Research on the impact of nano carbon fillers on the morphology of epoxy binder
Автор: Vlada N. Ilyina, Stepan V. Ilyin, Gulnara R. Khalikova, Victoria A. Gafarova, Iskander R. Kuzeev
Журнал: Nanotechnologies in Construction: A Scientific Internet-Journal @nanobuild-en
Рубрика: Development of new materials
Статья в выпуске: 4 Vol.15, 2023 года.
Бесплатный доступ
Introduction. When developing a composite material, it is important to understand how the components included in its composition affect its properties. Fillers, by interacting with the matrix, can alter its initial structure, resulting in the composite acquiring characteristics different from the matrix. The high modifying ability of nanofillers is determined by their significant specific surface area. This allows for the total interfacial area between the matrix and the dispersed phase to be covered even with a relatively low concentration of particles, thereby enabling the use of a small amount of filler. Methods and materials. Composite materials with nano carbon fillers were investigated, including fullerenes, nanotubes, and graphene. Fractographic analysis of the tensile fracture surfaces of the samples was chosen to evaluate the structure of the composites, which allows determining the nature of the failure and the ability of the composite to restrain crack propagation. The microstructure of the composite materials, as well as the morphology of the reinforcing nano carbon fillers, were examined with a Tescan MIRA3 scanning electron microscope. Results and discussion. In a graphene composite, crack energy is dissipated through branching and elongation of the crack path. Carbon nanotubes, being embedded in the crack walls, hinder the opening of the crack edges. Crack energy is also consumed in overcoming friction forces during the extraction of nanotubes from the epoxy matrix. Agglomerates of fullerenes act as effective crack front arresters, forcing the crack to circumvent them, thereby creating new areas of fracture surfaces. This leads to an increase in the crack front length and the energy required for material failure. Conclusion. Adding nano-carbon fillers (graphene, CNT and fullerenes) as reinforcing components in the epoxy binder alters the structure. The study defines possible mechanisms for hardening of the composite materials due to adding the nano-carbon fillers.
Composite material, fractographic analysis of cracks, scanning electron microscope
Короткий адрес: https://sciup.org/142238305
IDR: 142238305 | DOI: 10.15828/2075-8545-2023-15-4-328-336
Текст научной статьи Research on the impact of nano carbon fillers on the morphology of epoxy binder
Original article
A s of today, polymeric composite materials are actively used in various areas: aircraft and space engineering [7–9], instrument and mechanical engineering [10, 11, 33, 34], construction [12–15], oil and gas. It is used as repair materials and protective covering for surfaces to prevent corrosion [1–6, 28–32].
The scope of application of composites directly impacts requirements to their physical and mechanical properties. When developing a composite material, it is important to understand how the components that make up its composition affect its properties. Fillers, by interacting with the matrix, can modify its original structure, thereby giving the composite characteristics different from those of the matrix. This allows for the creation of composite materials with desired physico-mechanical properties.
Unlike macro- and micro-sized fillers, nano-filler have a high modifying power determined by their significant specific area [8, 9, 37–43]. Therefore, relatively small concentration of particles allows to cover the entire surface of the boundary line between the matrix and the dispersion phase. In addition, this feature allows to effectively influence physical and mechanical properties of the composites despite of small amount of the filler.
The aim of this study was to investigate the influence of fillers on the morphology of the epoxy binder and the composite’s ability to restrain crack growth.
THE STUDY OF THE PROPERTIES OF NANOMATERIALS
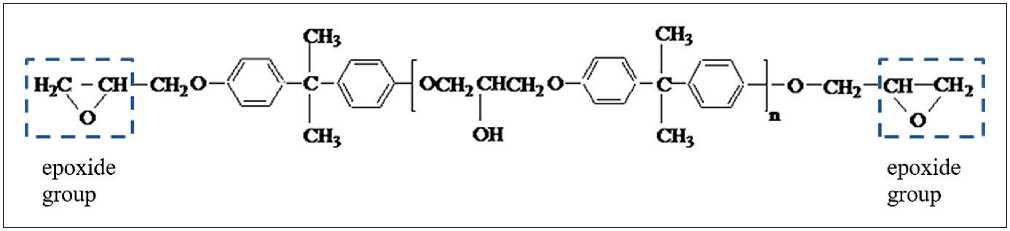
Fig. 1. The structural formula of ED-20
METHODS AND MATERIALS
Epoxy diane resin ED-20 was used as a polymeric matrix. The structural formula of the resin is presented in Fig. 1. Epoxy resin is an oligomer. It has epoxy groups at the ends of the chain.
Polyethylenepolyamine (PEPA) was used as a hardener. The structural formula of the hardener is presented in Fig. 2. When the material is hardening, it causes a chemical reaction with the hardener’s amino-groups. The reaction disrupts the epoxy group and forms a cross-linked polymer.
The reinforcing fillers are nano-carbon materials, such as fullerens, nano-tubes and graphene. Such a list is determined by different morphology of the fillers’ structures.
Carbon nano-tubes (CNT) are one-dimensional structures. They are rolled up sheets of graphene. They form hollow cylindric molecules. Their specific area is approximately 500-1,000m2/g [16]. The typical structure of CNT is presented in Fig. 3a and 3b.
Fullerenes are the three-dimensional fillers since they are polyatomic molecules with an enclosure and the sur-
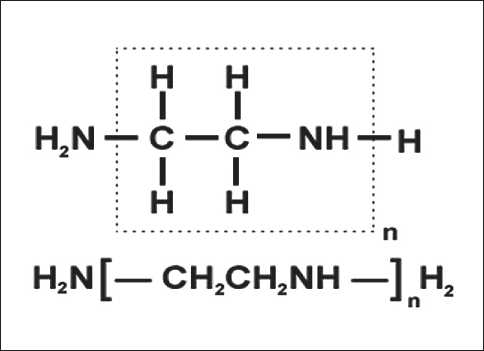
Fig. 2. The structural formula of polyethylene polyamine face of a high curvature. Their specific area is approximately 1,340 m2/g [35]. The typical structure of fullerenes is presented in Fig. 3e and 3f.
The diluent of the experiment is a kerosene-based liquid. The liquid has magnetic particles Fe2O3 sized from 5 to 30 nm. This diluent can improve the composite’s movement through narrow channels [1, 36]. The liquid does not form huge agglomerates of magnetic particles, because it has a surface active agent (SAA) in it. The agent is stearic acid C17H35COOH. The acid pulls to O–H+ polar structures to the magnetic particle surface and forms a 2 nm molecular layer around Fe2O3 particles. Flexible non-polar tails of the SAA in the non-polar dispersive environments are pointed away from the particles toward the liquid. (Fig. 4).
The component proportions in the composite materials are chosen based on the previous factorial experiments done by the authors of this research [21]. As a result, the study detects the most suitable patterns for getting the required balance of the adhesive and cohesive strength of the composites.
To evaluate the structure of the composites, this study applies fractographic research to test sample cracks for tensile strength. The test allows to define the destruction and how the composite resits the expansion of the cracks.
The microstructure of the composite materials, as well as the morphology of the hardening nano-carbon fillers, are studied with a scanning electron microscope (SEM) Tescan MIRA3. Initially, the sample surface was sprayed with a thin layer of carbon using Polaron E6700. The approximate thickness is 20 nm.
RESULTS AND DISCUSSION
The surface of the epoxy resin without fillers and its typical structure are presented in Fig. 5.
It is distinct that destruction is caused by insufficient strength of the material since the crack is straight. Few pores do not influence the crack’s expansion. There are also limited areas which prove that the material is flowing while getting destroyed. The long microcracks are found across the whole surface of the crack. They expand in the
THE STUDY OF THE PROPERTIES OF NANOMATERIALS
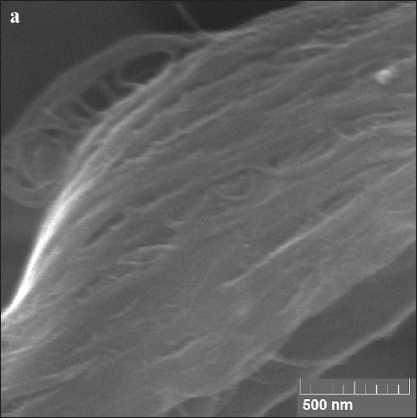
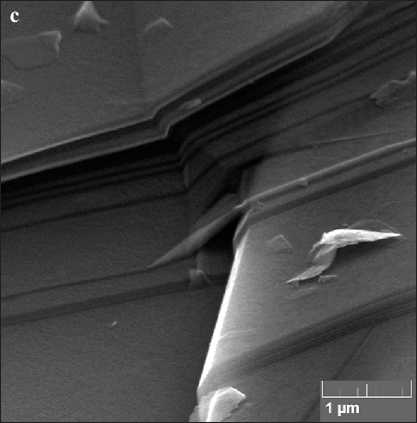
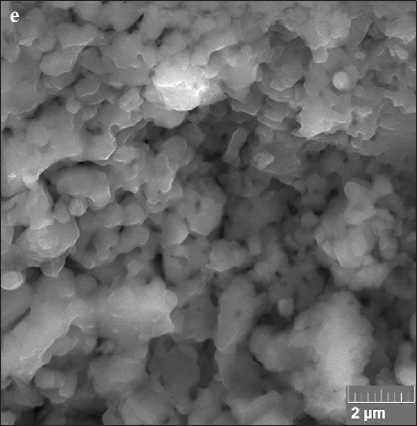
Fig. 3. The typical structure of nanocarbon fillers: a, b – graphene, c, d – carbon nanotubes, e, f – fullerenes
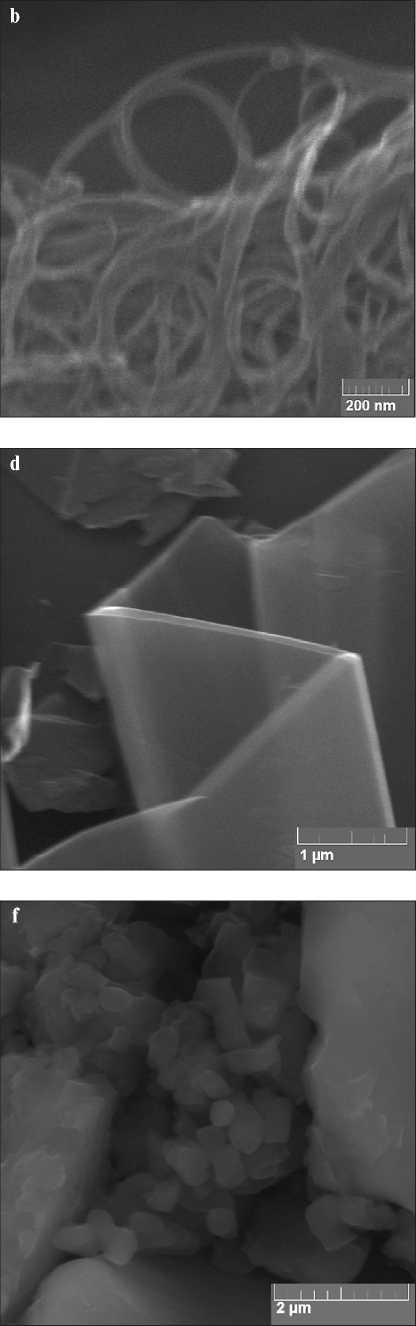
THE STUDY OF THE PROPERTIES OF NANOMATERIALS
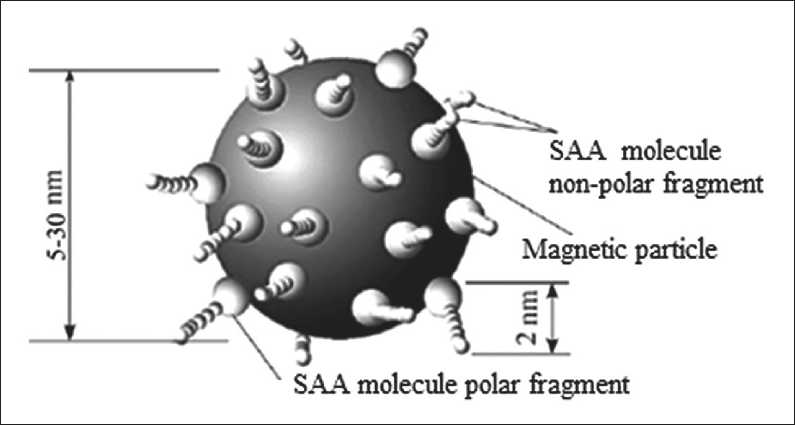
Fig. 4. Fe2O3 Particle with Adsorbed Layer of SAA on it
same direction as the main crack (Fig. 5a). Microcracks spread in a coral-like manner (Fig. 5b).
Unlike the epoxy resin without the fillers, if we add carbon fillers to the epoxy resin, it will form numerous pores (Fig. 5a). This is associated with the fact that the nano-fillers have the big specific surface area. As a result, they are able to adsorb the epoxy resin or the hardener. At the same time they alter the stoichiometry in the limited areas. The nano-sized particles also tend for adhesion and can form agglomerates. The size of the agglomerates may reach hundreds of micrometers [11].
Adding graphene to the composite material causes a layered structure (Fig. 6b). The crack in the sample is straight. Therefore, the destruction is caused by strength insufficiency. (Fig. 6a). The composite is found to become stronger because the crack energy disperses to overcome the friction forces between the layers of the composite material (Fig. 6c). Also the energy is dispersed because the crack is branching (Fig. 6b).
Adding CNT as the filler forms a fibred composite material (Fig. 7b). The surface of the crack in the composite with CNT, and its typical structure are pre-
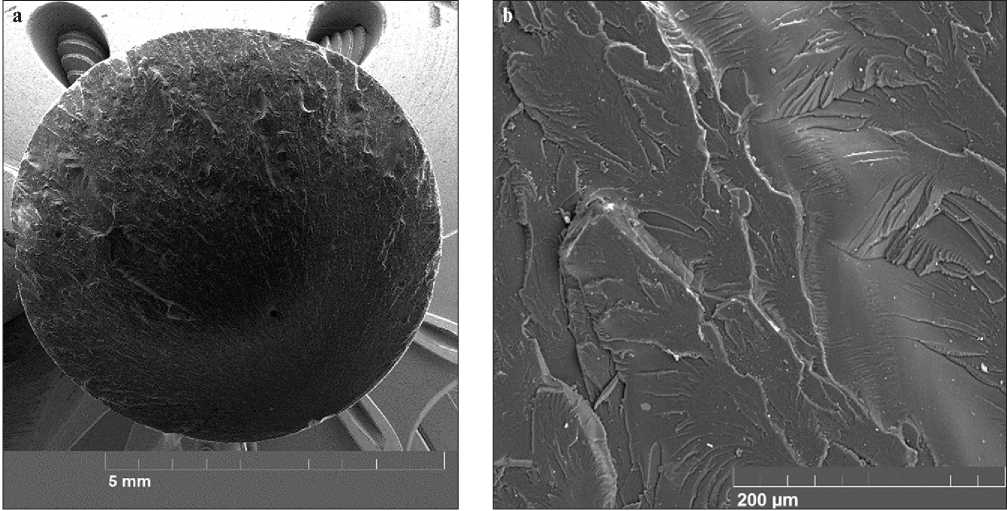
Fig. 5. Typical Macrostructure (a) and Microstructure (b) of Epoxy Resin Crack without Fillers
THE STUDY OF THE PROPERTIES OF NANOMATERIALS
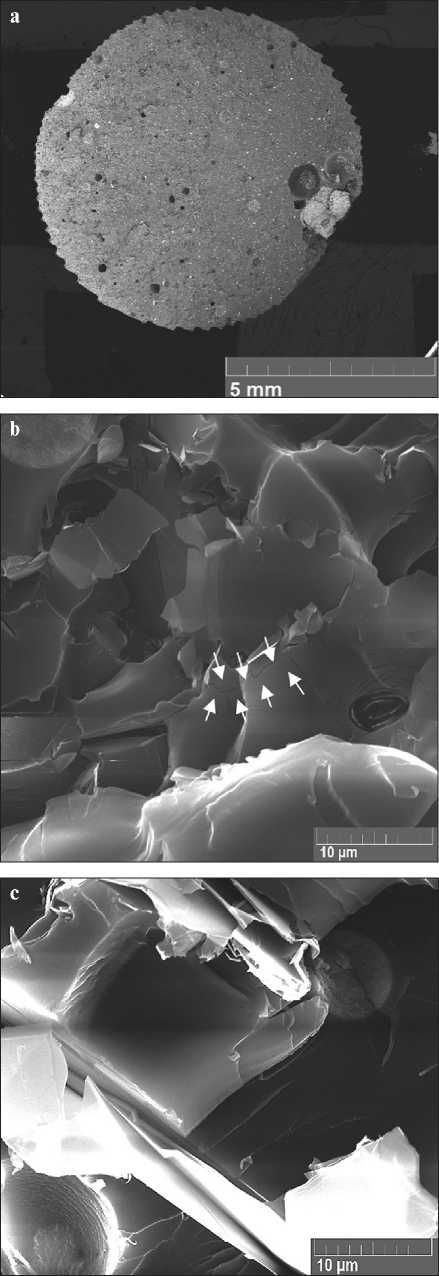
Fig. 6. Typical Macrostructure (a) and Microstructure (b, c) of Crack in Composite with Graphene Filler: Arrows Indicate Branching of Microcrack
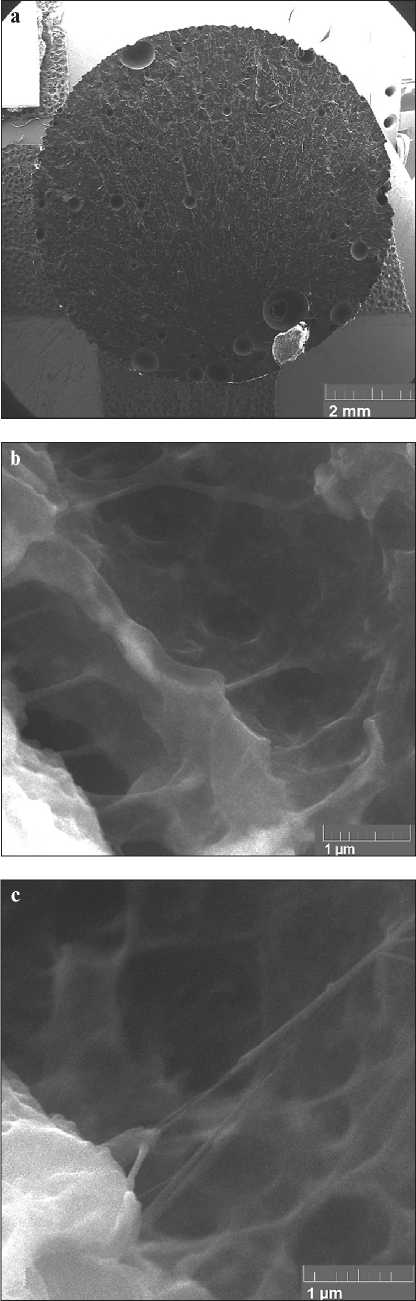
Fig. 7. Typical Macrostructure (a) and Microstructure (b, c) of Crack in Composite with CNT Filler
THE STUDY OF THE PROPERTIES OF NANOMATERIALS
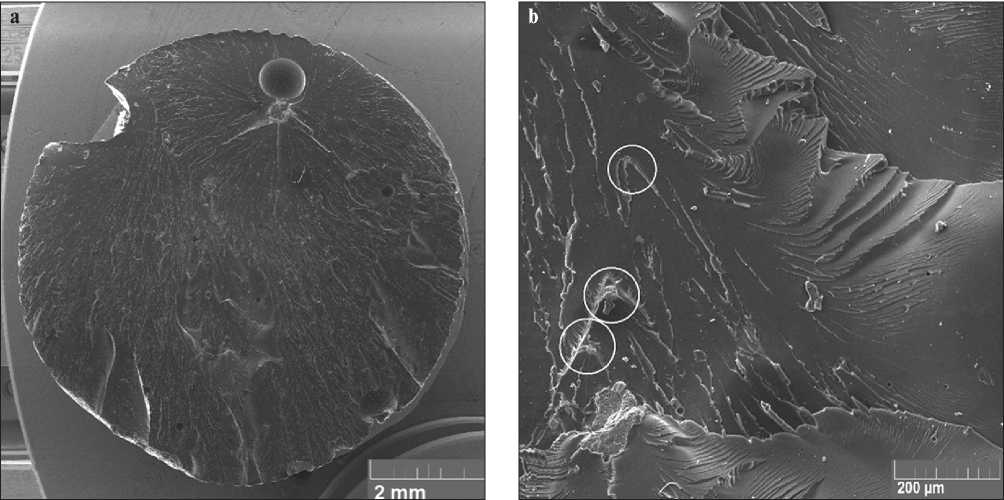
Fig. 8. Typical Macrostructure (a) and Microstructure (b) of Crack in Composite with Fullerene Filler: Circles Indicate Places Where Crack Front Goes Around Fullerene Agglomerates
sented in Fig. 7. It is clear that the microcracks expand radially away from the pore concentration area. CNT get attached to the walls and prevent the crack edge from expanding (Fig. 7b). For example, we have similar findings in [26]. The CNT-filled composite material hardens because the crack energy disperses due to friction forces caused by CNTs extracted from the epoxy matrix (Fig 7c).
Adding the fullerenes does not significantly alter the structure of the default matrix (Fig. 5b). However, the sample faces major plastic destruction (Fig. 8a). The fullerene agglomerates effectively obstruct the crack expanding. It forces the crack to go around the agglomerates. (Fig. 8b). This causes the new crack areas, extension of the crack front and boosts the energy necessary for the material to get destroyed. For example, we have similar findings in [27].
CONCLUSION
The research showed that adding nano-carbon fillers (graphene, CNT and fullerenes) as the reinforcing components in the epoxy binder causes altering its structure. The study defines possible mechanisms for hardening of the composite materials due to adding the nano-carbon fillers. The crack energy disperses through the graphene-filled composite due to branching and elongation of the crack. The carbon nano tubes get attached to the walls and prevent the crack edge from expanding. The crack energy may also be dispersed to overcome the frictional forces caused by carbon nano tubes extracted from the epoxy matrix. The fullerene agglomerates effectively obstruct crack expanding. They force cracks to go around the agglomerates. This causes new crack areas. Alongside, the crack front extends while boosting the energy necessary for the material to get destroyed.
Список литературы Research on the impact of nano carbon fillers on the morphology of epoxy binder
- Gafarova V.A. Materials and method of sealing cracks in oil and gas equipment during the maintenance period of operation: diss. … cand. tech. sciences: 05.16.09. Ufa. 2019. 132 p. (In Russ.).
- Gafarova V.A., Krioni N.K., Mingazhev A.D. Restoration repair of the main pipeline during its operation. Prom-Engineering: III International Scientific and Technical Conference. 2017;121-125. (In Russ.).
- Gafarova V.A., Babin A.Yu., Bazarova Yu.V., Kuzeev A.M. Influence of composite material on stress distribution in the crack region Modern technologies of composite materials. 2019;295-296. (In Russ.).
- Gafarova, V.A., Babin A.Yu., Gareeva E.R., Abdrakhmanova K.N., Lomakina L.N. Influence of a filler on strength characteristics of the properties of a composite material based on epoxy resin. Materials Today: Proceedings. 2019; 11:252-257.
- Abdrakhmanova K. N., Babin A.Yu., Gareeva E.R., Gafarova, V.A. Modeling of crack filling with composite material in the Abaqus software package. Industrial safety expertise and diagnostics of hazardous production facilities. 2018;135-140. (In Russ.).
- Gafarova V. A., Nevzorov V.N. Modeling of the process of penetration of composite material into the crack cavity. Welding and control – 2016. Ufa. 2016;85-86. (In Russ.).
- Kondrashov S.V., Shashkeev K.A., Petrova G.N., Mekalina I.V. Polymer composite materials of structural purpose with functional properties. Aviation materials and technologies. 2017; 405-419. https://doi.org/10.18577/2071-9140-2017-0-S-405-419. (In Russ.).
- Zagora A.G., Kondrashov S.V., Antyufeeva N.V., Pykhtin A.A. Investigation of the influence of technological modes of manufacturing epoxinanocomposites with carbon nanotubes on their heat resistance. Proceedings of VIAM. 2019;1(73):64-73. https://doi.org/10.18577/2307-6046-2019-0-1-64-73. (In Russ.).
- Pykhtin A.A. High-tech epoxy nanodispersions and nanocomposites with a controlled structure and a set of properties: diss. ... cand. tech. sciences: 05.17.06. Moscow: 2017. (In Russ.).
- Ivanov V.A. Methods of restoration of technological and auxiliary equipment with wear-resistant composite materials: diss. ... cand. tech. sciences: 05.02.13. Moscow; 2015. (In Russ.).
- Brusentseva T.A., Filippov A.A., Fomin V.M. Composite materials based on epoxy resin and nanoparticles. Proceedings of the Altai State University. 2014;1-1(81):25-27. https://doi.org/10.14258/izvasu(2014)1.1-04. (In Russ.).
- Chebotareva E.G. Nanomodified composites for construction purposes using epoxy resin: abstract of the dissertation of the candidate of technical sciences: 05.23.05. Belgorod; 2010. (In Russ.).
- Novoselova S.N. Development and research of properties of low-viscosity polymer composites of functional purpose: abstract of the dissertation of the candidate of technical sciences: 05.17.06. Biysk; 2012. (In Russ.)
- Gorbunov F.K., Shevtsov Yu.N., Berdnikova L.K. Thermodynamic characteristics of materials used for the repair of road and airfield coatings. Roads and bridges. 2017;2(38):21. (In Russ.).
- Gorbacheva S.N., Gorbunova I.Y., Kerber M.L., Antonov S.V. Properties of composite polymer materials based on epoxy resin modified with boron nitride. Advances in chemistry and chemical technology. 2017;11(192):35-36. (In Russ.).
- Irzhak V.I. Structure and properties of polymer materials: textbook. Saint Petersburg: Lan; 2019. URL: https://e.lanbook.com/book/123663 (accessed: 11.22.2022). (In Russ.).
- Ilyina V.N., Gafarova V.A., Bugai D.E., Ilyin S.V., Kuzeev I.R. Adhesive and cohesive strength of composite material with carbon fillers for sealing cracks. Petroleum engineering. 2021;19(6):124-133. https://doi.org/10.17122/ngdelo-2021-6-124-133. (In Russ.).
- Chen Ya., Marakhovsky P.S., Malysheva G.V. Determination of thermophysical properties of epoxy materials during their curing. Works of VIAM. 2018;9(69):119-123. https://doi.org/10.18577/2307-6046-2018-0-9-119-123. (In Russ.).
- Brusentseva T.A., Zobov K.V., Filippov A.A., Bazarova D.J., Lhasaranov S.A., Chermoshentseva A.S., Syzrantsev V.V. Introduction of nanopowders and mechanical properties of materials based on epoxy resins. Nanoindustry. 2013;3(41):24-31. (In Russ.).
- Mostovoy A.S. Development of compositions, technologies and determination of properties of micro- and nanofilled epoxy composites of functional purpose: abstract of the dissertation of the candidate of technical sciences. 05.17.06. Saratov; 2014. (In Russ.).
- Samoilova D.O. Investigation of the conditions for the introduction of carbon nanotubes into a polymer-carbon composite in order to increase strength. Chelyabinsk: SUSU. ET. 2018;443:138 p. (In Russ.).
- Marakhovsky P.S., Kondrashov S.V., Akatenkov R.V. About modification of heat-resistant epoxy binders by carbon nanotubes. Bulletin of the Bauman Moscow State Technical University. Mechanical Engineering series. 2015;2(101):118-127. (In Russ.).
- Topolyansky P.A. Investigation of adhesive properties and the mechanism of formation of a coating applied by the method of finishing plasma hardening. Part 2. Mater. 7th international. practical conference-exhibitions “Technologies of repair, restoration and hardening of machine parts, mechanisms, equipment, tools and technological equipment”. 12–15th April 2005. St. Petersburg. 2005:316-333. (In Russ.).
- Zimon A.D. Adhesion of films and coatings. Moscow: Chemistry; 1977 (In Russ.).
- Zorin V.A., Baurova N.I. The use of intelligent materials in the production, diagnosis and repair of machines. Second edition, revised and expanded. Moscow: Limited Liability Company “Scientific and Publishing Center INFRA-M”; 2015 (In Russ.).
- Ognev A.Yu., Teplykh A.M., Bataev V.A. Polymer composite material based on epoxy resin, reinforced with multilayer carbon nanotubes. Scientific Bulletin of the Novosibirsk State Technical University. 2009;4(37):115-122. (In Russ.).
- Khvostov S.A. Principles of modification of epoxy binders by carbon nanoparticles and technology for obtaining composites based on them: specialty 05.02.01: abstract of the dissertation for the degree of candidate of technical sciences. Barnaul; 2007. (In Russ.).
- Krutikov I.Y. Restoration of operability of parts of technical devices with crack-like defects by composite materials: diss. ... cand. tech. sciences: 05.02.13. Ufa; 2010. (In Russ.).
- Tlyasheva R.R., Gafarova V.A., Vagazova K.R., Kuzeev A.M. Composite material for filling the cavity of cracks and crack-like defects. Bashkir Chemical Journal. 2016;23(3):56-62. (In Russ.).
- Patent for invention No. 2601782 Method of pipeline restoration repair and device for its implementation. Kuzeev I.R., Gafarova V.A., Mingazhev A.D. (RF). Application no. 2015122333. Announced on 10.11.2015. Zareg. 14.10.2016 Publ. 10.11.2016, Byul. No. 31. 11 p. (In Russ.).
- Gafarova V.A. Application of composite materials for containment of crack growth in oil and gas equipment. Petroleum engineering. 2018;16(5):99-107. https://doi.org/0.17122/ngdelo-2018-5-99-107. (In Russ.).
- Gafarova V.A., Kravtsov V.V., Kuzeev I.R. Analysis of methods and review of composite materials for sealing cracks in structures. Actual problems of science and technology: materials of the VII International Scientific and Practical Conference of Young Scientists, Ufa, November 18–20, 2014. Ufa. 2014;2:104-106. (In Russ.).
- Tulinov A.B., Ivanov V.A., Goncharov A.B. Progressive technologies and materials for the restoration of mining equipment. Modern technologies in mining engineering: collection of scientific papers from the seminar. Moscow; 2012.
- Gvozdev A.A. Ways to improve the technology of repair of parts and joints with HMS compounds – cold molecular welding. Vladimirsky husbandman. 2014;4(70):39-40. (In Russ.).
- Berezkin V.I., Viktorovsky I.V., Vul A.Ya. Fullerene microcrystals as adsorbents of organic compounds. Physics and Technology of semiconductors. 2003;37(7):802-810. (In Russ.).
- Berkovsky B.M., Medvedev V.F., Krakow M.S. Magnetic fluids. Moscow: Chemistry; 1989. (In Russ.).
- Smirnov I.V. Modeling of physical and mechanical properties and climatic resistance of epoxy composites: diss. ... cand. tech. sciences: 05.23.05. Saransk; 2017. (In Russ.).
- Kondrashov S.V., Shashkeev K.A., Popkov O.V., Solovyanchik L.V. Promising technologies for obtaining functional materials for structural purposes based on nanocomposites with CNT (review). Proceedings of VIAM. 2016;3(39):7. https://doi.org/10.18577/2307-6046-2016-0-3-7-7. (In Russ.).
- Yeletsky A.V. Sorption properties of carbon nanostructures. Successes of physical sciences. 2004;174(11):1191-1231. (In Russ.).
- Bondaletova L.I., Bondaletov V.G. Polymer composite materials: textbook. Tomsk: Publishing House of Tomsk Polytechnic University. 2013. (In Russ.).
- Korneev A.D., Burkov P.V., Klyshnikov A.A., Papin I.V. Structuring of protective polymer coatings. Bulletin of the Volgograd State University of Architecture and Civil Engineering. Series: Construction and Architecture. 2011;22(41):69-72. (In Russ.).
- Danchenko Yu., Andronov V., Teslenko M., Permiakov V., Rybka E., Meleshchenko R., Kosse A. Study of the free surface energy of epoxy composites using an automated measurement system. Eastern-European Journal of Enterprise Technologies. 2018;12:9-17.
- Lizunov D.A. Development of high-strength carbon fiber plastics based on epoxy-containing oligomers: diss. ... cand. tech. sciences: 05.17.06. Moscow; 2014. (In Russ.).