Определение точности обработки изделий на деревообрабатывающих станках в системе MathCAD
Бесплатный доступ
Статья посвящена расчету точности работы деревообрабатывающего оборудования в среде MathCAD. Приведен пример расчета точности работы шипорезного станка.
Точность работы станка, среда mathcad
Короткий адрес: https://sciup.org/147112196
IDR: 147112196
Текст краткого сообщения Определение точности обработки изделий на деревообрабатывающих станках в системе MathCAD
Определение точности работы станков, в том числе и деревообрабатывающего оборудования, является актуальной задачей.
В производстве изделий из древесины одним из основных производственных показателей качества является изготовление изделий с заданной точностью, так как именно точность изготовления позволяет осуществлять взаимозаменяемость деталей и сборочных единиц, что в значительной степени влияет на снижение себестоимости готовой продукции.
При изготовлении изделий из древесины детали и сборочные единицы обрабатывают на станках, как правило, партиями. Партия деталей – это детали, обработанные на одном станке при одной его настройке.
Для получения качественной механической обработки деталей очень важно знать:
-
1) какую точность обработки изделий позволяет получить данное оборудование (станок);
-
2) соответствие полученных размеров обработанных изделий заданной точности (допуску).
Эти факторы, как правило, определяются статистическими расчетами.
В настоящее время одним из наиболее прогрессивных способов статистической обработки в производст- венных условиях является использование системы MathCAD на персональном компьютере.
Данная система позволяет создавать алгоритм расчетов с последующим изменением входных параметров и получением новых расчетных значений точности работы оборудования, его настройки и определения процента годных и бракованных изделий при обработке их на любом оборудовании при условии, что вероятность распределения случайных величин подчинено закону нормального распределения.
Рассмотрим данный способ расчета на конкретном примере.
Пример . Выполнить расчет на персональном компьютере основных статистических характеристик партии деталей (50 замеров толщины шипа) при обработке их на шипорезном станке в соответствии с допуском 20у13 и определить:
-
• величину систематической погрешности;
-
• процент годных и бракованных деталей, соответ -ствующих заданному допуску, без учета систематической погрешности;
-
• процент годных и бракованных деталей, соответствующих заданному допуску, с учетом систематической погрешности;
-
• точность обработки деталей на станке - поле рассеивания размеров.
Замеры толщины шипа деталей после их обработки на шипорезном станке приведены в таблице 1.
Таблица 1
Значения замеров толщины шипа, мм
20,28 |
20,39 |
20,36 |
20,33 |
20,44 |
20,41 |
20,38 |
20,35 |
20,46 |
20,30 |
20,38 |
20,49 |
20,32 |
20,43 |
20,32 |
20,40 |
20,37 |
20,34 |
20,45 |
20,28 |
20,25 |
20,36 |
20,48 |
20,31 |
20,42 |
20,41 |
20,52 |
20,36 |
20,47 |
20,44 |
20,55 |
20,38 |
20,49 |
20,43 |
20,26 |
20,40 |
20,51 |
20,34 |
20,46 |
20,43 |
20,54 |
20,37 |
20,48 |
20,45 |
20,42 |
20,39 |
20,50 |
20,33 |
20,44 |
20,55 |
Для размера с допуском 20у13 по ГОСТ 6449.1 - 82 + 0,39
найдем предельные отклонения: 20( + о 06 ) , тогда в системе MathCAD запишем и рассчитаем: d:=20.00 – номинальный диаметр, мм;
es:=0.39 – верхнее предельное отклонение допуска, мм;
ei:=0.06 – нижнее предельное отклонение допуска, мм;
dmax:=d+es;
dmax=20.39 – максимальный предельный размер, мм;
dmin:=d+ei;
dmin=20.06 – минимальный предельный размер, мм;
IT:=dmax - dmin;
IT=0.33 – значение допуска, мм;
dsd:=dmin+ ;
dsd=20.225 – среднее значение размера, мм;
n:=50 – количество замеров;
i:=1..n – ранжированная переменная.
p1:=
z2p(x1)dx1
z1
p1=97.00 % – процент годных деталей;
p2:=
z1 p(x1)dx1
a
p2=1.50 % – процент бракованных деталей (размеры шипа меньше заданного допуска);
b p3:= p(x1)dx1 (7)
z2
Создадим входную таблицу, обозначим ее индексированной переменной хi и введем в нее 50 значений из таблицы 1.
p3=1.50 % – процент бракованных деталей (размеры шипа больше заданного допуска).
Выполним расчет среднего значения хср и среднеквадратического отклонения s по формулам [1] и [2]:
хi хср:= ∑ i n хср=20.404 мм;
s:=
n-1
⋅∑(xi -xcp)2
i
s=0.076 мм.
Для построения графика функции нормального распределения (рис. 1) запишем предельные значения а и b, зададим значения ранжированной переменной х1 и выполним расчет функции p(x1) по формуле [3].
x1:=a,a+0.01..b – ранжированная переменная;
a:=xcp - 3s;
a=20.176 мм;
b:=xcp+3s;
b=20.633 мм.
p(x1):= (
s
- (x1 - xcp) 2
1 )⋅e 2⋅s2⋅N2⋅3.14
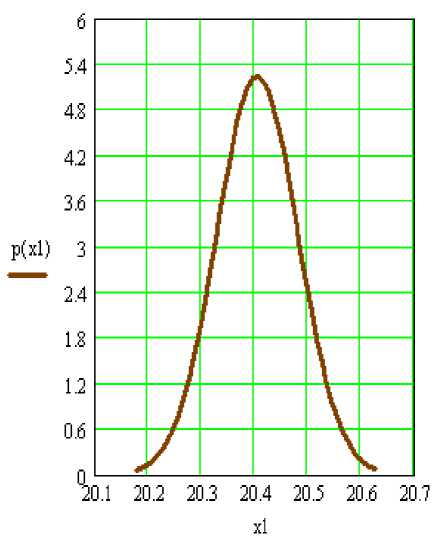
Рис. 1. График функции нормального распределения
Расчет систематической погрешности sp выполняем по формуле [4]:
sp:=xcp - dsd sp=0.179 мм.
Для расчета процента годных и бракованных деталей, с точностью в пределах шести среднеквадратических значений, без учета систематической погрешности (при правильной настройке станка) зададим граничные значения z1 и z2 и выполним расчет по формулам [5], [6] и [7]:
IT z1:=xcp- ;
z1=20.239 мм;
z2:=xcp+ ;
z2=20.569 мм;
Тогда общий процент брака составит:
brak:=p2+p3;
brak=3.00 %.
Для расчета процента годных и бракованных деталей с учетом систематической погрешности sp (при неправильной настройке станка) зададим граничные условия z3 и z4 и выполним расчет по формулам [8], [9] и [10]:
sp:=xcp - dsd;
sp=0.179 – систематическая погрешность, мм;
IT z3:=dsd- ;
z3=20.06 мм;
z4:=dsd+ ;
z4=20.39 мм;
∫ z4
p(x1)dx1 ; (8)
z3
p4=42.51 % – процент годных деталей;
∫ a
p(x1)dx1 ; (9)
z3
p5=0.135 % – процент бракованных деталей (размеры шипа меньше заданного допуска);
b p6:= p(x1)dx1; (10)
z4
p6=57.355 % – процент бракованных деталей (размеры шипа больше заданного допуска).
Тогда общий процент брака составит:
brak:=p5+p6;
brak=57.49 %.
Поле рассеивания размеров толщины шипа с вероятностью 99.72 %, а также точность работы станка определяем по формуле [11]:
pr:=6s (11)
pr=0.457 мм.
ВЫВОДЫ
В результате выполненной работы установлено:
-
1. Точность обработки деталей (поле рассеивания случайных погрешностей) на шипорезном станке соответствует 6s=0.457 мм.
-
2. Систематическая погрешность составила sp=0.179 мм.
-
3. Процент годных деталей, соответствующих допуску IT=0.33 мм без учета систематической погрешности (при правильной настройке станка), соответствует 97 %, брак – 3 %.
-
4. Процент годных деталей, соответствующих допуску IT=0.33 мм с учетом систематической погрешности sp=0.179 мм (при некачественной настройке станка) составил 42.51 %, брак – 57.49 %.
Таким образом, для получения 100 % годных деталей при правильной настройке данного шипорезного станка надо иметь допуск размера больше или равным 0,457 мм, а для получения 100 % годных деталей с допуском размера 20у13 (0,33 мм) станок следует подвергнуть среднему или капитальному ремонту или заменить его на новый.