опасное сечение зуба и максимальное растягивающее напряжение в этом сечении.
В качестве критерия прочности и долговечности зубчатой передачи также может быть принята интенсивность напряжений.
Программный модуль «Оболочка» предназначен для объединения программных блоков в единое целое и обеспечения пользователю удобного интерфейса. В оболочку включена подпрограмма подготовки отчета, который составляется автоматически в виде документа MS Word. В него входят исходные данные, результаты расчетов по вызванным программным модулям и карту наладок конкретных станков. Оболочка позволяет легко добавлять новые и удалять временно неиспользуемые модули в зависимости от пожеланий заказчика.
Пример расчета. Приведем некоторые результаты работы модулей ПК «Эксперт» на примере конической передачи с круговыми зубья-
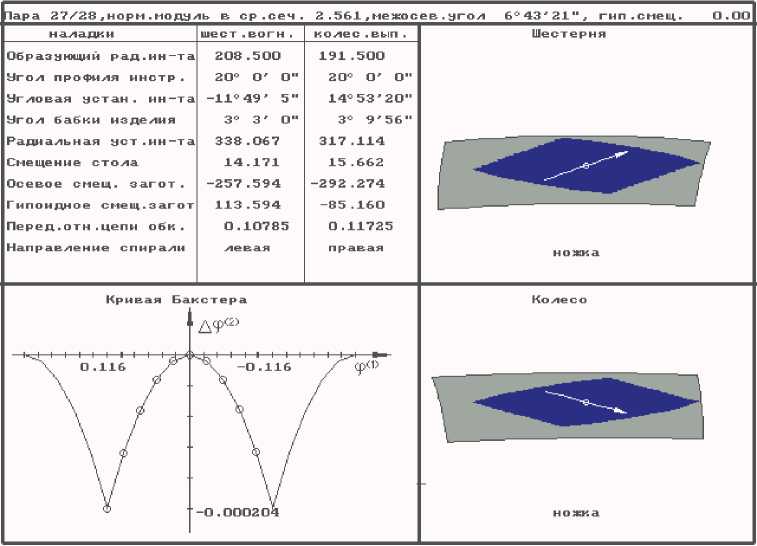
Рис. 2. Значения наладок и результаты предварительного анализа
ми (числа зубьев 27:28) с малым межосевым углом, равным 6° 43' 21", модуль средний нормальный 2,56 мм, рабочая сторона зуба шестерни вогнутая. Ширина зубчатого венца 20 мм, среднее конусное расстояние 693,55 мм.
На рис. 2 приведены результаты работы некоторых модулей первого блока для указанной передачи. Для получения локализованного пятна контакта была введена модификация обкатки со значением коэффициента модификации Кm = 0,4.
Слева вверху на рис. 2 приведены значения универсальных наладок, под ними – кривая Бакстера, т.е. график неравномерности передачи вращения одной парой зубьев (по оси абсцисс – угол поворота шестерни в радианах, по оси ординат – ошибка в угловом положении колеса в радианах по сравнению с положением колеса при равномерной передаче вращения); справа вверху – пятно контакта на вогнутой стороне зуба шестерни, под ним – пятно на выпуклой стороне зуба колеса.
Следует обратить внимание, что для обработки не случайно выбран инструмент диаметром d 0 = 400 мм. Действительно, при использовании инструмента диаметром менее 400 мм не удается получить прямого сужения вершинных ленточек (имеет место обратное сужение), а при диаметре больше 400 мм получаются наладки (гипоидное смещение заготовки и радиальная установка инструмента), превышающие паспортные данные станка мод. 528С.
На рис. 3 показаны результаты анализа рассматриваемой передачи при действии нагрузочного момента 65000 Н·мм на ведомом валу ко- леса. Пятна контакта при наиболее неблагоприятном сочетании отклонений окружных шагов рабочих сторон зубьев даны на рис. 3 справа.
Справа вверху на рис.3 в виде четырехугольника, окрашенного светло серым цветом, показана цилиндрическая проекция зуба шестерни на осевую плоскость. Справа внизу изображена аналогичная проекция зуба колеса. Оси вращения шестерни и колеса горизонтальны. Внешние торцы зубьев расположены слева, внутренние – справа. Полосы различных цветовых оттенков, изображенные на проекциях зубьев на рис. 3, – это наложенные одна на другую мгновенные контакта эллипсы в различных фазах зацепления. При движении в процессе зацепления центры эллипсов описывают рабочую линию, которая на рис. 3 показана темным цветом и пересекает все мгновенные контактные эллипсы. Объединение всех мгновенных контактных эллипсов представляет пятно контакта. На рис. 3 слева внизу – представлена кривая неравномерности передачи вращения или кривая Бакстера.
На рис.4 приведены графики зависимости максимального контактного давления и парциального (нормального) усилия на зуб от угла поворота шестерни. Максимальное в процессе зацепления контактное давление на рабочей стороне зуба оказалось равным 1144 Н/мм2.
Значения наладочных параметров на рис. 2 и результаты анализа, приведенные на рис. 3-4, показывают возможность изготовления передачи с межосевым углом 6° 43' 21" с локализованным контактом на станке мод. 528С благодаря использованию механизма модификации.
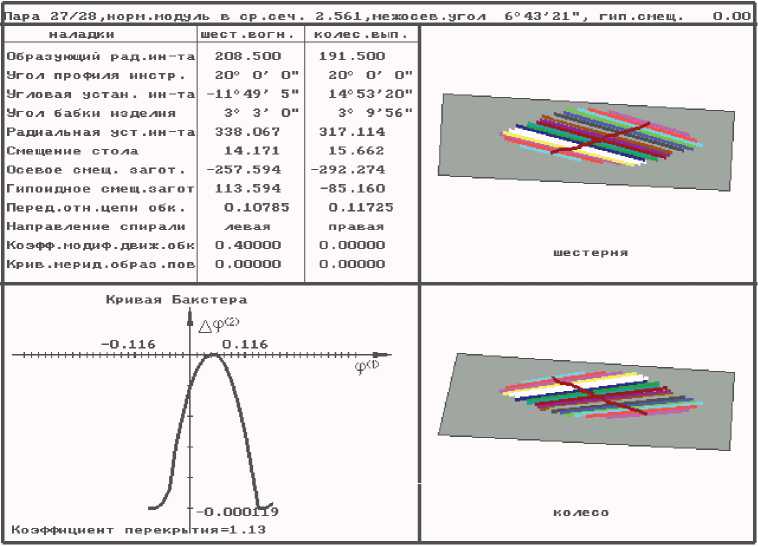
Рис. 3. Пятна контакта рабочих сторон зубьев под нагрузкой с учетом погрешности окружных шагов зубьев
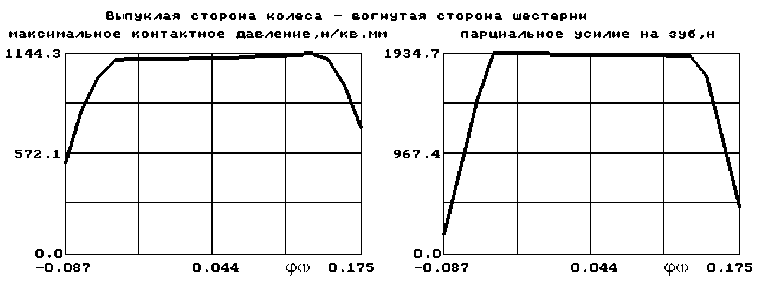
Рис. 4. Результаты работы модулей блока «Анализ под нагрузкой»
С помощью ПК «Эксперт» рассчитано и проанализировано несколько десятков передач, в основном для авиационной промышленности и машиностроения. Значительная часть из них изготовлена.
Список литературы Компьютерная подготовка производства конических авиационных передач
- Волков А.Э., Медведев В.И. Проектировочные и технологические расчеты конических передач с круговыми зубьями. Учеб. пособие. М.: Изд-во МГТУ "Станкин", 2007. 151 с.
- Волков А.Э., Медведев В.И., Романчук Ф.М. Использование измерительной техники для воспроизведения поверхностей круговых зубьев конических колес//Измерительная техника. 2006. № 8. С. 33-37.
- Кедринский В.Н., Писманик К.М. Станки для обработки конических зубчатых колес. -М.: Машиностроение, 1967. 584 с.
- Лопато Г.А., Кабатов Н.Ф., Сегаль М.Г. Конические и гипоидные передачи с круговыми зубьями. М.: Машиностроение, 1977. 424 c.
- Писманик К.М. Гипоидные передачи. Монография. М.: «Машиностроение», 1964. 227 c.
- Хлебалин Н.Ф. Нарезание конических зубчатых колес. Монография. Л.: Машиностроение, 1978. 158 с.
- Шевелева Г.И. Теория формообразования и контакта движущихся тел. -Монография. М.: Изд-во "Станкин", 1999. 494 с.
- Baxter M.L. Basic Geometry and Tooth Contact of Hypoid Gears//Industrial Mathematics. 1961. Vol. 11. P. 19-42.
- Litvin F.L., Fuentes A. Gear Geometry and Applied Theory. Cambridge: Univer. press, 2004. 800 p.
- Simon V. Load Distribution in Spiral Bevel Gears//ASME J. Mech. Des. 2007. Vol. 129. P. 201-209.