Optimization of a sustainable composition of fine-grained concrete for 3D printing with partial substitution of sand with fly ash and slag waste
Автор: Rakhimov M.A., Aubakirova Z.A., Aldungarova A.K., Menéndez Pidal de Navascués I., Moldamuratov Zh.N.
Журнал: Nanotechnologies in Construction: A Scientific Internet-Journal @nanobuild-en
Рубрика: Manufacturing technology for building materials and products
Статья в выпуске: 3 Vol.17, 2025 года.
Бесплатный доступ
Introduction. In the context of sustainable construction, one of the key challenges is the development of effective strategies for the management and recycling of fly ash and slag waste produced by thermal power plants. Recent studies confirm the potential of such waste as a partial substitute for conventional sand in concrete mixtures. However, most research focuses on conventional concrete and does not consider the specific requirements for rheological properties and interlayer adhesion, which are critical for 3D printing technology. Methods and Materials. The study used Portland cement CEM I 42.5N, fly ash and slag waste from the Ust-Kamenogorsk TPP, crushed sand, and the MasterGlenium superplasticizer. The concrete mix design was developed in stages: a base mix, a control mix (with an increased water-to-cement ratio), and experimental mixes with 25% and 50% sand replacement by fly ash and slag waste. Samples were printed using a construction 3D printer (model S-6045) and tested for compressive strength, density, interlayer adhesion, and subjected to micro and nanostructural analysis. Results and Discussion. Experimental mixtures with 25% and 50% sand replacement showed reduced density and strength compared to the control mix. However, the 25% replacement mix maintained satisfactory strength, shape stability, and interlayer bonding. Micro and nanostructural analysis confirmed the relationship between structural compaction and physical-mechanical properties. Despite some limitations, the study demonstrated the potential of TPP-derived ash and slag waste as a viable component in 3D printing, provided the composition and extrusion parameters are optimized. Conclusion. The results indicate that replacing 25% of sand with fly ash and slag waste is optimal for fine-grained concrete mixtures intended for 3D printing. This approach improves resource efficiency and environmental sustainability without compromising the performance of the final products.
3D concrete printing, fly ash and slag waste, shape stability, interlayer bonding, sustainable construction, micro and nanostructure
Короткий адрес: https://sciup.org/142244833
IDR: 142244833 | DOI: 10.15828/2075-8545-2025-17-3-296-306
Текст научной статьи Optimization of a sustainable composition of fine-grained concrete for 3D printing with partial substitution of sand with fly ash and slag waste
Original article
Рахимов М.А., Аубакирова З.А., Алдунгарова А.К., Менендес Пидаль де Наваскуэс И., Молдамуратов Ж.Н. Оптимизация устойчивого состава мелкозернистого бетона для 3D-печати с частичной заменой песка золошлаковыми отходами. Нанотехнологии в строительстве. 2025;17(3):296–306. – EDN: BISWAS.
In today’s context of sustainable construction, it is a significant task to find efficient solutions for the recycling and treatment of ash and slag waste (ASW) generated by combined heat and power plants (CHPPs). Literature review demonstrates significant interest in this topic, but also reveals several unresolved issues related to the use of ASW in fine-grained concrete for 3D-printing.
Studies [1, 2] represented that the incorporation of ash and slag aggregates can preserve or even improve the strength of concrete. Nevertheless, both studies focus on traditional concrete and do not consider specific rheological properties which is critical for 3D-printing, as well as the impact of texture and porosity of slag components on the adhesion between layers.
The research work [3] considered the potential use of cement-ash compositions in 3D-printing. This work focuses on properties of mixtures in their fresh state without considering their long-term strength and micro- and nanostructural stability. In studies [4-6], authors analyzed the effect of 3D-printing parameters (thickness of lay-
MANUFACTURING TECHNOLOGY FOR BUILDING MATERIALS AND PRODUCTS ers, feed rate, time interval between layers) on strength characteristics. However, they do not address how the specific composition of fillers impacts on shape stability and adhesion.
A review of 3D-printing methods [7] indicates on the potential of mineral additives, including ash and slag, however, it does not evaluate their direct impact on micro- and nanostructures of printed products. Researchers in [8] underlined the essential need for individual approach to adjust the composition for each type of 3Dprinter, enhancing the importance of selecting active components based on ash and slag. Study [9] describes the pozzolanic activity of ash and its influence on micro- and nanostructure, and on strength of concrete at later stages of curing. Nevertheless, this work lacks the analysis of behaviour of ash in extrudable mixtures and under layered deposition conditions. The research study [10] demonstrates that fly ash, formed as by-product of the coal-fired power plants, is frequently being used as a component in the production of high – strength concrete. This underlines its potential for effective use as a filler and binder component in mixtures for 3D-printing.
Understanding of rheology has a critical importance for managing pumpability and shape stability, specifically in 3D-printing. As mentioned in [11], numerical models, considering the shape of the constructing element, characteristics of concrete mixture, and specifics of placement technology, are required for an effective use of self-compacting concrete – that are also relevant in 3D-printing. In 3D-printing, the concrete mixture is extruded under high pressure and at low rate. As noted in [12], it requires precise management for rheological properties. The need for thermal treatment to achieve an early strength in geopolymer concrete, based on [13], limits its application in monolithic structures. Simultaneously, studies [14, 18–20] suggested the use of ash in geopolymers as an alternative to cement. It is noted that ash can replace up to 20% of cement [15, 19, 21], however, they do not consider the specifics for the 3D-printing. Despite the active development of additive technologies in construction, as mentioned in [16, 22–24], there is a still lack of comprehensive studies embracing data about material properties, their applicability for printing, and durability of printed structures.
Thus, the analysis of relevant studies reveals the following unresolved issues:
– insufficient research on the influence of ash and slag particle size distribution on shape stability and adhesion between layers in 3D-printing conditions;
– the absence of an integrated approach, combining micro and nanostructural analysis, and assessment for strength and other rheological properties;
– limited data about interactions between ash and slag components with additives (plasticizers) in the context of geometric stability of extruded products.
These gaps justify the relevance of this study, based on developing and optimizing the composition of finegrained concrete for 3D-printing using ASW as an alternative to partial sand.
The aim of this research is to determine the influence of ASW used as partial sand alternative (at 25% and 50% in volume) on physical, mechanical, and technological properties of fine-grained concrete intended for 3D-priniting.
The study is focused on the establishment of the patterns of variations in strength, plasticity, shape stability, and interlayer adhesion of the concrete mixture depending on the quantity of ASW, as well as on the investigation of their influence on micro and nanostructures of material.
Obtained results will form a basis for the development of an efficient fine-grained concrete composition, ensuring the shape stability, reliable layered adhesion, and longevity of printed structures, that promotes the rational use of industrial waste and reduces the demand for natural resources in construction.
METHODS AND MATERIALS
The following materials were used for the experimental part of the study: Portland cement M450 (produced by Bukhtarma Cement Company LLP), crushed sand, ash and slag from ash dump No. 2 of the Ust-Kamenogorsk CHPP, and a polycarboxylate – based superplasticizer MasterGlenium.
Chemical compositions of the applied materials are shown in Tables 1 and 2. Crushed sand was characterized by a fineness modulus of 1.5, bulk density of 1.5 g/cm3, true density of 2.75 g/cm3, clay component in lumps of 0.9%, and specific surface area 280 m2/g. Ash and slag were characterized by a fineness modulus of 1.0, bulk density of 1080 g/cm3, true density of 2.4 g/cm3 and specific surface area 0.2 m2/g.
Based on the granulometric composition, ash and slag meet the requirements for fine aggregate: in accordance with GOST 25592-2019, the proportion of particles larger than 0.315 mm is at least 50%, confirming its suitability for use in concrete mixtures.
The composition of the mixture was selected based on the requirements for fine-grained concrete, with the aim of ensuring shape stability of the mixture. Shape stability was evaluated using the slump test (Fig. 1a). The resulting composition illustrated satisfactory performance and was used as the base mix.
Following that, the base composition was modified in two stages. At the first stage, a control mixture was developed by increasing the ratio of water to cement to improve extrudability, since the initial base composition has shown increased rigidity and did not provide a stable feed rate of material through the nozzle. While determining rheological properties of the mixture, increasing its
MANUFACTURING TECHNOLOGY FOR BUILDING MATERIALS AND PRODUCTS
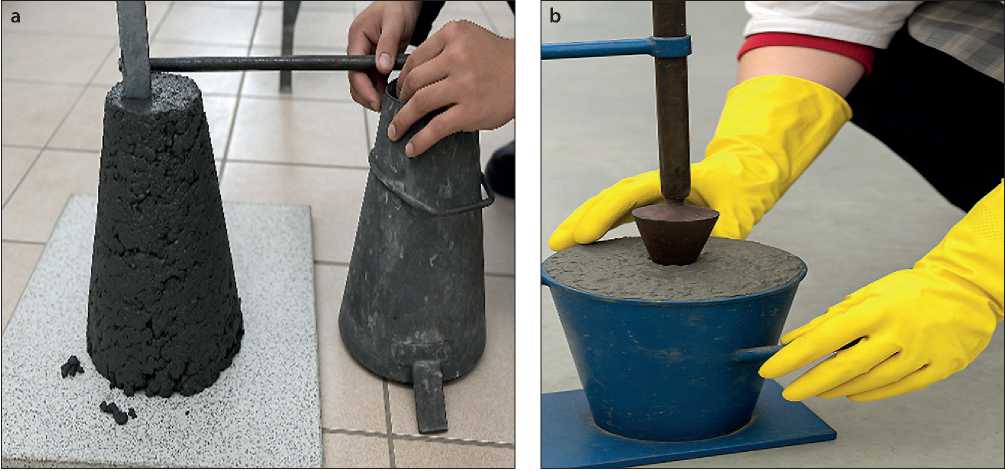
Table 1. Chemical composition of cement M450 (Bukhtarma Cement Company LLP, Kazakhstan)
№ |
Material |
Oxide content, % |
||||||||
Al2O3 |
FeO3 |
CaO |
MgO |
Na2O |
K2O |
TiO2 |
P2O5 |
SrO |
||
1 |
Cement BCC |
5.01 |
3.07 |
40.38 |
1.77 |
1.75 |
0.9 |
0.245 |
0.1119 |
0.0426 |
Table 2. Chemical composition of ASW (Ash Dump No. 2 of the Ust-Kamenogorsk CHP, Kazakhstan)
№ |
Material |
Oxide content, % |
||||||||
SiO2 |
Al2O3 |
Fe2O3 |
CaO |
MgO |
Na2O |
K2O |
TiO2 |
MnO |
||
1 |
CHP ash and slag |
2.139 |
1.889 |
1.429 |
1.400 |
1.658 |
1.348 |
1.204 |
1.668 |
1.291 |
Fig. 1 . Determination of rheological properties of concrete mixture: a - cone slump test for the base composition, b – determination of the mobility of the mixture for control and experimental mixtures.
mobility allowed to achieve the optimized balance between shape stability and manufacturability, essential in 3D-printing. (Fig. 1b). The need for careful regulation of the water-to-cement ratio and the dosage of admixtures is supported by other studies involving complex additives for improving mix properties [25].
At the second stage, experimental composition was developed. In concrete mixtures, sand was partially replaced with ash and slag of 0.315–0.14 mm fractions in volumes of 25% and 50%. The ash – slag material was pre – sieved using sieve No. 2.5–0.16 mm. Angular shape of crushed sand was used as the base aggregate to enhance bonding within the mixture.
The material quantities were recalculated for a batch size 25 kg, as practical experience showed that increasing the mix volume caused difficulties during mixing in the hopper and reduced stability of extrusion through the nozzle due to the design specifics of equipment.
Fabrication of samples was carried out using an S-6045 construction 3D-printer (Fig. 2) installed at D. Serikbayev East Kazakhstan Technical University, designed for printing architectural and landscape elements.
The S-6045 is an improved version of S-series, developed based on the S-6043 platform. Experimental and control samples were produced by layer-by-layer printing, maintained under normal conditions, and tested for strength characteristics. After days of printing, the samples were sawed out and placed in a hardening chamber, where they kept for 7, 14, and 28 days.
To identify the strength of interlayer bond, tests for splitting of cylindrical samples using PGM-1000MG4 press were applied. Methodology was adapted to evaluate
MANUFACTURING TECHNOLOGY FOR BUILDING MATERIALS AND PRODUCTS
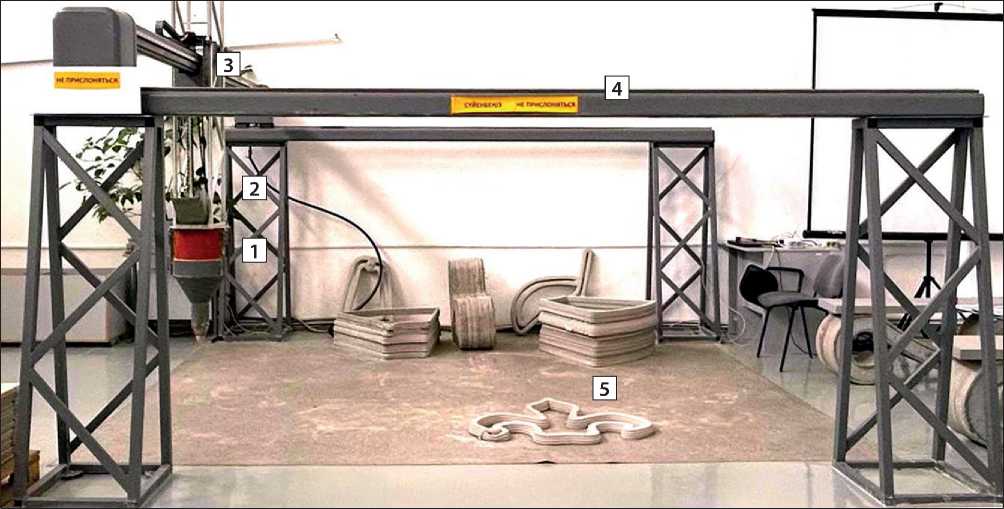
Fig. 2. S-6045 construction 3D-printer: 1 – printing head, 2 – loading hopper, 3 – transverse movement mechanism, 4 – 3D-printer frame, 5 – finished product.
the strength on the contact layers formed during 3Dprinting, like proposed method in [18]. The general view of the equipment is shown in Figure 3.
Compressive strength was evaluated on PGM-1000MG4 hydraulic press in accordance with GOST 10180–2012. The general view of the test is shown in Fig. 4.
The average density of the samples was determined in accordance with EN 1015–11. A scanning electron microscope (SEM) was used to evaluate the micro and nanostructure.
RESULTS AND DISCUSSION
As a result of experimental formulation of the composition, including the regulation of water-cement ration and the introduction of a plasticizer to ensure the required rheological properties of the mixture. The change in dosages of the components led to a change in the watercement ratio, contents of water and aggregates, which is shown in Table 3.
As shown in Table 4, experimental data on density, strength during cracking, and compressive strength of
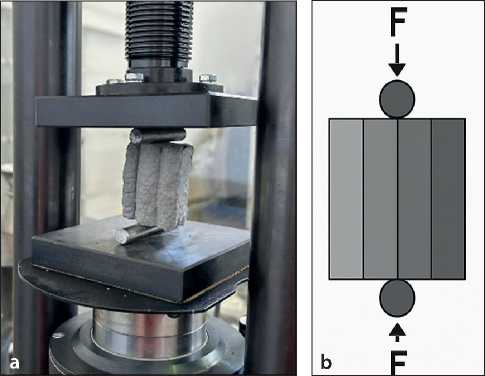
Fig. 3. Splitting test for the strength of the interlayer joint: a – hydraulic press PGM-1000MG4, b – test scheme.
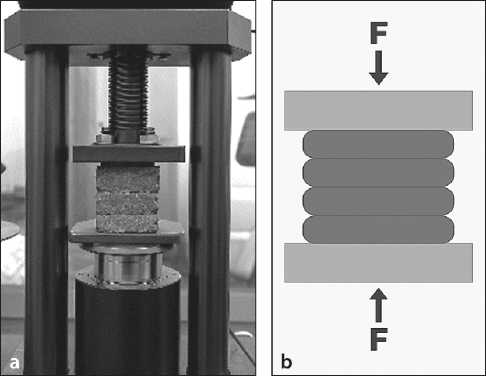
Fig. 4. Compression testing of printed materials on a 3D-printer: a – test press for determining compressive strength, b – test scheme.
MANUFACTURING TECHNOLOGY FOR BUILDING MATERIALS AND PRODUCTS
Table 3. Experimental composition fine-grained concrete with a different content of ASW
Mixture |
Cement (kg) |
Crushed sand (kg) |
Ash and slag (kg) |
Water (mL) |
Plasticizer (mL) |
W/C |
К |
594 |
1367 |
0 |
220 |
5.94 |
0.37 |
(25% ash and slag) |
594 |
1025 |
342 |
255 |
5.94 |
0.42 |
(50% ash and slag) |
594 |
684 |
683 |
298 |
5.94 |
0.50 |
Table 4. Physical and mechanical characteristics of concrete mixtures with ash and slag
Analysis of Table 4 shows that increasing the dosage of ash and slag leads to reducing the density and strength of the concrete, especially at early stages of hardening.
Figure 5 demonstrates the average density of concrete mixtures depending on proportion of sand replacement with ASW. There is a pattern of decreasing density with an increasing ash and slag content, that is explained by a lower bulk density and high porosity of ash and slag particles.
Figure 6 demonstrates the dynamics of changes in axial compressive strength depending on the age of hardening. The strength of the control mixture consistently exceeds the values of samples with the addition of ash and slag, especially at early stages. However, the differ-
Density of Concrete Mixtures at Different Ages
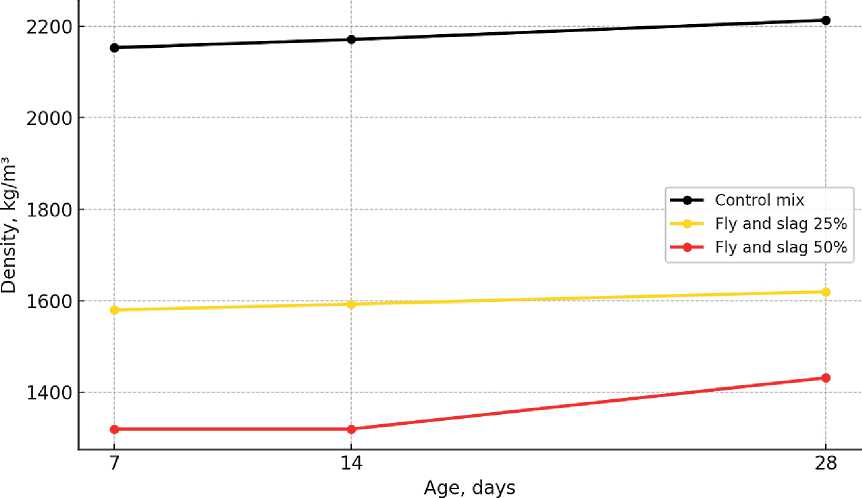
Fig. 5. Average density of concrete mixtures with varying proportions of sand replacement by ash and slag (X-axis – composition of the mixture: control, 25%, 50%; Y-axis – density, kg/m³)
MANUFACTURING TECHNOLOGY FOR BUILDING MATERIALS AND PRODUCTS ence decreases by day 28, indication the development of pozzolan activity of the ash and slag components.
Figure 7 illustrates similar tendency in terms of strength during cracking. Mixtures with 25% of ash and slag content demonstrated acceptable strength characteristics. Meanwhile, mixtures with 50% of ash and slag content have shown a decrease in strength in the early stages of material structure.
SEM images of micro and nanostructures of concrete samples are shown in Figure 8.
Analysis of micro and nanostructures showed that the structure in (c, d) with 50% of ash and slag is less
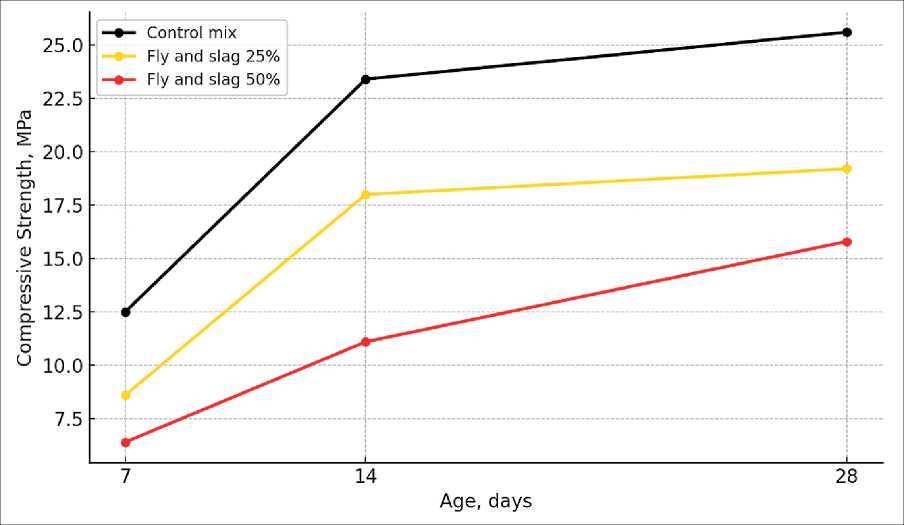
Fig. 6. Dynamics of compressive strength mixtures with axial different proportions of ash and slag at the age of 7, 14, and 28 days
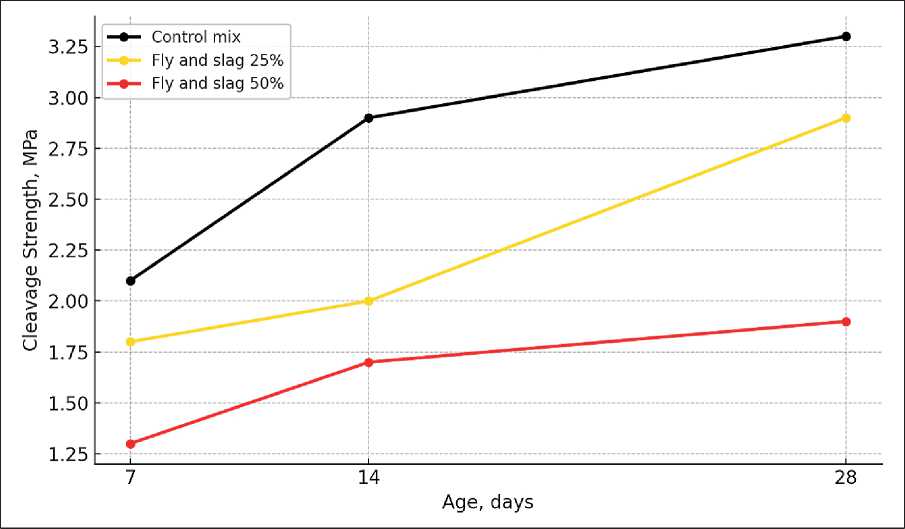
Fig. 7. Strength during cracking of concrete samples on days 7, 14 и 28 depending on dosage of ash and slag
MANUFACTURING TECHNOLOGY FOR BUILDING MATERIALS AND PRODUCTS
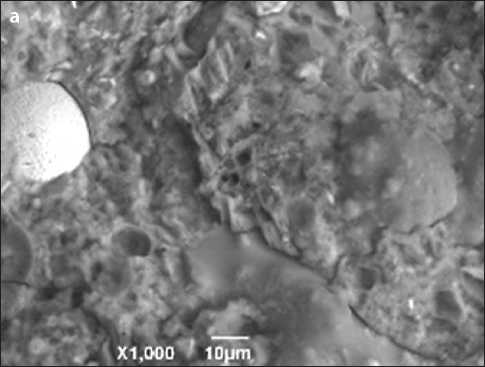
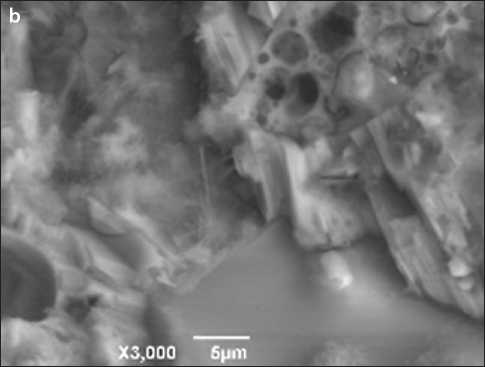
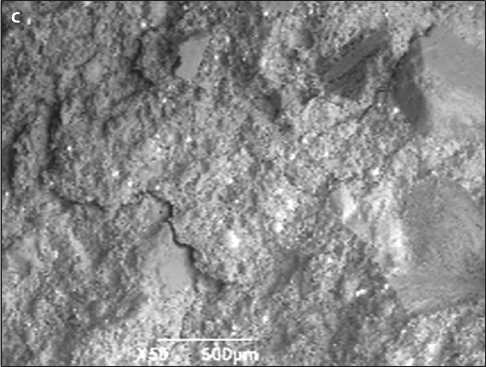
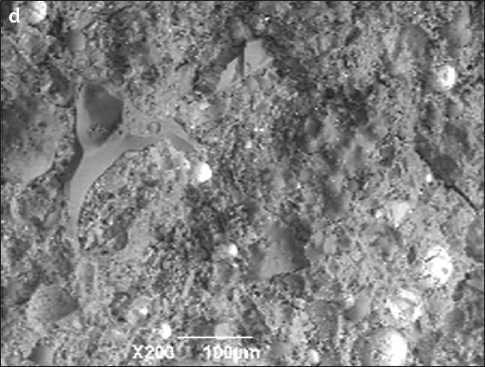
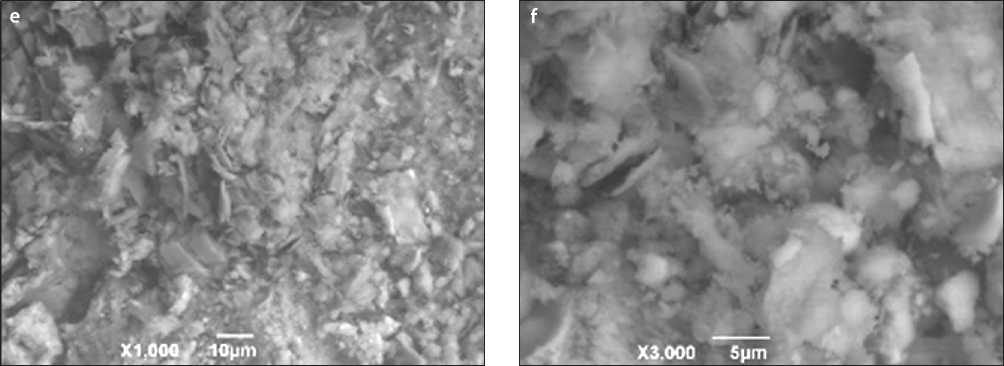
Рис. 8. SEM images of samples: a, b – 25% of ash and slag; c, d – 50% of ash and slag; e, f – control
compacted, with pronounced porosity, and unfilled pores. Meanwhile, a mixture with 25% of ash and slag (a, b) displays a more compact packing of hydrate products. Control composition (e, f) is characterized by a homogeneous and dense structure with C–S–H phases. These observations are consistent with results of strength tests and confirm the influence of micro and nanostructure on the physical and mechanical properties mixtures.
The suggested method differs from existing ones by including a comprehensive assessment of not only strength characteristics, but also shape stability, interlayer adhesion, and manufacturability of mixtures. Using targeted
MANUFACTURING TECHNOLOGY FOR BUILDING MATERIALS AND PRODUCTS
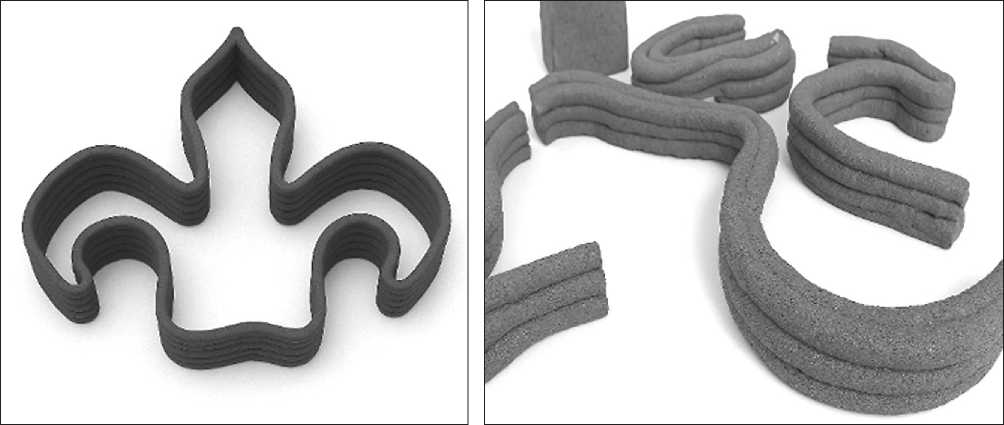
Fig. 9. External view of 3D-printed samples
fractional selection of ash and slag (0.315–0.14 mm) allowed to achieve the balance between pumpability and shape stability, and the application of extrusion modes ensuring the stability of layered structure (Fig. 9).
Nevertheless, this study has several limitations. The work was limited with the use of only one type of ash and slag, reducing the generalizability of the result. In addition, the strength characteristics were determined only within 28 days, whereas it is known that the activity of ash and slag materials may develop at later stages of curing. Also, analysis on resistance to aggressive environments and conditions such as freeze-thaw cycles was not conducted, which is needed for a comprehensive evaluation of the durability of material.
For further research, it is planned to focus on areas in quantitative analysis of porosity and phase composition (e.g., applying X-ray and computed tomography and X-ray diffraction), expanding the statistical sample size, and studying shrinkage and deformation properties, critically important for 3D-printing.
The development of the following direction may also include the application of various types of ash and slag or other industrial additives, the analysis of printing parameters (speed, interval between layers, curing regimens), also the incorporation of numerical methods of control and mathematical modelling of shape stability and strength. One of the key tasks of future work is to develop normative criteria for evaluation of the composition properties using industrial waste for additive construction. Challenges related to high variations of ash and slag compositions, the scalability of technology, and the need to align with requirements of mixture and printing parameters are expected.
Thus, this study confirmed the possibility of effective use of ash and slag waste as a partial sand replacement in concrete mixtures for 3D-prinitng under optimized composition and manufactural parameters, ensuring the required strength and processing properties.
CONCLUSION
Conducted study allowed to successfully implement all objectives and obtain a comprehensive assessment of influence of ash and slag waste on properties of fine-grained concrete for 3D-printing. Based on physical and mechanical analysis of components, the initial parameters were justified for selecting the composition of concrete mixture. Development of experimental samples with partial sand replacement of 25% and 50% by ash and slag demonstrated that replacement level of 25% ensures an optimal combination of shape stability, strength, and manufacturability.
Rheological test confirmed that mixtures with added ash and slag can adapt to the conditions of extrusion printing based on regulations of water-cement ratio and dosage of plasticizer. Limits in mobility were identified to ensure stability installation and reliable interlayer adhesion.
Results of mechanical tests demonstrated that compressive and cracking strength of the composition with 25% of ash and slag get close to the control, and micro and nanostructural analysis revealed development pf an amorphous aluminosilicate phase, which promotes hardening in later stages. Data confirm the effectiveness of the application of ash and slag under suitable conditions of preparation and dosage.
Thus, obtained results allow to recommend a partial replacement of sand with ash and slag waste by 25% to apply in compositions of fine-grained concrete used in 3D-printing. This solution not only improves the environmental friendliness of construction methods but also expands the raw material base without compromising the operational characteristics of the product.
MANUFACTURING TECHNOLOGY FOR BUILDING MATERIALS AND PRODUCTS