Технологические решения в производстве химически устойчивых силикатных материалов
Автор: Мырзалиева С.К., Аймбетова Э.О., Шаихова Ж.Е.
Журнал: Вестник Алматинского технологического университета @vestnik-atu
Рубрика: Естественные науки
Статья в выпуске: 3 (99), 2013 года.
Бесплатный доступ
В статье представлены результаты исследования по получению химически устойчивых композиционных силикатных материалов с использованием шлаков ниобиевого производства. Примеси ниобия в шлаках придают получаемым материалам дополнительную коррозионную стойкость, механическую прочность и химическую устойчивость. Разработаны оптимальные составы силикатных композиционных материалов и технологическая схема их приготовления.
Отходы, металлургическое производство, керамические материалы, фракции, композиционные материалы, электрокорунд
Короткий адрес: https://sciup.org/140204666
IDR: 140204666
Текст научной статьи Технологические решения в производстве химически устойчивых силикатных материалов
Одной из тенденций в современном производстве защитных материалов является переход на составы из отходов металлур- гических производств с высоким содержанием химически устойчивых и термостойких материалов, что позволяет вести формирование защитных композиционных материалов с наименьшими энергетическими затратами. Такой переход при бесспорных экономических и технологических достоинствах создает и проблемы, связанные с пластичностью формируемой массы. Эта проблема может быть решена путем введения пластифицирующих добавок. Ранее нами [1-5] были выполнены работы по введению тугоплавкой глины в химически устойчивые композиционные силикатные материалы, что позволило получать определенные технологические преимущества.
Керамические материалы из полифрак-ционных порошков обладают рядом достоинств по сравнению с такими же материалами из металлов, стекла, пластмасс. Они имеют более высокие значения прочности, устойчивы в кислотах и щелочах, расплавах черных и цветных металлов, агрессивных шлаков и могут длительно работать в широком диапазоне температур. Изделия из таких материалов могут изготавливаться различной геометрической формы (трубы, гребки, своды печей и т.д.), разных размеров и эксплуатироваться в условиях воздействия на них различных агрессивных сред, высокой температуры, сжимающих, изгибающих и других нагрузок. В связи с этим актуальным является проведение исследований по определению физико-технических и, в частности, прочностных характеристик химически устойчивых композиционных силикатных материалов, так как знание этих характеристик позволит целенаправленно подбирать материалы для конкретных условий их эксплуатации.
Объекты и методы исследований
Для приготовления химически устойчивых композиционных силикатных материалов были использованы следующие материалы: шлак ниобиевого производства (электрокорунд), тугоплавкая глина Ленгерского месторождения, жидкое стекло и кремнефтористый натрий.
Основу полученного композиционного силикатного материала составляет электрокорунд, являющийся побочным продуктом при получении металлического ниобия. Переработанный шлак представляет собой корундовый порошок. Остатки примесей ниобия в получаемом нами кислотоупорном композиционном материале дают дополнительную коррозионную стойкость, так как ниобий имеет ряд уникальных физических характеристик. Ниобий нашел широкое применение благодаря таким свойствам, как высокая температура плавления, значительная коррозионная стойкость, механическая прочность, малый коэффициент термического расширения. Электрокорунд является устойчивым материалом при всех температурах и отличается повышенной химической стойкостью.
Эти особенности определяют сферу его применения – изготовление коррозионностойких, огнеупорных кирпичей, футеровок, замазок и бетонов; возможность применения его как конструкционного материала для агрегатов химической промышленности.
Результаты и их обсуждение
Установлен химический состав электрокорунда, проведен рентгенофазовый, дифференциально-термический анализы, инфракрасная спектроскопия. Рентгенофазовый и петрографический анализ показал, что корунд в шлаке по марке соответствует электро-плавленному 23-25А с показателями преломления n g =1,768 и n p =1,760.
По результатам рентгенофазового анализа наблюдаются преобладающие максимумы дифракции, соответствующие набору межплоскостных расстояний, характерных для корунда (1,3749; 1,406; 1,603; 1,748; 2,0792; 2,384; 2,549; 3,490); кроме того, наблюдаются максимумы дифракции, характерных для Nb 2 О 5 (1,547; 1,965; 2,032) и SiO 2 (1,3378; 1,513).
Были проведены исследования по влиянию гранулометрического состава электрокорунда на физико-технические свойства получаемого композиционного силикатного материала.
Для получения смеси максимальной плотности и прочности необходимо правильно подобрать гранулометрический состав смеси. Термическая и химическая стойкость кислотоупорного материала полностью определяется зерновым характером структуры. Электрокорунд дает зернистую структуру, что повышает термическую стойкость и теплопроводность смеси, при связывании корунда глиной можно получить материал с минимальной пустотностью и высокой химической стойкостью. За счет регулирования зернового состава корундового наполнителя, можно подобрать оптимальный состав защитного материала, отвечающего всем перечисленным требованиям.
Подбор гранулометрического состава заключается в получении смеси с минимальной пустотностью, т.е. с наименьшим объемным весом. Все составляющие смеси дозируют по весу в соответствии с установленной рецептурой.
Исследован ряд составов материалов, приготовленных на основе электрокорунда с размерами зерен в пределах от 0,063 до 1,0 мм. В таблице 1 представлены грануломет- рические составы композиционных материалов. Из указанных составов были отобраны оптимальные гранулометрические составы для получения кислотостойких, прочных материалов и футеровочных масс: СКМ-2, СКМ-3, СКМ-4, СКМ-8, СКМ-9, СКМ-12, СКМ-14.
Таблица 1 - Гранулометрический состав композиционного материала
Образцы |
Фракции, мм., % |
||||
0,8-0,6 |
0,5-0,4 |
0,3-0,2 |
0,2-0,1 |
0,1-0,063 |
|
СКМ-1 |
50 |
25 |
25 |
||
СКМ-2 |
40 |
20 |
40 |
||
СКМ-3 |
50 |
40 |
|||
СКМ-4 |
30 |
70 |
|||
СКМ-5 |
70 |
30 |
|||
СКМ-6 |
80 |
20 |
|||
СКМ-7 |
100 |
||||
СКМ-8 |
100 |
||||
СКМ-9 |
100 |
||||
СКМ-10 |
70 |
30 |
|||
СКМ-11 |
30 |
70 |
|||
СКМ-12 |
30 |
70 |
|||
СКМ-13 |
50 |
50 |
|||
СКМ-14 |
50 |
50 |
|||
СКМ-15 |
40 |
60 |
|||
СКМ-16 |
75 |
25 |
Исследование влияния гранулометрического состава масс на основные физикотехнические свойства позволило установить следующее:
-
1. размер используемого зерна электрокорунда в пределах 1,0-0,063 мм практически не оказывает влияния на плотность, термическую стойкость и теплопроводность материала;
-
2. сочетание двух, трех фракций зерен электрокорунда в указанных пределах материалов не оказывает заметного изменения свойств материала;
-
3. уменьшение размера зерна электрокорунда приводит к пропорциональному возрастанию механической прочности и соответственно сопротивлению истираемости (износу) материала;
-
4. из исследуемых композиционных материалов с различным гранулометрическим составом наиболее высокой механической прочностью и сопротивлением к истиранию при сохранении прочих физико-технических свойств (термостойкости, теплопроводности и т.д.) обладают материалы с размером зерен от 1,0 до 0,2 мм.
Все исследованные материалы обладают высокой механической прочностью, термической стойкостью, высокой теплопроводностью и могут быть рекомендованы для защиты аппаратуры от агрессивной среды (в частности при футеровочных работах).
Так как размер используемого зерна электрокорунда в пределах 0,8-0,02 мм практически не оказывает влияния на плотность, термическую стойкость и теплопроводность материала, нами предложены оптимальные составы керамической массы, которые содержат тугоплавкую глину, шлак промышленного производства, жидкое стекло и кремнефтористый натрий, при следующем соотношении компонентов, масс., %: жидкое стекло – 20,0-30,0 %, тугоплавкая глина, фракции не более 0,5 мм – 5-10 %, электрокорунд, фракции до 1 мм – 65,0-70,0 %, кремнефтористый натрий – 3,4-5,1 % (таблица 2).
Полученная керамическая масса с содержанием электрокорунда, тугоплавкой глины, жидкого стекла и кремнефтористого натрия (введенного поверх общей массы для ускорения твердения) именно в таких соотношениях (65-70%х5-10%х20-30%) поз- воляет получить состав с высокими прочностными показателями, термостойкостью и химической стойкостью (в серной, соляной кислотах и в щелочном растворе), низким водопоглощением.
Таблица 2 - Оптимальные составы керамической массы
Образцы |
Гранулометрический состав электрокорунда |
Электрокорунд |
Тугоплавкая глина |
Жидкое стекло |
Na 2 SiF 6 (поверх массы в количестве 17% от массы жидкого стекла) |
СКМгл.-1 |
0,5-0,4 мм – 50% 0,2-0,1 мм – 50% |
65 |
5 |
30 |
5,1 |
СКМгл.-2 |
0,5-0,4 мм – 50% 0,2-0,1 мм – 50% |
66 |
6 |
28 |
4,7 |
СКМгл.-3 |
0,5-0,4 мм – 50% 0,2-0,1 мм – 50% |
67 |
7 |
26 |
4,4 |
СКМгл.-4 |
0,5-0,4 мм – 50% 0,2-0,1 мм – 50% |
68 |
8 |
24 |
4,0 |
СКМгл.-5 |
0,5-0,4 мм – 50% 0,2-0,1 мм – 50% |
69 |
9 |
22 |
3,7 |
СКМгл.-6 |
0,5-0,4 мм – 50% 0,2-0,1 мм – 50% |
70 |
10 |
20 |
3,4 |
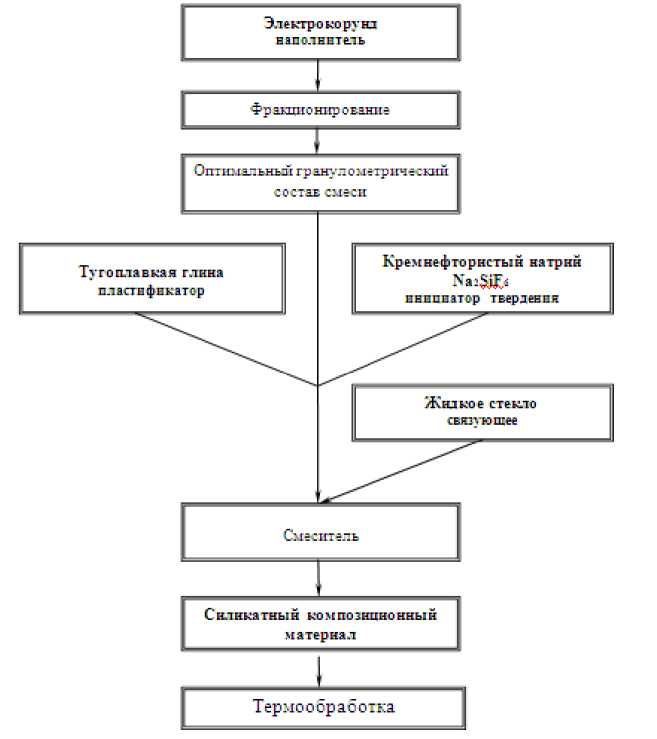
Рисунок 1 - Технологическая схема приготовления силикатных композиционных материалов.
При содержании электрокорунда более 70%, тугоплавкой глины более 10% и жидкого стекла более 30 %, наблюдается повыше- ние открытой пористости, показателей водопоглощения, газопроницаемости и снижение химической стойкости, полученные изделия теряют прочностные свойства.
Использование электрокорунда менее 65%, тугоплавкой глины менее 5 % и жидкого стекла менее 20 % недостаточно для получения изделия с высокими прочностными свойствами, химической стойкостью, низким водопогло-щением и газопроницаемостью.
При введении компонентов смеси в указанных соотношениях и соответствующем фракционном составе обеспечиваются условия более плотного заполнения пространства между частицами смеси и получения однородной пластичной массы.
На основе проведенных исследований нами разработана технологическая схема приготовления силикатных композиционных материалов, которая представлена на рисунке 1.
Заключение, выводы.
Полученные композиционные материалы на основе электрокорунда, являющегося отходом металлургического производства, обладают высокой потребительской стоимостью, значительной механической прочностью, термической стойкостью, высокой теплопроводностью и могут быть рекомендованы для защиты аппаратуры от агрессивной среды и в качестве конструкционного материала.
Список литературы Технологические решения в производстве химически устойчивых силикатных материалов
- Под.ред. А.А.Жарменова Комплексная переработка минерального сырья Казахстана. Состояние, проблемы, решения. в 10 томах, 2-ое издание, дополненное. Том 10: Инновация: идея, технология, производство.-Алматы, 2008, Глава 3, С.-153-171.
- Патент. РК № 21332. Химически стойкая футеровочная масса/А. А. Жарменов, С. К. Мырзалиева, Э. О. Аймбетова; опубл. 15.04.2011//Бюл. 2011. № 4.
- Патент. РК № 21333. Керамическая масса для изготовления конструкционных материалов/А. А. Жарменов, С. К. Мырзалиева, Э. О. Аймбетова; опубл. 15.04.2011//Бюл. 2011. № 4.
- Жарменов А. А., Мырзалиева С. К., Аймбетова Э. О. Использование отходов электро-металлургического производства для получения защитных композиционных материалов//Стекло и керамика. -2011. -№ 8. -С. 6-10. (г.Москва)
- Zharmenov A. A., Myrzalieva S. K., Aimbe-tova E. O. Use of by-products from the metallurgical industry in the manufacture of protective composite materials//Glass and Ceram. 2011. (USA). -V. 68. -N 7-8. -P. 242-246.