Способы совершенствования производства сорбитизированной высокоуглеродистой катанки с целью получения гарантированного комплекса эксплуатационных свойств
Автор: Назаров Д.А.
Журнал: Вестник Южно-Уральского государственного университета. Серия: Металлургия @vestnik-susu-metallurgy
Рубрика: Обработка металлов давлением. Технологии и машины обработки давлением
Статья в выпуске: 1 т.24, 2024 года.
Бесплатный доступ
В статье рассмотрены варианты проведенных модернизаций действующих мелкосортных станов. Проведен анализ действующей технологии охлаждения проката на стане 170 ПАО «ММК». Рассмотрены результаты проведения научно-исследовательской и опытно-конструкторской работы в 2020-2021 годах, которые показали преимущество разработанных в МГТУ им. Г.И. Носова режимов прокатки над действующими на стане режимами.
Сортовой прокат, катанка, сорбитизация, перлит, воздушное охлаждение
Короткий адрес: https://sciup.org/147242994
IDR: 147242994 | DOI: 10.14529/met240103
Текст научной статьи Способы совершенствования производства сорбитизированной высокоуглеродистой катанки с целью получения гарантированного комплекса эксплуатационных свойств
Получение сорбитной структуры в заготовках из сталей с содержанием углерода 0,3–1,0 %, предназначенных для передела в проволоку холодным волочением, производится до настоящего времени патентированием в расплавах солей, и этот процесс в своей технологической сущности оказался столь консервативным, что, несмотря на присущие ему недостатки, остается основным способом получения сорбитной структуры на сталепроволочных заводах, массово производящих канатную, пружинную и струнобетонную проволоку. Разработка путей для решения вопроса получения сорбитизированной катанки с прокатного нагрева началась ещё в 1970-х годах [1, 2]. Несмотря на то, что полностью отойти от патентирования на сталепроволочных заводах вряд ли удастся в силу объективной необходимости проведения рекристаллизации в процессе волочения, отказаться от рекристаллизации после прокатного передела становится возможным. За последние два десятка лет начали появляться и активно внедряться на производстве работающие решения по получению сорбитизированной катанки с прокатного нагрева.
На современных проволочных станах температура раската в конце прокатки составляет 1000-1100 °С. Для управления температурным режимом в последних клетях стана температуру варьируют в более широких пределах с помощью блоков водяного охлаждения – от 750 до 1100 °С. Таким образом, появляется возможность термомеханической обработки с контролируемой прокаткой и охлаждением. Это позволяет улучшить качественные характеристики катанки и повысить технологичность ее на последующем метизном переделе [3].
С совершенствованием данных процессов вырос и комплекс получаемых свойств. На сегодняшний день различными предприятиями предъявляются достаточно высокие требования к катанке, подвергающейся сорбитизации в линии стана. Часть существующих стандартов представлена в табл. 1.
Для осуществления подобной термомеханической прокатки повсеместно проводились и проводятся реконструкции действующих сортопрокатных производств.
Например, в 2006 году была произведена модернизация стана 150 АО «БМК», город
Таблица 1
Требования НД, предъявляемые к параметрам механических свойств и микроструктуре катанки диаметром 5,5 мм из стали марки 70 и 80 после сорбитизации в линии прокатного стана
Table 1
Requirements of regulatory documentation for the parameters of mechanical properties and microstructure of wire rod with a diameter of 5.5 mm made of steel grades 70 and 80 after sorbitization in a rolling mill line
Контролируемые параметры |
Сталь |
Требования НД |
|||
ОАО «БМЗ» |
СЗАО «ММЗ» |
Зарубежные фирмы, потребляющие катанку |
|||
ЗТУ 840-03 2006 |
ТУ У 14-4470-2000 |
Bekaert GS-02-070, GS-02-002; Good Year I. M 180 E 17.12.04 |
Pirelli N.02B.002, N.18.V.001, N.02.В.002 |
||
Временное сопротивление (цель), Н/мм2 |
70 |
970–1130 (1035) |
≤ 1160 |
1050–1180 |
980–1120 |
80 |
1070–1210 (1140) |
≤ 1250 |
1100–1200 (1150) |
1180–1220 |
|
Относительное удлинение, % |
70 |
≥ 11 |
≥ 9 |
– |
– |
80 |
≥ 10 |
≥ 8 |
– |
– |
|
Относительное сужение, % |
70 |
≥ 35 |
≥ 30 |
≥ 40 |
≥ 35 |
80 |
≥ 30 |
≥ 27 |
32–48 |
≥ 35 |
|
Глубина обезуглероженного слоя, max мм (%) |
70–80 |
max 0,1 мм |
max 2 % |
max 2,2 % |
max 2,5 % |
Размер действительного зерна |
70–80 |
Не норм. |
Не норм. |
30–60 мкм |
6–11 балл |
Количество перлита 1-го балла, % |
70–80 |
1–2 балл |
1 балл, ≥ 50 % |
1 балл, ≥ 80 % |
1 балл, ≥ 80 % |
Цементит |
70–80 |
Не замкнут |
Не норм. |
Не норм. |
До типа Б |
Белорецк (входит в Группу «Мечел»). Была проведена реконструкция управления электроприводов линии двухстадийного охлаждения и реконструкция системы цифрового задания скорости и системы индикации скоростей электроприводов клетей с 1-й по 23-ю, модернизация цифрового задания скоростей приводов чистовых блоков, трайбаппаратов и виткоукладчиков стана 150, были автоматизированы рабочие места операторов.
Одной из основных целей реконструкции было обеспечение требуемой температуры катанки на всех стадиях охлаждения, достижение и стабильное обеспечение требуемых механических свойств металла.
Для этого было установлено оборудование управления процессом контролируемого охлаждения катанки в сочетании с параметрами прокатки для прогнозирования достигаемых в результате охлаждения заданных характеристик материала. Оборудование имеет возможность развития положенных в его основу баз данных параметров и характеристик. В связи с тенденцией повышения скорости проката и необходимостью освоения производства сорбитизированной катанки во всем диапазоне размеров поперечного сечения проката была произведена установка 4 вентиляторов с мощностью привода 200 кВт, 3 вентиляторов с мощностью привода 160 кВт, что позволило регулировать скорости охлаждения витков катанки воздухом в широких пределах [4].
В 2006 году была проведена реконструкция стана 150 ОАО «БМЗ – управляющая компания холдинга «БМК», город Жлобин. По аналогии с проволочным станом на заводе Quingdao (Китай) была проведена модернизация хвостовой части стана.
После модернизации новое оборудование хвостовой части позволяет при производстве проката использовать схему комбинированной термомеханической обработки (КТМО) с контролируемой прокаткой и контролируемым охлаждением, включающей линию предварительного охлаждения подката перед блоком с секцией водяного охлаждения раската (до температур 900-950 °С); десятиклетьевой чистовой блок (скорость прокатки до 100 м/с); линию водяного контролируемого охлаждения (до среднемассовых температур 850-950 °С); четырехклетьевой редукционно-калибрующий блок (РКБ) фирмы «Морган» (скорость прокатки до 110 м/с), после которого катанка транспортируется через линию окончательного водяного контролируемого охлаждения, профилемер и виткоукладчик на роликовый транспортер, где осуществляется регулируемое охлаждение воздухом (от 1,0 до 20,0 °С/с) с целью получения необходимых свойств в готовой продукции.
В июне 2019 года на стане 170 ПАО «ММК» была осуществлена реконструкция компанией DANIELI. Одной из целей реконструкции было повышение содержания сорбитизирован-ного перлита в микроструктуре прокатываемой высокоуглеродистой нелегированной стали и получение механических свойств после охлаждения на роликовом конвейере, соответствующих российским стандартам для высокоуглеродистой стали. Для этого были заменены 14 существующих вентиляторов 16 новыми на каждой линии. Мощность вентиляторов – от 132 до 152 кВт.
Несмотря на тот факт, что реконструированная линия была снабжена достаточно мощными вентиляторами и технология производства сорбитизированного проката в линии стана была в определенной степени известна в научном сообществе [5, 6], возникли некоторые затруднения в получении необходимой структуры и свойств готового проката [7].
Для разрешения данных затруднений в рамках научно-исследовательской и опытно-конструкторской работы специалистами ФГБОУ ВО «МГТУ» был проведен комплекс исследований, результатом которых стал цифровой двойник линии воздушного охлаждения стана 170 ПАО «ММК» (ЦД-170) [8]. Одной из основных частей ЦД-170 является адаптированная математическая модель для расчёта кривых охлаждения катанки. Она позволяет рассчитать изменение температуры во времени и построить кривую охлаждения катанки для выявления необходимой скорости охлаждения (попадания в нужный диапазон скоростей охлаждения с целью получения ожидаемой микроструктуры и свойств катанки).
При моделировании учитывался комплекс таких целенаправленно управляющих параметров, как температура катанки при выходе из виткообразователя, степень загрузки двигателя вентилятора, угол открытия заслонки дутьевой системы и скорость секций транспортера линии охлаждения. Основные технологические параметры режима прокатки, включая марку стали, температуру нагрева, скорость прокатки, степень обжатия, предва- рительное охлаждение в водяных коробах, термокинетическую диаграмму охлаждения и т. п., при моделировании являлись исходными данными [9].
Сопоставление действующих на ММК и разработанных в МГТУ с помощью ЦД-170 режимов охлаждения катанки в комиссионных условиях экспериментальных прокаток и последующих испытаниях продемонстрировали высокую степень адекватности работы математической модели.
Суммарно же за время опытных прокаток для проведения металлографических исследований в рамках учебно-научного центра МГТУ было подготовлено и изучено свыше 100 микрошлифов, около 150 образцов для изучения механических свойств.
Схема отбора проб представлена на рис. 1.
В настоящее время по результатам исследования сформирована библиотека шлифов, а также физическая и электронная база исследованных образцов. Накоплен опыт, позволяющий сократить время поиска рациональных режимов для последующих актуальных профилеразмеров проката.
Наиболее показательными являются испытания, проведенные на образцах, прокатанных 03.12.2021. Эксперимент проводился на катанке диаметром 6,5 мм из стали марки 75. Замеры проводились на обеих нитках линии воздушного охлаждения. Результаты испытаний, проведенных в лаборатории МГТУ им. Г.И. Носова, представлены на рис. 2 и в табл. 2.
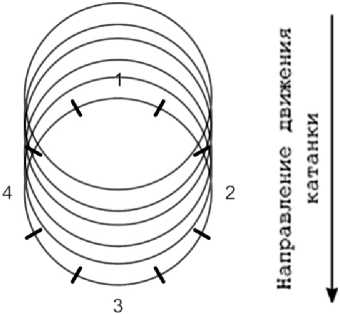
Рис. 1. Схема отбора проб: 1 – положение 0°; 2 – положение 90°; 3 – положение 180°; 4 – положение 270°
Fig. 1. Sampling scheme: 1 – position 0°; 2 – position 90°;
3 – position 180°; 4 – position 270°
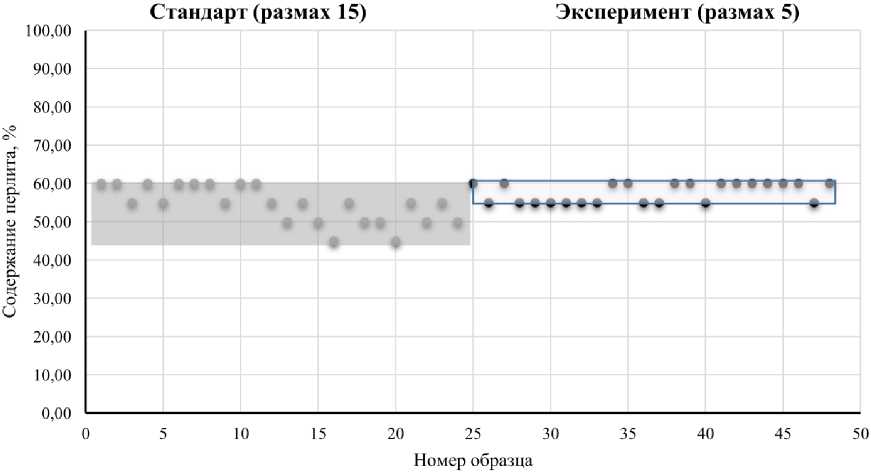
Рис. 2. Результаты металлографических испытаний катанки диаметром 6,5 мм из стали марки 75
Fig. 2. Results of metallographic tests of wire rod 6.5 mm diameter made of grade 75 steel
Таблица 2
Сравнение стандартного и экспериментального режимов по выполнению требований равномерности по величине временного сопротивления
Comparison of standard and experimental modes for meeting the requirements of uniformity in terms of tensile strength
Table 2
Линия и режим |
Часть бунта |
Положение пробы в витке, ° |
Механические свойства |
Разбег временного соп |
ротивления |
|||
Временное сопротивление σв, Н/мм² |
Относительное сужение ψ, % |
Относительное удлинение δ 10 , % |
по витку |
по мотку |
по плавке |
|||
≤ 1180 |
– |
– |
≤ 40 |
≤ 50 |
≤ 60 |
|||
Стандартный режим, линия А |
задний конец |
0 |
1161,69 |
41,54 |
11,70 |
31,48 |
99,85 |
103,09 |
90 |
1130,21 |
42,12 |
8,81 |
|||||
180 |
1147,12 |
43,75 |
12,85 |
|||||
270 |
1148,45 |
– |
6,42 |
|||||
середина |
0 |
1101,09 |
45,24 |
12,07 |
29,81 |
|||
90 |
1099,24 |
47,27 |
11,35 |
|||||
180 |
1114,12 |
– |
7,16 |
|||||
270 |
1129,05 |
44,78 |
7,92 |
|||||
передний конец |
0 |
1159,81 |
43,29 |
12,08 |
72,44 |
|||
90 |
1174,42 |
– |
6,34 |
|||||
180 |
1199,09 |
– |
7,12 |
|||||
270 |
1126,65 |
44,44 |
11,79 |
|||||
Стандартный режим, линия В |
задний конец |
0 |
1152,01 |
45,01 |
12,38 |
80,37 |
85,30 |
|
90 |
1176,37 |
43,40 |
11,76 |
|||||
180 |
1096,00 |
44,55 |
12,35 |
|||||
270 |
1144,08 |
43,40 |
8,19 |
|||||
середина |
0 |
1119,29 |
45,47 |
10,06 |
18,93 |
|||
90 |
1126,37 |
43,17 |
12,09 |
|||||
180 |
1108,62 |
48,82 |
12,32 |
|||||
270 |
1127,55 |
46,82 |
9,09 |
|||||
передний конец |
0 |
1111,64 |
45,47 |
11,71 |
69,66 |
|||
90 |
1138,23 |
– |
5,78 |
|||||
180 |
1169,80 |
– |
7,21 |
|||||
270 |
1181,30 |
43,17 |
6,57 |
|||||
Предлагаемый режим, линия А |
задний конец |
0 |
1142,38 |
46,93 |
13,11 |
14,78 |
69,03 |
70,81 |
90 |
1141,89 |
46,26 |
11,30 |
|||||
180 |
1145,34 |
44,90 |
12,27 |
|||||
270 |
1156,67 |
– |
7,22 |
|||||
середина |
0 |
1131,36 |
45,47 |
12,05 |
24,12 |
|||
90 |
1121,39 |
– |
5,39 |
|||||
180 |
1132,33 |
44,33 |
11,74 |
|||||
270 |
1145,51 |
44,33 |
10,75 |
|||||
передний конец |
0 |
1158,78 |
42,47 |
10,90 |
38,13 |
|||
90 |
1168,85 |
43,87 |
5,62 |
|||||
180 |
1152,29 |
43,52 |
11,06 |
|||||
270 |
1190,42 |
42,94 |
7,91 |
|||||
Предлагаемый режим, линия В |
задний конец |
0 |
1152,92 |
45,58 |
10,13 |
39,28 |
49,83 |
|
90 |
1155,11 |
45,58 |
7,37 |
|||||
180 |
1187,50 |
45,58 |
12,43 |
|||||
270 |
1192,20 |
– |
7,51 |
|||||
середина |
0 |
1148,23 |
46,60 |
5,31 |
34,15 |
|||
90 |
1142,37 |
46,60 |
10,87 |
|||||
180 |
1176,52 |
46,60 |
10,76 |
|||||
270 |
1174,04 |
– |
12,02 |
|||||
передний конец |
0 |
1165,03 |
46,26 |
11,71 |
19,08 |
|||
90 |
1184,11 |
46,93 |
10,52 |
|||||
180 |
1165,78 |
45,24 |
6,07 |
|||||
270 |
1178,00 |
– |
7,17 |
Для экспериментальных режимов удалось повысить содержание перлита 1–2 балла не менее чем на 5 %, тем самым в большей степени удовлетворить требованиям нормативной документации.
Из полученных данных видно, что стандартный режим обеспечивает равномерность по витку в 3 случаях из 6 (50 %), в то время как экспериментальный режим обеспечивает равномерность в 6 случаях из 6 (100 %). Для стандартного режима не достигается равномерность ни по мотку, ни по плавке (разница между полученными значениями и требуемыми больше 30 Н/мм²), в то время как экспериментальный режим обеспечивает равномерность по мотку в 1 случае и близкие (разница между полученными значениями и требуемыми составляет ~ 10 Н/мм²) к требуемым значениям во втором случае по мотку и плавке.
Данные показатели характеристик качества сорбитизированной катанки являются результатом проведенного комплексного вариационного моделирования с применением разработанного цифрового двойника линии ускоренного охлаждения стана 170.
Данного результата удалось достичь только с помощью настройки существующего оборудования. Для достижения более высокого комплекса механических свойств может потребоваться модернизация действующей линии стана 170.
При дальнейшем переделе на ОАО «ММК-Метиз» проволока, изготовленная из катанки по технологии МГТУ им. Г.И. Носова, показала меньшие значения стандартного отклонения по временному сопротивлению разрыву и повышенный комплекс прочностных и пластических свойств (запас по количеству перегибов) по сравнению с проволокой, изготовленной по стандартной технологии.
Выводы
Проанализировав историю развития идеи получения высокоуглеродистой катанки с прокатного нагрева, можно сделать вывод, что на протяжении многих лет металлурги пытаются решить данную проблему. На сегодняшний день на ряде предприятий удалось достичь требуемых показателей механических свойств и получить нужную микроструктуру в прокате. Для ряда станов, которые будут проходить модернизацию в ближайшее время, для получения сорбитизи-рованной катанки с прокатного нагрева рациональным видится путь установки более мощных вентиляторов для расширения границ варьирования скоростей охлаждения и разработка современных, комплексных решений автоматизации и цифровизации, позволяющих как управлять технологическим процессом, так и разрабатывать новые режимы производства.
Список литературы Способы совершенствования производства сорбитизированной высокоуглеродистой катанки с целью получения гарантированного комплекса эксплуатационных свойств
- Шаповалов С.И., Алимов В.И., Эстрин Ю.С. Высокоуглеродистая катанка, сорбитизированная с прокатного нагрева, и арматурная проволока из нее // Сталь. 1974. № 6. С. 567-569.
- Шаповалов С.И., Алимов В.И., Эстрин Ю.С. Сорбитизация углеродистой катанки в потоке непрерывного прокатного стана // Проблемы производства черных металлов: сб. 1974. С. 143-149.
- Особенности термомеханической обработки высокоуглеродистой катанки в потоке высокоскоростного проволочного стана 150 ОАО "БМЗ" / В.А. Луценко, П.А. Бобков, О.М. Кириленко, О.В. Луценко // Литье и металлургия. 2012. № 3 (66). С. 172-175. EDN: SJCCIF
- Фомочкина А.А., Клековкин А.А., Евтеев Е.А. Оптимизация технологических параметров производства пружинной проволоки из сорбитизированной катанки // Сталь. 2007. № 7. С. 99-100. EDN: IBCTNB
- Опыт производства круглого сортового проката из стали марки 60С2ХА с повышенными требованиями к глубине обезуглероженного слоя в условиях ОАО "ММК" / О.Н. Тулупов, А.Б. Моллер, С.А. Левандовский [и др.] // Вестник Магнитогорского государственного технического университета им. Г.И. Носова. 2015. № 2 (50). С. 28-36. EDN: TXHUAP
- Особенности влияния термомеханической обработки в потоке стана 150 Белорусского металлургического завода на качественные характеристики высокоуглеродистой катанки / В.А. Луценко, М.А. Муриков, П.А. Бобков [и др.] // Литье и металлургия. 2012. № 4 (68). С. 110-114. EDN: SEXFNB
- Оценка перспективы и определение стратегии освоения технологии производства сорбитизированной катанки согласно требованиям ОАО "ММК-Метиз" в существующих условиях стана 170 на основе создания Цифрового двойника реконструированных линий ускоренного охлаждения. Отчет по НИОКР № 242586 от 16.03.2020 г.
- Способы повышения качества производимой продукции в условиях стана 170 ПАО "ММК" / Н.А. Баранов, О.Н. Тулупов, А.Б. Моллер [и др.] // Моделирование и развитие процессов ОМД. 2022. № 1 (34). С. 4-8. EDN: FQPNTT
- Моделирование процесса воздушного охлаждения катанки / М.Е. Ишметьев, О.Н. Тулупов, А.Б. Моллер [и др.] // Моделирование и развитие процессов ОМД. 2022. № 1 (34). С. 9-13. EDN: CXOCZS