Организация цифрового производства деталей узлов малоразмерных газотурбинных установок
Автор: Смелов В.Г., Кокарева В.В., Чертыковцев П.А.
Журнал: Известия Самарского научного центра Российской академии наук @izvestiya-ssc
Рубрика: Машиностроение и машиноведение
Статья в выпуске: 4-2 т.25, 2023 года.
Бесплатный доступ
В статье приводятся результаты организации цифрового производства деталей и узлов малоразмерных газотурбинных установок. Разработаны функциональная структура информационных компонентов цифрового производства МГТУ, функциональная модель цифрового производства, контекстная IDEF0-диаграмма функциональной модели процесса «Цифровое производство МГТУ», построены контекстные диаграммы «Управление производством» и «Интеллектуальное решение», приведена структурная модель цифрового производства. Представлены три уровня цифрового производства и атрибуты их данных. А также разработана схема формирования производственных заданий с описанием атрибутов данных объектов производственной системы и атрибутов событий цифрового производства. Функциональная модель цифрового производства выполнялась в соответствии с рекомендациями по стандартизации Р 50.1.028-2001 Информационные технологии поддержки жизненного цикла продукции «Методология функционального моделирования». Для создания цифрового производства применялся ГОСТ Р 57700.37- 2021 «Компьютерные модели и моделирование. Цифровые двойники изделий. Общие положения», ГОСТ Р 59799 - 2021 «Умное производство. Модель эталонной архитектуры индустрии 4.0 (RAMI 4.0)».
Организация производство, цифровая модель, малоразмерная газотурбинная установка, информационная система, конструкторско-технологическая подготовка производства
Короткий адрес: https://sciup.org/148327532
IDR: 148327532 | DOI: 10.37313/1990-5378-2023-25-4(2)-287-299
Текст научной статьи Организация цифрового производства деталей узлов малоразмерных газотурбинных установок
Цифровое производство деталей узлов малоразмерных газотурбинных установок (МГТУ) представляет собой сеть взаимодействующих физических и информационных компонентов производства, проектируемая как единая информационно-аналитическая система (ЕИАС), организованная в рамках единой модели производственной системы и адаптирующаяся к изменениям требований к изделиям и ограничений производства на базе технологии взаимосвязанного комплекса математических, физических и имитационных моделей объектов с соответствующими наборами параметров, входами/выходами, управляющими воздействиями, критериями, ограничениями и переменными оптимизации. На основе этих моделей
проводятся процедуры имитационного моделирования, прогнозирования характеристик, отбора перспективных вариантов, оптимизации параметров, как самого изделия (детале-сборочной единицы), так и средств его производства, с сокращением дорогостоящих испытаний опытных образцов, натурных экспериментов и внесения дорогостоящих изменений в производственную, сбытовую, сервисную и инфраструктуру двигателестроительного предприятия.
В состав ЕИАС входят:
-
- интеллектуальная конструкторско-технологическая подготовка производства (КТПП);
-
- имитационные модели производственных участков;
-
- информационная система управления ресурсами предприятия (APS/ERP-системы);
-
- системы оперативного учета и диспетчи-рирования (MDC/MES-системы);
-
- единая база данных (знаний) об отказах и сбоях производственного оборудования;
-
- ассоциативные и корреляционные связи между данными КТПП и производственной системой;
-
- интегрированная модель логистической поддержки бизнес-процессов, унифицирован-
- ный подход описания объектов на каждом этапе жизненного цикла изделия (ЖЦИ) и связей между ними с учетом их набором атрибутов для описания данных об изделиях;
-
- онтология данных на каждом этапе ЖЦИ: аккумулирование и анализ данных для формализации новых знаний средствами систем поддержки принятия решений;
-
- сбор, аналитическая обработка организационно-технической, технологической и измерительной информации.
Сегодня производство МГТУ является сервис-ориентированным, то есть предприятия продает не только само изделие, но и сервис, тем самым обеспечивая поддержку этапа эксплуатации энергоустановки. Реализация полного функционала ЕИАС позволит сформировать содержание цифрового паспорта изделия/ ДСЕ , который представляет собой совокупность проектно-производс твенных процедур и данных об изделии, связанных между собой и создаваемых на этапах жизненного цикла. При этом в цифровом паспорте отражаются те процедуры, в результате которых появляются данные об изделии в виде информационных объектов, которые в свою очередь описываются виде содержания (непосредственно файлы систем CAD/CAE/CAM/CAAM) и реквизитов (атрибутов). Информация по ходу реализации этапов ЖЦИ в ЕИАС накапливается, хранится, прогнозируется и оптимизируется для принятия проектных и/или производственных решений. Цифровой паспорт по сути является цифровым двойник изделия и ассоциируется с физическим изделием с помощью QR-кода, штрих-кода или другой технологии, например NFC. Исходными данными для ЕИАС является матрица требований, включающая требования к технико-экономическим параметрам изделия, к проектным решениям, к производственно-технологическим решениям, результаты маркетингового исследования. Цифровой паспорт представляет собой кортеж (набор данных), который состоит из множества классов, атрибутов, матрицы сопоставлений атрибутов классов и смежности классов. Электронные данные изделия/ДСЕ в цифровом паспорте содержат всю необходимую актуальную (in situ) информацию, характеризующую этапы КТПП, производства, испытания, эксплуатации и представляют собой передаваемые через IoT электронные документы различных форматов, графические (2D и 3D) объекты, файлы с результатами измерений и т.п. Таким образом, цифровой паспорт является «живой» электронной структурой изделия/ДСЕ, обобщающим документом, консолидирующим все технические данные об изделии, полученные по ходу реализации бизнес-процессов производства.
МЕТОДИКА ИССЛЕДОВАНИЯ
Функциональная модель цифрового производства выполнялась в соответствии с рекомендациями по стандартизации Р 50.1.028-2001 Информационные технологии поддержки жизненного цикла продукции «Методология функционального моделирования», а именно методологией IDEF0. В результате была построена первая версия функциональной модели системы цифрового производства, отображающая ее структуру и функции (сервисы), а также потоки информации, в том числе заданий, и материальных объектов, преобразуемых этими функциями. Функциональная модель «As–Is» позволяет определить взаимодействие процессов предприятия при проектировании и производстве МГТУ.
Укрупненно процесс управления цифровым производством МГТУ включает реализацию следующих функций:
-
1) анализ требований и составление технического задания – согласование с заказчиком или определение по результатам маркетинговых исследований функциональных параметров и характеристик качества МГТУ, его ДСЕ, в том числе стоимости изготовления, то есть формирование плана продаж;
-
2) проектирование и разработка конструкции МГТУ – реализация конструкторской подготовки производства, направленной на формализацию требований к изделию – МГТУ и его ДСЕ;
-
3) проектирование и разработка технологических процессов – реализация технологической подготовки производства, направленной на создание производственных мощностей, необходимых для производства и сборки ДСЕ МГТУ, то есть формирование плана операций;
-
4) планирование и организация производства – согласование плана операций с производственными ресурсами, формирование объемно-календарного и оперативного производственного планов;
-
5) производство и контроль – производство и сборка ДСЕ МГТУ согласно заданным объемам и характеристикам качества продукции и процессов.
Обратные связи между функциями обеспечивают интегрированность данных на каждом этапе производства ДСЕ МГТУ, что обуславливает наличие в структуре цифрвого производства следующих компонентов (рисунок 1):
-
- автоматизированное проектирование (САПР - система автоматизированного проектирования, CAD - Computer Aided Design);
-
- технологическая подготовка (АСТПП - автоматизированная система технологической подготовки производства, САРР - Computer Aided Process Planning);
-
- управление технологическими процессами (АСУТП автоматизированная система управления технологическими процессами, САМ -Computer Aided Manufacturing);
-
- планирование и управление производством (АСУП - автоматизированная система управления производством, APS - Advanced Planning and Scheduling, ERP - Enterprise Resource Planning, MES - Manufacturing Execution System);
-
- контроль качества (CAQ - Computer Aided Quality Assurance).
Исходя из анализа рисунка 1 в функциональной структуре цифрового производства выделено три компонента из множества информационных потоков:
-
1. Информация об изделии. В процессе разработки МГТУ данные о них преобразуются в конкретную концепцию - технический проект и техническое задание, затем проводится конструирование сборки МГТУ и отдельных его функциональных узлов – ДСЕ: колесо компрессора, колесо турбины, вал, камера сгорания. На основе спецификации МГТУ, в частности спецификации турбогенератора МГТУ, проектируются все его составляющие, и оформляется соответствующая конструкторская документация. Для этих бизнес-процессов используется система САПР (CAD) – Компас. Выполнение функций анализа принципиальной возможности изготовления проектируемых изделий, их прочностных, температурных и других характеристик осуществляется с помощью систем САЕ путем моделирования механических, термодинамических, кинематических процессов изготовления и эксплуатации. Результаты моделирования прикрепляются к соответствующим объектам
-
2. Информация о технологии изготовления изделий. В процессе разработки технологии сборки изделия и изготовления (формообразования) его отдельных деталей создается операционная и маршрутная технология, формируются требования к заготовкам, определяется потребность в комплектующих (нормалях, покупных деталях), оснастке, инструменте [1]. На этом же этапе - этапе технической подготовки производства - осуществляется программирование станков ЧПУ, промышленных роботов, контрольно-измерительных машин; планируются испытания изделий и отдельных его узлов на различных этапах производства. Данные биз-нес-процессы выполняются в системе АСТПП (САРР) – Вертикаль/Лоцман. При этом в результате моделирования технологических процессов, например технологии прямого лазерного выращивания при изготовлении заготовки корпуса, технологии литья по выплавляемым моделям при изготовлении заготовки колеса турбины, файлы и отчеты прикрепляются к соответствующим объектам ДСЕ МГТУ в виде отдельных файлов и архивов в PLM системе «Лоцман». Данный компонент отвечает за технологический состав изделий.
-
3. Информация о состоянии заказов. В процессе производственного планирования и управления производством используются данные о заказах, технологии изготовления изделий, сведения об имеющихся производственных мощностях, а также информация о текущем состоянии технологического оборудования и
Рисунок 1 – Функциональная структура информационных компонентов цифрового производства МГТУ
ДСЕ МГТУ в виде отдельных файлов и архивов в PLM системе «Лоцман». Данный компонент отвечает за конструкторский состав изделия.
межоперационного задела. Все эти бизнес-про-цессы реализуются на уровне АСУТП. Данный компонент отвечает за производственный состав изделия.
Уровень АСТПП получает от систем САПР и АСУП скоординированные, осуществимые в реальных производственных условиях конструктивные решения, а также заказы на техническую подготовку производства МГТУ. Автоматизированная система управления цифровым производством обеспечивает выполнение завершающего этапа создания изделия, когда используются, транспортируются и хранятся материалы и вспомогательные средства производства, необходимые для формообразования заготовок, а также происходит обработка деталей и сборка узлов и самих изделий.
ФУНКЦИОНАЛЬНАЯ МОДЕЛЬ ЦИФРОВОГО ПРОИЗВОДСТВА
На рисунке 2 приведена контекстная IDEF0-диаграмма функциональной модели процесса «Цифровое производство МГТУ», построенная в Business studio. Входными данными для начала работы над разработкой конструкторской документации МГТУ являются: технические условия работы двигателя, типовые характеристики узлов, параметры двигателя-прототипа, свойства материалов.
Инструментами, участвующими в процессе разработки конструкторской документации ДСЕ МГТУ, являются инженеры-конструкторы конструкторского бюро. Помимо этого, в процессе подготовки конструкторской документации участвуют инженеры смежных конструкторских отделов, выполняющие инженерные расчеты.
В процессе разработки конструкторской документации ДСЕ МГТУ на этапах начального проектирования и проектирования узлов управляющим воздействием является нормативно-техническая документация: руководящие документы, своды правил, государственные стандарты, руководящие технические материалы, отраслевые стандарты.
Выходными данными при разработке конструкторской документации МГТУ являются: рабочая конструкторская документация, чертежи деталей, сборки, технические описания и паспорта ДСЕ, содержащие данные о ресурсе, экологичности, CFD и тепловые модели, отчеты о проведении инженерных расчетов.
В качестве механизмов управления цифровым производством используются подсистемы организационно-технической системы ситуационного центра, реализующие процессы: управления деятельностью по созданию продукции; ОКР и разработки технического предложения; НИОТР и разработки технологий про-
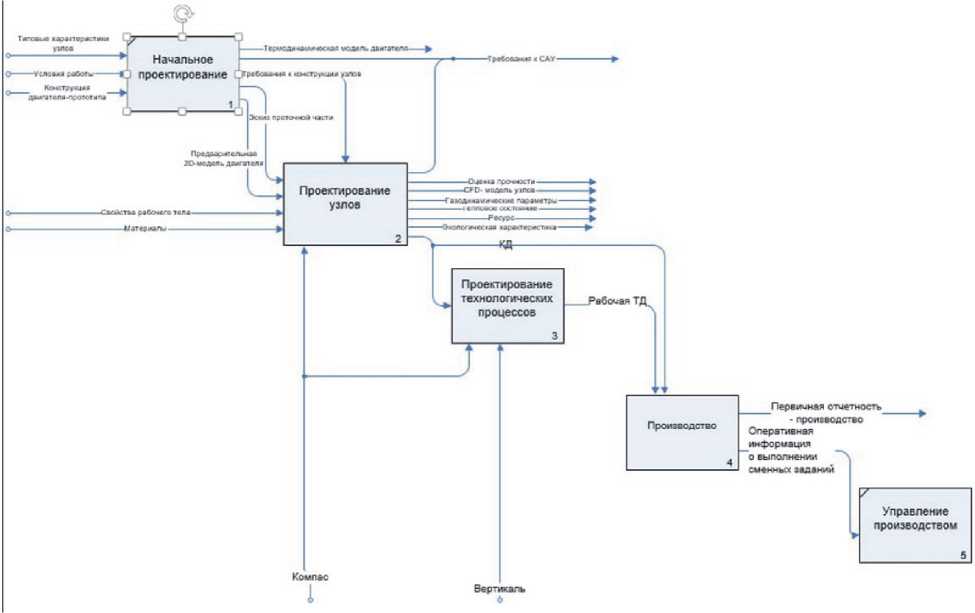
Рисунок 2 – Контекстная IDEF0-диаграмма функциональной модели процесса «Цифровое производство МГТУ»
Информация о
Оперативная информация а
"состоянии оборудования
Отчет о сравнении фактических показателей
Информация о - движении и -остатках ТМЦ
-------Заказ клиента
—Производственная программа
____Г рафик доступности мощностей Информация о состоянии оборудования
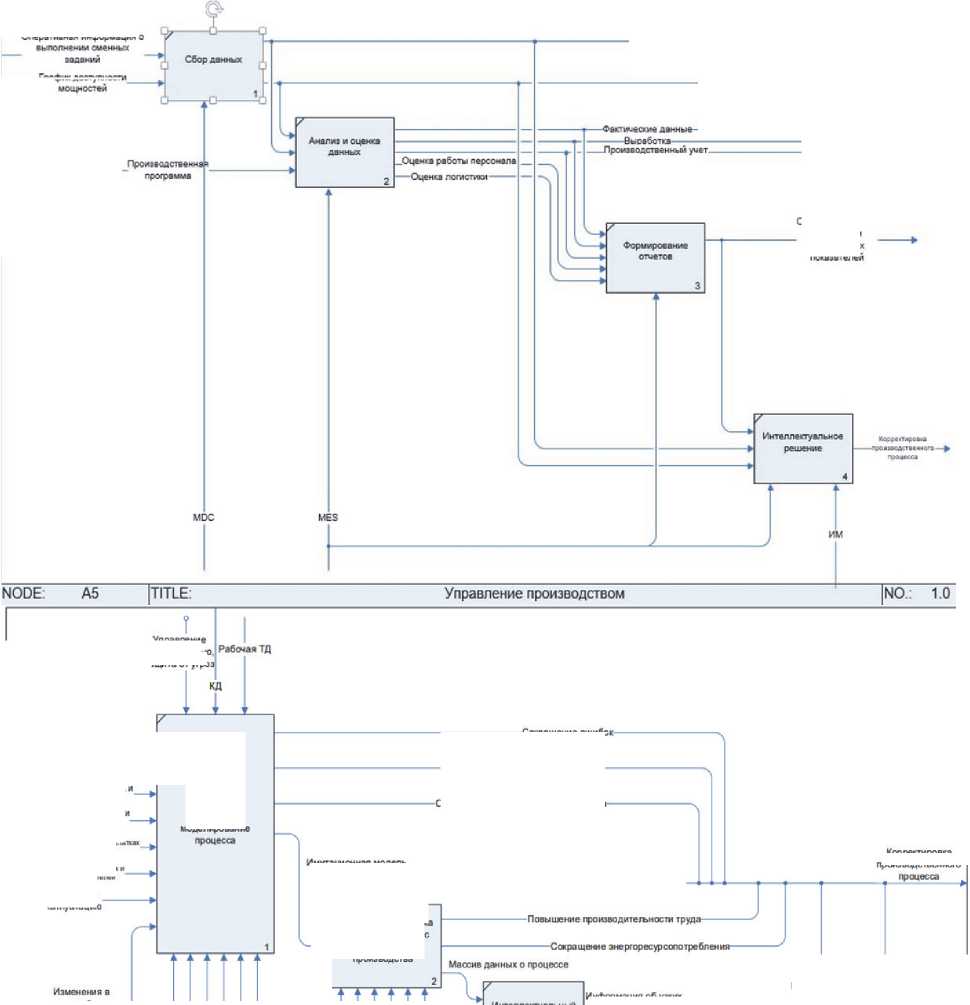
____Г рафик доступности oetorte
Прозрачность управления процессами настройках оборудования и ПО в случае сбоев и отклонений в протекании процессов
Информация об узких lecrax на производстве
управление безопасностью защита от угроз]
Сокращение ошибок
Сокращение отходов
Ькфсрмаци» о движений и остэпах
Омет о срвемент плановых факлнеоих гкмзатепей
_ Акт ввода в эксплуатацию
Симуляция и моделирование
Имитационная модель, цифровой двойник, цифровой макет
Сокращение производственного цикла-
Синхронизация потока данных о процессе с системой умного производства
корректировка произ водствен него
анализ данных
Повышение качества управления процесами
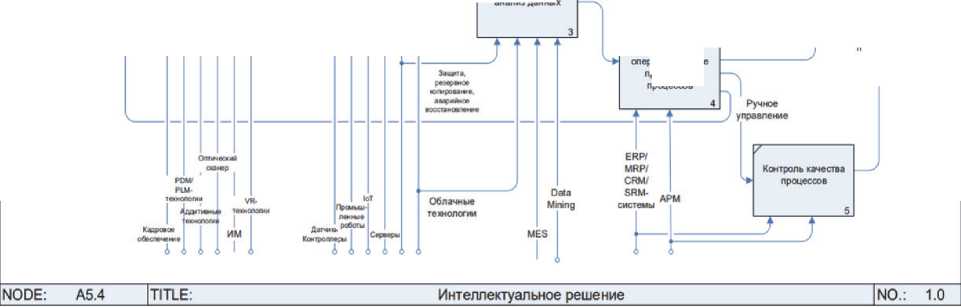
Облачные
Рисунок 3 – Контекстные диаграммы «Управление производством» и «Интеллектуальное решение»
Уведомление оратора о ходе протекания процессов
изводства; управления производством МГТУ заданного качества в установленные сроки; управления техническим обслуживанием и ремонтом (ТОиР) мощностей.
В целом этапы производства ДСЕ МГТУ реализуют внутрицеховую систему оперативного управления и диспетчерский контроль производством «точно в срок» под заданный такт сборки МГТУ, состоящей из 125 наименований ДСЕ.
Особенностью цифрового производства в части управления производством является сервис принятия интеллектуальных решений в блоке «Управление производством», контекстные диаграммы представлены на рисунке 3. В основной блок бизнес-процесса «Интеллектуальное решение» входят следующие задачи:
-
- симуляция и моделирование процесса,
-
- синхронизация потока данных о процессе с системой умного производства,
-
- интеллектуальный анализ данных,
-
- уведомления о ходе протекания процессов, - контроль качества процессов.
Основными ресурсами в задаче «Симуляция и моделирование процесса» являются технологии виртуальной реальности, имитационного моделирования. Моделированию подвергаются технологические процессы аддитивного производства с целью предотвращения появления брака на этапе изготовления заготовок, производственные процессы и организационно-технические решения. Синхронизация потоков данных о процессах в системе умного производства реализуется с использованием технологий IoT, датчиков и контролеров, серверов и промышленных роботов. Для диспетчеризации протекания процессов применяются ERP/MES-системы и автоматизированные рабочие места. Интеллектуальный анализ данных происходит с использованием Data Mining и MES-системы.
СТРУКТУРНАЯ МОДЕЛЬ ЦИФРОВОГО ПРОИЗВОДСТВА
Для оперативного управления производством используется сервис мониторинга состояния станков на базе MDC системы «АИС Диспетчер», который позволяет сформировать диаграммы загрузки производственного оборудования, количества обработанных деталей. Диспетчер имеет возможность получить полную информацию, как по всем деталям, так и по выборочным партиям, система позволяет с периодичностью получить сведения о степени готовности деталей, их текущем положении, а также о трудоемкости, стоимости и составе выполняемых технологических операций. В основе сервиса лежит сбор и обработка информации непосредственно с рабочих мест (центров) с применением SCADA технологий.
После передачи заказа в цех, актуальной становится задача составления производственного расписания, решение которой позволит оптимизировать работу цеха, исходя из различных критериев оптимальности (равномерности загрузки оборудования. минимума себестоимости производства, максимума загрузки оборудования, отсутствия пролеживания деталей и т. п.).
В общем виде структурная модель цифрового производства МГТУ состоит из трех уровней управления: управление предприятием, межцеховой уровень и внутрицеховой уровень (рисунок 4). Объектами управления и учетными единицами первого уровня (уровня предприятия) являются производственные заказы на определенную конфигурацию двигателей, что выражается соответствующей спецификацией, на втором уровне учетная единица – детале-сборочная единица конкретной спецификации МГТУ (ДСЕ), а на третьем уровне объектами управления являются технологические операции, реализующиеся на рабочих центрах (РЦ) с соответствующими ресурсами.
На модели указаны основные отделы (подразделения) производства, принимающие участие в разработке и изготовлении МГТУ: отдел главного конструктора (ОГК), отдел главного технолога (ОГТ), планово-экономический отдел (ПЭО), планово-диспетчерский отдел (ПДО), отдел материально-технического обеспечения (ОМТС), планово-диспетчерское бюро цехов (ПДБ). На схеме выделены база данных «Полном» (Вертикаль/Лоцман), в которой находятся единые данные для формирования технологических маршрутов и последующих сменных заданий, и MES-система, выполняющая функции производственного учета.
На рисунке 5 приведены основные бизнес-процессы цифрового производства по трем информационным уровням (слоям): PLM: Лоцман, Управление ресурсами ERP, Управление производством MES. В левой части изображены информационные системы и основные биз-нес-процессы. В правой части представлены результаты выполнения бизнес-процессов в соответствующих ПО, например, управляющие программы (УП) для станков с ЧПУ и 3Д принтеров - в результате написания УП в САМ модуле.
Цифровое производство создается с целью удаленного мониторинга состояния реального объекта (производственная система и объект производства) путем отображения на цифровой модели параметров его функционирования и индикации узлов и деталей оборудования, рабочие значения параметров которых отклоняются от нормальных; организации системы предиктивного обслуживания через анализ больших объемов статистических данных по работе оборудования за период времени; а также удаленного управления объектами через цифровую модель (передача управляющих сигналов от цифровой модели на реальный объект).
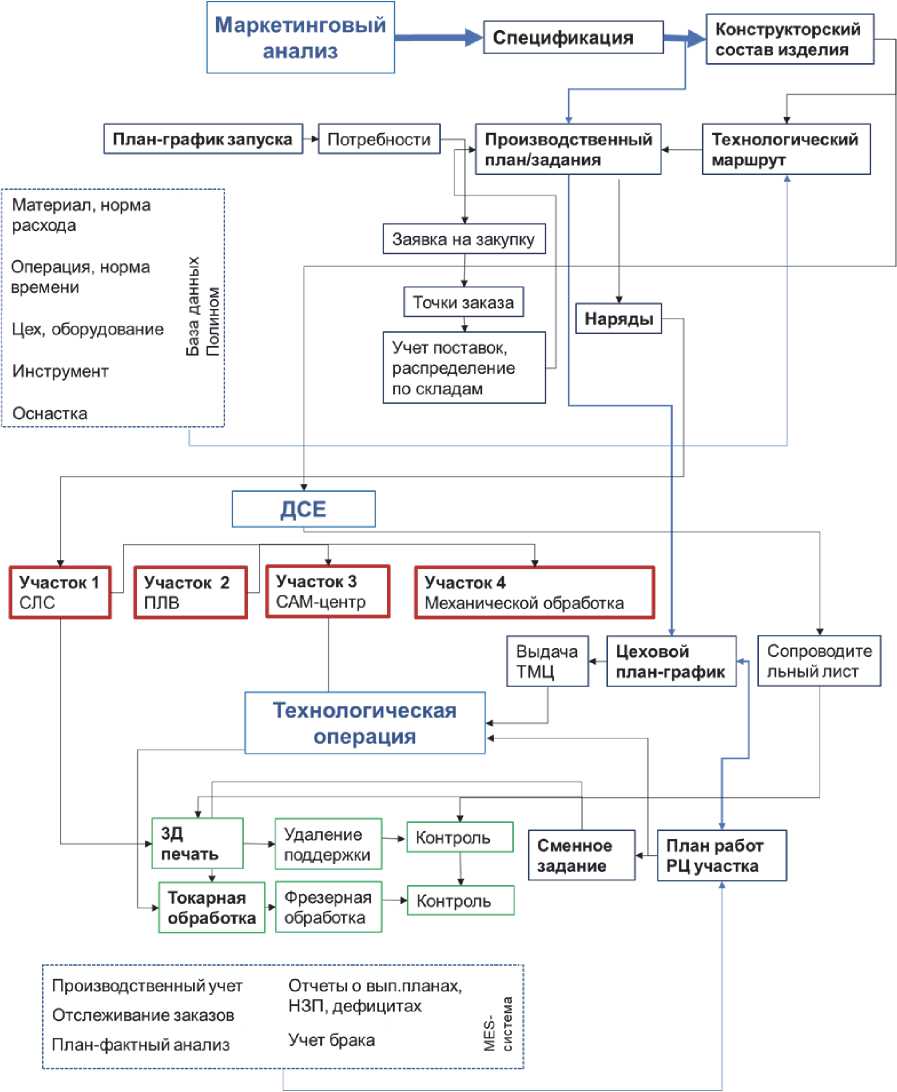
Рисунок 4 - Структурная модель цифрового производства
УРОВНИ ЦИФРОВОГО ПРОИЗВОДСТВА И АТРИБУТЫ ДАННЫХ
Концептуально цифровое производство состоит из трех уровней: уровень конструкторской подготовки, технологического процесса и производственного процесса.
-
1. Уровень конструкторской подготовки (модель включает процесс проектирования изделия с проведением инженерных расчетов, виртуальных сборок и испытаний). В результате формируется электронный макет ДСЕ, определяемый как совокупность электронных моделей
-
2. Уровень технологической операции/про-цесса (модель включает процесс изменения формы или свойств материала заготовки: механическая обработка, обработка давлением, термическая обработка, литье, сварка, аддитив-
Рисунок 5 - Структурно-информационная модель цифрового производства МГТУ
ные
и электронных документов, определяющих состав, форму и свойства изделия или его составной части в объеме, определяемом стадией его жизненного цикла.
Атрибутами данных являются: наименование и код ДСЕ, масса, размеры, данные о предельных отклонениях, технические требования, разработчик, подразделение.
технологии, контроль и сборка ДСЕ МГТУ).
В результате формируется электронная технологическая документация (ЭТД) и средства технологического оснащения, необходимые для осуществления заданного объема выпуска продукции с установленными технико-экономическими показателями: электронная модель тех- нологического маршрута; электронная модель технологического процесса; электронная модель технологической операции; электронная модель технологического перехода; управляющая программа для оборудования с ЧПУ. Электронная модель технологического маршрута содержит полное описание технологии изготов- ления ДСЕ, включая контроль и перемещения, а также информацию о применяемых материалах, заготовках, комплектующих, задействованных производственных единицах (в том числе их последовательности). Электронная модель технологического процесса содержит операционное описание технологического процесса изготовления ДСЕ в технологической последовательности, а также информацию о средствах технологического оснащения, материальных затратах, применяемом оборудовании, в том числе виды ЭТД, ориентированные на оборудование. Электронная модель технологической операции содержит описание последовательности выполнения переходов, информацию о применяемом оборудовании и предполагаемых трудовых затратах (профессии, разряды, количество исполнителей, длительность выполнения). Электронная модель технологического перехода содержит непосредственное описание технологических режимов, установов, ходов, приемов, наладки оборудования и т.д.
Атрибутами данных являются: характеристики оборудования (тип, стоимость, наименование), характеристики технологических переходов (режимы, инструмент, трудоемкость, номер перехода, текст перехода).
В технологический состав ДСЕ МГТУ входят следующие модели:
-
а) структурные модели:
-
1) технологическая структура изделия;
-
2) структурная модель технологического маршрута;
-
б) процессные модели:
-
1) процессная модель изготовления детали, заготовки и др.;
-
2) процессная модель сборки;
-
в) геометрические модели:
-
1) технологическая модель детали (заготовки);
-
2) технологическая модель сборочной единицы;
-
3) модель контроля изделия.
Технологический состав ДСЕ используется для оценки собираемости изделия, отображения особенностей технологии сборки, а также разработки на ее основе технологии сборки и формирования производственной кооперации и отражает иерархические взаимосвязи ДСЕ.
Структурная модель технологического маршрута предназначена для проработки и оценки возможных вариантов технологических решений и выбора рационального маршрута движения ДСЕ при его изготовлении и содержит возможные варианты совокупности и последовательности технологических процессов изготовления ДСЕ. Электронная модель технологического процесса включает в себя модели технологических операций в виде структуры, отражающей последовательность применения всех операций, относящихся к одному виду формоо- бразования, обработки, сборки и т.д., или к одной производственной единице (цеху/участку).
Процессные модели предназначены для проработки возможных вариантов, оценки, визуализации, рационального выбора и обоснования технологических решений и содержат информацию о возможных технологических операциях и вариантах применения инструмента, оборудования, средств технологического оснащения и др. Электронная модель технологической операции включает в себя модели технологических переходов в виде структуры, отражающей последовательность выполнения переходов на одном рабочем месте. Модель технологической операции отражается в операционной карте.
Технологическая модель ДСЕ (заготовки) отражает параметры детали, соответствующие технологическим процессам ее изготовления.
Модель контроля отражает параметры изделия, подлежащие контролю при завершении изготовления (или отдельных технологических процессов и операций), в том числе для контроля с применением контрольно-измерительных средств (приборов), 3Д сканирования.
В качестве исходных данных на уровне технологической операции выступает информация о свойствах материала заготовки, конструкции изделия, оборудования и технологической оснастки, предварительно выбранных технологических режимах. Моделирование осуществляется с помощью специализированных САЕ-систем, основанных на методе конечных элементов, и др. С помощью модели технологической операции решаются следующие задачи:
-
- отработка конструкции на технологичность;
-
- разработка технологического процесса производства изделия — выбор технологических режимов для каждой конкретной операции;
-
- проектирование и производство технологической оснастки;
-
- оценка стоимости производства.
Одновременно с моделью технологической операции создается модель изделия, учитывающая его микроструктуру, сформированную в процессе изготовления, а процесс моделирования носит итерационный характер. Результат моделирования технологической операции — расчетное время ее выполнения. Эти данные используются при построении имитационной модели технологического процесса — модели производственной ячейки.
На уровне технологического процесса моделируется совокупность процессов изменения формы заготовки при изготовлении изделия или изменения состава изделия в процессе операций сборки или разборки. Также на этот уровень выносится моделирование работы производственной ячейки, автоматизированных линий и участков, на которых технологический процесс реализуется полностью в рамках одной производственной ячейки, состоящей из различных технологических модулей (обрабатывающих, транспортных, сборочных и т. д.).
В качестве исходных данных выступает информация о выбранной технологии производства (в виде маршрутных технологических процессов), параметрах, полученных при моделировании отдельных технологических операций, о геометрических ограничениях производственных участков, на которых располагается или должно располагаться оборудование, его составе в рамках производственного участка, а также 3Д модели отдельных станков и технологической оснастки, роботов и других устройств автоматизации и механизации.
С помощью модели технологического процесса решаются следующие задачи:
-
- программирование отдельных устройств автоматизации для выполнения заданных операций в рамках основного или вспомогательного процесса;
-
- определение длительности операций для устройств автоматизации с учетом управляющих программ;
-
- синхронизация совместно работающих устройств на уровне виртуальных контроллеров и логических последовательностей сигналов и переменных, запускающих или останавливающих выполнение заранее заданных программ;
-
- расчет времени рабочих циклов для производственной ячейки и отдельного оборудования, задействованного в технологическом процессе;
-
- оптимизация времени циклов автоматизированных линий;
-
- расчет производительности элементов технологической системы.
-
3. Уровень производственного процесса (модель включает основные процессы, вспомогательные процессы: поставка, управление складами, человеческими ресурсами).
Таким образом, разработка моделей уровня технологического процесса позволяет не только получить управляющие программы для устройств и отработать в виртуальной среде алгоритмы их взаимодействия, но и получить данные, необходимые для экономического анализа того или иного организационного решения, а в отдельных случаях даже данные для отделов планирования производства, внутрипроизводственной логистики и планирования продаж.
Производственный состав ДСЕ включает в себя имитационную модель производственной системы по изготовлению ДСЕ МГТУ. На этапе имитационного моделирования определяются (задаются) виртуальные контроллеры для каждой единицы оборудования. Затем организуется связь между виртуальными контроллерами на уровне входных и выходных сигналов, посылаемых между устройствами. Далее моделируются основные и вспомогательные операции (задачи) для отдельных устройств, например, извлечение из формы и перемещение роботами полученной заготовки, удаление материала поддержек, перемещение по конвейеру и т. д. Для обеспечения синхронной работы и своевременного выполнения задач несколькими устройствами в программу каждой отдельной задачи вводятся переменные, инициирующие или останавливающие движение исполнительных устройств.
В результате моделирования получаются следующие данные:
-
- цифровая модель автоматизированного участка;
-
- управляющие программы для промышленных роботов;
-
- алгоритм взаимодействия оборудования;
-
- определение и оптимизация времени производственного цикла;
-
- расчет производительности автоматизированного литьевого участка.
Полученные данные по отдельно взятым участкам и автоматизированным производственным ячейкам и линиям служат основой для моделирования производственных процессов на межцеховом уровне.
Модели производственного процесса учитывают межцеховое взаимодействие и логистику, глобальные и локальные системы хранения и объединяют множество реализуемых технологических процессов на производственном предприятии в единую цифровую модель производственного процесса [2]. Подобные модели представляют собой уровень виртуального завода для задач проектирования производственных систем с нуля или комплексной модернизации существующих цехов и участков (расстановка оборудования и создание планировок, геометрические расчеты по планированию операций перемещения крупногабаритного оборудования). Модель необходима для расчетов производительности уже в рамках общего производственного процесса, оптимизации загрузки с учетом расчета производительности и загрузки соседних (параллельных) участков. Модель применяется для синхронизации процессов, что приводит к минимизации складских запасов полуфабрикатов, сокращению количества или размеров промежуточных складских систем и, возможно, к пониманию необходимости увеличения количества производственных ресурсов для определенных процессов с целью увеличения общей производительности и устранения узких мест [3].
На основе данных моделей создаются модели, описывающие конструктивные особенности здания завода, этапность строительства и необходимое строительное оборудование и содержащие в себе информацию о различных инженерных и информационных коммуникациях: электрических сетях и энергетических системах, гидравлических системах подачи технических жидкостей и промышленных газов к производственному оборудованию, информационных моделях, описывающих обмен данными между компьютерными системами, оборудованием, людьми и многое другое. При этом на одной модели реализуются одновременно несколько слоев информации:
-
- 2D-планировка;
-
- 3D-планировка и оборудование;
-
- инженерные системы;
-
- функциональные и логические диаграммы информационных потоков;
-
- технологические процессы и материальные потоки и др.
Модель предназначена для решения ряда задач:
-
- визуализация комплексных проектных решений;
-
- поиск узких мест в технологических маршрутах с учетом имеющегося и планируемого к закупке оборудования;
-
- оптимизация локальных систем хранения, расположенных в зонах между производственными участками и непосредственно у автоматизированных ячеек типа «робот — станок».
Исходными данными для моделирования служат:
-
- технологическая планировка цехов и участков;
-
- маршрутный технологический процесс в виде таблицы Excel;
-
- спецификация изделия, которое должен выпускать завод.
Результаты моделирования:
-
- масштабируемая 3Д модель завода;
-
- выявлены и устранены за счет добавления дополнительного оборудования узкие места в технологическом процессе; рассчитана производительность обозначенного технологического процесса с учетом планового объема выпуска и продолжительности рабочих смен;
-
- сокращение количества промежуточных складов;
-
- принятие принципиального решения об изменении и перепроектировании всего механического производства.
На рисунке 6 представлена схема формирования производственных заданий на рабочие центры согласно разработанным технологическим процессам в структуре цифрового производства.
Атрибутами данных производственного состава ДСЕ являются: тип оборудования, коэффициент загрузки оборудования, расход материала и инструмента, количество и тип бракованных ДСЕ, даты, сроки производства [4]. При этом стоит различать атрибуты данных объектов и событий производственной системы.
Атрибуты данных объектов производственной системы:
-
1. Идентификатор (ID) - идентификатор данных производства партии ДСЕ, задается на этапе КТПП;
-
2. Описание - информация о данных производства партии ДСЕ, например, соответствие установленным требованиям;
-
3. Дата создания – дата создания данных о производстве партии ДСЕ;
-
4. Применяемое оборудование - ссылка для идентификации ДСЕ и подразделений с рабочими центрами внутри физической иерархии производства, например: цех №, производственный участок №, рабочий центр № (РЦ);
-
5. Статус данных: отражает текущее состояние жизненного цикла данных партии ДСЕ: в работе, ожидает, сдано и т.п.
Атрибуты событий цифрового производства:
-
1. Тип события – определяет тип события: в процессе, не работает, выполнено;
-
2. Идентификатор оборудования – идентификация РЦ на конкретном производственном участке;
-
3. Значение - значение, ассоциированное с событием, например, штатный режим, аварийный, открыта дверь и т.п.
-
4. Идентификатор персонала - идентификация лица, ассоциированного с событием.
ЗАКЛЮЧЕНИЕ
Цифровая модель производства генерирует большие объемы данных, которые могут быть переданы в систему машинного обучения вместе со статистическими данными о качестве выпускаемой продукции. После сбора и анализа информации система начинает самостоятельно обучаться и становится способной к прогнозированию и предотвращению издержек производства, связанных с браком или поломкой производственного оборудования, в том числе путем проведения высокоточного, высокопроизводительного моделирования и статистического анализа его результатов, что и формирует модель цифрового производства малоразмерных газотурбинных установок.
Модели технологических операций служат для проведения множества виртуальных экспериментов, результаты которых в совокупности с данными о браке и результатами реальных экспериментов могут стать статистической базой для обучения ICPS в плане качества, что уже сейчас приводит к сокращению натурных экс-
План производства по срокам объемам

качества
.^ Сроки
Детализированное расписание для РЦ
Текущий план выпуска
Производственные мощности
Портфель заказов = номенклатурный план выпуска
Рисунок 6 – Схема формирования производственных заданий
Показатели
Объемнокалендарное планирование
Оперативно-производствен планирование
Производств енное
расписание
Расписание
для цехов
Производственные условия

периментов. Модели уровня производственных процессов (отдельное оборудование, участки и линии) служат для отображения на них данных и состояний производственного оборудования, приема сигналов с датчиков и отправки сигналов на PLC. Для создания цифрового производства применялся ГОСТ Р 57700.37– 2021 «Компьютерные модели и моделирование. Цифровые двойники изделий. Общие положения», ГОСТ Р 59799 – 2021 «Умное производство. Модель эталонной архитектуры индустрии 4.0 (RAMI 4.0)».
Список литературы Организация цифрового производства деталей узлов малоразмерных газотурбинных установок
- Громовая, Е.А. Разработка тренажера автоматизированного рабочего места технолога для проектирования технологических процессов магнитно-импульсной обработки металлов / Е.А. Громовая, И.Н. Хаймович // Современные информационные технологии и ИТ-образование. - 2021. - Т. 17. - № 3.
- Хаймович, И.Н. Организационно-экономическое моделирование системы автоматизации проектирования на предприятии заготовок и штампов компрессорных лопаток авиационных двигателей / И.Н. Хаймович, А.С. Кутумов, В.М. Рамзаев // Вестник Самарского муниципального института управления. - 2021. - № 3. - С. 45-52.
- Чурилин, С.В. Базовая концептуальная модель данных конструкторско-технологической подготовки производства в едином информационном пространстве предприятия / С.В. Чурилин, И.Н. Хаймович // Известия Самарского научного центра РАН. - 2020. - Т. 22. - № 4 (96). - С. 57-63.
- Махитько, В.П. Имитационное моделирование в мелкосерийном производстве / В.П. Махитько, И.Н. Хаймович, А.С. Клентак // Вестник Самарского муниципального института управления. - 2019. - № 3. - С. 17-25.