Технология ультразвукового формирования непаяных соединений электрических плат с контролем усилия запрессовки
Автор: Шуваев В.Г.
Журнал: Известия Самарского научного центра Российской академии наук @izvestiya-ssc
Рубрика: Машиностроение и машиноведение
Статья в выпуске: 3 т.24, 2022 года.
Бесплатный доступ
В работе рассматриваются вопросы технологии формирования непаяных соединений электрических плат с применением ультразвуковых колебаний. Описывается разработанное и запатентованное устройство для формирования ультразвуковых продольно-крутильных колебаний, дающее возможность существенно уменьшить усилие запрессовки, модифицировать свойства поверхностных слоев деталей и проводить контроль усилия запрессовки контактных штырей.
Непаяные соединения, качество, ультразвук, сложные колебательные воздействия, усилие запрессовки
Короткий адрес: https://sciup.org/148325125
IDR: 148325125 | DOI: 10.37313/1990-5378-2022-24-3-60-62
Текст научной статьи Технология ультразвукового формирования непаяных соединений электрических плат с контролем усилия запрессовки
Непаяные соединения стали применять вследствие невозможности использования пайки и припоя в некоторых случаях, связанных как с увеличением плотности монтажа, наличием больших массивов металла (меди) и невозможностью его прогрева. В таких случаях производят запрессовку контактов в металлизированные отверстия в печатных платах. Этот метод непаяного соединения получил название press-fit и широко распространен в технологии сборки электронных плат, в тех случаях, когда методы пайки не обеспечивают качественного соединения [1].
Соединения запрессовкой формируются путем впрессовывания контактов в металлизированные отверстия в платах, причем диаметр контакта больше чем диаметр отверстия, что и обеспечивает надежность соединения. Прессовые соединения обладают существенными преимуществами по сравнению с паяными, у них исключается вероятность возникновения коротких замыканий из-за мостиков припоя, отсутствуют температурные воздействия на печатную плату, простота реализации соединений, отсутствие газовых выделений и остатков флюса и т.д. [2].
значение усилий запрессовки не должно превышать в процессе запрессовки 150 Н, то есть при формировании соединения необходимо производить контроль усилия запрессовки, что приведет к повышению надежности и работоспособности прессовых соединений.
В статье рассматривается технология запрессовки штырьков в платы с дополнительным использованием ультразвуковых колебаний, вводимых в процессе сборки. В процессе ультразвукового поверхностного пластического деформирования имеет место одновременное статическое и динамическое нагружение, периодически повторяющееся с частотой колебаний и распространяющееся на сравнительно малую площадь деформирования поверхности детали. Ультразвуковое воздействие снижает исходную шероховатость поверхности детали и формирует остаточные напряжения сжатия, повышает микротвердость поверхности и обеспечивает благоприятное ее распределение по глубине модифицированного слоя. Кроме того, под действием ультразвуковых колебаний происходит самоцентрирование контактного штыря и существенно снижается трение в процессе запрессовки [4].
Контроль качества прессовых соединений в процессе запрессовки предлагается проводить методами вибрационной диагностики, путем измерения вибраций механической колебательной системы, образованной запрессовываемыми деталями. Когда частота вынуждающих колебаний приближается к частоте собственных колебаний системы, происходит быстрое увеличение коэффициента динамичности системы μ, показывающего во сколько раз амплитуда вынужденных колебаний больше перемещения, вызываемого статически приложенной силой [5]:
μ = 1/[1- ω в2/ ω 2с ] , где ω в – частота вынуждающих колебаний;
ω с – частота собственных колебаний механической системы.
Резонансная кривая системы строится как зависимость коэффициента динамичности μ от отношения частот ω в/ ω с. Непрерывное измерение коэффициента динамичности в процессе запрессовки и сравнение его с эталонными значениями позволяет определять качество запрессовки для каждого соединения.
На рисунке 1 представлено устройство для монтажа контактных штырей на печатные платы и непрерывного контроля качества соединения [6, 7].
Устройство содержит концентратор для усиления механических колебаний 1, на боковой поверхности которого выполнены наклонные пазы 2. Выполнение на боковой поверхности концентратора наклонных пазов приводит к возникновению дополнительных крутильных колебаний, способствующих запрессовке. Для возбуждения ультразвуковых колебаний применен пакетный пьезокерамический преобразователь 3, зажатый при помощи шпильки и гайки 6 между концентратором 1 и противовесом 5. Под крышкой 4 размещен датчик силы 7, замеряющий усилие запрессовки. Запрессовываемый электрический контакт 8 через сквозное металлизированное отверстие 9 запрессовывается в печатную плату 10. Датчик вибрации 11 воспринимает прошедшие через формируемое соединение механические колебания и преобразует их в электрический сигнал, который поступает на входы частотомера 13 и измерителя амплитуды вибрации 12. С выхода измерителя амплитуды вибрации сигнал поступает в блок определения резонанса 15 и в программный блок 14, в котором определяется амплитудночастотная характеристика и вычисляется коэффициент динамичности колебательной системы. К выходу программного блока подключен блок индикации 16. В состав блока определения резонанса 15 входит пиковый детектор, при помощи которого амплитуда вибрации запоминается в строгом соответствии с текущим значением частоты.
Устройство работает следующим образом.
Преобразователь колебаний 3 возбуждает продольные ультразвуковые колебания с частотой 18000-23000 Гц и амплитудой до 10-20 мкм. Преобразователь колебаний может быть выполнен, например, на основе пакетного пьезокерамического преобразователя из шайб пьезокерамики осевой поляризации типа ЦТС-19.
При подаче с генератора электрического напряжения синусоидальной формы и резонансной частоты (на чертеже не показан) на обкладки пакетного пьезокерамического преобразователя, он, изменяя вследствие обратного пьезоэффекта свои геометрические размеры, возбуждает механические колебания концентратора 1 и, соответственно, электрического контакта 8, который и запрессовывается в отверстие 9 платы 10. Одновременно сдатчика вибрации 11 поступает электрический сигнал, пропорциональный вибрационным сигналам, который обрабатывается в программном блоке 14 и в блоке определения резонанса 15. Измеренное текущее значение коэффициента дина-
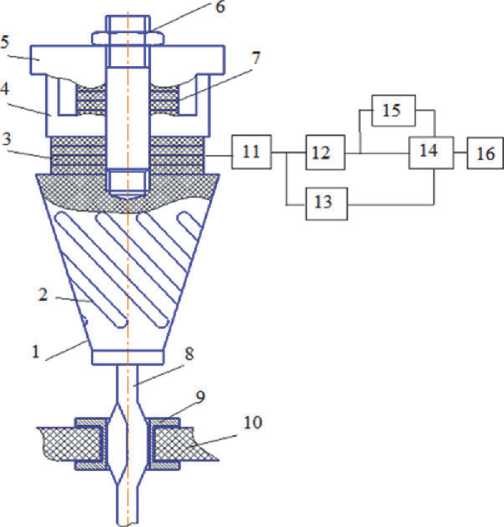
Рис.1. Ультразвуковое устройство для монтажа контактных штырей на печатные платы
мичности сравнивается с эталонным значением и по результатам сравнения принимается решение о качестве сформированного соединения.
Предлагаемая технология ультразвуковой запрессовки деталей дает возможность получать оперативную информацию о параметрах формируемого соединения, выявлять отклонения от заданных характеристик и оперативно вносить необходимые коррективы в технологический процесс. Увеличение глубины диагностики позволяет выявлять и локализовывать «тонкие» дефекты, повышать качество соединений без ужесточения технологии за счет средств неразрушающего контроля. Применение устройства позволит снизить в 2-4 раза усилие запрессовки за счет снижения коэффициента трения в условиях ультразвуковых колебаний.
Список литературы Технология ультразвукового формирования непаяных соединений электрических плат с контролем усилия запрессовки
- IEC 6 0352-5, Solderless Connections - Part 5: Press-in connections - General requirements, test met hods and practical guidance, Edition 3.0, 2008-01.
- Reliability of PressFIT Connections / Stolze Т. Etall // Infineon T echnologies A G, www.bodospower.com, june. 2008.
- Плотников, Ф.Г. Непаяные соединения, выполняемые запрессовкой, - новый класс соединений на российском рынке электронной техники / Ф.Г. Плотников // Компоненты и технологии. - 2001. - № 1.
- Шуваев, В.Г. Адаптивная система управления ультразвуковой запрессовкой с оценкой качества формируемых соединений / В.Г. Шуваев // Международный симпозиум "Надежность и качество", Пенза, 25-31 мая, 2013. - 2 том. - С. 278-279.
- Патент РФ № 1731572. Способ запрессовки деталей/ В.А. Николаев, В.Г. Шуваев // 11.10.93. Бюл. № 19.
- Шуваев, В.Г. Формирование непаяных соединений электрических плат с применением ультразвуковой запрессовки / В.Г. Шуваев, Е.В. Благороднова // Международный симпозиум "Надежность и качество". - 2020. - № 2. - С. 302 -303.
- Патент РФ № 2 759 639. Устройство для монтажа контактных штырей на печатные платы / В.Г. Шуваев, Е.В. Благороднова // 16.11.2021. Бюл. № 32.