Пути повышения эффективности использования древесного сырья на целлюлознобумажных комбинатах
Автор: Девятникова Людмила Анатольевна, Емельянова Елена Геннадьевна
Журнал: Ученые записки Петрозаводского государственного университета @uchzap-petrsu
Рубрика: Технические науки
Статья в выпуске: 8 (129) т.2, 2012 года.
Бесплатный доступ
Рассмотрены вопросы ресурсосбережения на стадии древесно-подготовительного цикла целлюлозно-бумажного комбината. Определены возможности снижения затрат на сырье за счет оптимального соотношения доли короткомеров в общем объеме перерабатываемых балансов на примере одного из комбинатов. Акцент сделан на рассмотрении двух звеньев наиболее распространенной в настоящее время технологии древесно-подготовительного производства целлюлозно-бумажного комбината, которыми являются окорка сырья и производство щепы из короткомерных балансов. Предложены пути снижения потерь древесины за рубительной машины.
Ресурсосбережение, длина бревен, раскрой
Короткий адрес: https://sciup.org/14750301
IDR: 14750301
Текст научной статьи Пути повышения эффективности использования древесного сырья на целлюлознобумажных комбинатах
Древесно-подготовительный цикл целлюлозно-бумажного комбината (ЦБК) представляет собой цепочку технологических звеньев, на входе которой – круглые неокоренные лесоматериалы, а на выходе – технологическая щепа. Качество технологической щепы является ключевым фактором, определяющим конкурентоспособность конечной продукции ЦБК. В свою очередь, качество щепы зависит от того, насколько совершенными являются звенья древесноподготовительного цикла и их технологическая согласованность. В современных условиях актуальным является не только повышение качества выпускаемой продукции, но и экономия ресурсов на каждой из технологических стадий производственного процесса. Технологические аспекты данной проблемы рассмотрены в статьях [5], [8], [9]. Технико-экономические аспекты той же проблемы представлены в данной статье.
Одним из направлений ресурсосбережения для российских производителей целлюлознобумажной продукции становится работа с издержками, то есть текущими затратами на сырье, эксплуатацию технологического оборудования, электроэнергию, оплату труда персонала и т. п.
Решить проблему уменьшения затрат и повышения конкурентоспособности возможно двумя основными способами: повышение качества целлюлозно-бумажной продукции и снижение затрат на уже производимую целлюлознобумажную продукцию с определенным достигнутым уровнем качества. На практике в большинстве случаев применяется первый способ,
и повышение качества целлюлозно-бумажной продукции достигается путем модернизации основного производства. Этот подход является достаточно эффективным, и на ряде предприятий целлюлозно-бумажного производства (ЦБП) процесс модернизации проходит успешно, хотя и не так быстро. Второй способ в целлюлознобумажной промышленности применяется редко. Это обусловлено тем, что в отраслях промышленности, связанных с глубокой переработкой древесины, наибольшее место в производственных затратах занимают расходы на древесное сырье с учетом транспортных расходов и затрат на топливно-энергетические ресурсы. Суммарная величина этих затрат, по проведенным расчетам, может достигать 40–45 % от общих затрат. Например, в ЦБП затраты на сырье и топливно-энергетические ресурсы (ТЭР) составляют 25,8 и 19,4 % соответственно [13], [14], [19]. Поэтому приоритетным направлением повышения эффективности работы предприятий лесопромышленного комплекса является уменьшение затрат на производство древесного сырья, транспортные расходы и ТЭР. Снижение затрат на производство сырья для ЦБП является проблемой сложной и многоплановой.
Окорка сырья является самым дорогим процессом в подготовке древесного сырья [20]. Недостатки окорки балансов в корообдирочных барабанах специалистам хорошо известны и связаны со сложностью технологии, высокой капиталоемкостью и энергоемкостью производства, трудностями утилизации коры. Кроме того, имеет место повышенный износ дорогостоящего корообдирочного оборудования. По нашим данным, на одном из ЦБК толщина стальных стенок корообдирочного барабана в течение 12 лет уменьшается с 32 до 6 мм по причине абразивного и коррозионного износа, что приводит к достаточно большим затратам на ремонт оборудования и вынужденным простоям.
На ЦБК имеется опыт очистки от коры длинномерных и короткомерных круглых лесоматериалов. Исследования [2], [6], [9], [11] показывают, что в корообдирочном барабане древесина сортиментов длиной 0,8 м и менее (так называемые ко-роткомеры) повреждается в существенно большей степени, чем древесина балансов, длина которых равна 1,2 м и более. Это объясняется тем, что древесина в примыкающих к торцам областях на отрезках, примерно равных диаметру, подвергается разрушающему воздействию сил контактного взаимодействия при очистке от коры. Наблюдаемые после окорки повреждения древесины вблизи торцов балансов приводят к появлению некондиционной щепы при дальнейшей переработке балансов в рубительной машине.
Проблемы, связанные с производством щепы из короткомерных балансов, рассмотрены в работах [4], [10]. Щепа, вырабатываемая рубитель-ной машиной, при последнем резе баланса практически всегда короче требуемой и очень часто уходит в отходы. Поэтому, чем короче длина баланса, тем больше «последних резов» при переработке сырья и тем выше потери древесины. Минимальные потери древесины могут быть достигнуты при измельчении сырья длиной, равной длине хлыста. Но размеры круглых лесоматериалов, поступающих на ЦБК, имеют различные размеры, по этой причине после раскроя на слешерной установке появляются некондиционные отрезки, длина которых меньше 0,8 м.
Негативное влияние короткомеров на изменение качественных показателей операций древесно-подготовительного цикла рассматривалось в работах [4], [5], [7], [9]. Влияние корот-комеров в общем массиве балансов на качество получаемой щепы проверено экспериментально на ЦБК. Цели, методика и результаты эксперимента представлены в статье [10]. Согласно полученным данным, наибольшее количество технологической кондиционной щепы получается из балансов длиной от 1,2 до 2,5 м. При добавлении к ним короткомеров уменьшается выход технологической щепы, при этом увеличивается выход крупной некондиционной щепы и мелких некондиционных фракций. Согласно ГОСТ 15815-83 «Щепа технологическая. Технические условия» в щепе марки Ц1 доля крупной фракции не должна превышать 3 %, но по проведенным экспериментальным исследованиям, этот показатель составил 3,3 %, то есть превышение доли крупной щепы, получаемой только с одной рубительной машины, по сравнению с допустимыми значениями составило 0,3 %. Для того чтобы достичь нормативных значений, крупная щепа должна поступать на дополнительное измельчение и возвращаться в общий поток. Так, доизмельчение крупной фракции щепы в дезинтеграторе позволяет вовлечь в технологический процесс 60 % крупной щепы [3], но при этом, соответственно, увеличиваются расходы на электроэнергию, эксплуатацию, обслуживание и износ оборудования. В рамках данной работы этот вопрос не рассматривается.
Форма и размеры частиц щепы для варки целлюлозы имеют большое значение. При малых размерах щепы улучшается пропитка и нагрев, но ухудшаются механические свойства целлюлозы как результат повреждения древесных волокон. Напротив, варка крупной щепы дает целлюлозу с высокими прочностными свойствами, но с неравномерным проваром и повышенным содержанием непровара. Выход целлюлозы из древесины зависит главным образом от степени провара целлюлозы. Чем в большей степени проварена целлюлоза, тем больше расход балансов, и наоборот [14], [15].
Согласно данным [19], потери древесины в расчете на 1 млн м3 перерабатываемых однометровых балансов по сравнению с переработкой хлыстов составляют около 40 тыс. м3 (4 %). Чтобы выразить потери древесины в денежном эквиваленте, возьмем за основу среднюю цену производителей одного кубометра круглого леса (еловой балансовой древесины) в СевероЗападном федеральном округе (на декабрь 2011 года эта цена составила 1233 руб.) [12]. Тогда получим 40 000 м3 × 1233 руб./м3 = 49 320 000 руб. на 1 млн м3 перерабатываемых однометровых балансов в виде убытков или упущенных возможностей за счет потерь древесины. В разрезе предприятий Республики Карелия ситуация в отрасли определяется практически целиком двумя мощными ЦБК в Кондопоге и Сегеже. Каждое предприятие рассчитано на переработку приблизительно 2,5 млн м3 древесины в год [16]. Сделав несложные расчеты, определим упущенные возможности каждого из этих предприятий: 49,32 × 2,5 = 123,3 млн руб. в год. В этих расчетах принято, что переработке подлежат только еловые балансы длиной 1 м (± 0,2 м). Но в реальных производственных условиях ЦБК, где наряду с однометровыми балансами присутствует доля короткомеров в общем потоке балансов, поступающих на рубительную машину, потери древесины, как указано выше, будут еще больше.
Рассмотрим пример Кондопожского ЦБК, на базе которого проводились экспериментальные исследования [5], [10]. При производстве щепы использовалось сырье, состоящее из однометровых балансов и короткомеров. По наблюдениям, длина короткомеров составляет от 0,10 до 0,80 м.
Для расчетов примем среднюю длину коротко-мера - 0,45 м, то есть примерно половина однометрового баланса. Логично предположить, что и потери древесины увеличатся вдвое и составят 80 тыс. м3 в расчете на 1 млн м3 перерабатываемых балансов. По данным эксперимента, доля короткомеров в общем массиве перерабатываемых на щепу балансов варьировалась от 38 до 68 % [5].
Если доля короткомеров 38 %, то доля балансов составит 62 % и потери древесины: 0,38 х 80 тыс. м3 + 0,62 х 40 тыс. м3 = 55 тыс. м3 на 1 млн м3 перерабатываемых балансов.
Если доля короткомеров 68 %, то доля балансов будет равна 32 % и потери древесины составят: 0,68 х 80 тыс. м3 + 0,32 х 40 тыс. м3 = 67,2 тыс м3 на 1 млн м3 перерабатываемых балансов.
Чтобы представить объемы потерь древесины в рамках отдельного комбината, необходимо обратиться к производственным данным. Комбинат в 2010 году произвел 113,6 тыс. т целлюлозы по варке [17], следовательно, получим ориентировочно 568 тыс. м3 древесины, перерабатываемой на щепу, учитывая, что фактический расход древесины в зависимости от ее породы и качества составляет 4,5-5,0 пл. м3/т целлюлозы [15]. При таком объеме производства потери древесины составят:
-
• для доли короткомеров 38 %: 55 х 0,568 = 31,24 тыс. м3;
-
• для доли короткомеров 68 %: 67,2 х 0,568 = 38,17 тыс. м3.
С учетом объема производства (568 тыс. м3 древесины, перерабатываемой на щепу в год) и средней цены производителей одного кубометра круглого леса (еловой балансовой древесины) в Северо-Западном федеральном округе 1233 руб., убытки или упущенные возможности составят:
-
• при доле короткомеров 38 %: 1233 руб. х 31,24 тыс. м3 = 38 млн 519 тыс. руб. в год;
-
• при доле короткомеров 68 %: 1233 руб. х 38,17 тыс. м3 = 47 млн 64 тыс. руб. в год.
Таким образом, уменьшив долю короткомеров в массиве балансов с 68 до 38 %, получим не только щепу лучшего качества, но и сокращение потерь древесины в 38,17/31,24 = 1,2 раза и сокращение убытков с 47,064 до 38,519 млн руб. в год. Это ожидаемый экономический эффект.
Данные потери можно уменьшить за счет оптимизации процесса подготовки сырья для рубительной машины. Такая оптимизационная работа уже осуществляется на ЦБК на стадии транспортировки пиленой древесины в корообдирочный барабан. Для отбраковки короткомеров предусмотрены провалочные окна на рольгангах. Однако, по нашим наблюдениям процесса транспортировки балансов на одном из ЦБК, часть короткомеров не проваливается в эти окна и поступает на дальнейшую обработку в корообдирочный барабан (см. рисунок). Эти данные указывают на необходимость модернизации секций рольганга.
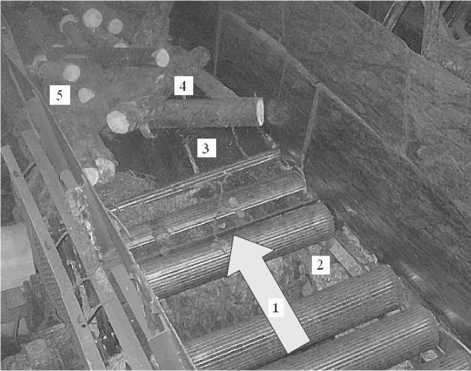
Участок рольганга с провалочным окном для удаления короткомеров: 1 - направление движения сырья к корообдирочному барабану; 2 - провалочное окно для удаления короткомеров; 3 - ленточный конвейер; 4 -балансы стандартной длины; 5 - неудаленный короткомер
В качестве модернизации на стадии транспортировки можно предусмотреть изменение конструкции роликов конвейера с целью создания циклически повторяющихся вертикальных перемещений транспортируемых лесоматериалов. Это предположительно даст технический эффект, выражающийся в повышении эффективности автоматической сортировки по длине перемещаемых с помощью рольганга лесоматериалов, то есть в более качественной отбраковке короткомеров для предотвращения их попадания на дальнейшую обработку. Техническая реализация такой модернизации рольганга вполне осуществима и не требует больших затрат [18]. Описанная модернизация наиболее целесообразна и менее затратна именно на этой стадии, до загрузки в корообдирочный барабан, что способствует не только повышению экономической эффективности производства, но и отвечает современным экологическим требованиям.
ВЫВОДЫ
-
1. При существующей технологии подготовки древесины уменьшение доли короткомеров в массиве балансов с 68 до 38 % позволит сократить потери древесины в 1,2 раза. При этом отбракованные после стадии раскроя коротко-меры могли бы быть использованы, например, в качестве топлива, в производстве строительных конструкций, в элементах параметрической архитектуры.
-
2. На одном из ЦБК с годовым выпуском 113,6 тыс. т целлюлозы по варке, уменьшив долю короткомеров в общем массиве балансов с 68 до 38 %, можно получить не только щепу лучшего качества, но и сокращение убытков по потерям древесины с 47,064 до 38,519 млн руб. в год.
-
3. Доля короткомеров может быть уменьшена на стадии транспортировки балансов за счет совершенствования конструкции провалочных окон на рольгангах.
-
4. Переработку продуктов раскряжевки целесообразно вести раздельно, используя специальное оборудование для производства щепы из короткомеров.
* Работа выполнена при поддержке Программы стратегического развития (ПСР) ПетрГУ в рамках реализации комплекса мероприятий по развитию научно-исследовательской деятельности на 2012–2016 гг.
Список литературы Пути повышения эффективности использования древесного сырья на целлюлознобумажных комбинатах
- Бойков С. П. Теория процессов очистки древесины от коры. Л.: ЛГУ, 1980. 152 с.
- Вальщиков Н. М., Лицман Э. П. Рубительные машины. М.: Лесн. пром-сть, 1980. 96 с.
- Васильев С. Б. Комплексные исследования процесса производства щепы//Труды лесоинженерного факультета ПетрГУ. Петрозаводск: Изд-во ПетрГУ, 2003. С. 13-15.
- Васильев С. Б., Вдовин А. А., Гусев А. В. Обоснование рациональных режимов переработки отходов раскряжевки и крупной фракции щепы//Научно-методическое обеспечение лесного комплекса Карелии: Тез. докл. науч.-практ. конф. докторантов и аспирантов лесоинженерного факультета ПетрГУ. Петрозаводск: Изд-во ПетрГУ, 1999. С. 16-17.
- Васильев С. Б., Девятникова Л. А., Колесников Г. Н. Влияние технологии раскроя балансовой древесины на фракционный состав щепы//Известия СПбЛТА. 2011. Вып. 195. С. 125-133.
- Васильев А. С., Никонова Ю. В., Раковская М. И. Математическое моделирование технологического процесса очистки древесины в корообдирочном барабане//Ученые записки Петрозаводского государственного университета. Сер. «Естественные и технические науки». 2008. № 1. С. 117-119.
- Газизов А. М., Шапиро В. Я., Григорьев И. В. Влияние влажности на развитие процесса разрушения коры при роторной окорке//Вестник Московского государственного университета леса -Лесной вестник. 2008. № 6. С. 129-133.
- Герасимов Ю. Ю., Селиверстов А. А., Суханов Ю. В., Сюнёв В. С. Основные факторы планирования производства древесного топлива из древесной биомассы//Ученые записки Петрозаводского государственного университета. Сер.: «Естественные и технические науки». 2011. № 8 (121). С. 77-80.
- Девятникова Л.А. Комплекс задач по совершенствованию технологии и оборудования древесно-подготовительного цикла для производства целлюлозы//Леса России в XXI веке: Материалы 5-й Междунар. науч.-практ. интернет-конф. СПб.: СПбЛТА, 2010. С. 151-158.
- Девятникова Л. А., Васильев С. Б., Колесников Г. Н. Влияние технологии раскроя балансов на фракционный состав щепы//Вестник МГУЛ -Лесной вестник. 2012. № 3. С. 120-124.
- Девятникова Л. А., Никонова Ю. В. О совершенствовании технологии очистки круглых лесоматериалов от коры и их переработки на щепу//Материалы четвертой международной научно-практической Интернет-конференции «Леса России в XXI веке». СПб.: ЛТА, 2010. С. 111-114.
- Ежемесячный ценовой обзор « Круглый лес». 2012. Вып. № 37 (46) [Электронный ресурс]. Режим доступа: www.lesprom.com
- ЗАО «ЭКСПО-Трейд» Технологическая щепа высокого качества с минимальными затратами? Гарантируем!//Журнал «ЛесПромИнформ». 2009. № 4 (62). С. 74-76 [Электронный ресурс]. Режим доступа: http://lesprominform.ru/jarchive/articles/itemshow/694
- Иванов К. А. Влияние качества щепы на величину и вариацию характеристик сульфатной целлюлозы: Автореф. дис.. канд. техн. наук. Архангельск, 2009. 141 с.
- Комплексная химическая переработка древесины: Учебник для вузов/И. Н. Ковернинский, В. И. Комаров, С. И. Третьяков, Н. И. Богданович, О. М. Соколов, Н. А. Кутакова, Л. И. Селянина; Под ред. И. Н. Ковернинского. Архангельск: Изд-во Архангельского гос. техн. ун-та, 2002. 347 с.
- Кузьминов И. Ф. Республика Карелия: современное состояние и перспективы развития лесопромышленного комплекса, 2011 [Электронный ресурс]. Режим доступа: http://www.wood.ru/ru/loa767.html
- Официальный сайт ОАО «Кондопога» [Электронный ресурс]. Режим доступа: http://www.oaokondopoga.ru/index.html
- Патент на полезную модель 117411 РФ, МПК B65G 13/11. Секция рольганга для сортировки транспортируемых лесоматериалов по длине. Колесников Г. Н., Васильев С. Б., Девятникова Л. А., Доспехова Н. А.
- Суханов В. С. О повышении эффективности работы ЦБК за счет снижения затрат на производство сырья//Журнал «ЛесПромИнформ». 2005. № 3 (25).
- Шапиро В. Я., Григорьев И. В., Гулько А. Е. Анализ методов расчета параметров и обоснование математической модели разрушения коры при групповой окорке древесины//Ученые записки Петрозаводского государственного университета. Сер. «Естественные и технические науки». 2011. № 8 (121). С. 92-96.