Методы и средства снижения момента трения в узле подвода окислителя рулевого агрегата ракетного двигателя
Автор: Балякин Валерий Борисович, Лаврин Андрей Владимирович
Журнал: Известия Самарского научного центра Российской академии наук @izvestiya-ssc
Рубрика: Механика и машиностроение
Статья в выпуске: 2-1 т.17, 2015 года.
Бесплатный доступ
В данной работе предлагаются методы и средства снижения момента трения узле качания подвода окислителя ракетного двигателя ракеты-носителя «Союз». Выявлены основные трибосопряжения в узле подвода и оценено их влияние на общий момент трения. Намечены основные пути снижения трения во вращающихся элементах.
Момент трения, узел подвода, рулевой агрегат, трибосопряжения
Короткий адрес: https://sciup.org/148203618
IDR: 148203618
Текст научной статьи Методы и средства снижения момента трения в узле подвода окислителя рулевого агрегата ракетного двигателя
Рис. 1. Схема узла подвода окислителя рулевого агрегата:
1 –корпус;
2– подшипник 6-208Ю2;
3– подшипник 6-766907Ю;
4– торцевое уплотнение основной полости;
5 – место присоединения камеры;
6 – манжетное уплотнение;
7- основная полость узла;
8- дренажная полость узла.
Для решения поставленной задачи была составлена функциональная схема узла подвеса и выявлены пять основных трибосопряжений, влияющих на суммарный момент трения, а именно радиально-упорный подшипник 2, два подшипниковых узла 3, торцовое уплотнение 4 и манжетное уплотнение 6.
Была проведена теоретическая оценка вклада выбранных трибосопряжений в суммарный момент трения и построена иерархическая структура влияния. Показано, что наибольший вклад в суммарный момент трения оказывает подпятник в торцовом уплотнении основной полости узла подвода, где осуществляется смазываемый трибоконтакт фторопласт - 4 и сталь 12Х18Н9Л и 12Х18Н10Т. В качестве штатной смазки использу- ется ЦИАТИМ-205, которая согласно последним нормативным требованиям считается недостаточно взрывобезопасной в контакте с жидким кислородом, что требует отработки применения в составе узлов подвода окислителя консистентных смазок новых типов.
Основными методами снижения момента сопротивления в узлах трения являются:
трибологические; технологические; конструктивные и организационные.
Трибологические методы и средства это подбор новых типов смазочных материалов, выбор способа и оптимальных режимов смазки и т.д.
Технологические методы - применение новых материалов, наноструктурированных покрытий, снижение шероховатости поверхностей трения, уменьшение внешних нагрузок на узлы трения.
Конструктивные методы -разработка новых конструкций деталей узлов трения, а также применение перспективных подшипников.
К организационным методам можно отнести разработку, оптимизацию и соблюдение графиков монтажных, испытательных и пусковых работ.
Наибольший эффект при решении поставленной задачи может быть достигнут при комплексном подходе, когда будут использованы все или большинство методов и средств.
В качестве конструктивных методов снижения момента трения в торцовом уплотнении из фторопласта предлагается изменить площадь контактирующих поверхностей, так как момент трения в контакте кольцевых поверхностей зависит от площади поверхности и удельного давления в контакте МТР = n Pfd ( D2 + d 2)/8 [1]. Важно отметить, что и коэффициент трения для фторопласта-4, зависит от удельного давления, поэтому данная задача не является однозначной [2]. Однако вследствие консерватизма заказчиков конструктивные изменения достаточно сложно внедрить в узлы и детали, поэтому необходимо определить наименее затратные методы и решать поставленную задачу поэтапно. Наиболее предпочтительными на наш взгляд являются трибологические и технологические методы и средства снижения трения. Первым этапом при решении поставленной задачи можно оптимизировать тип и режимы смазки. С этой целью была разработана программа исследования влияния типа и режима смазки на коэффициент трения в трибосопряжениии фторопласт-4 и нержавеющая сталь. Испытания проводятся на трибометре швейцарской фирмы CSM (рис. 2). Для обеспечения идентичности условий испытаний различных типов смазок необходимо использовать испытательные образцы из фторопласта-4 изготовленные из одной партии материала с одинаковой шероховатостью. Для этого из партии образцов необходимо выбрать те, у которых ра-
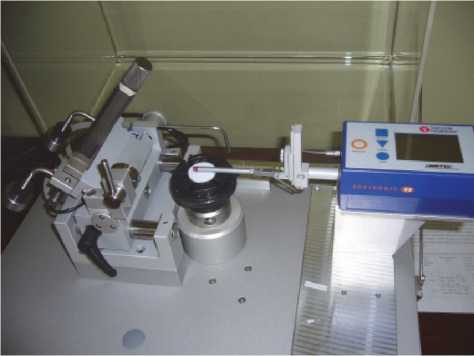
Рис. 2. Внешний вид трибометра с системой измерения шероховатости рабочей поверхности бочие поверхности отличаются по шероховатости не более чем на 0,1 Ra. Очень важно в процессе эксперимента обеспечить режимы, соответствующие рабочим условиям по удельному давлению, скорости скольжения, влажности и температуре. В частности имитировать работу трибосопряжения в среде сжиженного газа и при очень низких температурах. Для этого используется жидкий азот и специальная чаша для испытаний (рис. 3).
Вторым этапом необходимо оценить влияние шероховатости и технологических методов обработки поверхностей трения на силу трения. Известно, коэффициент трения поверхностей зависит от их шероховатости. Причём зависимость коэффициента трения от шероховатости неоднозначна[1], для несмазанных материалов. Для смазанных контактов, эта зависимость ещё более сложная.
Третьим этапом можно исследовать влияние различных физических воздействий на фторопласт-4 с целью снижения трения. Известно, что радиоактивное облучение фторопласта-4 существенно уменьшает коэффициент трения и многократно снижает интенсивность износа рабочей поверхности [3]. В связи с этим предлага-
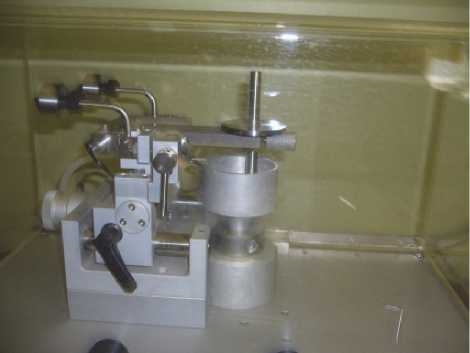
Рис. 3. Внешний вид установки для испытания в жидком азоте ется заменить материал торцового уплотнения на радиационно –модифицированный фторопласт Ф4-РМ20[4].
Однако необходимо провести дополнительные экспериментальные исследования с целью определить трибологические свойства данного материала при условиях работы, соответствующих функционированию узла качания подвода окислителя.
Важным на наш взгляд условием работы трибосопряжений в ЖРД является их функционирование в вакууме, что необходимо исследовать. Для этого на кафедре ОКМ СГАУ смонтирован вакуумный трибометр швейцарской фирмы CSM (рис. 4).
Исследования на данном стенде позволят оценить, как изменится коэффициент трения, а, следовательно, и момент трения во время работы двигателя с набором высоты ракеты. Это необходимо, чтобы оценить достоверность границы допускаемых значений момента трения в узле качания при наземных сдаточных испытаниях.
Существенное влияние на момент трения в опоре узла подвески оказывает трение в радиально-упорных подшипниках. Потери на трение в смазочном слое определяются сопротивлением сдвигу смазки при скольжении и верчении в контактах. Силу и момент трения в эластогидро-динамическом смазочном слое эллиптического контакта определим по формулам работы [5].
Силу трения скольжения в контакте шарика с внутренним кольцом определяют по формуле:
F fcc = n a H b H M o njVJh 0 , (1) здесь а Н = f ( v ) и Ь Н = f ( v ) — полуоси эллипса пятна контакта шарика, где v ■ угол пе-рекоса колец подшипника; μо – вязкость смазки; VS – скорость скольжения в контакте шарика с дорожкой; h0 –толщина слоя смазки ; n f = ((a P m - 1 ) exP VaP m ) + 1^ (a P m ) 2 - пьезокоэффициент трения скольжения,
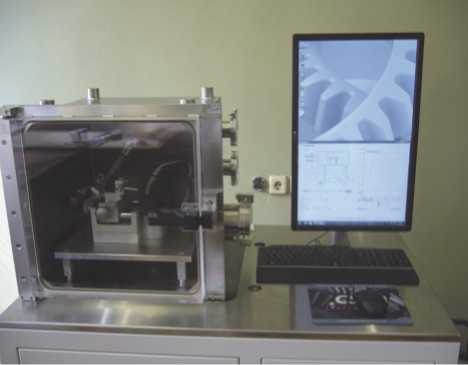
Рис. 4. Внешний вид вакуумного трибометра фирмы CSM при этом: pm = oH при cH < pa и Pm Pa при aH > pa, где pa = 7,914 • 11;518 - давление «затвердевания» смазки, здесь tм – температура смазки, nf = ((apm -X^exp^apm)+^(«Pm)2 -пъезокоэффициент смазки.
Момент трения верчения в эллиптическом контакте определяют по формуле:
Тfcc = n ( a HbH + a H b H К n m ® в/ h 0 .
Здесь nm – пьезокоэффициент трения верчения, определяемый по зависимости:
n = [2exp( g pm ) + 1 — 6 exp( a p m Жфт ) 2 .
m («Pm ) + 6(exP (aPm ) — 1)K«Pm )2 ’
to B - угловая скорость вращения шарика относительно внутреннего кольца.
Согласно данным работы [5], полное значение момента трения верчения получим интегрированием по площадке контакта:
Tfk = 3П^ fFnaH (Чк А )• ^/(16 (1 + m )), (2)
где f – коэффициент трения в контакте, Fn – нормальное усилие в контакте; q и q k – полная и единичная нагрузка в контакте; m = ( aH - bH )/( aH + bH ) ; 5 - значение ряда, вычисляемого по формуле:
m2 m 4 42 m 6 42 • 32 m 8 42 • 32 • 52
=1 + 22? + 22Г42 + 22 • 42 • 62 + 22 • 42 • 62 • 82 + ^
Анализ уравнений (1) и (2) показывает, что для снижения момента трения в подшипнике качения необходимо уменьшать коэффициент трения в контакте и угол перекоса колец подшипника. В связи с этим необходимо провести исследования по влиянию несоосности подшипников в конструкции с целью оценки её влияния на момент трения в опоре.
Предложенные направления исследований не являются полными и всеобъемлющими, поэтому в дальнейшем могут быть рассмотрены и другие пути снижения момента трения в узлах качания подвода окислителя и горючего жидкостного ракетного двигателя.
Список литературы Методы и средства снижения момента трения в узле подвода окислителя рулевого агрегата ракетного двигателя
- Жильников Е.П., Самсонов В.Н. Трение и изнашивание в узлах авиационной техники./Е.П. Жильников. Самара: Изд. Самарского аэрокосм. ун-та. -2007. 143 с.
- Крагельский И.В. Основы расчётов на трение и износ/В.Крагельский, М.Н. Добычин, В.М. Камбалов. М.:Машиностроение,1977. 487 с.
- Прикладная трибология (трение, износ, смазка)/Ю.Н. Дроздов, Е.Г. Юдин, А.И. Белов. М.: Эко-Пресс. 2010. 604с.
- Новый класс износостойких материалов, полученных радиационной модификацией политетрфторэтилена в расплаве/С.А.Хатипов, С.А. Серов, Н.В. Садовская//Вопросы материаловедения. 2012. №4. С.191-201
- Теория и проектирование опор роторов авиационных ГТД/В.Б. Балякин, Е.П. Жильников, В.Н. Самсонов, В.В. Макарчук. Самара: Изд. Самарского аэрокосм. ун-та. 2007. 253 с.