Сокращение выбросов ПАУ и защита анодных штырей от коррозии при формировании вторичного самообжигающегося анода
Автор: Сторожев Ю.И., Леонов В.В., Абкарян А.К.
Журнал: Журнал Сибирского федерального университета. Серия: Техника и технологии @technologies-sfu
Статья в выпуске: 5 т.5, 2012 года.
Бесплатный доступ
Для уменьшения выбросов смолистых веществ при формировании вторичного анода и защиты анодных штырей от коррозии серой предложено применять прессованные необожженные брикеты из анодной массы с низким содержанием связующего с добавкой измельченного алюминия. На прессовом оборудовании изготовлены брикеты цилиндрической формы, в том числе с размерами, сопоставимыми с размерами гранул подштыревой анодной массы. Небольшие размеры брикетов позволяют обеспечить их механизированную загрузку в подштыревые лунки с помощью бункера-дозатора, используемого на производстве. Для изготовления брикетов в промышленном масштабе предложено применить пресс экструдеры. Опробована изоляция поверхности анодных штырей алюминиевой фольгой.
Смолистые вещества, анодная масса, анодные штыри, измельченный алюминий, прессованные брикеты
Короткий адрес: https://sciup.org/146114676
IDR: 146114676
Текст научной статьи Сокращение выбросов ПАУ и защита анодных штырей от коррозии при формировании вторичного самообжигающегося анода
К недостаткам электролизеров Содерберга с верхним токоподводом относятся загрязнение окружающей среды выбросами смолистых веществ и бенз(а)пирена и повышенный износ анодных штырей вследствие коррозии.
Источником выделения и выбросов смолистых веществ и бенз(а)пирена при производстве алюминия является каменноугольный пек, используемый в качестве связующего при получении анодной массы. Эмиссия ПАУ в атмосферу корпуса с поверхности анода и в процессе перестановки штырей составляет 15-20 % от всех ПАУ, образующихся при электролизе алюминия. Наибольшее выделение смолистых веществ связано с операцией по перестановке штырей (рис. 1) в результате поступления подштыревой анодной массы в образовавшуюся лунку после извлечении штыря.
Количество смолистых веществ, выделяющихся в атмосферу корпуса при перестановке анодных штырей, колеблется в зависимости от свойств и состава подштыревой анодной массы, технологического режима работы электролизеров, уровня их эксплуатации и других условий. По данным [1], количество смолистых веществ, выделяющихся на электролизерах с верхним
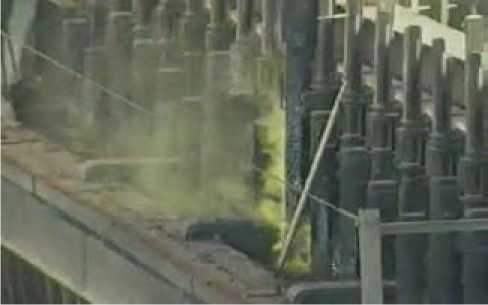
Рис. 1. Интенсивный выброс смолистых веществ во время перестановки штырей токоподводом в атмосферу корпуса, составляет от 2 до 3 кг/т Al, дополнительное количество смолистых выделяется из-за прилипания анодной массы к штырям при их перестановке. При этом фонарные выбросы бенз(а)пирена от электролизного корпуса составляют до 75 % от общего его количества, выделяемого электролизерами.
В практике алюминиевого производства проработано несколько технических решений по сокращению и улавливанию выбросов при перестановке анодных штырей.
-
1. Применение предварительно обожженных и необожженных подштыревых пробок.
-
2. Использование мобильной газоочистной установки.
-
3. Установка стационарного газосборного коллектора с отводом газов в горелочное устройство электролизера.
-
4. Применение заглушек с газоотводящими шлангами, устанавливаемых на место извлеченного штыря на период коксования анодной массы.
-
5. Применение децентрализованной автономной газоочистной установки.
-
6. Использование органической пены для блокирования выбросов из подштыревых лунок.
Однако все эти технические решения не вышли из стадии лабораторных и опытнопромышленных исследований. Наибольшее развитие получили работы по применению подштыревых пробок [2]. В свете вышеизложенного актуальной является разработка экономичного способа сокращения выбросов смолистых веществ во время перестановки штырей. Он реализуется за счет применения предварительно изготовленных углесодержащих пробок из анодной массы с содержанием связующего 18-28 %.
Применение предварительно обожженных пробок при перестановке анодных штырей дает целый ряд технологических и экологических преимуществ:
-
• снижается падение напряжения в аноде;
-
• улучшается токораспределение в аноде;
-
• создаются условия для уменьшения минимального расстояния от низа штыря до подошвы анода;
-
• существенно уменьшаются выбросы смолистых веществ, в том числе канцерогенных ПАУ.
Испытания, проведенные на опытном участке ОАО «РУСАЛ Красноярск», показали [3], что снижение падения напряжения в аноде при использовании предварительно обожженных пробок составило 50-60 мВ, среднее значение коэффициента неравномерности токораспреде-ления по штырям снизилось, по сравнению со свидетелем, на 10-15 %, выбросы смолистых веществ, по экспертным оценкам, уменьшились на 40 %.
Применение предварительно обожженных пробок при перестановке анодных штырей связано с необходимостью организации дополнительного передела по их производству, поэтому представляет интерес применение «зеленых», т.е. необожженных пробок, с низким содержанием связующего.
Важной задачей является защита от коррозии стальной части штыря и, соответственно, увеличение периода их эксплуатации. Интенсивная коррозия происходит при взаимодействии стали с серой и кислородом. Доминирующий вклад в поступление серы в процесс электролиза вносит кокс, составляющий основу анодной массы. Низкая стоимость и большая распространенность высокосернистых нефтяных коксов с содержанием серы 2,0-3,0 % вес. являются основными причинами их широкого применения на алюминиевых заводах. Повышение содержания серы в анодной массе приводит к ряду нежелательных последствий.
В частности, в результате контакта с воздухом на поверхности конусной части штыря, имеющей температуру около 900 оС после извлечения штыря из анода, образуется слой окалины, являющейся диэлектриком. Коррозия усиливается действием сульфатов и сульфидов, образующихся из серы в анодной массе. С образованием окалины изменяются геометрические размеры и форма стальной части штыря. Окалина увеличивает сопротивление контакта между штырем и телом анода, что приводит к механическим напряжениям и появлению трещин, снижает сортность алюминия-сырца, уменьшается срок службы штырей.
Увеличение содержания серы в анодной массе вызывает увеличение скорости износа и сокращение срока службы анодного штыря. Отслоение оксидов и сульфидов железа при замене анодных штырей и попадание их в тело анода приводят к нарушению технологии анода, что увеличивает операционные затраты при производстве алюминия-сырца.
Перспективным направлением защиты анодного штыря от коррозии и повышения срока его службы является разработка способов поверхностного упрочнения рабочей части анодного штыря и применение легирующих добавок в анодную массу для нейтрализации воздействия серы на рабочую поверхность анодного штыря.
Поскольку основная коррозия анодного штыря – это его сульфидирование, то возможны три варианта продления его срока службы:
-
– исключить попадание серы в анодную массу,
-
– сделать штыри из материала, который не взаимодействует с серой,
-
– создать такое покрытие на анодном штыре, которое бы предотвращало сульфидирование штыря.
Одним из способов защиты анодного штыря от коррозии серой является его изоляция алюминиевой фольгой (рис. 2). Перестановка штырей с защитой из алюминия и их работа не оказали влияния на технологическое состояние электролизера: температуру электролита, напряжение анода, величину шума, ФРП, уровень и температуру КПК и другие параметры анода.
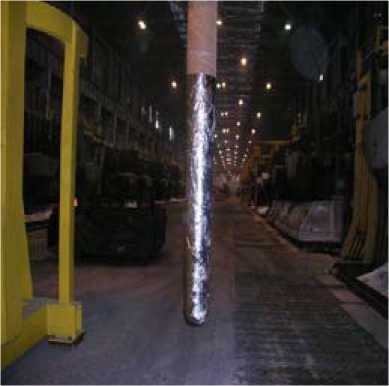
Рис. 2. Штырь, защищенный от коррозии алюминиевой фольгой
Алюминиевая фольга защищает анодный штырь от коррозии, удлиняет срок его службы в 1,5 раза, но ее применение связано с большими трудозатратами, в связи с чем заслуживает внимания газодинамическое напыление на поверхность штыря оксида алюминия высокоскоростным нагретым потоком сжатого воздуха [4].
Другой способ защиты штыря от коррозии – введение измельченного алюминия в виде опилок, гранул, стружки в подштыревую пробку, изготовленную из анодной массы с пониженным содержанием связующего (14-20 % пека). Под действием высокой температуры измельченный алюминий расплавляется и при достаточном количестве обволакивает поверхность опущенного в лунку анодного штыря. При этом уменьшается падение напряжения в контакте анодный штырь–тело анода. Расплавленный алюминий взаимодействует с серой, содержащейся в анодной массе подштыревой пробки, и предохраняет стальную часть анодного штыря от взаимодействия с серой и образования на его поверхности пленки сернистого железа. Алюминий взаимодействует с серой в объеме подштыревой анодной массы по следующей реакции:
2Al + 3S =Al 2 S 3 .
Эта реакция при температурах 700 оС и выше термодинамически вполне возможна [5]. Кроме того, на поверхности штыря расплавленный алюминий может нейтрализовать серу при взаимодействии с сульфидом железа по реакции
2Al + 3FeS =Al 2 S 3 ↑ +3Fe.
В зависимости от содержания серы в анодной массе, согласно рекомендациям [6], измельченный алюминий вводится в брикеты в количестве 0,5-2,5 % от их веса. При этом обеспечивается эффективная нейтрализация серы, содержащейся в анодной массе, и образование защитной алюминиевой пленки на поверхности анодного штыря. Применение подштыревых пробок с низким содержанием связующего в виде брикетов с добавкой в анодную массу измельченного – 534 –
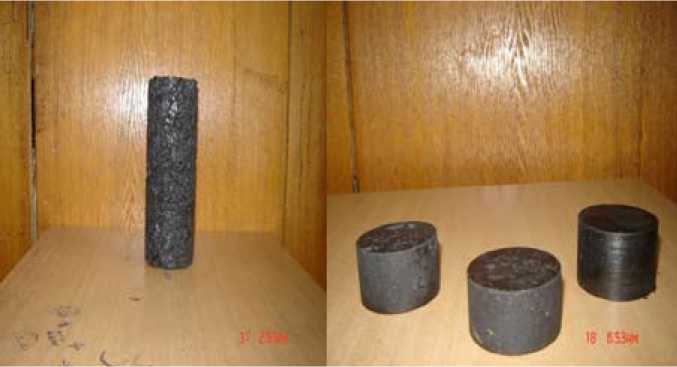
Рис. 3. Образцы подштыревых пробок с добавкой измельченного алюминия алюминия уменьшает падение напряжения в контакте штырь – тело анода, минимизирует уменьшение длины анодного штыря в процессе его работы и одновременно сокращает выброс в атмосферу корпуса смолистых веществ.
Брикетирование подштыревых пробок цилиндрической формы из анодной массы с разным содержанием связующего опробовано на прессах с предварительным подогревом прессовых матриц (рис. 3).
Большие пробки имели диаметр 75 мм, высоту 150-160 мм, вес 1,1 кг, плотность 1500– 1600 кг/м3. Малые пробки имели диаметр 39 мм, высоту 20-25 мм, вес 40 г и диаметр 20 мм, высоту 19-20 мм, вес около 10 г, плотность 1600-1700 кг/м3.
Рассматриваемый способ формирования вторичного анода предлагается реализовать следующим образом. При перестановке анодных штырей в теле анода на верхние горизонты в подштыревую лунку вводят брикеты с помощью бункера-дозатора и крана.
Брикеты необходимых размеров прессуют в пресс-экструдере (рис. 4) из анодной массы с добавкой измельченного алюминия. Под действием высокой температуры (>700 0С) измельченный алюминий расплавляется, химически реагирует с серосодержащими компонентами в объеме анодной массы и на поверхности штыря и образует неактивное соединение Al 2 s з. Присутствие в анодной массе расплавленных частиц алюминия обеспечивает качественное заполнение микротрещин и пор на поверхности подштыревой лунки при значительных колебаниях содержания связующего. Электропроводящие алюминиевые частицы повышают электропроводимость контакта штырь – тело анода и анода в целом. Использованный во вторичном аноде алюминиевый заполнитель частично переходит в конечный продукт.
Предложенный способ формирования вторичного анода, согласно расчетам, позволяет уменьшить расход электроэнергии на 4,8 кВтч/т алюминия и увеличить срок службы анодных штырей в 1,3 раза [6].
Общий экономический эффект с учетом затрат на установку двух пресс-экструдеров и электроэнергию в производстве подштыревых пробок для завода масштаба «РУСАЛ Красно -ярск» оценивается в 55-60 млн руб/год.
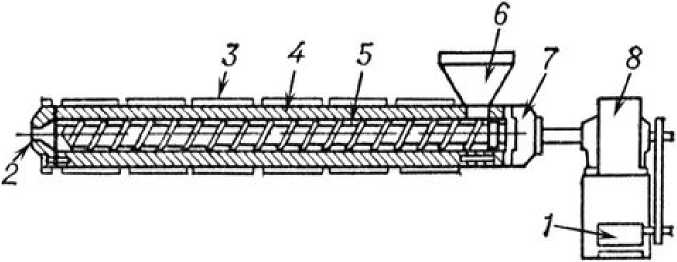
Рис. 4. Схема одношнекового горизонтального экструдера: 1 – двигатель; 2 – сменная экструзионная головка; 3 – нагреватель корпуса; 4 – корпус; 5 – шнек; 6 – загрузочное устройство; 7 – упорный подшипник; 8 – редуктор