Разработка методов контроля момента возникновения автоколебаний стана холодной прокатки
Автор: Вишняков С.Г., Третьяков Д.А., Васильева С.В., Иванов А.И., Васильев В.А., Рубанов Д.В.
Рубрика: Контроль и испытания
Статья в выпуске: 1 т.24, 2024 года.
Бесплатный доступ
На стане холодной прокатки автоколебания возникают при ручном увеличении скорости прокатки тонкой полосы. Толщина подката при этом, как правило, не более 2-2,5 мм. Спектр колебаний достаточно широк. Первая гармоника - 120 Гц. При контроле вибрационных и технологических параметров выявлена жесткая связь вибрации элементов клетей стана с виброперемещением гидравлического натяжного устройства (ГНУ) рабочих валков и колебаниями уровня натяжения прокатываемой полосы. Штатный контроль перемещения ГНУ проводит 200 измерений в секунду. В соответствии с теоремой Котельникова полоса частот спектральной характеристики в этом случае - 100 Гц. Колебания уровня натяжения прокатываемой полосы позволяют контролировать полосу частот в диапазоне от 0 до 43 Гц, не более. Этого явно не достаточно для надежного контроля момента возникновения автоколебаний. Существующая система контроля технологических параметров имеет внутренний ресурс по частоте опроса при формировании базы данных. Программными средствами удалось увеличить частоту опроса виброперемещений ГНУ до 1000 измерений в секунду. При этом полоса частот спектральной характеристики охватывает диапазон от 0 до 500 Гц. Это позволяет контролировать не только первую гармонику 120 Гц, но и высшие гармоники до 400-500 Гц. Колебания уровня натяжения прокатываемой полосы после перевода на более быстрый ресурс контроллера позволили увеличить частоту опроса до 250 измерений в секунду. Таким образом, по этому каналу также можно надежно контролировать первую гармонику возникающих автоколебаний. Анализ процесса возникновения автоколебаний показал, что причина автоколебаний клетей стана - самопроизвольное колебание уровня натяжения прокатываемой полосы при ручном увеличении линейной скорости прокатки. Колебания клетей стана запаздывают относительно колебаний уровня натяжения от 2 до 3 секунд. Используя алгоритмы дискретного преобразования Фурье и преобразование Фурье на коротком временном интервале (STFT), можно надежно и своевременно распознавать момент возникновения автоколебаний.
Стан холодной прокатки, автоколебания, быстрое преобразование фурье, преобразование фурье на коротком временном интервале
Короткий адрес: https://sciup.org/147243220
IDR: 147243220 | DOI: 10.14529/engin240104
Текст научной статьи Разработка методов контроля момента возникновения автоколебаний стана холодной прокатки
Автоколебания стана холодной прокатки – реально существующее явление, для борьбы с которым разрабатываются и внедряются различные контрольные и диагностические системы. В соответствии со стандартом ГОСТ ИСО 2041 [1] автоколебания – это «вибрация механической системы, вызванная преобразованием энергии в колебательные движения внутри системы». Но в различных областях автоколебания имеют свои собственные названия. В авиации колебания самолета в пространстве как единое целое – это бафтинг, автоколебания крыла самолета при срыве потока – флаттер, автоколебания шасси – шимми. Шимми – это и автоколебания колеса обычной тележки в магазине самообслуживания. В металлорежущих станках автоколебания называют чаттером. В прокатном производстве чаттер – это автоколебания стана, как правило, холодной прокатки [2–6].
Процесс автоколебаний стана холодной прокатки изучен достаточно подробно. Причиной появления колебаний могут быть крутильные колебания [7], продольные колебания прокатываемой полосы. Особенно опасны автоколебания тонких полос на станах холодной прокатки [8]. Результаты исследований автоколебаний станов тандема приведены в работах [9].
Обзор систем контроля и диагностики технического состояния и оценки остаточного ресурса станов холодной прокатки приведен в работе [10, 11]. Тенденции развития систем контроля и предупреждения возникновения автоколебаний (чаттера) и методы автоматического регулирования скорости прокатки в зависимости от уровня вибрации приведены в работе [12].
Контроль вибросостояния проводится либо по общему уровню вибрации (виброскорости), либо по спектральному составу виброускорений. Спектральную характеристику реализации виброускорения можно получить, используя дискретное преобразование Фурье (ДПФ) [13] либо используя быстрое преобразование Фурье (БПФ). Реальная возможность анализа прямого спектра вибрации появилась только после публикации алгоритма БПФ [14].
Процесс возникновения автоколебаний носит взрывной характер. С момента зарождения до развитого состояния автоколебательного процесса стана холодной прокатки проходит всего несколько секунд. Сбор данных и обработка вибропараметров с использованием алгоритма быстрого преобразования Фурье также требуют значительного времени относительно времени зарождения автоколебаний. Необходимо не менее 1 секунды на получение спектральной характеристики. Для анализа вибросостояния и построения моделей БПФ является эффективным инструментом, но для предупреждения момента возникновения автоколебаний использовано быть не может.
Одним из методов, с помощью которых можно контролировать момент возникновения автоколебаний, может быть преобразование Фурье на коротком временном интервале (Short-time Fourier transform). Метод STFT позволяет существенно сократить время преобразования и с достаточной точностью определить момент возникновения автоколебаний [15, 16]. Кроме того, с этой целью можно использовать и вейвлет-преобразования [17]. Пример использования вейвлет-преобразования в диагностике технического состояния стана холодной прокатки приведен в работе [18].
Управление работой непрерывного травильного агрегата, совмещенного с 5-клетевым станом, осуществляется автоматизированной системой АСУ ТП. Непосредственно из контроллеров АСУ ТП формируется база данных технологических параметров системы контроля и диагностики технического состояния (поставка фирмы «IBA»). Общее количество параметров порядка – 4000 каналов, 2000 параметров травильного агрегата и более 2000 технологических параметров прокатного стана. Анализ данных производится программным модулем IbaAnalyzer. Запись данных производится в 5-минутные (стан) или 10-минутные (травильный агрегат) проприетарные файлы с расширением.dat. Сжатие данных производится методом кодирования длин серий (RunLength Encoding). Используя этот метод, заменяют серию из двух или более одинаковых символов числом, обозначающим длину серии, за которым идёт сам символ. Максимальное число повторений – 255.
Используя такой алгоритм сжатия, не всегда удается эффективно сжать данные. Даже на стационарных каналах при условии, что погрешность канала приводит к изменению измеряемого технологического параметра с очень малым уровнем сигнала (электронный шум канала), запись будет проводиться каждые 5 миллисекунд.
В качестве примера приведем запись линейной скорости прокатки и перемещения плит CVC клети № 5 стана 2000 (рис. 1). Минимальные изменения перемещений – на уровне 10 мкм, амплитуда изменений линейной скорости прокатки – 0,0125 м/с. В качестве шкалы измерения линейной скорости можно принять скорость нормальной прокатки 25 м/с, Максимальные перемещения плиты CVC равны 100 мм. Изменения происходят в диапазоне от +10 до –10 мкм. При дальнейшем увеличении видно, что запись производится каждые 5 миллисекунд. Такая плотная запись объясняется коротким циклом процесса прокатки и необходимостью контролировать появления неустойчивости параметров, например натяжения или момента в клетях стана. Подроб- ная запись сигналов приводит к очень большому объему данных. Размер одного 5-минутного файла данных стана – от 50 до 75 МБт. За сутки только по стану набирается более 21 ГБт данных. За месяц – 650 ГБт. Большой объем данных не позволяет сохранять данные более 2 недель.
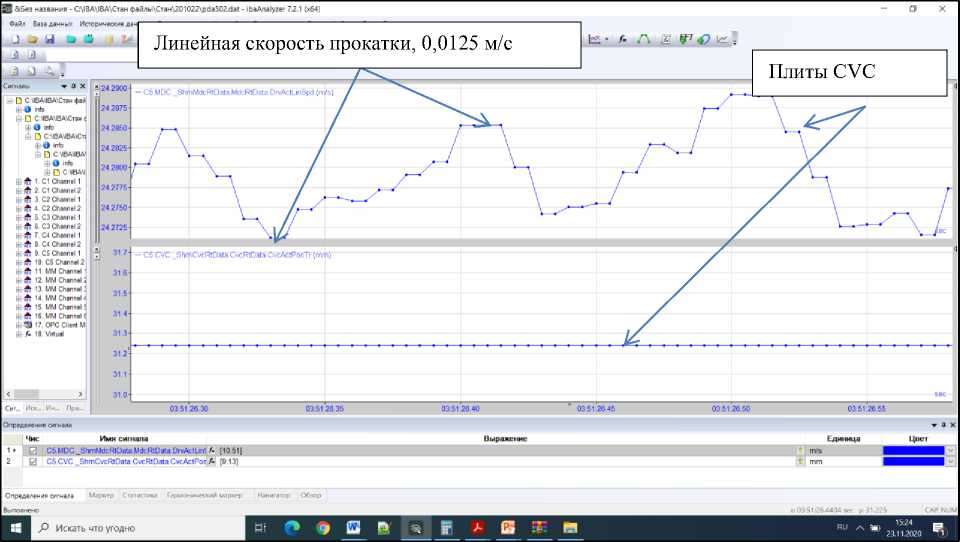
Рис. 1. Запись данных скорости прокатки и перемещения плиты CVC, происходящая каждые 5 миллисекунд Fig. 1. Data recording of the rolling speed and movement of the CVC plate occuring every 5 milliseconds
Промышленный эксперимент
Автоколебания стана холодной прокатки происходят, как правило, при работе в ручном режиме при выходе на нормальную скорость прокатки. Колебания виброускорений в поперечном, вертикальном и осевом направлениях приведены на рис. 2. Колебания релаксационные, разрывные. Спектры частот в автоколебательном режиме приведены на рис. 3. Частота первой гармоники равна 120 Гц, есть вторая, третья, четвертая – до 600 Гц.
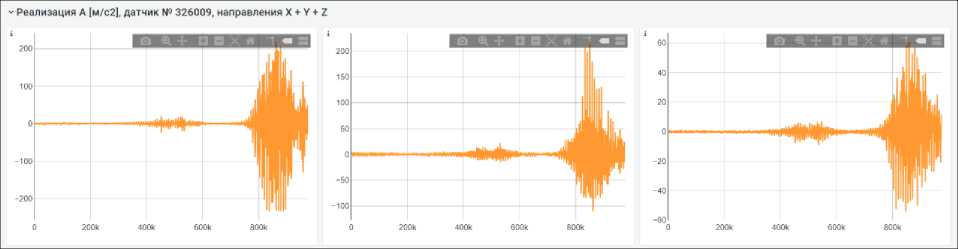
Рис. 2. Временная форма колебаний Fig. 2. The time form of oscillations
Измерение перемещения гидравлического натяжного устройства производится прямым измерением и практически ограничивается только быстродействием контроллера. Измерение натяжения полосы на 5-клетевом стане тандем производится опосредованно с помощью тензометрических датчиков (месдоз) типа PFCL201CE-50кН [19] (рис. 4).
Датчики располагаются под подшипниками роликов и измеряют вертикальную составляющую усилия Fr, действующую со стороны полосы на измерительный ролик (рис. 5).
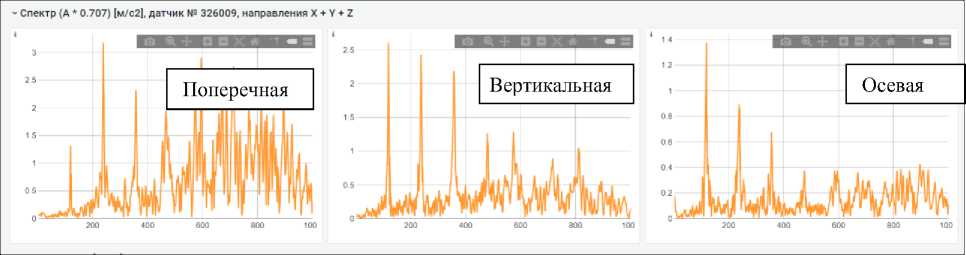
Рис. 3. Спектр виброускорений.
Fig. 3. Vibration acceleration spectrum.
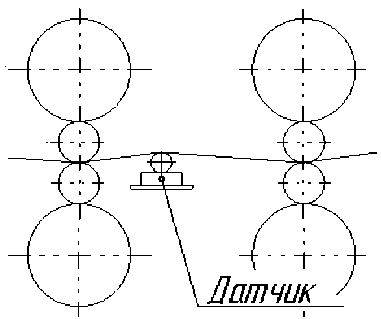
Рис. 4. Расположение датчика
Fig. 4. Sensor location
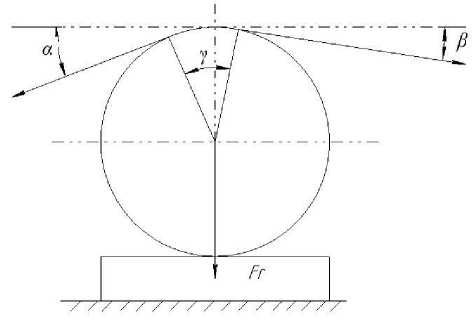
Рис. 5. Угол охвата ролика полосой
Fig. 5. The angle of coverage of the roller strip
Углы охвата постоянны для каждого измерительного ролика и учитываются при калибровке вторичного прибора измерительной системы. Натяжение рассчитывается по формуле
т= ∗ Wrap gain; i i
Wrap gain= =.
sin α+sin β sin у
Принцип действия датчика основан на изменении магнитных свойств некоторых видов сталей под механическим воздействием. Датчик состоит из собственно тела – сердечника и двух обмоток, расположенных перпендикулярно друг к другу (рис. 6). На первичную обмотку подается переменный ток, который создает магнитное поле. Когда на датчик начинает действовать механическая сила, поле частично формирует индуктивную связь со второй обмоткой, формируя в ней переменный ток, напряжение которого соответствует натяжению полосы.
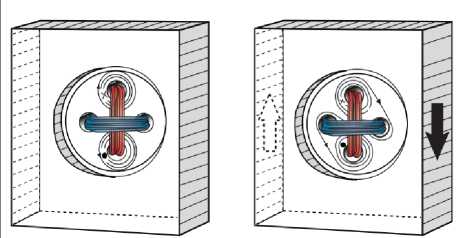
Рис. 6. Распространение магнитного поля вокруг вторичной обмотки при механическом воздействии на датчик
Fig. 6. Propagation of the magnetic field around the secondary winding during mechanical action on the sensor
Параметры натяжения штатно собираются со скоростью 12 миллисекунд на одно измерение, т. е. 83 измерения в секунду. Частота Найквиста при этом равна 41,5 Гц в соответствии с теоремой Котельникова [19–23].
Штатный контроль перемещений гидравлического натяжного устройства и натяжение прокатываемой полосы не соответствуют спектру частот процесса автоколебаний стана. Для надежного контроля и своевременного предупреждения оператора о возможном возникновении автоколебаний необходимо увеличить частотный диапазон каналов измерения технологических параметров.
Увеличение полосы частот перемещения (колебаний) гидравлического натяжного устройства проводится с использованием программных средств системы контроля. В диспетчере ввода-вывода изменен параметр «опорное время записи» с 5 на 1 мс (рис. 7). Кроме того, было изменено время обновления каналов считывания перемещения гидравлического нажимного устройства с 5 на 1 мс и изменено «время обновления» 16-го канала, корзины контроллера MillMaster (рис. 8).
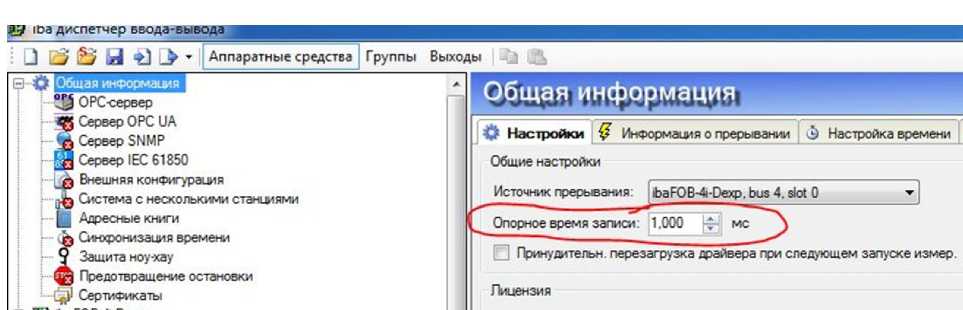
Рис. 7. Диспетчер ввода-вывода фирма IBA Fig. 7. Input/output manager company “IBA”
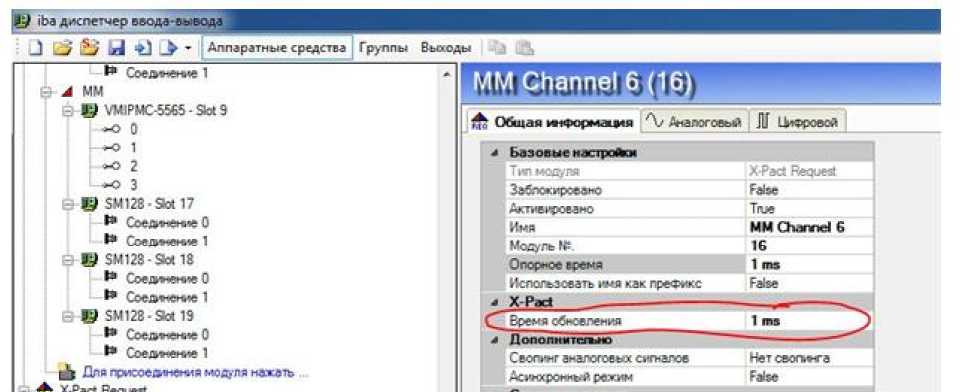
Рис. 8. Корзина контроллера MillMaster Fig. 8. MillMaster controller basket
Для каналов прямого измерения этих изменений достаточно для увеличения скорости обновления данных. Время обновления аналогового сигнала определяется временем (обновления данных) скана ресурса, который читает этот сигнал с периферии. Поэтому штатный, медленный ресурс, которым обрабатываются все каналы натяжения, SCM (Speed Control Master), скан которого 12 мс должен быть заменен на быстрый ресурс этого контроллера DSH (Drum Shear Handling) с временем скана 4 мс.
До 12 июля время записи – 5 мс. После 12 июля изменены параметры «опорное время» в диспетчере ввода-вывода. В настоящее время записи – 1 мс. Обозначение параметров гидравлического нажимного устройства в базе данных не изменилось.
Обозначение натяжения при обработке в ресурсе SCM (Speed Control Master) до 12 июля 2023 года после второй клети со стороны привода – MM.SCM.AiMmItenC2XsTenActDs, после третьей клети со стороны привода – MM.SCM.AiMmItenC3XsTenActOs, после пятой клети со стороны оператора – MМ.SCM.AiMmItenC5XsTenActOs.
-
12 июля 2023 года заменен ресурс контроллера натяжения SCM (Speed Control Master) на ресурс контроллера DSH (Drum Shear Handling). Обновление данных – 4 мс. Обозначение натяжения при обработке в ресурсе контроллера DSH (Drum Shear Handling): после второй клети со стороны привода – MM.DSH.AiMmItenC2XsTenActDs(23), после третьей клети со стороны привода – MM.DSH.AiMmItenC3XsTenActDs(34), после пятой клети со стороны оператора – MМ.DSH.AiMmItenC5XsTenActOs [kN].
При проведении промышленного эксперимента для построения модели оценки технического состояния необходимо совместно использовать как технологические параметры, так и вибрационные параметры. Гибридная база данных, объединяющая технологические параметры стана холодной прокатки (фирма IBA), технологические параметры травильного агрегата (фирма IBA) и вибрационные параметры элементов клетей стана (фирма СИГМА), позволяет связать процесс возникновения автоколебаний и параметры работы стана.
При контроле вибрационных и технологических параметров выявлена жесткая связь вибрации элементов клетей стана с виброперемещением гидравлического натяжного устройства (ГНУ) рабочих валков и колебаниями уровня натяжения прокатываемой полосы. Анализ процесса возникновения автоколебаний показал, что причина автоколебаний клетей стана – самопроизвольное колебание уровня натяжения прокатываемой полосы при ручном увеличении линейной скорости прокатки. Колебания клетей стана запаздывают относительно колебаний уровня натяжения от 2 до 3 секунд. Используя алгоритмы дискретного преобразования Фурье и преобразование Фурье на коротком временном интервале (STFT), можно надежно и своевременно распознавать момент возникновения автоколебаний.
На рис. 9 приведена зависимость линейной скорости прокатки от времени в момент возникновения автоколебаний и аварийном выключении стана: 21 час, 41 минута, 1 секунда. Значение центрирования зазора валков (виброперемещение) гидравлического нажимного устройства (ГНУ) на стороне оператора приведено на рис. 10. После дополнительной настройки и изменения параметра «опорное время» в диспетчере ввода-вывода опорное время записи равно 1 мс. Колебания рабочих валков начинаются практически одновременно с подачей сигнала АСУ ТП на останов стана. Прекращаются колебания примерно через 3 секунды на скорости прокатки порядка 10 м/с.
Натяжение прокатываемой полосы после второй клети со стороны привода – MM.DSH.AiMmItenC2XsTenActDs – во время автоколебаний приведено на рис. 11. Момент останова стана запаздывает примерно на полсекунды относительно начала заметных колебаний уровня натяжения после 2-й клети. Колебания уровня натяжения продолжается всего 2 секунды. Длительность колебаний ГНУ примерно на 2 секунды больше. Вероятнее всего колебание уровня натяжения полосы после 2-й клети не может быть причиной возникновения автоколебаний клетей стана.
Натяжение прокатываемой полосы после третьей клети со стороны привода – MM.DSH.AiMmItenC3XsTenActDs(34) в режиме автоколебаний приведено на рис. 12. Обработка в ресурсе контроллера DSH (Drum Shear Handling) после 12 июля 2023 года – обновление данных 4 мс. Существенное изменение (виброперемещения) уровня натяжения заметно уже за 3–3,5 секунды. На рис. 13 выделена временная зона перед остановом стана, в которой существует развитое колебательное движение натяжения прокатываемой полосы. Аналитический сигнал изменения уровня можно представить в виде модулированного сигнала с несущей частотой первой гармоники 120 Гц, модулированной колебательным процессом с низкой частотой.
Натяжение прокатываемой полосы за пятой клетью MМ.DSH.AiMmItenC5XsTenActOs приведено на рис. 14. До останова стана уровень натяжения полосы не совершает колебаний. Низкочастотные колебания возникают уже после останова стана. Частота колебаний – примерно 1 Гц. Амплитуда колебаний – до 30 кН.
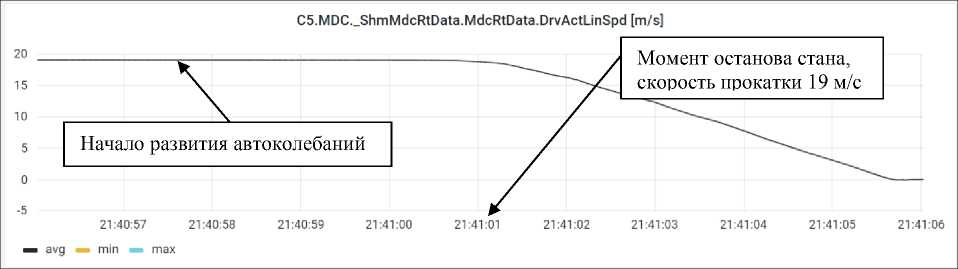
Рис. 9. Зависимость скорости прокатки от времени при аварийном останове Fig. 9. Dependence of rolling speed on time during emergency stop
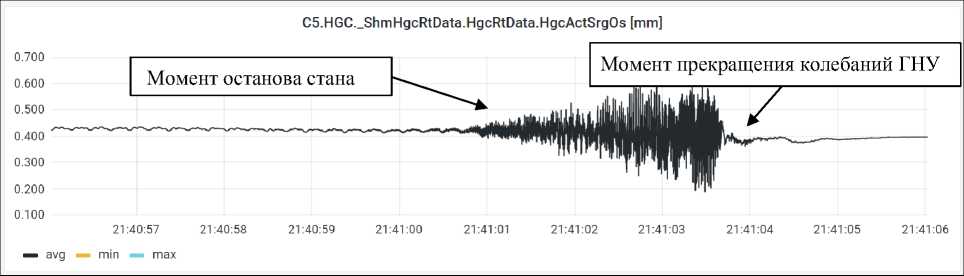
Рис. 10. Виброперемещение ГНУ при аварийном останове
Fig. 10. Vibration displacement of wildebeest during emergency stop
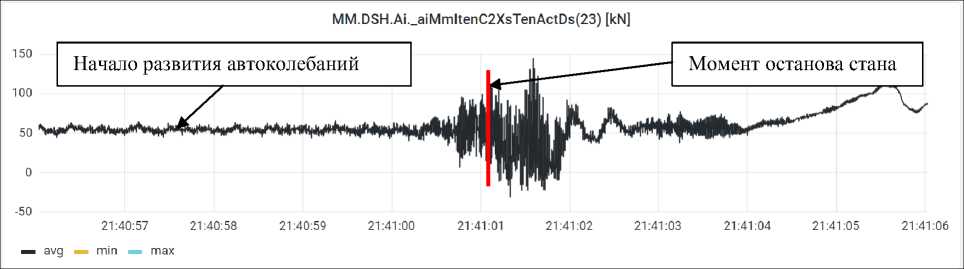
Рис. 11. Натяжение прокатываемой полосы между второй и третьей клетью Fig. 11. Tension of the rolled strip between 2 and 3 cages
Выводы
-
1. Анализ процесса возникновения автоколебаний показал, что причина автоколебаний клетей стана – самопроизвольное колебание уровня натяжения прокатываемой полосы при ручном увеличении линейной скорости прокатки. Колебания клетей стана запаздывают относительно колебаний уровня натяжения от 2 до 3 секунд. Используя алгоритмы дискретного преобразования Фурье или преобразование Фурье на коротком временном интервале (STFT), можно надежно и своевременно распознавать момент возникновения автоколебаний.
-
2. Колебание уровня натяжения полосы возникает в разное время на разных клетях стана. Для надежного контроля момента возникновения автоколебаний вероятнее всего потребуется контроль за поведением натяжения полосы на всех клетях стана.
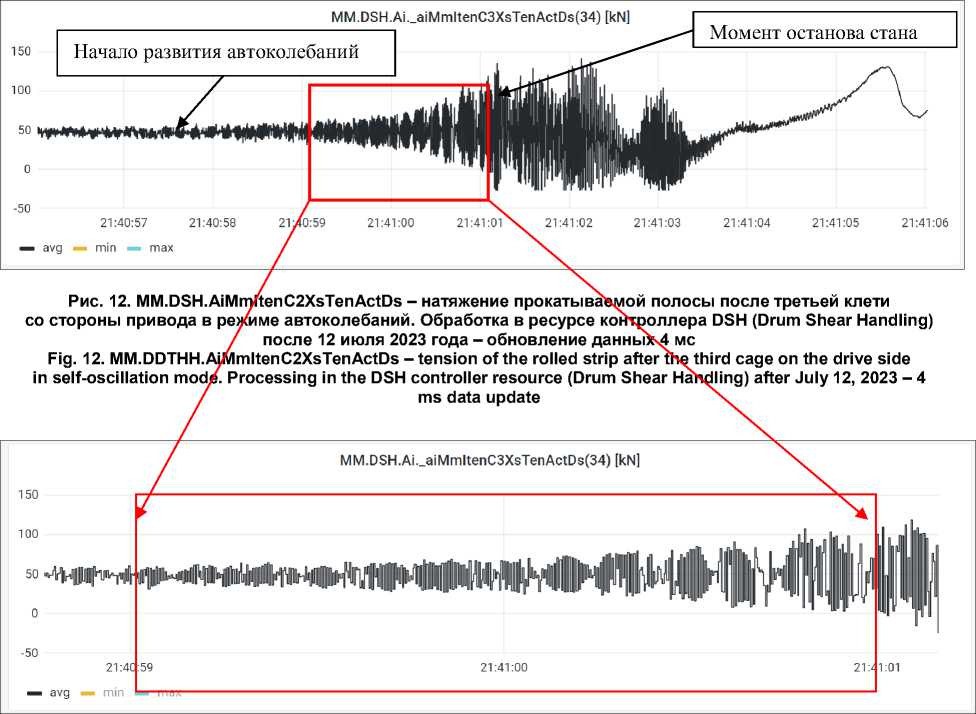
Рис. 13. Натяжение прокатываемой полосы после второй клети со стороны привода в режиме автоколебаний.
ЗОМ – 2 секунды. Обновление данных – 4 мс
Fig. 13. Tension of the rolled strip after the second stand on the drive side in self-oscillation mode.
The ZOOM is 2 seconds. Data update – 4 ms
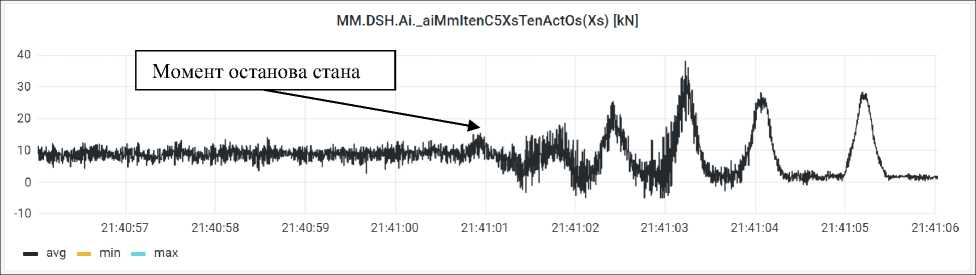
Рис. 14. Натяжение прокатываемой полосы за пятой клетью Fig. 14. Tension of the rolled strip behind the fifth cage
Список литературы Разработка методов контроля момента возникновения автоколебаний стана холодной прокатки
- ГОСТ Р ИСО 2041-2012 Вибрация, удар и контроль технического состояния. Термины и определения. Дата введения 2013-12-01.
- Эльясберг М.Е. Автоколебания металлорежущих станков. Теория и практика. СПб.: Особое КБ станкостроения, 1993. 180 с.
- Characteristic recognition of chatter mark vibration in a rolling mill based on non-dimensional parameters of the vibration signal / Shao Yimin, De Xiao, Yuan Yilin, K. Mechefske Chris, Chen // Journal of Mechanical Science and Technology. 2014. Vol. 28(6). P. 2075–2080. DOI: 10.1007/s12206-014-0106-6
- Asit K.C., Vinay S.G., Rahul K.V. A Review on Chatter Analysis in Cold Rolling process // JOJ Material Sci. 2017; 2(1): 555578. DOI: 10.19080/JOJMS.2017.02.555578
- Zhao H., Ehmann K.F. Stability analysis of Сhatter in tandem rolling mills-part 1: single- and multi-stand negative damping effect // J Manuf Sci Eng. 2013. Vol. 135(3). P. 031001–031001. DOI: 10.1115/1.4024032
- Chatter detection using principal component analysis in cold rolling mill / N.I. Usmani, S. Ku-mar, S. Velisatti, P.K. Tiwari, S.K. Mishra, U.S. Patnaik // Diagnostyka. 2018. Vol. 19(1). P. 73–81. DOI: 10.29354/diag/81692
- Amer Y.A., El-Sayed A.T., El-Bahrawy F.T. Torsional vibration reduction for rolling mill’s main drive system via negative velocity feedback under parametric excitation // J. Mech. Sci. Technol. 2015. Vol. 29(4). P. 1581–1589
- Yarita I Analysis of chattering in cold rolling for ultra-thin gauge steel strip/ I Yarita //Trans Iron Steel Inst Jpn. 1978. Vol. 18(1). P. 1–10. DOI: 10.2355/isijinternational1966.18.1
- High-speed rolling by hybrid-lubrication system in tandem cold rolling mills / Y. Kimura, N. Fu-jita, Y. Matsubara et al. // J. Mater Process Technol. 2015. Vol. 21(6). P. 357–368. DOI: 10.1016/j.jmatprotec.2014.10.002
- Analysis of chatter in tandem cold rolling mills / Y. Kimura, Y. Sodani, N. Nishiura et al. // ISIJ International. 2003. Vol. 43(1). P. 77–84. DOI: 10.2355/isijinternational.43.77
- Веренев В.В., Большаков В.И. Состояние вибрационной диагностики и мониторинга оборудования прокатных станов // Фундаментальные и прикладные проблемы черной металлургии: сб. научн. тр. Днепропетровск.: ИЧМ НАН Украины, 2006. Вып. 12. С. 267–281.
- Система обнаружения признаков развития «чаттера» и своевременной коррекции технологического режима непрерывной холодной прокатки полос / И.Ю. Приходько, П.В. Крот, Е.А. Парсенюк и др. // Труды VII Конгресса прокатчиков. М., 2007. Т. 1. С. 115–123.
- Harris F. On the Use of Windows for Harmonic Analysis With the Discrete Fourier transform // Proceedings of the IEEE February 1978 66(1):51–83. DOI: 10.1109/PROC.1978.10837
- Cooley, J. W., Tukey, J. W. An algorithm for the machine calculation of complex Fourier series (англ.) // Mathematics of Computation. 1965. Vol. 19. P. 297–301. DOI: 10.1090/S0025-5718-1965-0178586-1
- Zhivomirov H. On the Development of STFT-analysis and ISTFT-synthesis Routines and their Practical Implementation // TEM Journal. February 2019. Vol. 8, Iss. 1. P. 56–64. DOI: 10.18421/TEM81-07
- Hohyub J., Yongchul J., Seongjoo L., Yunho J. Area-Efficient Short-Time Fourier Transform Processor for Time-Frequency Analysis of Non-Stationary Signals // Appl. Sci. 2020, 10, 7208. DOI: 10.3390/app10207208
- Ali M. Al-Haj Fast Discrete Wavelet Transformation Using FPGAs and Distributed Arithmetic/ 160 Int. J. Appl. Sci. Eng // International Journal of Applied Science and Engineering. 2003. 1, 2: 160–171.
- Харахнин К.А., Маслов Е.А., Кожевников А.В. Алгоритм идентификации вибраций на стане бесконечной холодной прокатки // Вестник Череповецкого государственного университета. 2010. № 1. С. 131–136.
- PFCL201CE-50KN Pressductor PillowBlock Load Cells | saulcontrol. Обращение 05.02.2024.
- Котельников В.А. О пропускной способности «эфира» и проволоки в электросвязи // Репринт статьи в журнале УФН, 176:7 (2006), 762–770.
- Nyquist H. Certain topics in telegraph transmission theory // Trans. AIEE. Apr. 1928. Vol. 47. P. 617–644. Reprint as classic paper in: Proc. IEEE, Vol. 90, No. 2, Feb 2002.
- Shannon C.E. Communication in the presence of noise // Proc. Institute of Radio Engineers. Jan. 1949. Vol. 37, no. 1. P. 10–Reprint as classic paper in: Proc. IEEE, Vol. 86, No. 2 (Feb 1998).
- Жмудь В.А. Теорема Котельникова–НайквистаШеннона. Принцип неопределенности и скорость света // Автоматика и программная инженерия. 2014. №1(7). C. 127–136.