Технология. Рубрика в журнале - Вестник Южно-Уральского государственного университета. Серия: Машиностроение
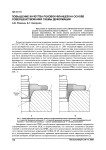
Повышение качества поковок фланцев на основе совершенствования схемы деформации
Статья обзорная
Предложена и опробована новая схема деформации методом прошивка-раздача-выдавливание/вытяжка-калибровка в технологии штамповки фланцев воротниковых. На основе анализа результатов компьютерного моделирования и физических экспериментов установлен критерий качества поковок и рекомендована область применения схемы.
Бесплатно
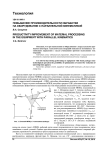
Повышение производительности обработки на оборудовании с параллельной кинематикой
Статья научная
Показано, что при выполнении на оборудовании с параллельными приводами некоторых технологических операций появляется возможность оптимизации управления с целью уменьшения времени выполнения этих операций.
Бесплатно

Повышение производительности точения резьбы резцами с керамическими пластинками
Статья научная
Несмотря на множество хорошо разработанных процессов высокопроизводительного формирования резьб давлением на деталях массового производства в некоторых случаях приходится нарезать резьбы резцами. К таким случаям относят нарезание резьбы на тонкостенных заготовках или повышенной твердости, нарезание резьб несимметричного профиля. Ведущие инструментальные фирмы разрабатывают и выпускают для этих случаев специальные резьбовые пластины и дают программы для расчета режимов резания и схемы срезания припуска в зависимости от шага резьбы и твердости обрабатываемой заготовки. Обычно резьбовые пластины изготавливают из металлокерамических твердых сплавов, зачастую с упрочняющими покрытиями. Особенностью профиля резьбовых пластинок является малый радиус скругления вершины, связанный с размерами шага нарезаемой резьбы. Это обстоятельство приводит к высоким механическим и тепловым нагрузкам на вершину резьбовой пластины и вынуждает для обеспечения приемлемой стойкости снижать режимы резания: скорость, связанную с частотой вращения заготовки, и подачу врезания на каждый рабочий ход. В последнее время появились пластинки из минералокерамики на основе окиси алюминия с легированием карбидами тугоплавких металлов. Эти пластинки обладают высокой теплостойкостью, что позволяет повышать скорость резания. Однако в литературе практически нет сведений о применении пластинок из минералокерамики для нарезания резьбы на высокопрочных заготовках. В статье приведены результаты экспериментов по нарезанию резьбы резцами с керамическими пластинками на стальных заготовках высокой твердости (HRC 52…55). Показано влияние отрицательного переднего угла, величины заглубления резца и подачи на врезание на составляющие силы резания. Доказано, что при оптимизации геометрических параметров пластинок возможно высокопроизводительно нарезать резьбы на закаленных заготовках из высокопрочных материалов, что в сочетании с меньшей стоимостью материала пластинок сулит существенные экономические преимущества.
Бесплатно
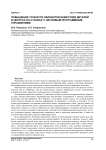
Статья научная
В статье описывается метод расчета траектории движения токарного инструмента на станке с числовым программным управлением для компенсации упругой деформации при обработке заготовки. В процессе точения тел вращения с малой жесткостью под действием режущей силы Py происходят упругие деформации, что негативно влияет на точность обработанной поверхности. Вследствие этого появляется погрешность в виде бочкообразности, седлообразности или комбинации данных погрешностей в зависимости от жесткости станка и его отдельных частей. На основе расчета деформации при постоянной глубине резания предлагается определить погрешность, которую необходимо в дальнейшем компенсировать с помощью приведенного метод расчета. Он позволяет проводить компенсацию за счет предыскажения траектории на этапе программирования управляющей программы. Тем самым в процессе точения будет получен требуемый диаметр с минимальными погрешностями, что в свою очередь положительно будет влиять на сокращение дополнительной обработки для удаления погрешностей формы и повышения качества обработки детали.
Бесплатно
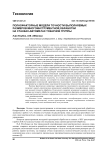
Статья научная
В данной статье показано современное состояние разработки теории проектирования многоинструментной обработки на станках-автоматах токарной группы. Отмечено, что существующие модели погрешности обработки учитывают лишь плоско-параллельные перемещения подсистем технологической системы вдоль координатных осей декартовой системы координат X, Y, Z. Такой подход к моделированию процесса образования погрешностей обработки допустим для деталей, имеющих габаритные размеры одного порядка по всем координатным направлениям. Однако на практике нередки случаи, когда обрабатываются детали с габаритными размерами, существенно различающимися в разных направлениях. В этих случаях существенный вклад в погрешность обработки могут вносить повороты обрабатываемой заготовки, особенно по направлениям преобладающих габаритных размеров. Поэтому указана необходимость учета угловых перемещений заготовки под действием сил резания в этих моделях. С этой целью были разработаны полнофакторная матричная модель искажения и поля рассеяния выполняемых размеров многоинструментной двухсуппортной обработки. В этих моделях учитывается комплексная характеристика податливости технологической системы, то есть, кроме собственных упругих свойств системы (плоско-параллельных перемещений технологических подсистем, их угловых перемещений вокруг базовых точек), еще и параметры наладки, для которой эта податливость рассматривается. Поэтому для формирования комплексной характеристики податливости подсистемы были проведены эксперименты по определению податливостей подсистемы технологической системы. Наличие фактических матричных характеристик податливости для реального станка позволяет оценить практическую применимость разработанных полнофакторных матричных моделей точности обработки. В результате появится возможность выявлять степень влияния на точность обработки комплекса технологических факторов, включая структуру многоинструментной наладки, деформационных свойств подсистем технологической системы, режимов резания.
Бесплатно

Получение металлических микропорошков газодинамическим распылением
Статья научная
Показаны технологические схемы распыления металла с плавлением в тигле и бесконтактным способом. Оценены режимы и характеристики получаемого материала.
Бесплатно
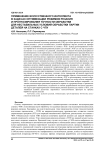
Статья научная
В статье рассматривается возможность применения искусственного интеллекта (ИИ) при технологической подготовке производства (ТПП) на стадии расчета оптимальных режимов резания с учетом нестабильных условий обработки партии деталей на примере плоского шлифования, выполняемого на станках с ЧПУ. Задачи прогнозирования точности обработки и оптимизации режимов резания для станков с ЧПУ до сих пор не решены полностью из-за сложности их решения, связанной: со слишком большой размерностью оптимизируемого поля параметров, с необходимостью одновременного решения большого количества сложных взаимосвязанных математических моделей процесса обработки, оптимизацией многочисленных параметров режимов резания и учетом ограничений целевой функции в многомерном пространстве состояний процесса обработки, сложностью учета разнонаправленного влияния различных нестабильных технологических факторов на процесс съема припуска, сложностью моделей формирования технологического размера и параметров качества обрабатываемой поверхности. Большая размерность задач требует огромных вычислительных мощностей суперкомпьютерной техники, которая не имеет ни одно производственное предприятие. Применение ИИ позволяет преодолеть «проклятие размерности». Задачи прогнозирования точности обработки и оптимизации режимов резания предложено решать в заводских условиях путем применения обученной сверточной нейронной сети (НС), использующейся для распознавания образов, позволяющей рассчитывать оптимальные режимы резания для станков с ЧПУ и прогнозировать точность обработки. Обучение НС проводится на множественной выборке (сто тысяч и более операций с ЧПУ) с готовыми оптимальными режимами резания. Подготовка выборки операций с готовыми оптимальными решениями проводится заранее на суперкомпьютере с применением программного обеспечения, созданного на основе разработанной методики комплексной структурно-параметрической оптимизации режимов резания для станков с ЧПУ, учитывающей влияние различных переменных технологических факторов на процесс обработки партии деталей.
Бесплатно
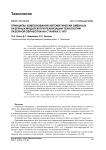
Статья научная
Статья посвящена вопросам разработки автоматически сменных модулей для реализации технологий лазерной обработки на станках ЧПУ. В основе решений использована элементная база оптоволоконных лазеров. Предложено техническое решение данного устройства, в котором оптическая система, коллиматор и излучатель лазера выполнены в виде отдельного модуля, скомпонованного из отдельных блоков, параметры каждого из которых определяются требованиями заказчика. При этом модуль выполнен сменным и вне рабочих циклов ЧПУ-обработки может быть установлен в инструментальном магазине станка. Модуль устанавливается в шпиндель из инструментального магазина станка автоматически по команде системы ЧПУ, а непосредственно источник излучения вынесен за пределы рабочей зоны станка. Связь с модулем обеспечивается оптоволоконным кабелем. Предложенное техническое решение будет востребовано на рынке производственных услуг за счет кратного снижения капиталоемкости, так как отсутствует необходимость приобретения отдельной позиции лазерного центра, обеспечивается высокая производительность и точность обработки, не требуется дополнительная транспортировка и переустановка детали, сокращаются потери времени на обработку всей детали. Применительно к этому в статье предложена методология перекомпонования устройств для лазерной обработки и приведены основы принципа их блочно-модульного компонования. В основе принципа блочно-модульного компонования лежит кинематический анализ устройств, который позволяет, исходя из требований заказчика, определить комплект блоков для компонования устройства в конечном состоянии поставки заказчику. Развитием этого стала возможность проработки конструкции устройств как на этапе анализа и модернизации уже существующих исполнений, так и на этапе подготовки коммерческого предложения заказчику.
Бесплатно
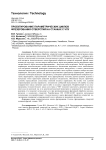
Проектирование параметрических циклов фрезерования отверстий на станках с ЧПУ
Статья научная
В работе представлено описание этапов проектирования технологического цикла, реализующего фрезерную обработку отверстий концевой фрезой. Также представлено разработанное программное обеспечение (ПО) CONICALINT, генерирующее G-код с набором аргументов, используемый для вызова технологического цикла из памяти системы ЧПУ. Разработанный алгоритм технологического цикла фрезерной обработки отверстий концевой фрезой имеет ветвистую структуру, так как имеется выбор между двумя методиками расчёта внутренних параметров цикла и двумя методами фрезерования - попутным либо встречным. Расчёт внутренних параметров технологического цикла заключается в вычислении координат точек, необходимых для построения винтовой траектории движения режущего инструмента, а также в вычислении значения максимально допустимой величины винтового шага в рамках заданного набора входных параметров. Исходные данные для расчета представлены тринадцатью параметрами, характеризующими геометрию режущего инструмента, геометрию требуемой обработанной поверхности, а также параметрами, определяющими метод фрезерования, методику расчёта режима резания и начальные точки траектории движения режущего инструмента. Обозначено восемь граничных условий, определяющих допустимые значения входных параметров. На основе этих условий спроектирована система неравенств с комплектом сообщений пользователю об ошибке в случае некорректного ввода значения какого-либо из входных параметров. Разработанный G-код подпрограммы технологического цикла для станка с ЧПУ позволяет рассчитать движение инструмента как по винтовой, так и по конической винтовой траектории в зависимости от входных параметров, что позволяет использовать его при программировании фрезерной обработки цилиндрических и конических отверстий. Разработанное ПО CONICALINT является визуальным дополнением для разработанного технологического цикла фрезерной обработки отверстий, позволяющим генерировать управляющий G-код с набором из двенадцати аргументов.
Бесплатно
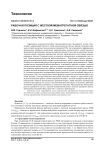
Рабочая позиция с жесткой межагрегатной связью
Статья научная
Современное конкурентоспособное машиностроительное предприятие должно обеспечивать оперативный переход с одной номенклатуры на другую. Данная тенденция отражена в стратегии научно-технологического развития РФ в части приоритета цифровизации производства. Наиболее ресурсоемка перекомпоновка автоматических линий массового производства, включающих множество рабочий позиций. Связь между агрегатами автоматических линий в массовом производстве жесткая, характеризуется отсутствием межоперационных заделов. Остановка одного из агрегатов автоматически останавливает всю линию. Оценка времени сохранения работоспособности - безотказности работы позиции с жесткой межагрегатной связью является комплексным и требует оценки многих факторов. В работе для проведения расчета была применена структурная схема надежности. Проведенный расчет показателей работоспособности и надежности рабочей позиции с жесткой межагрегатной связью позволяет получить показатели надежности для второго направления развития перекомпонуемых рабочих позиций с автоматической сменой узлов без нарушения жесткой межагрегатной связи базовых узлов. Отмечено, что при расчете можно не учитывать вероятность возникновения отказа агрегатных узлов по причине простоты их конструкции. При этом определение общей формулы вероятности безотказной работы рабочей позиции с жесткой межагрегатной связью позволяет перейти к определению вероятности безотказной работы элементов рабочей позиции с жесткой межагрегатной связью. Обеспечение гибкости автоматических производственных линий массового производства возможно при переходе от систем с жесткой межагрегатной связью к системам с рабочими позициями переменной компоновки со сменными модулями. Математическое обеспечение расчета надежности систем с жесткой межагрегатной связью позволит расширить область применения концепций «Индустрии 4.0» и «умного» производства.
Бесплатно
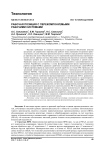
Рабочая позиция с перекомпонуемыми рабочими системами
Статья научная
Высокие требования по скорости переналадки и надежности обеспечения качества продукции для современного производства требуют новых принципов построения производственных систем. Высокая производительность и гибкость при различной номенклатуре производства может обеспечиваться за счет применения перекомпонуемых производственных систем. Данные системы объединяют преимущества агрегатных станков и обрабатывающих центров за счет конструктивных особенностей, описанных в данной статье. Приведены виды узлов и элементов системы в скомпанованном и дескомпанованном состоянии. Разработаны алгоритмы и схемы функционирования ярусов перекомпонуемых рабочих позиций (ПРП) в сравнении с рабочими позициями автоматических линий (РПАЛ). Сформулирована формула определения средней наработки до отказа ПРП. Проведена визуализация элемента системы и схема элемента системы - межмодульного элемента базирования (МУБК). Определены комплексные показатели эксплуатационной надежности ПРП одновременно по частным и комплексным показателям безотказности и ремонтопригодности с учетом особенностей функционирования и конструкции ПРП в сравнении с РПАЛ. Разработаны методики определения показателей безотказности и ремонтопригодности, учитывающие конструктивные и функциональные особенности ПРП в условиях многономенклатурного производства, основанные на значениях эксплуатационной надежности РПАЛ. Разработанные решения соответствуют направлениям развития современного машиностроительного производства и стратегии развития РФ. В условиях действующего машиностроительного предприятия точность оценки экономического эффекта требует применения робастных расчётных моделей, реализованных не только в виде алгоритмов, но и программ. В дальнейшем планируется разработать специальное программное обеспечение, позволяющее определить надежность перекомпонуемой рабочей позиции относительно позиции с жесткой межагрегатной связью.
Бесплатно
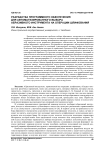
Статья научная
Рассмотрена практическая проблема выбора абразивного инструмента на операции шлифования, заключающаяся в сложности назначения многочисленных характеристик инструмента и высоком влиянии квалификации инженера-технолога. Предлагается решение этой проблемы путем разработки программного обеспечения для автоматизированного выбора абразивного инструмента. Для разработки программного обеспечения необходим алгоритм, базирующийся на некоторой существующей методике выбора инструмента. В качестве базы выбрана методика из справочника Уральского НИИ абразивов и шлифования, учитывающая основные физические взаимосвязи и закономерности процессов высокоскоростной обработки. По методике построен укрупненный алгоритм, состоящий из девяти блоков и включающий выбор всех основных параметров абразивного инструмента. Алгоритм реализован в инструментальной среде Microsoft Visual на объектно-ориентированном языке программирования C#, в результате чего получено программное обеспечение, включающее в себя набор справочных таблиц и аппарат выбора необходимых значений из этих таблиц. Показан пример функционирования приложения: на основе введенных исходных данных, демонстрирующих некую производственную ситуацию, программное обеспечение выбирает три подходящих маркировки шлифовальных кругов по мере их предпочтительности. Использование разработанного программного обеспечения показало, что время, затрачиваемое на выбор шлифовального круга, составляет 10-30 с, на качество выбора квалификация инженера-технолога не влияет. В связи с этим разработанный программный модуль позволяет решить поставленную задачу, повысить эффективность обработки шлифованием и сократить время технологической подготовки производства.
Бесплатно
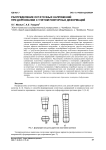
Распределение остаточных напряжений при дорновании с учетом повторных деформаций
Статья научная
В статье обоснована необходимость учета повторного деформирования при технологической операции дорнования или деформирующего протягивания, приведены экспериментальные распределения остаточных наряжений при дорновании. Представлено моделирование остаточных напряжений в полом толстостенном цилиндре при дорновании с учетом вторичных деформаций и повторного деформирования. Рассмотрены области, в которых прошли пластическое нагружение и упругая разгрузка, упругое нагружение и упругая разгрузка; приведены примеры моделирования окружных остаточных напряжений, т. е. результаты расчетного определения окружных остаточных напряжений в полом цилиндре по приведенным математическим моделям. Даны рекомендации по назначению количества дорнующих колец на дорнующем инструменте: их для формирования нужного распределения остаточных напряжений в приповерхностном слое достаточно двух, третье кольцо обеспечивает шероховатость. Рассмотрены особенности распределения окружных сжимающих остаточных напряжений в зонах вторичных и повторных деформаций; повторные деформации проявляются в приповерхностном слое, прилежащем к обработанной поверхности, т. е. остаточные напряжения от повторного деформирования накладываются на вторичные остаточные напряжения. Сформулированы подробные выводы по влиянию на остаточные напряжения в приповерхностном слое изменений давления (натяга) при дорновании, изменений толщины стенки цилиндра и изменений предела текучести обрабатываемого материала. Результаты моделирования не противоречат экспериментальным данным.
Бесплатно
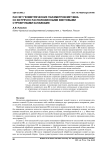
Расчет геометрических параметров метчика со встречно расположенными винтовыми стружечными канавками
Статья научная
С распространением изделий из волоконно-армированных композитов (ВК) в различных отраслях промышленности все актуальнее становится вопрос их эффективной сборки. Наиболее распространенные методы соединений деталей из ВК, к которым относятся склеивание, клепка и применение различных вставок, обладают рядом существенных недостатков, обуславливающих необходимость поиска новых более эффективных решений. Одним из наиболее перспективных методов сборки деталей из ВК является применение резьбовых соединений, которые получили широкое распространение в виде металлических и полимерных вставок. Однако ряд технологических ограничений, накладываемых на процесс установки данных вставок, вынуждает обратиться к резьбам, полученным в самих композитах. При этом получение резьб возможно как на этапе формовки неотвержденных изделий, что накладывает ограничения на их форму и размеры, так и методами лезвийной обработки, которые в настоящее время мало изучены. Процесс механической обработки заготовок из ВК значительно отличается от обработки гомогенных материалов. Специфические дефекты обработанных поверхностей, которые свойственны только ВК, обуславливают необходимость разработки специальных инструментов, учитывающих особенности различных видов композитов. Анализ результатов предварительных экспериментальных исследований по нарезанию резьб традиционными метчиками показал, что наибольшее влияние на качество нарезаемой резьбы в заготовках из ВК оказывают углы резания на вспомогательных режущих кромках, образованных боковыми сторонами профиля резьбы. Для обеспечения благоприятных условий резания на данных участках разработана конструкция специального метчика со встречными винтовыми стружечными канавками. Для данной конструкции подготовлена методика расчета углов резания на вспомогательных режущих кромках, позволяющая подготовить конструкцию данного метчика под обработку конкретного вида ВК за счет обеспечения оптимальных углов резания, взятых из литературных источников или полученных по итогам натурных экспериментов.
Бесплатно
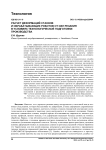
Статья научная
Расчет деформаций нежесткого технологического оборудования (специальных станков и обрабатывающих роботов) необходим для прогнозирования достижимости требуемой точности обработки. В настоящее время эта задача теоретически разрешима с применением численных методов расчета, в частности метода конечных элементов, для применения которого используются CAD-модели устройств. Такие расчеты требуют многомиллионных конечно-элементных сеток и выполняются, как правило, на суперкомпьютерах крупных компаний по производству данного оборудования. Применение этого подхода для решения этой же задачи в технологических службах машиностроительных предприятий вызывает как трудности вычислительного порядка, так и трудности с получением CAD-моделей данного оборудования, поскольку они являются технической тайной их производителей. Для преодоления этих трудностей предлагается подход, в основу которого положены три решения. Первое решение связано с отказом от использования полноценных твердотельных CAD-моделей оборудования. Вместо этого предлагается использовать STL-модели, в которых представлены лишь триангулированные поверхности сборок с перемещаемыми друг относительно друга узлами оборудования. Второе решение связано с использованием воксельного подхода и связанного с ним расчета кубических элементов конечно-элементных моделей. Третье решение связано с заменой реальных моделей деталей контактирующих пар приводов подач на их эквивалентные по жесткости модели эквивалентных деталей. Приведены примеры результатов перечисленных видов моделирования оборудования и расчеты его деформаций от сил резания. Показано, что такие расчеты доступны для современных персональных компьютеров технологических служб предприятий и не требуют раскрытия технических тайн производителей технологического оборудования. Данный подход имеет перспективы для использования в продвинутых CAM-системах расчета управляющих программ станков с ЧПУ с учетом влияния таких технологических факторов, как деформации оборудования.
Бесплатно
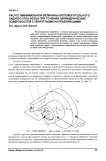
Статья научная
Рассматривается обработка точением внутренней цилиндрической поверхности детали с некруглой направляющей линией. Точение производится резцом, совершающим синхронные с вращением заготовки радиальные перемещения. Для исключения удара задней поверхности резца о заготовку необходимо обеспечить достаточную величину заднего угла. Статья посвящена расчету минимальной величины последнего на основе определения огибающей семейства линий - направляющих поверхности детали при ее движении относительно инструмента
Бесплатно
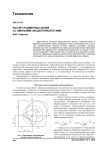
Расчет размерных цепей со звеньями-эксцентриситетами
Статья научная
Предлагается методика вероятностного расчета технологических и сборочных размерных цепей, содержащих звенья-эксцентриситеты, в качестве математических моделей которых приняты случайные векторы, имеющие круговое или сферическое нормальное распределение. Векторная размерная цепь приводится к линейной размерной цепи, в которую в качестве составляющего звена входит модуль вектора результирующего эксцентриситета. Приведены алгоритмы вычисления математического ожидания и дисперсии этого звена для различных условий обработки и сборки.
Бесплатно
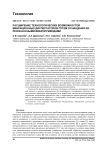
Статья научная
Рассмотрены проблемы, возникающие при производстве порошков, волокон и гранулоподобной стружки из вязких и хрупких материалов, применяемых в различных отраслях. Особенность данной проблемы заключается в обеспечении жестких требований к размерам, отклонениям размеров и формы дисперсных частиц, которые не могут быть получены при использовании традиционных устаревших технологиях переработки материалов. Обосновано применение нового способа возбуждения резонансных колебаний в виброприводах, обеспечивающего улучшение технологических параметров вибрационных станков-диспергаторов. Новизна способа состоит в получении синхронных колебаний в технологической системе и поддержании их на заданном уровне, а также в обеспечении возможности управления формой генерируемых колебаний. Предлагаемый способ позволяет повысить мощность, универсальность и эффективность работы виброприводов за счет обеспечения возможности управления формой траектории колебаний рабочего органа и одновременной синхронизации высокочастотной и низкочастотной составляющих колебаний. Показано, что функциональные возможности виброприводов могут быть расширены за счет возбуждения механических колебаний на резонансных частотах. Для более полного и наглядного представления процесса возбуждения резонансных колебаний средствами суперкомпьютерных ресурсов ЮУрГУ были выполнены расчёты частотных характеристик колебаний роторов вибропривода. Для сравнения траекторий и форм колебаний были представлены векторные диаграммы движения радиус-векторов суммарных амплитуд колебаний при несинхронном и синхронном режимах работы. В результате расчётов были выявлены три формы собственных резонансных колебаний каждого из роторов вибропривода. Для мониторинга и поддержания требуемых технологических параметров вибропривода была разработана система автоматизированного управления, позволяющая производить сбор у виброприводов параметрической информации, ее автоматическую обработку и поднастройку устойчивой синхронной работы посредством электрической обратной связи.
Бесплатно
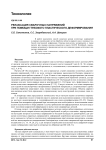
Релаксация сварочных напряжений при помощи глубокого пластического деформирования
Статья научная
В работе рассмотрен способ снижения уровня остаточных напряжений в сварных конструкциях путем обработки области сварного шва с помощью глубокой пластической деформации. Описаны результаты эксперимента, а также расчета при помощи конечно-элементного пакета ANSYS Workbench, показывающие возможность применения метода для снижения уровня остаточных сварочных напряжений.
Бесплатно
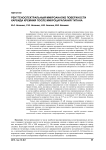
Рентгеноспектральный микроанализ поверхности карбида кремния после микроцарапания титана
Статья научная
Рассмотрена структура поверхности карбида кремния непосредственно после микроцарапания титана и после удаления налипшего металла травлением в растворе плавиковой кислоты. Исследования проведены на электронном микроскопе Versa 3D. Морфологию поверхности изучали при увеличении от 800 до 20000×. Химический состав определяли методом локального микрорентгеноспектрального анализа при съемке в отдельных точках и сканировании участков поверхности. Ускоряющее напряжение электронов возбуждения изменяли от 5 до 20 кВ. В нанослоях карбида кремния микрорентгеноспектральный анализ показал наличие пяти элементов: углерод, кремний, титан, азот и кислород. При 5 кВ, когда глубина зоны генерации рентгеновского характеристического излучения не превышает 270-320 нм, на участках поверхности карбида кремния без видимых следов налипшего металла концентрация титана достигает 3 % атом. Соотношение между атомами кремния и углерода свидетельствует о наличии избыточных атомов углерода. С увеличением ускоряющего напряжения до 15 кВ глубина слоя генерации рентгеновского характеристического излучения атомов титана может достигать 2000 нм. Поэтому с ростом U концентрация титана снижается, поскольку такое же количество титана, сконцентрированного в приповерхностном слое, теперь усредняется по значительно большему объему. При U = 15 кВ концентрация титана на нетравленой и травленной поверхностях составила соответственно 0,56 и 0,36 % атом. До травления количество атомов углерода в 1,7 раза больше чем атомов кремния. Наличие избыточного углерода объясняется присутствием достаточно большого количество углерода на поверхности материла. После травления, в результате снижения содержания атомов титана, кислорода и азота, общей тенденции к снижению атомов углерода концентрация атом кремния с(Si) увеличивается. В результате количественное соотношение между атомами углерода и кремния снижается до 1,4. Увеличение ускоряющего напряжения означает и увеличение объема основного материала, т. е. карбида кремния, находящегося в зоне генерации. С ростом U концентрация титана, азота, кислорода снижается, так как эти элементы находятся в основном на поверхности карбида кремния. Содержание атомов кремния и углерода, входящих в состав карбида кремния, будет возрастать практически пропорционально объему генерации. Поэтому с ростом U концентрация кремния должна увеличиваться, а углерода - снижаться. В действительности с увеличением U в диапазоне 5-15 кВ с(Si) на нетравленой поверхности возрастает более чем на 25 % и на 10 % после травления. Концентрация углерода имеет тенденцию к снижению. Только при ускоряющем напряжении 20 кВ атомные концентрации углерода и азота с учетом доверительного интервала на средние арифметические значения можно считать приблизительно одинаковыми. В данных интервалах U концентрация углерода снижается значимо, что подтверждает ранее высказанное предположение о тенденции снижения с(C) с увеличением U.
Бесплатно