Статистический подход к оптимизации сил крепежей при сборке авиационных конструкций
Автор: Зайцева Н.И.
Журнал: Международный журнал гуманитарных и естественных наук @intjournal
Рубрика: Технические науки
Статья в выпуске: 10-1 (97), 2024 года.
Бесплатный доступ
В данной статье рассматривается оптимизация процесса сборки деформируемых деталей с применением крепежных элементов в авиастроении. Основное внимание уделяется формулировке контактной задачи, описывающей соединение деталей с учетом случайных отклонений сборочного процесса. Предложенный метод основан на математическом моделировании и использовании подхода Монте-Карло для оценки необходимых сил крепежей, обеспечивающих сведение результирующих зазоров до заданных значений с заданной вероятностью. В качестве практического примера проанализирован процесс присоединения укрепляющих накладок к крылу самолета. Результаты тестирования различных статистических оценок сил позволяют выбрать оптимальный набор значений для сил в крепежах, что способствует повышению качества сборки и увеличению долговечности конструкции.
Процесс сборки, крепежи, начальный зазор, деформируемые конструкции, контактная задача
Короткий адрес: https://sciup.org/170206843
IDR: 170206843 | DOI: 10.24412/2500-1000-2024-10-1-159-164
Текст научной статьи Статистический подход к оптимизации сил крепежей при сборке авиационных конструкций
Одним из основных способов сборки деталей в авиастроении является крепежное соединение. Отдельные детали закрепляются на сборочном стенде и соединяются с помощью установки крепежей в заранее просверленные отверстия. Крепежи прижимают детали друг к другу и сводят зазор между соединяемыми деталями. Поскольку эта операция является достаточно времязатратной, оптимизация этого процесса относительно количества, расположения и типа используемых крепежей может значительно снизить затраты на сборочный процесс. Самым удобным на данный момент подходом к оптимизации сборочных процессов является математическое моделирование, поэтому данная статья рассматривает существующие методы моделирования сборочного процесса с использованием крепежей и предлагает метод анализа и оптимизации процесса крепежного соединения деталей применительно к авиастроительной области.
Математическое моделирование позволяет снизить затраты на проверку строгих требований к качеству сборки и определение наиболее оптимальных технологий сборки. Однако, для получения надежных результатов необходимо проводить моделирование с учетом специфики сборки конструкций в авиастроении.
Одной из особенностей процесса сборки в авиастроении является то, что собираемые детали представляют собой многокомпонентные и гибкие конструкции. Процессы сборки состоят из нескольких этапов, и они в большой степени подвержены вариациям сборки, возникающим из-за отклонений при изготовлении деталей и в процессе позиционирования и скрепления деталей. Для учета этих отклонений используется так называемое моделирование и анализ вариаций сборки.
На качество в процессах сборки самолетов влияют различные факторы, включая вариации формы деталей и высокую гибкость отдельных компонентов [1]. В области вариационного моделирования были разработаны специализированные методы моделирования сборочных процессов, учитывающие как отклонения отдельных деталей, так и вариаций самого сборочного процесса. Традиционный метод Монте-Карло (Direct Monte-Karlo, DMC) [2] основан на том, что для большого набора случайных отклонений проводят моделирование процесса сборки с помощью конечно-элементного анализа. Данный подход достаточно универсален [3], однако, для сложных конструкций этот метод становится чрезвычайно время затратным и не позволяет с достаточной точностью проводить оптимизацию отдельных аспектов сборочного про- цесса. Другая группа методов, основанная на методе коэффициентов влияния (Method of Influence Coefficients, MIC) [4], направленном на сокращение времени вычислений путем линеаризации задачи контакта. Это ускоряет вычисления, но снижает точность моделирования контактного взаимодействия [5]. В [6] предложена модификация МКЭ на основе редуцирования матрицы жёсткости и сведения контактной задачи к задаче квадратичного программирования. Использование этого подхода к моделированию сборочного процесса в авиастроении позволяет получить точное решение относительно перемещения деформируемых деталей в процессе сборки. Дополнительно, для данного подхода разработаны специальные численные методы [7], позволяющие существенно снизить время расчётов.
Особенности сборки деформируемых деталей с помощью крепежей
Отклонения формы и размера собираемых деталей и случайные отклонения позиционирования деталей приводят к тому, что до установки крепежных элементов между деталями образуется ненулевой начальный зазор. Поскольку источник этих зазоров – это случайные отклонения, то и результирующие зазоры имеют случайный характер.
Установка крепежей призвана свести эти зазоры до минимума, учитывая возможную вариативность этих зазоров. Результирующие зазоры между деталями, остающееся после установке крепежей, могут снизить качество сборки и повлиять на усталостную долговечность самолета. На практике на результирующие зазоры между деталями накладывают где х - это вектор перемещений деталей в зоне стыка, К - редуцированная матрица жесткости, f - вектор, содержащий силы от крепежных элементов, gres - результирующий зазор между деталями после установки крепежей, [5] у - вектор, определяющий ограничения на зазор в местах установки крепежей: это вектор равен 5 в тех узлах, где установлены крепежи, и равен +^ во всех других узлах.
ограничения в виде допуска: эти зазоры необходимо свести до какого-то небольшого заданного значения.
Для того, чтобы свести зазоры, установленные крепежные элементы прикладывают заданную сжимающую силу, которая зависит от типа и технологии используемого крепежа. В ответ на эту силу и на возникающее контактное взаимодействие в деталях появляются ответные сборочные силы и, соответственно, сборочные напряжения. Большие сборочные напряжения являются рискованными, так как могут привести к образованию трещин и снижению прочности материала, что критично для безопасности использования самолета в полете. По этой причине, при установке крепежей требуется приложить минимальную сжимающую силу. Вместе с тем, эта сила должна гарантировать сведение зазора между деталями.
Таким образом, в процессе разработки сборочного процесса с крепежным соединением возникает следующая задача: необходимо оценить минимальные силы, которые нужно приложить в крепежных элементах для того, чтобы результирующие зазоры между соединяемыми деталями не превышали заданного допуска.
Оценка сил в крепежных элементах
Подход, предложенный в [6], позволяет сформулировать контактную задачу, описывающую процесс соединения деформируемых деталей с ограничением на зазор в местах установки крепежей, в виде решения задачи следующего вида [8]:
min (—хтК х — fTx ), 0< g™s <[%\2 J )
Результирующий зазор вычисляется как gres = gmit — Атх, где gmit - начальный зазор между деталями, А - матрица, определяющая контактные пары узлов. Решение задачи (1) в двойственной постановке позволяет через использование множителей Лагранжа получить значения сил f в крепежах, которые гарантируют сведение зазора в местах установки крепежей до 5 мм. На рисунке 1 приведена соответствующая схема моделирования соединения деталей.
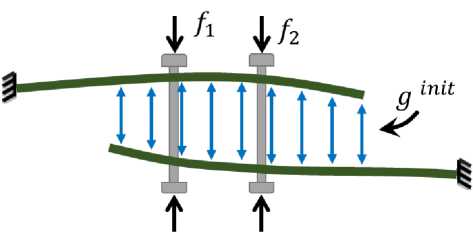
(а) до установки крепежей
Рис. 1. Схематичное предствление соединения деталей
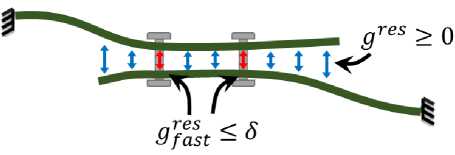
(б) после установки крепежей
В данной постановке случайные отклонения задаются в виде начального зазора. Учитывая случайность результирующих зазоров, для нахождения требуемых сил предлагается использовать подход Монте-Карло, то есть проводить серию расчётов для большого числа сгенерированных начальных зазоров. Методы моделирования начальных зазоров на основе модели случайного поля предложены в [9].
В результате серийных расчётов для каждого i-ого крепежа получается итоговая выборка значений сил F1 = {/Д)к_1 ,, где ^ — число расчётов (соответствует числу сгенерированных начальных зазоров). Для того, чтобы оценить оптимальные силы, предлагается использовать статистические оценки характеристик этой выборки – можно рассмотреть среднее, разные квантили и максимальное значение получившегося распределения.
От выбора конкретной статистической оценки зависит величина получаемых сил и, соответственно, качество соединения деталей. Для сравнения эффективности и подбора нужной оценки предлагается проводить тестирование получаемых наборов сил. В качестве оценки качества соединения деталей можно оценивать статистическую кривую
(функции распределения) для результирующих зазоров, получаемых при использовании тестируемого набора сил. По получаемым статистическим кривым и заданным требованиям допуска на результирующий зазор выбирается наиболее оптимальная статистическая оценка выборки, соответственно, оптимальный набор значений сил в крепежах. В следуем разделе данной стати применение предлагаемой методики иллюстрируется на конкретном практическом примере.
Применение предложенного метода для процесса сборки
Для иллюстрации эффективности предлагаемой методики рассматривается одна стадия процесса сборки самолета: процесс присоединения к крылу укрепляющих накладок. На Рисунке 2 приведены общий вид модели и конкретная зона стыка с рассматриваемой расстановкой крепежей. Крепежи в этом процесса разделены на 5 групп по конкретным типам (на рисунке отличаются цветами), каждая группа крепежей характеризуется своей сжимающей силой f\..., f5. Необходимо оценить требуемые силы для каждой группы крепежей, чтобы снизить результирующий зазор до Л = 0.2 мм с вероятностью Р = 95%.
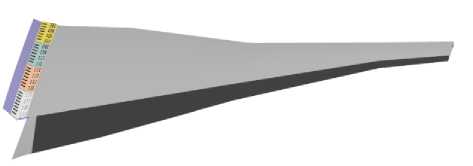
(а) общий вид
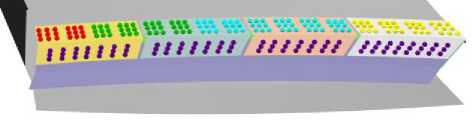
(б) расстановка крепежей
Рис. 2. Модель исследуемого соединения
Для рассматриваемого процесса сборки на основе модели случайного поля была сгенерирована выборка случайных начальных за- зоров (пример такого зазора приведен на рисунке 3(а)). Для каждого начального зазора проводилось решения задачи (1). На рисун- ке 3(б) приведен пример результирующего зазора, соответствующего представленному начального зазору. Из решения задач также были получены силы, сводящие результирующий зазор до 3 = 0.01 мм в местах установ- ки крепежей. Поскольку с рассматриваемой постановке крепежи разделены на группы, внутри каждой группы выбиралось максимальное значений силы.
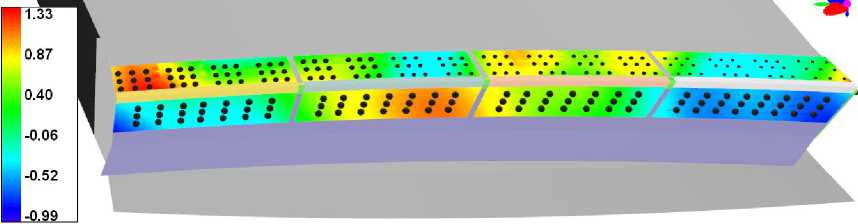
(а) Начальный зазор до установки крепежей и контактного взаимодействия
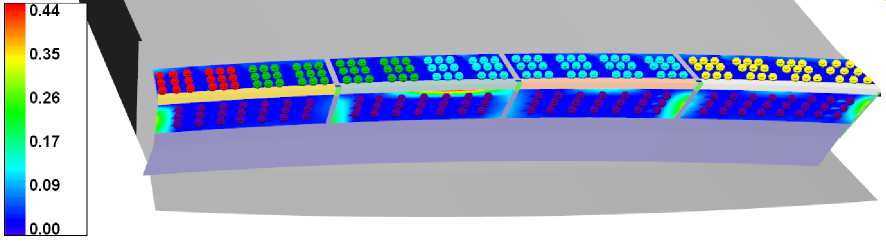
(б) Результирующий зазор после установки крепежей
Рис. 3. Моделирование процесса присоединения накладок к крылу
По итогам расчётов для N = 200 начальных зазоров, получились выборки F1,., F5 для каждой группы сил, где Fl = {/i, ■ ■■,/ }• В качестве статистических оценок для этого примера будут рассматриваться среднее значение, 95-й квантиль и максимальное значение выборки. Пример полученных выборок для двух групп приведены на Рисунке 4, где отображены гистограммы для выборок, а также оценки (среднее, 95-й квантиль и максимум). Полученные оценки для всех групп крепежей приведены в таблице 1.
Для каждой оценки проводилось тестирование полученного набора сил: проводился анализ сборочного процесса на втором наборе сгенерированных начальных зазоров, по итогам которого строились распределения значений результирующего зазора (статистические кривые) 5(x) = Prob {gres < x}, x G R. Полученные кривые приведены на рисунке 5.
По полученным данным видно, что под требование уменьшить результирующий зазор до △ = 0.2 мм с вероятностью P = 95% подходят два набора сил (оценка с помощью 95ого квантиля и по максимальным значениям), а оценка с помощью средних значений не дает нужного качества соединения деталей. Соответственно, если выбирать минимальные силы из исследованных, то подходящим набором будут значения, оцененные с помощью 95-ого квантиля. В дальнейшем для уточнения оценок можно провести дополнительные исследования и найти также минимальный уровень квантиля, который будет подходить заданным требованиям.
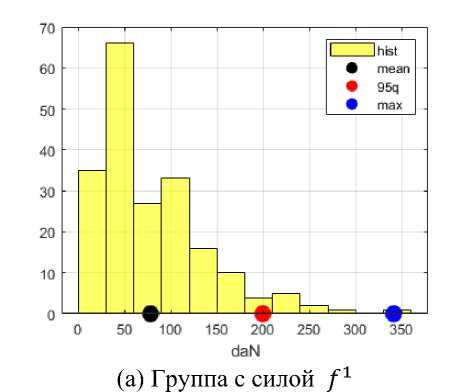
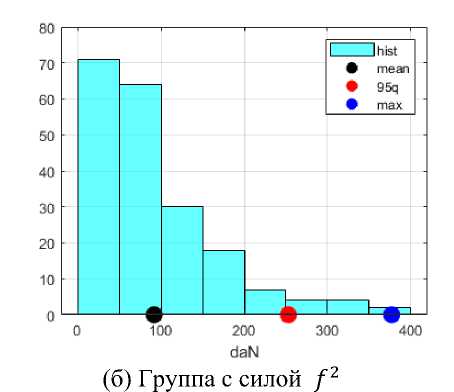
Рис. 4. Примеры полученных распределений для сил в крепежах
Таблица 1. Статистические характеристики для оценки полученных сил в крепежах
Тип крепежа |
Цвет отображения |
Оценка силы, даН |
||||
Средне значение |
95-й квантиль |
Максимальное значение |
||||
f1 |
11 |
78 |
199 |
341 |
||
f2 |
2в |
92 |
253 |
377 |
||
f3 |
22 |
99 |
274 |
515 |
||
f4 |
33 |
94 |
238 |
308 |
||
f5 |
44 |
150 |
290 |
413 |
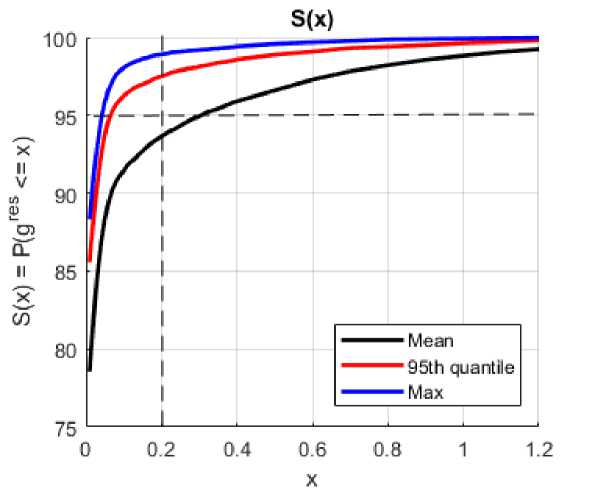
Рис. 5. Полученные функции распределения результирующего зазора (статистические кривые) для разных оценок сил в крепежах
Заключение
В ходе исследования была разработана методика оптимизации процесса сборки деформируемых деталей с использованием крепежных элементов, позволяющая решить проблемы, связанные с вариативностью зазоров между деталями. Применение математического моделирования и метода Монте-Карло дало возможность оценить минимальные силы, необходимые для обеспечения требуемого качества соединения. Результаты практического примера продемонстрировали, что использо- вание статистических оценок, таких как 95-й адаптирован для применения в различных об- квантиль и максимальные значения, является наиболее эффективным подходом для достижения заданных требований к результирующим зазорам. Данный метод может быть ластях машиностроения и авиастроения, спо собствуя улучшению надежности и безопас ности сборочных процессов.
Список литературы Статистический подход к оптимизации сил крепежей при сборке авиационных конструкций
- Hu M., Lin Z., Lai X., Ni J. Simulation and analysis of assembly processes considering compliant, non-ideal parts and tooling variations // Int. J. Mach. Tools Manuf. - 2001. - Vol. 41. - P. 2233-2243. -. DOI: 10.1016/S0890-6955(01)00044-X
- Gao J., Chase K.W., Magleby S.P.Comparison of Assembly Tolerance Analysis by the Direct Linearization and Modified Monte Carlo Simulation Methods // Proceedings of the ASME Design Engineering Technical Conferences. - 1995. - Vol. 1. - P. 353-360. -. DOI: 10.1115/DETC1995-0047
- Saadat M., Cretin L., Sim R. Deformation analysis of large aerospace components during assembly // Int J Adv Manuf Technol. - 2009. - Vol. 41. - P. 145-155. -. DOI: 10.1007/s00170-008-1464-y EDN: JJTKPT
- Liu S.C., Hu S.J. Variation simulation for deformable sheet metal assemblies using finite element methods // ASME J. Manuf. Sci. Eng. - 1997. - Vol. 119, № 3. - P. 368-374. -. DOI: 10.1115/1.2831115
- Wärmefjord K., Lindkvist L., Söderberg R. Tolerance simulation of compliant sheet metal assemblies using automatic node-based contact detection // ASME 2008 International Mechanical Engineering Congress and Exposition. - 2008. - Vol. 14. - P. 35-44. -. DOI: 10.1115/IMECE2008-66344
- Lupuleac S., Petukhova M., Shinder Y., Bretagnol B. Methodology for solving contact problem during riveting process // SAE International Journal of Aerospace. - 2011. - Vol. 4, № 2. - P. 952-957. EDN: PERVMZ
- Stefanova M., Minevich O., Baklanov S., Petukhova M., Lupuleac S., Grigor'ev B., Kokkolaras M. Convex optimization techniques in compliant assembly simulation // Optimisation Engineering. - 2020.
- Lupuleac S., Zaitseva N., Stefanova M. et al. Simulation and optimization of airframe assembly process // ASME International Mechanical Engineering Congress and Exposition 2A. - 2018. -. DOI: 10.1115/IMECE2018-87058 EDN: JRJWRE
- Zaitseva N., Lupuleac S., Shinder J. Initial gap modeling for wing assembly analysis // Aerospace Systems. - 2024. -. DOI: 10.1007/s42401-024-00302-4 EDN: IRWTEC