Перспективы использования энергосберегающего оборудования в вагоноремонтном производстве
Автор: Алферова Тамара Викторовна, Разон Валерий Федорович, Бирилло Наталья Сергеевна
Журнал: Агротехника и энергообеспечение @agrotech-orel
Рубрика: Энерго- и ресурсосбережение
Статья в выпуске: 4 (17), 2017 года.
Бесплатный доступ
В статье на примере Барановичского депо рассмотрены перспективы использования энергосберегающего оборудования в вагоноремонтном производстве. На основании анализа балансов электроиспользования по группам электрооборудования и по фактическому сроку эксплуатации электропотребляющего оборудования определены приоритетные мероприятия по энергосбережению: использование тепловых вторичных энергоресурсов (ВЭР), образующихся при работе компрессорного оборудования на нужды отопления и горячего водоснабжения; применение инверторных источников питания сварочной дуги Nebula-315; внедрение системы автоматизированного учета электроэнергии. Выполнен расчет экономической эффективности энергосберегающих мероприятий, определены сроки окупаемости.
Энергосберегающее оборудование, вагоноремонтное производство, баланс электроиспользования, вторичные энергоресурсы, эффективность, окупаемость
Короткий адрес: https://sciup.org/14770230
IDR: 14770230
Текст научной статьи Перспективы использования энергосберегающего оборудования в вагоноремонтном производстве
Введение. Эффективность использования топливноэнергетических ресурсов является одной из важнейших задач, стоящей перед экономикой Республики Беларусь [1].
Железнодорожный транспорт является одним из крупнейших потребителей энергоресурсов в стране, расходуя около 5% электроэнергии и почти 11% дизельного топлива. Энергетическая эффективность в современных условиях является важнейшим фактором повышения конкурентоспособности Белорусских железных дорог на внутреннем и международном рынке транспортных услуг.
Снижение расхода энергии посредством совершенствования технологических процессов и применяемого оборудования – основное направление, относящееся к наиболее эффективным способам энергосбережения. Повышение КПД дизельного или электрического двигателя, механической части локомотива, коэффициента сцепления колес и рельсов, лубрикация рельсов и гребней колес приводит к существенному снижению энергопотребления. Изменение структуры энергопотребления – переход на полное или частичное использование природного газа или экологически чистого жидкого топлива приводит к двукратному снижению выбросов вредных веществ в атмосферу, что значительно дешевле использования газоочистного оборудования [2].
В условиях увеличения конкуренции на рынке транспортных услуг важную роль играет сокращение всех видов издержек, связанных с эксплуатацией, ремонтом и обслуживанием подвижного состава [3]. Учитывая высокую степень насыщения предприятий вагонного хозяйства технологическим оборудованием, непрерывный рост степени механизации технологических процессов, обусловленный необходимостью улучшения показателей производительности труда, вопросы энергосбережения при ремонте и обслуживании вагонов приобретают все большую значимость. При этом важно отметить, что вопросы энергосбережения в вагоноремонтном производстве должны рассматриваться комплексно с учётом как непосредственного снижения затрат топливно-энергетических ресурсов (ТЭР) на ремонт и техническое обслуживание (ТО) вагонов, так и повышения энергетической эффективности перевозочного процесса в целом. В связи с этим проблема энергосбережения на вагоноремонтном производстве является актуальной и заслуживающей внимания.
Основная часть. Перспективы использования энергосберегающего оборудования в вагоноремонтном производстве рассмотрим на примере Барановичского депо. Основным функциональным назначением вагонного производства является обеспечение перевозок пассажиров и грузов исправными вагонами, удовлетворяющими требованиям безопасности движения, при наличии необходимых для удобств пассажиров и сохранности перевозимых грузов. Основные задачи: поддержание вагонов в исправном состоянии путем проведения технического обслуживания, текущего, деповского, капитального, капитально-восстановительного ремонтов, подготовка вагонов к перевозкам, обслуживание пассажирских поездов и рефрижераторных вагонов в пути следования. Барановичское вагонное депо является структурным подразделением Барановичского отделения Белорусской железной дороги и предназначено для производства деповского и капитального ремонта всех типов грузовых вагонов колеи 1520 мм, а также для изготовления и ремонта отдельных узлов и деталей.
В состав вагонного депо входят следующие участки:
-
– вагоносборочный производственный участок, на котором производится ремонт кузовов вагонов, крыш вагонов, выгрузочных устройств;
-
– ремонтно-коплектовочный производственный участок, на котором выполняются работы по ремонту тележек грузовых вагонов и их комплектующих, а также их диагностика;
-
– колесно-роликовый производственный участок, на котором производится полная и промежуточная ревизии колесных пар, а также полная диагностика колесных пар;
-
– автоконтрольный производственный участок, на котором производятся работы по ремонту тормозных приборов и их испытанию.
Для обеспечения бесперебойной работы основных ремонтных участков в депо имеются также вспомогательные участки:
-
– ремонтно-механический производственный участок;
-
– энергосиловой участок;
-
– участок по обслуживанию зданий и сооружений.
Предприятие осуществляет также текущий отцепочный ремонт и техническое обслуживание грузовых и пассажирских вагонов, контроль технического состояния вагонов при подготовке их к перевозкам на пунктах технического обслуживания вагонов.
Структура потребления энергоресурсов предприятием за 2016 год приведена на рисунке 1.
1,9% 1,5% 1,0%
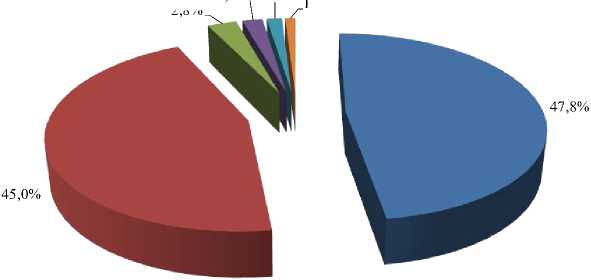
■ Теплоэнергия ■ Электроэнергия ■ Печное топливо ■ Торфобрикет ■ Дрова на отопление ■ Уголь
Рисунок 1 - Структура потребления энергоресурсов за типовой год, %
Из анализа рисунка 1 следует, что основная доля в общем балансе потребления энергоносителей приходится на тепловую и электрическую энергию.
Основные потребители тепловой энергии предприятия: система отопления и вентиляции; бытовое горячее водоснабжение (ГВС); моечные машины букс, подшипников и автотормозного оборудования
Расход тепловой энергии на отопление и вентиляцию производственных зданий и помещений депо с учетом потерь тепловой энергии в наружных внутризаводских тепловых сетях за 2016 год составил 1895,2 Гкал/год.
Годовой расход тепла на ГВС за 2016 г. составил 240,4 Гкал/год, расход технологическими потребителями – 845,4 Гкал/год.
Годовой расход электроэнергии по депо в целом за 2016 год составил 1834 тыс. кВт.ч/год.
В рамках проводимого на предприятии энергетического обследования [4,6] был составлен ориентировочный баланс расхода электроэнергии по группам электрооборудования (таблица 1 и рисунок 2), определена эффективность электроиспользования технологического оборудования и разработаны мероприятия по энергосбережению.
Таблица 1 – Распределение расхода электроэнергии по группам оборудования
№ |
Наименование группы электроприемников |
Расход электрической энергии |
|
тыс. кВт∙ч |
% |
||
1 |
Станочное оборудование и электропривод |
222,9 |
12,2 |
2 |
Подъемно-транспортные механизмы |
109,3 |
6,0 |
3 |
Сварочное оборудование и зарядные преобразователи |
291,2 |
15,9 |
4 |
Освещение |
400,1 |
21,8 |
5 |
Коммунально-бытовые приемники |
112,5 |
6,1 |
6 |
Вентиляционное, насосное и компрессорное оборудование |
400,1 |
21,8 |
7 |
Испытательное и лабораторное оборудование |
41,2 |
2,2 |
8 |
Оборудование с электронагревом |
141,7 |
7,7 |
9 |
Моечное оборудование |
64,5 |
3,5 |
10 |
Прочее |
50,4 |
2,7 |
Итого |
1 834,0 |
100,0 |
Эффективность электроиспользования оборудования определяется его КПД, удельным расходом электроэнергии или выполняемой работой и, в определенной степени, зависит от физического и морального износа (срока эксплуатации), а также оптимальной интенсивности его работы. Под физическим износом понимается изменение технического состояния вследствие длительных переменных или постоянных нагрузок, под моральным износом – старение исправного оборудования, дальнейшая эксплуатация которого нецелесообразна из-за создания нового технически и экономически более совершенного аналогичного назначения. О степени физического и морального износа можно судить по фактическому сроку эксплуатации оборудования.
Станочное оборудование и электропривод
П одъемно-транспортные механизмы
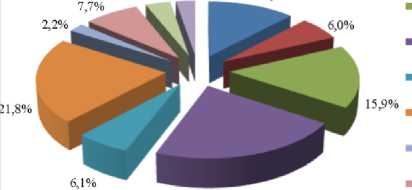
21,8%
Св арочное оборудование и зарядные преобразователи Освещение
Коммунально-бытовые приемники
Вентиляционное, насосное и компрессорное оборудование Испытательные и лабораторное оборудование
Оборудование с элекгронагревом
Моечное оборудование
Прочее
Рисунок 2 – Структура баланса электроиспользования по группам электрооборудования, %
Баланс электропотребляющего оборудования по фактическому срок ке 3.
10,20%
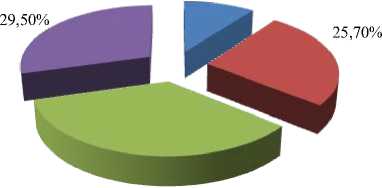
■ до 5 лет
■ 5-10 лет
■ 10-20 лет
■ более 20 лет
34,60%
я по фактическому сроку эксплуатации, %
Из анализа рисунка 3 следует, что 64,1 % электропотребляющего оборудования имеет фактический срок эксплуатации более 10 лет, из которых 29,5 % эксплуатируется более 20 лет. Оборудование, имеющее возраст 10 лет и более имеет большой физический и моральный износ, низкую эффективность, что требует повышенных удельных энергозатрат на его эксплуатацию. Оценка состояния активной части основных фондов позволяет утверждать, что на предприятии имеется значительный неиспользованный потенциал сокращения электропотребления за счет модернизации и замены морально и физически устаревшего оборудования, срок эксплуатации которого значительно превысил нормативный. Данное направление требует значительных материальных затрат со сроком окупаемости мероприятий более 15-20 лет, поэтому снижение электропотребления за счет модернизации и замены морально и физически устаревшего оборудования необходимо рассматривать в комплексе с мероприятиями по совершенствованию технологии и повышению качества услуг по ремонту вагонов.
На основании анализа вышеприведенных балансов были определены следующие приоритетные направления энергосбережения на предприятии:
-
- использование тепловых ВЭР .
К тепловым ВЭР, имеющимся на предприятии, можно отнести тепловую энергию, образующуюся при работе компрессоров [5]. Тепло от его работы передаётся маслу, которое в итоге и является основным источником тепла. Основная задача состоит в том, чтобы забрать у масла это тепло и утилизировать. Охлаждение масла в компрессорах осуществляется при помощи воздуха.
Тепловая энергия, выработанная двигателем и охладителями, может быть использована для отопления помещения соседнего метизного участка в отопительный период и нагрева горячей воды для нужд столовой в летний период.
Утилизацию тепла можно осуществлять 2-мя путями:
-
1. путём утилизации теплоты отработанного воздуха с применением воздушных каналов, применением вентиляционных решеток;
-
2. путём утилизации теплоты отработанного воздуха с применением теплообменного оборудования с жидкостным теплоносителем.
Направление теплого отработанного компрессором воздуха по воздушным каналам – это простой и экономичный способ рекуперации тепла. Возможно осуществление водяной рекуперации даже при использовании винтовых маслосмазываемых компрессоров с воздушным охлаждением. Для этого потребуется установка теплообменника в масляном контуре, однако, такая система выдает более низкую температуру, чем безмасляный компрессор.
На рисунке 4 представлена схема водяной рекуперации тепла отработанного воздуха компрессорами. Принцип работы заключается в следующем: теплота, утилизируемая от системы охлаждения компрессоров через масло-водяной (масло-масляный) теплообменник, будет использоваться для отопления соседнего помещения метизного участка в отопительный период. При этом существующую систему отопления (чугунные радиаторы типа МС-140) метизного участка оборудуем термостатическими вентилями, автоматически поддерживающими необходимую температуру воздуха в помещении. При полном покрытии отопительной нагрузки метизного участка теплом от компрессоров система термостатов будет автоматически отключать радиаторы существующей системы отопления, снижая тем самым потребление тепловой энергии от внешних тепловых сетей.
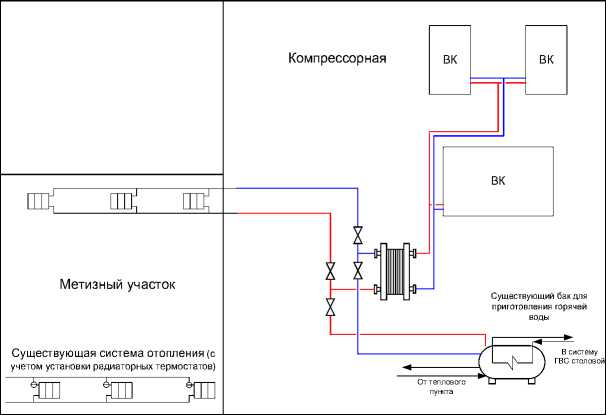
Рисунок 4 – Схема рекуперации тепла, выделяемого компрессорами
В летний период теплота, утилизируемая от компрессоров, может использоваться для подогрева горячей воды для нужд столовой в существующем теплообменном баке-аккумуляторе, что позволит отключаться от внешнего источника теплоснабжения в летний период и сократить потери в тепловых сетях.
Годовая экономия тепловой энергии при использовании системы рекуперации тепла составит:
Q = k ⋅ q ⋅ T ⋅ n ⋅η ⋅ 10-3,
где k
коэффициент загрузки по времени работы
компрессоров;
q – энергия вторичного использования тепла, Мкал/ч;
Т – время работы компрессоров в сутки, ч;
n – количество суток использования компрессоров в году, сут.; η – КПД системы рекуперации, отн. ед.
Экономия тепловой энергии при использовании системы рекуперации тепла составит:
– отопительный период
Qз = 0,25 ·(2·47+76)·24·194·0,8·10-3 = 158,3 Гкал/год.
-
– летний период
Qл = 0,1 ·(2·47+76)·24·194·0,8·10-3 = 63,32 Гкал/год.
Итого за год: Q =158,3+63,22=221,52 Гкал/год, или 37,7 т у.т./год.
Годовой экономический эффект равен 18544,6 бел. руб. Тогда, при стоимости рекуператоров тепла с учетом монтажных работ 3225,1 бел. руб, срок окупаемости данного мероприятия составит 0,2 года.
-
- замена устаревшего сварочного оборудования
На предприятии 15,9% потребляемой электрической энергии приходится на электросварку. Сварочное оборудование применяется для соединения металлов и их сплавов при проведении ремонтных работ. Основную часть сварочного оборудования составляют сварочные выпрямители типа ВД и ВДУ. Сварочные выпрямители предназначены для ручной дуговой электросварки прямого и сложного профиля, различных металлов и сплавов на постоянном токе, любой полярности, штучными электродами всех видов, а также в среде защитных газов. Постоянный ток в сварочных выпрямителях получается путём выпрямления переменного тока промышленной частоты с использованием полупроводниковых вентилей. Также на предприятии широко используются сварочные трансформаторы, предназначенные для ручной дуговой сварки (MMA), а так же резки и наплавки малоуглеродистых и низколегированных сталей покрытыми электродами на переменном токе.
В качестве мероприятий по снижению расхода электрической энергии на электросварку, предлагается внедрение современного сварочного оборудования, построенного на базе инверторных источников. В отличие от традиционных диодных выпрямителей, инверторные позволяют получить не только качественную сварку, но и существенную экономию электродного металла, за счет снижения величины разбрызгивания, экономию электроэнергии в результате высокого КПД и высокого коэффициента мощности.
Проведенные сравнительные исследования по стабильности процесса сварки, величине потерь на разбрызгивание, величине тепловложения, потреблению электрической энергии позволили сравнить наиболее часто применяемые источники питания ВД-306 (310) и инверторный источник питания Nebula-315, технические характеристики которых представлены в таблице 4.
Таблица 4 – Технические показатели источников питания дуговой сварки плавлением
Параметр |
ВД-306 |
ВД-310 |
Nebula-315 |
Максимальный ток, А |
315 |
315 |
315 |
Максимальная мощность в нагрузке (P2), кВт |
9,77 |
10,22 |
11,0 |
КПД, %, не менее |
70 |
70 |
90 |
Потребляемая мощность при максимальной нагрузке, кВА |
24 |
22 |
12,5 |
Исходя из вышесказанного, предлагается выполнить замену источников питания типа ВД-306(310) на инверторный источник питания Nebula-315, а также выпрямителей типа ВДУ-506 на инверторный источник питания Nebula-500.
Экономия электроэнергии при замене сварочного оборудования определяется по выражению [7,8]:
СУЩ ЭКОН
CB = ( УСТ УСТ ) И ГОД , ( )
где N – количество сварочных аппаратов, предлагаемых к замене, шт;
СУЩ
P УСТ – установленная мощность существующих сварочных аппаратов, кВт;
ЭКОН
P УСТ – установленная мощность энергоэкономичных сварочных аппаратов, кВт;
К И – коэффициент использования сварочных аппаратов;
Т ГОД – время работы сварочного оборудования за год, ч.
Основные показатели экономического эффекта приведены в таблице 5. Коэффициент загрузки принимается равным: для сварочных трансформаторов автоматической и полуавтоматической сварки – 0,35;
для однопостовой дуговой сварки постоянным током с полупроводниковыми выпрямителями – 0,35.
Таблица 5 – Расчет экономического эффекта при замене сварочных аппаратов
Наименование подразделения |
Экономи я ЭЭ, кВт∙ч |
Годовая экономи я денежны х средств, бел. руб |
Ориентировочны е капиталовложени я, бел. руб |
Средний срок окупаемост и, лет |
Вагоносборочный цех |
10669,7 |
2536,2 |
5557,0 |
2,23 |
Отделение по ремонту разгрузочных устройств |
4936,2 |
1173,3 |
3754,7 |
3,2 |
Отделение автосцепки |
1763 |
419,1 |
1885,8 |
4,5 |
Тележечное отделение |
2820,7 |
670,5 |
1877,3 |
2,8 |
Отделение плазменной резки |
10455 |
2485,2 |
6958,4 |
2,8 |
Отделение по наплавке надрессорных балок |
8554,2 |
2033,3 |
7116,7 |
3,5 |
Экспериментальн ый участок |
1303,5 |
309,8 |
1890,0 |
6,1 |
Участок изготовления крыш вагонов |
15881,9 |
3775,1 |
8886,9 |
2,3 |
ПТО ст Барановичи централ. |
2820,7 |
670,5 |
1877,3 |
2,8 |
Итого |
59204,9 |
14073 |
39804,1 |
2,83 |
-внедрение системы автоматического учета электроэнергии
Учет потребления электроэнергии на предприятии осуществляется 38 измерительными приборами преимущественно индукционной системы. В целях повышения эффективности учета потребления электроэнергии и достоверности измерительных комплексов необходимо планомерно произвести замену приборов учета индукционной системы на современные электронные. Применение электронных приборов позволит внедрить автоматизированную систему учета, контроля и управления электропотреблением (АСКУЭ), что даст возможность объективно анализировать и оценивать принимаемые технические или организационные решения, направленные на экономию ТЭР, выявить нерациональное использование электрической энергии[9,10]. Возможная экономия электроэнергии при использовании системы АСКУЭ за счет упорядочения учета составит не менее 1-3 % от общего потребления электроэнергии на предприятии, или 36680 кВт·ч/год.
При стоимости системы АСКУЭ с учетом монтажных работ, составляющей примерно 46209,8 бел. руб, срок окупаемости данного мероприятия составит 5,3 года.
Выводы. Анализ полученных результатов позволяет сделать следующие выводы:
– основная доля в общем балансе потребления энергоносителей Барановичского депо приходится на тепловую и электрическую энергию; основными потребителями тепловой энергии на предприятии является система отопления и вентиляции; бытовое горячее водоснабжение; моечные машины букс, подшипников и автотормозного оборудования;
– в структуре баланса электроиспользования по группам электрооборудования наибольшее электропотребление приходится на, вентиляционное, насосное и компрессорное оборудование (21,8%), на электрическую сварку (15,9%);
– из анализа баланса электропотребляющего оборудования по фактическому сроку эксплуатации следует, что 64,1% электропотребляющего оборудования имеет фактический срок службы более 10 лет, из которых 29,5% эксплуатируется более 20 лет;
– на основании проведенной оценки эффективности электроиспользования разработаны следующие приоритетные энергосберегающие мероприятия для Барановичского депо: использование тепловых ВЭР, образующихся при работе компрессорного оборудования на нужды отопления и ГВС; применение инверторных источников питания сварочной дуги Nebula-315; внедрение системы автоматизированного учета электроэнергии;
– экономическая эффективность предложенных энергосберегающих мероприятий подтверждена их невысокими сроками окупаемости, составляющими от 0,2 до 5,3 лет.
Список литературы Перспективы использования энергосберегающего оборудования в вагоноремонтном производстве
- Директива Президента Республики Беларусь «Экономия и бережливость -главные факторы экономической безопасности государства».
- Ресурсосберегающие технологии на железнодорожном транспорте: учеб. пособие для вузов ж.-д. трансп./Н. И. Зубрев, М. В. Устинова. -Москва: Учебно-методический центр по образованию на железнодорожном транспорте, 2015. -392 с.
- Энергосбережение на железнодорожном транспорте: учебник для вузов/В.А. Гапанович, В.Д. Авилов, Б.А. Аржанников ; под ред. В.А. Гапановича. -М.: Изд. Дом МИСиС, 2012. -620 с.
- Постановление Комитета по Энергоэффективности при Совете Министров Республики Беларусь «Об энергетическом обследовании организаций» № 964 от 29.07.2006 г.
- Закон Республики Беларусь «О возобновляемых источниках энергии» от 27 декабря 2010 г. № 204-З -Минск, 2010. -16 с.
- Закон Республики Беларусь от 8 января 2015 № 239-3 «Об энергосбережении». -Минск, 2015. -14с.
- СТБ 1776-2007 Энергетическое обследование потребителей топливно-энергетических ресурсов. -Минск, 2007. -8 с.
- Методические рекомендации по составлению технико-экономических обоснований для энергосберегающих мероприятий (дополнение). -Минск, 2008. -31 с.
- Методические рекомендации по составлению технико-экономических обоснований для энергосберегающих мероприятий. -Мн., 2000. -150 с.
- Свидерская, О.В. Основы энергосбережения: курс лекций/О.В. Свидерская. 4-е изд., стер. -Мн.: Акад. Упр. при Президенте Респ. Беларусь, 2006. (Система открытого образования).