Wood-polymer nano-modified composite materials for construction purposes
Автор: Liliya R. Asfandiyarova, Guzel V. Khakimova, Inna V. Ovsyannikova, Anna Y. Matveeva
Журнал: Nanotechnologies in Construction: A Scientific Internet-Journal @nanobuild-en
Рубрика: Application of nanomaterials and nanotechnologies in construction
Статья в выпуске: 6 Vol.15, 2023 года.
Бесплатный доступ
Introduction. The advantages of nano-modified composite materials for construction purposes based on polyvinyl chloride (PVC) include enhanced strength characteristics compared to other materials [1]. Composite nanomaterials based on plant resources are versatile materials, whose properties can be modified through additives and processing technology to obtain a wide range of products in various application areas, particularly in construction, decking, outdoor and garden furniture, siding, picket fences, packaging, pallets, and much more. The research aims to investigate the influence of different additives on the technological and operational properties of the resulting composite. Nano-modified composite materials based on PVC are superior to polyolefin composites in terms of stiffness and strength, have high light-resistance as well as resistance to many chemicals, and are comparatively inexpensive as raw materials [2]. Methods and materials. The research aims to determine the preparation of composite materials that provide a highly effective stabilizing system against thermal decomposition, which increase the flow properties of the polymer melt, reduce water sorption, and impart sufficiently high outdoor stability; therefore, products made from composite materials can be successfully used in the construction area. Results. Research results have shown that the use of nanostabilizers in the technology of producing building materials can ensure preservation and ageing quality of polymer composites. They also have application potential on industrial scale. Conclusion. Investigations carried out on the use of a number of nanostabilizers, give to construction composites higher color retention and therefore increase environmental resistance of material.
Nanostabilizers, wood-polymer composite material, construction
Короткий адрес: https://sciup.org/142239112
IDR: 142239112 | DOI: 10.15828/2075-8545-2023-15-6-543-551
Текст научной статьи Wood-polymer nano-modified composite materials for construction purposes
Original article
I n recent years, demand for nano-modified composite materials based on plant resources has grown rapidly in the Russian construction materials market, which is associated with the record pace of construction sector development, especially private housing construction, and a multiple increase in wood prices, which forced buyers to look for more financially and commercially beneficial alternatives.
Nano-modified wood-polymer materials are supernew and topical construction materials including thermoplastics filled with wood pulp, which combine useful qualities of both polymers and plant resources. At that, polyethylene, polypropylene, and polyvinyl chloride are used as plastics. The ratio rating of woodflour to polymer in the compound can modify its physical and mechanical characteristics.
Polymer composite materials based on polyvinyl chloride (PVC) are currently widely used in various areas of the economy. Main areas of their application are construction, cable industry as well as manufacture of containers and packaging. A particular attention is paid to the use of woodflour in the formulation of composites due to its low cost, large reserves, and non-toxicity.
Pre-eminent manufacturers and consumers of woodflour-filled PVC products are China, Japan, etc. In Russia, this material is not widely used enough, but its prospects are not questioned. Availability of forest resources and the ever-growing demand for high-quality construction and structural materials are high-powered incentives for the development of this market.
APPLICATION OF NANOMATERIALS AND NANOTECHNOLOGIES IN THE CONSTRUCTION
There is great interest in the market of nano-modified construction composite materials In Russia. The number of manufacturers in Russia is growing every year: if in 2010, there were only four companies having operated in this sector, then in 2015, there were already more than sixty manufacturers. The leading companies are: Multi-Plast – 3% and Techno-Polymer – 11%.
Main European manufacturers of composite materials are Germany, France, and Finland. The most important reasons limiting the growth of the domestic market are considered to be unformed demand, lack of product homogeneity as well as lack of standards and technical documentation [3].
Nano-modified wood-polymer composites are modern construction materials made on the mixing technology of woodflour, various polymers, and other components. Main way of obtaining nano-modified polymer composites is extrusion. At that, to completely homogenize the mixture resulting in a high-quality moulded product, a twin-screw extruder is used [4–6].
These materials are more weather-proof and much more durable than wood materials, which is important for use in our climatological conditions.
Compared to true lumber products, they have greater resistance to the influence of water and microorganisms as well effects of the atmosphere. Composite materials are considered to be multifunctional products. Their characteristics are quickly modified, which ultimately makes it possible to produce a wide range of products with different mechanical and aesthetic properties [7–8].
Woodflour is the main component of the composite. In order to facilitate recycling of plastic waste and reduce consumption of forest reserves, development and use of wood-filled plastic products has been widely encouraged in our country in recent years [9].
Polyethylene and polypropylene are mainly used as a polymer matrix in the composition of nano-modified composite materials. As for PVC-based composites, they exceed polyolefin composites in stiffness and strength. They possess high light resistance as well as resistance to chemicals, and comparative low price for raw materials. However, they are characterized by insufficient heat resistance and impact resilience as well as hydrophobicity [10–11].
Therefore, wood-polymer composite materials based on PVC belong to the most promising modern materials having wide performance characteristics, cost-effective production, and relative ease of processing [12–16].
Currently, extrusion is considered to be the most established technology for obtaining products from composite thermoplastic polymers. A grate number of foreign companies use this technology to produce profiles and tubular components, etc.
Rawwood, containing cellulose has a porous structure. When exposed to high temperature and pressure, it under- goes oxidation, and is also an abrasive wear material. In this regard, a number of problems often arise: in particular, adsorption of gaseous substances by sawdust and release of them in the extruder; risk of fires and explosions due to the resulting gas mixture; release of resinous substances from coniferous wood during the sawdust processing.
These disadvantages can be eliminated through using nano-modified additives included in the composite formulation [17]. They consist of the following components: – external and internal lubricants, which prevent stick ing to the extrusion head, increase free mobility, and reduce viscosity;
– bonding and dispersing agent to improve the dispersion of the polymer matrix, and the mechanical properties such as tensile strength, flexural toughness, and impact strength;
– flame retardants which increase fire-resistance of plastics;
– foaming agents, which reduce the weight of wood-polymer composites and facilitate nailing, drilling, fastening, screwing, and cutting during the construction work;
– antioxidants, traditionally used to prevent aging the material during its use;
– impact strength modifiers, which improve weather resistance for outdoor construction;
– fungicides, which protect building products against microorganisms and fungus, as well as ultraviolet stabilizers (UV stabilizers);
– pigments, which protect products from exposure to light rays and prevent their color fading.
In general, nanostabilizers can be divided into two groups: functional and technological ones. Functional nanostabilizers define the behavior of the composite while technological ones affect the process of high-temperature processing of the polymer compound. Main groups of nanomodifiers commonly used in the manufacture of PVC-based materials are stabilizers, lubricants, as well as impact and processability modifiers.
The content of nanomodifiers is about 1–5% by weight of the mixture, but it is they what has a significant effect on the characteristics of the final building product, such as strength, physical configuration, and ageing quality. Therefore, a vital task of today is to investigate the influence of various nanomodifiers on the operating ability of obtained constructional materials.
METHODS AND MATERIALS
The research aims to identify effective nanomodifying components, in particular nanostabilizers, which ensure the integrity of polymers during the processing and operation since fracture of polymers leads to changes in such parameters as viscosity, color, strength, and deterioration of physical and mechanical characteristics.
APPLICATION OF NANOMATERIALS AND NANOTECHNOLOGIES IN THE CONSTRUCTION
This group includes antioxidants, temperature and light stabilizers ensuring integrity of polymers in use and processing. The nano-modified antioxidants prevent oxidation during the technological process and operation. These include hindered phenols, alkyl/aryl phosphites, etc.
Main requirements in relation to stabilizing additives are removal of labile chloride groups, absorption of hydrogen chloride, increase in moisture resistance and robustness against oxidation process, as well as low toxicity and low cost.
Currently, nano-thermal stabilizers, which contain toxic substances such as cadmium, lead and barium stearates are strictly limited, therefore the share of non-toxic stabilizers such as calcium stearate and zinc stearate is increasing on the market [18–20].
In addition to the above, shockproof nanomodifiers increasing impact strength of products and giving them ability to withstand sudden loads without destruction, are used in the production of composites. Such nanomodifiers are divided into the following groups: nanomodifiers having a “core-shell” structure (MBS – methacrylate-bu-tadiene styrene, AIM – acrylic nanomodifiers of impact strength), nanomodifiers ABS – acrylonitrile-butadiene-styrene, and nanomodifiers with a semi-compatible network structure (CPE – chlorinated polyethylene, EVA – ethylene-vinyl acetate, NBR – acrylonitrile-butadiene-rubber) [21].
Processing additives or processing nanomodifiers, which simplify the melt processing, are polymers compatible with polyvinyl chloride including those that weaken the restrictions on the motion of polymeric chain and segments. They are necessary to promote the polymer particles decay, ensure homogeneity of the melt as well as afford rapid gelling and desired degree of plasticization.
A wide range of copolymers of methyl methacrylate (MMA) with styrene, acrylate, methacrylate, and m-vinyl lactam, MMA and glycidyl methacrylate, MMA and acrylic acrylates, and other can be used as additives [22].
The above nanoadditives provide reduction of friction during the processing. According to the mechanism of action, they are divided into internal, external, and mixed actions. In particular, the first group of nanomodifiers thermodynamically compatible with the polymer; they reduce intermolecular interaction force and, therefore, viscosity of the polymer.
Externally acting lubricants facilitate the processing of polymer through switching the mode from shear sliding to “plug” sliding mode. It should also be noted that due to insufficient compatibility with the polymer, they are released during the processing at the melt-metal interface and decrease adhesion of polymer to the metal surface of processing equipment [23].
The necessity to use nanomodifiers is determined based on the requirements for the final products depend- ing on their operating conditions and fabricability in processing, which in turn depend on the design features of the extrusion line.
Composite materials based on the plant components are finding an ever increasing commercial use in construction industry. An important in-use performance of this material is its long-term strength outdoors.
Under the influence of ultraviolet irradiation as well as in the presence of oxygen and moisture, the polymer undergoes very rapid dehydrochlorination and peroxidation resulting in formation of polyenes, which leads to a sharp change in the mechanical properties of the polymer [24].
Investigations of effecting of nanostabilizers on the technological and operational properties of composite materials were carried out at a mass ratio of PVC : woodflour – 1:1.
The wood-polymer composition was obtained by mixing the components in the high-speed mixer when heated to 120оC; then, the obtained polymer mass was cooled to the temperature of 40–60оC and melted down by means of laboratory extruder to obtain a chunk. Test samples (granules) were obtained from the chunk by rolling. Rolling time was 5–8 minutes; rolling temperature was 170±5оC.
Effect of formulation factors on the processing properties of polymer compound was assessed upon the processing by means of a laboratory twin-screw extruder.
Research examined the effect of various nanostabilizers on the technological and operational properties of the resulting composites since the process of oxidation takes place at every stage of the life of polyvinyl chloride material.
RESULTS
To prevent the perishing, and improve technological and operational characteristics of compositions during the processing, an important measure is introduction of nano-thermal stabilizers, whose addition in small quantities is comparable to the effect of stoichiometric ratio of the substances involved in the reaction.
A very large percentage of nanomodifiers for polymer are used to improve mechanical characteristics (strength and stiffness). Homopolymer polyvinylchloride is quite strong and light but not stiff enough. To impart improved properties, which is very important in the construction sector, cadmium was previously used in Europe and Russia. However, its use was gradually reduced since it was recognized as unsafe. According to well-known European analytical databases, cadmium was excluded from polyvinyl chloride modifiers throughout Europe by 2007.
A known fact is also replacement of lead nanostabilizers (75% reduction between 2000 and 2010; currently, they
APPLICATION OF NANOMATERIALS AND NANOTECHNOLOGIES IN THE CONSTRUCTION are almost completely excluded). This is confirmed by the corresponding growth of calcium-based nanostabilizers used as an alternative.
Tin is also used as a stabilizer in Russia, Europe, but mainly in the USA. According to European manufacturers of PVC products, tin stabilizers have passed the stage of successful testing for environmental safety and are increasingly used along with calcium stabilizers.
A global trend in the PVC industry is introduction of calcium-zinc stabilizers, i.e. additives designed for obtaining safe products from polyvinylchloride. Such stabilizers are capable of performing the following functions: – prevent degradation during extrusion;
– protect PVC profiles from deformation, discoloration and yellowing under the effect of ultraviolet light;
– simplify forming of PVC;
– ensure high-temperature performance.
In addition to environmental improvement, there are also technical grounds for the widespread use of calciumzinc systems:
– these stabilizers are non-toxic;
– provide high thermal stability;
– provide weather resistance equal to or better than that of lead-containing systems;
– high protection against UV radiation.
The research involved the testing of calcium-zinc stabilizers designed for processing the unplasticized polymers of the Baeroran and Rhythmix brands. These stabilizers were introduced into the basic formula of nano-modified composite within the limits recommended by the manufacturers, i.e. in quantities of 3–6 parts by mass. The results are presented in Table 1.
Tests of calcium-zinc stabilizers in the basic formula show that the Baeroran brand provides comparatively better results. However, at the dosage of 6 parts by mass, the Rhythmix stabilizer provides the required level of thermal stability.
Calcium-zinc stabilizers are generally complex ones, i.e. contain small antioxidant additives, lubricants, and etc. in addition to calcium and zinc stearates. Despite this, according to the results of investigation of melt flow index it is clear that the “lubricating” effect of these stabilizers both in Baeropan and Rhythmix is slightly expressed.
To optimize the rheological properties of nano-modified composite during extrusion, internal and external lubricants should be added to its composition. As the result of extrusion of PVC compositions, in addition to thermal effect, also mechanical loads have severe impact on the polymer material, under the influence of which several sequential-parallel reactions proceed in the polymer macromolecules:
– in the spots of the highest voltage concentration, the breaking of C-C bonds takes place, which leads to the decrease in the molecular weight of the polymer;
– elimination of hydrogen chloride molecule and polyene blocks;
– redistribution of the resulting radicals without a noticeable change in the viscosity-average molecular weight, i.e. “chemical flow”;
– cross-linking of macromolecules through increasing the viscosity, etc.
Addition of a stabilizer into the composite material, which modifies its chemical and mechanical properties, leads to extinction of destructive effect of physical loads on the material at forcing the polymer melt through the molding hole in the extruder. Reduction in internal friction as well as in heat, which is releasing in the process of mechanical work, proceeds as a result of introducing into the polymer composition the lubricants, which reduce the viscosity of the melt. As a result, the processing temperature goes down, destruction of polymer lessens, and distribution of the components included in the composition becomes easier [25, 26].
In order to facilitate the processing procedure of highly filled formulation of wood-polymer composites, investigations of nanoadditives of the ester type (glycerol monostearate, LoxiolG and Lubstab) concerning their melt flow index were carried out (Figure 1). Upon that, an increase in this parameter was found when using ester nanoadditives. Best result was obtained when using Lubstab brand
Table 1
Effect of stabilizers on the properties of nanomodified composite materials
Content of Ca–Zn stabilizer in the basic formula, parts by mass |
Name of the test parameters |
|||
Thermal stability at 180оC, min |
Melt flow index g/10 min (I = 21.6 kgf, Т = 190оС) |
Water sorption, % |
||
Baeroраn |
2 |
56 |
0.56 |
6.1 |
4 |
73 |
0.85 |
5.8 |
|
6 |
85 |
1.1 |
5.2 |
|
Rhythmix |
2 |
49 |
0.49 |
6.2 |
4 |
67 |
0.64 |
6.0 |
|
6 |
80 |
0.97 |
5.4 |
APPLICATION OF NANOMATERIALS AND NANOTECHNOLOGIES IN THE CONSTRUCTION
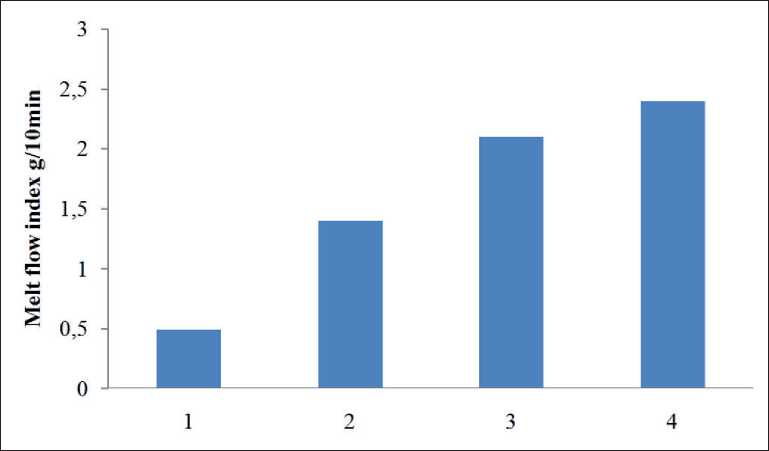
Fig. 1. Results of the experiment to evaluate the effect of nanoadditives on melt flow index: 1 – without nanoadditive; 2 – glycerol monostearate; 3 – LoxiolG; 4 – Lubstsab (at 190оC and 21.6 kg load)
lubricant, which makes it possible increasing the melt flow index from 0.49 to 2.4 g/10 min.
Studies carried out to determine the optimal dosage of Lubstab lubricant show that at its dosage in an amount of 2 parts by mass (Figure 2), the melt flow is 3.3 g/10 min. With the increase in its content, melt flow index of flexible PVC compound increases, which indicates an increase in the mobility of supermolecular structures in the polymer melt. A further increase in the dosage of nanoadditives is impractical, because it may adversely affect the physical and mechanical characteristics of the resulting nanobuilding materials.
The addition of nanoadditives of this type to the wood-polymer composites allows achieving an increase in the productivity of processing equipment, in particular, of the laboratory extruder. In addition, the improve-
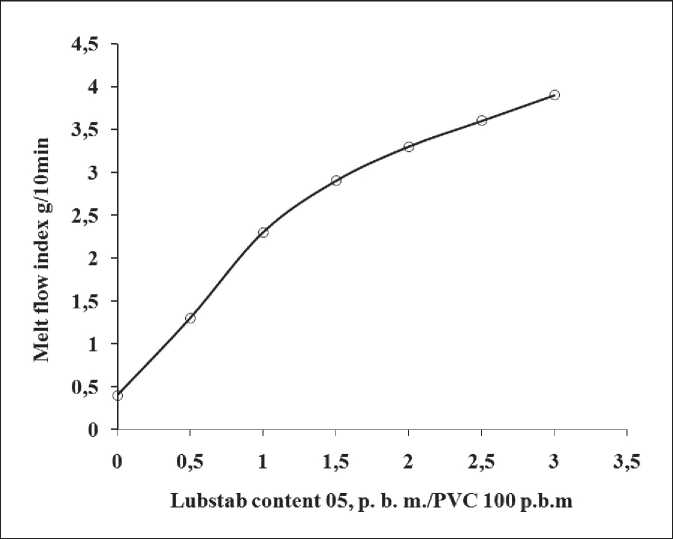
Fig. 2. Dependence of the melt flow index on the amount of Lubstab introduced
APPLICATION OF NANOMATERIALS AND NANOTECHNOLOGIES IN THE CONSTRUCTION ment of the performance of composites is influenced by the uniform distribution of woodflour particles in the polymer volume as well as the enhancement of their interaction.
Nanoadditives based on titanates contribute to increase the strength of polymers and enhance the bond between organic polymers and inorganic fillers.
The possibility of increase in adhesive interaction of polymer with woodflour through introducing the organ-otitanate nanoadditive into the composition is evaluated.
It has been established that addition of 1% of organoti-tanate to the composition leads to increase in the strength of composite, and a further increase in its dosage to 2% does not affect the physical and mechanical properties of the composite (Table 2).
Nanoadditives under investigation have a great impact on the water absorption index. In particular, with the introduction of Lubstab, a decrease in the value of this index is observed. Addition of organotitanate reduces water absorption. This is explained by the more uniform distribution of woodflour in the polymer composition under the effect of ester lubricant, as well as by increase in the adhesive interaction between the polymer and filler due to the effect of organotitanate.
To give maximum exterior resistance to the products, the effect of the UV stabilizer Chimassorb (BASF Germany) and antioxidant Agidol, which is a mixture of pentaerythritol tetrakis [3- [3,5-di-tert-butyl-4-hydroxyphenyl] propionate and tri(2,4-di-tert-butylphenyl) phosphite was studied.
Investigation of the UV stabilizers’ effect on the lightresistance of composite materials was carried out in the Solarbox desktop camera 1500E, which has luminous flux intensity of 765 W/m2; testing time lasted for 300 hours. The test results are shown in Table 3 and Table 4.
DISCUSSION
Effect of various modifiers on the technological and operational properties of nano-modified composite materials has been studied. As a result of the research, components are selected, which ensure high efficiency of stabilizing system against thermal decomposition, increase melt flow of polymer, reduce water absorption and give sufficiently high outdoor stability to the materials, which is particularly true when used in construction.
Thus, it was established in the course of investigations that Rhythmix stabilizer and Lubstab lubricant provide
Table 2
Research results of assessing the effect of organotitanate on the mechanical properties of composite
No. |
Name of the index |
Content of organotitanate, % |
||
0 |
1 |
2 |
||
1 |
Tensile strength, MPa |
28 |
34 |
35 |
2 |
Elongation at break % |
33 |
57 |
59 |
Table 3
Result of investigation of the UV irradiation effect on the appearance of nano-modified composite
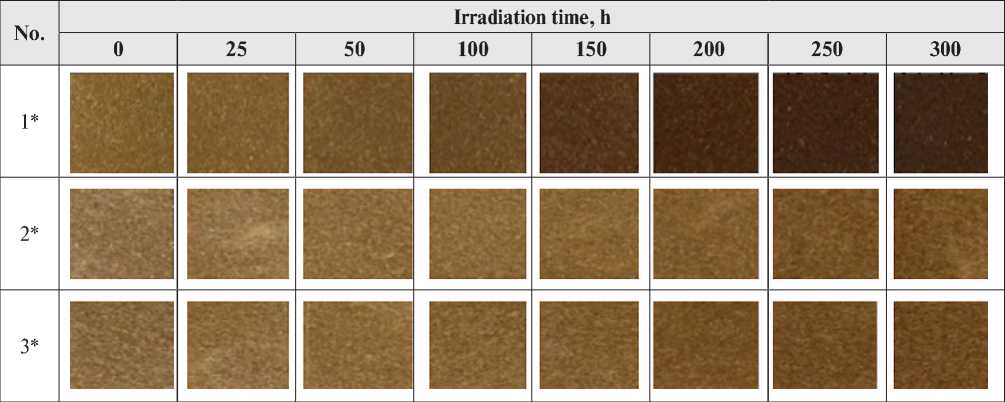
* sample 1 – without UV stabilizer; sample 2 – with the addition of Chimassorb; sample 3 – with the addition of Chimassorb and Agidol
APPLICATION OF NANOMATERIALS AND NANOTECHNOLOGIES IN THE CONSTRUCTION
Table 4
Test results on the change in color of nanocomposites under the influence of UV irradiation in CIELab coordinates
Based on the obtained decoloration values ∆E calculated on the color separation of composite materials during the sample exposure, it was found that the composition containing UV stabilizer Chimassorb is more resistant to decoloration under the influence of UV irradiation. In this case, the total color difference (chromatic) decreases from 25.57 to 12.74.
Combined use of Chimassorb and Agidol provides the composite higher color retention, and therefore increases the environmental resistance of material.
CONCLUSION
This research shows a possibility of combining utilization of various nanoadditives. To achieve this goal, components were selected, which ensure high efficiency of the stabilizing system against heat degradation of polymer, increase its melt flow, reduce water absorption and give composite materials high outdoor stability.
Components selected during the investigation have a prospect of being used on industrial scale in the process of manufacturing composite materials based on plant resources.
This study was funded by the Ministry of Science and Higher Education of the Russian Federation «PRIORITY 2030» (National Project «Science and University»)
APPLICATION OF NANOMATERIALS AND NANOTECHNOLOGIES IN THE CONSTRUCTION
Список литературы Wood-polymer nano-modified composite materials for construction purposes
- Abdrakhmanova L.A., Khantimirov A.G., Nizamov R.K., Khozin V.G. Wood-polymer nanomodified polyvinyl chloride building composites. Bulletin of MGSU. 2018; 13(4) (115): 426-434.
- Ekimenko A.N. Prospects for the use of organosilanes in thermoplastic composites with plant fillers. Plastics. 2018; 1-2: 28-33.
- Burmakina E.V. Main characteristics and trends in the development of the market for wood-polymer composites. International scientific and technical conference of young scientists of BSTU. V.G. Shukhova. 2019; 2682-2686.
- Fayzullin I.Z., Musin I.N., Wolfson S.I. Features of the production of products from wood-polymer composite. Bulletin of the Technological University. 2015; 18(3): 130-134.
- Faizullin I.Z., Musin I.N., Wolfson S.I. Influence of filler particle size on the properties of wood-polymer composites. Bulletin of the Kazan Technological University. 2013; 16(5):106-109.
- Musin I.N., Faizullin I.Z., Wolfson S.I. The influence of additives on the properties of wood-polymer composites. Bulletin of the Kazan Technological University. 2012; 15(24): 97-99.
- Cai Hong Zhen, Yang Keyan, Yi Weiming. Effects of calcium carbonate preparation and mechanical properties of wood plastic composite. Int J Agric & Biol Eng. Open Accessat. https://www.ijabe.org. 2017; 10(1): 184-190.
- Klyosov A. A. Wood-polymer composites. St. Petersburg: Scientific foundations and technologies. 2010; 736.
- Safin R.R., Khasanshin R.R., Danilova R.V., Khazieva D.R. Study of the properties of wood-polymer composites based on thermally modified filler. Bulletin of the Kazan Technological University. 2013; 16(24): 53-55.
- Editor Vijay Kumar Thakur. Green composites from natural resources. CRC Press; 2013; 419.
- Solovyov P.V., Knyazkov E.S. Review of technology for producing wood-polymer composites. February Readings. 2017; 270-273.
- Girevaya Kh.Ya., Shubina N.I. Recycling of polymer waste by obtaining wood-polymer composite material and studying its properties. Theory and technology of metallurgical production. 2012; 12: 156-161.
- Burmakina E.V. Main characteristics and trends in the development of the market for wood-polymer composites. International scientific and technical conference of young scientists of BSTU. V.G. Shukhova. 2019; 2682-2686.
- Nesterova A.V., Chernova A.O. Wood-polymer composites made by extrusion. Youth and scientific and technical progress. 2020; 286-290.
- Valeev I.A. Study of the influence of filler and binder on the physical and mechanical properties of wood-polymer composite. Bulletin of the Kazan Technological University. 2014; 17(10): 40-42.
- Yurchenko V.V. Analysis of modifying additives used in thermoplastic wood-polymer composites. Collection of scientific works of DonIZT. 2012. 30: 135-140.
- Minsker K.S., Fedoseeva G.T. Destruction and stabilization of polyvinyl chloride. Moscow: Chemistry; 1972.
- Yakubovsky S.F., Khoroshko S.I. Properties of wood-polymer composites obtained from powdered copolymer and sawdust. Bulletin of Polotsk State University. Series B. Industry. Applied Science. 2014; 3: 106-109.
- Gonzalez. J. Pastor J. Dc Saja. F. dc la. Monitoring the UV degradation of PVC window frame by microhardness analysis. J. Appl. Polym. Sci. 38(1989): 1879-1882.
- Shkuro A.E., Glukhikh V.V., Mukhin N.M. Preparation and study of the properties of wood-polymer composites with fillers from plant waste. Bulletin of the Moscow State Forest University. Forest Bulletin. 2016; 20(3). 101-105.
- Sheryshev M.A., Tikhonov N.N. Production of profile products from PVC. St. Petersburg: Scientific principles and technologies. 2012; 614.
- Minsker K.S. Classification of lubricants for PVC. K.S. Minsker, L.I. Karpacheva, T.B. Zavarova, L.N. Malyshev. Plastic masses. 1977; 1: 29-31.
- Milov V.I. Relationship between the plasticizing effect of lubricants and technological parameters of extrusion of PVC-based compositions. V.B. Mozzhukhin, V.I. Maksimenko. Plastic masses. 1989; 12: 52-53.
- Marsakova E.V. Modern wood-polymer composites. In the collection: Scientific community of students. Interdisciplinary research. Collection of articles based on the materials of the LXX student international scientific and practical conference. 2019; 17-27.
- Lisitsky V.V. Mechanochemical destruction of PVC. V.V. Lisitsky, A.P. Savelyev, V.I. Manushkin, K.S. Minsker. Plastic masses. 1981; 3: 24-26.