The Research of Fuzzy Variable Transmission Ratio for Steer-by-wire System of Electric Forklift
Автор: Benxian Xiao
Журнал: International Journal of Intelligent Systems and Applications(IJISA) @ijisa
Статья в выпуске: 5 vol.7, 2015 года.
Бесплатный доступ
Combining with the TE30 electric forklift produced by an enterprise, the principle of Steer-by-wire (SBW) system, steering motion state, ideal steering ratio are analyzed and studied. The biggest characteristic of SBW system is that the transmission ratio is free to design. Based on the establishment of two-degree-freedom linear model of Forklift, the paper designed the nonlinear transmission ratio function on vehicle speed and steering angle with the application of fuzzy control rules. The simulation results show that the fuzzy variable transmission ratio can make the yaw velocity gain tend to be constant, also can make Forklift light sensitive at low speeds and steady heavy at high speed. In order to ensure that the yaw velocity gain does not vary with the change of speed and steering angle, this paper presents a dynamic correction control strategy based on the steady-state control for Forklift. The simulation results show that the amplitudes of yaw velocity and sideslip angle are reduced with the dynamic correction of yaw velocity feedback, also the handling stability is improved.
Electric Forklift, SBW System, Variable Transmission Ratio, Dynamic Correction of Yaw Velocity
Короткий адрес: https://sciup.org/15010713
IDR: 15010713
Текст научной статьи The Research of Fuzzy Variable Transmission Ratio for Steer-by-wire System of Electric Forklift
Published Online April 2015 in MECS
With the rapid development of modern forklift technology, people on the requirements of forklift steering performance are also increasing, not only steering light flexible and small steering radius, but also good mobility performance. In order to make the steering portability and handling stability meet the requirements when the Forklift steering wheel is turned in any working conditions, the forklift steering system was constantly improved. Forklift steering technology is gradually developed from Mechanical steering system, Hydraulic power steering system, Electronic-hydraulic power steering system to Electric Power Steering (EPS) system and the active steering system[1,2].
SBW system eliminates the mechanical connection between the steering wheel and the steering actuator, it can realize active steering control for the forklift steering system.
In SBW system, the electrical signal and controller replace mechanical connection mode between the steering wheel and the steering actuator, it is no longer bounded by the mechanical connection, this makes the angle transmission characteristics and force transmission characteristics of the forklift steering system are free to design, this makes the forklift steering characteristics with a huge space for development. Practice has proved, SBW system compared with the traditional steering system improves the steering characteristic and the operation stability, reduces the driver's physical consumption[3,4,5].
The main research work of this paper is as follows:
-
(1) Takes TE30 type SBW forklift produced by an enterprise as an example, introduces the working principle of SBW system and the forklift steering motion coordinate system.
-
(2) Presents the concept of ideal transmission ratio, analysis the influence factors of ideal transmission ratio based on two-degree-freedom forklift model. Determines the ideal transmission ratio according to the value of the actual TE30 forklift, designs the variable transmission ratio function based-on fuzzy control rules, finally simulation analysis is done for the variable transmission ratio function in typical conditions.
-
(3) Introduces the dynamic correction of yaw velocity feedback, simulation results show that the strategy can reduce the amplitude of yaw velocity and sideslip angle, improves forklift handling stability.
-
II. The Principle of SBW System
SBW system is developed on the basis of the EPS system, it eliminates the mechanical connection between the steering handle and the steering wheel, overcomes the mechanical structure constraint for the steering characteristic, and can make the vehicle light sensitive at low speeds and steady heavy at high speed.
The working principle of SBW system is: when the driver turns the steering handle, torque, angle and vehicle speed signal etc. are transmitted to the main controller ECU through the sensors, ECU will send the control command after the logical analysis and calculation of these signals, directly control steering motor and realize the steering of the vehicle wheel.
Because the steering wheel is completely controlled by ECU, So the SBW system can realize the variable angle transfer characteristics of the steering system according to the actual condition of forklift.
-
III. The Description of Forklift Steering Motion State
In the forklift steering coordinate system, taking the vehicle mass center O as the origin of coordinates, taking the forward direction of the vehicle as positive x axis in the horizontal plane passing through the origin, taking the direction on the left side of the driver as the positive y axis in the horizontal plane through the origin, taking vertical direction as the positive z axis in the vertical plane through the origin.
There are three main motion parameters relevant to the vehicle steering system, respectively: yaw velocity ω , that is the angular velocity of the vehicle body around z axis. Lateral velocity v , namely the vehicle mass center along the y axis speed. Lateral acceleration a , namely the vehicle mass center on the y axis acceleration. Forklift coordinate system is shown in Fig. 1.[6]
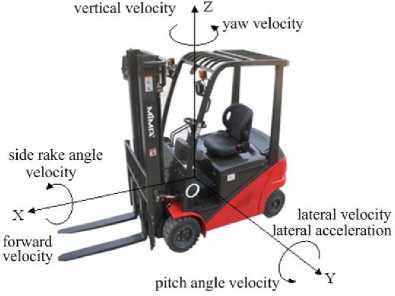
Fig. 1. Schematic diagram of Forklift coordinate system
A. The Lateral and Longitudinal Stability of Electric Forklift
Unlike ordinary passenger cars, as a logistics tool, electric forklift has a main feature that its load is variable. Relevant data shows that forklift accidents often happen because of improper stacking and excessive speed. And most of the accidents are caused by the excessive centrifugal force when the forklift is steering. This shows that, on the one hand, the main reason of such accidents is the improper stacking, however, the most important reason is the excessive speed. These make the steering security and the steering stability of electric forklift become noteworthy.
The steering stability of electric forklift refers to the lateral and longitudinal stability in the loading, unloading and transportation process when the forklift is driving on different ways. The longitudinal stability refers to the ability to prevent electric forklift from rolling over longitudinally around the axle caused by gravity and inertia force (such as forward or backward rollovers). Factors that affect the longitudinal stability are generally the forks lift speed and the forklift gantry tilt speed. Combined with the effect of inertial force, it is easy to roll over longitudinally when the center of gravity has changed caused by an excessive forks lift speed and the forklift gantry tilt speed. However, the lateral stability refers to the ability to prevent electric forklift from rolling over and slipping laterally. When the forklift is driven on a steep slope with an excessively high or partial center of mass, or steering on a curve with a high speed, it is probably to cause lateral rolling over. And when the forklift is driven on a road in water or being braked suddenly when steering, the lateral force will be greater than the adhesive force between the wheel and the grand, then the forklift will slip. Therefore, in order to ensure the security of electric forklift, it is necessary to make the lateral and longitudinal stability conform the control requirement.
In terms of the longitudinal stability, it depends mainly on manmade control on the forks lift speed and the forklift gantry tilt speed. However, the lateral stability is affected by the speed and the steering angle of electric forklift, so it can be improved through the research on the steering speed and the steering angle. The following mainly discussed the control requirements of the lateral stability of electric forklifts.
-
IV. Study on Steering Transmission Ratio for Forklift SBW System
-
A. Handling Stability
Under the driver is not excessive fatigue and tension situations, forklift handling stability refers to that forklift can be in accordance with the driver intention, by operating steering system the steering wheel will travel in a given direction, when encountered outside interference, forklift keeps the ability of stable running with no interference effect[7].
Forklift handling stability is an important evaluation index of forklift active safety, the main influence factors are four physical quantities, respectively, vehicle speed, yaw velocity, lateral acceleration and vehicle mass center sideslip angle. Among them, the yaw velocity is the most important influence factor, it is the control variables to keep the lateral stability.
When the forklift mass center sideslip angle is relatively smaller, forklift cornering capability is reflected by the yaw velocity. When forklift is traveling at a certain speed, and when the yaw velocity becomes large, the turning radius will become small. That is to say, the forklift with higher yaw velocity is allowed higher speed through the same bend road.
-
B. The Concept of Ideal Steering Ratio
In the traditional mechanical steering system, the transmission ratio is a fixed value, this makes the system steering characteristics change in the large range.
In SBW system, the transmission ratio may be changed, by optimal setting of the transmission ratio, the steering characteristics varying with the vehicle speed change will be adjusted, it will make up for the deficiencies of traditional mechanical steering system. This variable transmission ratio is known as the ideal transmission ratio[8].
The ideal transmission ratio and the traditional steering system transmission ratio have the same definition, it is defined as the ratio of steering handle angle 5 and steering wheel angle ^h , by using the symbol i , formula is as follows:
-
(7) Only the small disturbance near the equilibrium state acts on forklift, guarantee the motion equations of vehicle is linear.
-
(8) Forklift mass center and forklift coordinate system origin O are coincident.
i = ^ sw- 5 Wh
In the research of vehicle SBW, the main research is to study the steering gain. One is the ratio of yaw velocity ® and the steering handle angle 5SW, known as the yaw velocity gain, it is an important vehicle steering characteristics, by using the symbol G® , in the steady 5sw state conditions[9], the formula (2) is written as follows:
G ® = —
5 ■ g sw
Another is the ratio of yaw velocity ® and front wheel angle 5 , , by using the symbol G® , in the steady wh 5wh state conditions, the formula (3) is written as follows:
G ®
5 wh
®
5 wh
By formula (1), (2), (3):
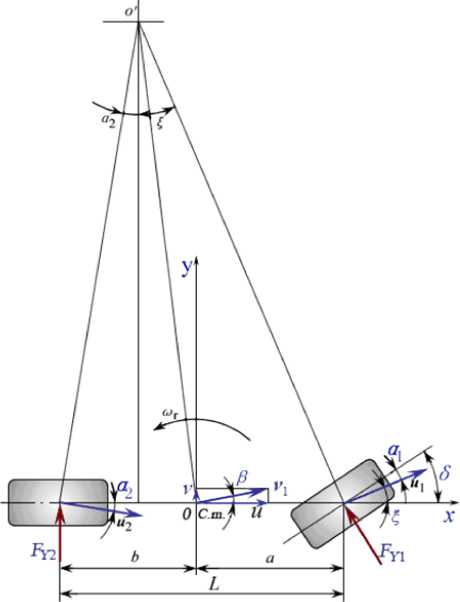
Fig. 2. The two degrees of freedom linear forklift model
i =
G ®
5 wh
®
G 5
Formula (5) is obtained based-on the two-degree-freedom mode:
-
C. Ideal Steering Ratio based-on two-degree-freedom Model
For the convenience of study, the whole forklift model is simplified as a two-degree-freedom linear model, a simplified forklift model[10-13] which only considers the two-degree-freedom of sideslip angle and yaw velocity. Using the vehicle speed and the steering angle of the front wheel as input, sideslip angle and yaw velocity as the output, the vehicle static response is researched. The model is shown in Fig. 2.
Firstly, the following idealized assumptions are needed for the simplification of two-degree-freedom model[14]:
-
(1) The vehicle body only does motion parallel to the ground, side rake angle around x axis, the pitch angle around y axis, displacement around z axis are zero.
-
(2) Forklift drives on the flat road, therefore, ignore the vertical force influence factors and coupling effect that associated with the driving dynamics.
-
(3) Forklift structure is rigid.
-
(4) Ignore the variation of wheel tire characteristics generated by the variation of vertical load.
-
(5) Ignore the influence of the steering system and the air force.
-
(6) Tire sideslip characteristics is in the linear range, the lateral acceleration of vehicle is less than 0.4g.
k 1 I P +-- Y - 5 wh 1 + k 2 I в--Y I = m ( v + u ® )
I u J I u J
a® b® akA в + -5wh I-bk21 в--Y I = I®
I u J I u J
When the forklift sideslip angle в is small, в - tan в = v/, formula (5) is modified as follows:
Ku ® - K2 u в + Кз и 5ь = ®
K 4 и в -f K / - K 6 u 1 ® + K 7 5 wh = в \ u J
Where: к = I z ,^ = ak 1 - bk 2 ,^ _ ak 1 ,
-
1 a 2 k + b 2 k2 2 a 2 kx + b 2 k2 3 a 2 kx + b 2 k2
K = -m , K = ak j^ bk i, к = -m- , K = ^1-
-
4 k + k2 5 k + k2 6 k + k2 7 k + k2
Symbol definition: в — sideslip angle (rad), ® —yaw velocity (rad/s), ®h — the steering angle of the front wheel (rad), m - vehicle quality (kg), a - distance from mass center to the front axle (m), b - distance from mass center to the rear axle (m), I - rotation Inertia of
Vehicle ( kg • m 2 ), kx — Lateral stiffness of front tire (N/rad), k - Lateral stiffness of rear tire (N/rad), u - the speed component in horizontal direction (km/h), v - the speed component in the vertical direction (km/h).
The above formula contains forklift quality, tire lateral stiffness, yaw velocity, sideslip angle etc. the important parameters, reflects the basic characteristics of forklift handling dynamics.
The following equation is obtained based-on the vehicle model:
forklift "floating", transmission ratio should be greater, so the handling stability of forklift is improved[15]. Obviously, the transmission ratio is related to the vehicle speed, it is designed as the function of speed, the function curve is shown in Fig. 4.
?
u ( a + b ) ki k 2 8 wh
( a + b ) 2 kxk2 + ( akx - bk2 ) mu2
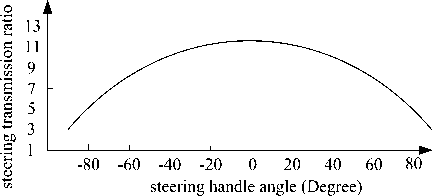
Fig. 3. The relationship between steering handle angle and transmission ratio
So:
G ?
8 wh
u ( a + b ) k,k2
( a + b ) 2 kxk2 + ( akx - bk2 ) mu2
? u ( a + b ) k 1 k 2 1
G 8 = -----9--
"w ( a + b ) kxk2 + ( akx - bk2 ) mu 2 i
Formula (9) is modified as follows:
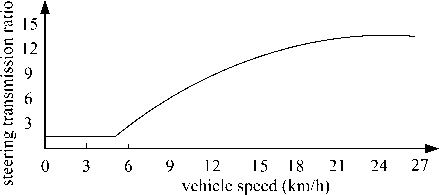
Fig. 4. The relationship between vehicle speed and transmission ratio
г =----
?
8Л
L
m [ a b 1 2
J--- v
L ( k 2 k 1 J
Where: L = a + b . The ideal transmission ratio is not only related with the vehicle parameters, also related with the steering angle, vehicle speed and yaw velocity.
D. Analysis of Influence Factors about the Transmission Ratio of SBW System
When the fork handle angle is small, that is the steering wheel is needed to turn small angle, in order to improve the precision of steering system, it should make the steering system response “dull”, that is to say the transmission ratio value should be greater. When the forklift steering angle is increased, that is the steering wheel is needed to turn large angle, in order to guarantee the response speed, steering system should be "flexible", at this time, transmission ratio value of system should be less, this will reduce the steering handle range of the driver and reduce the burden of driver. Thus, the transmission ratio is related to the steering angle, it is designed as the function of the steering angle, the function curve is shown in Fig. 3.
When the forklift is low speed or static steering, the larger static friction force makes the steering resistance torque is large, in order to make the steering "light", transmission ratio should be smaller, so it will reduce the driver's physical consumption. When the forklift is at high speed, the smaller dynamic friction force makes resistance torque is reduced. In order to prevent the
2) The relationship between transmission ratio and yaw velocity
When the forklift runs at a steady speed, the vehicle is in a steady state, at this time, yaw velocity ? is a fixed value. Therefore, v = 0 , ? = 0 . By formula (10) of two-degree-freedom vehicle model, the steady-state yaw velocity can be obtained as follows:
L sw
®Y = i ( 1 + Ku 2 )
Where: K is the stability coefficient, an important index of forklift steady-state response, the unit is s 2 m 2 , its expression is modified as follows:
m I a
K = —г -
L I k 2

Yaw velocity gain G ? reflects the following
8"W performance of forklift to the input of steering angle, also known as the steering sensitivity. If the yaw velocity is too small, then the response of Forklift is too slow. Otherwise, the response of forklift is too fast, the operation stability will decrease. Yaw velocity gain is an important index of the steering flexibility.
In the traditional mechanical steering system, the transmission ratio is a fixed value, this makes the system steering characteristics varies with the change of vehicle speed. If the drivers control the steering of forklift according to the target direction, drivers must make real
time compensation to the variable steering characteristic. This increases the requirements of driver experience.
Transmission ratio of SBW system is variable, the front wheel angle can be independently controlled, that is the angle transmission ratio of the steering system can be controlled. Seen from formula (11), the transmission ratio and the yaw velocity are the function relation, yaw velocity is controlled through the change of transmission ratio, the ideal handling characteristics is achieved by designing ideal transmission ratio based-on the driver subjective evaluation.
E. Determining Method of the Ideal Transmission Ratio
When the vehicle speed is below a certain value u , the transmission ratio of steering system is a fixed value i . When the steering wheel is turned to the maximum angle 5 , the limit values of forklift front wheel angle is the 5 h , here the steering system transmission ratio is as follow:
min
5 sw max
^ wh max
When the vehicle speed increases to a certain value u , lateral force provided by the tire reaches the limit value. Therefore, steering system transmission ratio can not be increased, that is the maximum value . Thus, ideal max transmission ratio of the steering system is as follow:
i min ,
0 < u < u 1
u ( a + Ь ) k1 k 2 5 sw (14)
2 , u| u u 2
( a + b ) k 1 k 2 - ( ak 1 - bk 2 ) mu 2 ®y
max ,
u > u2
In the case of the example, the related calculation data of TE30 type SBW forklift is shown in Table 1.
Table 1. Forklift Model Parameters Table
Parameters |
The physical meaning of the parameters |
numerical value |
unit |
m |
Vehicle weight |
640 |
kg |
a |
Distance from mass center to the front axle |
0.518 |
m |
b |
Distance from mass center to the rear axle |
0.95 |
m |
k 1 |
Lateral stiffness of front tire |
55856 |
N/rad |
k 2 |
Lateral stiffness of rear tire |
55856 |
N/rad |
u max |
Maximum vehicle speed |
15 |
km/h |
δ sw |
handle angle range |
[-90,90] |
Degree |
δ wh |
Steering wheel angle range |
[-90,90] |
Degree |
According to the formula of steering system ideal transmission ratio, / Vn = 1 . the sensitivity G "' = 0.4 is obtained based-on the test on the driver subjective evaluation and the actual data of forklift according to the State Key Laboratory of automobile dynamic simulation of Jilin University, at this time, driver's subjective feeling is best. To adapt to the various speed and driving conditions, determine , take the integer 13.
max
The above analysis and calculation are static results, but the actual running process of forklift is a dynamic process.
-
F. Control Rules Design of Fuzzy Variable Transmission
Ratio
By the above analysis, transmission ratio and vehicle speed are related with the steering handle angle, but the actual operation is also associated with operating experience and thinking, it is basically not able to establish a precise mathematical model. Fuzzy control has the characteristics of intelligent, it is based on fuzzy logic and fuzzy set theory, and simulates human thinking mode, so it is an ideal method to solve the problem.
Based-on fuzzy rules, the paper designs the nonlinear transmission ratio function on vehicle speed and steering angle. The vehicle speed v and the steering handle angle
5 are used as input, transmission ratio i is used as output, the input quantization factors are respectively K and K , the output proportion factor is K , fuzzy control structure is shown in Fig. 5.
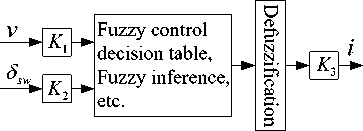
Fig. 5. Structure diagram of two dimensional fuzzy variable transmission ratio
The speed range is [0, 15]km/h for this type of forklift, handle angle range is [-90 ° , 90 ° ], the calculation range of transmission ratio is [1 , 13], proportion factor Kv = 2 , K2 = 1, K3 = 1. In the fuzzy control system, if the control rules are more, the description will be more accurate and vivid, but the more control rules will cause the programming difficult.
According to the control method of expert experience, in general, a linguistic variable selection is suitable for 2 to 10 language value[16,17,18]. Here the linguistic values of language variables v, ^, i are divided into 7 levels, respectively, PB(Positive Big), PM(Positive Mid), PS(Positive Small), Z(Zero), NS(Negative Small), NM(Negative Mid), NB(Negative Big), each level corresponds to a linguistic variables.
The vehicle speed is divided into 7 levels from low to high grade, correspondingly the transmission ratio is divided into 7 levels from low to high grade. From experience, it should improve vehicle "sensitive" at low vehicle speed, also it should improve vehicle "dull" at the high vehicle speed, when the vehicle speed increases in 10 - 25km/h range, transmission ratio will corresponding increase. When the steering handle angle changes from 0 degree to ± 90 degree, the corresponding transmission ratio will change from the high to the low.
Fuzzy rules based on safety considerations are as follows:
increases, but the amplitude of change is not big. This shows that the steering ratio of SBW system is a function of steering angle, the yaw velocity gain will tend to a certain value, so the handling stability of forklift is improved.
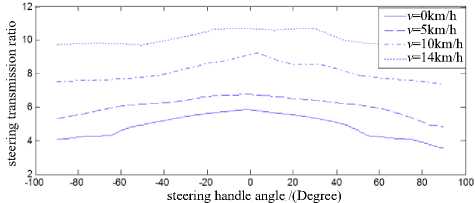
Fig. 7. Relationship between the steering handle angle and steering transmission ratio
V = {NB . NM . NS . Z . PS . PM . PB}, the language values are {0 , 5 , 10 , 15 , 20 , 25 , 30}.
5SW = {NB , NM , NS , Z , PS , PM , PB}, the language values are {-90 , -60 , -30 , 0 , 30 , 60 , 90}.
i = {NB . NM . NS , Z , PS , PM , PB}, the language values are {1 , 2 , 4 , 6 , 8 , 10 , 13}.
According to the fuzzy rules, the steering transmission ratio curve diagram is shown in Fig. 6 by using the fuzzy control toolbox in MATLAB.
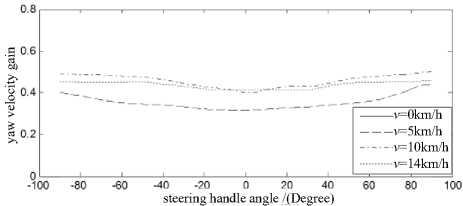
Fig. 8. Relationship between the steering handle angle and yaw velocity gain
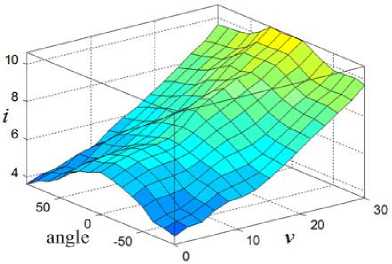
Fig. 6. The curved surface chart of steering transmission ratio
In Fig. 6: i ― steering transmission ratio, angle ― the steering handle angle, v ― forklift speed.
-
V. Simulation and Analysis
Seen from Fig. 7 and Fig. 8, at the same speed, the steering transmission ratio will decrease gradually with the increase of handle angle to the left or right, but the yaw velocity gain tends to a fixed value. With the increase of vehicle speed, steering transmission ratio increases, the corresponding yaw velocity gain slightly
In Fig. 9, the abscissa is vehicle speed, the ordinate is the steering transmission ratio. In Fig. 10, the abscissa is vehicle speed, the ordinate is the yaw velocity gain. Fig. 9 is the change chart of steering transmission ratio when the vehicle speed changes in the range from 0 to 15km/h and the handle steering angle is at 0 degrees, 30 degrees, 60 degrees, 90 degrees. Fig. 10 is yaw velocity gain curve.
Seen from these figures, on the same handle angle, steering transmission ratio will increase with the increase of vehicle speed, the yaw velocity gain will tend to a certain value with the increase of vehicle speed, yaw velocity gain is substantially constant when the vehicle speed reaches 5km/h. In different steering angles, steering transmission ratio will decrease with the increase of handle angle, the yaw velocity gain has a slight increase. This shows that the steering transmission ratio of SBW system will change with the change of vehicle speed, but the yaw velocity gain will tend to a certain value, so the handling stability of forklift is improved.
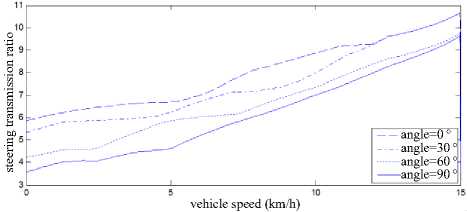
Fig. 9. Relationship between the vehicle speed and steering transmission ratio
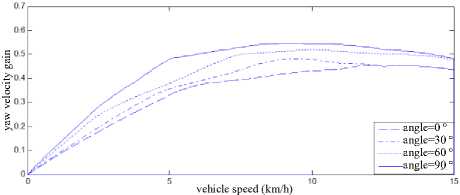
Fig. 10. Relationship between vehicle speed and yaw velocity gain
Seen from the simulation, SBW system will be sensitive in the low-speed steering, be dull in the highspeed steering, and make a few small changes to the sensitivity, the driver will need no excessive sensitivity compensation, so the operation stability of forklift is improved.
Fig. 11 is the comparison chart of yaw velocity gain between traditional steering and SBW steering. Seen from the chart, the yaw velocity gain of SBW system will tend to a steady value along with the increased speed, but the yaw velocity gain of traditional steering system will change greatly along with the speed variation, this shows that the handling stability of SBW system is better than the traditional steering system.
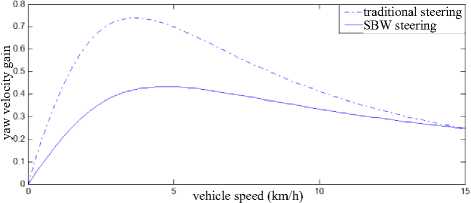
Fig. 11. Relationship comparison between the yaw velocity gain and vehicle speed
Through the study of the transmission ratio of the SBW system based on two-degree-freedom forklift model, steering transmission ratio function on vehicle speed and handle steering angle is proposed based on fuzzy rules. Seen from the MATLAB simulation, the designed Forklift transmission ratio with fuzzy rules not only meets the forklift steering requirements of light sensitive at low speeds and steady heavy at high speed, but also improves the handling stability.
-
VI. Feedback Control of Yaw Velocity
Yaw velocity gain is one of the important indexes to evaluate the handling performance of forklift, and changes with the change of vehicle speed. The same steering angle will produce different yaw velocity at various vehicle speeds, that is the different steering effect. In order to achieve the same steering effect at various speeds, the driver had to make adjustments and compensation to the steering action according to the driving experience, so this will increase the burden for the driver.
It is the control of steady-state significance to ensure the yaw velocity gain does not vary with the change of speed and steering angle, while the actual driving of forklift is a dynamic process. Therefore, In order to ensure the constant yaw velocity gain, Forklift dynamic correction control strategy is proposed based on the steady state control[19]. The strategy will provide feedback on the real-time yaw velocity to the system, and eliminate the difference between actual yaw velocity and ideal yaw velocity, adjust the motion state of forklift actively, and recover stability when the forklift has unstable trend[20]. The principle diagram of yaw velocity feedback is shown in Fig. 12.
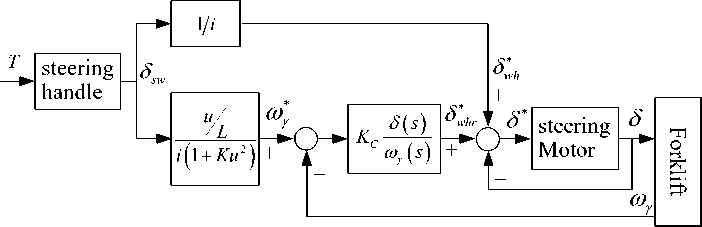
Fig. 12. The principle diagram of yaw velocity feedback
In Fig. 12, T - given torque on the steering handle by the driver, i —the steering transmission ratio, <5 —the angle of steering handle, 3*h — the steering angle of the front wheel determined by the steering handle angle and steering transmission ratio, ® * — yaw velocity obtained from two-degree-freedom linear vehicle model under steady state, 5whr — the compensation angle of the front wheel based-on the yaw velocity feedback control strategy, 5* — the ideal front wheel angle determined by 5 *й and 5 *ftr together, 5 —the actual steering angle.
Fig. 13 and Fig. 14 respectively indicate that forklift is driving at the speed of 10km/h, when 2Nm square wave torque is given on the steering handle, the comparison of the simulation diagram for yaw velocity and sideslip angle is given before and after the yaw velocity feedback dynamic correction. Seen from these figures, the amplitude of forklift yaw velocity and sideslip angle is obviously decreased with dynamic feedback, the response characteristics of forklift is improved, the operation stability of forklift is increased.
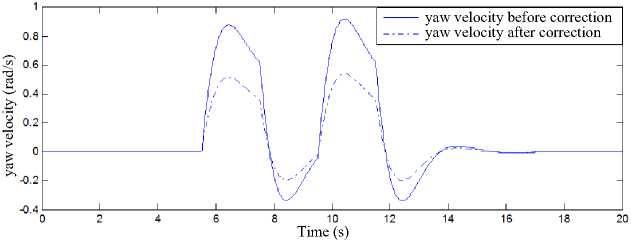
Fig. 13. Comparison chart of yaw velocity before and after correction
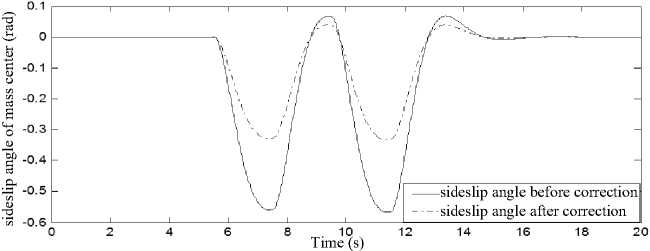
Fig. 14. Comparison chart of sideslip angle before and after correction
-
VII. Conclusion
Combining with the TE30 electric forklift produced by an enterprise, the paper describes the working principle and characteristics of SBW system, introduces the concept of ideal transmission ratio, analyzes the factors affecting the steering transmission ratio, designs the steering transmission ratio function on the vehicle speed and the steering angle based on fuzzy rules. Seen from the simulation results, variable transmission ratio can make the yaw velocity gain close to a constant value, it will greatly improve the steering characteristics, even may achieve the ideal steering characteristics. Through the yaw velocity feedback control strategy, the dynamic correction is used to the front wheel SBW, from the simulation results, the amplitudes of yaw velocity and sideslip angle are decreased, so the handling stability of forklift is improved.
SBW system is not bounded by the mechanical structure, as a significant innovation of vehicle steering system, thus it will provide a huge design space for forklift steering characteristics.
This work is supported by Hefei Banyitong Science and Technology Development Co. Ltd., thanks to senior engineer Junliang Guo, Jin Fan, Zijian Fang, Pengfei Li, Lei Zhang, Jian Xu, Xingzhi Fang for their cooperation and helpful suggestions. Besides, my sincere thanks should go to my graduate students Jianan Wu, Luxi Pan et al.
-
[1] Pan Luxi. “Research of the Forklift Power Assisted Steering System based on Speed Control of Safety Steering,”. Anhui, Hefei: Hefei University of Technology, Master's Degree Thesis , 2014. (in Chinese)
-
[2] Wu Xinli, Luan Ying, Yao Gang. “Discussion on Several Control Forms of Electric Forklift Steering System,” Logistics technology , pp. 43-45, May 2011. (in Chinese)
-
[3] Stanton N.A., Marsden P. “From fly-by-wire to drive-bywire: Safety implications of automation in vehicles,” Safety Science , vol. 24, pp.35-49, January 1996.
-
[4] Halton M., Hayes M.J., Iordanov P. “State-space μ analysis for an experimental drive-by-wire vehicle,” International Journal of Robust and Nonlinear Control , vol. 18, pp. 975992, September 2008.
-
[5] Howser Gerry, McMillin Bruce. “Modeling and reasoning about the security of drive-by-wire automobile systems,” International Journal of Critical Infrastructure Protection , vol. 5, pp. 127-134, Apirl 2012.
-
[6] Wu Jianan. “Research on Control Strategy of Steer-by-wire System for Electric Forklift,” Anhui, Hefei: Hefei University of Technology, Master's Degree Thesis , 2014. (in Chinese)
-
[7] Qin Xubai. “Modeling of Four-wheel Steering Car Virtual Model and Dynamics Simulation,” Jiang Su, Nan Jing: Southeast University, Master's Degree Thesis , 2003. (in Chinese)
-
[8] Yu Leiyan, Lin Yi, Shi Guobiao. “Research of Steer-by-wire System’s Steering Ratio,” Transactions of the Chinese Society for Agricultural Machinery , vol. 38, pp. 190-192, August 2007. (in Chinese)
-
[9] Yao Jiangyun, Kong Feng, Wu Fangyuan. “Research on Intelligent Control Strategy for Steering Ratio of Steer-by-wire System,” Computer Measurement &Control , vol. 20, pp. 678-686, March 2012. (in Chinese)
-
[10] Liu yong. “Analysis of Automotive Steering-by-wire
System,” Hube, Wuhan, Wuhan University of Technology, Master's Degree Thesis, 2005. (in Chinese)
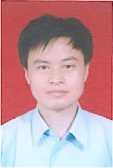
Benxian Xiao was born on April 4, 1964 in Anhui, China. He received the B.Sc degree and the M.Sc degree and Ph.D. degree in Electrical Engineering and Automation from Hefei University of Technology, Hefei, China, in 1986 and 1989 and 2004, respectively.
Since 1989, he has been with the Department of Automation, School of
In recent years, completed the enterprise funded projects more than 10, included Electric Power-assisted Steering (EPS) controller for Electric Forklift, Steer-by-Wire (SBW) System for Electric Forklift, Automated Mechanical Transmission (AMT) controller, the automatic carrier and navigation AGV etc.
Список литературы The Research of Fuzzy Variable Transmission Ratio for Steer-by-wire System of Electric Forklift
- Pan Luxi. “Research of the Forklift Power Assisted Steering System based on Speed Control of Safety Steering,”. Anhui, Hefei: Hefei University of Technology, Master's Degree Thesis, 2014. (in Chinese)
- Wu Xinli, Luan Ying, Yao Gang. “Discussion on Several Control Forms of Electric Forklift Steering System,” Logistics technology, pp. 43-45, May 2011. (in Chinese)
- Stanton N.A., Marsden P. “From fly-by-wire to drive-by-wire: Safety implications of automation in vehicles,” Safety Science, vol. 24, pp.35-49, January 1996.
- Halton M., Hayes M.J., Iordanov P. “State-space μ analysis for an experimental drive-by-wire vehicle,” International Journal of Robust and Nonlinear Control, vol. 18, pp. 975-992, September 2008.
- Howser Gerry, McMillin Bruce. “Modeling and reasoning about the security of drive-by-wire automobile systems,” International Journal of Critical Infrastructure Protection, vol. 5, pp. 127-134, Apirl 2012.
- Wu Jianan. “Research on Control Strategy of Steer-by-wire System for Electric Forklift,” Anhui, Hefei: Hefei University of Technology, Master's Degree Thesis, 2014. (in Chinese)
- Qin Xubai. “Modeling of Four-wheel Steering Car Virtual Model and Dynamics Simulation,” Jiang Su, Nan Jing: Southeast University, Master's Degree Thesis, 2003. (in Chinese)
- Yu Leiyan, Lin Yi, Shi Guobiao. “Research of Steer-by-wire System’s Steering Ratio,” Transactions of the Chinese Society for Agricultural Machinery, vol. 38, pp. 190-192, August 2007. (in Chinese)
- Yao Jiangyun, Kong Feng, Wu Fangyuan. “Research on Intelligent Control Strategy for Steering Ratio of Steer-by-wire System,” Computer Measurement &Control, vol. 20, pp. 678-686, March 2012. (in Chinese)
- Liu yong. “Analysis of Automotive Steering-by-wire System,” Hube, Wuhan, Wuhan University of Technology, Master's Degree Thesis, 2005. (in Chinese)
- Zheng Hongyu. “Research on Road Feeling and Active Steering Control Strategy for Vehicle Steer-By-Wire System,” Jilin University, Master's Degree Thesis, 2009. (in Chinese)
- Baslamisli S.C., Polat I., Kose I.E. “Gain Scheduled Active Steering Control Based on a Parametric Bicycle Model,” Proceedings of the 2007 IEEE Intelligent Vehicles Symposium, Istanbul, Turkey, 2007:1168-1173.
- Basa K., Zemva A. “Simulation and Verification of a Dynamic Model of the Electric Forklift Truck,” Intelligent Automation and Soft Computing, vol. 17, pp.13-30, January 2011.
- Wen Yi. “Control Method and Simulation Analysis of Electric Power Steering System on Car,”. Guangdong, Guangzhou: South China University of Technology, Master's Degree Thesis, 2010. (in Chinese)
- Ou Yanghai. “Study of Control Algorithm for Steer by Wire,” Hube, Wuhan: Wuhan University of Technology, Master's Degree Thesis, 2010. (in Chinese)
- Li Hongming, Bi Xiang, Wei Zhenchun, etc. “Research on Rule Description Method based on Fuzzy Control,” Journal of Hefei University of Technology, vol. 34, pp. 493-496, Apirl 2011. (in Chinese)
- Anupama Kaushik, A.K. Soni, Rachna Soni. “A Type-2 Fuzzy Logic Based Framework for Function Points,” I.J. Intelligent Systems and Applications, vol. 5, pp. 74-82, March 2013.
- Azita Yazdanpanah, Farzin Piltan, Ali Roshanzamir, Marjan Mirshekari, Narges Gholami mozafari. “Design PID Baseline Fuzzy Tuning Proportional-Derivative Coefficient Nonlinear Controller with Application to Continuum Robot,” I.J. Intelligent Systems and Applications, vol. 6, pp. 90-100, May 2014.
- Zong Changfu, Zheng Hongyu, Tian Chengwei, etc. “Steady-state Gain and Dynamic Feedback Correction Algorithm for Steer-by-wire,” Automotive Engineering, vol.29, pp. 686-691, August 2007. (in Chinese)
- Zheng Hongyu, Zong Changfu, Tian Chengwei, etc. “Control Algorithm for Steer-by-wire System with Ideal Steering Ratio,” Journal of Jilin University (Engineering and Technology Edition), vol.37, pp. 1230-1235, June 2007. (in Chinese).