Оценка точности измерений с использованием видеосистемы анализа полей перемещений и деформаций
Автор: Третьякова Татьяна Викторовна, Третьяков Михаил Павлович, Вильдеман Валерий Эрвинович
Статья в выпуске: 2, 2011 года.
Бесплатный доступ
В работе представлены результаты испытаний по оценке точности измерений, проводимых оптической системой анализа полей перемещений и деформаций при одновременном использовании навесного осевого датчика деформации. Показана высокая эффективность применения метода корреляции цифровых изображений для изучения поведения материалов на стадиях неупругого деформирования при возникновении неоднородных полей деформаций, а также волн локализованной пластической деформации.
Экспериментальная механика, оптические методы механики деформируемого твердого тела, метод корреляции цифровых изображений, поле перемещений и деформаций, оценка точности, "зуб" текучести, локализация пластической деформации
Короткий адрес: https://sciup.org/146211379
IDR: 146211379
Текст научной статьи Оценка точности измерений с использованием видеосистемы анализа полей перемещений и деформаций
Вопросы повышения прочности и обеспечения безопасности ответственных элементов конструкций, связанные с исследованиями неоднородности полей деформаций и анализом напряженно-деформированного состояния материалов, могут решаться с использованием оптических методов механики деформируемого твердого тела [1, 2]. Неоднородность поля может быть вызвана как наличием различных концентраторов, так и процессами возникновения и эволюции дефектов в материале, локализации пластической деформации. Авторами [3] с помощью оптико-телевизионного измерительного комплекса проведены исследования механического поведения материала на стадии накопления повреждений и разрушения, в [4] рассмотрены особенности макролокализации пластического течения на базе метода двухэкспозиционной спекл-фотографии. К оптическим методам также относится активно развивающийся метод корреляции цифровых изображений [5].
Корреляция цифровых изображений (digital image correlation) является эффективным бесконтактным методом измерения полей перемещений и деформаций на поверхности исследуемых объектов путем сравнения цифровых фотографий, снятых в процессе нагружения [5, 6]. Идея данного метода заключается в возможности определения поля смещений с высокой точностью путем отслеживания изменений на поверхности.
В настоящей работе рассмотрено применение трёхмерной цифровой оптической системы Vic-3D, математический аппарат которой основан на методе корреляции цифровых изображений. Видеосистема предназначена для анализа полей перемещений и деформаций на поверхности образцов различной геометрии, элементов конструкций. Имеется опыт использования оптической системы для экспериментального изучения полей деформаций в телах с концентраторами и анализ условий разрушения при упругопластическом и за-критическом деформировании, а также для исследования процессов неупругого деформирования и разрушения при плоском напряженном состоянии [7-11].
Точность оптической системы зависит от технических характеристик объективов и цифровых камер (разрешающая способность, чувствительность матрицы, максимальная частота съемки). На результат также может повлиять качество подготовки поверхности образца, корректная настройка резкости, точность калибровки, а так как система является трёхмерной, то на точности скажется и величина угла взаимного расположения двух камер.
Для оценки точности измерений трёхмерной цифровой оптической системы Vic-3D проведен ряд тестовых испытаний на универсальной сервогидравлической двухосевой испытательной машине In-stron 8850 с использованием навесного динамического датчика осевых деформаций Instron 2620-601 (рис. 1). Согласно сертификату заводских испытаний, максимальная погрешность измерений датчика не превышает (0,059±0,022)% от измеряемой величины.
Методика определения погрешности измерений видеосистемы заключалась в одновременной регистрации деформации на плоском образце с одной стороны с помощью системы Vic-3D, с обратной стороны - навесным экстензометром (рис. 2, а ). Следует учесть, что на показания навесного датчика может повлиять точность его позиционирования, несоосность, неполный контакт ножей экстензометра с поверхностью образца. Возможны также отличия в показаниях между видеосистемой и датчиком в связи с измерением деформаций на разных поверхностях одного образца.
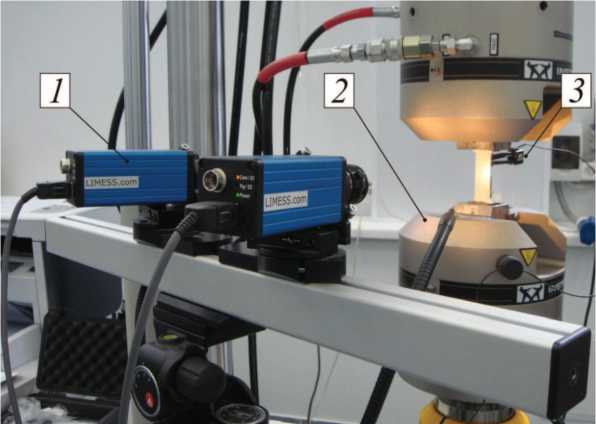
Рис. 1. Общий вид экспериментального оборудования: 1 - цифровая оптическая система Vic-3D; 2 - универсальная сервогидравлическая двухосевая испытательная машина Instron 8850; 3 - навесной динамический экстензометр Instron 2620-601
Регистрация продольной деформации оптической системой Vic-3D осуществлялась с использованием дополнительного модуля программного обеспечения системы «виртуальный экстензометр». Основным отличием от навесного датчика является то, что «виртуальный экстензометр» используется после проведения испытаний при обработке результатов, а не в режиме реального времени. С помощью данного модуля имитируется использование нескольких «экстензометров» на одном и том же образце. На поверхности образца между двумя точками, отмеченными на базе требуемой длины, отслеживается взаимное смещение в соответствии с прикладываемым усилием. На рис. 2, б представлен образец, на котором «установлено» пять «виртуальных экстензометров». При сопоставлении с результатами навесного осевого датчика вычислялось среднее значение продольной деформации.
Механические испытания образцов на одноосное растяжение проводились со скоростью удлинения 1,0 мм/мин. Плоские образцы изготовлены из алюминиевого сплава АМГ2М методом лазерной резки в форме лопаток толщиной 1,9 мм, шириной 20 мм. В испытаниях использован экстензометр с базой, равной 50 мм, диапазон измерений для данного датчика составляет ±5 мм. Экстензометр устанавливался таким образом, чтобы его элементы крепления не перекрывали по- верхность образца с другой стороны, что позволило получить значения продольной деформации с применением видеосистемы на базе одной длины и снизить погрешность измерения. При достижении максимально допустимой величины удлинения датчика нагружение было остановлено, образец разгружен.
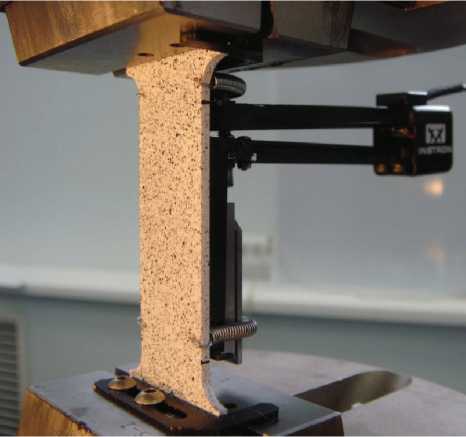
а
Рис. 2. Фотография образца с установленным навесным датчиком осевых деформаций ( а ), регистрация продольной деформации в процессе нагружения с использованием дополнительного модуля программного обеспечения оптической системы «виртуальный экстензометр» ( б )
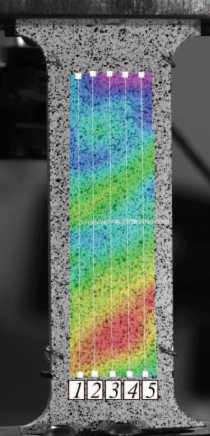
б
На начальной стадии деформирования кривые 2 и 3 , иллюстрирующие временные зависимости продольных деформаций, зафиксированные с использованием навесного экстензометра и цифровой оптической системы, практически совпадают (рис. 3). Многочисленные зубцы на диаграмме нагружения (кривая 1 , см. рис. 3) связаны с явлением прерывистого деформирования, что характерно для многих алюминиевых сплавов [12].
На рис. 4 приведены графики продольной деформации, полученные цифровой оптической системой с помощью пяти «виртуальных экстензометров». На упругой стадии деформирования зависимости продольных деформаций (кривые 1 -5, см. рис. 4) и их среднее значение - аср практически совпадают, однако следует отметить, что на не- которых участках показания «виртуальных экстензометров» отличались существенно. Так, на стадии формирования «зуба» текучести максимальное отличие между значениями продольной деформации составило 16,8 % от измеряемой величины. Данное отличие связано с неоднородностью полей деформаций, что будет проанализировано далее.
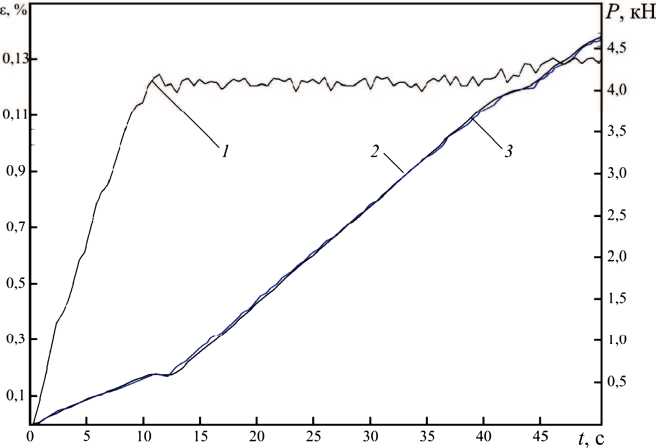
Рис. 3. Временные зависимости нагрузки ( 1 ), деформации по результатам измерений при помощи цифровой оптической системы ( 2 ) и экстензометра ( 3 ) на стадии упругого и упругопластического деформирования
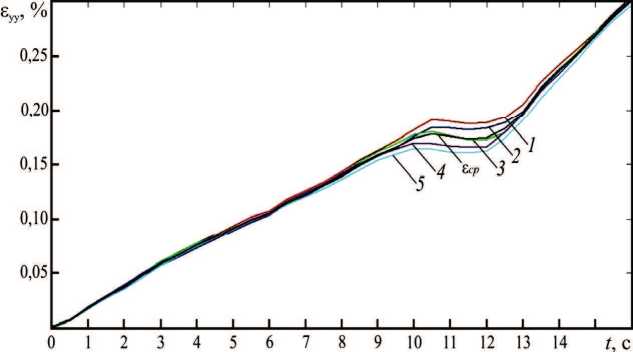
Рис. 4. Зависимости продольной деформации от времени пяти «виртуальных экстензометров» ( 1 - 5 ) и среднее значение еср продольной деформации на стадии формирования «зуба» текучести
При дальнейшем нагружении на стадии упрочнения материала расхождение между показаниями измерительных систем увеличивается (рис. 5).
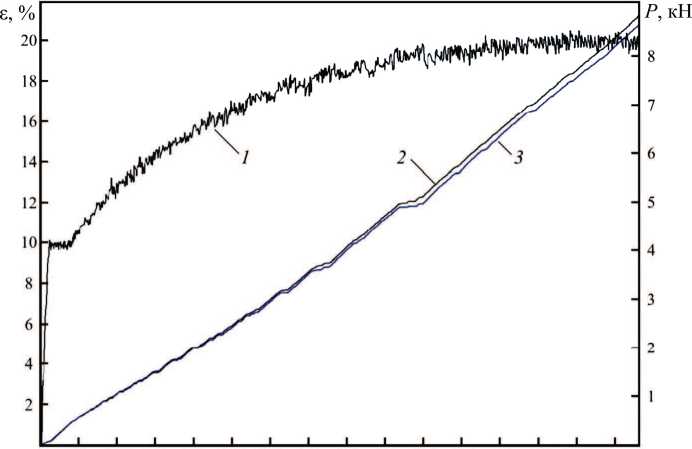
О 50 100 150 200 250 300 350 400 450 500 550 600 650 700 t, сек
Рис. 5. Зависимости нагрузки ( 1 ), деформации по результатам измерений при помощи цифровой оптической системы ( 2 ) и навесного экстензометра ( 3 ) от времени при одноосном растяжении алюминиевого сплава АМГ2М
Представляет интерес анализ эволюции полей перемещений и деформаций на поверхности образцов во время испытаний. С помощью видеосистемы Vic-3D определены поля продольных деформаций при различных уровнях прикладываемого усилия (рис. 6). Видно, что процесс деформирования материала являлся неоднородным, на поверхности образца зафиксированы зоны локализованной деформации, которые перемещаются по длине и имеют волновой характер [13]. Этим можно объяснить расхождение кривых на рис. 4 и 5. Следует отметить, что с увеличением неоднородности полей деформаций на поверхности образцов возрастает отклонение между показаниями двух средств измерения.
Наличие неоднородных полей деформации могло повлиять на регистрацию данных навесного экстензометра, так как прохождение полос локализованной деформации может отразиться на профиле поверхности образца. В качестве примера на рис. 6, в показано, как в области крепления ножа осевого датчика проходит полоса локализованной деформации.
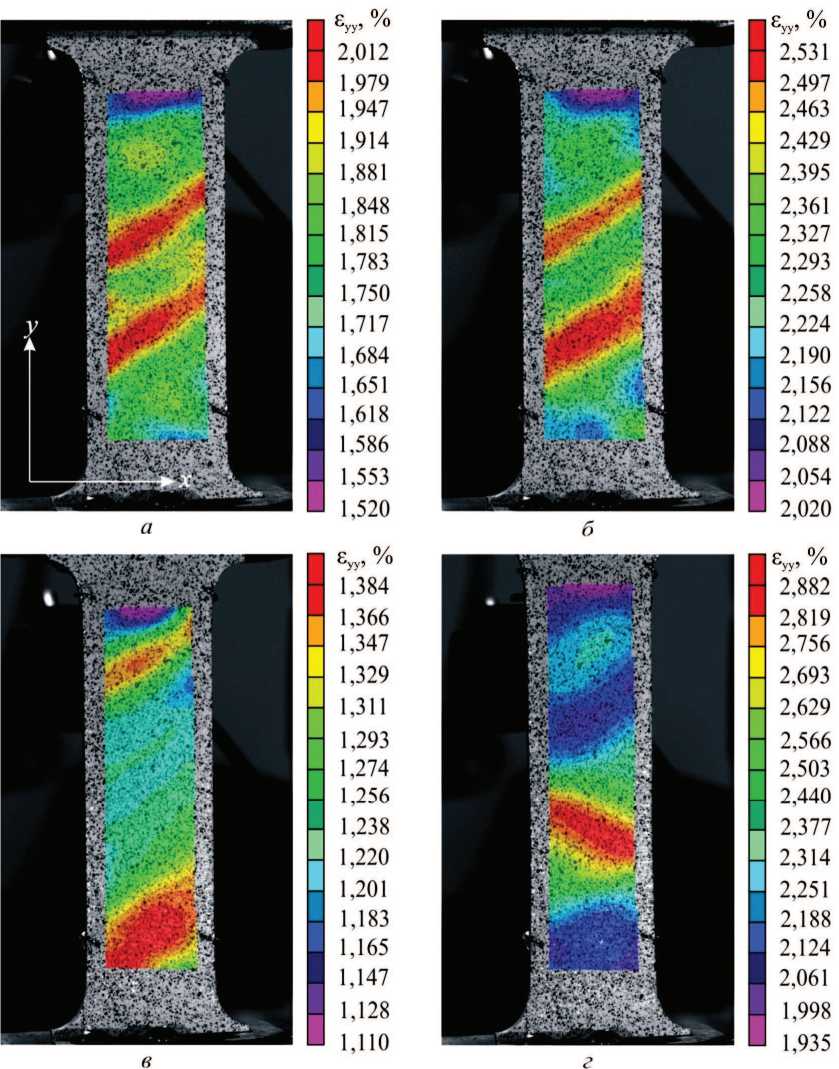
Рис. 6. Неоднородные поля продольных деформаций £ yy , полученные методом корреляции цифровых изображений, соответствующие нагрузке: 4,694 кН ( а ), 5,229 кН ( б ), 8,119 кН ( в ), 8,322 кН ( г )
По результатам проведения серии испытаний на одноосное растяжение плоских образцов из алюминиевого сплава АМГ2М сделан вывод, что применение цифровой оптической системы Vic-3D позволяет определять значения деформации на фиксированной базе, с точностью сопоставимые с данными навесного динамического датчика осевых деформаций. Кроме того, видеосистема обладает дополнительным преимуществом, так как позволяет зафиксировать эволюцию полей перемещений и деформаций, оценить характер неоднородности полей, отследить процессы деформирования материала, протекающие на поверхности образца.
Работа выполнена при финансовой поддержке по проекту (Гос. контракт № 13.G25.31.0093 от 25 октября 2010 г.) в рамках Постановления Правительства России от 9 апреля 2010 г. № 218 «О мерах государственной поддержки развития кооперации российских высших учебных заведений и организаций, реализующих комплексные проекты по созданию высокотехнологичного производства».