Aviation and spacecraft engineering. Рубрика в журнале - Siberian Aerospace Journal
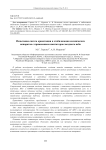
Testing of spacecraft orientation and stabilization systems using starry sky simulators
Статья научная
The paper investigates the need to create a method of simulating the starry sky for testing spacecraft and conducting tests of orientation and stabilization systems in laboratory conditions. Modern space exploration and, as a consequence, the complexity of technical requirements for flight support facilities are constantly increasing, respectively, the requirements for ensuring the accuracy of determining the position and orientation of the spacecraft are increasing. The history of the development of astroorientation devices and, in particular, stellar sensors is given. The modern stage of development of stellar sensors came with the advent of matrix radiation receivers: charged coupled device (CCD) and complementary metal-oxide semiconductor (CMOS) video matrices. Such stellar sensors are no longer tied to individual, predefined stars, but determine their orientation from images of groups of stars visible in the field of view of the device. Examples are given for their field of application, namely, determining the orientation of the sensor, pointing some device mounted on a spacecraft, and others. Modern requirements for astrogation are given. The basic principles of ground-based testing of the spacecraft orientation and stabilization system using starry sky simulators are considered. This is a stage of development and autonomous tests on a hardware and software stand of semi-natural modeling. To date, the ISS JSC enterprise has a complex modeling stand for conducting these types of spacecraft tests, using methods of both mathematical and semi-natural modeling, which includes various simulators of the starry sky. The development of these simulators has a long history, a comparative table of previously used simulators is given. The structures of both past and modern simulators of the starry sky are shown. The conclusions state the need to create a method that will simulate the rotation of the spacecraft at speeds up to 15–30 °/s. This method will allow testing the orientation and stabilization system of modern spacecraft.
Бесплатно
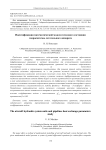
The aircraft hydraulic system units and pipelines heat exchange parameters study
Статья научная
The paper offers a method of mathematical modelling of aircraft hydraulic system thermal state. The given mathematical model presents a system of partial differential equations for carbon-fiber composite thermal insulation together with ordinary differential equations for hydraulic system components that describe their heat exchange with the ambient air and close-located surfaces. To solve the direct thermal state problem for hydraulic system components, i. e., to solve a stiff ordinary differential equation system, a Rosenbrock-type second order approximation numerical scheme for non-autonomous systems was applied. A solution of a partial differential equation system in Monte-Carlo method based on a probabilistic representation of the solution as a functional expectation of the diffusion process was also used. The inverse problem of the hydraulic system elements’ thermal state was solved applying a composition of the steepest descent method, Newton method and quasi-Newton method of Broydon-Fletcher-Goldfarb-Shanno. A mathematical model of the thermal state of a hydraulic system unit operating in an unpressurized aircraft compartment has been also developed, and the confidence intervals of each of the required model coefficients have been estimated using 2 1 α χ distribution at confidence probability = 0.95.
Бесплатно
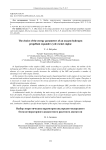
The choice of the energy parameters of an oxygen-hydrogen propellant expander cycle rocket engine
Статья научная
In liquid-propellant rocket engines (LRE), made according to a gas-free scheme, the turbine of the turbopump unit (TPU) is driven by heated fuel in the coolant system of the combustion chamber (CC). The absence of a gas generator greatly increases the reliability of the LRE and provides a number of advantages over other engine schemes. At the moment, the existing oxygen-hydrogen gasless liquid-propellant rocket engines do not meet mod-ern tactical and technical requirements for the level of thrust and pressure in the (CC) engine. Therefore, it is necessary to study ways to increase the energy parameters of the liquid-propellant rocket engine and identify promising engine schemes. This article proposes schematic solutions for an oxygen-hydrogen LRE, provides an analysis of the influence of various factors on the power parameters of the engine, as well as recommendations for the design of gasless LRE. A mathematical model for calculating the main energy and geometric parameters of the engine has been developed. Prospective pneumohydraulic schemes of an oxygen-hydrogen gasless liquid-propellant rocket engine are proposed, depending on the tactical and technical requirements.
Бесплатно
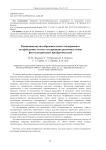
Статья научная
The article proposes the concept of an experiment for conducting flight testing of various samples of photo voltaic converters. The purpose of the experiment is to study the behavior of new types of solar cells in outer space. The research will be carried out by testing samples on board the spacecraft. The experiment will be carried out by a device that collects data on the electrical properties of solar cells. The information re-ceived will be presented in the form of a voltage characteristic. During the experiment, its dependence on external parameters will also be studied. In particular, the correlation of the current-voltage characteristic from the values of temperature and illumination of solar cells will be investigated. Based on the data ob-tained, the efficiency of photo voltaic converters will be determined. Their degradation as a result of expo-sure to cosmic ionizing radiation will also be studied. The authors are tasked with designing and develop-ing an experimental installation that will be a payload module of a small CubeSat-class spacecraft. Based on the results of the work, the appearance of the flight testing experiment was developed, the re-quirements for the payload module were determined and a project for its creation was proposed. At this stage, the circuit design and software implementation of the module itself are under development. In the course of the work, the main requirements that this module provides to the main systems of the spacecraft were also formulated. To carry out the mission of the experiment, it is planned to integrate the payload module on the plat-form of the ReshUCube-2 form factor 3U. This satellite will be equipped with equipment enabling techno-logical experiments.
Бесплатно
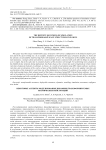
The definite questions of simulation of transformable space structures dynamics
Статья научная
This paper describes large transformable space structures with various configuration in the folded transport position and in the open working one. As an example, simulation of transformable space structures dynamics is shown for the antenna circuit foldable load-bearing frame with diameter of 5 m. For investigation of the foldable frame deployment dynamics, a design scheme presented by a system of rigid bodies connected with each other by hinges is accepted as it is simple, but at the same time it considers features of the structure well enough. For performing stress analysis of the foldable frame elements during deployment, the frame shape at the certain time point of deployment, when relative velocities of adjacent elements are ultimate, is chosen. As a results of calculation using MSC.Adams software, positions, velocities and accelerations of the centres of mass of the foldable frame elements as well as the angular velocities and accelerations of the elements for each time step of the deployment are obtained. To perform stress analysis of the foldable load-bearing frame, finite element model of the frame is developed using MSC.Patran/Nastran software. As a results of investigation of stressed and deformed states of antenna circuit foldable frame elements both without taking into account damping and with consideration of damping, stresses arising in the foldable frame elements at the certain time points during deployment are found.
Бесплатно
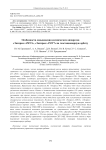
The feature of raising the “Express-AMU3” and “Express-AMU7” satellites into geostationary orbit
Статья научная
At present, in order to increase the launch mass, raising satellites into geostationary orbit by their own propulsion subsystem is widely used. Oly the JSC “Academician M. F. Reshetnev “Information Satellite Systems” applied such a scheme for several satellites of their own design - "Express-AM5", "Express-AM6", "Express-80" and "Express-103". Along with this, some diversity of approaches to the implementa-tion of this operation can be noted. In particular, the orbit raising of the above satellites was carried out using the onboard propulsion subsystem based on SPT-100 plasma thrusters. The operation was carried out by one or two thrusters. The use of two thrusters of the "Express-80" and"Express-103" satellites was due to the desire to keep within a reasonable amount of no more than six months with a significant increase in the output mass. Nevertheless, the duration of the orbit raising of about 150 days, which took place dur-ing the raising of satellite data, is also excessively long. It is evidemnt that it can be reduced, other things being equal, only by increasing the available thrust of the thrusters. This can be achieved both by increas-ing the thrust of individual units, and by increasing the number of simultaneously used thrusters. Therefore, for the new Express-AMU3 and Express-AMU7 satellites (with dimensions similar to the Express-80 and Express-103 satellites), for which a paired launch was also assumed, both of these methods were used. For orbit raising, two SPT-100V thrusters and, additionally, an SPT-140D type thruster were used. The total thrust of a cluster of thrusters made it possible to count on a significant reduction in the duration of orbit raising in comparison with the Express-80 and Express-103 satellites. The SPT-140 thruster developed by JSC "Experimental Design Bureau FAKEL" was used in Russia for the first time. For its power supply, the CCS-140D control and conversion device was specially created at the JSC "Design Bureau Polyus". The use of a combination of three thrusters made it possible to significantly reduce the duration of the opera-tion of raising into geostationary orbit.
Бесплатно
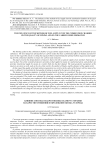
Статья научная
The burning of fuel in the combustion chamber of a gas turbine engine (GTE) is accompanied by formation of toxic substances. The most dangerous among them are carbon oxides that have a detrimental effect on humans and environment. In this regard the article is solving the urgent problem of determining the optimal method of gaseous fuel supplying in GTE combustion chamber to ensure low carbon-oxide emissions. The paper presents the design features of injectors that work with a separate supply of air and fuel. Natural gas is used as fuel. One of the considered injectors provides jet fuel supply by means of a perforated spray, and another one provides twisted fuel supply by means of a swirler built into the fuel channel. The main geometric parameters of the injectors are given as well, such as the size of the swirler, the number of blades, and the diameter of the output nozzle. In this regard the quality of air-fuel mixture preparation in a swirl jet in the outlet of the burner with two types of injector is defined. It is found that the best quality of mixing is ensured by the injector with jet spray. The design of a heat pipe simulator, in which the tested nozzle is placed, is considered. The design of a stand installation designed for testing injectors in a heat pipe simulator, as well as the modes under which these tests were carried out, are presented. The results were obtained in a heat pipe simulator with installed jet injectors and injectors with a swirling fuel jet. An analysis was conducted, which resulted in conclusions about the effectiveness of using jet injectors. According to the conducted research, the parameters of the injector with a swirling fuel jet are characterized by the presence of high values of CO levels in the combustion products, which is explained by the extremely low quality of mixing fuel with air and, consequently, low efficiency of fuel combustion. Jet fuel injection has low CO values, which indicates good quality of mixing fuel with air and high efficiency of a combustion process. As a result, we have received recommendations on setting the selected type of injectors in a full-size combustion chamber.
Бесплатно
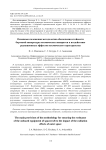
Статья научная
In this paper, the issues of ensuring the resistance of the onboard equipment of spacecraft to the effects of ionizing radiation from outer space, which significantly limits the period of active existence of the space-craft, are considered. The paper describes the methodology for ensuring radiation resistance, developed by the specialists of JSC “ISS”. The result of the work done is to ensure the guaranteed performance of the target function by spacecraft with long period of active lifetime of 15 or more years. Among the outer space factors affecting the spacecraft, ionizing radiation of outer space is the main factor limiting the period of active existence. Exposure to energetic particles of ionizing radiation from outer space causes degradation of the electronic component base, which leads to failures and malfunctions of on-board equipment and degradation of its functional surfaces. Ensuring the radiation resistance of a spacecraft (SC) is a complex task, one of the stages of which is to determine the radiation resistance of components that complete the on-board equipment. As a result of accumulated experience in conducting radiation tests and analysis of the results, specialists of JSC “ISS” developed a methodology that allows to guarantee the radiation resistance of the spacecraft under conditions of tight production deadlines and optimized costs.
Бесплатно
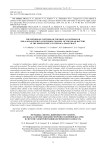
Статья научная
A method of synthesizing a digital controller for a solar energy conversion channel in a power supply system of a spacecraft is presented. The method is based on the initial functional diagram of the pulse converter and the method of switching discontinuous functions. In accordance with the technique, which is formally presented in the form of eight consecutively executed items, a block diagram of the shunt converter has been developed in the basis of switching functions, which is taken as an example for testing the technique. The shunt converter is one of the three energy conversion channels in modern power supply systems of a spacecraft. The block diagram showed that all nonlinearity of the system can be reduced to nonlinearities of two multiplication links and nonlinearity of a pulse-width modulator. The possibility and acceptability of joint linearization of each of the specified nonlinear multipliers with a pulse-width modulator at the selected operating point is shown. A linearized block diagram of the control object was obtained, after which the transformation and simplification of the block diagram to a convenient form for calculation was carried out. Using the transfer functions of the linearized block diagram, the logarithmic frequency characteristics were calculated analytically and the results of their comparison with the frequency characteristics obtained experimentally on a simulation model, which confirmed their identity in the working frequency domain, were presented. At the same time, the specified simulation model of a shunt pulse converter, built in the Simulink package of the Matlab design environment, took into account all the mentioned nonlinearities of the real converter. According to the obtained logarithmic characteristics, a classical synthesis of the analogue prototype correcting section was produced. The transition from the analog correcting section of the prototype to the implementation of the digital correcting section is shown. Simulation modeling of a closed-loop power supply system with a synthesized analog controller, in its mode of operation from a solar battery, confirmed the correctness of the methodology and the achievement of the goals. The results of the work are intended to create a new onboard energy conversion equipment for power supply systems of high-potential spacecrafts. The scope of application of the project results is space instrumentation.
Бесплатно
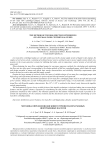
The method of the disk friction determining of low mass flow centrifugal pumps
Статья научная
Low mass flow centrifugal pumps are currently widely used in the energy supply system of liquid rocket engines, the engines of correction, docks, consisting of on-Board power sources on-Board sources power supply system of fuel components in the in gas generator systems for inflating fuel tanks, and in temperature control systems of aircraft and spacecraft. When designing low mass flow centrifugal pumps for aerospace purposes, methods for calculating and optimizing the flow rate are often used corresponding to the design methods of full-size centrifugal pumps, which limits the mode and design potential of pumps and affects their energy characteristics and reliability. Reliability requirements often lead to the need to reserve units and fuel-supply systems. Despite the large amount of research works, the issues of reliable design of low mass flow centrifugal pumps with high energy and operational parameters for spacecraft and aircraft remains an urgent task. The article analyses the operational parameters of low mass flow centrifugal pumps used in aircraft and spacecraft power systems. Taking into account working fluid used and the temperature range, it was found that a laminar rotational flow with Reynolds number characteristic Re 103 3105 is realized in the lateral cavity between the impeller and the pump housing. The determination of power losses on disk friction of the impeller technique is developed taking into account design features and the applied schemes. Equations for determining the disk friction coefficients are consistent with the dependencies obtained by other authors. The obtained equations for the laminar rotational flow made it possible to determine the dependences for the resistance moment and the disk friction power of the impeller determining of a low mass flow centrifugal pump.
Бесплатно
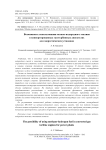
The possibility of using methane-hydrogen fuel in converted gas turbine engines for power plants
Статья научная
Taking into account the fact that recently the topic of using methane-hydrogen mixtures as a fuel for gas turbine engines used in power plants has been actively developed, it is necessary to have engineering methods for calculating the fuel system and combustion chamber of engines operating on such fuel. The paper proposes the methodology that allows performing such calculations. A gas turbine unit (GTU) based on a converted aircraft engine NK-16ST was taken for the calculation. The calculation according to this method is carried out in three stages. At the first stage the composition is selected and the thermophysical characteristics of the gas under consideration are determined. At the second stage the fuel system is calculated, the consumption characteristics of the engine fuel system and the combustion chamber system are built. The consumption characteristics built for natural gas and for methane-hydrogen mixture are compared. The analysis makes it possible to develop recommendations for optimizing the design of the fuel supply equipment and fuel nozzles in terms of changing the volume of internal channels. At the third stage the combustion chamber is calculated and recommendations about the need to change the flame tube head or redistribute air along the flame tube length are made. The volumetric heat intensity parameter is used to estimate the sufficiency of the available volume of the flame tube for operation on methane-hydrogen mixture and to determine the gas average temperature in the combustion zone of the combustion chamber. The possibility of operation of the NK-16ST gas turbine unit on a methane-hydrogen mixture was confirmed on the basis of the results of the work performed. It was also concluded that in order to supply large volumes of methane-hydrogen mixture in comparison with natural gas, it is required to increase the size of fuel pipelines, metering and control units and fuel nozzles.
Бесплатно
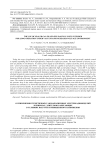
Статья научная
Today, the scope of application of electric propulsion systems for orbit correction and spacecraft’s attitude control is rapidly expanding due to their high efficiency compared to liquid jet systems. The main elements of electric jet systems are plasma or ion thrusters. To ensure power supply of such thrusters, complex electronic power processing systems – power processing units (PPU) – are used. These units are capable to operate for a long time (up to 15 years or more) in a high vacuum environment and generate sufficiently high accelerating voltages – from 300 V and higher. PPU’s comprise various EEE-parts, mainly in the case design. As a rule, the technology of their production is such that air or nitrogen is initially located inside the housing at atmospheric pressure. During the operation of the unit, the non-absolute hermeticity causes pressure decrease inside EEE housings. Due to high voltages applied, this can lead to electrical breakdowns between current-carrying ele-ments inside the parts, their failure with the subsequent failure of the functional blocks of the unit. The paper considers the physical principles of the breakdown occurrence inside EEE-parts cases. The results of non-hermiticity measurements of several types of HV EEE-parts are presented. The dynamics of the pressure drop to the values dangerous from the point of view of breakdown event and the relevant occurrence duration are esti-mated. It is shown that duration of being exposed to the pressure-dangerous conditions can be as long as space-craft service lifetime. It can make difficult to use packaged gas-filled EEE-parts at the level of units intended to operate in non-pressurized compartments of spacecraft. Recommendations are provided for selecting the design of EEE parts with an operating voltage of about 300 V or more, as well as circuit solutions used to develop high-voltage equipment intended to operate in vacuum environment.
Бесплатно
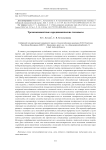
Three-component aerodynamic load cells
Статья научная
The article examines the effect of flow on models studied in wind tunnels. To determine the force effect of the flow on the model under study, a more accurate and reliable method of directly measuring forces and moments using aerodynamic strain gauge balances is proposed. When solving a plane problem for a symmetrical model at zero slip angle, a design of three-component scales is proposed that measures the lift force, the drag force and the pitching moment. To eliminate the interaction between the supporting devices and the model, which causes disturbances in the flow near the model, the scales are located outside the model and the working part of the wind tunnel. The components of the aerodynamic force and moment acting on the model are measured using resistance strain gauges, which convert the deformation of the elastic element into a change in electrical resistance, which is measured by an instrument connected to an appropriate measuring circuit. The choice of strain gauges as weight elements is due to their very small size and weight, the ability to measure very small relative deformations of elastic elements, low inertia, which makes it possible to measure not only static but also dynamic loads, and the possibility of remote measurements. To compensate for the influence of various sources of errors, increase sensitivity and ensure greater measurement accuracy, the strain gauges are connected via a bridge circuit and included in all four arms of the bridge. Deformation of the horizontal measuring beam causes a change in resistance not only in the strain gauges that measure the pitching moment, but also in the strain gauges designed to measure the lift force. Since the design of the scales does not allow for electrical separation of these components, the influence of the pitching moment on the magnitude of the lift force is determined during the calibration process and is assessed using a special influence graph constructed from the results of calibration data. In strain gauge measurements, the output values of forces and moments acting on the model under test are obtained in the form of corresponding readings from a device that measures electrical signals proportional to the applied forces. To convert instrument data into values of forces and moments, a joint calibration of scales and instruments is carried out in order to obtain calibration coefficients. Additional components of aerodynamic forces and moments created by the holder are determined by purging it in the presence of the model. Calculated dependencies for determining the components of the aerodynamic impact are given. The values of the coefficients of aerodynamic forces and moments are given in the flow coordinate system. The pledge has been given.
Бесплатно
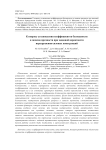
Статья научная
Ensuring high reliability of unique high-critical products at the design stage is an actual task that the aerospace industry faces. For high reliability indicators, at the design stage, it is necessary to ensure the basic property of the product – its strength, with a high probability of non-destruction. It is provided by introducing the corresponding coefficients – «safety coefficient» and «margin of safety» into the strength calculations. The necessity in these coefficients is based on the spread of values of external loading factors: magnitude of forces, combination of forces, kind of actions, place of connection, etc. In this case, the safety coefficient is related to external factors. The margin of safety refers to internal factors: the spread of the mechanical characteristics of the product material, the spread of the geometric dimensions of the product, etc. To determine, with a given probability, the safety coefficient and margin of safety, it is necessary to know their dependence on the combination of spread of external and internal factors. The purpose of this work is to determine the mathematical connection between the internal factors of the spread and the safety coefficient, external factors of the spread and the margin of safety, the combination of these factors and the probability of non-destruction of structures. In this work the values of internal and external factors, which affect the strength and probability of non-destruction of the product and have the boundaries of the spread of their values, using the tools of probability theories, were characterized as random variables, the values of which are determined by the distribution density, expected value and variance. I this work there was found a high dependence of the product strength on the spread of its geometric characteristics and tools were defined to determine the total spread of the values of the main strength characteristics of the product with a given probability of non-destruction. The practical significance of the results of this work can be achieved in the aerospace industry, in particular, at the design stage of unique high-critical products.
Бесплатно
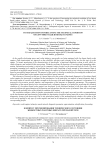
To the question of forecasting the technical condition of low-thrust liquid rocket engines
Статья научная
In the rapidly developing space and rocket industry, spacecrafts are being equipped with low-thrust liquid rocket engines. Нigh requirements are imposed on the reliability, efficiency and economy of fuel use for this type of rocket engine. To ensure monitoring of the characteristics of spacecrafts, a functional diagnostic system is used, which includes telemetry and analytical data processing. Telemetry performs the functions of receiving and transmitting information. Information processing is carried out in computer centers located on the spacecraft and the Earth. The most promising computing tool capable of predicting time series and classifying a large amount of interconnected data is considered an artificial neural network. In this regard, the subject of research in the work is data processing methods based on an artificial neural network. The purpose of the work is to develop a method for forecasting the technical condition of low-thrust liquid rocket engines using an artificial neural network. The relevance of research on the use of a neural network in the system of functional diagnostics of low-thrust liquid rocket engines for spacecraft is explained in the introduction. In the main part, an analysis of many telemetric data of the rocket engine is carried out and their strength in the forecast of the main diagnostic parameters is determined. It is proposed to use traction, specific impulse, and temperature of the structure as diagnostic parameters. The prognostic capabilities of the neural network were investigated and a schematic diagram of a method for predicting the technical condition of a low-thrust liquid rocket engine was developed. In the developed method, at the first stage, the neural network performs the approximation of the function and extrapolates the time series of telemetric data; the second stage determines the probable class of the technical condition of the engine. The conclusion outlines a plan for further experimental research in the study area and provides recommendations on the development and improvement of algorithms for functioning of artificial neural networks as part of the functional diagnostics system of the spacecraft. Due to the generalized nature of the methodological schemes, the results of the work can be applied to any type of rocket engines and used at all enterprises of the rocket and space industry of the corresponding profile.
Бесплатно
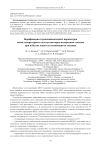
Статья научная
Liquid gas generators (LGG) are additional firing units in the power system of liquid rocket engines (LPRE). The LGG ensure the operation of the power units of the turbopump unit (TPU) of the engine by feeding combustion products (CP) to the turbine drive. The main criteria for the efficiency of the generator gas is the complex (RT)gg and the thermodynamic properties of the mixture, depending on temperature, pressure, the degree of excess of the oxidizer and the enthalpy of the fuel, attributed to the conditions of supply to the nozzles of the GG. Changing the parameters of the generator gas leads to a change in the turbine power parameters due to its effect on the adiabatic operation of the Lad turbine. Depending on the engine circuit under consideration, CP GG can perform work in other units and elements of the engine, as well as influence many parameters of the LPRE. Among the main ones can be noted: the power of the booster gas turbine of the booster turbopump unit (BTPU) in the case of the selection of the generator gas after the GG or turbogas after the main turbine; the temperature of heating the refrigerant in the heat exchanger introduced in the GG; specific impulse of a liquid rocket propulsion system (LRPS), depending on the quantity and properties of the turbogas entering the exhaust pipe of the engine (for the engine circuit without afterburning the generator gas); mixing in the combustion chamber (CC) due to afterburning of turbogas entering the engine chamber after the turbine (for the engine circuit with afterburning of generator gas); parameters of the firing wall of the engine in the case of using a high-temperature gas curtain by blowing generator gas into the supersonic part of the nozzle. For many pairs of fuel during combustion in GG, the nonequilibrium of combustion products is characteristic (especially in hydrocarbon fuels).Due to the fact that the combustion products (CP) during the combustion of an oxygen-hydrogen mixture, due to the simplicity of the reaction, have time to form while staying in the GG (i.e., the time of chemical equilibrium of the CP is less than or equal to the time of stay in the GG), their thermodynamic parameters can be reliably determined using programs that simulate chemical equilibrium reactions. In this article, the issue of obtaining reliable results of thermodynamic calculations of generator gas at low and high coefficients of oxidant excess is investigated. Verification of parameters obtained in the programs “Astra” and “Rocket Propulsion Analysis” with calculated values was carried out. The most suitable program for performing engineering calculations and modeling the thermodynamics of liquid gas generators has been determined.
Бесплатно
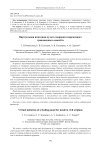
Virtual imitation of a fueling panel for modern civil airplane
Статья научная
The article considers the design and development of a computer model of the fueling monitoring and control panel of the Sukhoi SuperJet 100 civil aircraft. The presented model is included in a simulator program for training technical specialists in aircraft maintenance skills under conditions of limited access to real or hardware-simulated equipment. In the process of designing of the presented simulation model, the refueling panel and the SSJ-100 aircraft refueling system sufficient components were considered and selected for further software implementation. The selection of the necessary components for the model was carried out using the decomposition method of the real system. First, the functional elements of the refueling panel itself were selected, after which the refueling system was disassembled into components that allow simulating the operation of the simulated panel. To implement the simulation model, software classes of objects and interactions between them were described. Software algorithms are implemented in the Unity environment using the C# language. The created program uses a three-dimensional graphic component and compiled for launching on a web browser. Software components have also been developed that allow studying the functions of the fueling panel both independently and in the mode of control of knowledge of the elements and algorithms for working with the fueling panel. The developed model is used as part of a practical simulator at the Reshetnev Siberian State University, and can be functionally expanded in the future.
Бесплатно
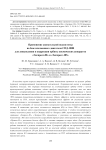
Статья научная
Recently, there has been an increase of interest in satellite orbit raising using electric propulsion subsys-tems. Theoretic analyses and practical experience demonstrate that while orbit raising to the geostationary orbit (GEO) via a transfer orbit is feasible, it requires a certain amount of time due to the thrust of onboard electric thrusters being low (40-300 mN) and thus incomparable with that of propulsion systems of liquid propellant thrusters (22-400 N). Due to low thrust, orbit raising by electric thrusters is time-consuming. However, the associated increase in mass to GEO may counterbalance the long duration of satellite commis-sioning. Calculations demonstrate a potential added satellite mass on GEO of up to several hundred kilo-grams with orbit raising duration of about 6 months. In particular, with satellite mass not exceeding 2500 kg, coupled launch is possible using existing launch vehicles. ISS took into consideration the positive results ob-tained with Express-AM5, and Express-AM6 satellites to design the Express-80 and Express-103 with orbit raising in mind. Such approach allowed for a coupled launch on the Proton-M carrier rocked with a Breeze-M upper stage, and a twofold launch cost saving. To increase thrust during orbit raising and decrease its du-ration, coupled thruster operation in high thrust mode was implemented. The resulting total mass on GEO increase constituted over 700 kilograms with maneuver duration of up to 158 days. This allows performing coupled launches of heavier satellites with orbit raising by means of electric propulsion in a feasible timeframe.
Бесплатно