Влияние обработки поверхности пластин на скорость термического окисления карбида кремния
Автор: Евишев А.В., Ивенин С.В.
Журнал: Огарёв-online @ogarev-online
Статья в выпуске: 11 т.3, 2015 года.
Бесплатный доступ
Исследуется влияние качества обработки поверхности пластин 4H-SiC на скорость термического окисления карбида кремния в атмосфере сухого кислорода. Показано, что на поверхностях пластин с большей шероховатостью при прочих равных условиях образуется более толстая окисная пленка.
Карбид кремния, механическая обработка, окисление, окисная пленка, шероховатость
Короткий адрес: https://sciup.org/147248871
IDR: 147248871
Текст научной статьи Влияние обработки поверхности пластин на скорость термического окисления карбида кремния
Известно, что скорость термического окисления кремния и карбида кремния зависит от таких характеристик полупроводникового материала как уровень легирования, кристаллографической ориентации, качество подготовки поверхности [1].
В литературе имеется достаточно много сведений о влиянии уровня легирования и кристаллографической ориентации на скорость термического окисления кремния и карбида кремния. Однако исследований влияния качества обработки поверхности очень мало, а исследования по карбиду кремния совсем отсутствуют. В книге «Технология СБИС» под редакцией С. Зи приводятся некоторые сведения о влияние повреждений поверхности кремния на скорость роста окисных пленок. Тем не менее, результаты исследований различных авторов противоречивы и неоднозначны. В основном повреждения поверхности создавались путем ионной бомбардировки различными ионами, и только бомбардировка поверхности кремния ионами аргона однозначно приводила к ускорению процесса окисления [1].
При изготовлении полупроводниковых приборов на основе любого материала обязательной операцией в технологическом маршруте является механическая обработка, которая включает резку, шлифовку и полировку полупроводниковых пластин. Операция резки не обеспечивает требуемой точности и качества поверхностей пластин. Полученные пластины имеют различные погрешности формы (неплоскостность, непараллельность плоскостей, изгиб, шероховатость и др.), значительный нарушенный слой и довольно большие отклонения по толщине. Поэтому необходима дальнейшая обработка для улучшения точности и качества их поверхностей. Эту обработку подразделяют на шлифовку и полировку, которые осуществляются с использованием алмазных паст и мелкодисперсных абразивов с различной величиной зерна. И все же после всех операций механической обработки остается нарушенный слой, который существенным образом влияет как на дальнейшую технологическую обработку (эпитаксия, травление, окисление, фотолитография), так и на параметры полупроводникового прибора.
Карбид кремния обладает рядом особенностей, которые проявляются как в процессе механической обработки, так и в процессе термического окисления. Так, скорость термического окисления в SiC существенно меньше, чем в Si. Глубина нарушенного слоя не столь велика как в Si [2]. Поэтому исследование влияния результатов механической обработки на процесс термического окисления является актуальной задачей технологии изготовления приборов на основе карбида кремния.
В данной работе мы исследовали влияние шероховатости поверхности пластин 4H-SiC на скорость термического окисления в атмосфере сухого кислорода. Измерение шероховатости поверхности и толщины окисной пленки проводилось с помощью профилометра P-16+ KLATencor. Для эксперимента были взяты две полированные половинки одной пластины SiC. На рисунке 1 (а, б) представлены фотографии пластин, выбранных для эксперимента.
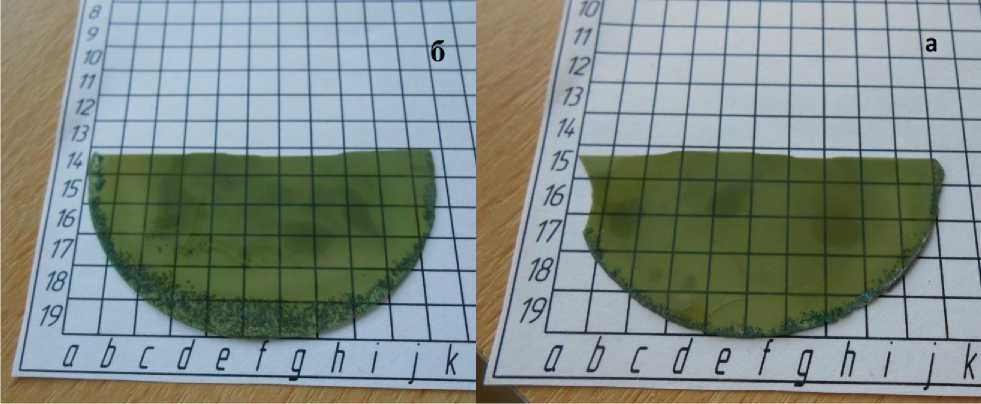
Рис. 1. Фотографии образцов 4H-SiC: (а) – образец; (б) – образец.
Обе половинки предварительно были исследованы на шероховатость. Параметры шероховатости можно увидеть на рисунке 2 [3].
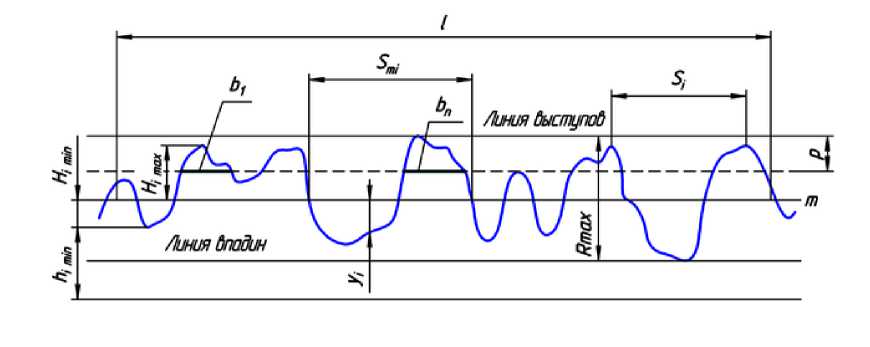
Рис. 2. Нормальный профиль и параметры шероховатости поверхности.
На рисунке схематично показаны параметры шероховатости: l – базовая длина (длина линии, используемой для выделения неровностей); m – средняя линия профиля; S mi – средний шаг неровностей профиля; S i – средний шаг местных выступов профиля; H i max – отклонение пяти наибольших максимумов профиля; H i min – отклонение пяти наибольших минимумов профиля; h i max – расстояние от высших точек пяти наибольших максимумов до линии параллельной средней и не пересекающей профиль; h i min – расстояние от низших точек пяти наибольших минимумов до линии параллельной средней и не пересекающей профиль; R max – наибольшая высота профиля; y i – отклонения профиля от линии m; p – уровень сечения профиля; b n – длина отрезков, отсекаемых на уровне p.
Для определения класса шероховатости поверхности чаще используют следующие параметры (которые определяются на базовой длине l ):
-
1. R a – среднее арифметическое отклонение профиля;
-
2. R z – высота неровностей профиля по десяти точкам.
Измерение шероховатости проводились на 4 участках каждого образца (рис. 3). Координаты каждого участка фиксировались.
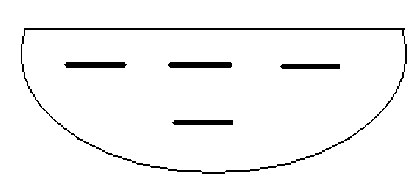
Рис. 3. Расположение базовых линий для измерения шероховатости на каждом образце.
Результаты измерений шероховатости для одного участка на каждом образце представлены на рисунках 4 и 5.
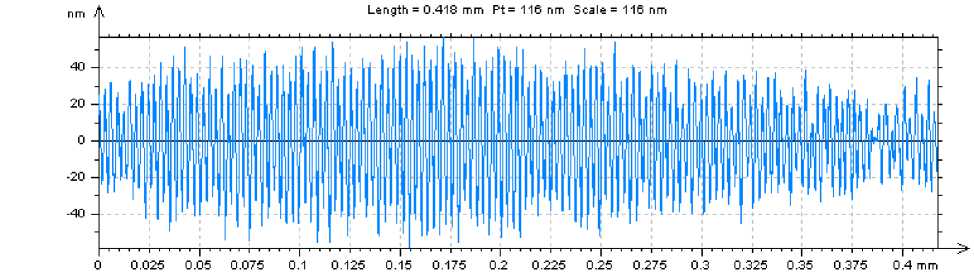
Рис. 4. Двумерный профиль пластинки (а).
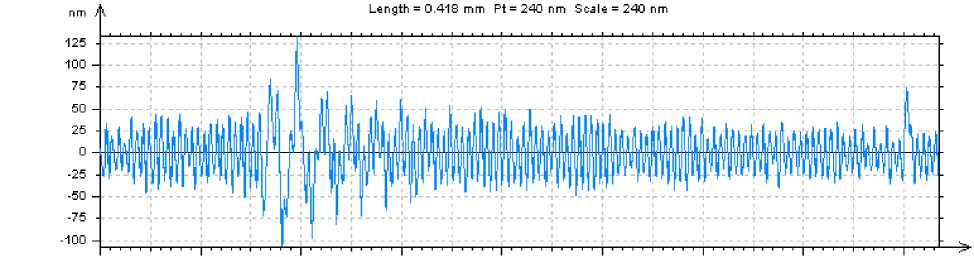
a 0.025 0.05 0.075 0.1 0.125 0.15 0.175 0.2 0.225 0.25 0.275 0.3 0.325 0.35 0.375 0.4 mm
Рис. 5. Двумерный профиль пластинки (б).
Из анализа двумерных профилей следует, что на разных участках поверхности образца шероховатость меняется в достаточно широких пределах. Есть участки, где шероховатость находится в пределах 100–120 нм. Есть отдельные участки, где шероховатость достигает значения 145 и 240 нм. Из представленных двумерных профилей видно, что при одинаковой длине базовой линии 0,418 мм для образца (а) R z = 114 нм, R a = 24,1 нм, R шах = 116 нм, а для образца (б) эти значения равны 235 нм, 25,3 нм и 240 нм, соответственно.
Процесс термического окисления проводился в диффузионной печи СДОМ3-100 в сухом кислороде при 11500С в течение 5 часов для обеих образцов одновременно. Полученный окисел локально стравливался, образовывалась ступенька окисел/стравленный участок. После чего снимался профиль данной ступеньки, ее высота принималась за толщину окисной пленки. Результаты измерений представлены на рисунках 6 и 7.
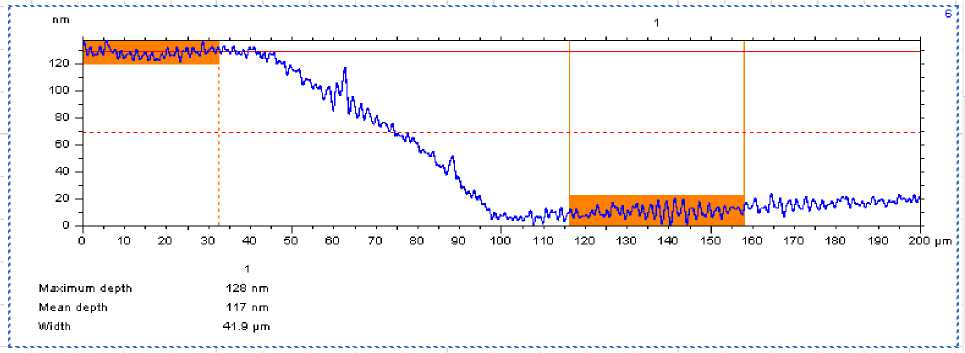
Рис. 6. Профиль ступеньки, снятый на образце (а) после окисления в сухом кислороде в течение 5 часов.
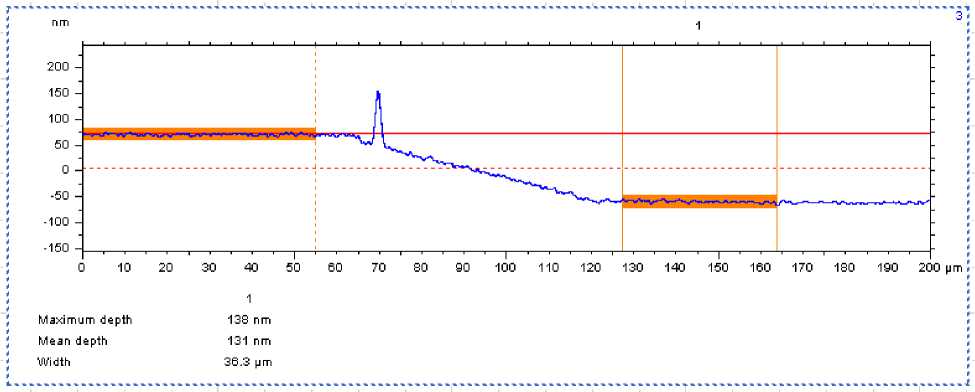
Рис. 7. Профиль ступеньки, снятый на образце (б) после окисления в сухом кислороде в течение 5 часов.
На рисунке 6 показан профиль ступеньки, снятый на образце (а), подвергнутом окислению в сухом кислороде в течение 5 часов. Значение толщины окисла равно 117 нм.
На рисунке 7 показан профиль ступеньки, снятый на образце (б), подвергнутом окислению в сухом кислороде в течение 5 часов. Значение толщины окисла равно 136 нм.
Аналогичные результаты получены и на остальных участках каждого образца. Большим значением параметров шероховатости R a , R z и R max соответствовало большее значение толщины окисной пленки полученной термическим окислением в атмосфере сухого кислорода.
Следует отметить, что взятые для исследования образцы 4H-SiC имеют низкий уровень качества обработки поверхности, Ra > 20 нм, а в технологических процессах SiC приборов часто требуется более высокий класс обработки поверхности, при котором влияние шероховатости на скорость термического окисления будет не столь заметно.
Список литературы Влияние обработки поверхности пластин на скорость термического окисления карбида кремния
- Технология СБИС: в 2 кн./под ред. С. Зи., пер. с англ. -кн. 1. -М: Мир, 1986. -404 с.
- Сысоев А. А. Процессы обработки затравок для выравнивания совершенных объемных монокристаллов полупроводникового карбида кремния методом ЛЭТИ: дисс. …канд. тех. наук. -СПб., 2001. -105 с. EDN: NLVGHL
- Шероховатость поверхности. Параметры и характеристики. ГОСТ 2789-73, издание официальное. -М.: Стандартинформ, 2006. -15 с.