Применение рентгеноструктурного анализа и шумов Баркгаузена для исследования конструкционной стали 30ХГСА после дробеударной обработки
Автор: Николаева Елена Павловна, Гридасова Елена Владимировна, Герасимов Виталий Валерьевич
Журнал: Известия Самарского научного центра Российской академии наук @izvestiya-ssc
Рубрика: Механика и машиностроение
Статья в выпуске: 2-1 т.17, 2015 года.
Бесплатный доступ
Цель работы - определение остаточных напряжений, возникающих в стали 30ХГСА после обработки дробью. При выполнении исследований использовался портативный рентгеновский дифрактометр “Xstress 3000/G3R”, анализатор шумов Баркгаузена “Rollscan 300”. Остаточные напряжения определялись методом рентгеноструктурного анализа. Показана взаимосвязь остаточных напряжений и шумов Баркгаузена.
Рентгеноструктурный анализ, шумы баркгаузена, остаточные напряжения, дробеударная обработка, сталь 30хгса
Короткий адрес: https://sciup.org/148203607
IDR: 148203607
Текст научной статьи Применение рентгеноструктурного анализа и шумов Баркгаузена для исследования конструкционной стали 30ХГСА после дробеударной обработки
Вульфа-Брегга, согласно которому:
2d • sin 0 = пЛ, где λ – длина волны; d – межплоскостное расстояние; θ – угол дифракции лучей (угол между падающим лучом и атомной плоскостью hkl), n – целое число, порядок дифракции, n=1, 2,..
Действие остаточных напряжений в поверхностном слое детали вызывает различное смещение атомных плоскостей материала (рис. 1).
Смещение атомных плоскостей приводит к тому, что периоды решетки и значения бреггов-ских углов одной и той же кристаллографической линии в разных направлениях к действующим напряжениям будут различны. Изменение параметра решетки происходит прямо пропорционально изменению величины остаточных деформаций. Напряжения, соответствующие деформациям кристаллической решетки, вычисляются из уравнений упругости изотропных, сплошных и однородных сред [5]. В отличие от механического метода [7], который позволяет оценить общую деформацию, равную сумме упругой деформации и деформации пластической, вызванной сдвигом слоев образца по отношению друг к другу, рентгеновский метод позволяет измерить только упругую деформацию, с которой непосредственно связаны напряжения, и перейти от деформаций к напряжениям [8]. Напряжения, действующие в элементарной кубической ячейке, показаны на рис. 2.
Для вычисления остаточных напряжений выбирается система отсчета, связанная с деталью (рис. 3).
Распределение остаточных напряжений, в частности напряжений сжатия, может изменяться в широких пределах для различных материалов и обладает существенными различиями в зависимости от вида обработки материала [2]. В общем случае остаточные напряжения приводят к однородному изменению межплоскостных значений
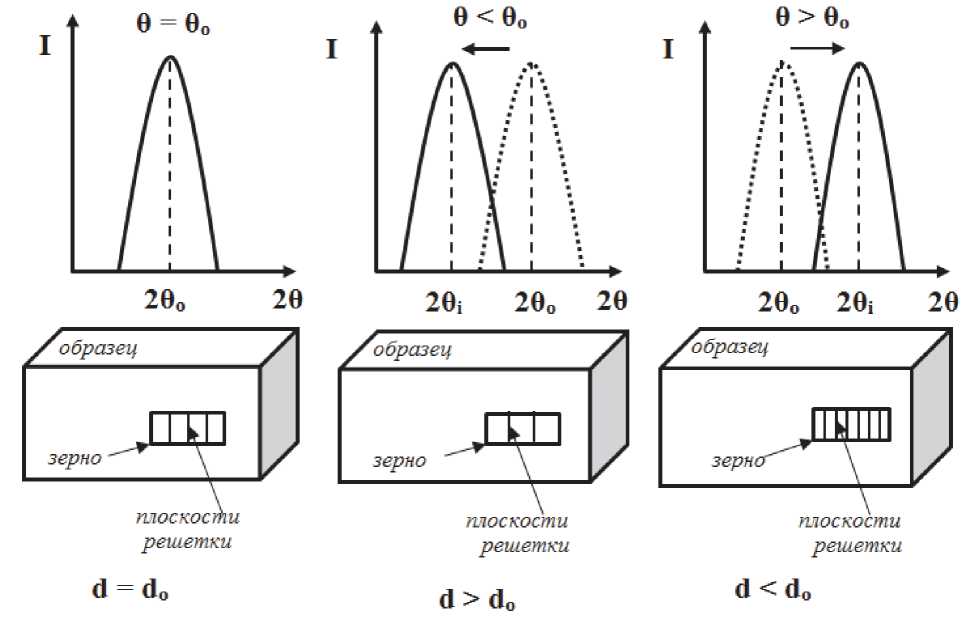
Рис. 1. Геометрия вектора рассеяния рентгеновских лучей, отвечающая закону Вульфа-Брегга
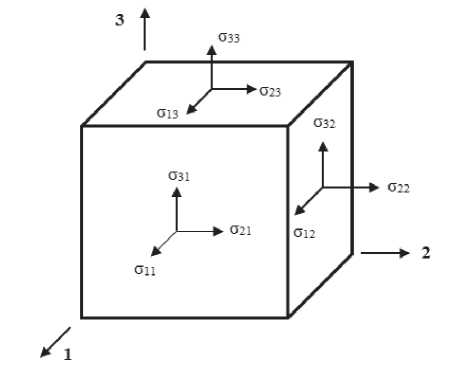
Рис. 2. Напряжения, действующие в элементарной кубической ячейке
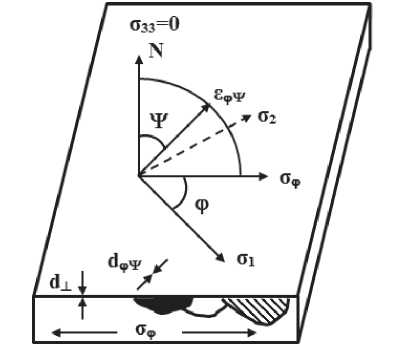
Рис. 3. Система отсчета, связанная с деталью для определения остаточных напряжений
рентгеноструктурным методом
на величину A d , и, следовательно, к смещению рентгеновской интерференционной линии на угол A9. Величина смещения интерференционной линии (A9) связана с величиной деформации кристаллической решетки (ефф) через соотношение: dg)^ ^О ^
£ ''*f do
= ~(9<р^ ~ е«) ‘ ct99^~ A9ctgeo, где d0, dфу - межплоскостные расстояния кристаллической решетки для недеформированного и деформированного материала; 90, 9фф - углы Вульфа-Брегга для недеформированного и деформированного материала; ф - азимутальный угол;
V — угол между нормалями к поверхности образца и к плоскости кристаллической решетки (hkl).
В материале необходимо выбрать кристаллическую фазу, в которой будут определяться напряжения. Для этой фазы измеряется положение или смещение дифракционной линии (hkl) в зависимости от углов ф и у . Связь между деформацией и напряжением в любом направлении ф в случае плоского напряженного состояния (а33 = 0 и т^ = 0) определяется соотношением (метод sin2i/^) [4]:
1 Z Ч
£<рдр — ^^{/iki} " ®ф " ^^ V' + $1ЦгкП " Тт^СТ), где Тг^ст) = <ти + а22 + – рентгеновские упругие постоянные, которые определяются с учетом модуля Юнга E и коэффициента Пуассона ν по формулам: 1 (1 + v) 2^2{Ш} = , V . Для измерения остаточных напряжений применялся портативный рентгеновский дифрактометр Xstress 3000 G3/G3R (Stresstech Oy, Финляндия). Прибор оснащен малогабаритной рентгеновской трубкой с полной защитой от неиспользуемого излучения и твердотельными линейными датчиками, способными преобразовывать рентгеновское излучение в электрический сигнал (рис. 4). В дифрактометре реализован χ-модифици-рованный гониометр: вместо углов ψ, и в традиционном методе sin2ψ [4], используются углы вращения χ. Все измерения остаточных напряжений проводились в режиме Modified χ (модифицированный χ), который является стандартным режимом измерений для большинства деталей. Положение гониометра в режиме Modified χ показано на рис. 5. Формула расчета остаточных напряжений на рентгеновском дифрактометре с χ-модифицированным гониометром Xstress 3000 G3/G3R имеет вид: _ E 1 1 дйфф ф 1 + v <1^=0^ cos2[3 d sln2ip D (тг±20) где P = . Режим измерения: хромовый анод, K-α излучение, напряжение на рентгеновской трубке – 25 кВ, ток – 5,5 мА. Использовались оба детектора – А и В, коллиматор – 5 мм. Угол дифракции – 156,4°. Плоскость отражения (311). Количество наклонов – 8, отклонение наклона (осцилляция) ±5º. Время экспозиции – 5 сек. Измерение на- пряжений проводилось в 3-х направлениях (ϕ): 0° (положение гониометра вдоль пластины), 45° и 90° (положение гониометра поперек пластины). Определялись нормальные и касательные напряжения, полный тензор напряжений одним из стандартных способов обсчета пиков, Peak fit, предлагаемый программным обеспечением прибора. Для упрощения расчетов напряжения σ33 не учитывались. Для автоматизированного расчета напряжений вводились параметры материала: модуль Юнга – 215000 МПа; коэффициент Пуассона – 0,3. Остаточные напряжения определялись на пластинах из стали 30ХГСА, которые предварительно подвергались закалке и отпуску на 45HRC, что примерно соответствует условному пределу текучести в 1270 МПа. После термической обработки пластины подвергались шлифованию, затем обрабатывались на дробемётной установке контактного типа УДФ-4 шариками из стали ШХ-15 диаметром 3,5 мм. Обработка осуществлялась с разной частотой вращения дробемётного колеса, ωд, об/мин. 700, 1000 и 1300, время обработки 50 секунд [1]. Степень покрытия дробью изменялась по длине пластины: от нулевой (на необработанном участке) до максимальной (0,9). Остаточные напряжения измерялись на различных участках пластин: необработанных дробью, на участках с условно называемой – промежуточной, а также с максимальной степенью покрытия дробью. На необработанных дробью участках пластин определены различные по величине сжимающие напряжения, которые составили: -10 МПа вдоль пластины; -210 МПа для угла ϕ=45o;-348 МПа для ϕ=90o. Для построения эпюр напряжений проводилось удаление поверхностных слоев стали электрохимическим способом с помощью портативного устройства Movipol-3 (Struers A/S, Дания). Использовался стандартный реактив А-2. Величина удаленного слоя определялась с помощью микромера (рис. 4): за глубину принималось среднее значение, вычисленное из пяти измерений. Рис. 4. Общий вид дифрактометра Xstress 3000 G3/G3R Рис. 5. Положение гониометра в режиме Modified χ На рис. 6 показаны эпюры напряжений, построенные для участка, обработанного дробью по максимальным режимам. Остаточные напряжения после дробеударной обработки во всех направлениях – сжимающие: от -780 до -820 МПа на поверхности в зависимости угла ф. Сжимающие напряжения достигают максимальных значений на глубине 0,2-0,3 мм и составляют от -1041 до-1044 МПа. Главные напряжения (ст1, ст 2) рассчитывались для ф =45o (рис. 7). Микротвердость измерялась на приборе HMV-2T (Shimadzu, Япония) с системой автоматического считывания отпечатков при нагрузке в 490,3 mN (HV 0,05), время выдержки под нагрузкой – 5 секунд (рис. 8). Наибольшая микротвердость определяется на глубине 0,335 мм, что соответствует уровню залегания максимальных сжимающих напряжений (см. рис. 6, 7). Влияние интенсивности дробеударной обработки на формирование поверхностных сжимающих напряжений в стали 30ХГСА показано на рис. 9 и 10: в зависимости от режима дробеударной обработки в поверхностном слое могут быть получены остаточные напряжения, достигающие 0,8 ст 2. Рис. 6. Эпюры напряжений для стали 30ХГСА: степень покрытия дробью 0,9; год = 1300 об/мин Рис. 7. Эпюры главных напряжений для стали 30ХГСА: степень покрытия дробью 0,9; год = 1300 об/мин Глубина, мм Рис. 8. Изменение микротвердости в 30ХГСА: степень покрытия дробью 0,9; ωд = 1300 об/мин Рис. 9. Влияние интенсивности дробеударной обработки на поверхностные остаточные напряжения в стали 30ХГСА: участки с промежуточной степенью покрытия Для экспресс-оценки упрочнения стали при дробеструйной обработке использовался метод шумов Баркгаузена [9]. Магнитошумовой метод основан на концепции индуктивного измерения их амплитуды шумов Баркгаузена, которые генерируются в ферромагнитной стали 30ХГСА при приложении магнитного поля. Остаточные напряжения влияют на способность доменов располагаться в направлении наиболее легкого намагничивания. В результате «магнитоупругого» взаимодействия сжимающие напряжения вызывают уменьшение амплитуды шумов Баркгаузена во многих сталях [4]. Измерения проводились с помощью цифрового анализатора шумов Баркгаузена Rollscan 300 (Stresstech Oy, Финляндия) в комплекте со специ- Рис. 10. Влияние интенсивности дробеударной обработки на поверхностные остаточные напряжения в стали 30ХГСА: степень покрытия дробью 0,9 альным программным обеспечением ViewScan. Использовался датчик, предназначенный для плоских поверхностей. Положение датчика при измерении показано на рис. 11. Параметры измерения: частота намагниченности – 175,0 Гц; напряжение намагниченности – 8,0 В. На рис. 12 и 13 показаны результаты измерения шумов Баркгаузена. Как видно из рис. 12, 13, наблюдается общая тенденция к снижению амплитуды шумов в зависимости от интенсивности обработки, что соответствует большему наклепу на обрабатываемой поверхности. В точках с максимальной степенью покрытия дробью разброс значений амплитуды шумов меньше, чем для точек, расположенных в менее упрочненной зоне. Рис. 11. Анализатор шумов Баркгаузена Rollscan 300 ВЫВОДЫ Дробеударная обработка обеспечивает равномерное распределение остаточных напряжений независимо от направления и исходного состояния материала. Для сравнения приведем результаты измерения поверхностных остаточных напряжений, полученные в том же режиме, в закаленной стали 30ХГСА после маятникового шлифования плоских деталей [10], которое создает преимущественно растягивающие поверхностные напряжения. На начальном участке шлифования растягивающие напряжения достигают 238, 366 и 495 МПа для трех направлений ф, соответственно. На всех остальных участках распределение напряжений крайне неравномерное: в зависимости от расположения анализируемой точки на поверхности шлифованного образца определяются как небольшие сжимающие, так и значительные растягивающие напряжения, МПа: -45; 176; 398. Проведенные исследования показали, что дробеударная обработка создает сжимающие напряжения на заданной глубине, что регулируется режимом обработки. Представленная в рамках данной статьи работа проводится при финансовой поддержке Правительства Российской Федерации (Минобрнауки России) по комплексному проекту 2012-218-03-120 «Автоматизация и повышение эффективности процессов изготовления и подготовки произ- Рис. 12. Зависимость максимальных значений амплитуды шумов Баркгаузена от режима обработки на участках с промежуточной степенью покрытия дробью Рис. 13. Зависимость максимальных значений амплитуды шумов Баркгаузена от режима обработки: степень покрытия дробью 0,9 водства изделий авиатехники нового поколения на базе Научно-производственной корпорации «Иркут» с научным сопровождением Иркутского государственного технического университета» согласно Постановлению Правительства Российской Федерации от 9 апреля 2010 г. № 218.
Список литературы Применение рентгеноструктурного анализа и шумов Баркгаузена для исследования конструкционной стали 30ХГСА после дробеударной обработки
- О повышении эффективности дробеметной установки контактного типа/А.Е. Пашков, В.В. Герасимов, А.А. Пашков//Вестник ИрГТУ, №10 (81), 2013. -С.46-51.
- Totten G., Howes M., Inoue T. Handbook of Residual Stress and Deformation of Steel. -USA: ASM International, Materials Park, Ohio, 2002. 500 p.
- Franco Rustichelli, Jacek J. Skrzypek. Innovative technological materials. Structural properties by neutron scattering, Synchrotron radiation and modeling. London-New York: Springer, 2010. 280 p.
- Viktor Hauk. Structural and residual stress analysis by nondestructive methods: evaluation, application, assessment. Amsterdam: Elsevier Science B.V. 1997. 640 p.
- Русаков A.A. Рентгенография металлов. М.: Атомиздат, 1977. 237 c.
- Высокопрочные коррозионно-стойкие стали аустенитно-мартенситного класса/Н.М. Вознесенская, Е.Н. Каблов, А.Ф. Петраков, А.Б. Шалькевич//Металловедение и термическая обработка металлов. 2002. № 7. С. 34-37.
- Биргер И.А. Остаточные напряжения. М.: Машгиз, 1963. 232 с.
- Краус И., Трофимов. Метод рентгеновской тензометрии в технической диагностике металлических изделий//Современное машиностроение. Наука и образование: материалы междунар. науч.-практ. конференции. СПб.: Изд-во политехн. ун-та. 2011. С. 278 -283.
- Николаева Е.П. Применение метода шумов Баркгаузена для контроля упрочнения деталей поверхностным пластическим деформированием//Известия Самарского научного центра РАН. 2013. Т.15. №6(2). С.428-431.
- Прогнозирование шероховатости поверхностей плоских деталей из закаленной стали 30ХГСА при различном задании поперечной подачи в условиях маятникого шлифования высокопористым синтеркорундом/Я.И. Солер, С.С. Небого, А.А. Доморат//Вестник ИрГТУ. 2013№7 (78). С.22-31.