Study of the influence of innovative metallurgical processing technologies on the structure and properties of spheroidal graphite cast iron
Автор: Ramiz Hasanli
Журнал: Science, Education and Innovations in the Context of Modern Problems @imcra
Статья в выпуске: 1 vol.8, 2025 года.
Бесплатный доступ
This paper investigates the effect of economic alloying and efficient heat treatment mode on the structure and properties of spheroidal graphite cast iron. High demands are placed on complex structural parts made of spheroidal graphite cast iron (SGCI) used in various branches of mechanical engineering. The material of these parts must have a set of properties, such as high strength, hardness, good machinability, low friction coefficient, corrosion resistance, and the ability to operate in aggressive environments. Achieving the set of listed properties of cast iron is a very important task. Therefore, the use of the possibilities of innovative technologies for metallurgical processing (alloying and heat treatment mode) of high-strength cast iron is a topical issue on the agenda.
Spheroidal graphite cast iron, structure, properties, economical alloying, heat treatment, bainite
Короткий адрес: https://sciup.org/16010320
IDR: 16010320 | DOI: 10.56334/sei/8.1.13
Текст научной статьи Study of the influence of innovative metallurgical processing technologies on the structure and properties of spheroidal graphite cast iron
Introduction. At present, bainitic cast iron with spheroidal graphite is finding ever wider application in various branches of national economy due to the optimal combination of mechanical, operational and technological properties [1, pp.8-13 ; 3, pp.7-15] .
The properties of bainitic cast iron with spheroidal graphite are determined by the -dispersion of the structural components, which depends on the selected heat treatment mode and the corresponding degree of alloying [2; 4] .
Bainitic structures in products made of graphitized cast irons is isothermal hardening, which consists of heating for austenitization and subsequent hardening in a salt bath at intermediate transformation temperatures [5, pp. 72-74; 6, pp. 48-58] .
By changing the temperature and time conditions of the corresponding stages of heat -treatment, it is possible to vary the structure and properties of cast irons. Alloying elements play an important role in the processes of bainitic structure formation; by changing the stability of austenite, they affect the hardenability of cast iron and the optimization of the parameters of the isothermal hardening mode [7, pp. 7-12; 9, pp. 7-10]. Traditionally, molybdenum and nickel are considered the main alloying elements in bainitic cast irons. However, their use for alloying cast irons leads to an increase in the cost of the material [3, pp. 117-124; 8, pp. 26-31].
Research. The paper summarizes studies on the effect of alloying elements, namely nickel and copper, on the mechanical properties and structure of isothermally hardened high-strength cast iron. Copper was used as an alternative to expensive molybdenum when alloying cast iron.
As part of the study of the influence of alloying elements on mechanical properties, three experimental melts were carried out, the chemical composition of which is presented in Table 1.
The cast iron melt was poured into sand-clay molds in order to obtain cast blanks for further study. The initial structure in the blanks is obtained from cast irons with chemical composition corresponding to melts No. 1 and 2 (Table 1), – ferritic, and in the blanks of melt No. 3 – ferritic-pearlite.
Table 1
Chemical composition of experimental melts
Melt No. |
Chemical composition, wt . % |
|||||||
C |
Si |
Mn |
P |
S |
Ni |
Cu |
Mg |
|
1 |
3,3 |
3, 75 |
0.23 |
0.024 |
0.011 |
1,5 |
0.5 |
0.025 |
2 |
3,2 |
3.9 |
0.22 |
0.025 |
0,001 |
1,7 |
0.8 |
0.024 |
3 |
3,1 |
4 |
0.23 |
0.025 |
0,001 |
2 |
1,2 |
0,029 |
∅ 25 × 15 and standard samples according to GOST 7293-85 were cut from cast blanks on a lathe to determine mechanical properties. Experimental products made of the studied cast irons were subjected to isothermal hardening according to the following mode: austenitization -temperature 900 oC, time 1 hour; isothermal hardening - temperature 320 o C, time 2 hours. Melted lead-tin solder was used as a hardening medium.
Since the density of the quenching medium is higher than the density of cast iron, the samples were loaded with special devices for complete immersion in the melt . After holding in the quenching bath, they were cooled in air.
The results of mechanical properties of experimental samples are presented in Table 2.
The obtained results were analyzed. As can be seen from Table 2, the optimal combination of strength and plastic properties was obtained for samples 2. With a relatively high tensile strength of 129.5 MPa, the relative elongation value is 7.3 %, and the impact strength value is 150 kJ/ m2.
The microstructure of cast iron after isothermal quenching (sample 2) is shown in the figures. It corresponds to bainitic - ferritic high-strength cast iron with spheroidal graphite.
Table 2
Mechanical test results
Sample |
Mechanical properties |
||
σ in, MPa |
δ, % |
KCU, kJ/ m2 |
|
1 |
1300 |
8.5 |
98 |
2 |
1295 |
7.3 |
149 |
3 |
1391 |
6.2 |
148 |
In this case, grain boundary and near-graphite precipitation of bainitic structures is observed. Such a regular distribution of bainitic structures in the matrix of high-strength cast iron became possible to obtain due to rational control of the austenitization process.
When heated, austenite in cast iron products initially appears in places where carbon diffusion is intense. Such areas in the original ferritic cast iron are areas of near-graphite inclusions and grain boundaries, which are paths of accelerated diffusion. Saturation of the ferritic matrix with carbon leads to the transformation of the original body-centered lattice into a face-centered one, which corresponds to the γ -phase.
The subsequent bainitic transformation occurs only in those places of the cast iron metal matrix where the γ- phase was formed after the austenitization process.
As is known, the formation of bainitic structures includes several stages: firstly, the decomposition of austenite into bainitic (acicular) ferrite and high-carbon austenite (γ вс ) γ→α+ γ вс ; secondly, the transformation of high- carbon austenite into bainite γ vs →α+ carbide [3, p . 88–91; 7, p.7–1 2] .
The release of carbides during the decomposition of high-carbon austenite is undesirable, as it leads to the formation of a brittle high-carbon phase along the boundaries of bainitic inclusions, reducing strength and plastic properties. It has been established that the bainitic transformation in ferritic cast iron initially develops more slowly than in pearlitic cast iron, as evidenced by their high hardness.
It was found that bainitic transformation begins to develop intensively in cast irons with a ferritic initial structure after more than 10 minutes of holding. At temperatures of 400 and 350 0 C it is practically completed in 15-16 minutes (Fig. 1). Cooling in a bath with a temperature of 350 0 C leads to the formation of lower bainite (Fig. 2), with a temperature of -400 and 450 0C - upper.
To increase the stability of the two-phase structure (ferrite + high -carbon austenite), alloying elements are introduced, which, by forming solid substitution solutions, strengthen the austenite, increase the hardness of the final α - phase and increase the bainitic hardenability of cast iron by suppressing pearlite transformation.
Often, as noted earlier, the choice of alloying elements is limited to copper, nickel, manganese and molybdenum. Molybdenum most significantly increases the bainitic hardenability . However, molybdenum, having a tendency to liquation along the boundaries of eutectic colonies and the formation of stable carbides in these areas, leads to a decrease in the plasticity and impact toughness of cast iron.
Nickel stabilizes austenite, increases hardenability, inhibits the precipitation of carbides, and lowers the temperature of the eutectoid transformation.
Copper effectively increases hardenability, prevents the precipitation of carbides from austenite, and slightly increases the stability of austenite. Copper secretes mainly around graphite inclusions, creating a barrier to carbon diffusion between graphite and austenite. Copper alloying sometimes carried out to neutralize the negative effects of molybdenum.
A.
B.
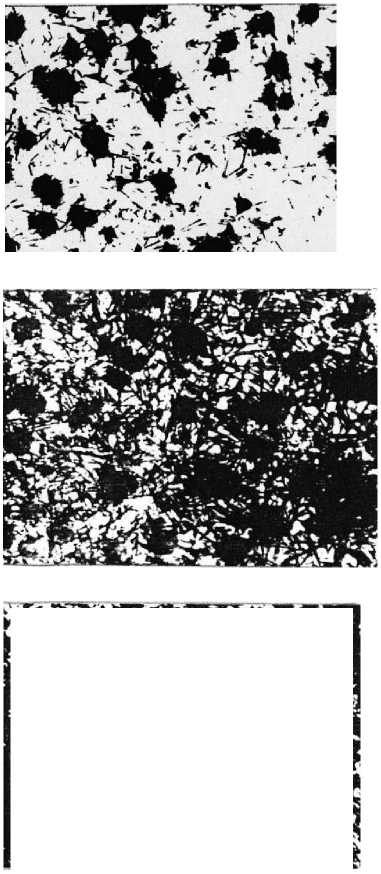
C.
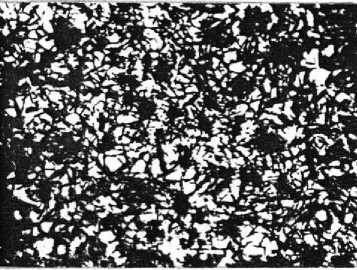
F ig. 1. Effect of holding time at 350 0C isotherm on structure of ferritic unalloyed cast iron: a - τ from = 2 min.; b - τ from = 10 min.; c - τ from = 16 min. x800
p: 164
Issue 1, Vol.8, 2025 | Science, Education and Innovations in the context of modern problems
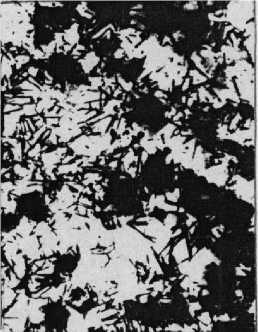
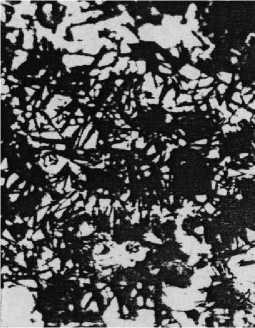
A B
C
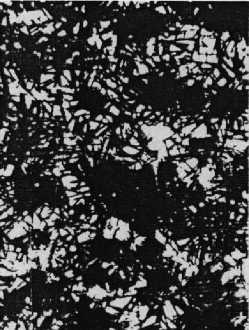
Fig. 2. Effect of holding time at 350 0 C isotherm on structure of pearlitic unalloyed cast iron:
a - τ = 2 min.; b - τ = 10 min.; c - τ = 16 min. d - τ = 2 hours
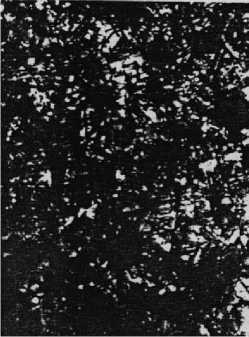
D
Conclusion: According to the research results, economical alloying of cast iron with only copper or only nickel cannot provide sufficient about the hardenability of products, but joint alloying of these elements increases the hardenability of cast iron in the region of bainitic transformation.
Alloyed copper-nickel bainitic cast iron with spheroidal graphite has a homogeneous structure, does not contain brittle phases at grain boundaries and has better mechanical properties compared to cast iron containing manganese or molybdenum.
During the study, the optimal combination of mechanical properties was obtained for samples containing 1.8% Ni + 1% Cu. With an increase in the mass fraction of these alloying elements, an increase in strength properties with a simultaneous decrease in plastic properties is observed. This occurs as a result of increasing segregation of the indicated alloying elements along the boundaries of phases and ferrite grains.
One of the ways to reduce the negative impact of alloying elements on the mechanical properties of cast iron is to increase the silicon content, which promotes a more uniform distribution of alloying elements.
However, an excessive increase in silicon in the composition of cast iron can contribute to the formation of a silicoferrite metal matrix during isothermal holding, which will lead to a sharp drop in the plastic properties of the products.