New Protective Coatings Based on Sulfur Nanoparticles Produced from Potassium Polysulfide
Автор: Ismail A. Massalimov, Alexander E.Chuikin, Burkhan I. Massalimov, Akhat G. Mustafin
Журнал: Nanotechnologies in Construction: A Scientific Internet-Journal @nanobuild-en
Рубрика: Technologies for production of construction materials and products
Статья в выпуске: 1 Vol.15, 2023 года.
Бесплатный доступ
Introduction. Impregnation with a new solution based on potassium polysulfide showed excellent results in the hydrophobization of cement stone and cement-sand mortar due to the formation of a nanoscale water-repellent coating on the surface of the pores from sulfur nanoparticles formed as a result of the destruction of the molecule during the drying process. An innovative solution based on potassium polysulfide refers to polysulfur compounds, from which, as a result of the destruction of polysulfide molecules, a nanoscale layer of sulfur particles is formed on the surface. Materials and research methods. Potassium polysulfide solutions of different densities were used for impregnation; the properties of the solutions were tested on cubic samples with a 40 mm edge, made on the basis of cement and cement-sand mortar. Particle characteristics were evaluated using a laser particle size analyzer, an electron microscope and a diffractometer. Results. The analysis showed that the average size of the particles forming the protective coating is 20 nm, they have a spherically symmetric shape and crystallize into an orthorhombic crystal lattice structure. The treatment of concrete with a solution of potassium polysulfide ensures the formation of a coating based on nanosized sulfur on the surface of the pores of the stone, which partially fills the pore space and, being hydrophobic, reduces the water absorption of samples by 2–3 times, and the water absorption of samples impregnated under vacuum for 0.5 hours, decreases to values of 1.3–1.9%. Results and discussion. Modification of concrete with an impregnating composition developed by us with a solution based on potassium polysulfide The impregnating solution based on potassium polysulfide is stable in the concentration range of 1.15–1.35 g/cm3; upon impregnation, it penetrates into the pore structure of concrete at a level of up to 4 cm or more, depending on the growth and structure of the sample. When the material dries in its pores, sulfur nanoparticles crystallize from the polysulfide solution, partially filling the pore space and forming a protective durable insoluble hydrophobic coating that makes it difficult for water to penetrate into the pores of concrete, but retains its vapor permeability, which is important for wall and facing materials. Conclusions. Impregnation of road building materials and concrete products with a composition based on potassium polysulfide improves their performance properties, increases durability and resistance to weathering, which makes it possible to recommend it for use in the climatic conditions of the Russian Federation.
Concrete, sulfur, impregnation, hydrophobization, potassium polysulfide, nanoparticle
Короткий адрес: https://sciup.org/142235803
IDR: 142235803 | DOI: 10.15828/2075-8545-2023-15-1-27-36
Текст научной статьи New Protective Coatings Based on Sulfur Nanoparticles Produced from Potassium Polysulfide
Original article
АPPLICATION OF NANOTECHNOLOGIES AND NANOMATERIALS IN CONSTRUCTION
INTRODUCTION ll known building materials (concrete, brick, slate, Agypsum, limestone, etc.) are porous and hydrophilic; when in contact with water, they are wetted by it, as a result, water easily gets inside the materials. The main reason for the degradation of building structures is the atmospheric-chemical factor. Aggressive chemical and atmospheric components that cause carbonization, sulfate deposition, chloride reactions, freeze-thaw cycles, increased mechanical stress – all this contributes to pore degradation, reduced water resistance and reduces the strength of concrete and other building materials. Water acts as a carrier for all aggressive agents and chemical reactions described above. Therefore, it is not difficult to understand the importance of waterproofing concrete and other building materials.
The most effective way to prevent the degradation of materials is to use various kinds of protective compounds. Now there is a huge number of different protective coatings for building materials, but most of them retain their protective properties for a certain, fairly short (2–3 years) time. Everyone knows the need to re-apply protective materials on the facades of buildings due to the destruction of the previous protective layer. Even more acute is the problem of protecting elements of buildings and structures exposed to hydrostatic water (hydraulic structures, flumes, drains, culverts, etc.), as well as to groundwater (foundations, tunnels, underground structures, etc.).
The building materials market has a huge selection of various protective coatings for building materials and structures. The main problem is that most of them retain their protective properties for a fairly short time. The short service life of the vast majority of protective materials is due to the fact that under atmospheric conditions (solar radiation, rain, snow, hail, alternating temperatures) they quickly lose their properties [1].
In this regard, the problem of creating specialized impregnating compositions that allow maintaining a high level of protective properties of building materials for a long time is very relevant. In works [2, 3], it was proposed to protect building materials by impregnating them with a solution based on calcium polysulfide (“Aquastat” impregnation), intellectual property objects were issued [4, 5], and good results were obtained. The water-repellent effect for a long time is provided by a composition based on calcium polysulfide and is similar to the action of water repellents such as Penetron (USA) and many others based on the principle of pore clogging. The advantages of this type of impregnating compositions, in contrast to organic and organosilicon coatings, are the depth of their penetration into the depth of concrete (more than 10 cm) and mineral nature, which provide reliable and long-term protection of concrete [6, 7]. The limited use of penetrating waterproofing is due to the relatively high cost of the materials used.
The use of penetron and others provides long-term protection of concrete, but water repellents based on calcium polysulfide are universal and protect not only concrete, but also ceramic and silicate bricks, shell rock, aerated concrete. The developed impregnating composition based on sulfur provides protection of building materials from atmospheric influences and aggressive environments for a long time. The technology for processing structural elements and products is simple and affordable: like most paints and varnishes, they are applied by brush, pouring, spraying, immersion at any positive temperatures. The fundamental novelty of the proposed solution lies in the fact that hydrophobization is achieved by using a material of inorganic nature – sulfur. The presence of sulfur in the pores of building materials gives them water-repellent properties for a long time, unlike organic paints and varnishes. The originality of the approach lies in the fact that at the impregnation stage a water-soluble substance is used, in which polysulfide molecules enter the smallest pores of the material. During the drying stage, this substance decomposes, and a water-insoluble (hydrophobic) layer of elemental sulfur forms on the surface of the pores.
The use of deep impregnation solves the main task of protecting building materials – the penetration of water into the pores stops. Water that has fallen on the surface of materials treated with “Aquastat” does not penetrate into the pores even with prolonged contact with water, for example, for foundations when exposed to groundwater, water pressure in hydraulic structures. But, there are a number of issues associated with the production of calcium polysulfide that make it difficult to produce. Firstly, during its production, quite a lot of waste is generated (up to 30% of the initial reagents) and they must be disposed of. Secondly, the calcium polysulfide solution is unstable, and special storage is necessary for long-term storage. In addition, the calcium polysulfide solution has a slight hydrogen sulfide odor.
In this regard, it is proposed to protect building materials a new composition from the family of polysulfides, namely, potassium polysulfide, devoid of the disadvantages inherent in calcium polysulfide. It should be noted that only potassium silicate has been used as a silicate paint on inorganic and organic surfaces to protect building materials from potassium salts [8–12]. Impregnation based on calcium polysulfide belongs to the type of penetrating waterproofing, which protects the material under conditions of constant exposure to water, and therefore is relevant, work in this direction does not stop to this day [13–18].
Potassium polysulfide is a multifunctional product with many practical applications. But it should be noted that solutions of potassium polysulfide have not yet been used for the purpose of hydrophobization of building materials, although they have been known for a long
АPPLICATION OF NANOTECHNOLOGIES AND NANOMATERIALS IN CONSTRUCTION time. They can be obtained by a reaction between sulfur and potassium in a boiling aqueous solution, they are dark red solutions containing potassium polysulfide molecules with the formula K2Sn, where n = 2÷6. It was found in [19] that the formula of the compound is potassium polysulfide K2S3 and that sulfur nanoparticles with an average size of 20 nm can be obtained from it by chemical precipitation. This work formed the basis of the present work. We assumed that if impregnation with a solution based on calcium polysulfide can give building materials (concrete, brick, aerated concrete, etc.) water-repellent properties, then impregnation with potassium polysulfide can give a hydrophobic effect. If impregnation with a solution of potassium polysulfide for building materials gives a hydrophobic effect, it will be more preferable in many cases, since no waste is generated during the synthesis of potassium polysulfide and solutions of sufficiently high concentrations can be obtained. In addition, the potassium polysulfide solution is stable in storage and does not deteriorate for a long time, does not smell of hydrogen sulfide, and therefore is more convenient to use.
MATERIALS AND RESEARCH METHODS
The particle sizes were measured with a Shimadzu SALT 7101 laser analyzer, the particle shape was analyzed with a Solver PRO-M probe microscope, and the structural and thermal characteristics were analyzed with a Rigaku Ultima IV X-ray diffractometer.
For impregnation, solutions of different densities were used – in Fig. 1a shows 1.33 g/m3 (flask on the left) and 1.18 g/cm3 (flask on the right). Sample cubes with a cement stone edge of 40 mm were made on the basis of cement TsEM II V-K (Sh-I) 42.5N (GOST 311082020) with a water-cement ratio W/C = 0.32, hardening time – 28 days. Similar samples of cement-sand mortar were prepared on the basis of cement CEM II V-K (Sh-I) 42.5N and sand with fineness modulus Mk = 1.4 at a ratio
(cement: sand) = 1:3.5 at a water-cement ratio B/C = 0.52, hardening period – 28 days.
RESULTS AND DISCUSSION
To protect building materials, the hydrophobic effect of sulfur, which is characteristic of this chemical element, is used (Fig. 1b). But to protect materials from the effects of water, it is necessary that sulfur covers the entire surface of the material, including the surface of the pores. For this purpose, sulfur is transferred to a liquid state, in which sulfur is in the form of polysulfide molecules (Fig. 1a). The originality of this approach lies in the fact that at the impregnation stage a water-soluble substance (polysulfide) is used, in which sulfur molecules enter the smallest pores of the material. During the drying stage, this substance decomposes, and a water-insoluble hydrophobic layer of elemental sulfur forms on the surface of the pores.
Figure 1c shows the transition from the polysulfide state (lower part of the figure) to the state of transition to elemental sulfur in the form of a hydrosol (Fig. 1c). When analyzing protective materials, the distribution of the impregnating solution over the surface of the material is considered. To analyze the particle size and shape, it is convenient to examine the images with a transmission microscope that appeared on the glass surface after the application of a potassium polysulfide solution. In Fig. 1c, the solution begins to become cloudy, and the transition from potassium polysulfide molecules to sulfur nanoparticles begins.
Figure 2 shows images obtained on glass at 40x magnification (2a) and at 100x magnification (2b) 4 hours after treatment; these objects also contain water along with potassium polysulfide molecules. In the process of processing building materials, a polysulfide solution is applied to the material, penetrates into the pores. As the solution dries, water is removed, dispersed sulfur remains on the surface and gives its hydrophobic effect. It can be seen from Fig. 2 that in all cases, spherically symmetrical
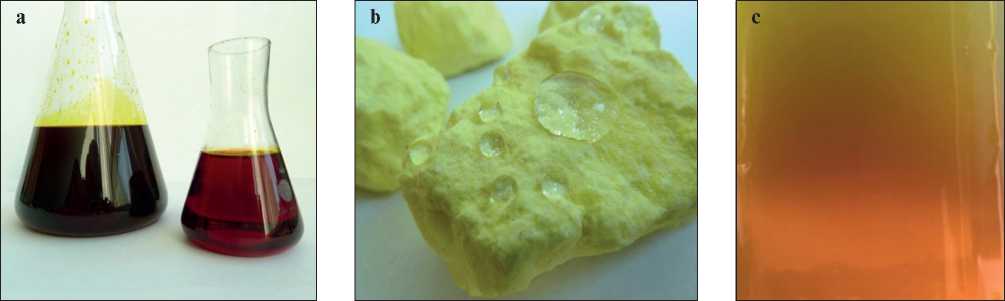
Fig. 1. Potassium polysulfide solutions of different concentrations (a), image of lump sulfur (b), and image of sol-gel transition of potassium polysulfide (c)
АPPLICATION OF NANOTECHNOLOGIES AND NANOMATERIALS IN CONSTRUCTION
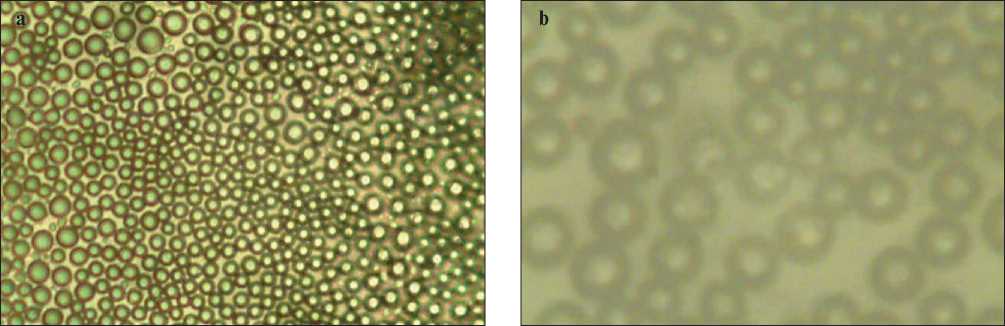
Fig. 2. Image of particles deposited on a glass substrate from a solution of potassium polysulfide: a – 40-fold increase; b – 100-fold increase
objects (a mixture of potassium polysulfide and water molecules) are formed on the surface, uniformly distributed over the surface.
It also turned out that when removing sulfur particles from the glass surface (Fig. 2) and measuring their sizes in a laser particle size analyzer, the particles in the aquatic environment decompose into sulfur particles with an average size of 20 nm. The discovered fact indicates that Fig. 2 shows agglomerates consisting of sulfur nanoparticles with an average size of 20 nm. Earlier for calcium polysulfide, it was found [20] that, when diluted with water, a sulfur hydrosol is formed from it; similarly, for a solution of potassium polysulfide, cloudiness of the solution was experimentally found (Fig. 1с).
Measurements on a laser analyzer showed that sulfur nanoparticles with an average size of 20 nm are formed in an aqueous medium (see Fig. 3a). Further, particles of sulfur powder were isolated from the aqueous medium and measurements were taken on an electron microscope; determination of their sizes showed that the main part of the sizes lies in the range of 20–30 nm (see Fig. 3b). X-ray phase analysis of these powder particles isolated from the hydrosol showed that it corresponds to the sulfur diffraction (Fig. 4)
Thus, nanoparticles 20 nm in size are deposited from a solution of potassium polysulfide, just as from a solution of calcium polysulfide, and are evenly distributed over the surface of the material. To illustrate the possibilities of potassium polysulfide solution as a method of protecting building materials, experimental data obtained for concrete materials tested under various conditions are presented. The potassium polysulfide solution is supposed
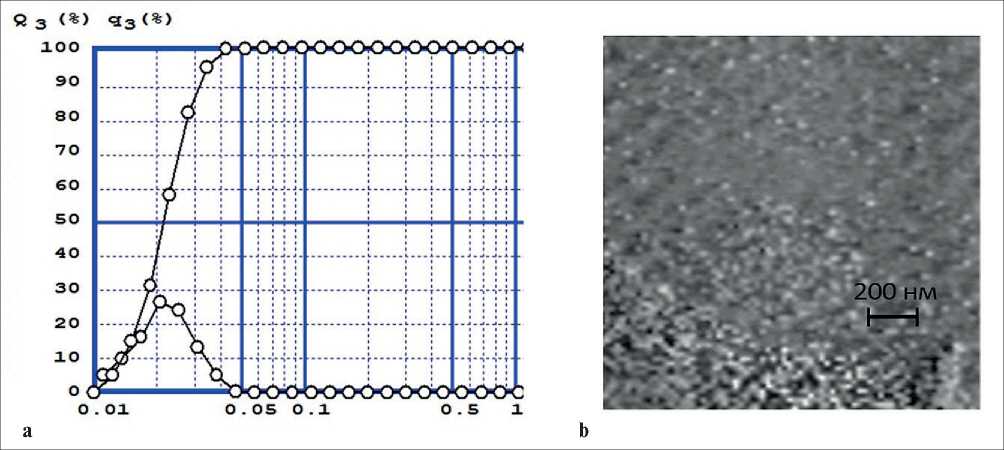
Fig. 3. Size distribution of sulfur particles isolated from potassium polysulfide by diluting it with water. Differential curve from below and integral curve from above (a) and image of powder of sulfur nanoparticles (b)
АPPLICATION OF NANOTECHNOLOGIES AND NANOMATERIALS IN CONSTRUCTION
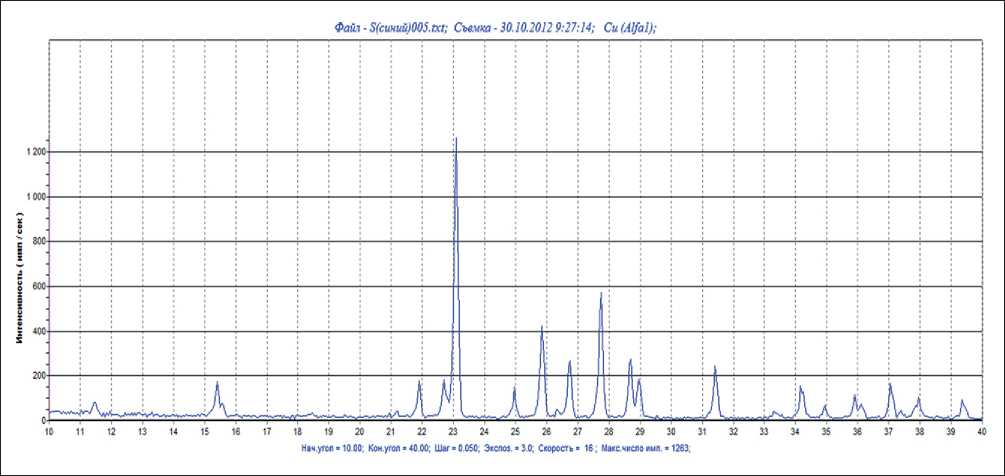
Fig. 4. X-ray phase analysis of sulfur
to be used in the same way as Aquastat, which is based on a calcium polysulfide solution, which is used mainly to protect building materials that are operated under conditions of constant exposure to moisture. Therefore, a study was made of the effect of impregnation with this composition on the water absorption of cement and sand-concrete samples by immersing them in a bath with a solution of potassium polysulfide.
Figure 5 shows experimental data on the measurement of water absorption by weight (Wm) for samples-cubes of cement stone impregnated by immersion in a bath filled with a solution based on potassium polysulfide for 1, 2, 4 hours, and also after vacuum impregnation at a temperature 22±1oC. The first column “untreat” means the observed water absorption from the unimpregnated sample. Columns with signs 1, 2, 4 hours correspond to immersion treatment for 1, 2 and 4 hours and corresponding values of the water absorption parameter from them. In addition, the last column with the sign “vacuum” corresponds to the value of water absorption from samples that were
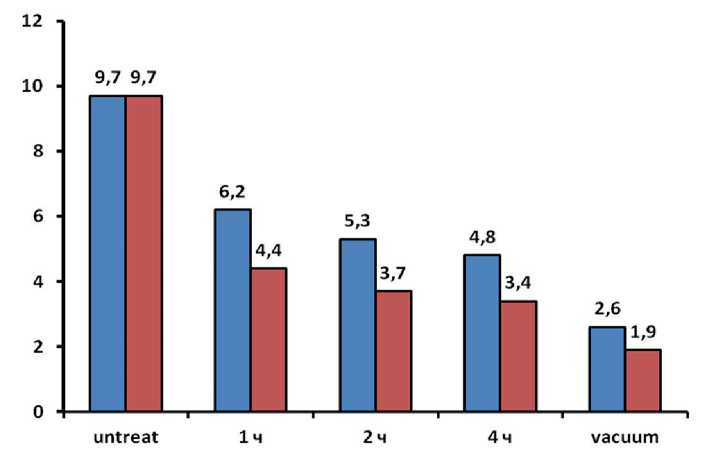
Fig. 5. Dependence of water absorption by weight of cement stone samples on the method of impregnation with solutions with a density of 1.18 g/cm3( ■ ) and 1.33 g/cm3 ( ■ )
АPPLICATION OF NANOTECHNOLOGIES AND NANOMATERIALS IN CONSTRUCTION previously evacuated before treatment with a solution. For samples of cement stone, it was found that the first treatment for 1-hour leads to a decrease in water absorption to 6.2%, treatment for 4 hours leads to a decrease in water absorption to 4.8%. A further increase in the duration of the impregnation did not lead to any significant decrease in water absorption below the value of 4.8%. Therefore, the water absorption of samples previously evacuated before treatment with a solution was measured, as a result, a water absorption parameter value of 2.6% was obtained.
In Fig. 5 also shows a diagram of the dependence of the water absorption parameter by weight of cement stone samples on the method of treatment with a solution with a density of 1.33 g/cm3. Treatment with a denser solution led to a more significant decrease in the values of the water absorption parameter: it was found that the first treatment for 1 hour leads to a decrease in water absorption to 4.4%, and treatment for 4 hours leads to a decrease in water absorption to 3,4%.
The influence of treatment with a solution based on potassium polysulfide on cement-sand samples is also considered. Figure 6 shows the dependences of the water absorption parameter by weight for samples of cementsand samples on the method of treatment with solutions with densities of 1.18 g/cm3 and 1.33 g/cm3. From the data shown in Fig. 6, it can be seen that an increase in the holding time in the solution and an increase in the density of the solution lead to a decrease in the amount of absorbed water.
It was found that the water absorption parameter of the samples, pre-evacuated before treatment with a more concentrated solution, makes it possible to reduce the value of the water absorption parameter, equal to 1.9%. Figure 7 shows the dependence of the penetration depth of cementsand stone samples on the method of impregnation with a solution with a density of 1.33 g/cm3. Fig. 7a shows a general view of the impregnated sample, and Fig. 7b shows a cleavage of a sample impregnated for 4 hours, it can be seen from it that the potassium polysulfide solution has a good penetrating ability, during the impregnation, equal in time to 4 hours, it penetrates to a depth of 2 cm. Using the pre-vacuum method, it penetrates to the entire depth (see Fig. 7c) within 15 minutes of impregnation
In general, the values of the water absorption coefficient for a cement sample are higher than for cement-sand samples. Thus, we observe a significant decrease in the water absorption parameter when treated with a solution based on potassium polysulfide of different density, and the results are better for a more concentrated solution. The results of the experiment show that impregnation based on potassium polysulfide can be used to protect against the negative effects of water in industrial and civil construction. As the main impregnating composition, it can be used to protect all structural elements exposed to intense moisture: foundation blocks, well rings, culverts, sleepers, wall sections, piles, arches, ceilings, curbstones, paving slabs. Impregnation based on potassium polysulfide provides reliable penetrating waterproofing of building structures by using the dipping method and the application method on facade surfaces on various building materials. Moreover, the method of hydrophobization with a composition based on potassium polysulfide is suitable both for recently created materials and for structures that have existed for more than a dozen years.
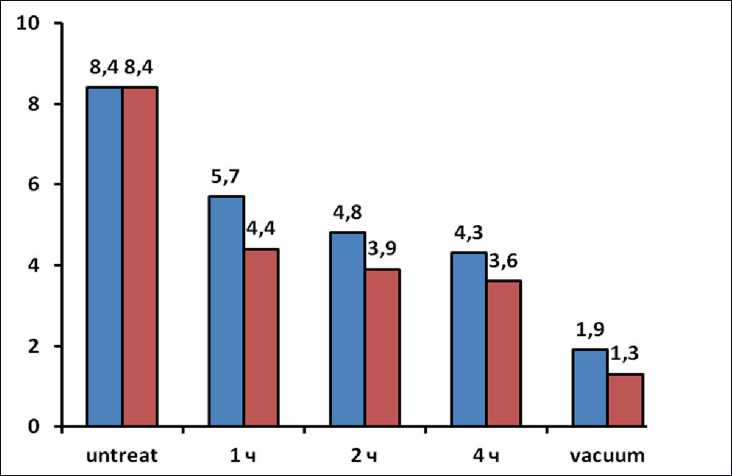
Fig. 6. Dependence of water absorption by weight of cement-sand stone samples on the method of impregnation with solutions with a density of 1.18 g/cm3 ( ■ ) and 1.33 g/cm3 ( ■ )
АPPLICATION OF NANOTECHNOLOGIES AND NANOMATERIALS IN CONSTRUCTION
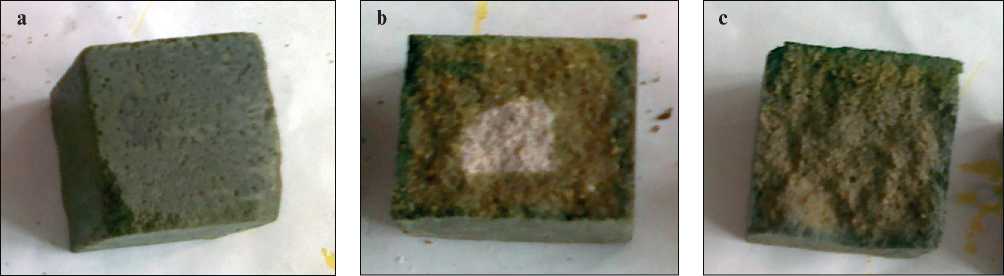
Fig. 7. Dependence of the depth of penetration of samples of cement-sand stone on the method of impregnation with a solution of density and 1.33 g/cm3: a – appearance of the impregnated sample; b – soaked for 4 hours;
c – impregnated using the method of preliminary evacuation
It should be noted that along with the above methods of protecting building structures using penetron and similar materials, attempts were made to protect building materials using impregnation with monomers and sulfur melts [21–24]. Despite the fact that the impregnation with monomers has shown good results, its practical application is limited due to the high cost; impregnation with molten sulfur has become more widespread. As a result of impregnation with molten sulfur, the density and mechanical characteristics of concrete increase, water resistance, frost resistance and chemical resistance increase. At the same time, the use of a large-capacity sulfur product obtained in the processes of oil and gas desulphurization as an impregnating material is also characterized by a number of undeniable advantages, including a rather low cost of sulfur compared to monomers used for the manufacture of concrete polymers.
The impregnation of sulfur-impregnated concrete is characterized by a lower energy intensity, as well as a lower complexity of the technological process than the production of a concrete polymer. All this, as well as the need to utilize the excess amount of sulfur accumulated at the enterprises of the gas and oil industries, contributed to the resumption of studies carried out back in the 20s of the last century on the study of the properties of concrete impregnated with molten sulfur, but then did not find practical application due to the high sulfur cost. Impregnation of materials with molten sulfur includes a number of successive technological processes: heating of sulfur to 150oC; drying and heating of products at a temperature of 130–140oC; immersion of products in the melt and impregnation; extraction of products from the sulfur melt and their cooling. For effective impregnation with molten sulfur, it is necessary to use a sealed bath equipped with a vacuum system.
As practice has shown, the method of impregnating concrete products with molten sulfur also has the following disadvantages. Firstly, in order to impregnate with a sulfur melt, it is necessary to heat both sulfur and concrete products to a temperature of 140–150oC, which significantly increases the energy intensity of the process. In addition, heating products to such temperatures can cause stress in the material and lead to a decrease in strength. Secondly, due to the relatively high viscosity of the sulfur melt, it is necessary to use vacuum or overpressure, which significantly complicates and increases the cost of the sulfur melt impregnation technology.
The use of a composition based on potassium polysulfide is an alternative method that solves the problem of creating reliable protective and durable coatings for building materials. As a means of long-term protection of building materials, it is proposed to treat the porous surfaces of building materials with a new sulfur-containing composition. The developed impregnating composition based on sulfur provides protection of building materials from atmospheric influences and aggressive environments for a long time. The technology for processing structural elements and products is simple and affordable: like most paints and varnishes, they are applied by brush, pouring, spraying, immersion at any positive temperatures.
Thus, the results show that a new method has been proposed for the long-term protection of building materials from water penetration in conditions of its constant presence using potassium polysulfide, which complements the class of polysulfide water repellents based on calcium polysulfide. The fundamental novelty of the proposed solution lies in the fact that hydrophobization is achieved using a material of inorganic nature – sulfur. The presence of sulfur in the pores of building materials gives them water-repellent properties for a long time – unlike organic paints and varnishes.
The novelty of the approach lies in the fact that at the impregnation stage a water-soluble substance is used, in which sulfur molecules enter the smallest pores of the material. During the drying stage, this substance decomposes and a water-insoluble (hydrophobic) layer of elemental sulfur forms on the surface of the pores. The use of deep impregnation allows, along with an increase in strength and
АPPLICATION OF NANOTECHNOLOGIES AND NANOMATERIALS IN CONSTRUCTION frost resistance, a decrease in water absorption, to significantly increase resistance to atmospheric factors, as well as to acids, salt solutions, and petroleum products. The mineral nature of the coating ensures its durability, and the water-repellent properties inherent in elemental sulfur block the access of water. Surfaces treated with the proposed composition acquire not only hydrophobic properties, but also pronounced bactericidal properties, as a result, the processes of decay and mold formation are prevented.
CONCLUSIONS
The images presented in Fig.1 indicate that the natural hydrophobic properties of sulfur (Fig.1b) make it possible for sulfur to be converted into potassium polysulfide molecules (Fig. 1a), as in the case of calcium polysulfide. At the impregnation stage, a water-soluble substance is used, in which sulfur molecules enter the smallest pores of the material and turn into sulfur hydrosol (Fig. 1c). It has been experimentally established (Fig. 2) that the impregnating solution is evenly distributed over the surface of the sample. During the drying stage, this substance decomposes, and a water-insoluble (hydrophobic) layer of elemental sulfur forms on the surface of the pores. The sizes of these particles, measured on a laser analyzer and an electron microscope, showed average values equal to 20 nm (Fig. 3). These particles have the structure of orthorhombic sulfur (Fig. 4). It is they who fill the porous structure of concrete and its voids fill the pores of concrete with a water-repellent material. During the drying stage, this substance decomposes, and a water-insoluble (hydrophobic) layer of elemental sulfur forms on the surface of the pores. The use of deep impregnation allows, along with an increase in strength and frost resistance, a decrease in water absorption, to significantly increase resistance to atmospheric factors, acids, salt solutions, and petroleum products. The mineral nature of the coating ensures its durability, and the water-repellent properties inherent in elemental sulfur block the access of water.
The data shown in Fig. 5 and 6 show that impregnation with a mortar leads to a significant decrease in water absorption by weight for both cement stone samples and cement-sand mortar samples. Moreover, the result is affected by both the duration of impregnation and the density of the solution. A successive increase in the duration of impregnation leads to a decrease in the value of the water absorption coefficient, since the impregnating solution penetrates into a greater number of pores over a longer time. A higher concentration solution contains less water and more polysulfide molecules, and when the solution dries, more sulfur remains. So, for the impregnation of a cement sample with a solution with a density of 1.33 g/cm3, after 4 hours of exposure to a solution with a density of 1.33 g/cm3, a value of 3.4% was achieved, and as a result of processing using a vacuum, a value of 1.9% was achieved. And for the impregnation of the solution sample with a solution with a density of 1.33 g/cm3, after 4 hours of exposure to a solution with the same density of 1.33 g/cm3, a value of 3.4% was achieved, and as a result of processing using a vacuum, a value of 1.3% was achieved g/cm3.
The results of potassium polysulfide cement-sand samples were compared with the results for calcium polysulfide [4]. When impregnated with calcium polysulfide for 1 hour, a water absorption coefficient of 6.2% is achieved, and for potassium polysulfide at ρ = 1.18 g/cm3 – 6.2% and at ρ = 1.33 g/cm3 the water absorption coefficient is 4.4%. When impregnated for 4 hours, calcium polysulfide shows a water absorption coefficient of 4.5%, and potassium polysulfide at ρ = 1.18 g/cm3 achieves a water absorption coefficient of 4.8%, and at ρ = 1.33 g/cm3 – water absorption coefficient 3.4%. As a result, for a cement sample, when impregnated with a solution of potassium polysulfide ρ = 1.33 g/cm3, we obtain values very close to values of the order of 3–4%, and under vacuum – a value equal to 1.3 g/cm3.
The data shown in Fig. 7 show that even a concentrated solution of potassium polysulfide with a density of 1.33 g/ cm3 has a good penetrating ability, and the penetration depth depends on the method of impregnation with the solution. Four hours of impregnation is enough for the solution to penetrate to a depth of 2 cm, and using the prevacuum method, it penetrates to the full depth (see Fig. 7c).
Thus, the use of a solution of potassium polysulfide to protect concrete, at least in terms of water absorption, is not inferior to a solution of calcium polysulfide and can be recommended as a means of protecting concrete. It can replenish the class of polysulfide water repellents [25–28], successfully serve in cases of penetrating hydrophobiza-tion as a means of long-term protection of building materials, treatment of porous surfaces of building materials, with a new sulfur-containing composition. The developed impregnating composition based on sulfur provides protection of building materials from atmospheric influences and aggressive environments for a long time.
CONCLUSIONS
Based on the work performed, we can draw the following conclusions:
-
1. Nanoparticles with an average size of 20 nm are deposited from a solution based on potassium polysulfide, as indicated by the results of measurements by a laser analyzer and probe microscopy. Sulfur nanoparticles are evenly distributed over the surface of the material and penetrate deep into the capillary tracts, resulting in the formation of a water-insoluble (hydrophobic) layer of elemental sulfur.
-
2. The results obtained in the work showed the high efficiency of the proposed hydrophobization method using a solution based on potassium polysulfide. It was found
-
3. Comparison of the proposed method showed that the preparation of a solution of potassium polysulfide is technologically more convenient compared to the method of preparation of calcium polysulfide. The proposed method makes it possible to apply mortars at room temperature on construction sites using dipping, pouring, brushing, spraying methods.
-
4. It has been established that impregnation with sulfurcontaining compositions can significantly reduce the water absorption of cement-sand and cement samples (2–3 times), makes it possible to vary the level of protection of materials by changing the concentration of the solution and the duration of treatment. Potential areas of application are
-
5. Impregnation with potassium polysulfide and subsequent removal of water as a result of drying leads to the formation of sulfur-based nanoscale coatings, which makes it possible to protect not only concrete from the effects of aggressive environments: acids, sewage and groundwater, sea water, but also other important building materials in the future, such as brick (ceramic and silicate), gypsum, asbestos, expanded clay, limestone and any other inorganic building materials. Processed materials acquire resistance to carbonates, chlorides, sulfates, nitrates, etc., increase water resistance, strength, and frost resistance of concrete.
АPPLICATION OF NANOTECHNOLOGIES AND NANOMATERIALS IN CONSTRUCTION that the efficiency of its use is ensured by the transformation of polysulfide molecules in the pores of materials into nanoparticles during the drying of the impregnating solution.
objects of industrial and civil construction, the proposed method of protection is effective for processing elements of road construction: sidewalk and road slabs, elements of underground communications for energy and water supply, sewerage, curbstones, well rings, trays, etc.
Список литературы New Protective Coatings Based on Sulfur Nanoparticles Produced from Potassium Polysulfide
- Mitkin B.A., Titov A.I. Reference manual for finishing materials. Minsk: Higher School: 1977.
- Massalimov I.A., Yanakhmetov M.R., Chuikin A.E., Massalimov B.I., Urakaev F.Kh., Uralbekov B.M., Burkitbaev M.M. Hydrophobization of dense and fine-grained concrete with polysulfide solutions. Nanotechnologies in construction. 2016; 8(5):85–99. https://doi.org/10.15828/2075-8545-2016-8-5-85-99
- Massalimov I.A., Yanakhmetov M.R., Chuikin A.E. Strength and durability of concrete modified with impregnating compositions based on sulfur. Nanotechnologies in construction. 2015; 7(3):61–75. https://doi.org/10.15828/2075-8545-2015-7-3-61-77
- Massalimov I.A., Babkov V.V., Mustafin A.G. Composition for the processing of building materials and a method for their processing. RF Patent 2416589. Appl. 09.23.2009. Published 04.20.2011. Bull. N11.
- Massalimov I.A., Chuikin A.E., Yanakhmetov M.R. Method for processing building materials with polysulfide solutions. Eurasian patent No. 024383 dated 03.26.2014.
- F.-L Tamas, I. Tuns, T.F. Galatanu: State of the art waterproofing technology. Bulletin of the Transilvania University of Brasov. Special Issue N1 Series I: Engineering Sciences. 2018; 11(60): 175-180.
- Tuns I., F-L.Tamas, M.Mantulescu:Waterproofing solution of an existing basement against water under hydrostatic pressure. Case study. Bulletin of the Transilvania University of Braşov, v.10 (59) No.1, 2017 Series I: Engineering Sciences, pp. 211–218.
- Loganina V.I., Kislitsyna S.N., Mazhitov E.B. Long-term strength of coatings based on sol-silicate paint. Vestnik MGSU. 2018;13-7 (118): 877–884. https://doi.org/10.22227/1997-0935.2018.7.877-884
- Osswald, J., Fehr, K.T. FTIR spectroscopic study on liquid silica solutions and nanoscale particle size determination. J Mater Sci. 2006; 41:1335–1339. https://doi.org/10.1007/s10853-006-7327-8
- Maohong Li, Yuanxiao Hong, HongYu, ShuxinQu, PingWang A novel high solar reflective coating based on potassium silicate for track slab in high-speed railway. Construction and Building Materials. 2019; 225:900-908. https://doi.org/10.1016/j.conbuildmat.2019.07.223
- Xu R., He T., Yang R., Da Y., Chen C. Application zinc silicate-potassium silicate coating for anticorrosion of steel bar in autoclaved aerated concrete. Construction and Building Materials. 2020; 237(2):117521. https://doi.org/10.1016/j.conbuildmat.2019.117521
- Antošová B., Kalendová A., Antoš P. Protective coatings based on alkali silicate Sci. Pap. Univ. Pardubice. Ser. A. 2013; 19 (2013):99–115.
- Cappellesso V.G., Petry N dos SantosDal Molin, D. C. C., Masuero A. B. Use of crystalline waterproofing to reduce capillary porosity in concrete, Journal of Building Rehabil. 2016; 1:9. https://doi.org/10.1007/s41024-016-0012-7
- Zhang Y.T., Zuo L., Yang J.C., Zhao W.X., Zeng X.X. Influence of Cementitious Capillary Crystalline Waterproofing Material on the Water Impermeability and Microstructure of Concrete. MSF. 2019; 953:209–14. https://doi.org/10.4028/www.scientific.net/msf.953.209
- Jie Sheng Liu, Jie Sheng Liu Application of Interpenetrating Silicone Waterproofing Material in the Protection of the Concrete. Advanced Materials Research. 2011; 701-704. https://doi.org/10.4028/www.scientific.net/AMR.306-307.701
- Nair, P.S. Gettu R. Commercially available waterproofing agents in India: A review – Indian Concr. J. 2016; 90(5): 36-53.
- Kapustin F.L. The use of penetrating waterproofing to improve the corrosion resistance of cement stone. In: Kapustin F.L., Spiridonova A.M., Pomazkin E.P. (ed.) Technology of concrete. M.: Collection of the XXI century: 2015.
- Valtsifer I.V. Astafiev S.A., Sizneva I.P. The effectiveness of the use of penetrating waterproofing compounds for concrete structures. Proceedings of the I International Scientific and Practical Conference “Problems of construction production and real estate management”. Kuzbass State Technical University, Kemerovo 2010; 209–212.
- Massalimov I.A., Shainurova A.R., Khusainov A.N., Mustafin A.G. Obtaining sulfur nanoparticles from an aqueous solution of potassium polysulfide. Zhurnal prikl. chemistry. 2012; 851(2): 1944–1949.
- Massalimov I.A., Khusainov A.N., Abdrakipova L.F., Mustafin A.G. Determination of the size of sulfur nanoparticles obtained from solutions of polysulfides of alkali and alkaline earth metals. Nanotechnics. 2009; 82(12):1946-1951.
- Bazhenov Yu. M. Concrete polymers. Moscow: Stroyizdat; 1983.
- Ramachandran V., Feldman R., Baudouin J. The Science of Concrete. Physical and chemical concrete science. Ed. Ratinova V.B. Moscow: Stroyizdat; 1986.
- Pokrovsky N.S. Impregnation waterproofing of concrete. Moscow: Energiya; 1964.
- Korolev E.V., Bazhenov Yu.M. Albbakasov A.I. Radiation-protective and chemically resistant sulfur building materials. Orenburg: Publishing House of the Orenburg State University; 2010.
- Massalimov I.A., Yanakhmetov M.R., Chuykin A.E., Mustafin A.G. Protection of Building Constructions with Sulfur Impregnating Solution. Study of Civil Engineering and Architecture (SCEA). 2013; 2(2):19-24.
- Massalimov I.A., Mustafin A.G., Chuikin A.E., Volgushev A.N., Khusainov A.N. Strengthening and increasing the water resistance of concrete with coatings based on nanosized sulphur. Nanotechnologies in construction. 2010; 2: 54–61.
- Agzamov F.A., Tokunova E.F., Sabirzyanov R.R. Application of calcium polysulfide to improve the corrosion resistance of well lining. Nanotechnologies in construction. 2019; 11(3): 308-324. https://doi.org/10.15828/2075-8545-2019-11-3-308-324
- Sabirzyanov R.R. Agzamov F.A. Tokunova T.F. Increasing the durability and corrosion protection of cement stone in aggressive environments. Materials of youth technical sessions. World Petroleum Council. London, UK. 2019; 352-358.