Влияние микроструктуры и фазового состава на трибологические свойства NiCrBsI лазерных покрытий
Автор: Соболева Н.Н., Малыгина И.Ю., Осинцева А.Л., Поздеева Н.А.
Журнал: Известия Самарского научного центра Российской академии наук @izvestiya-ssc
Рубрика: Системные разработки трибологии машин и приборов
Статья в выпуске: 4-3 т.13, 2011 года.
Бесплатный доступ
Изучено влияние микроструктуры и фазового состава на трибологические свойства Cr-Ni покрытий, получен-ных методом газопорошковой лазерной наплавки. Установлены механизмы разрушения покрытий при абразив-ном изнашивании по электрокорунду и по карбиду кремния. Показано влияние среды на интенсивность изна-шивания при трении скольжения.
Лазерная наплавка, микротвердость, абразивное изнашивание, износ при трении скольжения
Короткий адрес: https://sciup.org/148200225
IDR: 148200225
Текст научной статьи Влияние микроструктуры и фазового состава на трибологические свойства NiCrBsI лазерных покрытий
температуру плавления и способствует формированию твердых фаз. Кремний добавляется для увеличения самофлюсующихся свойств. Углерод образует твердые карбиды с повышенной твердостью, что обеспечивает износостойкость покрытий [6].
Существует множество работ, посвященных изучению твердости и износостойкости NiCrSiB покрытий [4-10], однако лишь немногие из покрытий получены лазерной наплавкой [2, 11]. При этом отмечается различие свойств покрытий, полученных лазерной наплавкой и другими метВодсавмяизи[12с , э1т3и].м, представляет интерес изучение трибологических свойств NiCrSiB лазерных наплавок различных составов в условиях абразивного изнашивания и в условиях трения скольжения в различных средах с использованием электронной сканирующей микроскопии для анализа механизмов изнашивания. Этим аспектам и посвящена данная работа.
Материалом для покрытий служили порошки марок ПГСР-2 и ПГН-10Н-01 (табл. 1). Наплавку порошков на пластины из стали Ст3 размером 100X 100X18 мм проводили с использованием непрерывного СО 2 -лазера при мощности излучения 1,4– 1,6 кВт, скорости 180 мм/мин, расходе порошка 4,9 г/мин, размере лазерного пятна на поверхности 6X 1,5 мм. Порошковая смесь гранулометрического состава 40–100 мкм транспортировалась в зону наплавки инертным газом – аргоном при давлении 0,5 атм. Для уменьшения поверхностных напряжений наплавка осуществлялась в два прохода путем наложения одного слоя на другой.
Таблица 1. Химический состав порошков
Марка порошка |
Содержание элементов, мас. % |
|||||
С |
Сr |
Ni |
Fe |
Si |
B |
|
ПГСР-2 |
0,3 |
13,5 |
основа |
<5,0 |
2,4 |
2,1 |
ПГН-10Н-01 |
0,8 |
16,0 |
основа |
5,0 |
4,0 |
3,5 |
Структуру, химический и фазовый состав покрытий изучали с применением сканирующего электронного микроскопа VEGA II XMU, оборудованном волнодисперсионным (Inca Wave 700) и энергодисперсионным (INCA Energy 450 XT) микроанализаторами, и рентгеновского дифрактометра SHIMADZU XRD-7000. Микротвердость измеряли на микротвердомере Leica VMHT. Для проведения исследований из пластин с нанесенными покрытиями вырезали образцы размером 7х7х18 мм (наплавленный слой – на торцевой поверхности). Изменение структуры, микротвердости и химического состава по глубине зоны лазерного воздействия изучали на поперечных шлифах.
Интенсивность абразивного изнашивания по глубине покрытий определяли в процессе многократных испытаний, приводящих к последовательному удалению (изнашиванию) поверхностного слоя. Испытания проводили при скольжении торцевых поверхностей (7 X 7 мм) наплавленных образцов по закрепленному абразиву – корунду и карбиду кремния зернистостью ~160 мкм со средней скоростью 0,175 м/с, при нагрузке 49 Н, длине рабочего хода 100 мм, пути трения отдельного испытания 9,0–18,0 м, поперечном смещении образца за один двойной ход 1,2 мм. Испытания торцевых поверхностей (7X 7 мм) наплавленных образцов в условиях трения скольжения осуществляли на воздухе и в без-окислительной среде аргона в паре с пластиной из стали Х12М твердостью 58–59 HRC э при возвратно-поступательном скольжении со средней скоростью 0,07 м/с, нормальной нагрузке 294 Н, длине рабочего хода образца 40 мм и пути трения 80 м. Коэффициент трения определяли как отношение силы трения к нормальной нагрузке f=F/N, где F – сила трения, Н; N – удельная нагрузка, Н. Интенсивность изнашивания рассчитывали по формуле Ih=Q/ρSL, где Q – потери массы образца, г; ρ – плотность материала, г/см3; S – геометрическая площадь контакта, см2; L – путь трения, см. Для расчета удельной работы изнашивания применяли формулу W=fNLρ/Q, где f – коэффициент трения; N – удельная нагрузка, Н; L –путь трения, м; ρ – плотность материала, г/см3; Q – потери массы образца, г.
Поверхности покрытий после абразивного изнашивания и после трения скольжения изучали с помощью сканирующего электронного микроскопа VEGA II XMU.
В результате двухслойной лазерной наплавки на поверхности стали Ст3 сформировались покрытия толщиной 1,2-1,6 мм, которые по всей толщине характеризуются достаточно равномерным распределением структурных составляющих (рис. 1). Структура покрытий имеет дендритное строение, направление дендритов соответствует градиенту температур при кристаллизации. По данным рентгеноструктурного и микрорентгеноспектрального анализа, металлическую основу покрытий ПГСР-2 и ПГН-10Н-01 составляет эвтектика, представляющая собой у-твердый раствор на основе никеля и Ni3B. Основными упрочняющими фазами покрытий являются карбиды и бориды хрома. Карбидная фаза в покрытии ПГСР-2 представлена дисперсными карбидами хрома типа Cr23C6 (микротвердостью 9,9-11,3 ГПа). В покрытии ПГН-10Н-01, вследствие более высокого содержания углерода и бора по сравнению с ПГСР-2, присутствуют более твердые (Н=16,2-19,3 ГПа) и более крупные карбиды типа Cr7C3, а также бориды CrB (Н>20ГПа).
На рис. 2 представлены изменения микротвердости и трибологических характеристик по глубине рассматриваемых покрытий. Рис. 2 показывает, что рассматриваемые покрытия имеют практически постоянные уровни микротвердости и интенсивности абразивного изнашивания по всей толщине наплавленного слоя. Резкий рост интенсивности абразивного изнашивания и падение твердости происходит лишь в переходном слое – при переходе от материала покрытия к стальной основе, где столь же резко изменяется структура и химический состав материала.
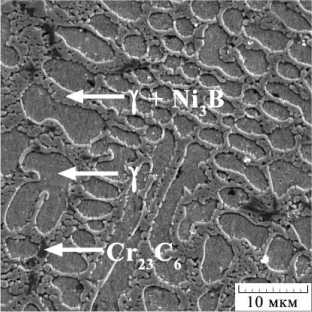
а
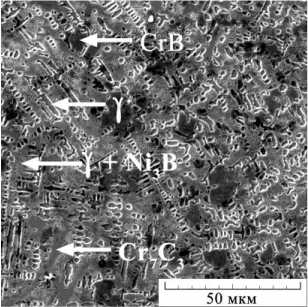
б
Рис. 1. Микроструктура покрытий: а – ПГСР-2, б – ПГН-10Н-01
Покрытие ПГН-10Н-01 характеризуется повышенной микротвердостью (6,8–9,7 ГПа) по сравнению с покрытием ПГСР-2 (4,3–5,7 ГПа), а также более низкими уровнями интенсивности изнашивания (повышенной износостойкостью) и коэффициента трения при скольжении по корунду и карбиду кремния (табл. 2). Это обусловлено наличием в составе покрытия ПГН-10Н-01 большей доли упрочняющих карбидных и боридных фаз – Cr 7 C 3 и CrB – значительно более прочных и крупных, чем карбид Cr23C6, который является упрочняющей фазой в покрытии ПГСР-2.
Видно, что у покрытия ПГСР-2 наблюдаются близкие уровни интенсивности абразивного изнашивания при испытании по электрокорунду (Al 2 O 3 ) и карбиду кремния (SiC) (см. рис. 2 а , табл. 2).
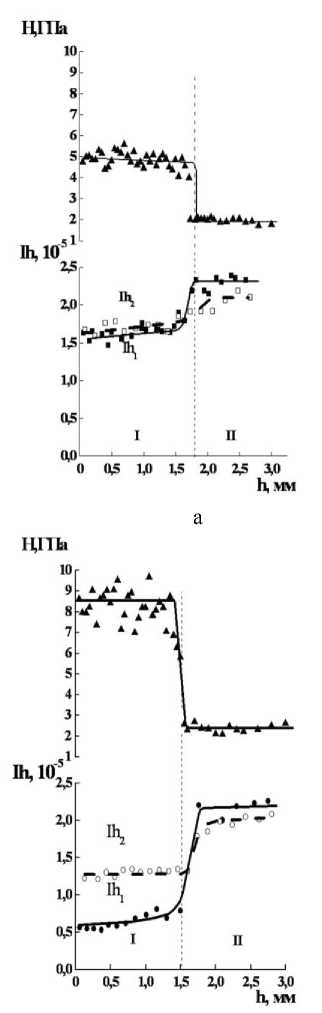
б
Рис. 2. Изменение по толщине покрытий (h) микротвердости (Н) и интенсивности абразивного изнашивания при испытании по электрокорунду (Ih 1 ) и карбиду кремния (Ih2):а - ПГСР-2; б - ПГН-10Н-01;
II – основной металл (сталь Ст3)
Таблица 2. Интенсивность изнашивания
Ih, коэффициент трения f и удельная работа изнашивания W покрытий при испытании по закрепленному абразиву различного вида
Пок-ры-тие |
электрокорунд (Al 2 O 3 ) |
карбид кремния (SiC) |
||||
Ih, 10-5 |
f |
W, кДж/ 3 см |
Ih, 10-5 |
f |
W, кДж/ 3 см |
|
ПГСР-2 |
1,7 |
0,78 |
47,0 |
1,8 |
0,69 |
41,0 |
ПГН-10Н-01 |
0,6 |
0,49 |
75,5 |
1,4 |
0,57 |
40,8 |
Представленные на рис. 3а и 3б участки покрытия ПГСР-2 после абразивного изнашивания при испытании по электрокорунду и по карбиду кремния характеризуются наличием борозд и отвалов; механизмом изнашивания для обоих случаев является микрорезание.
В этом случае продукты изнашивания содержат большое количество микростружки, образующейся в процессе одноактного отделения микрообъема металла от поверхности трения [14]. Это связано с тем, что упрочняющая фаза данного покрытия (Cr 23 C 6 , Н=9,9-11,3 ГПа) существенно уступает в твердости и электрокорунду (20 ГПа), и тем более карбиду кремния (30 ГПа), не препятствуя развитию микрорезания, что и объясняет близкие уровни интенсивности изнашивания при испытании по разным абразивам.
Покрытие ПГН-10Н-01 имеет меньшую интенсивность изнашивания (большую износостойкость) (рис. 2б, табл. 2). Интенсивность изнашивания покрытия ПГН-10Н-01 по сравнению с покрытием ПГСР-2 в 1,3 раза выше при испытании по карбиду кремния и в 2,7 раза выше при абразивном испытании по электрокорунду.
Анализ поверхностей изнашивания с помощью сканирующей электронной микроскопии показал, что при испытании покрытия ПГН-10Н-01 по электрокорунду наблюдается нарушение условий микрорезания (рис. 3в), так как твердые фазы (Cr7C3, Н=16,2-19,3 ГПа и CrB, H>20ГПа), присутствующие в покрытии, сравнимые с твердостью электрокорунда (20 гПа), сдер-живают процессы микрорезания. На поверхности (рис. 3в) видны протяженные выглаженные участки пластического деформирования, обусловленные механизмом пластического оттеснения материала, видно выполировывание твердых фаз в результате многократного деформирования без резания. При таком разрушении в продуктах изнашивания содержится большое количество частичек в виде чешуек [14]. Следует отметить, что твердость матричной фазы покрытия γ мала, поэтому пластическое оттеснение происходит не на всей поверхности покрытия.
Однако твердость карбида кремния (30ГПа) выше твердости всех упрочняющих фаз покрытия ПГН-10Н-01, поэтому в этом случае, как и для покрытия ПГСР-2, реализуется механизм изнашивания путем микрорезания (рис. 3г). Присутствующие упрочняющие фазы – карбиды и бориды – не вырываются, а свободно перерезаются зернами карбида кремния. Для рассмотренных случаев реализации механизма микрорезания (испытания покрытий по карбиду кремния и покрытия ПГСР-2 по корунду) отмечаются близкие значения удельной работы изнашивания W=40,8-47,0 кДж/см3 (табл. 2).
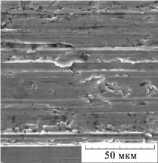
а
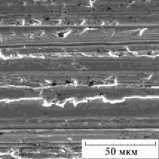
б
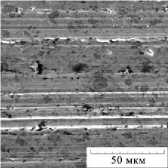
в
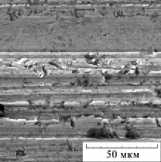
г
Рис. 3. Поверхности покрытий после абразивного изнашивания: а, б – покрытие ПГСР-2;
в, г – покрытие ПГН-10Н-01; а, в – испытания по электрокорунду; б, г – испытания по карбиду кремния.
Из рис. 4 а, 4б видно, что после испытаний на трение скольжения по стали Х12М покрытия ПГСР-2 происходит адгезионное схватывание, характеризуемое высокими уровнями интенсивности изнашивания (8,5*10-8 при испытании в аргоне и 8,9*10-8 при испытании на воздухе, см. табл. 3).
Таблица 3. Интенсивность изнашивания Ih и коэффициент трения f покрытий при трении по стали Х12М
Покрытие |
Испытания в аргоне |
Испытания на воздухе |
||
Ih, 10-8 |
f |
Ih, 10-8 |
f |
|
ПГСР-2 |
8,5 |
0,63 |
8,9 |
0,43 |
ПГН-10Н-01 |
0,5 |
0,41 |
4,4 |
0,40 |
Более прочное покрытие ПГН-10Н-01 за счет наличия крупных упрочняющих фаз характеризуется ограниченными процессами схватывания при трении скольжения в среде аргона (рис. 4в). Интенсивность изнашивания покрытия ПГН-10Н-01 в среде аргона более чем в 18 раз ниже, чем у покрытия ПГСР-2.
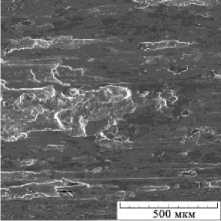
а
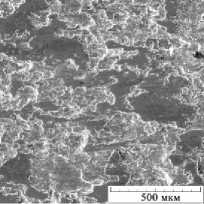
б
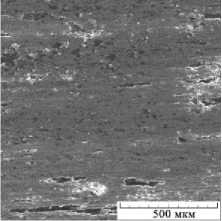
в
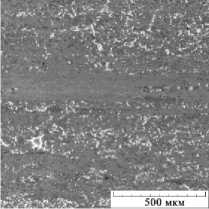
г
Рис. 4. Поверхности покрытий после трения скольжения по стали Х12М: а, б – покрытие ПГСР-2; в, г – покрытие ПГН-10Н-01; а, в – испытания в аргоне; б, г – испытания на воздухе.
Заключение:
Наличие более крупных и твердых упрочняющих фаз (Cr7C3, CrB) при увеличении легированности Cr-Ni покрытий обеспечивает повышенную твердость и пониженную интенсивность изнашивания покрытия ПГН-10Н-01 по сравнению с покрытием ПГСР-2 с упрочняющей фазой Cr 23 C 6 .
Установлено, что наличие высокопрочных фаз (Cr7C3, CrB) твердостью 16-20ГПа в покрытии ПГН-10Н-01 приводит к резкому снижению интенсивности изнашивания в 1,3-2,7 раза по сравнению с покрытием ПГСР-2. На основании электронно-микроскопических исследований показано, что у покрытия ПГН-10Н-01 при воздействии абразивов различной твердости наблюдается смена механизма изнашивания: микрорезание при испытании по карбиду кремния, царапание при испытании по электрокорунду, что приводит к снижению интенсивности изнашивания по электрокорунду покрытия ПГН-10Н-01.
При исследование механизмов изнашивания при трении скольжения установлено адгезионное схватывание для покрытия ПГСР-2 при испытании в аргоне и на воздухе. Наличие крупных высокопрочных фаз в покрытии ПГН-10Н-01 при испытании в безокислительной атмосфере (среде аргона) практически подавляет процессы адгезионного схватывания, что приводит к снижению интенсивности изнашивания. Однако при испытании покрытия ПГН-10Н-01 на воздухе за счет охрупчивания кислородом воздуха поверхностного слоя, происходит локально хрупкое разрушение микроучастков покрытия, что выражается в резком росте (на порядок) интенсивности изнашивания покрытия ПГН-10Н-01 при испытании на воздухе (по сравнению с испытаниями в среде аргона).
Работа выполнена при частичной поддержке проекта ОФИ УрО РАН № 11-1-11-УТ и проекта № 09-Т-1-1002 по программе ОЭММПУ РАН №13 .
Список литературы Влияние микроструктуры и фазового состава на трибологические свойства NiCrBsI лазерных покрытий
- Tobar M.J., Álvarez C., Amado J.M., Rodríguez G., Yánez A. Morphology and characterization of laser clad composite NiCrBSi=WC coatings on stainless steel//Surface and Coatings Technology. 2006. Vol. 200. P. 6313-6317.
- Huang S.W., Samandi M., Brandt M. Abrasive wear performance and microstructure of laser clad WC/Ni layers//Wear. 2004. Vol. 256. P. 1095-1105.
- Ming Q., Lim L.C., Chen Z.D. Laser cladding of nickel-based hardfacing alloys//Surface and Coatings Technology. 1998. Vol. 106. P. 174-182.
- Gurumoorthy K., Kamaraj M., Prasad Rao K., Sambasiva Rao A., Venugopal S. Microstructural aspects of plasma transferred arc surfaced Ni-based hardfacing alloy//Material Science and Engineering A. 2007. Vol. 456. P. 11-19.
- González R., Cadenas M., Fernández R., Cortizo J.L., Rodríguez E. Wear behaviour of flame sprayed NiCrBSi coating remelted by flame or by laser//Wear. 2007. Vol. 262. P.301-307.
- Miguel J.M., Guilemany J.M., Vizcaino S. Tribological study of NiCrBSi coating obtained by different processes//Tribology International. 2003. Vol. 36. P. 181-187.
- Kim H.-J., Hwang S.-Y., Lee C.-H., Juvanon P. Assessment of wear performance of flame sprayed and fused Ni-based coat-ings//Surface and Coatings Technology. 2003. Vol.172. P. 262-269.
- Sari N.J. Yilmaz M. Improvement of wear resistance of wire drawing rolls with Cr-Ni-B-Si+WC thermal spraying powders//Surface and Coatings Technology. 2008. Vol. 202. P. 3136-3141.
- Rodríguez J., Martín A., Fernández R., Fernández J.E. An experimental study of wear performance of NiCrBSi thermal spray coatings//Wear. 2003. Vol. 255. P.950-955.
- Martín A., Rodríguez J., Fernández J.E., Vijande R. Sliding wear behaviour of plasma sprayed WC-NiCrBSi coatings at different temperatures//Wear. 2001. Vol. 251. P. 1017-1022.
- Fernández E., Cadenas M., Gonsález R., Navas C., Fernández R., De Damborenea J. Wear behaviour of laser clad NiCrBSi coating//Wear. 2005. Vol. 259. P. 870-875.
- Xu G., Kutsuna M., Liu Z., Zhang H. Characteristics of Ni-based coating layer formed by laser and plasma cladding processes//Materials Science and Engineering A. 2006. Vol. 417. P. 63-72.
- Григорьянц А.Г., Сафонов А.Н. Методы поверхностной лазерной обработки: Учеб. пособие для вузов. М.: Высш. шк., 1987. 191 с.
- Макаров А.В., Коршунов Л.Г., Счастливцев В.М., Солодова И.Л., Яковлева И.Л. Структура и абразивная износостойкость закаленных и отпущенных заэвтектоидных углеродистых сталей//Физика металлов и металловедение. 2004. Т. 98, № 4. С. 96-212.
- Korshunov L.G., Makarov A.V., Chernenko N.L. Ultrafine Structures Formed upon Friction and Their Effect on the Tribological Properties of Steels//The Physics of Metals and Metallography. 2000. Vol. 90. № S1, P. 48-58.
- Макаров А.В., Анисимова Л.И., Коршунов Л.Г. Влияние больших концентраций водорода (0,10-0,65 мас. %) на трибологические свойства -титанового сплава ВТ35//Трение и износ. 2002. Т. 23, № 5. С. 541-550.