Приемы оптимизации параметров управления технической эксплуатацией МТП в АПК
Автор: Дунаев А.В.
Журнал: Агротехника и энергообеспечение @agrotech-orel
Рубрика: Технологии и средства технического обслуживания в сельском хозяйстве
Статья в выпуске: 3 (36), 2022 года.
Бесплатный доступ
Цель исследования - уточнить приемы для оптимизации предельных значений диагностических параметров. Методы. Проанализированы основные исследования и НТД, они сопоставлены с практикой техсервиса МТП АПК. Результаты. В оптимизации диагностических параметров машин в АПК преобладала оптимизация допускаемых их величин, не управляющих надежностью техники. Главный прием - технико-экономический по минимуму прямых и косвенных удельных затрат и издержек на техсервис. Широко его использовал проф. Михлин В.М. Но его конкретика оптимизации не корректна, трудоемка и в практике не реализована. А обоснование предельных величин, единственно управляющих - недостаточное. Но «новая стратегия» техсервиса от ГОСНИТИ усугубляет: в ней оптимизация допускаемых величин с учетом скоростей изнашивания деталей якобы уменьшает вероятность их отказов в 3,5-5 раз? Предложено разделить приемы оптимизации предельных величин диагностических параметров по их функционалу, сфере оптимизации: производителями, потребителями, службами контроля. Заключение. Для оптимизации нормативов техсервиса нужны оперативные приемы. Так предельные величины возможно определять по данным бухгалтерии из условия достижения затрат на техсервис и от потерь урожая при отказе техники к стоимости аналогичного объекта.
Диагностический параметр, предельное значение, технико-экономическое обоснование, затраты на техсервис и издержки от потерь урожая
Короткий адрес: https://sciup.org/147239792
IDR: 147239792
Текст научной статьи Приемы оптимизации параметров управления технической эксплуатацией МТП в АПК
Введение. В технической эксплуатации МТП АПК работами, например [4, 8], естественное исчерпание ресурса деталей, узлов, агрегатов и машин представлено как отказ. А регламентные работы технической эксплуатации МТП, прописанные изготовителями машин и выполняемые с учетом результатов диагностирования – в [8] представлены как управление эксплуатационной надежностью. Но ни производители машин, ни их потребители об этом не догадывались.
И для управления надежностью, уменьшения и предотвращения отказов выстроена система номинальных, допускаемых и предельных значений диагностических параметров по техническому и технико-экономическому критериям [1- 3, 6 - 11]. Номинальные значения – соответствуют новым и отремонтированным объектам после их обкатки и приработки сопряжений трения. Допускаемые - предназначены обеспечивать безотказную работу объектов в предстоящий межконтрольный период. А предельные – те, при которых эксплуатация объектов не целесообразна во избежание аварийного изнашивания, механического отказа и потери технической и экологической безопасности: потеря работоспособности из-за разрушений, заклинивания, прорывов, прогаров и т.п.
Однако, оптимальные значения предельных и допускаемых величин диагностических параметров должного обоснования не имеют. Более того, в «новой стратегии» [4] тех серви са
Агротехника и энергообеспечение. – 2022. – № 3 (36) 25
МТП сделана попытка оптимизировать допускаемые значения диагностических параметров, не являющихся управляющими надежность объектов, путем учета индивидуальных скоростей изнашивания деталей, что якобы уменьшает вероятность их отказа в 3,5-5 раз. Такое - ложный информационный шум: ведь не зависимо от любых значений допускаемых параметров все детали дорабатывают до предельного состояния, до ремонта объектов, а учет скоростей изнашивания в эксплуатации МТП практически не возможен. Казалось бы, учет скоростей изнашивания деталей целесообразен при подборе деталей, годных к ремонту объектов. Однако, комплектация деталей при этом проводится не по темпам их изнашивания, а по физико-механическим и геометрическим показателям поверхностей, по требованиям на зазоры/натяги сопряжений, что в целом задано разработчиком объектов и аналогично - разработчиком НТД на ремонт [10].
Цель исследования : утвердить главными управляющими техническим состоянием узлов, агрегатов и машин предельные значения диагностических параметров, а также уточнить приемы их обоснования. Материалы и методы исследования: Использована основная литература и НТД по организации техсервиса машин и оборудования и оптимизации его показателей с начала ХХ-го века. Проведен анализ соответствия рекомендаций практике технической эксплуатации МТП АПК. Показаны заблуждения и ложные основания для оптимизации допускаемых величин диагностических параметров и др.
Результаты и их анализ. В [8] для управления надежностью техники сделан упор на оптимизацию величин допускаемых диагностических параметров, которая может уменьшать вероятность или предупреждать наступление отказов. Но в последнее время Ученый Совет ГОСНИТИ без какой-либо апробации принял более решительную «новую стратегию» технического сервиса, выдвинув её [4] на соискание ученой степени к.т.н. В ней допускаемые величины диагностических параметров оптимизируют с учетом скоростей изнашивания (как их определять в эксплуатации машин) неких «типовых» деталей, создав систему «ступеньки допусков». Для деталей с большой скоростью изнашивания предложено устанавливать меньшее значение допускаемого диагностического параметра, а для деталей с малой скоростью – соответственно большее значение этого параметра. И считается, что такие «ступеньки» позволяют уменьшать вероятность отказов деталей в 3,5-5 раз. Эта «новая стратегия» на основе ложных положений дилетантов [4] в технической эксплуатации МТП АПК может давать негативные следствия из-за некорректных предложений по организации технической эксплуатации МТП. Отсюда вытекает важность уточнения понимания, назначения и действительной роли допускаемых и предельных величин диагностических параметров, а особенно - должного обоснования их предельных величин.
Исторически в технической эксплуатации МТП сложились рекомендации, что по мере диагностирования своевременно проводят расчет остаточного ресурса объектов контроля, полную, частичную или с превышением его реализацию, а далее - уточнение вида и объема ремонтных работ и их проведение, что как аксиома утверждено в [1, 3, 6, 7, 9-11]. Однако в [8] это четко не изложено и большое внимание уделено оптимизации по минимуму суммарных удельных затрат значению допускаемого диагностического параметра, принятого управляющим надежностью техники, что алогично. Т.е. справочная роль допускаемого параметра преувеличена. А в усугублении этого в [4] ложно представлена, естественно не подтвержденная практикой, «новая стратегия технического сервиса», якобы уникально уменьшающая вероятность отказов неких «типовых» деталей в 3,5-5 раз. Отсюда «новая страт егия» только математическими изысками заочно «увеличивает ресурс «типовых 26
деталей» в 3,5-5 раз . Однако известно, что технологии машиностроения к началу XXI века исчерпали возможности дальнейшего повышения надежности техники, производятся «одноразовые» автомобили. Поэтому «достижения» «новой стратегии» от чиновников ГОСНИТИ не соответствуют не только практике использования продукции машиностроения, но даже элементарному здравому смыслу. Особо «актуальна» «новая стратегия» стала, когда запад стремится нанести России стратегическое поражение.
Но следует учесть, что в эксплуатации машин, оборудования доступа к основным ресурсоопределяющим деталям (кроме звеньев гусениц и некоторым подшипникам ходовой части) для определения скоростей их изнашивания нет. И учет этих скоростей для оптимизации в эксплуатации допускаемых величин диагностических параметров не возможен. А при ремонте комплектацию деталей (в основном новых) в сборочные единицы, узлы, агрегаты производят не с ориентировкой на скорости их изнашивания, а по нормативам разработчиков машин, оборудования, принятыми и в ремонте [11]. Отсюда «ступеньки допусков» в «новой стратегии» [4] – нонсенс.
О роли и значении допускаемых и предельных величин диагностических параметров. Исторически первыми в 20-е гг. нормативами в организации техсервиса машин были предельные износы по техническому, аварийному изнашиванию и допускаемые, при которых детали, сопряжения, узлы отрабатывали межконтрольный период без аварийного изнашивания, без отказа. Но аналогичные величины, обосновывавшиеся в наше время по технико-экономическому критерию, с учетом потерь от ухудшения функционирования объектов контроля, оказались меньшими. И при их соблюдении физических отказов агрегатов, самих машин и оборудования естественно меньше или они исключены.
Вслед за первым обоснованием предельного и допускаемого износов в начале 20-го века были обоснования оптимальных сроков службы машин и оборудования по техникоэкономическому критерию. В наше время с его применением в НИИАТ, а за ним и в ГОСНИТИ предложено обосновывать все нормативы технического сервиса, хотя в ГОСНИТИ [8] по трудоемкому и практически не используемому алгоритму. Так в [8] выполнена «научная» оптимизация допускаемых значений (U д ) ресурсных диагностических параметров, которые представили управляющими техническим состоянием и надежностью сельскохозяйственных машин. Этому в [8] уделено преувеличенное внимание, что не соответствует реальной практике технического сервиса машин и оборудования многих отраслей. Допускаемое значение (U д ) не является управляющим параметром, а управляющим является предельное значение, т.к. только с его ориентировки проводятся ремонтные работы по исчерпании ресурса объектов. Но в [8] пространно и на первый взгляд убедительно изложено противоположное. Ведь при ресурсном диагностировании допускаемое значение параметра не используют, а оперируют с текущим (U контр ,, порой совпадающим с U д ) и с предельным (U п ) значениями диагностического параметра, по которым при известной наработке (t контр ) рассчитывают остаточный ресурс. Его значение можно уточнять при повторном ресурсном диагностировании по исчерпании рассчитанного или же просто отправляют объект контроля на ремонт. Отсюда представление допускаемого значения диагностического параметра как управляющего – ошибочно.
Но, как правило, и без диагностирования объекты контроля дорабатывают до предельного значения диагностического параметра, до общего предельного или даже до аварийного состояния. К тому же чаще, по организационным условиям ремонт проводят в осенне-зимний период и таким образом научные поиски в [4, 8] являются непродуктивными.
Итого, допускаемое значение ресурсного диагностического или структурного параметра управляющего воздействия на надежность, ресурс объектов контроля, вопреки [4, 8] не оказывает. Управляющим является только предельное значение диагностического или структурного параметра. Отсюда «новая стратегия» [4], усугубляющая ошибку в [8], является информационным шумом. А по регулируемым, не ресурсным параметрам при достижении ими допускаемого значения или более проводят многие последующие регулировки, например в ГРМ, в АТЭ, ДТА, заменяют форсунки и др. до полного исчерпания ресурса объекта. То есть и по регулируемым не ресурсным параметрам допускаемые их значения управляющего воздействия на ресурс, на отказы, при качественном ТО, практически не оказывают. Но естественно, что при превышении предельных значений регулировочных параметров может наступать локальный отказ.
В целом, по прогнозируемым параметрам управляющее воздействие на техническое состояние объектов проводят только по предельным значениям диагностических параметров. А по непрогнозируемым параметрам отказы случайны, управлению, в основном, не поддаются, что требует новых технологий и средств технического сервиса.
Все же необходимо повторить, что не зависимо от любых величин «допускаемых значений диагностических параметров» управляющими техническим состоянием продуктов машиностроения являются только предельные величины диагностических и структурных параметров. А допускаемые величины - лишь справочные. С их ориентировки вынужденно определяют остаточный ресурс объектов. А в иных отраслях [2] допускаемые нормы диагностических параметров практически отсутствуют, или же имеется несколько предельных величин, или же строят тренды диагностических параметров, по которым и назначают момент постановки объекта на переборку. Отсюда вытекает высокая значимость должного обоснования предельных величин диагностических параметров, чему было уделено мало внимания.
Но следует признать, что допускаемые значения по регулируемым не ресурсным диагностическим и структурным параметрам (например, тепловые зазоры ГРМ дизелей, давления впрыска форсунок, угол начала подачи топлива, регулируемое давление моторного масла, зазоры в подшипниках ходовой части машин, давления в пневмо- и гидросистемах и др.) актуальны. Их своевременный контроль и регулировки способствуют нормальной эксплуатации техники. И здесь видна разница в том, что по регулируемым не ресурсным параметрам имеется возможность прямого на них воздействия своевременным контролем и регулировкой. А по не регулируемым ресурсным параметрам, особенно соответствующим параметрическим отказам, возможно продление срока службы объектов только тщательным соблюдением условий эксплуатации, качественным обслуживанием (смена масел, фильтров масляных, воздушных, топливных, очистка и мойка, защита от загрязнений масел, топлива и впускного воздуха, подтяжка креплений, устранение мелких неисправностей и т.п.), а также вводом ремонтно-восстановительных составов [5]. Отсюда для ресурсных параметров важно иметь оптимальные, достоверно установленные предельные их значения, что весьма проблематично: в исследованиях по техсервису в АПК и в других отраслях такие глубокие обоснования не известны.
В современных бортовых системах контроля автомобилей некие критические значения показателей имеются, но они скорее назначаются из конструктивных соображений или из показателей динамики простых эксплуатационных показателей: расход топлива, давление масел, воздуха и т.п. А ресурсные параметры в них отсутствуют.
Для особых случаев обоснование допускаемого значения диагностического 28
параметра (и остаточного ресурса) для примерной ориентировки можно рассчитывать из соотношения показателей самой кривой динамики диагностического параметра (1):
ип/Тполн Uд/tконтр или Uд/(Тполн - tост) ~ ид/(Тполн !^контр), где Un,, Uд - предельное и допускаемое значения диагностических параметров,
Тполн, tост, tконтр, ориентировочный возможный полный, остаточный ресурс объектов контроля, наработка в момент контроля.
И с учетом нелинейности кривой динамики параметра имеем:
ил = U а дп
t контр
т полн
А, исключая трудоемкое «научное» определение остаточного ресурса для старого МТП, имеются «Рекомендации по постановке машин на ремонт…» [9], где остаточный ресурс (срок постановки машин на ремонт) при известной наработке и значении ресурсного параметра непосредственно находят в 12-ти обстоятельных таблиц.
Все же, как оперативно устанавливать предельное значение показателя, управляющего надежностью, например, полный срок службы объекта контроля. В этом плане давно имелись многие ориентировочные подходы. Затем последовали все более уточненные технико-экономические обоснования полного срока службы машин по критерию достижения минимума суммарных удельных затрат на их технический сервис: А в 60-е гг. Кузнецовым Е.С. (НИИАТ) было предложено оптимизировать все показатели технической эксплуатации машин только по минимуму суммарных удельных затрат на её работы. И на этом основании в 80-е гг. проф. В.М. Михлин [8] более глубоко и шире обосновал этот критерий для несколько абстрактного обоснования допускаемых величин параметров техсервиса с.-х. машин, но с недостатками, изложенными выше.
Но если перейти к реальной практике, то следует разделить приемы обоснования нормативов диагностических параметров для функциональных, скорее конструктивных параметров, и отдельно для ресурсных технико-экономических (таблица 1).
Нормативы для функциональных параметров должны быть такими, чтобы хотя и с некоторым ухудшением, но всёже обеспечивать требуемое функционирование сопряжений, узлов в режимах заданных их разработчиком и ремонтником, например в [10]. И особыми здесь являются те параметры сопряжений, узлов и агрегатов, конструктивы и режимы работы которых должны обеспечивать техническую и экологическую безопасность машин. Такие нормативы задаются только их разработчиками перед постановкой продукции на серийное производство.
Таким образом, в технической эксплуатации МТП для обоснования по экономическому и технико-экономическим критериям остаются только предельные (не допускаемые) значения ресурсных диагностических параметров по п. 2 и 3 таблицы.
В отношении допускаемых для ремонта показателей деталей практика изначально однозначна и утверждена, например, в [10]: детали с нормальными показателями физикомеханических и геометрических свойств поверхности комплектуются в сопряжения для обеспечения их конструктивов, заданных разработчиком объекта. Никакие здесь новации от дилетантов [4] в технической эксплуатации машин и оборудования, в т.ч. «по новой стратегии» [4] для учета скоростей изнашивания деталей, не требуются, являются информационным шумом и могут лишь вводить неопытных практиков в заблуждение.
Таблица 1. Разделение показателей технического состояния самоходных машин в АПК по приемам их оптимизации
№ |
Тип параметров |
Сущность параметров |
1 |
Функциональные, задаваемые разработчиком изделий |
Номинальные, допускаемые и предельные значения, обосновы-ваемые по техническому критерию: давление моторного масла, эффективная мощность дизеля, давление надувочного воздуха, давления масел в гидросистемах навесного механизма и КП, осевые и угловые зазоры в сопряжениях силовой передачи и ходовой части, показатели АТЭ, систем освещения и сигнализации. См., например, табл. 23 Технического описания и инструкции по эксплуатации тракторов Т-150, Т-150К. Харьков, «Прапор», 1984. и другую НТД от ХТЗ и Харьковского моторостроительного з-да СМД. |
2 |
Ресурсные, по прогнозируемым параметрам к параметрическим отказам, обосновываемые потребителем изделий |
Предельные, определяемые по критерию минимума суммарных удельных затрат на техническую эксплуатацию с учетом потерь от ухуд-шения функционирования машин: Расход (давление) картерных газов, расход моторного масла на угар, удельный расход топлива, ко-нцентрация частиц металлов и кремния в маслах, подача насосов гидросистем, для обоснования срока и вида ремонта. Организационные: межремонтный, полный срок службы, вид и объем ремонта. |
3 |
Ресурсные для легкосъемных деталей, работающих до отказа, задаваемые разработчиком с потребителем изделий, |
Предельные, обосновываемые по техническому критерию: Износ звеньев гусениц, их пальцев, удлинение ремней, цепей, износ ножей, патрубков… |
4 |
Безопасности и экологии, задаваемые разработчиком изделий |
Показатели функционирования рулевого управления, тормозной системы, сцепления, освещения и сигнализации, дымности отработавших газов, шума выпуска и др. |
5 |
Регулировочные с допускаемы-ми значениями, задаваемыми разработчиком с потребителем изделий |
Традиционные: Тепловые зазоры в ГРМ, давление впрыска форсунок, угол начала подачи топлива из ТНВД, пределы частот вращения коленчатого вала, разрежение за воздухоочистителем, перепад давления на ФТО, максимальная температура в системе охлаждения и др. |
Примечание: Цикловая подача топлива в ТНВД непосредственно на самих тракторах, автомобилях и на других дизельных машинах и установках не контролируется. Номинальная её величина устанавливается только при изготовлении, при ремонте ТНВД на соответствующих стендах на заводе-изготовителе ТНВД, а при ремонте - на спецпредприятиях. И обосновывать ей в [4] допускаемое уменьшение на 15- 20 % от номинала, что ныне предлагается в ГОСНИТИ – нонсенс.
По обоснованию предельных величин показателей техсервиса машин и оборудования известно первое обоснование предельного износа деталей на примере тяговых цепей «Галля». Здесь было установлено, что временная динамика их износа и соответствующего удлинения описана кривой с тремя участками: приработки, нормального естественного износа, ускоренного изнашивания до аварийного разрушения. Эту кривую приняли как классическую, хотя она присуща лишь немногим деталям и известно разнообразие кривых износа и ухудшения параметров. Все же по цепям «Галля» впервые было предложено назначать окончание срока службы деталей, работающих до аварийного, предельного износа и отказа до начала этого аварийного изнашивания с параметром (U п ). Допускаемое же значение износа (U д ) – назначают величиной в начале последнего нормативного доремонтного периода.
Из классической кривой допускаемый износ (U д ) определяют:
U д = U п – V c T м , (3)
где Vc – скорость нормального естественного изнашивания на втором участке кривой, Tм - задаваемый межконтрольный период использования объекта.
Но практика любого производства требует экономического обоснования нормативов её управления. И установлено, что оптимальный метод определения полного ресурса машин массового производства – технико-экономический, когда находят момент времени эксплуатации, при котором наступает минимум суммарных удельных затрат и издержек на использование, обслуживание и ремонт машин. Здесь [5] пионерами решения таких задач были с 1925 г. инженер МПС Васильев В.О., в 1939 г. к.э.н. Буянов А.И., в 1953 г. к.т.н. Кабенин Н.Г., в 60-е гг. к.э.н. Колегаев Р.Н., в 70-е гг. к.э.н. Петухов Р.М., а акад. Селиванов А.И. получил более точное выражение для определения оптимального срока службы t машины/оборудования:
t =
б ------
N ( б - 1) с
где А = Q м – О 1 - первоначальная стоимость Q м машины/агрегата, уменьшенная на стоимость О 1 годных остатков при снятии машины/агрегата с эксплуатации;
С - коэффициент прогрессирующих затрат на эксплуатацию машины/агрегата;
δ – показатель степени роста прогрессирующих эксплуатационных затрат.
Так как Кузнецовым Е.С. в НИИАТ было предложено оптимизировать все нормативы технической эксплуатации машин по критерию минимума суммарных удельных затрат, то такой подход, с описанными ниже серьезными недостатками, был всесторонне развит проф. Михлиным В.М. [8], доведен до использования по номограммам, таблицам и даже в компьютерной программе Турбо-НЭК, что получило признание в России и за рубежом. А абстрактная целевая функция, например, оптимизации остаточного ресурса объекта через минимум суммарных удельных затрат и потерь «С» выражена так в [8]:
С(tост) =
min <
Q ( t ост ) A , [ 1 - Q(t ост ) ] C ',
_ t ф ( t ост )
t^(t ) ф ост
где Q – вероятность отказа элемента (объекта исследования),
А и С – показатели затрат, соответственно, на устранение последствий вероятного

отказа элементов, на замену элементов (со значениями их параметров выше допускаемых)
для предотвращения отказов, tост – искомый остаточный, а tф - предполагаемый фактический ресурс объекта исследований.
В частном случае остаточный ресурс детали, сопряжения, узла (а при tост равном нулю косвенно определяется и оптимальный срок службы и агрегата и машины, если использовать соответствующие им ресурсоопределяющие параметры) предложено Михлиным В.М. [8] вычислять по уравнению (6):
t ост = t п олн
uп
л
а
( u ( t ) J
- 1
где u (t) – текущее, специально измеренное значение параметра.
Математический аппарат В.М. Михлина [8] для оптимизации искомых параметров по минимуму суммарных удельных затрат и издержек требует регистрации динамики ресурсоопределяющих параметров деталей, контроле отказов и неисправностей, учете непрерывных и дискретных затрат на обслуживание и устранение отказов, издержек и потерь от простоев машин и оборудования. То есть требуется сбор большого по объему и времени диагностических и технико-экономических данных (рисунок 1), что крайне ограничило или практически исключило применение такого подхода.
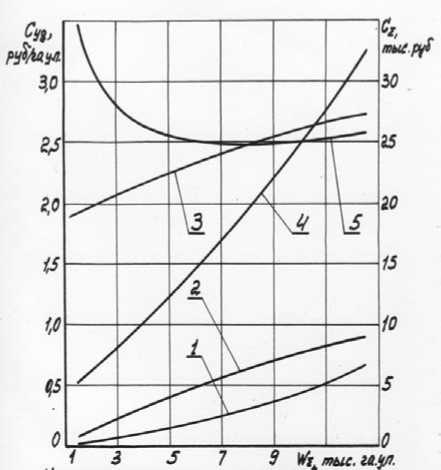
Рисунок 1 – Пример динамики затрат на использование гусеничных тракторов класса 3 т по наработке: 1 – удельные затраты на топливо-смазочные материалы; 2 - то же, на ремонт и техническое обслуживание; 3 - то же, что по п. 2, но с учетом зарплаты трактористу-машинисту; 4 - суммарные затраты; 5 – удельные затраты в расчете на га у.п.
Но ранее нами [5] было показано, что минимуму суммарных удельных затрат на техническую эксплуатацию машины примерно соответствует условие достижения абсолютной суммы этих затрат к стоимости новой машины. В те же 60-е гг. подобное мнение обосновал и Хан А.М. по погружным центробежным водяным насосам. А Чечет В.А. принял оптимумом срока службы деталей, узлов, агрегатов время при установлении равенства удельных дискретных (на ТО, ремонт) и удельных непрерывных (амортизационных) издержек на использование машин, что при их интегрировании примерно аналогично условию равенства суммы затрат на запасные части для ремонта к стоимости новой машины.
По такому подходу в 2000-2002 гг. в АТП Монголо-Российского горнорудного комбината «Эрдэнэт» по заданию руководства АТП для карьерных 110-тонных автосамосвалов БелАЗ-7512 оптимальный срок их списания определяли тем периодом эксплуатации, когда суммарные затраты на ремонт и устранение неисправностей машин (или хотя бы стоимость использованных запасных частей) становились равными стоимости новых машин [5]. Для этих машин стоимость перевозок ими руды с 0,25-0,30 $/т·км в начале эксплуатации через 4 – 6 лет снижалась до 0,07...0,0604 $/т·км с последующим ухудшением технического состояния машин, снижением производительности, повышенными простоями и затратами на ремонт, когда стоимость затрат на ремонт, по данным склада основных фондов АТП, достигала или несколько превышала стоимости машин 520 тыс. $ (рисунок 2). Отсюда оптимальные сроки службы машин были определены в 18-24 тыс. час, т.е. до 4-х лет.
Удельная стоимость перевозок по времени эксплуатации машин
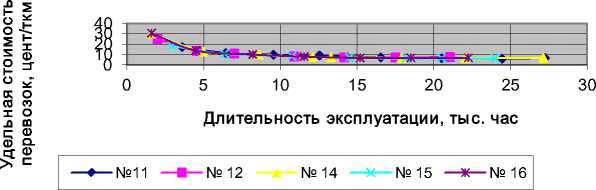
Рисунок 2 - Динамика удельной стоимости единицы работы пяти автомобилей БелАЗ-
7512 (учтены первоначальная стоимость автомобилей и затраты на их ремонт)
Но для служб СХП требуется оперативно определять остаточный ресурс ЦПГ для определения потребности ДВС в ремонте, например, по методу в [5] (рис.3).
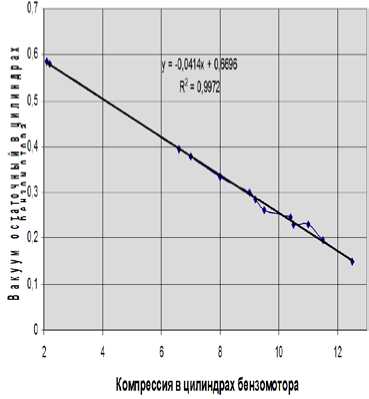
Рисунок 3 – Графики для определения остаточного ресурса отдель-ных цилиндров ДВС по зависимостям остаточного вакуума от компрессии (кгс/см2): бензиновых ДВС (а) со степенью сжатия 8-12; тракторных дизелей (б) со степенью сжатия 13,5-17
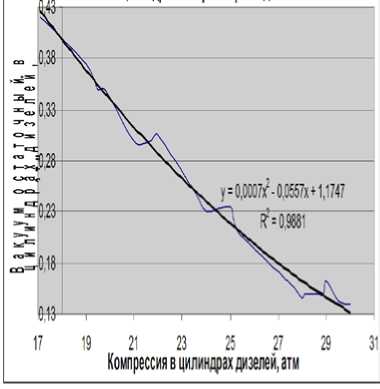
б
Примечание: При безаварийном изнашивании и точных измерениях точки диагностических параметров располагаются на кривых обоих рис. 3а и 3б. При аварийном же состоянии ЦПГ точки контроля располагаются выше или ниже линий тем далее, чем больше дефект ЦПГ.
Правое начало обеих линий – начало эксплуатации ДВС, остаточный ресурс – 100 %, а левый конец – выбраковка ЦПГ, остаточный ресурс – 0 %. Контрольные точки делят линии графиков на правую часть – использованный ресурс, и на левую – остаточный ресурс. Его вычисляют из соотношения длин обоих частей линий, умноженной на цену единицы длины правой части линий, если известна наработка (мото-ч, км пробега) в момент контроля.
Двигателям назначают наименьший остаточный ресурс какого-либо цилиндра. Первое диагностирование проводят после раскоксовки ЦПГ перед началом безразборного ремонта, например, вводом в ДВС трибосостава. Затем пускают ДВС на наработку около 50 мото-ч или на пробег 500 км и проводят второе диагностирование. И если первое диагностирование не показало аварийности ЦПГ, то эффект безразборного ремонта по данным второго диагностированию оценивают по смещению диагностических точек вправо, к «омоложению» ДВС.
Важная роль в методе по графикам рис. 3 принадлежит диагностированию ЦПГ. Применяемый для этого контроль компрессии, дополняемый контролем вакуума в цилиндрах по методике проф. Чечета В.А., позволяет определять как исправность деталей, образующих камеры сгорания, так и аварийные дефекты отдельных цилиндров в полевых условиях.
Но в обосновании нормативов технической эксплуатации МТП весомое углубление внес д.т.н. Ушанов В.А. (КрасГАУ [12]). В его методике назначения работ текущего ремонта тракторов по результатам диагностирования используются показатели:
R i∑ – степень изношенности трактора, оцениваемая как сумма средневзвешенных нормированных остаточных ресурсов его базовых агрегатов:
R i∑ = ∑γ i T остi /Т оi , (7)
где γ i – коэффициент весомости агрегата в технико-экономическом балансе трактора, учитывающий экономику последствий ресурсного отказа агрегата;
Т остi – остаточный ресурс i-го агрегата;
Т оi – исходный ресурс нового агрегата;
При этом учитываются:
S i – балансовая стоимость i-го агрегата и затраты на его сервис;
n
S Si
-
i = 1 - суммарная стоимость агрегатов трактора и затраты на их сервис;
-
n – количество агрегатов;
q – степень восстановления ресурса агрегатов при капитальном ремонте (q = 0,6; 0,8; 1,0);
С N – степень риска потери продукции при простое трактора в полевых работах (С N = 24 – низкая, С N = 33 – средняя, С N = 44 - высокая урожайность).
Таким образом, обоснование вида ремонтных работ тракторов проводится по величине средневзвешенных показателей их изношенности R i∑ согласно графическому их соотношению на диаграмме рисунка 4:
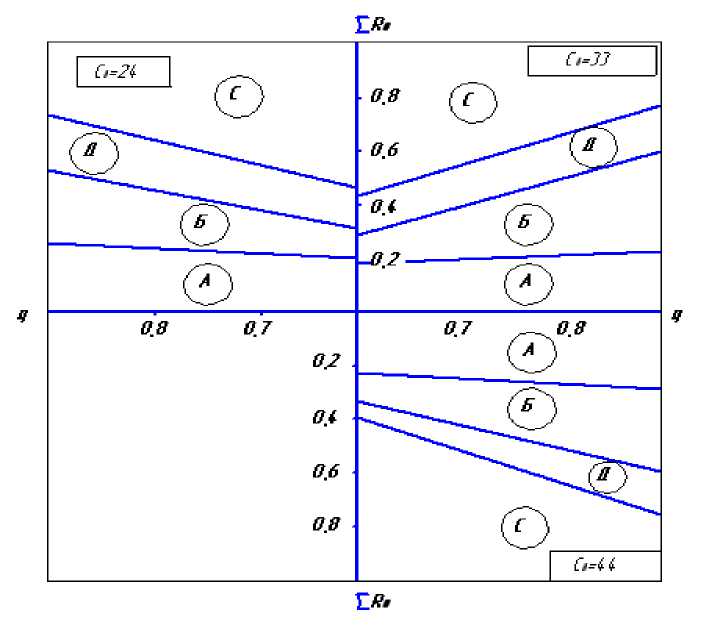
Рисунок 4 - Области допустимых и предельных значений изношенности тракторов для назначения вида ремонта их агрегатов
Если значение R i∑ принадлежит области «А» диаграммы, то наиболее эффективен полнокомплектный ремонт трактора. В остальных случаях целесообразен текущий ремонт. При этом если R i∑ соответствует области «Б» – текущий ремонт целесообразно осуществлять капитально отремонтированными агрегатами, а в области «Д» он целесообразен как капитально отремонтированными, так и новыми агрегатами. Если показатель R i∑ соответствует области «С» – текущий ремонт трактора рекомендуется осуществлять только новыми агрегатами.
Заключение
Управляющими техническим состоянием изделий машиностроения по ресурсу, сроку постановки их на ремонт являются только предельные значения диагностических параметров, обосновываемые, например, по минимуму суммарных удельных затрат на техническую эксплуатацию с учетом потерь урожая при отказе и простое техники в полевых работах. Для рядовой практики техсервиса необходимо тщательное обоснование этих предельных показателей простыми оперативными рекомендациями после их апробация практикой. Так, например, эти предельные величины предложено определять по данным традиционной бухгалтерской отчетности с.-х. предприятий из условия достижения затрат на технический сервис конкретного трактора (с учетом потерь урожая из-за его отказов в полевых работах) к стоимости его аналогичного нового или отремонтированного образца. Это проще, достовернее и конкретнее для любой машины, оборудования. А для допускаемых величин диагностических параметров достаточно примерного их технического обоснования. Но только успешная практика – законодатель подходов к обоснованию нормативов технической эксплуатации МТП по технико-экономическому или техническому критериям. Она избавит исследователей от информационного шума и ложных «новых стратегий».

Список литературы Приемы оптимизации параметров управления технической эксплуатацией МТП в АПК
- ГОСТ 28.001-83. Система технического обслуживания и ремонта техники. Основные положения. М.: Изд-во стандартов.1983.5 с.
- ГОСТ 20759-90. Дизели тепловозов. Техническое диагностирование и прогнозирование остаточного ресурса методом спектрального анализа масла. М.: Изд-во стандартов. 1991. 24 с.
- ГОСТ 20793-2009. Тракторы и машины сельскохозяйственные. Техническое обслуживание М.: Изд-во стандартов. 2011. 24 с. Примечание: Госстандарт завершает оформление современной редакции 2022 г.
- 4.Денисов В.А., Соломашкин А.А.Обеспечение безотказной работы деталей машин с использованием системы переменных допусков. Инженерные технологии и системы. 2020. Т 30. № 1. С 76-91.
- Дунаев А.В., Соловьев С.А. Исследование диагностических параметров, разработка методов и средств их контроля для совершенствования диагностирования и технического обслуживания МТП АПК. Монография. Издание ГОСНИТИ. 2014 г. 359 с.
- Игнатьев Г.С. Пpиpемонтнoe диагностирование и необезличивание составных частей агрегатов с.-х. тexники. Докторская диссертация. Челябинск. 1989.
- Комплексная система технического обслуживания и ремонта машин в сельском хозяйстве. М.: ГОСНИТИ. 1985. 144 с.
- Михлин В.М. Управление надежностью сельскохозяйственной техники. 1984. М.: Колос. 336 с.
- Рекомендации по постановке машин на ремонт по результатам диагностирования. М.: ГОСНИТИ. 1979. 37 с.
- Рабинович А.Ш., Шаровский A.A. Технико-экономические критерии и оптимизация ресурсов машин. Надежность и контроль качества. 1977. № 7. С. 24-25.
- Руководящий технический материал. Предельные и допускаемые параметры дизелей, их деталей и сопряжений. РТМ 10.16.0001.008-89. М.: ГОСНИТИ. 1989.100 с.
- Ушанов В.А. Практическое использование результатов оптимизации параметров системы ТОР для повышения эффективности эксплуатации машин. Труды КрасГАУ. Красноярск: 1995. С. 5 - 6.