Vacuum metallization of ultrafiltration polymer membranes with iron-chromium-nickel alloy
Автор: Slavova V.O., Petrov S.P., Bayeva M.R.
Журнал: Вестник Алматинского технологического университета @vestnik-atu
Рубрика: Естественные науки
Статья в выпуске: 6 (96), 2012 года.
Бесплатный доступ
Polyacrylonitrile (PAN) ultrafiltration (UF) membranes are prepared by the phase inversion in a wet process. PAN membranes have the typical asymmetric structure. The possibility for vacuum metallization of ultrafiltration polymer membranes with iron-chromium-nickel alloy was studied after preliminary modification with Sn 2 + in basic medium. The influence of pre-modification on polymer surface before the actual vacuum metallization is a prerequisite for successful metallization. The change of transport and selective characteristics of the vacuum metal coated membranes was studied, as well as the durability of the vacuum obtained coating during membrane performance. The metal coating was prepared by magnetron sputtering of iron - chromium - nickel alloy (H18N9T). The surface properties were investigated by scanning electron microscopy (SEM).
Polyacrilonitrile, membrane, vacuum metallization, ultrafiltration, magnetron sputter deposition
Короткий адрес: https://sciup.org/140204984
IDR: 140204984
Текст научной статьи Vacuum metallization of ultrafiltration polymer membranes with iron-chromium-nickel alloy
Membranes processes are states of the technologies in various industrial sectors, including gas separation, wasterwater treatement, food processing and medical application. Membrane modification is aimed either for improving the selectivity or creating an entirely novel separation function. Surface modification is a synergy between the useful properties of the base membrane and the novel functional layer [1].
As polymer systems, the membrane structures can be metallized using either chemical or physical methods. The process of metallization provides possibilities to change membrane transport and selective properties thus making them applicable in various fields of science and technology. The preparation of the metal coatings depends on polymer characteristics, metallization methods and the technological parameters of the process.
The objective of this work is the preparation of membranes with thin selective film which possesses a high stability, a low hysteresis area of water permeability and a possibility the metal thin film to be used as a centre of a complex formation. Depending on the characteristics and the conditions for the deposition of the metal thin film various membranes with different characteristics are obtained.
Two types of polyacrylonitrile membranes with differing characteristics and structure were studied to find the effect of exposition on the vacuum metallization, the possibilities for preliminary chemical modification of membrane surface. The structure and the basic transport and selective characteristics of the membranes were studied.
The metal coated membranes are polymer membranes covered with thin metal layer. Metal can be deposited on membrane surface by several methods: magnetron sputtering, chemically – in a solution, vacuum coating methods, including ion bombardment and thermal evaporation [2, 3].
The process of metal coating of membranes has a number of specific characteristics related to the type of polymer material and the method of metallization.
Experimental
The membranes used for the present studies were prepared under laboratory conditions by the phase inversion method, known also as the method of Loeb [4]. The first membrane (PAN I) had the following composition: PAN – 16.25 mass%, PMMA – 0.25 mass%, CuSO 4 .5H 2 O – 1.5 g/l. The other membrane (PAN II) had the following polymer composition: PAN – 16.25 mass%, PMMA – 0.25 mass%, CuSO 4 .5H 2 O – 2.0 g/l. The use of PMMA of modifying polymer gives membranes of higher efficiency. The change of transport characteristics of the membranes was due to the incompatibility of the two polymers. The addition of PMMA in the polymer solution during the phase inversion leads to formation of membranes of higher porosity which stipulates the lower selectivity of the membranes. This, in turn, determines the necessity for additional modification which can be accomplished either in the polymer solutions or on the working surface of the membranes obtained.
The metal coating was prepared in vacuum installation BUP-5 (Russia) by sputtering flat target of iron-chromium-nickel alloy (H18N9T) with size ø 100 х100 mm, at distance target/membrane L M - N = 180 mm and specific
-
• N = 5,4 W/cm 2
sputtering power p .
Magnetron sputter deposition of iron-chromium-nickel alloy was carried out at initial -3 vacuum in the operation chamber i a, medium Ar with purity of 99,99% and working
■ P =4 10-2 Pa pressure in the chamber w . 0 a. Five deposition times were used: 5, 10, 15, 20 and 25s. At the end of deposition process, the membranes were cooled to room temperature in the Ar medium and then they were taken out in air. The power of the direct current source of the magnetron was 8 kW with smooth variation of current 0÷10 А.
The performance characteristics of the metallized membranes – permeation (efficiency) flux (J) and retention (R) were determined on a laboratory apparatus “Sartorius“ SM-165 (England) by the following equation:
J = V^t)(m 3/ m2h) R = 0
Sbt
—
—
0 C 0
C .100 ( % )
Eq. (A.1)
where V(t) denotes the volume of passed 3
liquid ( m ); Sb – effective area of the membrane
2C
( m ); t – time (h); 0 - initial concentration
( kg / m ); Ci - concentration of the filtrate ( kg / m 3 ).
Membrane selectivity was measured using the calibrant “Albumin” – human serum
/Mw=67000/ (Fluka) with initial solution concentration 1 g/l. The separation ability of the membrane compared to the calibrant was determined spectrophotometrically at wave length λ=280 nm on a UV/VIS spectrophotometer “Unikam”-8625- France.
The micrographs have been taken on a scanning Electron Microscope JEOL JSM-5510. Prior to viewing the membrane sample was fractured in liquide nitrogen gold coated.
Results and discussion
Knowing and controlling the process of interaction between the metal layer and the polymer membrane is very important for the vacuum metallization, since it determines the type and quality of the metal coating [5, 6]. The factors determining the process are the material of substrate (membrane) and coating, the preliminary treatment of the membranes and the technological and conditions and parameters [7]. One of the conditions for better metallization (better adhesion between the polymer and the metal coating) is the preliminary treatment of the polymer surface. It ensures activation of the polymer surface to facilitate the formation of nuclei for the following vacuum metallization [8]. For this purpose, the opportunities for modification of the polymer structure with various chemical components were preliminarily studied [9, 10]. In this case, the most suitable turned out to be the aqueous system containing 50 g/l SnCl2.2H2O, 90g/l K-Na-tartarate, 75g/l NaOH – further referred to as “the modifying system”. The preliminary chemical modification of both types of membranes with the aqueous system selected appeared to be good enough which can be seen in Fig. 1 where the efficiencies of modified and unmodified membranes are shown for comparison.
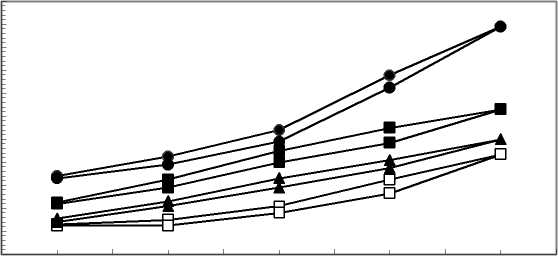
0,1 0,2 0,3 0,4 0,5
pressure P,MPa
Fig. 1 - Hysteresis curves of modified and unmodified ultrafiltration membranes □-.PAN I ▲- PAN I mod ■-PAN II •- PAN II mod.
The preliminary chemical modification of the membranes improves the adhesion between the polymer and the metal coating which is determined by the processes taking place within the system. The treatment with the aqueous solution activated the polymer surface, so the deposition of Sn (II) onto polymer surface did not occur in the sensibilizing solution but during the following washing of the polymer surface when, due to hydrolysis:
SnCl 4 — + H 2 O---- > Sn ( OH ) Cl + H + + 3Cl _
Eq. (A.2)
the scarcely soluble product
Sn OH .Cl
1.5 0.5
is
formed. It remained on membrane surface due to laminar coagulation and can form a layer of tens to thousands Å.
The modified membranes were vacuum metallized under the conditions described in the
Experimental section and their basic characteristics were studied.
As can be seen from Fig. 2, the water efficiency of chemically modified and vacuum metallic-zed membranes decreased from 54 l/m2h to 28 l/m2h with the increase of exposition from 5 to 25 s.
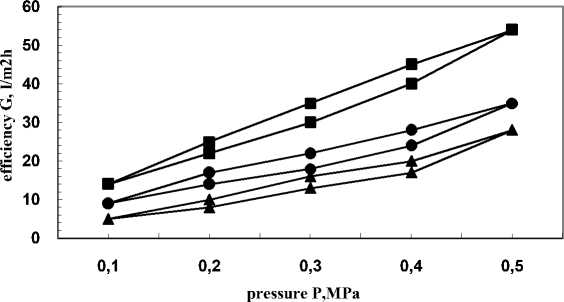
Fig. 2 - Hysteresises of membranes PAN-I chemically treated with the modifying system and vacuum metallized with H18N9T alloy ■-5 s •- 15 s ▲-25 s.
During the process of metallization, membranes efficiency significantly decreased compared to the chemically modified ones. Thus, this process is used to correct the selective layer of the membrane. A comparison of the efficiencies of the initial non-treated and nonmetallized membrane (87 l/m2h) and chemically modified non-metallized one (97 l/m2h) with the efficiency of a membrane coated with H18N9T, it can be seen that the latter had lower efficiencies for water regardless of the sputtering time (Fig. 2).
Some additional studied also showed that the adhesion metal-polymer can be strengthened by preliminary deposition of a sub-layer of oxides of the metals used for the coating. Thus, carrying out chemical modification, followed by deposition of metal oxide sub-layer and main coating, better mechanical strength of the modified membrane structure can be obtained. The basic characteristics of such membranes are presented in Fig. 3.
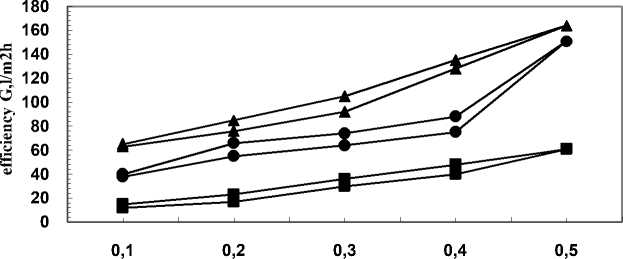
pressure P,MPa
Fig. 3 - Hysteresis curves of PAN-I membranes chemically modified and vacuum metallized with H18N9T, with additional sub layer of the oxides of the alloy metals. ■-5 s •- 15 s ▲-25 s.
It can be seen from the membranes’ hysteresis curves that their water permeability increased from 61 l/m2h to 164 l/m2h with the increase of sputtering time from 5 to 25 s. This tendency was contrary to the one discussed abobe for membranes of the same polymer composition but having only main coating. This was probably due to the additional sub-layer of the oxides of the metals of the sputtered alloy and the possibility for formation of a uniform metal surface on the membranes (Fig. 4).
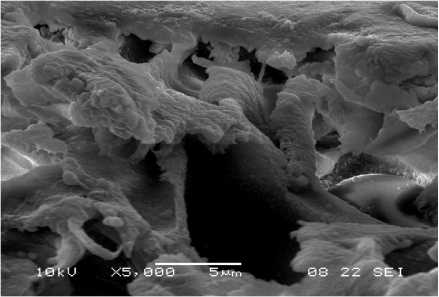
a
Fig. 4 - SEM (secondary) micrographs of PAN-I membranes treated with the modifying system and vacuum metallized with iron-chromium-nickel alloy at different sputtering times: а – 5 s, b – 25 s.
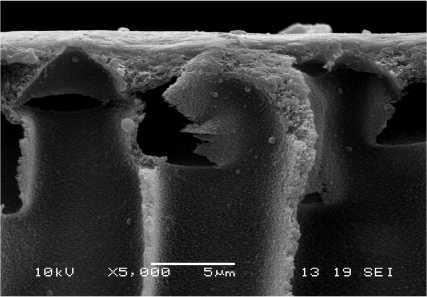
b
The second type of membranes used for the present studies (PAN-II) have much higher water efficiency compared to the PAN-I membranes, measured as initial structures. The higher efficiency leads to lower selectivity of these membranes (compared to PAN-I), as determined by the experimental data. It was interesting to find how this higher efficiency would be affected by the vacuum metallization. With the increase of coating time from 5 to 25 s, their efficiency increased from 87 to 159 l/m2h (Fig. 5). The value of the efficiency at exposition time of 25 s (159 l/m2h ) was close to these of chemically non-treated and non-metallized one (128 l/m2h) and chemically treated nonmetallized one (198 l/m2h) membranes.
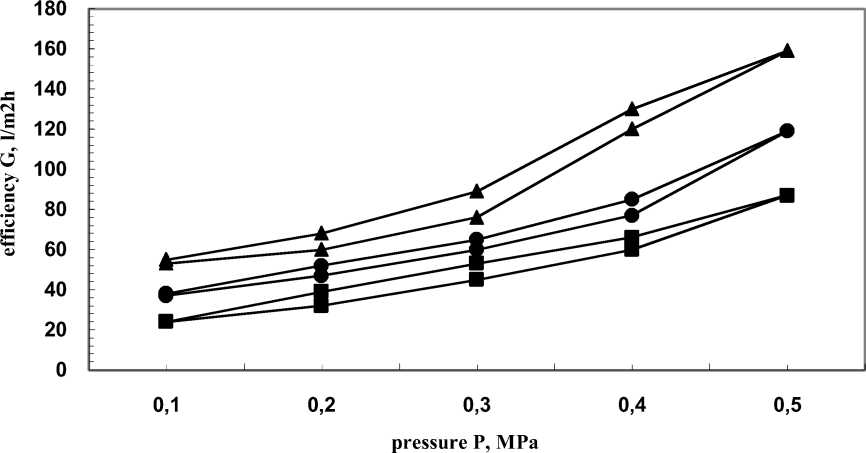
Fig. 5 - Hysteresis curves of PAN-II membranes chemically modified and vacuum metallized with H18N9T alloy with sub layer of the oxides of alloy metals. ■-5 s •- 15 s ▲-25 s.
Similar to the other type of membranes studied, the small exposition times have higher effect on the surface in the presence of an sub-layer of metal oxides The deposition of an additional oxide sub-layer gives a system where it is possible to obtain denser structure through the interaction between the metal oxides and small number of atoms, which could lead to destructive processes in the selective layer of the membrane under longer exposition. When only metal coating is deposited, membrane characteristics depend simply on the thickness of the metal coating.
The studies of membrane selectivity towards calibrant Albumin showed a dependence proportional to their efficiency. The structures of the initial membranes determine their selectivities while the presence of an oxide sublayer changes it within certain interval. These changes, however, are small. For the membranes with polymer composition PAN-II modified chemically with the solutions described above and vacuum coated with H18N9T alloy, the selectivity towards Albumin increased 86% (5 s exposition) to 88% (25 s) which is close to the valoes for the initial non-coated membranes (Fig. 6). The membranes with the same polymer composition, same chemical modification and vacuum coated with H18N9T alloy but with additional sub-layer of metal oxides, the selectivity decreased from 78% (5 s exposition) to 75% (25 s).
For the chemically modified and vacuum metallized membranes with composition PAN-I, the selectivity towards Albumin increased with exposition time from 84 to 86% which is the same tendency observed for the other type of membranes studied. The selectivities of the membranes of the same polymer composition but with additional sub-layer of metal oxides remained the same (72%) regardless of the sputtering time (Table 1).
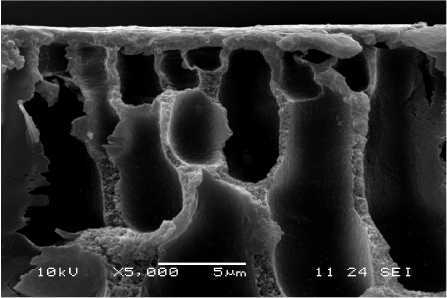
Fig. 6 – SEM (secondary) micrographs of PAN-II membranes treated with the modifying system and vacuum metallized with iron-chromium-nickel alloy at different sputtering times: а – 5 s, b – 25 s.
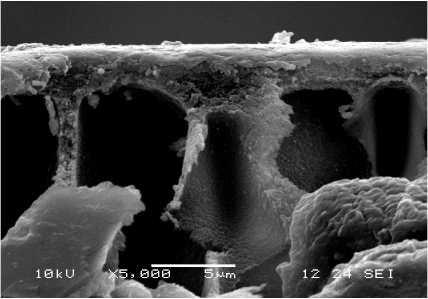
b
Table 1 - The change of selectivity (R, %) towards Albumin of vacuum metalized PAN membranes
Membrane type |
5 s |
15 s |
25 s |
PAN-II without sub-layer |
86 % |
87% |
88% |
PAN-II with sub-layer |
78 % |
76 % |
75 % |
PAN-I without sub-layer |
84 % |
85 % |
86 % |
PAN-I with sub-layer |
72 % |
71 % |
72 % |
Table 2 - The change of selectivity (R, %) towards Albumin at different intervals of the washing of porous structure of different type membranes to prove the stability of the metal coating. The washing was carried out under ultrafiltration regime with water volumes from 200 to 1500 ml
Membrane type |
200 ml |
500 ml |
1000 ml |
1500 ml |
PAN-II without sub-layer |
86 % |
85% |
85% |
86% |
PAN-II with sub-layer |
78% |
76% |
78% |
77% |
PAN-I without sub-layer |
85% |
86% |
86% |
85% |
PAN-I with sub-layer |
72% |
72% |
72% |
71% |
To establish the stability of the metal coating of the membranes, their selectivity was studied at different intervals of flushing the porous structure of the membranes. The flushing was carried out in regime of ultrafiltration with water volumes from 200 to 1500 ml (Table 2).
The change of the selectivities of the membranes studied was found to be insignificant and within the preciseness of the experimental method used. The standard deviation average value is 2-3 %.
The metallized membranes are a new class of membranes that possess properties conductance and success can be used both in the process of ultrafiltration and electrodialysis processes, electrophoresis or on the magnetic structure in baromembrannite processes. Also, these membranes can be used to selectively concentrate and extract valuable elements or toxic substances from multicomponent aqueous solutions - extracted proteins and enzymes
Conclusions
-
1. The studies carried out showed that the method of vacuum metallization can be used for modification of polymer membranes to obtain structures and properties necessary for specific processes.
-
2. The whole procedure depends on the initial membrane structure, polymer type, method of preliminary treatment and the degree of emission metallization.
-
3. The following dependence was observed for the membranes having an additional sub-layer of metal oxides: the values of the selectivity remained almost unchanged which means that the additional sub-layer improves the adhesion between the main metal coating and the polymer substrate.
Список литературы Vacuum metallization of ultrafiltration polymer membranes with iron-chromium-nickel alloy
- Ulbricht, M//Polymer. -2006. -№47. -Р. 2217-2262.
- Baker, R.W. Membrane Technology and Applications/2nd edn, John Wiley & Sons, Ltd, Chichester, 2004, Chapters 2, 3, 5, 6 & 9.
- Mulder, M. Basic Principle of Membrane Technology./2nd edn, Kluwer Academic Publishers. -Dordrecht. -1996.
- Loeb S., Sourirajan//Adv. Chem. Ser. -1962. -38. -Р. 117.
- Nunes, S. P. and al. Membrane Technology in the Chemical Industry/2nd edn, Wiley-VCH, Weinheim. -2006. -Part 1.
- Kato, K., and al.//Progress in Polymer Science. -2003. -№ 28. -Р. 209-259.
- Lipin, Yu, and al. Vacuum metallization of polymer materials//Khimiya. -Moscow. -1977.
- Sacher, E. Metallization of polimers//Edited. Proceedings of the Montreal Workshop on Polimer, Kluwer Academic Plenum Publishers. -2002. -Р. 208.
- Charbonnier, M. and al. Ni direct electroless metallization of polymer by a new palladium-free process//Surface & Coating Technology. -2006. -№200 (16/17). -Р. 5028-5036.
- Charbonnier, M., and al. Polymer pretreatments for enhanced adhesion of metals deposited by the electroless process//International Journal of Adhesives. -2003. -№23 (4). -Р. 277.