Модель системы автоматического управления процессом перемешивания пульпы перед флотацией
Автор: Осипова Н.В., Пипия Д.В.
Журнал: Горные науки и технологии @gornye-nauki-tekhnologii
Рубрика: Энергетика, автоматизация и энергоэффективность
Статья в выпуске: 1, 2018 года.
Бесплатный доступ
В статье приведен краткий обзор исследований по вопросам автоматизации флотационного обогащения. Выявлены основные недостатки существующих систем и способов регулирования параметров данного процесса, которые заключаются в низком быстродействии, ошибках выработки управляющего воздействия и отсутствии стабилизации плотности пульпы в перемешивателе. В связи с этим приводится вывод об актуальности разработки САУ процессом перемешивания пульпы перед флотацией, которая позволит поддерживать на заданном уровне указанную переменную. В качестве метода исследования выбрано моделирование с применением пакета прикладных программ Matlab Simulink. При этом дается математическое описание таких элементов модели САУ, как клапан, перемешиватель, насос, ПИД-регулятор. В результате моделирования получены временные диаграммы, отражающие принцип стабилизации плотности пульпы манипуляцией расхода воды в перемешиватель при скачкообразном изменении плотности твердой фазы в пульпе и ее расхода. Приводятся выводы о возможности использования САУ в составе АСУ ТП на горнорудных предприятиях, так как работа модели системы показала удовлетворительные результаты по управлению плотностью с малым перерегулированием и временем регулирования.
Флотация, перемешиватель, флотируемость, аэрация, концентрат, хвосты, обучающая выборка, клапан, регулятор, плотномер
Короткий адрес: https://sciup.org/140230116
IDR: 140230116 | DOI: 10.17073/2500-0632-2018-1-108-112
Текст научной статьи Модель системы автоматического управления процессом перемешивания пульпы перед флотацией
В последние годы деятельность горно-обогатительных комбинатов направлена на переработку бедного по минералогическому составу рудного сырья, что существенно усложняет технологию производства. Поэтому для получения стабильно высоких показателей автоматизация технологических процессов обогащения полезных ископаемых играет важную роль. От содержания металла в обрабатываемом материале во многом зависят технико-экономические показатели работы горно-обогатительного комбината.
Процесс флотации железной руды является одним из универсальных методов, позволяющих получить высокое содержание железа в концентрате путем удаления большей части пустой породы [12 - 17, 20 - 23]. При флотации происходит разделение мелких твердых частиц в пульпе или растворе вследствие избирательной концентрации минералов на границах раздела фаз [1, 9].
Основными факторами, влияющими на флотационное обогащение, являются:
ар - содержание металла в руде, ур -флотируемость сырья, d ср - гранулометрический состав измельченного продукта обогащения, рп - плотность исходного питания, p i - концентрация ионов реагентов в суспензии, h 1 , h 2 - уровень пульпы и пены, Y n - производительность флото-колонн, k а - степень аэрации пульпы и др. [ 4].
В качестве выходных показателей процесса флотации обычно выступают содержание металла в концентрате ак и хвостах α х , производительность установки Q уст . , выход концентрата Yк и хвостов Yх [4].
При этом у р , d ср , рп представляют из себя возмущающие факторы и во многом зависят от нестабильности физикомеханических свойств пульпы. Ее плотность рп - один из основных параметров контроля и регулирования процесса флотации, в то время как переменные ур, d ср являются достаточно трудно измеряемыми и управляемыми.
Проблеме автоматизации процесса флотационного обогащения посвящено
Национальный исследовательский технологический университет достаточно много исследований. Среди последних можно выделить работы [2, 6, 7], где описаны способы управления и контроля параметров флотации. Их суть заключается в формировании «обучающей выборки», которую используют для выявления взаимосвязи входных факторов, оказывающих влияние на данный процесс, и содержания полезного компонента в продуктах флотации. Управление также может быть основано на «правилах нечеткой логики» [18].
Недостатками указанных способов являются необходимость «переобучать» систему при изменении сортов руды, поступающей на фабрику, и слишком большое количество входных переменных, что увеличивает время работы алгоритма и ошибки выработки управляющего воздействия. Также указанные способы не предполагают стабилизацию параметра рп в перемешивателе.
Поэтому создание системы автома- тического регулирования, которая позволит поддерживать на заданном уровне плотность пульпы, поступающей на флотацию, является актуальной задачей.
Известно [4], что стабилизация данного параметра может осуществляться за счет изменения расхода воды в поток или емкость.
На рис. 1 показана схема модели САУ процессом перемешивания пульпы при подготовке к флотации Михайловского ГОКа. Структурная схема и пере- чень технических средств для данной системы изложены в статье [5].
Модель представлена следующими звеньями:
-
• регулируемый клапан с электроприводом с передаточной функцией по
каналу положение - расход воды B :
W %.B ( Р ) =
k к
Т к Р + 1,
где k к - коэффициент передачи клапана, (м3/ч)/%; Тк - постоянная времени, Т = 0,3 мин;
к
-
• нелинейная часть модели клапана с блоком ограничения его открытия от 0 до 100 % [3, 11];
-
• передаточная функция перемеши-вателя WB + Q Рп ( p ) по каналу сумма расхода воды B и твердой фазы Q - плот-
- ность пульпы в перемешивателе рп :
W B + Q _ Р п ( Р ) = T^. (2)
k = __РТВ__ Т = k V п B Ртв + Q ’ п п п’
где kп - коэффициент передачи переме-шивателя, (т/м3)/(м3/ч); Тп - постоянная времени, мин; ртв - плотность твердой фазы пульпы, (т/м3); Vn - объем рабо- чего пространства перемешивателя, V. = 3 м3[4];
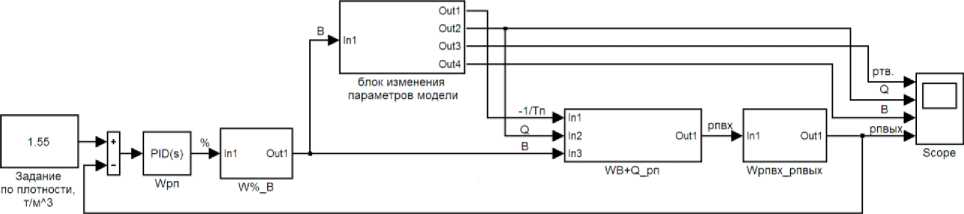
Рис. 1. Схема модели САУ процессом перемешивания пульпы перед флотацией
Национальный исследовательский технологический университет
-
• модель насоса имеет передаточную функцию по каналу плотность пульпы на входе ρ – плотность пульпы на выходе ρпвых [11]:
W p_p. -( Р ) =;, (4)
пвх пвых н где k – коэффициент передачи насоса, принятый равным 1, т.к. при прохождении через него пульпа плотность не меняет; T – постоянная времени, T = 0,0667 мин [10].
Коэффициент передачи клапана рассчитывался как отношение наибольшего расхода воды в перемешиватель Втах = 340 м3/ч к максимальной степени max открытия клапана, равной 100 %:
к = -B max- = 3,4 ( м 3 /ч ) /%. (5)
к 100%
Коэффициенты k и T были найдены по формуле (3), исходя из средних значений плотности твердой фазы пульпы ртв = 5 т/м 3 , ее максимального расхода О пах = 300 т/ч и расхода воды B шах = 340 м 3 /ч : к п = 0,15 ( т/м 3 ) / ( м 3 /ч ) ;
Тп = 0,45 мин.
Параметры B max , ρтв, Q max , V п взяты из характеристик оборудования и лабораторного анализа сырья Михайловского ГОКа.
Настройка регулятора плотности пульпы осуществлялась по критерию «модульного оптимума». Для компенсации двух наибольших постоянных времени T и T был выбран ПИД-регулятор с передаточной функцией [8, 19]:
W(Р)= kp + kdP + ki -, (6)
p где kp , k , k – коэффициенты пропорциональности, дифференцирования и интегрирования регулятора соответственно, kp = 1160,79; kd = 207,05; k, = = 1568,67 мин" 1.
В блоке «Изменение параметров модели» случайным образом варьировались величины ρтв и Q , которые рассматривались как возмущающие факторы, приводящие к колебаниям плотности пульпы.
Результаты моделирования приведены на рис. 2. Скачкообразное увеличение плотности твердой фазы ρтв с 5 до 5,5 т/м3 при 6 = 5 мин вызывает рост плотности пульпы ρ . Регулятор ее стабилизирует увеличением расхода воды B с 57 до 62 м3/ч. Если ρ снижается с 5,5 до 5 т/м3, а Q – с 300 до 250 т/ч при t 2 = 10 мин, то плотность пульпы также уменьшается, и регулятор компенсирует это уменьшением расхода воды до 47 м3/ч. В момент времени t 3 = 15 мин , неизменной величине Q = 250 т/ч и скачке плотности ρ с 5 до 5,5 т/м3 расход воды становится еще больше и достигает 51 м3/ч. Перерегулирование по выходной переменной ρ не превышает 0,5 %, а время регулирования составляет 1 мин, что меньше периода изменения свойств пульпы, который при моделировании принят равным 5 мин.
Заключение
Предложенная в данной статье модель САУ процессом перемешивания пульпы позволяет исследовать влияние таких факторов, как плотность и расход твердой фазы суспензии, на плотность пульпы, поступающей на флотацию.
Результаты моделирования показали, что в условиях нестабильности физико-механических свойств руды данная система поддерживает на заданном уровне плотность пульпы в перемешивателе. При этом величина перерегулирования
Национальный исследовательский технологический университет
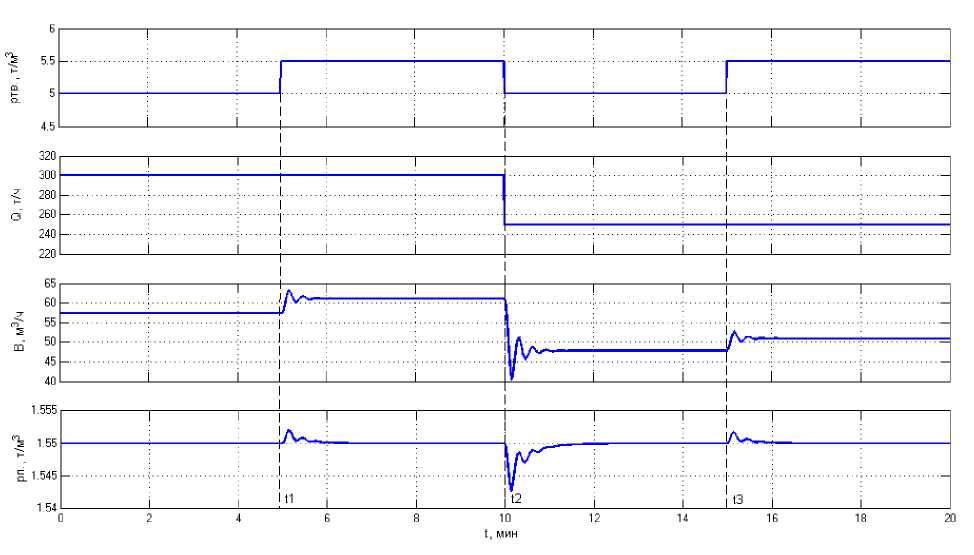
Рис. 2. Переходные процессы изменения расхода воды В и плотности пульпы ρп при скачкообразном изменении плотности ρтв и расхода по твердому Q
достигает 0,5 %, а время регулирования процесса меньше периода изменения свойств пульпы и составляет 1 мин.
Таким образом, доказана целесообразность применения САУ перемешиванием в составе АСУ ТП на горнорудных предприятиях при подготовке к флотационному обогащению.
Национальный исследовательский технологический университет
such model elements of the ACS, as a valve, agitator, pump, PID controller. The result of simulation timing diagram reflecting the principle of stabilization of the pulp density by manipulation of the water flow in the mixer by an abrupt change in the density of the solid phase in the slurry and its flow. At the end of the paper the conclusions about possibility of use of ACS in the industrial control system at mining enterprises, as the work model of the system showed satisfactory results for the control density with a small overshoot and time regulation.
Список литературы Модель системы автоматического управления процессом перемешивания пульпы перед флотацией
- Свириденко А.О., Беляков С.А. Средства автоматизации в технологическом процессе флотации руд полезных ископаемых//Записки Горного института. -2011. -Т. 192. -С. 183-186.
- Курчуков А.М. Автоматизированная система управления процессом флотации медно-никелевых руд на основе оптимизации параметров ионного состава и пенообразования: Дис.... канд. техн. наук. -Санкт-Петербург: 2011, ФГБОУ ВПО Санкт-Петербургский государственный горный университет. -160 c.
- Мандра А.Г. Анализ связанной системы автоматического регулирования уровня воды в баке системы химводоподготовки. URL: http://matlab.exponenta.ru/simulink/book3/10.php (дата обращения: 24.01.2017).
- Марюта А.Н., Качан Ю.Г., Бунько В.А. Автоматическое управление технологическими процессами обогатительных фабрик: Учеб. для вузов. -М.: Недра, 1983. -277 с.
- Осипова Н.В., Пипия Д.В. Система автоматического регулирования плотности пульпы в перемешивателе при подготовке к флотационному обогащению//Горная промышленность. -2017. -№ 3 (133). -С. 92-93.
- Патент РФ № 2567330, 10.09.2016. Куркин В.А., Народицкис А., Бабушкин А.А и др. Способ управления технологическим процессом флотации. 2016. Бюл. № 25.
- Патент РФ № 2567330, 10.11.2015. Зимин А.В., Арустамян М.А. др. Способ автоматического контроля и управления процессом флотации. 2015. Бюл. № 31.
- Певзнер Л.Д. Теория систем управления. -СПб.: Лань. -2013. -440 с.
- Подоляк М.В. Автоматизация процесса флотации золотосодержащих сульфидных руд//Молодежь и наука: Сборник материалов VIII Всероссийской научно-технической конференции студентов, аспирантов и молодых ученых, посвященной 155-летию со дня рождения К.Э. Циолковского . -Красноярск: Сибирский федеральный ун-т, 2012. URL: http://conf.sfu-kras.ru/sites/mn2012/section03.html
- Федюн Р.В., Абакумов А.Ю. Система автоматического управления теплообеспечением спортивного комплекса//Научные труды ДонНТУ. Серия: Вычислительная техника и автоматизация. -2013. -№ 1. -С. 64-71.
- Синтез и моделирование промышленной системы автоматического управления: методич. указ./В.М. Журомский, В.В. Чернокозов. -М.: МГТУ «МАМИ», 2009. -41 с.
- Pikilnyak A. Adaptive control system of the iron ore flotation using a control action based on high-energy ultrasound, Metallurgical and Mining Industry. 2015, no 2, pp. 27-30.
- Knights B.D.H. Performance improvements provided by Mintek’s FloatStar Advanced Control System on reverse-flotation of iron ore//The Southern African Institute of Mining and Metallurgy (SAIMM) 2011 -Iron Ore and Manganese Ore Metallurgy Conference, Johannesburg, South Africa, July 2011, pp. 1-4.
- Daniel Geraldo Cruz, Rosa Malena Fernandes Lima. Influence of Mn2+ ion in reverse cationic flotation of iron ore, Rem: Revista Escola de Minas, 2015, vol. 68, no 3, pp. 319-322. http://dx.doi.o DOI: rg/10.1590/0370-44672015680051
- Hasan Ali Taner, Vildan Onen. Control of clay minerals effect in flotation. A review//E S Web of Conferences, 2016, pp. 1-6. http://conf.sfu-kras.ru/sites/mn2012/section03.html.
- Li Lin, Liu Jiong-tian, Wang Yong-tian, Cao Yi-jun, Zhang Hai-jun, Yu He-sheng. Experimental research on anionic reverse flotation of hematite with a flotation column//The 6th International Conference on Mining Science & Technology, 2009, pp. 791-798.
- Mark Ma. Froth Flotation of Iron Ores. International Journal of Mining Engineering and Mineral Processing, 2012, 1(2), pp. 56-61 DOI: 10.5923/j.mining.20120102.06
- Mauricio Bergerman, Sérgio Coutinho, Filipe Guimarães etc. Optimizing control system for desliming and flotation in an iron ore column flotation at the pico mine//3rd International Meeting on ironmaking and 2nd International Symposium of Iron Ore, 2008, pp. 104-113.
- PID controllers: theory, design, and tuning/Karl Johan Aström and Tore Hägglund. -2nd ed, 1995, 344 p.
- Plinio Eduardo Praes, Rodrigo Oscar de Albuquerque, Antonio Furquim Oliveira Luz. Recovery of Iron Ore Tailings by Column Flotation, Journal of Minerals and Materials Characterization and Engineeringn Ore, 2013, vol. 1, no 5, pp. 212-216.
- Radić R., Milošević Ž., Jurić S., Čudić S. Flotation of ores and waste waters, Metalurgija 2016, vol. 55, no 4, pp. 832-834
- Wen-li Jiang, Hai-feng Xu. Treatment and Recycling of the Process Water in Iron Ore Flotation of Yuanjiacun Iron Mine, Journal of Chemistry, 2017, vol. 2017, pp. 1-8. https://doi.org/10.1155/2017/9187436
- Xianping Luoa, Bo Fenga, Cunjian Wonga, Jiancheng Miaoc, Bin Mac, Hepeng Zhou. The critical importance of pulp concentration on the flotation of galena from a low grade lead-zinc ore, Journal of Materials Research and Technology. 2016, vol. 5, pp. 131-135.