Управление рисками производственной площадки CAM-центр Самарский университет. Обзор и первые шаги
Автор: Колеганова Е.А., Хаймович А.И.
Журнал: Известия Самарского научного центра Российской академии наук @izvestiya-ssc
Рубрика: Машиностроение и машиноведение
Статья в выпуске: 2 т.24, 2022 года.
Бесплатный доступ
В статье предложен метод оценки рисков на производстве, в его основе сочетание таких инструментов, как анкетирование, матрица рисков, графовый метод и метод иерархий. Апробация метода была проведена на примере производственной площадки CAM-центра Самарского университета. По результатам анкетирования работников CAM-центра были проанализированы и выявлены причинно-следственные связи рисков. С использованием графоаналитической модели по разработанной методике произведена идентификация критических по значимости рисков, связанных с проблемами планирования выполнения сложных заказов.
Оптимизация производства, оценка рисков, графовая модель, управление рисками, высокотехнологичное производство
Короткий адрес: https://sciup.org/148324480
IDR: 148324480 | DOI: 10.37313/1990-5378-2022-24-2-48-57
Текст научной статьи Управление рисками производственной площадки CAM-центр Самарский университет. Обзор и первые шаги
Работы выполнены при финансовой поддержке Минобрнауки России в рамках реализации комплексного проекта по созданию высокотехнологичного производства по теме:
«Организация высокотехнологичного производства индустриальных ГТД с интеллектуальной системой конструкторско-технологической подготовки для повышения функциональных характеристик» (Соглашение о предоставлении гранта № 075-11-2021-042 от 24.06.2021 г.)
ПРОБЛЕМА УПРАВЛЕНИЯ ПРОИЗВОДСТВОМ
Для небольших предприятий, работающих в области металлообработки высокотехнологичной продукции, например, производства пресс-форм для литья под давлением, критичным является неравномерное распределение портфеля заказов в течение года. Эта неравномерность приводит к нарушению договорных сроков, авральной загрузке и стрессу сотрудников с одной стороны, простаиванию производства и связанным с ним потерями с другой. Отмеченное является следствием проблемы управления производством, что предъявляет особые требования к менеджменту рисков.
Для выявления ключевых рисков и тестирования разработанного метода их идентификации была рассмотрена производственная площадка Самарского университета, существующая более 10 лет. При наличии высококвалифицированных работников, качественного оборудования и возможности выполнять сложные заказы,
на этом предприятии часто возникает ситуация просрочки заказов.
Целью организации управления рисками на предприятии является снижение неопределенности и выявление скрытых резервов производства [1]. Следует отметить, что ценность предприятия возрастает, если руководство утверждает стратегию и цели для достижения оптимального баланса между целями роста и доходности и связанными с ними рисками, а также эффективно и результативно использует ресурсы для достижения целей организации [2].
ЗАДАЧИ ИССЛЕДОВАНИЯ
В этой связи ставятся две задачи:
-
- разработки системы оценки рисков для увеличения прозрачности процесса производства;
-
- разработка цифровой системы для мониторинга ситуации и оценки новых заказов.
Производственная площадка оборудована 8-ю станками, среди которых: токарно-фрезерный обрабатывающий центр, токарный станок, фрезерный обрабатывающий центр, фрезерный 3-х координатный станок с ЧПУ, 5-ти координатный фрезерный обрабатывающий центр, электроэрозионный проволочно-вырезной станок, электроэрозионный прошивочный станок, шлифовально-заточный центр с ЧПУ. Часть за- казов, включая термообработку, выполняется по аутсорсингу.
Так как портфель заказов ориентирован на единичное производство, то выполнение каждого заказа сопровождается индивидуальными рисками. Вместе с тем все риски имеют общие черты и, следовательно, могут быть проклассифицированы и ранжированы.
СИСТЕМА УПРАВЛЕНИЯПРОИЗВОДСТВЕННЫМИ РИСКАМИ
Чем более риски диверсифицированы, тем меньше могут быть потери от взятого в отдельности риска и тем меньше его влияние в целом на систему. Следует отметить, что виды рисков взаимозависимы и взаимосвязаны. Для удобства работы с диверсифицированными рисками их классифицируют [3]. Существует множество классификаций, но вопрос оптимальных критериев остается открытым. При идентификации рисков учитываются период их образования, метод подсчета, ареал охвата, причины и сфера возникновения, тип последствий.
Система управления рисков включает следующие этапы [2-7]:
-
. Планирование управления рисками;
-
. Идентификация или выявление рисков;
-
. Качественная оценка рисков;
-
. Количественная оценка рисков;
-
. Планирование реагирования;
-
. Осуществление реагирования
Среди методов идентификации рисков выделяют 3 группы: анализ опыта уже реализованных проектов, анализ текущего проекта, анализ возможных будущих условий. Инструменты первой группы – анализ лучших практик организации, анализ архивных документов, второй – анализ документации, анализ сетевых графиков и календарных планов работ (если есть), третьей – экспертные методы, включающие мозговой штурм, метод Дельфи, анкетирование и интервьюирование, а также диаграммы влияния и Ишикавы, SWOT-анализ, деревья отказов.
Методы количественного анализа включают карты рисков, FMEA-анализ, метод парных сравнений Саати, матрица «Вероятность-по-следствия», диаграмма Ишикавы.
В [8] приведен пример применения карты рисков в авиакомпании. Здесь же используется анкетирование и экспертная оценка. Диаграмма Ишикавы применяется в [9] для оценки пожарных рисков на территории объектов нефтепереработки. Как видно в [10], FMEA-анализ может включать в себя некоторые из методов. В [10] и [11] подробно рассмотрен процесс проведения FMEA-анализа на практике.
Для производственной площадки CAM-центр были рассмотрены организационные, технические и производственные риски. Основой для идентификации и количественной оценки рисков является анкетирование. Априори было очевидно, что планирование и регламентирующая бизнес-процессы документация отсутствуют. При анкетировании был проведен опрос ключевых сотрудников и выявлено мнение руководства на существующее положение. В процессе опроса список выявленных рисков был доработан. Оценка вероятности возникновения каждого риска дана по десятибалльной шкале, 0 – риск отсутствует, 10 – риск сопровождает производственные процессы. Также дана оценка критичности возникновения риска по шкале от 1 до 3, где 1 – слабое влияние, 2 – допустимо, 3 – критично.
Выявленные риски классифицируем по двум группам – технические и организационные (таблица 1). К организационным рискам относим риски, связанные с управлением, планированием, внутренним контролем, организацией работы. К техническим – риски, обусловленные непредсказуемым функционированием технических систем и некорректной работой с ними.
Для наглядного представления результатов опроса построен граф с обозначенными усредненными оценками вероятности возникновения и критичности событий на дугах графа и над ними соответственно (рисунок 1). Вершины графа f1-f25 – это соответствующие им риски. Так как оценка производственного коллектива субъективная, а выводы необходимо сделать объективные, учитываются факты о предыдущей деятельности производства, в случае разницы оценок более 7 пунктов принимается оценка человека, наиболее близкого к оцениваемой деятельности, с учетом его результатов в ней. В случае несоответствующих оценок полученным результатам производства их значение корректируется.
Ранее оценка рисков на данном производстве не проводилась, при заключении договоров и выполнении заказов риски не учитывались. Уже 2 событие графа говорит об отсутствии планирования на данном производстве. Без стратегического и оперативного планирования оценка сроков и стоимости производства берется интуитивно. Таким образом, выполнить заказы в срок для производственной площадки скорее счастливая случайность и удача, чем закономерность. Связано это с тем, что отсутствие планирования, прозрачности процессов, приоритетности заказов служит причиной неравномерного распределения работ в течение года и скопления заказов с горящими сроками и, следовательно, нарушением части из них, а также повышением уровня стресса и ошибок по невнимательности, в том числе из-за многозадачности. Также отсутствие
Таблица 1. Риски производственной площадки CAM-центр
По результатам опроса замечено, что оценка многих пунктов руководства и рабочих значительно различается. Это говорит о том, что данные риски не обсуждаются коллективно и не анализируются, а, значит, не учитываются при заключении новых договоров.
Организационными вопросами из команды в основном занимается один человек, его оценка и оценка руководящего производственной площадкой сильно разнятся по организационным рискам, таким как добавление незапланированных срочных заказов без учета уже имеющейся загрузки оборудования, отсутствие прозрачности в сроках и приоритетах, нехватка инструментов/ проблема закупки, нехватка персонала, поставщик сорвал срок, проблемы логистики при доставке заготовок, проблемы поиска поставщика материалов. Это говорит о том, что в команде данные вопросы не обсуждаются, при заключении новых договоров эти риски не учи-
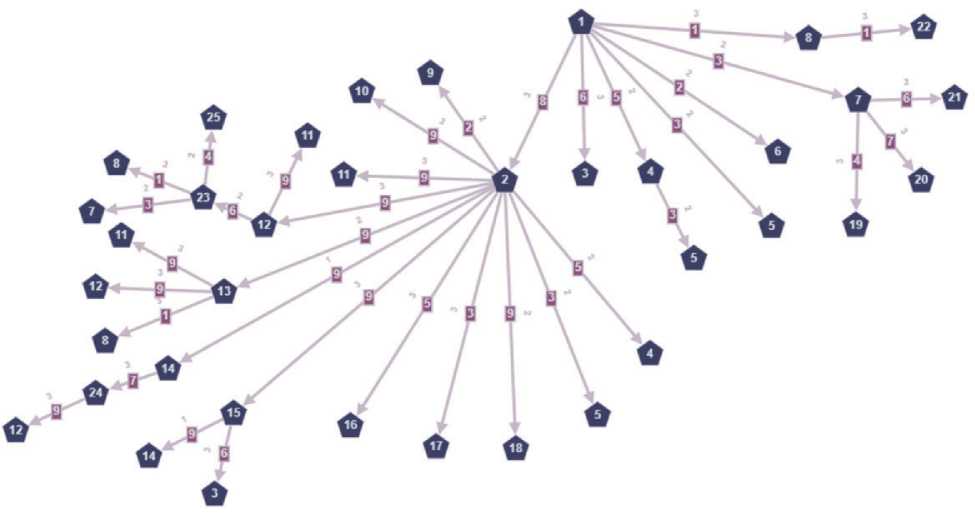
Рис. 1. Развернутый граф с экспертными оценками
-
1 – организационные риски
-
2 - Отсутствие планирования
-
3 - проблема закупки инструментов
-
4 - нехватка персонала
-
5 - Отсутствие мотивации
-
6 - некачественная заготовка под операцию
-
7 - Проблема общения с подрядчиками
-
8 - Проблема общения с заказчиком, ТЗ
-
9 - Экономия времени на стратегическом планировании
-
10 - Простои оборудования
-
11 - Срыв сроков заказов
-
12 - Скопление заказов с горящими сроками
-
13 - Отсутствие системы приоритетов заказов
-
14 - Неспособность предоставить план работ высшему руководству для согласованного добавления новых заказов, в т.ч. срочных
-
15 - отсутствие прозрачности в сроках и приоритетах
-
16 - нехватка инструментов
-
17 - нехватка материалов
-
18 – Экономия времени на детальной разработке технологии
-
19 - Поставщик сорвал срок
-
20 - Заказчик меняет требования к изделию
-
21 - Проблемы логистики при доставке заготовок
-
22 - Повышение уровня стресса работников
-
23 - Увеличение ошибок по невнимательности
-
24 - Добавление незапланированных срочных заказов без учета уже имеющейся загрузки оборудования
-
25 - Проблемы поиска поставщика материалов
тываются, проблемы эти неисследованные и не анализировались производственной командой.
Такие риски, как неверный технологический маршрут и операционная технология, неверный расчет времени обработки, большое количество доработок, отсутствие единого информационного пространства в команде рисками не считаются и также не учитываются при заключении договоров. Технологический маршрут существу- ет в виде приблизительного наброска, расчет времени обработки не производится, берется интуитивно, брак подгоняется под требования заказчика, на что тратится дополнительное время, отсутствие единого информационного пространства и работа в разных программах считается нормой, позволяющей перепроверять друг за другом расчеты и схемы, увеличение времени работы за этот счет также не учитывается.
Анализ опроса показал, что на производственной площадке высокие организационные риски, которые не учитываются и ранее не анализировались и незначительные технические и производственные риски. Это говорит о том, что на площадке не налажено управление процессами, однако на ней работают профессиональные высококвалифицированные рабочие. Проблемы решаются по мере поступления, плана работы и развития здесь нет.
Анкетирование проводилось в виде опроса каждого сотрудника индивидуально, некоторые вопросы были заданы в двух плоскостях – оценка риска при работе самого сотрудника и оценка риска при работе на том же месте другого человека. Также вопросы были о производстве в течение всего времени работы этих сотрудников. В будущем будет проведено подобное анкетирование применительно к действующим производственным проектам.
Инструментами качественной оценки рисков являются анализ чувствительности, сценарный анализ, деревья решений, метод теории графов, имитационное моделирование.
Анализ чувствительности зарекомендовал себя при оценке рисков инвестиций. [12] Как видно из [13], [14], сценарный анализ может быть разной степени детализации и отлично себя проявляет для стратегического анализа. Имитационное моделирование также проявляет свои многочисленные плюсы, например, в работах [15], [16]. В [17] подробно описывается метод иерархий или метод Саати, приводятся примеры использования как для дискретных, так и для непрерывных значений. В [18] с помощью графо-матричной модели определяются ключевые показатели производственной системы, а также эта модель поддерживает такие управленческие решения, как определение ассортиментной структуры для равномерной нагрузки, цен и другие.
В настоящем исследовании для анализа был применен графоаналитический метод как наи- более наглядный многозадачный метод, позволяющий дойти до корневых причин явно видимых следствий. Модель организационных рисков в виде графа причинно-следственных связей представлена на рисунке 2.
Для проведения качественной оценки рисков определяется иерархия факторов. Пусть задано множество факторов, составляющих модель предметной области

Задается на множестве факторов F отношение подчиненности RF, отражающее для каждой пары факторов
П(Яр) = {тг0 \t,j = 1...Q, элементы которой
-
1, если фактор f j подчинен фактору ^ (i ^ j), v (О, если факторы fj и f; не связаны друг с другом, либо i = j.
Для приведенного выше графа матрица выглядит следующим образом:
/О 1 ••■ 0\
_ / 0 0 0 0 | \ = 0 ■■■ ": . \о о ■■■ о/
Суммы строк и столбцов этой матрицы характеризуют роли факторов в иерархии.
^(тг) = 2}=!^, 5,(тг) = Е'=1ТГ0.
Фактор fj является корневым, если сумма соответствующего ему столбца равна нулю. Фактор fi образует лист иерархии, если сумма соответствующей ему строки равна нулю. [Анохин]
5<(тг) = ...;
Фактор 1 является корневым, факторы 3, 5,
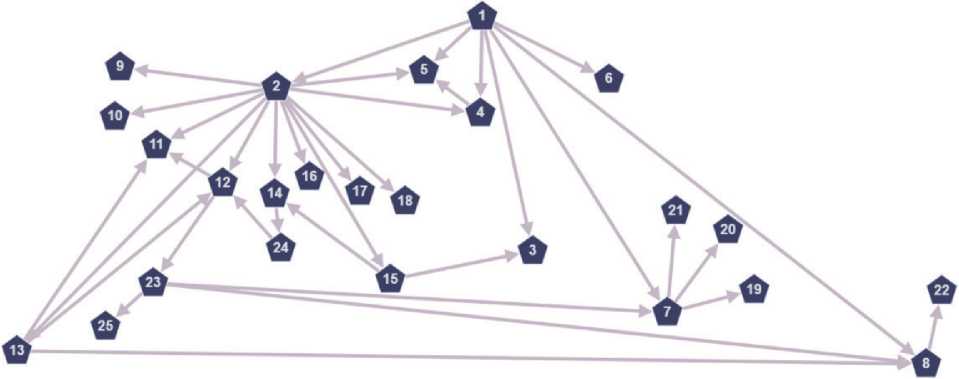
Рис. 2. Граф причинно-следственных связей организационных рисков

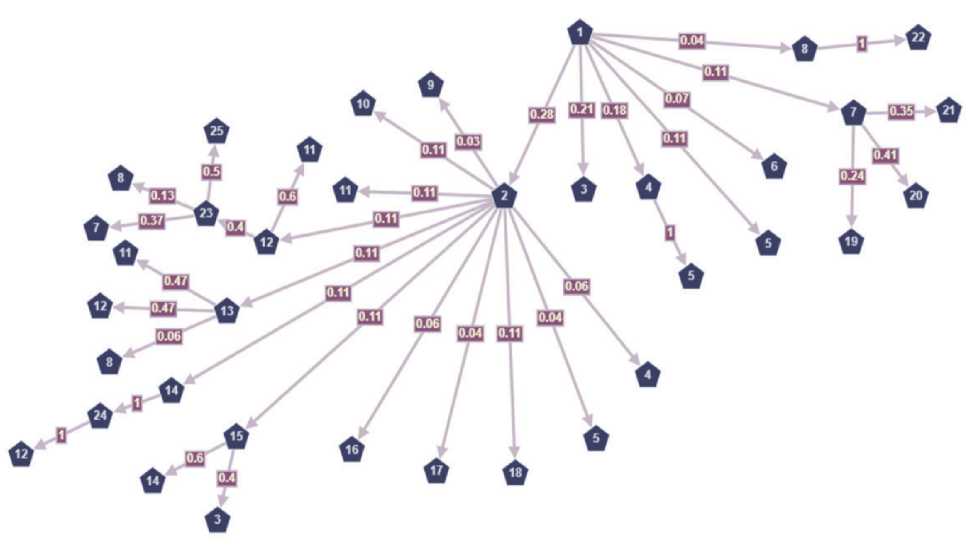
Рис. 3. Граф с назначенными весами по частоте возникновения событий
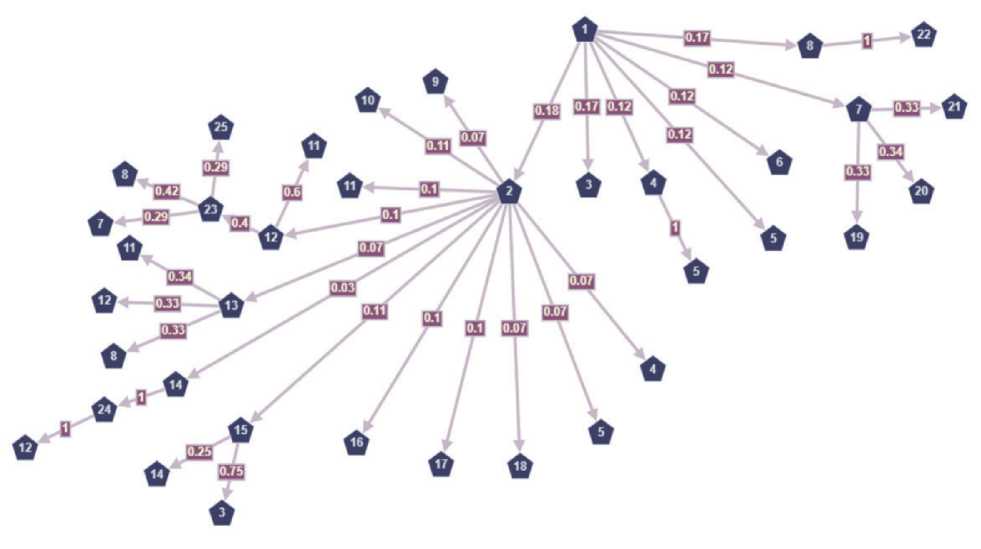
Рис. 4. Граф с назначенными весами по критичности рисков
-
6, 9, 10, 11, 16, 17, 18, 19, 20, 21, 22, 25 – листами иерархии.
Введем показатель относительной значимости λ ij порожденного фактора fj для исходного фактора fi - λ ij ∈ [0,1] ( λ ij=0, если факторы fi и fj не связаны друг с другом). Заменив коэффициенты πij на λ ij, получаем матрицу относительных значимостей факторов Λ ={ λ ij | i,j=1... l} [19].
где
Si Y – значимость каждого зависимого фактора j , связанного с фактором i.
На рисунках 3 и 4 представлен развернутый граф с назначенными весами по частоте возникновения событий и по критичности. Условная вероятность возникновения рисков в числителе, критичность – в знаменателе.
Чтобы исключить зависимость результата от количества событий внутри корневых рисков, производим нормирование всех событий в каждой ветке относительно наиболее критичного события в этой ветке (или вероятного, если оце-
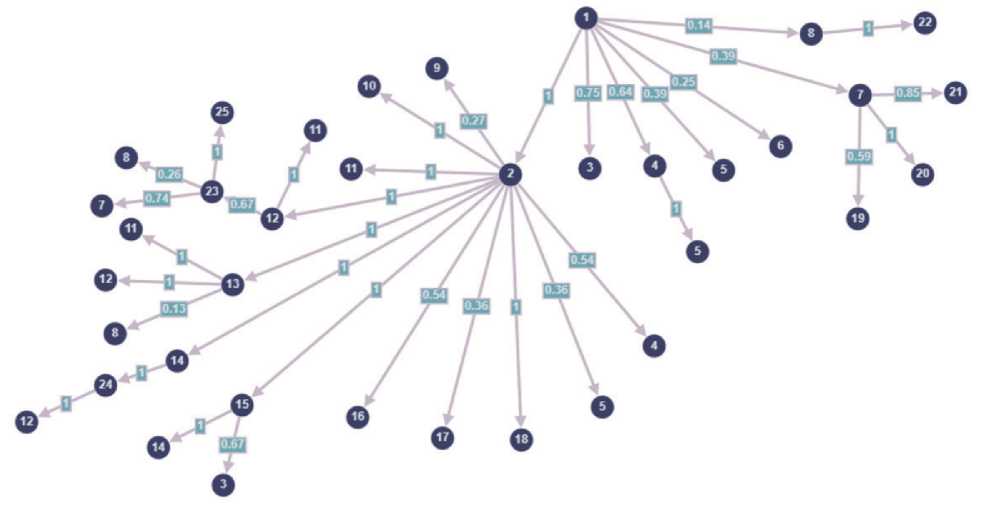
Рис. 5. Граф с пересчитанными весами по вероятности возникновения
нивается вероятность возникновения). Для этого выбираем событие с максимальным весом и условно принимаем его вес равным 1. Остальные события нормируем относительно выбранного.
g ij
A y <Ш
( AjX ax = max K }, j = 1.... / .
Полученные значения вероятности возник- новения и критичности представлены на рисунке 5. Аналогичные действия проведены для графа с назначенными весами по критичности рисков, результаты приведены на рисунке 7.
Расчет условной вероятности возникновения событий и критичности проведен по следующей формуле, включающей корневые для риска события:
.
Для удобства анализа можно ввести показатель значимости, который будет равен произведению оценки критичности на оценку вероятности.
Коэффициенты, полученные в результате оценки вероятности возникновения, критичности и значимости каждого события, запишем в таблицу 2.
Анализ показывает, что наиболее вероятными из рисков являются 11 - срыв сроков заказов и 12 - скопление заказов с горящими сроками, за ними следует риск 14 - неспособность предоставить план работ высшему руководству для согласованного добавления новых заказов. Все три риска являются следствием риска 2 - отсутствие планирования, ввиду его повышенной частоты возникновения.
Наименее вероятными рисками являются 22 -повышение уровня стресса работников, 6 – постав- ка некачественной заготовки на операцию, 9 - экономия времени на стратегическом планировании.
По критичности самым опасным является также риск 11 - срыв сроков заказов. Следующими по критичности: 8 – проблема общения с заказчиком, некорректное ТЗ и 5 - отсутствие мотивации.
Менее опасными среди названных рисков являются 24 - добавление незапланированных срочных заказов без учета уже имеющейся загрузки оборудования, 25 - проблемы поиска поставщика материалов и 23 - увеличение ошибок по невнимательности.
Видно, что событие 11 - срыв сроков заказов - лидирует и по вероятности возникновения, и по критичности. По значимости оно идет первым. Также значимым событием, на которое нужно обратить внимание, является событие 12 - скопление заказов с горящими сроками. Риск 2 - отсутствие планирования – включает все риски, опасные и по вероятности возникновения, и по критичности, и по значимости. Эти риски необходимо проработать в первую очередь.
В процессе набора статистики по новым заказам и уточняющего анкетирования исполнителей, рассчитанные веса могут быть скорректированы.
ВЫВОДЫ
В результате проведенного анализа была апробирована методика выявления ключевых рисков, основанная на графоаналитическом методе описания событий, приводящих к возникновению рисков. После обработки результатов анкетирования производственной площадки Самарского университета – САМ-центр, были классифицированы основные риски, связан-
Таблица 2. Коэффициенты событий графа организационных рисков
Риск |
Вероятность возникновения |
Критичность |
Значимость |
2 |
1 |
1 |
1 |
3 |
1,42 |
1,94 |
2,75 |
4 |
1,18 |
1,3 |
1,53 |
5 |
1,39 |
1,97 |
2,73 |
6 |
0,25 |
0,67 |
0,16 |
7 |
1,13 |
1,09 |
1,23 |
8 |
0,53 |
2,15 |
1,13 |
9 |
0,27 |
0,63 |
0,17 |
10 |
1 |
1 |
1 |
11 |
3 |
2,43 |
7,29 |
12 |
3 |
1,78 |
5,34 |
13 |
1 |
0,63 |
0,63 |
14 |
2 |
0,6 |
1,2 |
15 |
1 |
1 |
1 |
16 |
0,56 |
0,9 |
0,5 |
17 |
0,36 |
0,9 |
0,32 |
18 |
1 |
0,63 |
0,63 |
19 |
0,98 |
0,65 |
0,63 |
20 |
0,39 |
0,67 |
0,26 |
21 |
0,33 |
0,65 |
0,21 |
22 |
0,14 |
0,94 |
0,13 |
23 |
0,67 |
0,6 |
0,4 |
24 |
1 |
0,27 |
0,27 |
25 |
0,67 |
0,42 |
0,28 |
ные со сроками выполнения производственных заказов, выявлены связи между рисками и определены весовые значения вероятности и критичности рисков. С использованием графоаналитической модели по разработанной методике были идентифицированы критические по значимости риски, связанные с проблемами планирования выполнения сложных заказов.
Список литературы Управление рисками производственной площадки CAM-центр Самарский университет. Обзор и первые шаги
- Caraiman, A. Risk management in corporate governance I A. Caraiman, D. Mates II Business Excellence: Proceedings of the International Conference on Business Excellence (July, 2020). -2020. - P.182-201.
- COSO Enterprise Risk Management – Integrated Framework, 2004. Executive Summary, 2004. - 111 p.
- Ramos, A.G. Risk Management Perspectives to approach risk / A.G. Ramos // Third International Conference on Business Sustainability: Proceedings of the Third International Conference on Business Sustainability (November; 2013)
- A guide to the project management body of knowledge (PMBOK guide). - Sixth Edition. - Project Management Institute, Pennsylvania, 2017. - 579 p.
- ISO 31000:2018 Risk management - Guidelines. - 2th edition. - International Organization for Standardization, 2018. - 22 p.
- TSO Managing Successful Projects with PRINCE2. -6th edition. - Norwich: TSO (The Stationary Office), 2017. - 413 p.
- Николаенко, В.С. Риск, риск-менеджмент и неопределенность: уточнение понятий / В.С. Николаенко // Государственное управление. Электронный вестник. - 2020. - № 81. - С. 91-119.
- Чагина, О.А. Разработка системы риск-менеджмента как части целевого управления авиакомпании / О.А. Чагина // Научный Вестник МГТУ ГА. - 2010. - № 156. - С. 75-80.
- Гудин, С.В. Проблемы управления пожарными рисками на территории объектов нефтепереработки с использованием современных программных продуктов / С.В. Гудин, Р.Ш. Хабибулин, Д.Н. Рубцов // Пожаровзрывобезопасность технологических процессов и оборудования. - 2015. - № 12. - С. 40-45.
- Муха, Ар.А. Управление процессом разработки сложных технических систем и процессов. Особенности применения FMEA-анализа / Ар.А. Муха // Математические машины и системы. - 2012. -№ 2. - С. 168-176.
- Садченко, Ю.В. Планирование процесса метрологического обеспечения производства на основе оценки рисков / Ю. В. Садченко, Ю. Г. Малахова // Решетневские чтения. - 2016. - С. 391-393.
- Козлова, Е.С. Анализ инвестиционной чувствительности / Е.С. Козлова, В.П. Нежевин // Хроно-экономика. - 2018. - № 1 (9). - С. 49-52.
- Галкина, А.Н. Теоретические основы сценарного подхода к анализу инновационной деятельности / А. Н. Галкина // Инновационная деятельность. -2012. - № 37. - С. 35-43.
- Лаева, Т.В. Сценарный анализ как основа стратегического планирования в организации / Т.В. Лаева // Менеджмент в России и за рубежом. - 2006. - № 2. - С. 56-63.
- Бондарева, И.О. Многоуровневое управление организационными системами на основе моделирования и каскадирования рисков / И.О. Бондарева, А. А. Ханова // Прикаспийский журнал: управление и высокие технологии. - 2021. - № 4. - С. 18-26.
- Колеганова, Е.А. Методика определения сроков изготовления новых заказов на единичном производстве и снижения рисков производственной деятельности / Е.А. Колеганова, В.В. Кокарева, А.И. Хаймович // Известия Самарского научного центра Российской академии наук. - 2021. - № 4. - С. 27-34.
- Whitaker, R. The analytic hierarchy process-what it is and how it is used / R. Whitaker // Mathematical Modelling. - 1987. - № 9(3-5). - P. 161-176.
- Данилов, Г.В. Моделирование влияния ассортимента продукции на основные показатели предприятия / Г. В. Данилов, Е. С. Войнова, И. Г. Рыжова // Управленческий анализ. - 2012. - № 15(270). -С. 40-46.
- Анохин, А.Н. Методы экспертных оценок: Учебное пособие / А. Н. Анохин. М.: Редакционно-изда-тельский отдел ИАТЭ г. Обнинск, 1996. - 148 с.