Влияние скорости протягивания прокатываемой полосы на возникновение автоколебаний натяжной станции стана холодной прокатки 2000
Автор: Краснов М.Л., Качурин П.Л., Вишняков С.Г., Чернявский А.О., Васильев В.А., Савченко Ю.И., Ницкий А.Ю., Иванов А.И.
Рубрика: Технология
Статья в выпуске: 4 т.23, 2023 года.
Бесплатный доступ
При возникновении автоколебаний ролика натяжной станции петленакопителя стана холодной прокатки во время эксплуатации появляются трещины на наружных поверхностях ролика. С целью определения причин возникновения автоколебаний натяжной станции травильного агрегата стана 2000 проведен отсеивающий промышленный эксперимент по оценке влияния технологических и диагностических факторов на ее состояние. Базы данных технологических и вибрационных параметров стана и ролика натяжной станции представляют собой единую гибридную базу данных, объединенную графической оболочкой. Промышленный эксперимент - это, как правило, пассивный эксперимент. То есть эксперимент, в котором экспериментатор не имеет возможности вмешиваться в процесс проведения эксперимента. Но на стане холодной прокатки один отдельно взятый независимый эксперимент требует всего 5-6 минут. Каждый рулон - разной толщины, ширины, различного химического состава и, соответственно, с различными механическими свойствами. Кроме того, различна скорость прокатки, натяжение полосы, обжатие полосы, различные силы трения на натяжной станции и т. д. Каждый рулон - это независимый эксперимент. Если информация о технологических и диагностических параметрах хранится достаточно долго, например год или два, этой информации достаточно, чтобы работать с ней как с лабораторным экспериментом: с запаздыванием по времени, но с информацией, достаточной для планирования эксперимента. Нужно только из массива данных выбрать информацию, которая соответствует плану эксперимента. Используя базу данных, провели промышленный эксперимент по определению условий возникновения автоколебаний ролика натяжной станции и прокатываемой полосы. Получена явная зависимость возникновения автоколебаний НС8 от скорости протягивания полосы в момент вырезания неметаллического включения (класс 3). Скорость протягивания должна быть в пределах от 0,5 до 1,0 м/с. При скоростях протягивания в диапазоне от 2,0 до 2,5 м/с автоколебания не возникают. Условия возникновения трещин на торцовых поверхностях ролика отсутствуют.
Стан холодной прокатки, натяжная станция петленакопителя, автоколебания, трещинообразование, промышленный эксперимент
Короткий адрес: https://sciup.org/147242636
IDR: 147242636 | DOI: 10.14529/engin230405
Текст научной статьи Влияние скорости протягивания прокатываемой полосы на возникновение автоколебаний натяжной станции стана холодной прокатки 2000
На станах холодной прокатки, совмещенных с непрерывным травильным агрегатом, при определенных условиях возникают автоколебания роликов натяжных станций. Это происходит в тот момент, когда станом выполняются мероприятия по удалению неметаллических включений в полосе прокатываемого металла [1]. Интеллектуальная система определяет наличие дефекта, момент подхода дефекта к клети № 1 и выдает сигнал на останов стана. Рабочие валки разводятся на 15 мм, и полоса перематывается с первой на вторую моталку. Скорость протягивания полосы изменяется в пределах от 0,5 до 2–3 м/с. Перематывание на вторую моталку и вырезание дефекта производится при фактически стоящем стане с разведенными рабочими валками. Автоколебания приводят к возникновению окружных трещин на торцовых поверхностях роликов натяжных станций (рис. 1).
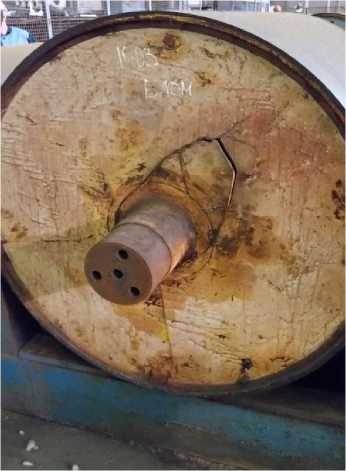
Рис. 1. Окружная трещина, зародившаяся в районе оси Fig. 1. A circumferential crack that originated in the area of the axis
Устранение автоколебаний можно проводить проведением предварительных ремонтов, например, определяя остаточный ресурс, или разработкой мероприятий для предотвращения возникновения автоколебаний. Оценка остаточного ресурса ролика натяжной станции с учетом трещинообразования требует построения 3-мерной численной модели для определения собственных частот и собственных форм колебаний, определения вынужденных колебаний и одновременно подсчета реального числа количества циклов нагружения. Численная модель построена, определены собственные частоты и формы колебаний, показано, что существенными являются осевые колебания ролика натяжной станции. Разработана методика подсчета количества циклов нагружения.
Термин «цифровой двойник» (Digital Twin) предложен Майклом Гривсом в 2014 году [2]. Сложность используемого цифрового двойника определяется задачей диагностики. Численная модель может быть сложной 3-мерной, мультидисциплинарной или более простой, не требующей больших вычислительных мощностей. Это может значительно уменьшить размер моделей и обеспечить быструю обработку [3] .
Эти модели позволяют современным продуктам моделирования визуализировать и моделировать сложные системы, включая их физическое поведение, в режиме реального времени и с приемлемыми вычислительными затратами [4].
Цифровой двойник может существовать на любом этапе жизненного цикла и нацелен на использование аспектов виртуальной среды, вычислительных методов и аспектов физической среды для улучшения элементов продукта в течение жизненного цикла [5].
В работе [6] представлен прототип цифрового двойника на примере модельной среды для интеллектуальных автомобилей, которые могут перенастраиваться во время эксплуатации. В работе [7] определены основные характеристики цифрового двойника в течение всего жизненного цикла изделия. Обзор научной литературы по теме «цифровые двойники в промышленности» приведен в работе [8]. В работах В.М. Дозорцева [9, 10] анализируется история возникновения и базовые технологии построения цифровых двойников. Анализ использования имитационных моделей при построении цифровых двойников проведен в работах [11-13].
Система связи физического объекта и его цифрового двойника оставляет цифровую тень. Термин «цифровая тень» (Digital Shadow) появился при работе с Интернетом. Пассивный цифровой след пользователь оставляет ненамеренно, он получается автоматически из данных, которые получают и сохраняют автоматически [14]. Сравнительному анализу отличия цифровых двойников и цифровых теней посвящена работа [15]. Цифровая тень способна предсказать поведение реального объекта только в тех условиях, в которых осуществлялся сбор больших данных, но не позволяет моделировать ситуации, в которых реальный объект ещё не эксплуатировался -«цифровая тень обладает лишь свойством памяти» [16]. Но этого может быть достаточно, если объем информации, хранящийся в цифровой тени, достаточно большой [17, 18]. В этом случае можно проводить отсеивающие эксперименты [19], строить факторные, дробные факторные модели, используя методы регрессионного анализа [20, 21].
Промышленный эксперимент
При проведении промышленного эксперимента, как правило, используются технологические параметры или диагностические данные, отраженные и сохраненные во внешней по отношению к промышленному объекту среде, т. е. используется «цифровая тень». Фирмой «СИГМА» разработана и внедрена система контроля, сбора и длительного хранения технологических параметров стана холодной прокатки 2000. Система хранения представляет собой гибридную базу данных, включающую в себя кроме технологических параметров данные виброконтроля. Вибродатчики установлены на подшипниковых опорах ролика натяжной станции. Вибропараметры собираются и хранятся в отдельной базе данных. Базы данных технологических и вибрационных параметров объединены графической оболочкой. По вибрационным параметрам определяется момент возникновения автоколебаний стана. Технологические параметры позволяют связать возникновение автоколебаний ролика натяжной станции с процессом прокатки на стане.
Промышленный эксперимент – это, как правило, пассивный эксперимент. То есть эксперимент, в котором экспериментатор не имеет возможности вмешиваться в процесс проведения эксперимента. Но на стане холодной прокатки один отдельно взятый независимый эксперимент требует всего 5–6 минут. За это время прокатывается один рулон – полоса длиной 7000 метров. Причем каждый рулон разной толщины, ширины, различного химического состава и, соответственно, с различными механическими свойствами. Кроме того, различна скорость прокатки, натяжение полосы, обжатие полосы, различные силы трения на натяжной станции и т. д.
Каждый рулон – это независимый эксперимент. В сутки – 240, в год – 86000. Если информация о технологических и диагностических параметрах хранится достаточно долго, например год или два, этой информации достаточно, чтобы работать с ней как с лабораторным экспериментом. С запаздыванием по времени, но с информацией, достаточной для планирования эксперимента. Нужно только из массива данных выбрать информацию, которая соответствует плану эксперимента. Это будет квазиактивный промышленный эксперимент.
Полный перебор факторов ( п !) для 7 факторов требует 5040 независимых экспериментов, для 10 факторов – 3628800 независимых экспериментов. Полный факторный эксперимент (2к , здесь к – количество факторов) для 7 факторов требует выполнения 128 независимых экспериментов, для 10 факторов – 1024 независимых эксперимента. Дробный факторный эксперимент позволяет сократить количество необходимых независимых экспериментов. Полуреплика для 7 факторов требует 64 независимых эксперимента, для 10 факторов – 512.
При большом количестве факторов число независимых экспериментов будет слишком большим. Поэтому можно попробовать использовать отсеивающий эксперимент. Методика отсеивающего эксперимента позволит существенным образом сократить количество независимых экспериментов. Если же удастся найти один или два фактора, определяющих техническое состояние оборудования, то количество независимых экспериментов может быть снижено с нескольких сотен до нескольких десятков.
В базе данных в цифровой тени собираются и хранятся контролируемые, но неуправляемые факторы. То есть факторы, уровни которых можно только регистрировать, но задать в каждом опыте их определенное значение практически невозможно. Но если работать с большим объемом информации и с большим или очень большим количеством независимых экспериментов, можно получить новое качество и работать с информацией и факторами как с контролируемыми и управляемыми факторами [17, 18]. Можно просто подбирать параметры факторов по величине [19], соответствующей выбранному плану эксперимента [20, 21].
В работе [1] показано, что автоколебания возникают в момент вырезания неметаллического включения, дефекта № 3, по классификации АСУ ТП. В этот момент рабочие валки разводятся на 15 мм и полоса протягивается и перематывается с одной моталки на другую. Эта операция практически штатная и происходит от 7 до 10 раз в сутки. Кроме того, автоколебания зависят от толщины подката. Интенсивные автоколебания возникают при толщине подката 5,0–6,0 мм и скорости протягивания от 0,5 до 1,0 м/с.
В качестве примера на рис. 2 показаны 4 момента разведения рабочих валков. Это моменты вырезания неметаллических включений. Каждый случай пронумерован. На рис. 3 приведены уровни вибрации на подшипниковых опорах натяжной станции № 8 (НС8). Как видно из рис. 3, в зоне 2 уровень виброускорений выше на порядок. В этой зоне при протягивании прокатываемой полосы возникают автоколебания.
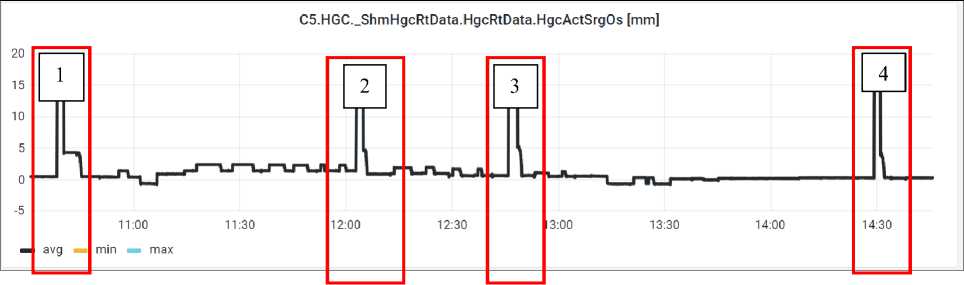
Рис. 2. Моменты разведения рабочих валков (15 мм) при протягивании полосы и удалении дефекта (неметаллические включения, класс 3)
Fig. 2. The moments of dilution of the working rolls (15 mm) when stretching the strip and removing the defect (non-metallic inclusions, class 3)
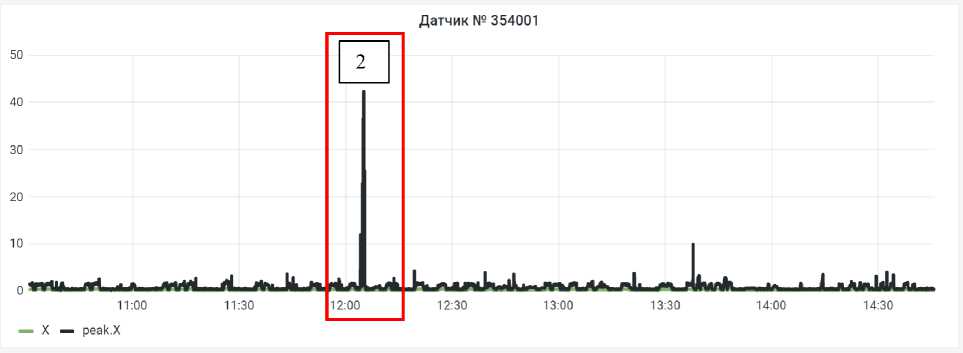
Рис. 3. Вибрация автоколебания ролика натяжной станции Fig. 3. Vibration of self-oscillation of the tensioning station roller
Моменты протягивания выбраны из условия максимальной толщины подката. В зонах 1 и 4 толщина подката – 5,0 мм, в зонах 2 и 3 – 6,0 мм (рис. 4). На рис. 5 и 6 приведены скорости протягивания прокатываемой полосы при перематывании с одной моталки на другую. На рис. 5 – скорость прокатки пятой клети, на рис. 6 – скорость протягивания натяжной станции. И в клетях стана, и на натяжной станции скорость прокатки одинакова и находится в пределах 2,0–2,5 м/с, за исключением зоны 2, в которой скорость протягивания находится в пределах от 0,5 до 1,0 м/с. В зонах 2 и 3 выполняются условия, при которых возможно возникновение автоколебаний.
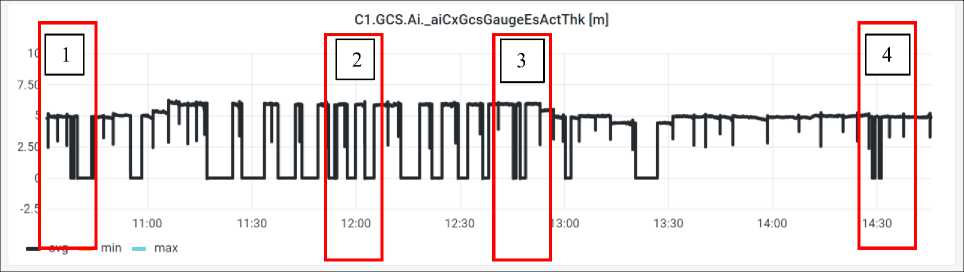
Рис. 4. Толщина подката в зависимости от времени Fig. 4. The thickness of the lining depending on the time
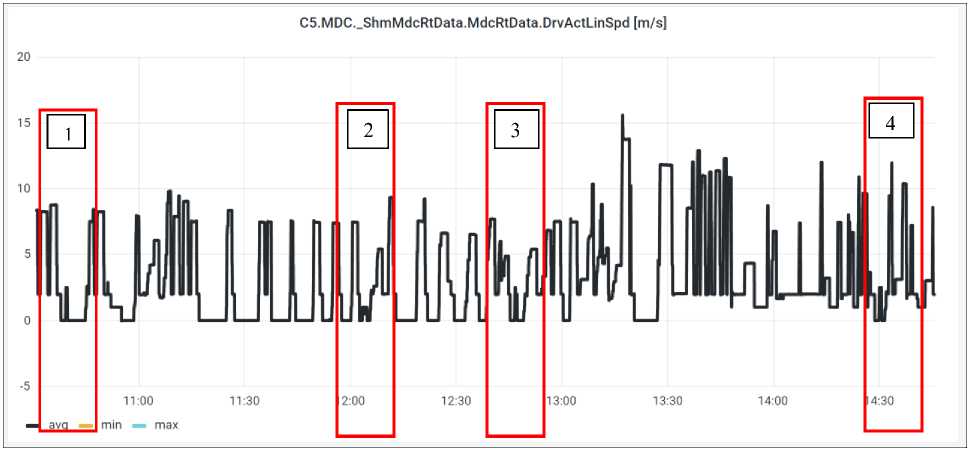
Рис. 5. Скорости прокатки в пятой клети Fig. 5. Rolling speeds in the fifth cage
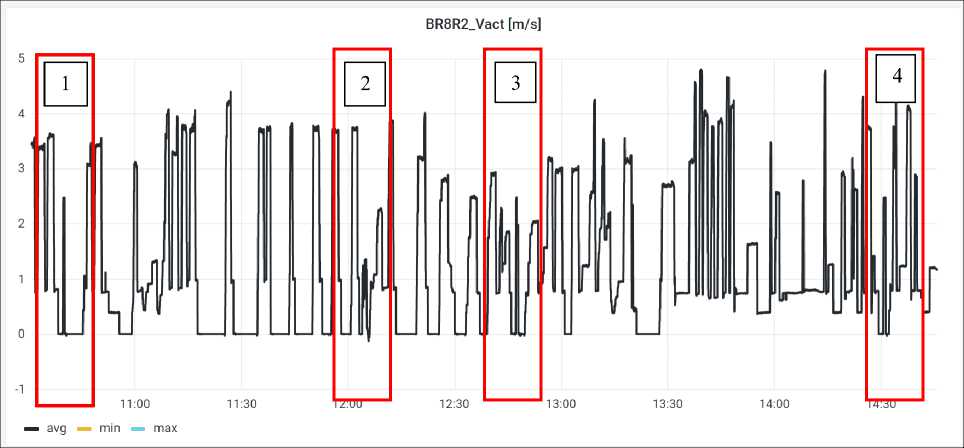
Рис. 6. Скорости протягивания натяжной станции 8
Fig. 6. Stretching speeds of the tension station 8
На рис. 7–10 приведены распределения во времени скоростей протягивания в зонах, в которых проводилось вырезание неметаллических включений. В зоне 2 скорости изменялись в диапазоне от 0,5 до 1,0 м/с, толщина подката равна 6,6 мм. Именно на этих скоростях возникали автоколебания с уровнями виброускорений до 35–40 м/с2. В зоне 3 при той же толщине подката, равной 6,0 мм, при скоростях протягивания 2,5 м/с автоколебания отсутствуют. Условия возникновения трещин на торцовых поверхностях ролика отсутствуют.
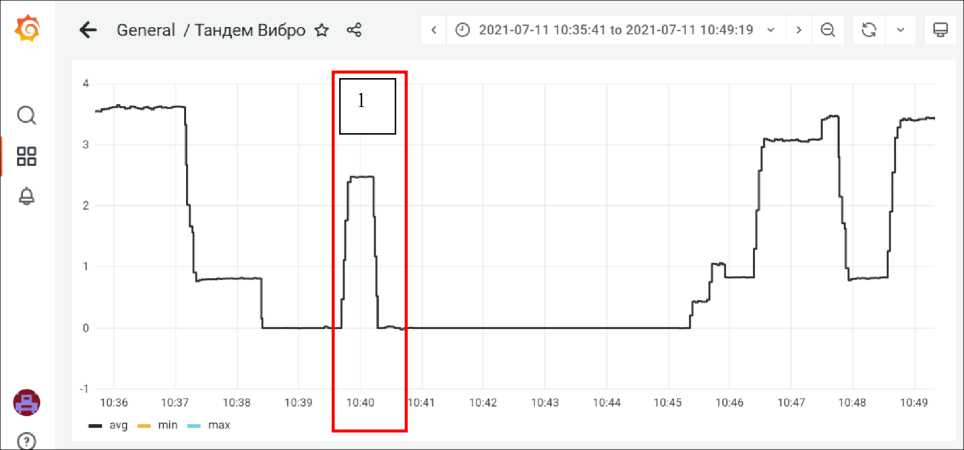
Рис. 7. Зона № 1: дефект класс 3, скорость протягивания 2,47 м/с Fig. 7. Zone No. 1: defect class 3, the pulling speed is 2.47 m/s
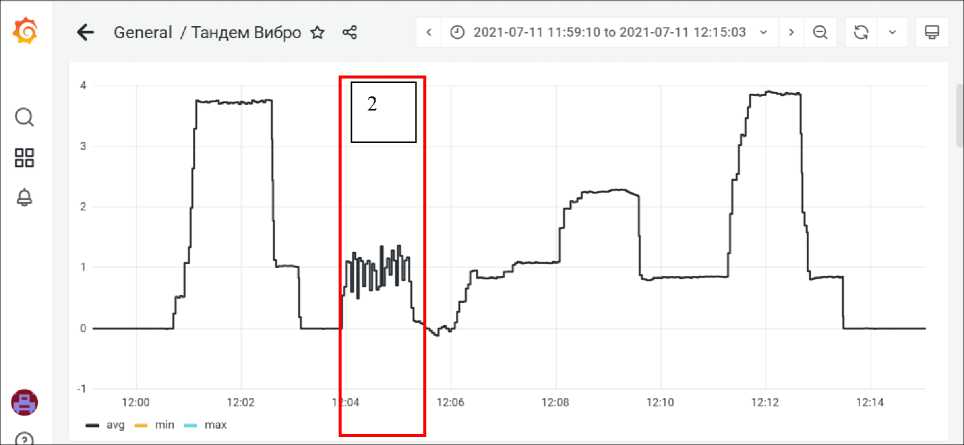
Рис. 8. Зона № 2: дефект класс 3, скорость протягивания 0,5–1,5 м/с. Автоколебания Fig. 8. Zone No. 2: defect class 3, stretching speed 0.5–1.5 m/s. Self-oscillation
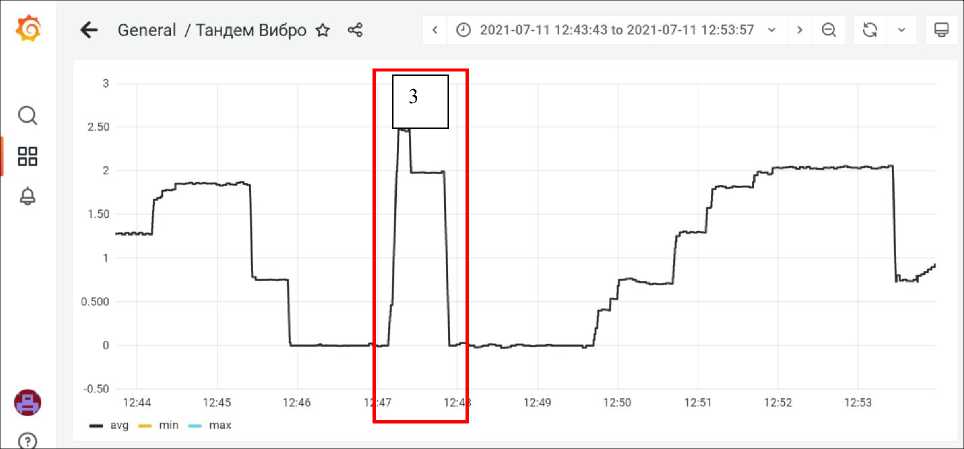
Рис. 9. Зона № 3: дефект класс 3, скорость протягивания 2,50 м/с Fig. 9. Zone No. 3, defect class 3, the pulling speed is 2.50 m/s
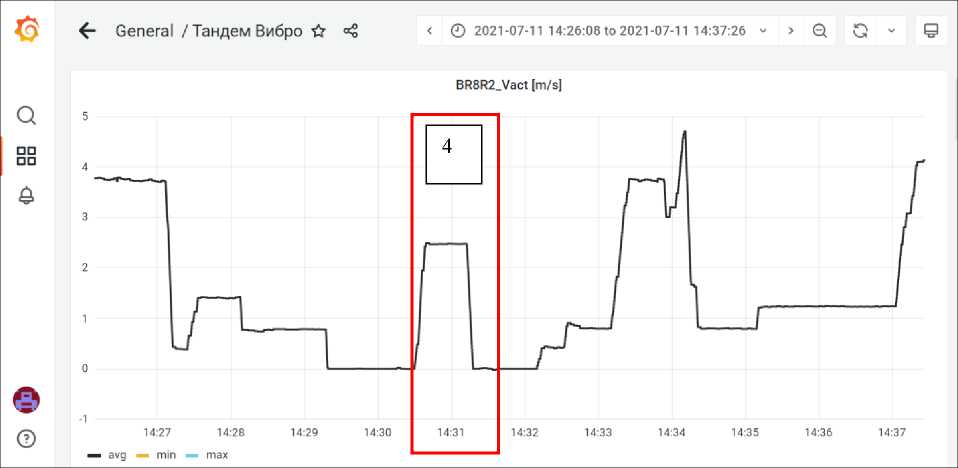
Рис. 10. Зона № 4: дефект класс 3, скорость протягивания 2,40 м/с Fig. 10. Zone No. 4: defect class 3, the stretching speed is 2.40 m/s
Выводы
-
1. Проведен промышленный эксперимент по определению условий возникновения автоколебаний ролика натяжной станции и прокатываемой полосы с использованием цифровой тени.
-
2. Получена явная зависимость возникновения автоколебаний НС8 от скорости протягивания полосы в момент вырезания неметаллического включения (класс 3). Скорость протягивания должна быть в пределах от 0,5 до 1,0 м/с.
-
3. При скоростях протягивания в диапазоне от 2,0 до 2,5 м/с автоколебания не возникают. Условия возникновения трещин на торцовых поверхностях ролика отсутствуют.
Список литературы Влияние скорости протягивания прокатываемой полосы на возникновение автоколебаний натяжной станции стана холодной прокатки 2000
- Автоколебания натяжных станций травильного агрегата, совмещенного со станом тандемом холодной прокатки 2000 / М.Л. Краснов, П.Л. Качурин, С.Г. Вишняков и др. // Вестник ЮУрГУ. Серия «Машиностроение». 2023. Т. 23, № 2. С. 61–71. DOI: 10.14529/engin230206
- Grieves M. Digital twin: manufacturing excellence through virtual factory replication. White Pa-per. LLC. 2014. Р. 1–7.
- Grieves M., Vickers J. Transdisciplinary Perspectives on Complex Systems. Cham: Springer, 2017. Р. 85–113. DOI: 10.1007/978-3-319-38756-7_4.
- Grieves M. Product lifecycle management: The new paradigm for enterprises // International Journal of Product Development. 2005. Vol. 2(1/2). Р. 71–84.
- Hicks B. Industry 4.0 and Digital Twins: Key lessons from NASA. URL: https://www.thefuture-factory.com/blog/24 (дата обращения: июль 2023)
- Abramovici M., Göbel J.Ch., Savarino Ph. Reconfiguration of Smart Products during their Use Phase based on Virtual Product Twins // IFIP International Conference on Product Lifecycle Manage-ment PLM. 2017. Р. 489–498. DOI: 10.1016/j.cirp.2017.04.042
- Шведенко В.Н., Мозохин А.Е. Применение концепции цифровых двойников на этапах жизненного цикла производственных систем // Научно-технический вестник информационных технологий, механики и оптики. 2020. Т. 20, № 6. C. 815–827. DOI: 10.17586/2226-1494-2020-20-6-815-827
- Царев М.В., Андреев Ю.С. Цифровые двойники в промышленности: история развития, классификация, технологии, сценарии использования // Изв. вузов. Приборостроение. 2021. Т. 64, № 7. С. 517–531.
- Дозорцев В.М. Цифровые двойники в промышленности: генезис, состав, терминология, технологии, платформы, перспективы. Часть 1. Возникновение и становление цифровых двойников. Как существующие определения отражают содержание и функции цифровых двойников // Автоматизация в промышленности. 2020. № 9. С. 3–11.
- Дозорцев В.М. Цифровые двойники в промышленности: генезис, состав, терминология, технологии, платформы, перспективы. Часть 2. Ключевые технологии цифровых двойников. Типы моделирования физического объекта // Автоматизация в промышленности, 2020. № 11. С. 3–11.
- Петров А.В. Имитация как основа технологии цифровых двойников // Вестн. Иркут. гос. техн. ун-та. 2018. № 10 (141). С. 56–66. DOI: 10.21285/1814-3520-2018-10-56-66.
- Коровин Г.Б. Возможность применения цифровых двойников в промышленности// Вестник Забайкальского государственного университета. 2021. Т. 27, № 8. С. 124–133. DOI: 10.21209/2227-9245-2021-27-8-124-133
- Боровков А.И., Рябов Ю.А. Цифровые двойники: определение, подходы и методы разработки // Цифровая трансформация экономики и промышленности: сб. тр. науч.-практ. конф. с зарубежным участием. СПб.: Политех-Пресс, 2019. С. 234–245. DOI: 10.18720/IEP/2019.3/25.
- Лаборатория Касперского, что такое цифровой след? 2022. URL: https://www.kaspersky.ru/resource-center/definitions/what-is-a-digitalfootprint (дата обращения: июль 2023)
- Анохов И.В. Цифровая тень как инструмент для исследования отрасли // E-Management. 2022. Т. 5, № 1. С. 80–92.
- Крылов И.А. Моделирование и визуализация «цифровой тени» человека на предприятиях // Вестник Российского экономического университета имени Г.В. Плеханова. 2021. Т. 5. С. 102–111. DOI: 10.21686/2413-2829-2021-5-102-111
- Налимов В.В., Чернова Н.А. Статистические методы планирования экстремальных экспериментов. М.: Наука, 1965. 340 с.
- Новик Ф.С., Арсов Я.Б. Оптимизация процессов технологии металлов методами планирования эксперимента. М.: Изд-во МГТУ им. Н.Э. Баумана, 2011.
- Григорьева Т.А., Толубаев В.Н. Корреляционно-регрессионный анализ технологических параметров // Системы. Методы. Технологии. 2018. № 3 (39). С. 57–61. DOI: 10.18324/2077-5415-2018-3-57-61
- Имитационное моделирование обжига цинковых концентратов в печах кипящего слоя / М.И. Алкацев, В.М. Алкацев, С.Б. Волошин и др. // Вестник ЮУрГУ. Серия «Металлургия». 2018. Т. 18, № 3. С. 26–32. DOI: 10.14529/met180303
- Оценка адекватности математических моделей металлургических процессов в рамках регрессионного анализа данных в пакете Mathcad / М.И. Алкацев, В.М. Алкацев, З.К. Абаев, А.Э. Дзгоев // Вестник ЮУрГУ. Серия «Металлургия» 2020. Т. 20, № 3. С. 12–20. DOI: 10.14529/met200302