Обоснование режимов электронно-лучевой сварки изделий оболочкового типа из нагартованных сплавов АМГ6Н и АМГ6НПП
Автор: Ерофеев Валерий Владимирович, Игнатьев Андрей Геннадьевич
Рубрика: Технология
Статья в выпуске: 4 т.15, 2015 года.
Бесплатный доступ
Рассмотрены вопросы выбора оптимальных режимов электронно-лучевой сварки нагартованных алюминиевых сплавов типа АМг6Н и АМг6НПП с различной степенью упрочнения (15, 30 %). Цель оптимизации режимов - обеспечить наименьшую степень разупрочнения и размеры разупрочненных зон в диапазоне значений, гарантирующих равнопрочность сварных соединений основному металлу оболочковых конструкций. Приведены особенности изготовления цилиндрических изделий из алюминиевых нагартованных сплавов с применением электронно-лучевой сварки. Для уменьшения размеров разупрочненных участков использована новая охлаждающая оснастка c экранирующим устройством и жидкий азот в качестве хладагента. Представлены принцип работы и схема экранирующего устройства. Доказано, что при совместном применении теплоотводящей оснастки и экранирующего устройства достигается минимальная ширина зоны разупрочнения. Приведены результаты испытаний цилиндрических образцов в условиях двухосного нагружения при различных значениях параметра двухосности. По данным испытаний определены допустимые размеры зон разупрочнения, при которых несущая способность сварных соединений, ослабленных разупрочненными прослойками, находится на уровне прочности основного упрочненного металла. Доказана эффективность применения предложенной теплоотводяшей оснастки и экранирующей насадки для обеспечения равнопрочности сварных соединений основному металлу изделия. Полученные результаты могут быть использованы на стадии конструктивно-технологического проектирования и изготовления оболочковых изделий из нагартованных алюминиевых сплавов.
Оболочковые конструкции, алюминиевые сплавы, электронно-лучевая сварка, сварные соединения, разупрочненная зона, равнопрочность, режимы сварки, сварочная оснастка
Короткий адрес: https://sciup.org/147151706
IDR: 147151706 | DOI: 10.14529/engin150406
Текст научной статьи Обоснование режимов электронно-лучевой сварки изделий оболочкового типа из нагартованных сплавов АМГ6Н и АМГ6НПП
Широкое применение в аэрокосмической и авиационной технике для изготовления цилиндрических изделий ответственного назначения (сосудов, баллонов, трубопроводных систем и т. п.) находят нагартованные алюминиевые сплавы типа АМг6Н и АМг6НПП с различной степенью упрочнения – 15, 30 % [1–4]. Изделия, как правило, изготавливаются с применением электроннолучевой сварки, в процессе которой в результате термического цикла в околошовной зоне наблюдается разупрочнение металла – появляются мягкие прослойки [5–9]. Размер этих участков и степень разупрочнения металла зависит от длительности и степени нагрева металла в процессе сварки [10–15]. В связи с этим актуальной является проблема обеспечения равнопрочности сварных соединений с разупрочненными участками основному металлу изделий из сплавов типа АМг6Н и АМг6НПП на стадии конструктивно-технологического проектирования или их изготовления [16, 17].
Для уменьшения размеров разупрочненных участков в настоящее время применяются различные способы, основанные на активном теплоотводе из зоны шва, в частности, рассмотренные в работах [18, 19]. Теплоотвод осуществляется, как правило, с помощью теплоотводящей оснастки или теплопоглощающих паст, которые наносятся на свариваемый стык.
Сварку продольных швов цилиндрических заготовок размерами 165 х 20 мм (рис. 1) проводили на установке ЭЛУ-4 с использованием лучевой пушки УЛ-119, укомплектованной источни-
Рис. 1. Вид сварного соединения из сплавов типа АМг6Н и АМг6НПП, выполненного электронно-лучевой сваркой
ком питания У250А, обеспечивающим работу электронно-лучевой пушки в диапазоне ускоряющих напряжений U уск до 30 кВ. Величина рабочего давления в камере (вакуума) при сварке составляла порядка 10–4 атм. Сварка выполнялась на следующих режимах: ускоряющее напряжение U уск = 27 кВ, сварочный ток I св = 210 мА, ток фокусировки I фок = 72 мА, скорость сварки V св = 30 м/ч, ток расфокусировки I рф = 1,5 мА. Форма сканирования луча – круг диаметром d = 1,5 мм, частота сканирования f ск = 920 Гц.
Использовалась охлаждающая оснастка, представляющая собой плотно прилегающие к поверхности изделия элементы, в которых циркулирует хладагент – жидкий азот. Для повышения эффективности теплоотвода из зоны сварки и уменьшения зоны разупрочнения использовали также вариант совместного применения теплоотводяшей оснастки и экранирующей насадки на электронно-лучевую пушку. Послед няя позволяет путем отражения периферийной части пучка электронов, которые не участвуют в процессе расплавления металла и формирования шва и лишь перегревают околошовную зону, исключить их из процесса перегрева. Схема экранирующего устройства и принцип его работы показаны на рис. 2.
Насадка была изготовлена из немагнитного материала для исключения отклонения луча в магнитном поле (сталь Х18Н10Т). Пропускное отверстие диффузора подбиралось с размерами, обеспечивающими минимум температуры нагрева в околошовных зонах сварного соединения. Оптимальные результаты были получены при диаметре отверстия диффузора 4 мм при расположении экрана в 10–15 мм от поверхности изделия, что обеспечивало снижение температуры нагрева на расстоянии 10 мм от границы шва на 130-150 ° С по сравнению со сваркой без экрана.
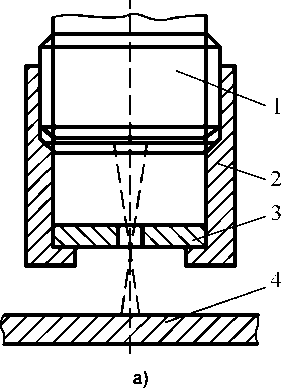
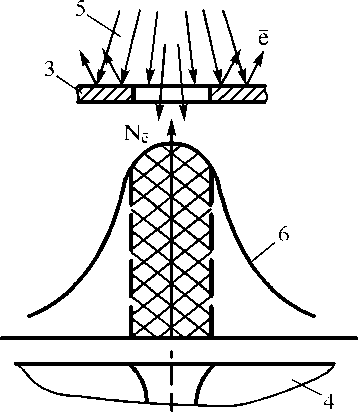
б)
Рис. 2. Схема экранизирующего устройства (а) и принцип действия экранизирующей насадки (б): 1 – лучевая пушка, 2 – корпус насадки, 3 – диффузор (отражатель), 4 – изделие, 5 – поток электронов, 6 – распределение мощности теплового потока (по Гауссу)
Использовали три варианта технологии изготовления сварных оболочковых изделий из на-гартованных сплавов АМг6Н и АМг6НПП: 1 – без теплоотвода; 2 – с применением теплоотводящей оснастки; 3 – комбинированный, сочетающий совместное использование оснастки и экранирующего устройства. В процессе электронно-лучевой сварки были получены сварные соединения со следующими размерами зоны разупрочнения: 1 – h = 8,5…9,0 мм; 2 – h = 4,1…4,3 мм; 3 – h = 2,0…2,1 мм, что соответствовало значениям относительных толщин мягких прослоек ж = h / 1 при использовании рассмотренных схем теплоотвода: 1 -ж = 0,425...0,45; 2 -ж = = 0,205…0,215; 3 – æ = 0,1…0,105.
Для выявления геометрической формы и размеров мягких прослоек, а также степени механической неоднородности сварных соединений, была исследована микроструктура и распределение твердости поперек сварного стыка. Степень механической неоднородности сварного соединения определяли на основании данных по твердости K в = НВт/ НВм, где НВт, НВм – твердость по Бринеллю соответственно основного металла и металла зоны разупрочнения. Кроме того, использовали данные о пределах прочности σвт и σвм , полученные в результате испытаний на разрыв образцов, вырезанных из разупрочненных и неразупрочненных участков сварного соединения: K в= σтв / σвм . Основные результаты измерений и механические характеристики различных зон сварных соединений приведены в табл. 1, 2.
Таблица 1
Средние значения твердости НВ (по Бринеллю) различных участков сварных соединений из сплава АМг6, выполненных электронно-лучевой сваркой
Материал изделия |
НВ, МПа |
||
околошовная зона |
шов |
основной металл |
|
АМг6Н (упрочнение 15 %) |
810 |
920 |
940 |
АМг6НПП (упрочнение 30 %) |
820 |
1040 |
1070 |
Таблица 2
Механические характеристики металла различных зон сварных соединений из сплава АМг6, выполненных электронно-лучевой сваркой
Материал, место вырезки |
Предел прочности σ в , МПа |
Предел текучести σ т , МПа |
Относительное удлинение δ, % |
Относительное сужение ψ , % |
Разупрочненная околошовная зона (ОШЗ) |
296 … 312 304 |
180 … 193 186 |
16,5 |
25,0 |
АМг6Н (основной металл, 60 мм от шва) |
342 … 356 351 |
246 … 259 263 |
10,1 |
19,1 |
АМг6НПП (основной металл, 60 мм от шва) |
394 … 402 397 |
292 … 302 298 |
9,0 |
18,5 |
Для определения влияния конструктивно-технологических параметров разупрочненных участков (æ, K в ) на несущую способность цилиндрических оболочек из сплавов АМг6Н и АМг6НПП в условиях двухосного нагружения стенки n = σ2 / σ1 (σ 1 и σ 2 – главные кольцевые и продольные напряжения) были проведены испытания при совместном нагружении цилиндрических образцов внутренним давлением и растягивающим (сжимающим) усилием с применением разрывной машины ЦДМу-30. С целью обеспечения параллельности границ зон разупрочнения, исключения разнотолщинности стенок оболочек сварные заготовки обрабатывали с двух сторон до размеров t = 6 мм; R вн = 72 мм, обеспечивающих отношение параметра толстостенности ψ= t / R вн = 0,083 (рис. 3). После этого к трубным заготовкам приваривались днища, приспособленные под захваты испытательной разрывной машины.

а)
б)
Рис. 3. Сварное соединение с разупрочненным участком из сплавов типа АМг6Н и АМг6НПП, выполненное электронно-лучевой сваркой (а), и сварной цилиндрический образец для испытания на двухосное испытание (б)
Обеспечение различных значений параметра двухосности в стенке тонкостенных оболочек n =σ2/ σ1 достигалось сочетанием внутреннего давления р и осевой силы F. В процессе экспе- римента моделировали следующие значения параметра двухосности: n = 0,3 – осевая нагрузка F сжимающая; n = 0,5 – осевая нагрузка F отсутствует; n = 0,7 – осевая нагрузка F растягивающая. По мере нагружения сосудов значения параметра двухосности поддерживались на одном уровне в соответствии с соотношением n = 0,5 1 ±
F I
—-— I = const.
nRP 7 вн
Формоизменение цилиндрических сосудов на стадиях, предшествующих разрушению, происходило в виде выпучины вдоль образующей цилиндрических оболочек. Несущая способность сосудов оценивалась величиной максимального давления p max. Основные результаты экспериментальных исследований ( p max , F ) и конструктивно-геометрические параметры сварных соединений, ослабленных разупрочненными участка ( K в , æ), приведены в табл. 3.
Таблица 3
Результаты испытаний цилиндрических сосудов из нагартованного сплава АМГ6, ослабленных разупрочненными участками
№ п/п |
Относительная толщина зоны разупрочнения ж = h / 1 |
Параметр двухосности в стенке сосудов |
|||||
0,3 |
0,5 |
0,7 |
|||||
p max , МПа |
F , кН |
p max , МПа |
F , кН |
p max , МПа |
F , кН |
||
1 серия: ом – сплав АМг6НПП ( K в = 1,3) |
|||||||
1–3 |
0,35 |
29,5 |
–207,7 |
29,7 |
0 |
29,9 |
196,4 |
4–6 |
29,1 |
–192,4 |
30,5 |
0 |
30,0 |
207,6 |
|
7–8 |
29,6 |
–205,6 |
– |
– |
29,0 |
189,9 |
|
9–11 |
0,68 |
27,6 |
–196,2 |
28,4 |
0 |
27,2 |
194,7 |
12–14 |
27,9 |
–194,7 |
27,7 |
0 |
28,3 |
185,1 |
|
15–16 |
27,3 |
–176,7 |
– |
– |
28,2 |
198,9 |
|
17–19 |
1,5 |
27,3 |
–181,4 |
27,4 |
0 |
27,2 |
190,6 |
20–22 |
26,4 |
–172,6 |
28,1 |
0 |
27,4 |
177,3 |
|
23 |
– |
– |
27,1 |
0 |
– |
– |
|
2 серия: ом – сплав АМг6Н ( K в = 1,15) |
|||||||
1–3 |
0,33 |
28,2 |
–198,0 |
28,6 |
0 |
28,6 |
187,3 |
4–6 |
28,7 |
–190,2 |
28,9 |
0 |
29,1 |
206,2 |
|
7–9 |
29,2 |
–189,9 |
29,5 |
0 |
28,3 |
196,2 |
|
10–12 |
0,72 |
27,0 |
–178,6 |
27,9 |
0 |
27,3 |
194,7 |
13–15 |
27,2 |
–179,6 |
27,7 |
0 |
27,3 |
194,7 |
|
16–18 |
27,7 |
–194,5 |
28,0 |
0 |
27,8 |
195,1 |
|
19–21 |
1,40 |
26,6 |
–175,1 |
27,5 |
0 |
26,7 |
189,5 |
22–24 |
27,1 |
–190,5 |
27,9 |
0 |
27,4 |
178,2 |
|
25 |
— |
— |
27,6 |
196,3 |
На рис. 4 приведены экспериментальные значения средних кольцевых напряжений в стенке цилиндрических сосудов сЭ^с, отвечающие стадии потери пластической устойчивости цилинд- рических оболочек в условиях выпучивания вдоль их образующей, полученные путем пересчета из опытных данных по pmax на основании котельной формулы [20]
Rвн сэрс = pmax — .
Там же приведено сопоставление данных экспериментальных значений сЭкс с их расчетными значениями срр сч, подсчитанными по соотношениям, полученным в работе [21]:
0 < ж < жр ссрасч =р „ св,жр < ж < ж сррсч = в n см|— + KnK^- I, (3)
\ K в K в )
Жк < ж ссасч = вn см .
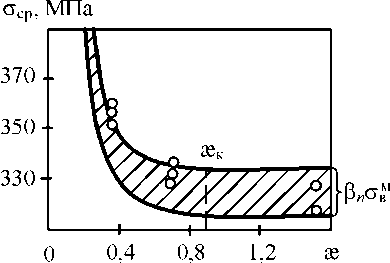
а)
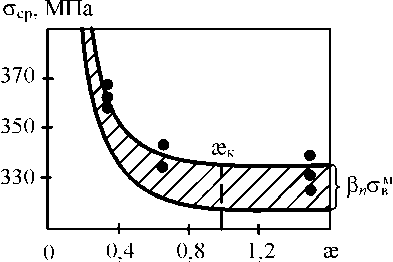
б)
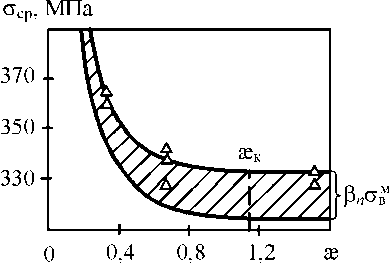
в)
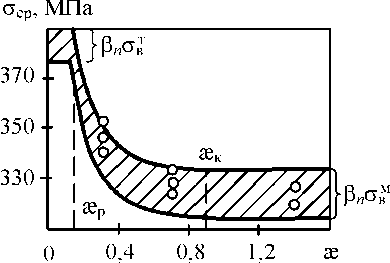
г)
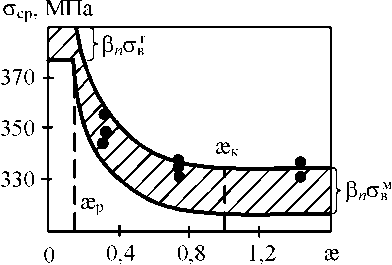
д)
Рис. 4. Сравнение расчетных и экспериментальных данных по несущей способности оболочковых сосудов σ ср , ослабленных разупрочненными прослойками (м) в околошовной зоне: а, б, в – сплав АМг6НПП ( K в = 1,3), г, д, е – сплав АМг6Н ( K в = 1,15); – n = 0,3; – n = 0,5;
– n = 0,7; по (3)
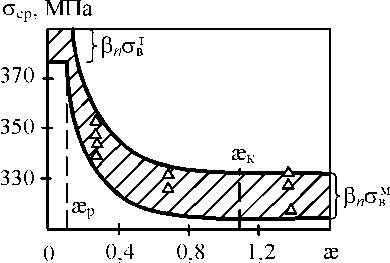
е)
В выражениях (3) коэффициент в n характеризует неустойчивость пластического формоизменения цилиндрической оболочки в условиях двухосного нагружения n :
В = ____^_____
n 1 + (р0,52 -1)(2n -1)2, где в0,5 — значение коэффициента вn для случая нагружения n = 0,5. Данная величина определяется механическими характеристиками металла оболочки (т) или разупрочненного участка (м) 5т,м,%, ^т,м,% и его склонностью к деформационному упрочнению ут = ст / ст или ум = см / см и может быть определена по методике, изложенной в работе [21].
Коэффициент контактного упрочнения мягкой (разупрочненной) прослойки KЖ в условиях двухосного нагружения рассчитывается по выражению
K Ж = a n + — + сп ж, (5)
ж где an, bn, сп - некоторые коэффициенты, зависящие от параметра двухосности нагружения n, n +1 к 1 ; 2 - n 2 - n
a n = ——, b n = ~ V( n + 1)(2 “ n ), C n =x Г"
3 6 n + + 16
Интервал значений мягких прослоек жк < ж (см. рис. 4) характеризует диапазон размеров зон разупрочнения, при которых несущая способность сварных соединений из нагартованных материалов АМг6Н и АМг6НПП находится на уровне прочности разупрочненного металла:
/ n +1 ж > жк = . -----.
V 2 - n
Интервал значений мягких прослоек 0 < ж < жр характеризует диапазон размеров зон разу- прочнения, при которых наблюдается равнопрочность сварных соединений, ослабленных разупроч- ненными прослойками, основному упрочненному металлу:
I 2 - n 3 Kв + 2 - n
V n + 1 ' 2
Как видно, имеет место вполне удовлетворительное соответствие расчетных и экспериментальных данных, полученных на базе испытания моделирующих образцов.
Для реальных размеров цилиндрических сосудов 165 х 20 мм, как указано выше, относи- тельные параметры зон разупрочнения, полученных в результате использования рассматриваемых трех вариантов технологий электронно-лучевой сварки, составляли: h = 8,5…9,0 мм (æ = 0,425…0,45) без теплоотвода; h = 4,1…4,3 мм (æ = 0,205…0,215) с применением теплоотводящей оснастки; h = 2,0…2,1 мм (æ = 0,1…0,105) с применением комбинированного метода, сочетающего совместное использование оснастки и экранирующего устройства. В соответствии с (7) использование третьего варианта изготовления цилиндрических изделий из нагартованных алюминиевых сплавов АМг6НПП (Kв = 1,3) и АМг6Н (Kв = 1,15), основанного на применении сочетания оснастки и экранирующего устройства, обеспечивает интервал относительных размеров разупрочненных участков в диапазоне равнопрочности ж < жр (жр = 0,13^0,14 при Kв = 1,3, n = 0,3…0,7 и æр = 0,14…0,16 при Kв = 1,15, n = 0,3…0,7).
Таким образом, способ электронно-лучевой сварки можно рекомендовать для изготовления цилиндрических изделий, выполненных из нагартованных алюминиевых сплавов, в условиях обеспечения активного теплоотвода на основе совместного применения теплоотводяшей оснастки и экранирующей насадки на электронно-лучевую пушку. Предложенная технология сварки нагартованных алюминиевых сплавов обеспечивает размеры зон разупрочнения в околошовных участках в диапазоне равнопрочности сварных соединений основному металлу изделий.
Список литературы Обоснование режимов электронно-лучевой сварки изделий оболочкового типа из нагартованных сплавов АМГ6Н и АМГ6НПП
- Ерыпалов, Л.А. Оптимизация технологии электронно-лучевой сварки изделий из алюминиевых сплавов/Л.А. Ерыпалов, Д.С. Ковалев, Н.В. Успенский//Актуал. проблемы авиации и космонавтики. -2012. -Т. 1, № 8. -С. 91-93.
- Бондарев, А.А. Электронно-лучевая сварка тонколистовых объемных конструкций из алюминиевых сплавов/А.А. Бондарев, В.М. Нестеренков//Автомат. сварка. -2011. -№ 6 (698). -С. 43-47.
- Трошин, А.А. Повышение качества сварных соединений из алюминиевых сплавов при электронно-лучевой сварке/А.А. Трошин, М.В. Шепелевич, В. Успенский//Актуал. проблемы авиации и космонавтики. -2013. -Т. 1, № 9. -С. 119-120.
- Терновой, Е.Г. Электронно-лучевая сварка толстостенных обечаек из алюминиевых сплавов АМг6 и М40/Е.Г. Терновой, А.А. Бондарев//Автомат. сварка. -2012. -№ 4 (708). -С. 8-14.
- Особенности структуры и свойств сварных соединений алюминиевого сплава В1469, выполненных электронно-лучевой сваркой/Р.В. Егоров, В.В. Овчинников, В.С. Магнитов, В.И. Лукин//Сварка и диагностика. -2011. -№ 3. -С. 18-22.
- Скальский, В.Р. Особенности структурной и механической неоднородности в сварных соединениях сплава 1201-Т, выполненных электронно-лучевой сваркой/В.Р. Скальский, Л.Р. Ботвина, И.Н. Лясота//Автомат. сварка. -2012. -№ 7 (711). -С. 19-23.
- Богомолов, Д.С. Электронно-лучевая сварка алюминия/Д.С. Богомолов//Науч. обозреватель. -2013. -№ 7. -С. 43-44.
- Особенности электронно-лучевой сварки деталей из перспективных алюминиевых сплавов, легированных литием и скандием/В.И. Кулик, Н.И. Созонович, А.В. Гудков, А.М. Ильинский//Сборка в машиностроении, приборостроении. -2009. -№ 11. -С. 31-34.
- Башенко, В.В. Особенности электронно-лучевой сварки прессованно-штампованных алюминиевых сплавов/В.В. Башенко, Н.И. Шаронов//Науч.-техн. ведомости СПбГПУ. -2010. -№ 106. -С. 139-143.
- Нестеренков, В.М. Механические свойства соединений жаропрочных сталей марок 10Х12М, 10Х9МФБА, выполненных электронно-лучевой сваркой/В.М. Нестеренков, Л.А. Кравчук, Ю.А. Архангельский//Автомат. сварка. -2013. -№ 9 (725). -С. 39-42.
- Свойства и структура кольцевых соединений труб, полученных орбитальной электронно-лучевой сваркой/Е.Г. Терновой, В.Ф. Шулым, А.Р. Булацев и др.//Автомат. сварка. -2011. -№ 1 (693). -С. 16-20.
- Технологические особенности электронно-лучевой сварки толстостенных заготовок/В.Н. Мартынов, А.С. Хохловский, М.С. Грибков, А.Г. Сысоев//Технология машиностроения. -2013. -№ 3. -С. 8-10.
- Овчинников, В.В. Электронно-лучевая сварка новых деформированных алюминиевых сплавов/В.В. Овчинников//Заготовит. пр-ва в машиностроении. -2013. -№ 1. -С. 11-16.
- Щербаков, А.В. Методы определения параметров технологических режимов при электронно-лучевой сварке тонкостенных изделий/А.В. Щербаков, А.Л. Гончаров, И.И. Чадова//Вестник МЭИ. -2012. -№ 2. -С. 85-90.
- Особенности электронно-лучевой сварки прессованных полос высокопрочного алюминиевого сплава системы Al-Zn-Mg-Cu/В.В. Овчинников, В.С. Магнитов, Е.Н. Иода и др.//Заготовит. пр-ва в машиностроении. -2009. -№ 11. -С. 9-13.
- Бакши, О.А. Влияние степени механической неоднородности на статическую прочность сварных соединений/О.А. Бакши, В.В. Ерофеев, М.В. Шахматов//Свароч. пр-во. -1983. -№ 4. -С. 1-3.
- Шахматов, М.В. Напряженное состояние и прочность сварных соединений с переменными механическими свойствами металла мягкого участка/М.В. Шахматов, В.В. Ерофеев//Свароч. пр-во. -1982. -№ 3. -С. 6-8.
- Лобанов, Л.М. Регулирование термодеформационных циклов при сварке листовых конструкций с применением теплопоглотителей/Л.М. Лобанов, П.П. Павловский, В.П. Логинов//Автомат. сварка. -1990. -№ 9. -С. 39-46.
- Макара, А.А. О разупрочнении стали при сварке/А.А. Макара, В.А. Саржевский, Н.Е. Протосей//Свароч. пр-во. -1968. -№ 8. -С. 1-6.
- Антикайн, П.А. Металлы и расчет на прочность котлов и трубопроводов/П.А. Антикайн. -М.: Энергоатомиздат, 1990. -368 с.
- Ерофеев, В.В. Несущая способность механически неоднородных сварных стыковых соединений в условиях двухосного нагружения/В.В. Ерофеев, А.А. Распопов//Вопр. свароч. пр-ва: сб. науч. тр. -Челябинск: ЧПИ, 1987. -С. 28-35.