Structural and heat-insulating cement-based concrete with complex glyoxal based additive
Автор: Aleksei B. Steshenko, Anna S. Simakova, Alexandr S. Inozemtcev, Sergei S. Inozemtcev
Журнал: Nanotechnologies in Construction: A Scientific Internet-Journal @nanobuild-en
Рубрика: Construction materials science
Статья в выпуске: 5 Vol.14, 2022 года.
Бесплатный доступ
Introduction. The article presents the results of studies of the effect of complex additive based on glyoxal on the properties of cement-based foam concrete mix and foam concrete of natural hardening. The relevance of the study is determined by the necessity to provide the required process parameters of mixture for transportation and laying the formwork, as well as providing strength and thermal and physical characteristics of wall structures for the development of the northern regions of Russia, including the Arctic zone. It has been proposed to decrease the shrinkage deformations of the concrete mix and increase compressive strength of hardened foam concrete by affecting the cement matrix with complex modifier based on glyoxal. Materials and methods. The effect of modifying additives on the properties of the foam concrete mixture and foam concrete was studied at a W/S mixture ratio of 0.45. Research has been carried out using test methods set out in national standards. The results of the study of the effect of complex modifying additives (CMA) based on an aqueous solution of glyoxal and organic acids on the rheological and strength properties of foam concrete are presented, the regularities of the processes and the mechanism of structure formation of the modified foam concrete are determined. Results. The use of modifying additives leads to increase result in increasing the aggregative stability and reducing the plastic shrinkage of the foam concrete mix by 22–70%. In foam concrete with the complex additive LA 0.5% + Gl 0.55% the compressive strength rises from 1.96 to 2.43 MPa at the age of 28 days while maintaining the average density of D600. The thermal conductivity coefficient of foam concrete modified with various additives decreased by 5–30% compared to references. Conclusions. The obtained results of the study create in the construction industry the basis for the import substitution of modifying additives on the domestic mineral resource base and the production of effective structural and heatinsulating concretes for the development of the northern regions of Russia.
Glyoxal, structure formation, modifying additives, foam concrete, porous structure, plastic shrinkage, compressive strength, average density, thermal conductivity
Короткий адрес: https://sciup.org/142235381
IDR: 142235381 | DOI: 10.15828/2075-8545-2022-14-5-353-362
Текст научной статьи Structural and heat-insulating cement-based concrete with complex glyoxal based additive
Original article
The development of the northern regions of Russia, including the Arctic zone, has a state development priority and is increasingly relevant in the domestic economy [1]. One of the key points of growth is the construction industry. Providing resources for the construction of modern buildings and structures, especially in the north- ern regions of Russia, special attention must be paid to the quality of building materials and, above all, products based on cement compositions [2]. Taking into account the specifics of these territories, the demanded result for the production of building materials on a cement binder is a composite with specified performance properties. Therefore, research on the development of scientific approaches to control structure formation in the technology
CONSTRUCTION MATERIAL SCIENCE of manufacturing modern multifunctional concretes with high performance indicators, which include structural and heat-insulating concretes, is one of the promising areas [3].
Foam concrete produced at present does not always meet the increased requirements in the design of building envelopes and modern building technologies [4]. As a rule an increase in the bearing capacity of enclosing structures is achieved by increasing the strength and average density of foam concrete, which simultaneously leads to an increase in the thermal conductivity coefficient and a decrease in the thermal protection of the building [3].
The structure of foam concrete is represented by macropores formed by foam (volume 50–92%, size 0.25÷10–4 cm), and interpore partitions, consisting of hydration products and non-hydrated cement, silica component, capillary (10–6÷10–4 cm) gel pores. The strength of the interpore partitions increases with a decrease in the number of capillary pores in it and the thermal conductivity and the average density grade of foam concrete decrease with an increase in the content of macropores [5]. It is necessary to manage the processes of structure formation of foam concrete, taking into account the factors affecting its pore structure:
-
- degree of deformation of spherical pores and their dimensions (pore shape);
-
- the character of the inner surface of the pores. The strength of foam concrete increases with an increase of pores with a dense and smooth inner surface;
-
- closed porous structure. A decrease in water absorption and high frost resistance of foam concrete are provided with an increase in the content of closed pores with a hydrophobized inner surface;
-
- uniform distribution of pores in the volume of the material, which lead to increase the uniformity of quality parameters (strength and thermal conductivity) of foam concrete;
-
- thickness and density of interpore partitions. This indicator depends on the water-solid ratio, the composition of the solid components, as well as the rheological characteristics of the mixture. Initially, part of the water is adsorbed at the air-solution interface, and most of it is located in a structured interpore wall. Part of the water is used to hydrate the cement, and the rest is removed during drying, forming a network of capillary pores of various sizes, directions and closures [6]. One of the effective ways to control the porous structure and strength of the interpore partitions of foam concrete is the introduction of modifying additives into the mixture during mixing, which reduce the water content while maintaining the necessary mobility of the concrete mixture and increase the strength of the cement matrix in the interpore partitions [5, 7–10]. Developing the composition of foam concrete, it must be taken into account that one part of the water is spent on foam formation, and the
other part is used for cement hydration. The use of such additives, both mineral and chemical (synthetic) nature, is one of the tools that provides the ability to control the processes of structure formation at the recipe level. At the same time, a significant role is given to the formation of the structure of hardened cement paste at the micro level [11], because it predetermines the potential for the development of complex modifying additives that implement versatile mechanisms for controlling structure formation [12, 13]. Mainly imported additives are used in the domestic construction industry. Therefore, the development and use of import-substituting modifying additives is relevant. This becomes possible with the development of chemical industry technologies.
In the Tomsk region (Russia) has been developed a technology for the synthesis of oxalic acid dialdehyde – glyoxal, which has a number of unique properties, which makes it very popular in various industries (pharmaceuticals, oil refining, textile, leather, paint and varnish, adhesive, metallurgical industries, etc.). Based on the existing experience of using glyoxal in the construction industry [14–17] it is relevant to review studies on the use of glyoxal-containing additives in building materials manufacturing technologies in order to develop promising areas for further study and creation of new materials with using Russian-made glyoxal.
The creation of an effective complex concrete mix modifier based on glyoxal is possible by combining glyoxal and organic compounds suitable for it according to the “retarder-accelerator” principle [18, 19]. The available scientific groundwork shows the possibility of forming a denser and more durable structure of hardened cement paste in the composition of concrete due to the combined control of structure formation, which consists in the simultaneous control of both the number of crystallization centers and their growth [11, 13, 14]. This is realized by a combination in the composition of the modifying additive of components that perform the function of an accelerator and retarder of the hardening of the binder, respectively [19]. That is, the implementation of complementary crystallization processes is ensured, which optimize the process of structure formation and composite strength gain [20].
The authors propose to use organic bifunctional acids, their salts and oligomers in the form of a combined additive based on glyoxal and a selective effect on the processes of foam concrete structure formation [21].
The aim of this work is to study the effect of a complex modifier based on glyoxal on the processes of structure formation, the features of changes in the technological and mechanical properties of foam concrete. Achieving this goal will make it possible to establish the optimal formulation solutions for obtaining the additive and the concentration of its use to obtain structural-heat-insulating concretes with improved performance properties.
CONSTRUCTION MATERIAL SCIENCE
METHODS AND MARERIALS
The raw materials used in the experimental studies were Portland cement without additives CEM I 42.5Н of Topki Cement Factory (Russian State Standard GOST 30515-2013), fine aggregate, foaming agents, complex modifying additives and tap water (Russian State Standard GOST 23732-2011).
Characteristics of Portland cement are given in Table 1.
Quartz-feldspar sand of the Kudrovskoe deposit of the Tomsk region (Russia) with a fineness modulus of 1.8 (Russian State Standards GOST 8736-2014 and GOST 26633-2012) was used as a fine aggregate for the manufacture of porous structural and heat-insulating concretes.
The following materials were used as foaming agents: foaming agent PBS and BLAIZER PB (Russian State Standards GOST 24211-2008). Technical characteristics of foam agents are presented in Table 2.
We used a 40% aqueous solution of glyoxal (oxalal-dehyde, ethandial) manufactured by Novokhim Trade House, Tomsk (Russia). It obtained by oxidative dehydrogenation of ethylene glycol. It is presented in the form of glyoxal hydrate in aqueous solution. Сhemical formula: С2Н2О2. Crystalline glyoxal is made from a 40% aqueous solution of glyoxal. It belongs to the third hazard class (moderately dangerous) (Russian State Standards GOST 12.1.007-76). Technical characteristics of glyoxal-containing additives are presented in Table 3.
Two series of complex modifying additives were used in the work. The basis of which is a 40% solution of gly-
Table 3
Technical properties of glyoxal
Lactic acid (LA) is an aqueous solution of 80% concentration in the form of a transparent, yellowish liquid, with the smell of whey, “Purac” (Amsterdam, The Netherlands).
Glycolic acid (GA) is a clear yellow liquid. Aqueous solution 67%, “Purac” (Amsterdam, The Netherlands).
Oligomers were obtained from lactic and glycolic acids obtained by polycondensation in the laboratory of polymers and composite materials of National Research Тomsk State University [28, 29].
Table 1
Cement characteristics
Bulk density, kg/m3 |
Residue on the sieve 0.08, % |
Normal density, % |
Setting time, h-min |
Tensile strength, MPa, at the age of 28 days |
||
start of setting |
end of setting |
bending |
compression |
|||
1010 |
2.5 |
26.4 |
2–20 |
3–20 |
6.3 |
50.4 |
Table 2
Technical characteristics of foaming agents
Parameter |
PBS |
BLAIZER PB |
Appearance |
clear to brown liquid |
yellowish liquid |
Foam density at, g/cm3 |
1.020 – 1.120 |
1.080 ± 0.004 |
Foam concentrate consumption per 1 m3 of foam concrete, l |
0.25 – 0.9 |
0.1 – 1.5 |
рН |
7.0 – 11.0 |
7.0 – 10.5 |
Foam ratio of 4% foam concentrate solution, not less than |
7 |
7 |
Foam stability, s, not less |
250 |
250 |
Warranty period of storage |
1 year |
1 year |
CONSTRUCTION MATERIAL SCIENCE
The determination of the physical and mechanical properties of the obtained cement based compositions were carried out using standard methods for testing building materials in accordance with national standards. It includes the determination of compressive strength (Russian State Standard GOST 10180-2012), water absorption (Russian State Standards GOST 12730.32020), thermal conductivity coefficient (Russian State Standards GOST 7076-99), average density (Russian State Standard GOST 12730.1-78), and frost resistance (Russian State Standard GOST 25485-2019). Original methods were used to determine the plastic shrinkage of foam concrete [5, 30].
The design of the composition of the foam concrete mixture was carried out taking into account the requirements of Russian Standard SN 277-80 “Instructions for the production of cellular concrete products”.
The basic compositions of foam concrete (Table 4) were designed taking into account the results of optimizing the technological regimes for the preparation of foam concrete in a laboratory mixer [5, 9, 13].
The study was conducted with the following additives: – 40% solution of glyoxal (Gl) in the amount of 0.55% by weight of cement;
– lactic acid (LA) with various dosages (from 0.25 to 1% by weight of cement);
– polylactic acid (PLA) with dosages of 0.5, 1, 1.5% by weight of cement;
– complex modifying additive Gl 0.01+LA, concentration 0.01% by weight of cement with a ratio of glyoxal and lactic acid 1:50.
Due to establish the regularities of the influence of additives on the properties of foam concrete mixture and foam concrete, additives were introduced into the basic composition of foam concrete without changing the number of components, followed by adjustment of the recommended composition according to the values of the actual average density of the foam concrete mixture. The preparation of the foam concrete mixture was carried out according to a one-stage technology using a laboratory foam concrete mixer.
For preparing a foam concrete mixture with additives firstly cement, sand and part of water are mixed. Then, an aqueous solution of the modifying additive was intro- duced into the mixer in the required amount. The mixing process continues until a homogeneous plastic mass is obtained. Then, a foaming agent diluted in water was introduced into the resulting mixture, and all components were mixed for another 4 minutes.
The finished foam concrete mix was placed in metal molds 15×15×15 cm. A series of samples was made from 6 pieces of each composition for testing. Molded foam concrete specimens were kept under normal conditions at a temperature of 20±2οС for a day and then stored for 27 days in a normal curing chamber at a temperature of 20±2οС and a relative humidity of at least 90% before testing. Testing and quality assessment of foam concrete was carried out according to Russian State Standards GOST 25485-2019. The diameter of the mixture flow was determined on the Suttard device for each mixture, as also the actual density of the foam concrete mixture was.
RESULTS AND DISCUSSION
The studies were carried out on a foam concrete mixture with a flowability of 12–15 cm (diameter on the Suttard’s Viscosity Analyzer). The effect of modifying additives on the properties of the foam concrete mixture and foam concrete was studied at a W/S mixture ratio of 0.45. The research results are presented in Figures 1–3 and in Table 5.
In a foam concrete mixture with modifying additives, a certain amount of water is released (water-reducing effect) and the foaming ability of the mixture increases [6]. As a result, the water content in the structure of interpore partitions decreases, which leads to a decrease in the number of capillary pores and an increase in the strength of foam concrete [9].
A certain amount of water is released (water-reducing effect) in a foam concrete mixture with modifying additives and also the foaming ability of the mixture increases. As a result, the water content in the structure of interpore partitions decreases, which leads to a decrease in the number of capillary pores and an increase in the strength of foam concrete [6].
The most expressed plasticizing effect is observed when the PLA additive is introduced in an amount of
Table 4
The basic composition of foam concrete, for 1 m3
Basic composition |
Component consumption |
|||
cement, kg |
sand, kg |
water, l |
foaming agent, l |
|
D600 |
330 |
165 |
222.75 |
1.2 |
D700 |
380 |
180 |
252 |
1.1 |
D800 |
400 |
200 |
270 |
1 |
CONSTRUCTION MATERIAL SCIENCE
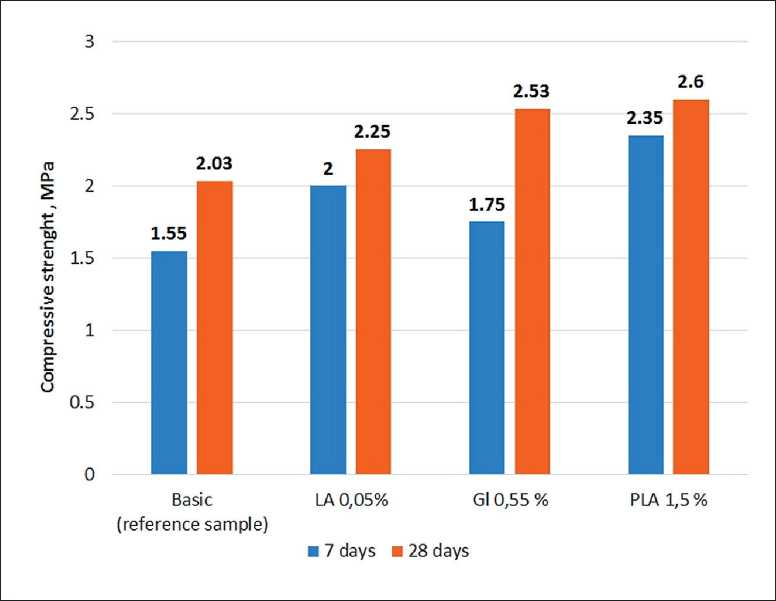
Fig. 1. Influence of modifying additives on the compressive strength of foam concrete by average density D700
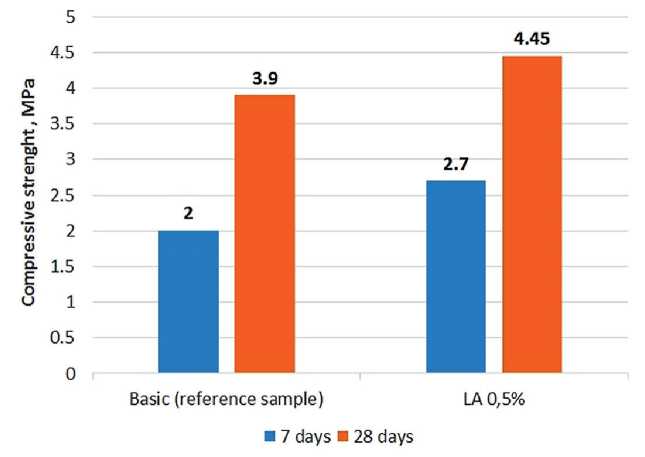
Fig. 2. Influence of lactic acid on the compressive strength of foam concrete by average density D800
CONSTRUCTION MATERIAL SCIENCE
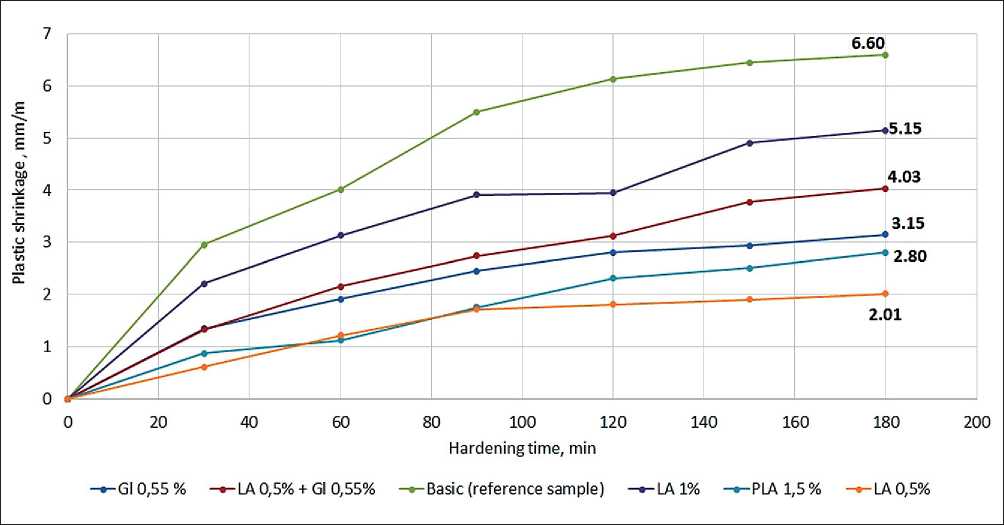
Fig. 3. Influence of modifying additives based on glyoxal on plastic shrinkage of foam concrete mix
Table 5
Influence of modifying additives on the compressive strength of foam concrete by average density D600
Type of fibers |
Mixture flowability, cm |
Average density of foam concrete, kg/m3 |
Compressive strength of foam concrete at the age of 7 days, MPa |
Compressive strength of foam concrete at the age of 28 days, MPa |
Basic (reference) |
12.5 |
610 |
1.35 |
1.96 |
PLA 1.5% |
15 |
594 |
1.6 |
1.7 |
PLA 0.5% |
13.5 |
577 |
1.35 |
1.75 |
PLA 1% |
13 |
609 |
1.7 |
2.2 |
Gl 0.55% |
12.75 |
600 |
1.45 |
2.1 |
LA 0.25% |
13 |
591 |
1.35 |
2.15 |
LA 0.5% |
13.75 |
608 |
1.65 |
2.23 |
LA 1% |
13.8 |
605 |
1.5 |
2.3 |
LA 0.5% + Gl 0.55% |
14 |
580 |
1.75 |
2.43 |
-
1.5% by weight of the cement. The spread diameter of the mixture increases from 12.5 cm to 15 cm in comparison with the reference.
The use of modifying additives makes it possible to increase strength in the early stages of hardening (Table 5). For example, the introduction of PLA additives in the amount of 1% and 1.5% by weight of cement into foam concrete mixture of the average density grade D600 leads to increase the compressive strength at the age of 7 days by 26 and 18%, respectively, compared with the basic composition. The introduction of LA additives in the amount of 0.5% and 1% by weight of cement leads to increase the compressive strength at the age of 7 days by 22 and 11%, respectively, compared with the reference. The best result in increasing the compressive strength at 7 days and 28 days of age is achieved with the use of a complex additive LA 0.5% + Gl 0.55% – 30% and 24%, respectively.
A positive effect of early structure formation is also observed with the introduction of modifying additives into a foam concrete mixture with a grade of average density D700 (Fig. 1) and D800 (Fig. 2). The best results are
CONSTRUCTION MATERIAL SCIENCE observed with the introduction of PLA additive in the amount of 1.5% by weight of cement. The compressive strength increases by 52% at 7 days of age, by 28% at 28 days of age compared with the basic composition while maintaining the D700 average density grade.
The use of LA additives in the amount of 0.5% by weight of cement leads to increase the strength of foam concrete at 7 days of age by 35%, at 28 days of age by 14% in comparison with the reference.
The parameters of performance properties for the compositions with the best results in terms of compressive strength were carried out as also, as the effect of modifying additives on the plastic shrinkage of the foam concrete mixture.
Plastic shrinkage is a consequence of the rapid loss of water from the concrete surface, leading to the formation of negative capillary pressure in micropores [5]. It causes compression of the mixture, which leads to the formation of cracks. Plastic shrinkage tests of foam concrete mixtures with and without additives were carried out in order to establish the regularity of the influence of additives on the shrinkage of the foam concrete mixture in the first hours of hardening.
The results of the study of plastic shrinkage of foam concrete mixtures are shown in Fig. 3. The assumption proposed by the authors was confirmed experimentally. The data obtained confirm the results of the study on the effect of modifying additives on the process of early structure formation of foam concrete. Accelerating this process, glyoxal makes it possible to stabilize the porous structure of the foam concrete mixture, thereby reducing shrinkage deformations of the foam concrete mixture. Plastic shrinkage decreases (aggregative stability increases) by 22–70% compared to the control composition in foam concrete mixtures with modifying additives. It has been established that the smallest plastic shrinkage (2.01 mm/m) is observed in the foam concrete mixture with LA 0.5% by weight of cement (Fig. 3). The obtained values of plastic shrinkage are 70% less basic composition without additives.
The introduction of modifying additives into the composition of the foam concrete mixture provides the required rheological parameters (mixture flowability) and increases the aggregative stability of the mixture. It leads to increase the strength of the hardened mortar of interpore partitions.
As a result of the analysis of data on statistical processing of measurements of the average density and compressive strength of foam concrete, it can be concluded that the coefficient of variation in compressive strength of foam concrete does not exceed 10% and 3.5% for average density. It indicates the stability of technological processes. The normative value of this parameter is 15% for compressive strength and 5% for the average density of foam concrete. An increase in the compressive strength grade of foam concrete from B1 to B1.5–B2 is provided as a result of increasing the stability of technological processes, while maintaining the average density grade D600, D700 and from B2.5 to B3.5 while maintaining the average density grade D800.
The specified quality indicators are provided with rational structures of foam concrete: compressive strength at a given average density, shrinkage, thermal conductivity and frost resistance. High rates of precisely these properties make it possible to attribute foam concrete to effective building materials.
Based on the foregoing, the work carried out studies of the influence of modifying additives on the coefficient of thermal conductivity and frost resistance of foam concrete. Data on the thermal conductivity of foam concrete samples with additives are given in table. 6.
Analyzing the results, we can conclude that the thermal conductivity coefficient of foam concrete modified with various additives decreased by 5–30% compared to references and corresponds to the standard values of Russian State Standard GOST 25485-2019 for a given average density (Table 6).
Pores with sizes from 0.3 to 0.5 mm are predominantly formed in the cement matrix with modifying additives. The probability of heat transfer due to convection is significantly reduced in such kind of pores. All this together proves the energy efficiency of foam concrete with the studied modifying additives.
As a result of the study, it was found that the frost resistance of modified foam concrete is not inferior to basic samples and is at least 25 cycles at an average density of 600–800 kg/m3 (Table 7). The introduction of the complex additive LA 0.5% + Gl 0.55% into the composition of the foam concrete mixture made it possible to increase the frost resistance grade from F15 to F25. The best result in terms of frost resistance was achieved with
Table 6
The values of the coefficient of thermal conductivity of foam concrete samples
Type of foam concrete |
Thermal conductivity coefficient, W/m • С in dry condition |
Basic (reference) D600 |
0.120 |
LA 0.5% + Gl 0.55% |
0.090 |
LA 1% |
0.085 |
Basic (reference) D700 |
0.174 |
Gl 0.55 % |
0.170 |
PLA 1.5 % |
0.168 |
Basic (reference) D800 |
0.194 |
LA 0.5% |
0.188 |
CONSTRUCTION MATERIAL SCIENCE
Table 7
Frost resistance grade for foam concrete with modifying additives
The introduction of additives into the composition of foam concrete made it possible to obtain porous structur- al-heat-insulating concrete with improved performance properties.
CONCLUSION
Using the obtained scientific results, actual compositions have been developed to create a resource-saving technology for the manufacture of cement building compositions with controlled volumetric changes using glyoxal-containing additives for the installation of wall structures in monolithic housing construction.
According to the research results, the use of the optimal amount of modifying additives indicated in this work in the production of cement foam concrete mixtures has a positive effect on the quality of foam concrete and products from it.
The obtained results of the study create the basis for the import substitution of modifying additives on the domestic mineral resource base in the construction industry and the production of effective structural and heatinsulating concretes for the development of the northern regions of Russia.
Список литературы Structural and heat-insulating cement-based concrete with complex glyoxal based additive
- Mestnikov A.E., Popov A.L. Efficiency of using lightweight concrete in the construction of buildings and underground structures in the arctic. Digital Technologies in Construction Engineering. Selected Papers. Сер. “Lecture Notes in Civil Engineering”. 2022; 173: 391–398. https://doi.org/10.1007/978-3-030-81289-8_49.
- Ilina L., Kudyakov A., Rakov M. Aerated dry mix concrete for remote northern territories. Magazine of Civil Engineering. 2022; 5(113): 11310. https://doi.org/10.34910/MCE.113.10.
- Markin V., Nerella V.N., Schröfl C., Guseynova G., Mechtcherine V. Material design and performance evaluation of foam concrete for digital fabrication. Materials. 2019; 12: 2433. https://doi.org/10.3390/ma12152433.
- Namsone E., Šahmenko G., Namsone E., Korjakins A. Development of high-strength foamed concrete compositions. Diffusion and Defect Data Pt.B: Solid State Phenomena. 320: 186–190. https://doi.org/10.4028/www.scientific.net/SSP.320.186.
- Steshenko A.B., Kudyakov A.I. Early structure formation of foam concrete mix containing modifying admixture. Magazine of Civil Engineering. 2015; 2: 56–62. https://doi.org/10.5862/MCE.54.6.
- Lam T.V., Dien V.K., Hung N.X., Vu D.T., Bulgakov B.I., Alexandrova O.V. Modelling of the effect of the water-cement ratios on properties foam concrete. IOP Conf. Series: Journal of Physics: Conf. Series. 2019; 1425: 012189. https://doi.org/10.1088/1742-6596/1425/1/012189.
- Inozemtcev A.S., Korolev E.V., Smirnov V.A. Nanoscale modifier as an adhesive for hollow microspheres to increase the strength of high-strength lightweight concrete. Structural Concrete. 2017; 18(1): 67–74. https://doi.org/10.1002/suco.201500048.
- Dien V.K., Ly N.C., Lam T.V., Bazhenova S.I. Foamed concrete containing various amounts of organicmineral additives. IOP Conf. Series: Journal of Physics: Conf. Series. 2019; 1425: 012199. https://doi.org/10.1088/1742-6596/1425/1/012199.
- Kudyakov A.I., Steshenko A.B., Simakova A.S., Latypov A.D. Methods of introduction of glyoxal-containing additives into foam concrete mixture. IOP Conf. Series: Materials Science and Engineering. 2019; 597: 012037. https://doi.org/10.1088/1757-899X/597/1/012037.
- Khalikov R.M., Ivanova O.V., Korotkova L.N., Sinitsin D.A. Supramolecular impactmechanism of polycarboxylate superplasticizers on controlled hardening building nanocomposites. Nanotechnologies in Construction. 2020; 12(5): 250–255. https://doi.org/10.15828/2075-8545-2020-12-5-250-255.
- Korolev E.V., Grishina A.N., Inozemtcev A.S., Ayzenshtadt A.M. Study of the kinetics structure formation of cement dispersed systems. Part I. Nanotechnologies in Construction: A Scientific Internet-Journal. 2022; 14(3): 176–189. https://doi.org/10.15828/2075-8545-2022-14-3-176-189.
- Kopanitsa N.O., Demyanenko O.V., Kulikova A.A. Effective polyfunctional additive for composite materials based on cement. Digital Technologies in Construction Engineering. Selected Papers. Сер. “Lecture Notes in Civil Engineering”. 2022; 173: 125–131. https://doi.org/10.1007/978-3-030-81289-8_17.
- Kudyakov A.I., Steshenko A.B. Investigation of the influence of the crystalline glyoxal on properties of air hardened cement-based foam concrete. Letters on Materials. 2015; 5(1): 3–6. https://doi.org/10.22226/2410-3535-2015-1-3-6.
- Kudyakov A.I., Steshenko A.B. Study of hardened cement paste with crystalline glyoxal. Key Engineering Materials: Multifunctional Materials: Development and Application. 2016; 683: 113–117. https://doi.org/10.4028/wwwscientific.net/KEM.683.113.
- Gandon L., Lehmann R.L., Marcheguet H.G.L., Tarbouriech F.P.M. Production of new compositions from glyoxal and alkali metal silicates. 1957; US Patent № 3028340.
- Sokolova Y., Ayzenshtadt A.M., Strokova V.V., Malkov V.S. Surface tension determination in glyoxal-silica dispersed system. Journal of Physics Conference Series. 2018; 1038(1): № 01214. https://doi.org/10.1088/1742-6596/1038/1/012141.
- Sokolova Y., Ayzenshtadt A.M., Strokova V.V. Evaluation of dispersion interaction in glyoxal/silica organomineral system. Journal of Physics Conference Series. 2017; 929(1): 012110. https://doi.org/10.1088/1742-6596/929/1/012110.
- Simakova A., Kudyakov A., Efremova V., Latypov A. The effects of complex glyoxal based modifiers on properties of cement paste and hardened cement paste. AIP Conference Proceedings. 2017; 1800: 020006. https://doi.org/10.1063/1.4973022.
- Kudyakov A.I., Simakova A.S., Steshenko A.B. Сement based compositions with complex modifyingadditives based on glyoxal. The Russian Automobile and Highway Industry Journal. 2021; 18(6): 760–771. https://doi.org/10.26518/2071-7296-2021-18-6-760-771.
- Gorlenko N.P., Sarkisov Yu.S., Volkova V.A., Kul’chenko K. Structurization processes in the system cement–water with chemical addition of glyoxal. Russian Physics Journal. 2014; № 57 (2): 278–284. https://doi.org/10.1007/s11182-014-0236-4.
- Kudyakov A.I., Simakova A.S., Kondratenko V.A., Steshenko A.B., Latypov A.D. Cement paste and brick properties modified by organic additives. Vestnik of Tomsk State University of Architecture and Building. 2018; 20(6): 138–147. (In Russian).
- Hazra M., Francisco J., Sinha A. Hydrolysis of glyoxal in in water-restricted environments: formation of organic aerosol precursors through formic acid catalysis. The Journal of Physical Chemistry A. 2014; 118: 4095–4105.
- Fratzke A.R., Reilly P.J. Kinetic analysis of the disproportionation of aqueous glyoxal. IJCK. 1986; 18: 757–773.
- Salomaa P. The kinetics of the Cannizzaro reaction of glyoxal. Acta Chemica Scandinavica. 1956; 10(2): 311–319.
- Maruful Malik, Jeffrey A. Joens. Temperature dependent near-UV molar absorptivities of glyoxal and glutaraldehyde in aqueous solution. Elsevier. Spectrochimica Acta Part A. 2000; 56: 2653–2658. https://doi.org/10.1016/S1386-1425(00)00311-5.
- Ge Yu., Amanda R. Bayer, Melissa M. Galloway, Kyle J. Korshavn, Charles G. Fry, and Frank N. Keutsch. Glyoxal in aqueous ammonium sulfate solutions: products, kinetics and hydration effects. Environmental science and technology. 2011; 45(15): 6336–6342. https://doi.org/10.1021/es200989n.
- Kurten T., Elm J., Prisle N., Mikkelsen K. Computation study of the effect of glyoxal-sulfate clustering on the Henry’s law coefficient of glyoxal. The Journal of Physical Chemistry A. 2015; 119 (19): 4509–4514. https://doi.org/10.1021/jp510304c.
- Kirsten W. Loeffler, Charles A. Koehler, Nichole M. Paul, David O.De Haan. Oligomer formation in evaporating aqueous glyoxal and methyl glyoxal solutions. Environ. Sci. Technol. 2006; 40: 6318–6323. https://doi.org/10.1021/es060810w.
- Avzianova E., Brooks S.D. Raman spectroscopy of glyoxal oligomers in aqueous solutions. Spectrochimica Acta Part A: Molecular and Biomolecular Spectroscopy. 2013; 101: 40–48. https://doi.org/10.1016/j.saa.2012.09.050.
- Markus G. Measuring the early shrinkage of mortars drymix mortar. Yearbook 2011. Editor: Ferdinand Leopolder; 2011.