Снижение динамического момента в главной линии прокатной клети толстолистового стана
Автор: Гасияров Вадим Рашитович, Басков Сергей Николаевич, Гасиярова Ольга Андреевна, Логинов Борис Михайлович, Усатый Дмитрий Юрьевич
Рубрика: Расчет и конструирование
Статья в выпуске: 3 т.19, 2019 года.
Бесплатный доступ
На примере электромеханических систем толстолистового прокатного стана 5000 рассмотрена проблема снижения динамических нагрузок в валопроводах клети при захвате металла валками. Отмечено, что амплитуда динамического момента в значительной степени зависит от соотношения скорости движения металла по рольгангу и линейной скорости валков реверсивной клети. Рассмотрен механизм возникновения ударных нагрузок при замыкании углового зазора в шпиндельных соединениях. Дано экспериментальное подтверждение колебательного характера моментов при захвате. Рассмотрен способ ограничения динамических нагрузок за счет предварительного разгона электропривода перед захватом и его последующего торможения с заданным отрицательным ускорением. Отмечено, что недостатком способа является зависимость динамических нагрузок от точности определения положения «головы» раската относительно клети. Предложен усовершенствованный способ управления скоростью движения металла по рольгангу, обеспечивающий инвариантность динамических процессов к точности определения положения металла. Рассмотрены тахограммы электропривода клети, поясняющие суть разработанного способа. Представлены результаты математического моделирования и экспериментальных исследований, выполненных на стане 5000. Подтверждена эффективность предложенного технического решения. Даны рекомендации по его внедрению на прокатных станах, работающих с ударным приложением нагрузки.
Толстолистовой прокатный стан, раскат, движение, реверсивная клеть, шпиндельное соединение, динамические нагрузки, электропривод, скорость, управление, способ, разработка, моделирование, эксперимент, рекомендации
Короткий адрес: https://sciup.org/147231748
IDR: 147231748 | DOI: 10.14529/engin190303
Текст научной статьи Снижение динамического момента в главной линии прокатной клети толстолистового стана
Одной из важнейших научно-практических задач, решение которой обеспечивает снижение аварийности оборудования главных линий клетей прокатных станов, является ограничение динамических нагрузок, возникающих при захвате металла валками.
Изучению процессов, возникающих при заполнении очага деформации в момент захвата, уделяется достаточно внимания в отечественной и зарубежной литературе. Среди известных публикаций следует отметить работы специалистов SMS-Demag, Siemens, VAI и ряда японских фирм [1–6]. В данном направлении активно работают отечественные научные школы ФГБОУ ВО «Липецкий государственный технический университет» [7–9], ФГАОУ ВО «Южно-Уральский государственный университет (НИУ)» совместно со специалистами ПАО «Магнитогорский металлургический комбинат» (ПАО «ММК») и ФГБОУ ВО «Магнитогорский государственный технический университет» [10–12]. Внедрены алгоритмы управления, обеспечивающие снижение нагрузок электроприводов вертикальных валков универсальных клетей широкополосного стана горячей прокатки. При этом проблема ограничения упругих моментов в валопроводах горизонтальных валков остается нерешенной.
Названная проблема актуальна для электромеханических систем толстолистового стана 5000 ПАО «ММК». Как и большинство современных толстолистовых станов, он содержит мощную прокатную клеть, в которой осуществляется прокатка металла в реверсивном режиме. По обе стороны клети расположены рольганги (подводящий и отводящий), обеспечивающие перемещение раската (рис. 1). Очевидно, что ударные нагрузки, возникающие при захвате металла, зависят от точности согласования скоростей роликов рольгангов и окружной (линейной) скорости валков клети.
Исследования показали, что при прокатке листов из труднодеформируемых марок стали в клетях толстолистовых станов возникают динамические нагрузки, в два и более раза превышающие установившийся момент прокатки. Как правило, это приводит к выходу электропривода на ограничение по моменту, размыканию контура регулирования скорости и возникновению затухающих колебаний. Это подтверждают результаты экспериментальных исследований, опубликованные в работах [13, 14]. Ударные нагрузки вызывают усталостные разрушения механического оборудования главной линии клети, чаще всего – шпиндельных соединений. Аварийные поломки головок шпинделей либо шеек валков приводят к длительным простоям стана и значительным затратам на устранение последствий [15, 16]. Также снижаются надежность и долговечность силового электрооборудования: синхронных
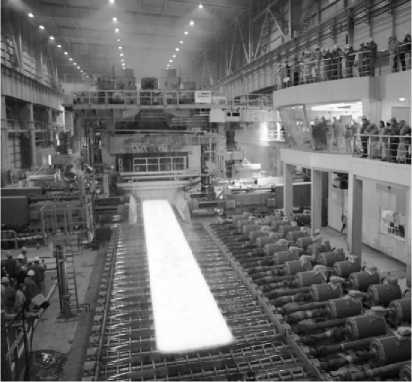
Рис. 1. Движение раската по рольгангу после выхода из прокатной клети стана 5000
двигателей и преобразователей частоты, на базе которых выполнены электроприводы большинства современных прокатных агрегатов, в том числе стана 5000. Это позволяет сделать вывод об актуальности ограничения электромагнитного момента двигателей и упругого момента в валопроводах клети. Как показали исследования, наиболее эффективным и наименее затратным способом является формирование оптимальных тахограмм электроприводов валков и подводящего и отводящего рольгангов.
Представленная статья является логическим продолжением материала, опубликованного в работе [17]. Это связано с тем, что дополнительно проведенные теоретические и экспериментальные исследования потребовали совершенствования ранее разработанных алгоритмов управления.
1. Постановка задачи
Упрощенный вид шпинделя показан на рис. 2, а [18, 19]. Конструкция шпиндельно г о соединения, механизм износа скользящего блока вследствие увеличения углового зазора δ поясняет рис. 2, б. На вновь устанавливаемом механизме угловой зазор в соединении небольшой и составляет 1–2 град. Он необходим для сочленения двух в р ащающихся устройс т в (непосре д ственно шпинделя и валка) и обеспечения свободного движения при вертикальном перемещении валков. Величину углового зазора определяет износ вилок и головок шпинделей (см. рис. 2, б). О ни наиболее подвержены усталостным разрушениям.
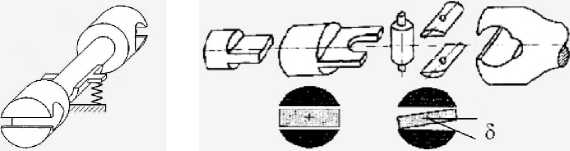
а) б)
Рис. 2. Шпиндель в сборе (а) и конструкция скользящего блока (б): δ – угловой зазор в соединении
Большая масса валка с одной стороны шпинделя и вращающихся частей двигателя с другой приводят к тому, что при закрытии (замыкании) угловых зазоров возникают удары в соединениях. Кроме этого, на динамические нагрузки оказывают влияние упругие свойства валопровода. Поэтому изменения момента на валу при захвате металла валками имеют колебательный характер. Амплитуда колебаний в 2–3 раза превышает величину динамического момента, обусловленного непосредственно замыканием зазора.
Расчет и конструирование
На основании проведенных теоретических и экспериментальных исследований авторами сформулированы задачи, направленные на снижение динамических нагрузок за счет разработки алгоритмов управления электроприводами. Основными являются:
-
1) ограничение ударного момента, возникающего непосредственно вследствие замыкания углового зазора в механических соединениях главных линий;
-
2) компенсация колебаний момента, вызванных упругими свойствами валопроводов, в рассматриваемом случае – упругими свойствами шпинделей.
Основным способом решения первой задачи является обеспечение захвата металла валками в режиме ускорения (предразгона) электропривода [20, 21]. Для решения второй задачи авторами предложен способ управления электроприводом, в котором наряду с предразгоном осуществляется торможение двигателя с заданным отрицательным ускорением после захвата. В результате выполненных исследований подтверждена техническая эффективность этих решений.
Таким образом, можно утверждать, что достижение поставленной цели в ранее разработанных способах обеспечивается за счет формирования оптимальных тахограмм электроприводов валков прокатного стана (более подробно разработанные тахограммы рассматриваются ниже). Для этого необходима разработка специальных алгоритмов управления скоростью электроприводов клети и скоростью раската при движении по рольгангу. Вместе с тем при проведении опытно-промышленных испытаний установлено, что недостатком известных алгоритмов управления электроприводами является недостаточная точность определения положения раската на подводящем и отводящем рольгангах. В результате сигналы на предразгон и торможение электроприводов подаются со сдвигом во времени как в сторону более раннего, так и более позднего начала ускорения (рис. 3, а). Это вызывает отклонения скоростного режима от заданного и нарушение цикла прокатки.
Для устранения указанного недостатка поставлена задача разработки способа управления электроприводами, который обеспечил бы ограничение динамических нагрузок независимо от точности слежения за перемещением раската по рольгангу. В отличие от [17] разрабатываемый способ должен удовлетворять следующим требованиям:
-
1. Формирование заданной тахограммы (режимов разгона – торможения) должно начинаться по сигналу о достижении «головой» раската контрольной точки на рольганге.
-
2. Режим предразгона должен продолжаться до захвата металла валками. Это обеспечит гарантированно замкнутое состояние углового зазора в момент захвата.
-
3. Тахограмма электроприводов (моменты времени, величины ускорений и т. д.) должна формироваться независимо от момента начала предварительного разгона электропривода, т. е. быть инвариантной к точности определения положения металла на рольганге.
-
2. Основная часть
В связи с последним условием разработанный способ получил название «инвариантного способа формирования скоростных режимов». Его рассмотрение является целью представленной публикации.
Анализ режима захвата металла валками
На рис. 3 приведены осциллограммы моментов M Д В двигателей, моментов M В, измеренных на валах шпинделей, и скоростей n электроприводов реверсивной клети стана 5000. Они зафиксированы в режиме захвата металла валками при прокатке профиля «тяжелого» сортамента. Кривые в окнах 1 и 2 приведены для электромеханических систем верхнего и нижнего валков соответственно. В окне 3 представлены осциллограммы сигналов заданий n 0 и фактических скоростей n в , n н для обоих электроприводов.
На рис. 3, а захват металла происходит в режиме торможения электроприводов при полностью открытых зазорах в шпиндельных соединениях. Размыкание углового зазора подтверждают небольшие отрицательные отклонения моментов на валах M В и электромагнитных моментов двигателей M ДВ в моменты времени t 1 и t 2 . При отработке данного режима моменты обоих двигателей достигают уровня ограничения M ДВmax , установленного равным 4500 кН·м.
Динамические отклонения моментов на осциллограммах, рис. 3, а и б (верхний валок), приведены в соответствующих столбцах таблицы. Их амплитуду характеризуют коэффициенты кратности k Вм (либо k ДВм ), которые определяются как отношение максимального момента M Вmax (либо M ДВmax ) к установившемуся моменту прокатки M ст .
Динамические отклонения моментов при захвате
Параметр |
Величина на осциллограммах |
|||||
рис. 3, а |
рис. 3, б |
|||||
Момент на валу |
M ст |
M Вmax |
k Вм |
M ст |
M Вmax |
k Вм |
кН∙м |
ед. |
кН∙м |
ед. |
|||
3000 |
6500 |
2,2 |
1500 |
2500 |
1,67 |
|
Момент двигателя |
M ст |
M ДВ max |
k ДВм |
M ст |
M ДВmax |
k Вм |
кН∙м |
ед. |
кН∙м |
ед. |
|||
3000 |
4500 |
1,5 |
1500 |
2000 |
1,33 |
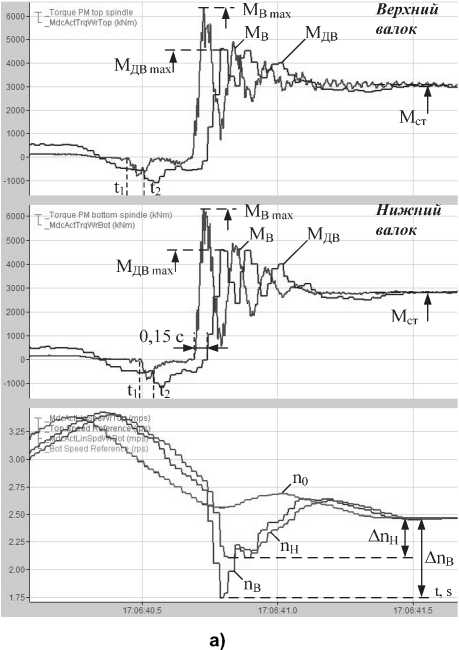
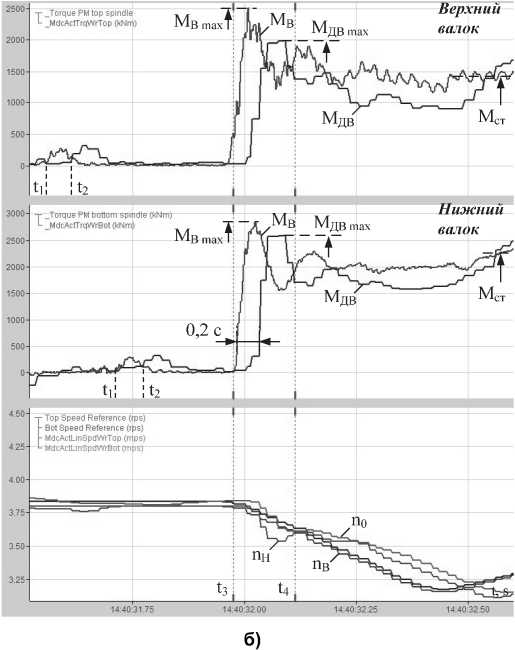
Рис. 3. Осциллограммы моментов и скоростей при захвате металла валками клети стана 5000 при открытых (а) и закрытых (б) угловых зазорах в шпиндельных соединениях
В результате анализа осциллограмм сделаны следующие выводы:
-
1. На рис. 3, а кратность динамического момента k Вм на валах обоих шпинделей в 2,2 раза превышает установившийся момент прокатки ( M Вmax = 6500 кН∙м, M ст = 3000 кН∙м).
-
2. Амплитуду электромагнитного момента двигателя определить невозможно, так как момент достигает уровня ограничения 4500 кН∙м. Это происходит в течение первых двух колебаний момента. Но даже в этом случае k Вм = 1,5.
-
3. После захвата возникают колебания моментов, которые затухают только благодаря диссипативным силам в передаче (вязкому трению, нагреву и др.). Влияние демпфирующих свойств двигателя происходит не в полной мере вследствие ограничения по моменту и кратковременной потере управляемости электропривода.
-
4. Осциллограммы моментов двигателей и шпинделей имеют идентичный характер с отличиями по максимальным значениям и времени их достижения. В силу инерционности электрической системы момент на валу достигает максимального значения M Вmax раньше, чем момент двигателя достигает величины M ДВmax . Разница составляет 0,15–0,2 с, эти данные подтверждаются выводами, сделанными в работах [22, 23].
Недопустимые нагрузки, имеющие колебательный характер, и потеря управляемости электропривода подтверждают актуальность разработки способов управления, обеспечивающих
Расчет и конструирование
ограничение динамических моментов в режиме захвата металла валками. Данные способы должны разрабатываться на основе концептуального подхода, согласно которому выполняется индивидуальное ограничение каждого из факторов, влияющих на амплитуду и степень затухания колебаний момента.
Способ ограничения динамического момента
Суть разработанного способа поясняется графиком задания скорости электропривода, представленным на рис. 4, а. Он включает выполнение следующих операций (показаны на средней тахограмме, выделенной жирной линией):
-
- до захвата металла валками в интервале t 1 - t 2 осуществляется повышение скорости электропривода на величину, компенсирующую динамическое снижение (просадку) скорости A n в, либо A n н на рис. 3, а;
-
- момент t 1 начала предразгона и длительность интервала t 1 - t 2 рассчитываются таким образом, чтобы захват металла осуществлялся на участке ускорения электропривода; это обеспечивает гарантированное замыкание зазоров в шпиндельных соединениях;
-
- после входа металла в клеть (в момент t 2) в интервале t 2- t 3 дополнительно увеличенная скорость снижается на величину полученного приращения;
-
- при t > t 3 в соответствии с технологией происходит ускорение до рабочей скорости.
Задание на скорость
Таблицы траекторий
Рис. 4. Задание скорости электропривода клети (а) и функциональная схема разработанной системы управления (б)
б)
Рег. токов и силовая часть
Рег. токов и силовая часть
На рис. 4, б представлена схема системы управления, реализующей данный способ [17]. Отличием является наличие блока расчета и управления компенсацией просадки скорости. Величина компенсации рассчитывается в модели второго уровня по ожидаемому моменту электропривода и характеристикам системы регулирования скорости. Для определения сигнала компенсации предварительно получена экспериментальная зависимость величины просадки скорости от мо- мента нагрузки. По этой характеристике определяется коэффициент динамической жесткости электромеханической системы.
Для обеспечения ускорения перед захватом в схему включен дополнительный задатчик интенсивности (ЗИ предразгона), выходной сигнал которого суммируется с выходным сигналом интерполятора. Величина ускорения в данном режиме определена экспериментально (равна 0,22 м/с2). Алгоритм системы реализован программным путем в управляющем контроллере электроприводов клети. Для определения момента начала ускорения используется информация, поступающая из системы слежения за металлом на рольгангах.
Пояснения к вычислению расстояния от головного участка до клети, необходимого для достижения требуемой скорости к моменту захвата, показаны на тахограмме, рис. 4, а. По известным значениям заправочной скорости V З и скорости опережения V оп вычисляется требуемое ускорение V оп /( t 2 – t 1 ). Исходя из этого рассчитывается расстояние S от «головы» раската до клети, при достижении которого начинается предразгон. При поступлении сигнала «Данные системы слежения за заготовками» о подходе раската на расстояние S подается управляющий сигнал на вход ЗИ предразгона. После захвата металла задание на предразгон обнуляется.
Теоретические и экспериментальные исследования показали, что точность задания скорости в момент захвата зависит от точности измерения расстояния, обеспечиваемой системой слежения за заготовками. При возникновении ошибки в определении положения «головы» заготовки (см. рис. 4, а, моменты tʹ 1 , tʺ 1 ) при ее входе в клеть в момент t 2 будет устанавливаться меньшее значение опережающей скорости по сравнению с расчетным ( Vʹ оп либо Vʺ оп ). Ломаная 1 на рис. 4, а соответствует раннему началу ускорения электропривода, линия 2 – поступлению задания на ускорение «с опозданием». В обоих случаях динамические отклонения моментов на валах шпинделей увеличиваются (на рис. 4 не показаны). Это было подтверждено результатами моделирования.
«Инвариантный» способ управления скоростным режимом электроприводов
Для устранения указанного недостатка разработан упомянутый выше способ управления электроприводами с формированием сигнала на замедление в момент захвата. Он обеспечивает захват металла в режиме ускорения независимо от точности определения положения металла на рольганге. Это поясняют диаграммы задания скорости, представленные на рис. 5. Предлагается осуществлять ускорение электропривода вплоть до захвата металла валками независимо от времени начала предразгона (моменты tʹ 1 , t 1 , tʺ 1 ). В этом случае момент начала торможения t 2 совпадает с моментом захвата металла валками. В результате негативные последствия от более раннего либо позднего ускорений будут сведены к минимуму.
Разгон с постоянным ускорением (время разгона и конечная скорость изменяются)
Торможение с постоянным ускорением (время торможения const)
Разгон до установившейся скорости прокатки
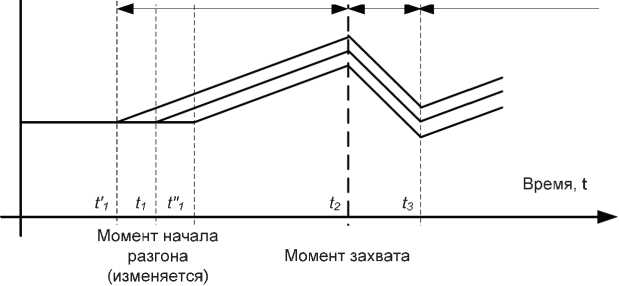
Рис. 5. Задание скорости электропривода клети согласно разработанному «инвариантному» способу управления
Задание на скорость
3. Теоретические и экспериментальные исследования
На рис. 6 показаны временные зависимости, полученные при формировании сигналов задания согласно разработанному способу. Для этого использована имитационная модель электропривода клети стана 5000, рассмотренная в [24]. Захват металла валками (окно 2) происходит
Расчет и конструирование
в момент времени t 2 = 2,25 с. В этот же момент начинается торможение электропривода (окно 1). Как видно из графиков, благодаря этому устраняется влияние точности определения положения металла на рольганге на переходный процесс момента при захвате. Перерегулирование момента остается на одном уровне, практически исключаются его колебания.
Преимущество предложенного способа заключается в том, что ошибка в определении положения «головы» раската относительно клети не влияет на перерегулирование момента при захвате. Данное отличие объясняется тем, что момент окончания предразгона (и начала торможения) всегда определяется без ошибки по усилию прокатки.
На рис. 3, б представлены осциллограммы, полученные на стане 5000 при опытно-промышленных испытаниях алгоритма, реализующего разработанный способ. Захват металла валками происходит в режиме ускорения при замкнутых угловых зазорах в шпинделях. Это подтверждают положительные приращения моментов М в и М дв в моменты времени t 1 , t 2 . Непосредственно после захвата в интервале t 3– t 4, выделенном пунктирными линиями, осуществляется принудительное замедление электропривода.
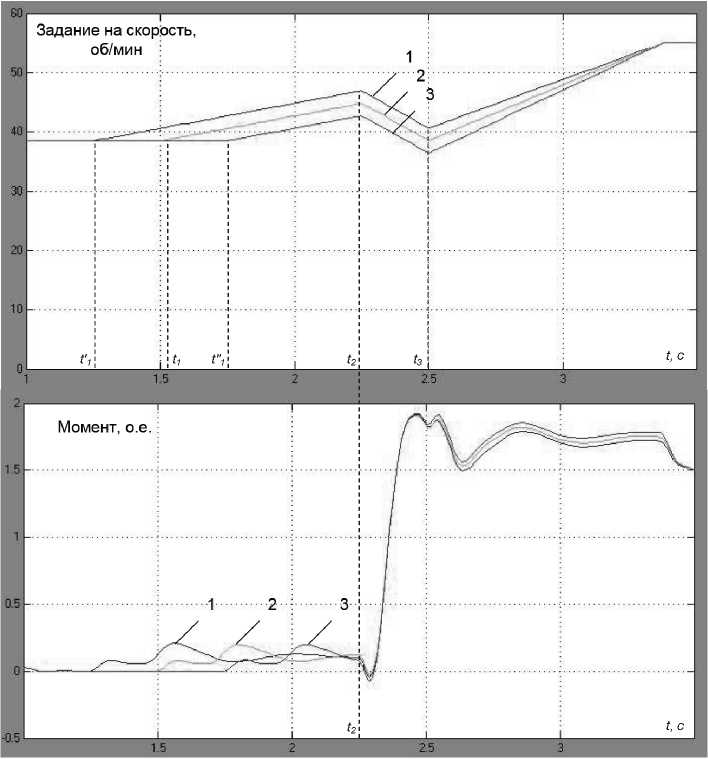
Рис. 6. Расчетные временные зависимости момента двигателя при моделировании разработанного способа
Динамические приращения момента представлены в столбцах таблицы с обозначением «рис. 3, б». Результаты их сравнения с показателями, соответствующими режиму, представленному на рис. 3, а, позволили сделать следующие выводы:
-
1. Кратность ударного момента на валу шпинделя при реализации разработанного алгоритма k Вм = 1,67, в то время как при исходном алгоритме k Вм = 2,2. Таким образом, максимальный динамический момент уменьшился в 1,3 раза.
-
2. Аналогичная кратность электромагнитного момента двигателя снижается в 1,13 раза от k Вм = 1,5 до k Вм = 1,33. Этот вывод не является полностью корректным, так как на рис. 3, а момент двигателя выходит на уровень ограничения.
-
3. Затухание колебаний происходит за меньшее время, с меньшей амплитудой. При этом количество колебаний момента уменьшилось.
Представленные результаты подтверждают техническую эффективность разработанного «инвариантного» способа ограничения динамического момента.
Заключение
Разработан способ управления скоростными режимами электроприводов клети и рольгангов толстолистового прокатного стана, согласно которому обеспечиваются:
-
– предварительное ускорение электроприводов перед захватом металла валками;
-
– снижение скорости с заданным отрицательным ускорением после захвата;
-
– формирование заданной тахограммы независимо от точности фиксации положения раската на рольганге.
Способ позволяет добиться снижения динамического момента двигателя и упругого момента на валу шпинделя. Это обеспечивается за счет ограничения составляющей момента, вызванной замыканием углового зазора в шпиндельных соединениях, и составляющей, обусловленной упругими свойствами валопроводов клети.
Теоретически и экспериментально доказано, что при реализации способа достигается существенное ограничение моментов на валах шпинделей и электромагнитных моментов двигателей валков. Уменьшение динамических нагрузок способствует снижению аварийности оборудования главных линий прокатной клети.
Разработанный способ управления рекомендуется для внедрения в электроприводах прокатных станов, работающих с ударным приложением нагрузки. Поскольку все предложенные операции реализуются в алгоритмах АСУ второго уровня, род тока электропривода и принцип построения системы регулирования скорости не являются ограничениями для применения способа.
Список литературы Снижение динамического момента в главной линии прокатной клети толстолистового стана
- Примеры инновационных разработок фирмы VAI в области технологии горячей прокатки / Т. Нийхьюс, А. Сейлингер, Т. Кирнер и др. // Черные металлы. - 2005, № 7-8. - С. 129-135.
- Bass, G.V. Minimum tension control in finishing train of hot strip mills / G.V. Bass // Iron and steel Engineer. - 1987. - № 11. - P. 48-52.
- Bhowal, P. Modeling and Simulation of Hidraulic Gap Control System in a Hot Strip Mill / P. Bhowal, S.K. Mukherjee // ISIJ International. - 1996. - Vol. 36, № 5. - P. 553-562.
- Tanimoto, S. New tension measurement and control system in hot strip finishing mill / S. Tanimoto, Y. Hayashi, M. Saito // Meas. And Contr. Instrum. Iron and Steel Ind. Prod 5-th Process Technical Congress, Detroit. Werrendale, Pa. - 1985. - P. 147-154.
- Hamada, K. Finishing mill tension control system in the Mizushima hot strip mill / K. Hamada, S. Ueki, M. Shitomi // Kawasaki steel technical report. - 1985. - № 11. - P. 35-43.
- Wright, J. Mill drive system to minimize torque amplification / J. Wright // Iron and Steel Engineer. - 1976, July. - Р. 56-60.
- Мещеряков, В.Н. Разработка способа снижения динамических нагрузок электропривода прокатной клети стана холодной прокатки / В.Н. Мещеряков, В.М. Толчеев // Электротехнические системы и комплексы. - 2015. - № 3. - С. 14-19.
- Мещеряков, В.Н. Регулирование натяжения полосы в чистовой группе непрерывного широкополосного стана горячей прокатки по косвенному принципу / В.Н. Мещеряков, Е.Е. Диденко // Электротехнические системы и комплексы. - 2014. - № 1 (22). - С. 40-43.
- Мещеряков, В.Н. Математическое описание механической системы двух смежных клетей чистовой группы непрерывного стана горячей прокатки / В.Н. Мещеряков, Е.Е. Диденко // Электротехнические комплексы и системы управления. - 2010. - № 3. - С. 8-13.
- Speed and Load Modes of Rolling Hollow Billet at the Wide-Strip Rolling Mill / A.A. Radionov, A.S. Karandaev, V.R. Khramshin et al. // Proceedings of 2014 International Conference on Mechanical Engineering, Automation and Control Systems (MEACS). - 2014.
- DOI: 10.1109/MEACS.2014.6986841
- System for Speed Mode Control of the Electric Drives of the Continuous Train of the Hot-Rolling Mill / V.R. Khramshin, A.S. Evdokimov, G.P. Kornilov et al. // Proceedings of the 2015 International Siberian Conference on Control and Communications (SIBCON-2015). - Omsk: Omsk State Technical University. - 2015.
- DOI: 10.1109/SIBCON.2015.7147264
- Algorithm of No-Pull Control in the Continuous Mill Train / V.R. Khramshin, S.A. Evdokimov, А.S. Karandaev, I.Yu. Andryushin, A.G. Shubin // Proceedings of the 2015 International Siberian Conference on Control and Communications (SIBCON-2015). - Omsk: Omsk State Technical University. - 2015.
- DOI: 10.1109/SIBCON.2015.7147263
- Hot strip mill nonlinear torsional vibration with multi-stand coupling/ Xiaobin Fan, Yong Zang, Feng Wang, Ke Jin // Jve International Ltd. Journal Of Vibroengineering. - 2015. - Vol. 17. - P. 1623-1633.
- Mackel, Jerry Maintenance and quality related monitoring of rolling mill main drives / Jerry Mackel, Martin Fieweger, Andreas Asch - Vanderbijlpark, South-Africa: Saruc, 2002. - 14 p.
- Asch, A. The influence of main drive design on economical operation of a wide hot strip mill / A. Asch, C. Aigner // Proceedings of the SEAISI Singapore Conference. - 2001.
- Reduction of the Dynamic Loads in the Universal Stands of a Rolling Mill / V.R. Khramshin, A.S. Karandaev, S.A. Evdokimov et al. // Metallurgist. - 2015. - Vol. 59. № 3-4. - P. 315-323. 15
- DOI: 10.1007/s11015-015-0103-8
- Constraining the Dynamic Torque of a Rolling Mill Stand Drive / V.R. Khramshin, V.R. Gasiyarov, A.S. Karandaev et al. // Вестник ЮУрГУ. Серия «Энергетика». - 2018. - Vol. 18, № 1. - P. 101-111.
- DOI: 10.14529/power180109
- Krot, P.V. Hot rolling mill drive train dynamics: torsional vibration control and backlash diagnostics / P.V. Krot // Millennium Steel China. Annual Issue. - 2009. - P. 91-95.
- Krot, P. Nonlinear vibrations and backlashes diagnostics in the rolling mills drive trains / P. Krot // Proceedings of the 6th EUROMECH Nonlinear Dynamics Conference (ENOC '08). Saint Petersburg - 2008. - P. 26-30.
- Progress in Equipment Diagnosis Techniques at Kawasaki Steel Corporation / Akira Ichihara, Satoshi Kasai, Hiromasa Yamamoto and others // Kawasaki Steel Giho. - 1990. - № 22. - P. 69-73.
- Gudehus, H. Measurement and calculation of rolling torque in the biting phase for hot rolling / H. Gudehus // Stahl und Eisen. - 1983. - № 15/16. - P. 15-24.
- Артюх, В.Г. Основы защиты металлургических машин от поломок / В.Г. Артюх. - Мариуполь: Издат. группа «Университет», 2015. - 288 с.
- Салганик, В.М. Современные технологии производства листового проката / В.М. Салганик // Инновационные технологии в металлургии и машиностроении: материалы 6-й международной молодежной научно-практической конференции «Инновационные технологии в металлургии и машиностроении. Уральская научно-педагогическая школа имени профессора А.Ф. Головина». - Екатеринбург: Изд-во Урал. ун-та, 2012. - С. 353-358.
- Mathematical Modeling of Mechatronics System "Hydraulic Screwdown Mechanism - Electric Drive of Rolling Mill Stand" / A.A. Radionov, V.R. Gasiyarov, S.N. Baskov et al. // 9th International Conference on Mechatronics and Manufacturing (ICMM 2018). IOP Conf. Series: Materials Science and Engineering. - 2018. - Vol. 361. - № 012020.
- DOI: 10.1088/1757-899X/361/1/012020