The production and research of nonwoven fabric from agricultural waste
Автор: Sarsenova G. Zh., Jurinskaya I. M., Ongar T.
Журнал: Вестник Алматинского технологического университета @vestnik-atu
Рубрика: Технология текстиля и одежды, дизайн
Статья в выпуске: 2 (140), 2023 года.
Бесплатный доступ
Currently, pollution due to textile materials is a crisis that threatens the whole world. Due to concern for the environment, our society has faced challenges when it comes to finding eco-friendly substitutes for textile fibers and leather materials. This can be achieved using renewable or recycled polymers or materials that are either readily biodegradable or easily recycled at the end of a product's life. Thus, the material is made from biodegradable natural resources, which is widely available, is economical and environmentally friendly. The article shows studies on the development of bio-based skin from fruit waste, the difference in the appearance of visual characteristics from banana peel, kiwi and apple residue, and depending on the basis for the cotton gauze material. Also, the article consists of the result of testing this material on a device for measuring tensile strength. The value of the study and the practical significance of this work lies in the possibility of further use of biologically based leather as a substitute for natural or artificial leather.
Sustainable fashion and textile, bio-based leather, material from wastes, ecofriendly material, sustainability
Короткий адрес: https://sciup.org/140300144
IDR: 140300144 | DOI: 10.48184/2304-568X-2023-2-201-207
Текст научной статьи The production and research of nonwoven fabric from agricultural waste
When it comes to slow fashion, we don't even know that this industry is so subject to change. Experts put an equal sign between slow and "green" fashion, believing that these two concepts define the ideal fashion that does not harm the environment. Now experts identify the following areas of slow fashion in the 21st century: environmentally friendly, conscious and ethical. The concept of eco-fashion is still being finalized, but the most important thing behind it is that “green” fashion is about caring for the environment, people's health and ethical treatment of animals.
By 2030, it will be producing roughly two big discoveries than the Paris Climate Agreement requires. From seaward to extreme rainfall and greater heatwaves, the effects of climate change are no longer ignored by society and the fashion industry, which will feel the consequences for its activities. [1]
Many fashion brands are shifting to natural sustainable fibers such as organic cotton, cotton, hemp and BCI (Better Cotton Initiative) certified linen. They aim to use materials derived from natural resources due to their biodegradability and recycled materials due to the closed cycle.
Some fashion brands spend most of their income looking for innovative new materials derived from waste, wood and other natural materi- als. Some of the examples include fibers such as soy, bamboo, milk and polylactic acid (PLA), which are produced from renewable biological sources and are biodegradable after disposal. These fibers provide a solution to the recycling problems associated with synthetic fibers.
Some sustainable fibers can be obtained from seaweed, lotus leaves, banana leaves, mushrooms, or even waste products such as orange peels and ground coffee bean waste.
Global consumption of nonwovens is growing; this applies to household, technical and disposable hygienic nonwovens. The rise of developing economies and the aging of populations will put additional pressure on resources, and there is a need to develop materials that have a much lower environmental impact and are sustainable. In addition, consumer awareness of the impact of household and industrial products on the environment is growing. Media attention, NGO campaigns, and product marketing have raised consumer expectations regarding the sourcing, production, and use of nonwovens.
Along with these market pressures, tighter government regulations regarding environmental impact have also been introduced, which apply to a number of industries; manufacturers of textiles and nonwovens are not immune. Due to various pressures, vendors and manufacturers consider the environmental impact of products along with performance and cost requirements.
In the past, the concept of product sustainability could be one-dimensional and only take into account limited aspects of the production, use, or disposal of a product. The practice of measuring impact through lifelong assessments means that manufacturers must consider the raw material and energy use of production, as well as the environmental impact and benefits during product use, and consider likely end-of-life scenarios. Often the use of nonwovens brings significant environmental benefits, which can justify the product's carbon footprint. Additional benefits can be achieved using renewable or recycled polymers or materials that are either readily biodegradable or easily recycled at the end of the product's life. For example, using recycled polypropylene (PP) geotextiles (nonwovens) can reduce the carbon footprint of a construction project, which outweighs the carbon footprint of manufacturing and transporting nonwovens.
The Scandinavians have long been concerned about environmental pollution caused by the global fashion industry. The only influential event in the fashion industry, the Copenhagen Fashion Summit was first held in 2009. Even back then, the participants were talking about this problem and insisted that corporations and brands apply the principles of sustainable fashion development in practice. Then the possibility of reducing hazardous emissions by 50 percent by 2050 was discussed. But today, the fashion industry continues to be one of the most environmentally hazardous, along with, for example, the oil industry. However, despite its relevance, sustainable fashion is just beginning to emerge in Kazakhstan and the CIS countries.
Material made from agricultural waste such as banana peel, fruit waste, etc. is completely safe and contains no harmful chemicals or toxins. Biobased textile can replace oil- and animal-based textiles and can be made from plant waste containing starch [2,3,4].
The main objectives of the study.
The main challenge is to develop an alternative source of textiles that is biodegradable, environmentally friendly and cost effective.
The purpose of the dissertation.
The purpose of this study is to produce biotextile material from agricultural waste such as banana peels as a replacement for conventional animal and oil-based textiles and to prove that the starch in banana peels can be used in the production of biodegradable plastic.
In accordance with the set goal, the following tasks were solved in the work:
-
- development of biotextiles based on banana peel;
-
- determination of the optimal parameters for the processing of waste of agricultural raw materials to impart mobile qualities;
-
- study of changes in the morphology of the surface of textile materials;
-
- study of the mechanism of interaction of components;
-
- study of textile properties (strength, creasing, breathability, etc.).
Research objects.
A textile material made from agricultural waste that can be used as a leather backing.
The scientific novelty of the results of the research carried out by the author is as follows:
Textiles made from agricultural waste such as banana peels, fruit waste, etc. are completely safe and contain no harmful chemicals or toxins. Biotextiles can replace petroleum and animalbased textiles and can be made from plant waste containing starch [5,6].
When it comes to slow fashion, we don’t even suspect that this industry is so subject to change. Experts put an equal sign between slow and "green" fashion, believing that these two concepts define the ideal fashion that does not harm the environment. Now experts identify the following areas of slow fashion in the 21st century: environmentally friendly, conscious and ethical. The concept of eco-fashion is still being finalized, but the most important thing behind it is: “green” fashion is about caring for the environment, people's health and ethical treatment of animals.
Practical significance.
The developed biotextile material using nonwoven technology provides a reduction in the process of environmental pollution, which continues at an enormous pace with increasing dynamics.
Expected results of the study.
Textile material from fruit waste will be made from banana peel, kiwi and apple waste showing differences in water absorption and decomposition behavior. Thus, this study can confirm that the leaves show good characteristics of banana compared to apple and kiwi. But kiwi fruit is expected to show good visual clarity and apple is dense and easy to produce as it has more starch. There should be no gaps or holes in the resulting plastic sheet.
The personal contribution of the author to obtaining the results presented in the dissertation is significant at the stages of planning, conducting and discussing the experiment, while developing material on a biological basis.
The aim of this study is to produce biobased textile material from agricultural waste such as banana peels as a replacement for conventional animal and oil-based textiles and to prove that the starch in banana peels can be used in the production of a biodegradable material [7,8].
Materials and Research Methods
The material of this work is an alternative textile material that can be used as a leather base. During the study, experiments were carried out to develop material from agricultural waste. Namely, from apple leftovers, from kiwi and banana peels. consists of two stages, the first stage is the development of a bioplastic from a banana peel. The second stage is the preparation of a skin-like film from banana peel, kiwi and apple waste.
Results and their discussion
After the development of bioplastics from banana peels, the idea arose to create a material to replace the skin. The main goal is to make bioplastic an elastic film so that it is also environmentally friendly and biodegradable. The following describes the process of creating an alternative leather based on agricultural waste [9].
-
1 Development of banana peel material
Grind the banana peel in a blender with the addition of water. It turns out a thick, dense mixture. To give a more antimicrobial property, this mixture is first boiled on high heat until the boiling stage. Next, leave on medium heat for 5 minutes and mix periodically. For ease of use in subsequent processes, the mixture should be allowed to cool for half an hour. If you look closely, you can see large parts of the banana peel in the mixture, since it was originally crushed with a kitchen blender, and not a special food waste grinder. Therefore, passing through a sieve is an important process to make the material smooth and uniform.
Now, when a uniform mixture is obtained, special ingredients such as glycerin and alginate are added. Here, sodium alginate is used to impart flexibility and elasticity. Once again you need to mix with a blender or with a mixer. It should be taken into account that the liquid mixture acquires the structure of the surface where it was poured. And you need to give preference to a flat surface, you can use parchment paper.
The result is an elastic film, which you can see in the figure 1 and 2. On the reverse side, where it was attached to parchment paper, the film is very similar to leather.
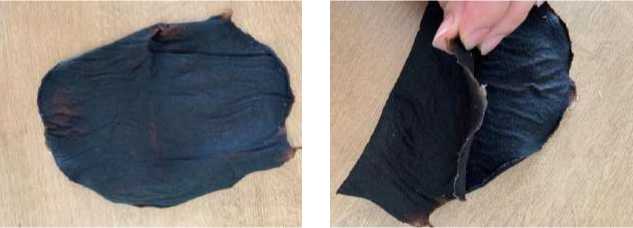
Figure 1,2 – Material from banana peel
-
2 Development of kiwi peel material
This experiment was also carried out on the kiwi peel. 5-6 kiwi peels were taken and the whole process, starting from grinding on a blender and end- ing with distribution to the surface, is repeated. In the Figure 3, you can see a mixture of kiwi peel. The final material is visible in the Figure 4.
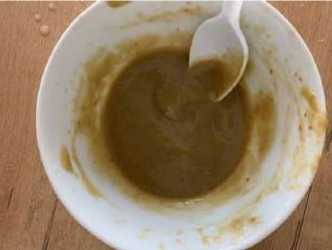
Figure 3 – Mixture from kiwi peel; Figure 4 – Material from kiwi peel
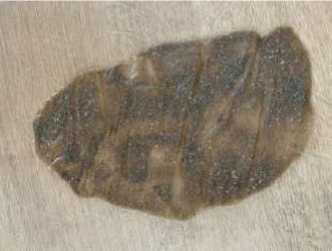
-
3 Development of material from apple waste
Making a review and research on materials from peel and residues in the Appleskin juice factory, a material was developed from apple waste. Unlike material from Mabel Appleskin, which is based in Italy, 100% apple waste is used in the study. Appleskin blends apple waste powder with polyurethane and other natural agricultural fibers.
As a general rule, the bio-base content should not be less than 50% when mixed with water-based polyurethane.
Here, the process is identical to that of developing banana peel material. Unlike bananas, apples have seeds inside and a tip, so they need to be removed [10].
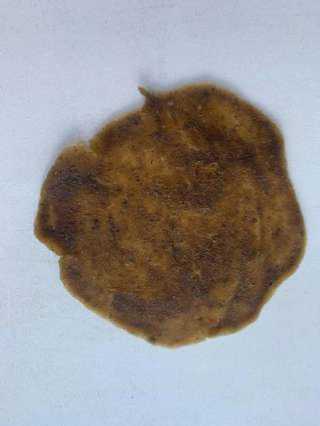
Figure 5,6 – Material from apple waste
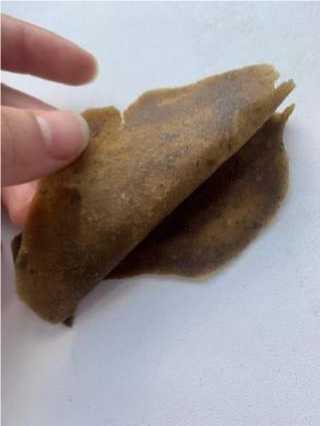
The result is also an elastic and skin-like material. Due to the fact that the apple is lighter than the banana, it looks dirty from the back.
-
4 Tensile strength of banana peel material on cotton gauze fabric
In the article that was discussed at the ATU conference there was also a study on the textile material of a mixture of banana peels. Resulting homogeneous thick mixture of banana peel is evenly distributed over the surface where the cotton gauze fabric was laid [11].
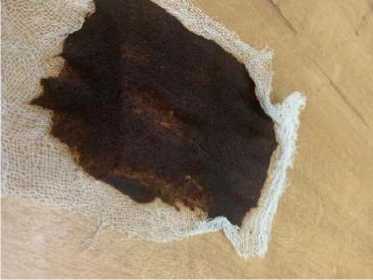
Figure 7,8 – Material from banana peel
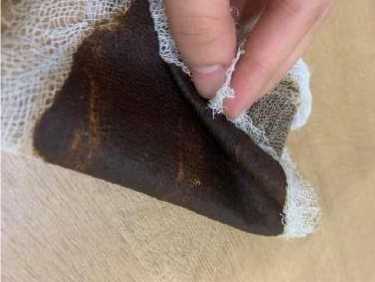
After 2 days of drying, the result is a biobased material that visually resembles leather. Textile fabric, in turn, made the material durable. In figures 7 and 8 shown final bio-based leather from banana peel on cotton gauze fabric.
The tensile strength characteristics of a fabric refer to the nature of the mechanical deformation of the fabric when subjected to tensile forces in the warp and weft directions. Generally speaking, it is a phenomenon in which tissue is elongated and deformed, or even torn and dam- aged by an external force when stretched. When the fabric begins to stretch, the strain is basically the stretching of the fiber's macromolecular chains themselves, i.e., strain in bond length and bond angle. Stretched yarn becomes straight, basically in accordance with Hooke's law, while yarn that is not stretched becomes more crooked [12,13,14].
Figure 9 and 10 show the process of testing a banana peel material on a textile tensile testing machine.
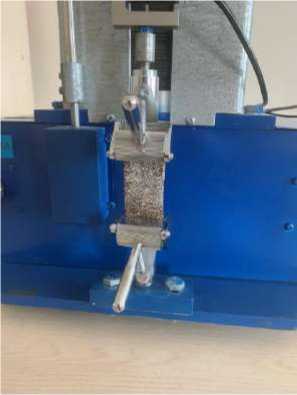
Figure 9 – Before testing; Figure 10 – After testing
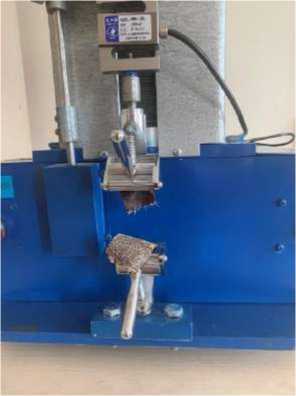
The test result as in figure 11 shows:
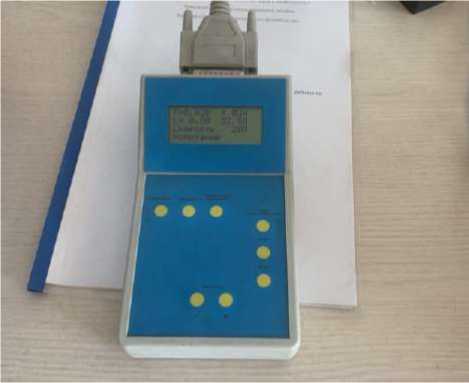
Figure 11 – Tensile strength result
The strength of the fabric is determined according to GOST 3813-72 Textile fabrics and piece goods. Methods for Determination of Tensile Characteristics. The strength of tissues is an important indicator characterizing its mechanical properties. The tensile strength of a fabric is understood as the magnitude of the greatest load that precedes the rupture of a strip of fabric 5 cm wide [15].
Conclusions
In recent years, concerns about sustainability in any area of industrial production have led to an urgent need to expand the use of natural mate- rials and replace non-renewable fossil raw materials. Although leather is bio-based and renewable, these considerations have not led to a leather renaissance.
Three kinds of material were prepared from fruit waste, which show differences in characteristics and properties. Basically, the materials turned out to be flexible and homogeneous. Can be further used in the fashion industry as bio-based leather. By a roughly identical process, leatherlike materials were developed from apple waste and from kiwi and banana peels.
Determination of tensile strength characteristics was carried out at the break of the machine after checking the serviceability, reliability of fixing the load, limit switch, chain and belt drive guards.
Список литературы The production and research of nonwoven fabric from agricultural waste
- A. Pellis, E. Herrero Acero, L. Gardossi, V. Ferrario, G.M. Guebitz. “Renewable building blocks for sustainable polyesters: new biotechnological routes for greener plastics” Polymer. Int., vol. 65, no. 8 (2016): 861–871.
- N.A. Sagar, S. Pareek, S. Sharma, E.M. Yahia, M. G. Lobo “Fruit and Vegetable Waste: Bioactive Compounds, Their Extraction, and Possible Utilization” Compr. Rev. Food Sci. Food Saf., vol. 17, no. 3 (2018): 512–531.
- Jawad, A.H., Rashid, R.A., Ishak, M.A.M., Ismail, K. “Adsorptive removal of methylene blue by chemically treated cellulosic waste banana (Musa sapientum) peels”, J. Taibah Univ. Sci. 12 (6), (2018): 809–819.
- Baiano A., “Recovery of biomolecules from food wastes—a review”, Molecules 19 (2014):14821–14842.
- Balasundram N, Sundram K, Samman S. “Phenolic compounds in plants and agri-industrial byproducts: antioxidant activity, ocurrence, and potential uses”, Food Chem 99 (2006):191–203.
- Ade-Omowaye BIO, Angersbach A, Taiwo KA, Knorr D. “Use of pulsed electric field pre-treatment to improve dehydration characteristics ofplant based foods”, Trends Food Sci Technol 12 (2001):285–295.
- Bharathiraja S, Suriya J, Krishnan M, Manivasagan P, Kim SK. “Production of enzymes from agricultural wastes and their potential industrial applications” Adv Food Nutr Res 80 (2017):125–48.
- P. Astuti, A. A. Erprihana, “Antimicrobial Edible Film from Banana Peels as Food Packaging” American Journal of Oil and Chemical Technologies,vol. 2 (2018): 65-70.
- Vinod, A., Sanjay, M. R., Suchart, S., & Jyotishkumar, P.. “Renewable and sustainable biobased materials: An assessment on biofibers, biofilms, biopolymers and biocomposites” Journal of Cleaner Production, Article 120978 (2020):258.
- Gomes, A.P., Mano, J.F., Queiroz, J.A., Gouveia, I.C.. “Layer-by-layer deposition of antimicrobial polymers on cellulosic fibers: a new strategy to develop bioactive textiles” Polym. Adv. Technol. 24(2013): 1005-1010.
- I.M.Jurinskaya, T.Ongar, G.Zh.Sarsenova. “Development and research on the action with textile material of bioplastic from agricultural waste” UTECA International Scientific-Practical Conference, Azerbaijan, Ganja (2022): 209-210.
- Meyer, M., Dietrich, S., Schulz, H., Mondschein, A. “Comparison of the technical performance of leather, artificial leather, and trendy alternatives”. Coatings 11(2), (2021): 226.
- G. Ferrara, M. Pepe, E. Martinelli, R.D. Toledo Filho “Tensile behavior of flax textile reinforced lime-mortar: Influence of reinforcement amount and textile impregnation” Cem. Concr. Compos. 119 (2021): 709.
- Huda MS, Mohanty AK, Drzal LT, Schut E, Misra M. “Green composites from recycled cellulose and poly (lactic acid): physico-mechanical and morphological properties evaluation” J Mater Sci, 40(16) (2005): 4221–4229.
- Mathew, S., Brahmakumar, M., Abraham, T. E. “Microstructural imaging and characterization of the mechanical, chemical, thermal, and swelling properties of starch–chitosan blend films” Biopolymers, 82(2) (2006): 176–187.