Manufacturing technology for building materials and products. Рубрика в журнале - Nanotechnologies in Construction: A Scientific Internet-Journal
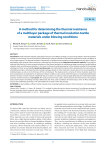
Статья научная
Introduction. Textile industrial materials, particularly in the form of multilayer packages, are extensively utilized as thermal insulation coatings in construction. One of the functional characteristics of these materials is their effective performance under conditions of strong wind exposure. The thermal insulation characteristics of textile thermal insulation materials depend on the value of their air permeability, while minimal thermal resistance is observed from the blowing side. Materials and research methods. The article lists methods that allow for the most accurate calculation of the thermal resistance of multilayer packages consisting of textile building materials under wind-blowing conditions. In this case, the thermal-insulating properties of the materials included in the package will depend on their air permeability. Results and discussion. Our mathematical model used for calculating the thermal resistances of building envelopes, containing thermal insulation packages based on textile materials, includes data on the air permeability of individual layers, as well as on the thickness of their air interlayers. The study presents a scheme of thermal insulation layers that shows temperature curves plotted on it. Stationary medium conditions were used as initial information on temperature distribution between the layers. Further research established that an increase in air velocity of the package affected by the wind influenced the reduction of thermal resistance. Conclusion. The study presents formulas used in determining the thermal resistance of insulating layers and interlayers of building envelopes affected by the wind, under conditions of frontal impact of the air flow, taking into account the established parameters of air permeability of the layers within the package.
Бесплатно
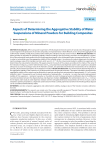
Статья научная
Introduction. When using water suspensions of finely dispersed mineral systems of natural and anthropogenic origins as active agents in the production of concrete composites, an important factor in their effective use is to ensure the aggregative and sedimentation stability of solid phase particles before adding the solid phase into the reaction mixture. Methods and materials. The paper provides an algorithm for quantifying stability criteria according to the DLVO theory provisions as exemplified by a suspension of fine polymineral sand powder from the Kholmogorskoye deposit in the Arkhangelsk region (average particle size is 195 nm). In order to successfully assess the aggregative stability of this colloidal system, it is necessary to conduct experiments for determining the analogue value of the Hamaker constant, which was 0.5 •10–20 J for the mineral sand studied, in addition to experiments for determining the zeta potential of particles. This paper presents the results of the analysis according to the criteria of the value of the interaction energy (Uint) and the sedimentation rate (Vsed) of a polymineral sand dispersed system (water suspension) calculated taking into account the analogue value of the Hamaker constant, zeta potential and dimensional characteristics of its solid phase particles, physicochemical properties of the dispersion medium. Results and discussion. It is shown that the determining factor of the aggregative stability of the suspension is the electrostatic barrier for particle interaction. Theoretical calculation showed that the aggregative stability of the system may be affected by its particles reaching their zeta potential of approximately 10–4 mV (a nearly isoelectric state). It is proposed to use the kinetic parameter of sedimentation – its velocity – to assess the kinetic (sedimentation) stability of this suspension – resistance to gravity, i.e. the ability to resist the dispersed system stratification due to the difference in particle densities between the dispersed phase and dispersion medium. Conclusion. The sedimentation rate is Vsed ≈ 4 nm/sec for the object under study in water dispersion medium with the averaged dimensional characteristics of 195 nm. At such a rate of solid phase particle precipitation, a dispersed system based on finely crushed polymineral sand from the Kholmogorskoye deposit can be considered sedimentatively stable.
Бесплатно
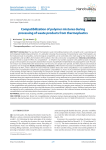
Compatibilization of polymer mixtures during processing of waste products from thermoplastics
Статья научная
Introduction. The recycling of thermoplastic waste into building materials with a long-life cycle is a promising and technologically feasible disposal direction. It is advisable to develop the processing of mixed polymer waste. Thermoplastics are thermodynamically incompatible, and technological compatibility can be controlled at the melt stage by the introduction of compatibilizers and nanofillers, the formation of free radicals in the melt, and reaction compatibilization. Materials and methods. The work aimed to study the effect of a compatibilizer – an ethylene-vinyl acetate copolymer with grafted acrylate and epoxy groups on the properties of composites obtained from mixtures of polyethylene terephthalate and polypropylene waste. The polymer mixture was melted, filled with limestone flour (50–85 wt.%), the samples were pressed, and their physical and mechanical properties were investigated. Results and discussion, conclusions. Differential thermal analysis established the melt preparation temperature of 240оC, which is below the onset of thermal oxidative destruction of the compatibilizer. It was established that the optimal ratio of polyethylene terephthalate: polypropylene: compatibilizer as 70:25:5 wt.% provided the greatest improvement in the bending strength without compromising the compressive strength of filled composites; the optimal degree of filling was found to be 60–70%. The volume fractions of polymers in the mixture are comparable. Therefore, one can expect the formation of both the matrix structure of the composite and the interpenetrating networks type structures. In both cases, the compatibilizer is distributed along the interphase boundaries. Its effect on properties can be attributed to its plastic deformation in the interfacial layer and morphological changes in the structure of the polymer mixture. There is evidence of increased structure-sensitive properties, tensile and tensile strength, of polymer mixtures containing this compatibilizer. This fact indicates an increase in adhesion between polymer phases, which is difficult to explain only for physical reasons. Possible reactions between the functional groups of the compatibilizer and polyethylene terephthalate in the melt with epoxy ring opening were analyzed. An increased effect of compatibility was revealed; however, the actual effectiveness of the compatibilizer is difficult to assess. Additional mechanical tests are required as well as optimization of the melt temperature. It is also necessary to find a balance between activating the reaction compatibilization and minimizing destructive processes in polymers.
Бесплатно
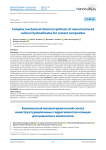
Complex mechanical-thermal synthesis of nanostructured calcium hydrosilicates for cement composites
Статья научная
Introduction. The use of nanosized calcium hydrosilicates as additives accelerating the structure formation of cement compositions is becoming increasingly popular. The reason for this lies in their high efficiency as accelerators in the absence of a negative effect on the long-term strength and durability of cement composites. An additional advantage of nanoscale calcium hydrosilicates is the variety of existing methods for their synthesis, among which the mechanochemical method stands out due to the availability of raw materials and the simplicity of the technical design of the synthesis. Article body. The review considers a new method for the synthesis of nanostructured calcium hydrosilicates – complex mechanical-thermal synthesis, which is a combination of mechanochemical synthesis of carbohydrate-modified calcium hydrosilicates with their subsequent thermal decomposition. Modified calcium hydrosilicates , in the interlayer space of which the carbohydrate is intercalated , are capable of decomposition under conditions of low-temperature thermolysis (<150 oC ) with the formation of hydrosilicate nanoparticles, the coagulation of which leads to the formation of a nanostructured phase of calcium hydrosilicates – xerogel. A mixture of xerogel with residues of raw materials, hydrated phases that have not decomposed during thermolysis is a calcium silicate dispersion (CSD). The technological features of CSD synthesis and some properties of CSD are described. In particular, a moderate (up to 60%) acceleration of daily strength gain of CSD-modified cement mortars with a parallel increase in grade strength (17%) is revealed. A significant effect of CSD on the rheological properties of cement mixtures is noted. Conclusion. Complex mechanical-thermal synthesis is a new synthetic direction for obtaining nanosized calcium hydrosilicates. The development of this direction is far from complete and is closely related to the development of the theoretical base, in particular, the concept of non-classical nucleation as applied to hydrosilicate phases. The development of the method can be aimed at searching for new organic modifiers with the acquisition of new properties of modified hydrosilicates and products of their thermal decomposition, at improving synthesis modes in order to regulate the quantitative and qualitative parameters of the nanostructured phase, consumer properties of the CSD, and expanding the scope of its application.
Бесплатно
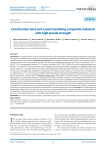
Construction heat and sound insulating composite materials with high tensile strength
Статья научная
Introduction. The objective of this study is to examine the impact of the impregnation (with the aliphatic polyurethane water dispersion) degree on the deformation properties of the polyacetal, polyethylene terephthalate and polypropylene fibers based nonwoven needle-punched composite fabrics. Materials and methods. We investigated the deformation properties of the nonwoven fabrics manufactured from the 0.33 tex linear density fibers of: polyethyleneterephthalate (diameter 20–25 microns, according to TU 6-13- 0204077-95-91), polypropylene (diameter 27–30 microns, according to TU 2272-007-5766624-93) and the original polyacetal ones (diameter 18–22 microns). The nonwoven fabrics were obtained by the mechanical formation technique. The needlepunching surface density was 180 cm–2. The water dispersion of anionic stabilized aliphatic polyethyruretane (IMPRANIL DL 1380 (China)) with a dry residue of 40% was used for the impregnation. The experimental samples’ linear dimensions were determined in accordance with the requirements of GOST 15902.2-2003. The sample’s thickness was determined by a thickness gauge with a pressure of 10 kPa and an instrumental error ~ 0.01 mm according to GOST 11358-70. The samples’ mechanical properties were determined in accordance with the requirements of GOST 15902.3-79. Results and discussion. The fiber filler composition influence on the ob-tained (by the impregnation of polyethyleneterephthalate, polypropylene and polyacetal fibers based non-woven needle-punched fabrics with polyurethane aqueous dispersion) composite materials tensile resistance has been established. We found the impregnation degree (depending on the chemical nature of the fibers and on the direction of nonwoven fabrics formation) at which the tensile resistance of the composite materials reaches the maximum value. It is demonstrated that, in the construction of buildings and structures, it is advisable to utilize materials based on composite polyacetal fibers. These materials exhibit higher tensile resistance compared to those based on polypropylene and polyethylene terephthalate at equivalent impregnation levels. Conclusion. The obtained optimal impregnation degree (at which the maximum tensile resistance of polyacetal fiber based composite materials was achieved) depends on the direction of the non-woven fabric formation. The maximum tensile resistance was observed: in the transverse direction – at 0.44 and in the longitudinal direction – at 0.35 impregnation degree values.
Бесплатно
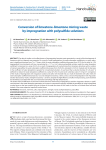
Conversion of limestone-limestone mining waste by impregnation with polysulfide solutions
Статья научная
The data of studies on the effectiveness of impregnating Aquastat waste generated as a result of the development of limestone-shell rock deposits are presented. As a result of sand impregnation, the water absorption coefficient as a result underwent a significant decrease from 7 to 17 times, while the water absorption coefficient decreases from 32.5% for the initial to 1.9% impregnated. Even treatment with low concentrated (ρ = 1.17 g / cm3) calcium polysulfide solution made the water absorption coefficient to decrease to a value of 4.5%. As a result of impregnation of crushed stone from limestone-limestone with a solution of calcium polysulfide, the water absorption coefficient decreases from 25.0% for untreated to 5.2% for treated, and the decrease in the coefficient of water absorption is greater for concentrated solutions. It was found that a solution density of 1.24 g/cm3 is sufficient to reduce the water absorption coefficient to a value of 5.2%, the same as for a density value of 1.35 g/cm3. Comparison of the results of impregnation with «Aquastat» solution and sulfur melt showed that as a result of treatment with sulfur melt, the water absorption coefficient decreases by 13.3 and strength increases by 2 times, and as a result of impregnation with «Aquastat» solution decreases by 4.62%, strength increases by 1.35 times. Despite the high efficiency of sulfur melt processing, such treatment has drawbacks associated with the use of autoclave technology and high temperatures. The results of the modification of sand and crushed stone from shell rock by impregnating it with the «Aquastat» solution, a significant decrease in the water absorption parameter, an increase in compressive strength, revealed the possibility of using impregnated crushed stone as the layer material lying at the base of the road structures of local roads in the form of crushed stone and sand instead of the more expensive imported crushed stone.
Бесплатно
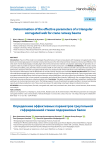
Determination of the effective parameters of a triangular corrugated web for crane runway beams
Статья научная
Introduction. The aim of this study is to investigate the performance of crane runway beams with triangular corrugated webs. These beams are increasingly popular in industrial construction because of to their enhanced shear resistance and structural efficiency. Flat webs have several disadvantages, including high stress levels and excessive material consumption. Optimizing the geometry of corrugations makes it possible to improve strength and reduce the overall construction cost. Methods and Materials. The study is based on numerical modeling using the finite element method (FEM) in LIRA-CAD 2022 software and full-scale experimental testing. The performance of beams with both corrugated and flat webs was analyzed under wheel loads from cranes with lifting capacities of 10, 30, and 50 tons. Deformations and the distribution of normal and shear stresses were evaluated. Results and Discussion. The numerical model demonstrated high accuracy, with a maximum deviation of only 2.9% from experimental results. Crane runway beams with corrugated webs exhibited lower shear and normal stresses, reduced deflections, and more uniform force distribution. They also proved to be more economical due to lower material consumption and reduced labor intensity. Additionally, the corrugated beams showed enhanced economic performance, reducing material costs. Conclusion. Triangular corrugated web beams outperform traditional flat web beams in structural and economic terms. The findings support the use of optimized corrugation profiles to increase load-bearing capacity and reduce production costs. These results are relevant for optimizing crane beam design in industrial structures.
Бесплатно
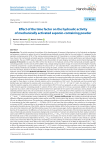
Статья научная
Introduction. The article examines the problem of the development of transport infrastructure in the Solovetsky archipelago and proposes a solution to reduce the cost of manufacturing reinforced concrete slabs for the road surface. It is proposed to use saponite-containing waste (SCW) of the mining and processing plant JSC Severalmaz as a mineral additive in concrete. Studies have shown that mechanically activated saponite-containing powder (MSP) improves concrete performance and reduces binder consumption. The use of MSP makes it possible to solve the problem of waste disposal and reduce environmental damage. The purpose of the work is to assess the effect of the time factor on the hydraulic activity of the mechanically activated saponitecontaining powder, since the activity of the additive may change during long-term storage. It is known that the degree of activity of mineral components is usually estimated by the amount of Ca2+ ions absorbed from a saturated lime solution. A number of direct analytical methods are available to monitor the change in Ca(OH)2 content over time during the course of the hydraulic reaction. This technique, based on the measurement of the potential of the ion-selective electrode, is fully suitable for monitoring the hydraulic activity of the MSP. Methods and Materials. Saponite-containing waste was used as the main material for the studies, which was isolated, dried and dispersed. A mechanically activated saponite-containing powder was thus obtained. Control of the degree of grinding of the obtained finely divided MSP samples was carried out according to the specific surface area (Ssp, m2/kg). To perform potentiometric analysis, an electrode system consisting of a measuring electrode with a calcium ion detection function (pCa) and a reference electrode was used. In preparation for the experiment, the calcium selective electrode of the Elite-041 model was kept for three days in a calcium chloride solution with a concentration of 0.01 mol/L. The electrode was then washed with distilled water and calibrated to solutions with concentrations (CCa) of 10–1, 10–2, 10–3, 10–4 and 10–5 mol/L, for which pCa = 1÷5. To study the sorption capacity, a lime solution with a concentration of 0.015 mol/l was prepared, as well as a suspension from samples of fine mineral saponite-containing powder. A solution of lime with a volume of 0.2 ml was successively added to the resulting suspension by a doser, while measuring the electromotive force (potential) of the system with continuous stirring. Based on the obtained potential values (mV), the concentration of calcium ions (Сfact Ca) in the bulk phase of the suspension was calculated using a predetermined calibration relationship. Further, using the algorithm for calculating the activity parameters of powders, according to potentiometry data, the maximum amount of absorbed calcium hydroxide (ΔССaO) was determined as the difference between the Сteor Ca and Сfact Ca, and the hydraulic activity coefficient . Results and Discussion. The resulting mechanically activated saponite-containing powder had a specific surface area of 196 m2/kg (10 min), 644 m2/kg (30 min), 1209 m2/kg (60 min), 1428 m2/kg (90 min) at different milling times. The preliminary calibration dependence of the potential of the electrode pair on the pCa value is characterized by the linear equation: E = –23,23pCa+520,35. It was found that when adding a lime solution to the suspension, an increase in EMF is observed due to the sorption of calcium ions by a mechanically activated saponite-containing powder. After reaching the threshold volume of the Ca(OH)2 solution, the potential stabilizes. With a further increase in the concentration of calcium ions, when their interaction with the MSP particles ceases, the E value increases again. Further, dependencies were obtained for all batches of the experiment, the difference of which lies only in the quantitative characteristics of the functional parameters. Initial value of electrode pair potential characterizes background concentration of calcium ions determined by their residual content in water and/or MSP. The obtained functional relationships of the Сfact Ca = f(Сteor Ca) for the test samples made it possible to determine the threshold values of the concentration of calcium ions in the solution, the excess of which creates their excess in the reaction medium. The built functional dependence of the G∞ = f(Ssp), showed that the G∞ reaches its maximum value already at a specific surface area of more than 600 m2/kg (30 minutes of grinding). Since the grinding of 10 minutes has little effect on the specific surface area of the saponite powder, which affects the value of the hydraulic activity coefficient of the MSP, the dependence of G∞ = f(Ssp) for grinding more than 10 minutes was considered.
Бесплатно
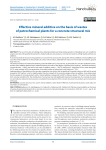
Статья научная
The use of concrete in building allows obtaining reliable and long-lasting operation of buildings, but such conditions require concrete with specified characteristics. Today hardly one can produce a concrete structural mix of high quality without any additives. To control actively the structure and properties of a concrete mix and concrete, along with chemical additives, mineral additives are used. The mineral additives are the powders of various mineral nature, obtained from natural or man-made raw materials: ground slag, rocks, etc. The article introduces the method of obtaining a mineral additive for a structural mix, in particularly for concrete. Qualitative characteristics of the additive obtained were studied as follows: the index of the degree of grinding to be equal to 1, standard consistency (normal density) – (180±5) mm with a mass ratio of «additive: water») – 100: 70, setting time – beginning 20 min, water absorption 0.27%, water content 9.65%, the proportion of insoluble residue in hydrochloric acid solution is 1.70%. Implementation of the additive in the concrete composition has shown that the quality of the product does not fall, and the actual strength is 250.7 kgf/cm2, which is slightly higher than the strength of the concrete sample without an additive. It was determined that the quality of concrete products with a mineral additive corresponds to GOST as follows: density 1775 kg/m3; mass humidity 0.3%; volume humidity 0.5%. The introduction of a structural mix will significantly improve the properties of a concrete structural mix and will also reduce the fuel resources consumption for production of the concrete structural mix, products and constructions of its basis.
Бесплатно
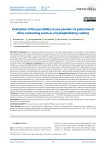
Статья научная
Introduction. An important performance characteristic of many building materials is one related to water. Therefore, hydrophobization of the surface of the material is an important task, which at the current level is solved by applying special means. It has been found that it is possible to impart water repellent properties to the surface by using polydisperse mineral materials capable of forming a rough surface. Fine powder from polymineral sand is proposed to be used as a hydrophobisate. The revealed functional relationship between the specific surface and the value of the average particle diameter of the powders, having a linear character, allows assessing their morphological structure and predicting the powder's ability to form a rough layer that enhances the water repellent properties of the surface. Methods and Materials. Four deposits of polymineral construction sands are selected as raw materials. The samples were washed and dried. Then their size modulus and true density were determined. To obtain finely dispersed powders, the raw material was ground by dry dispersion. Particle dimensional characteristics were determined by photon-correlation spectroscopy. The visual characteristic of the shape and size of the particles is determined on a laser analyzer. The specific surface area of highly dispersed rock systems was determined by gas sorption, according to BET theory. Measurement of the edge stationary wetting angle was carried out by applying a drop of distilled water to the powder surface. Results and Discussion. The dimensional characteristics of the obtained fractions showed that with a milling time (30 min) for the sands of all deposits, the average particle size (d) is 360±45 nm. At the same time, the sands of the Kenitsy and Nekhtskoye deposits have the highest values of specific surface area (Ssp). The functional relationship between the Ssp of the powders tested and 1/d was determined. The resulting linear dependencies were characterized by mathematical expressions of the form Ssp = (a/d)+b, a where reflects the rate of change in the specific surface value as the average particle diameter of the samples changes; b – is the regression line shift associated with the asymmetric shape of the particles and the non-uniformity (roughness) of the surface. It has been found that as the value of b increases, the degree of inhomogeneity of the surface formed by these particles also increases. Determination of the edge wetting angle of the surface of the powders under study showed that as the grinding time increased, the wetting angle (surface hydrophobicity) increased. So, for the surface of the fine powder of the Nekhtskoye deposit, the wetting edge angle reaches a value (114о) close in magnitude to superhydrophobicity (120о). Conclusion. The experiments showed the validity of the proposed working hypothesis related to the possible assessment of surface hydrophobicity by the experimentally determined dependence of Ssp = f (1/d). This technique can be used to select mineral powders whose fine systems are capable of hydrophobizing (if necessary hydrophilizing) the surface of the material.
Бесплатно
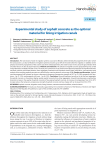
Experimental study of asphalt concrete as the optimal material for lining irrigation canals
Статья научная
Introduction. The main losses of water in irrigation systems occur due to filtration, determined by the properties of the soil in which the canal passes. Loss due to filtration in irrigation systems amounts up to 50% of the water taken for irrigation. In addition to the physical and chemical properties of the soil, the size of the wetted perimeter, the water horizon in the canal, the groundwater level and other factors are also of great importance. Methods and materials. The selection of asphalt concrete proportioning was carried out by laboratory method and Tsiat curves. The study was carried out on the chemical and physical properties of Shymkent bitumen and their mixtures with Aktau bitumen; loess aggregate, limestone and Shymkent cement were used. Micro- and nanostructural analysis of the resulting asphalt concrete was carried out by scanning electron microscope (SEM). Results and discussion. Asphalt concrete prepared with cement has shown a decrease in temporary compressive strength at 50°C by 70–38%, prepared with limestone – by 47–33%, and prepared with loess – by 66–20%. Conclusion. Ground limestone turned out to be the best aggregate for asphalt concrete, as it produces higher quality asphalt concrete than other aggregates. Ground limestone gives a particularly dramatic increase in the quality of asphalt concrete in fine-grained asphalt concrete. An increase in temperature from 20 to 50°C sharply reduces the temporary compressive strength of asphalt concrete and less sharply with an increase from 50 to 70°C.
Бесплатно
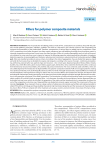
Fillers for polymer composite materials
Статья научная
Introduction. For the production of building products made of PVC, compositions are used that, along with the polymer, include additives: plasticizers, stabilizers, modifiers. This leads to a decrease in the chlorine content in the composition and increases the flammability of the productitself. Therefore, nanoparticles of various fillers are added into the compositions. Fillers inPVC compositions (more often inorganic, less often organic substances) are solid additives that differ from the polymer matrix in chemical composition and structure.In most cases, the main function of fillers is to reduce flammability and cut costs of the products obtained, in some cases they serve to impart or improve the following properties: reducing plasticizer absorption, changing in dielectric properties, increasing rigidity and hardness, reducing noise transmission, reducing toxicity of combustion products. Main part. Fillers are classified according to various criteria. According to the state of aggregation, they are divided into gaseous, liquid and solid. By their nature, they are divided into organic and inorganic; according to the source of receipt – reinforcing, strengthening, reinforcing, neutral; bythe size, particle shape and structure – into 4 main types: dispersed (powder); fibrous (fibers, threads, bundles, etc.); sheet (film) with a given structure (fabrics, paper, tapes, sheets, films, nets); volumetric (framework) with a continuous three-dimensional structure (bulk fabrics, felt, skeletal and porous frameworks). The most commonly used solid fillers, which are also called dispersed. The introduction of dispersed fillers into polymer composite materials (PCM) is more appropriate for creating mass-produced materials, more technologically advanced, with a low level of strength characteristics. Dispersed fillers are introduced into thermoplastics with high fracture energy to reduce their cost, increase stiffness and compressive strength, and improve their technological characteristics during processing. At the same time, their tensile strength and impact strength decrease due to reduction in the proportion of polymer in the filled composition. The introduction of solid and hard particles leads to an increase in the elastic modulus (E); and soft, elastic or gaseous fillers – to its decrease. According to the mechanism of action, dispersed fillers can be divided into inert ones, which do not affect the properties of the matrix and are introduced into its composition to reduce the cost of the composition, and active ones. Dispersed fillers are divided into mineral, organic and metal. The commonest of those are minerals. Conclusion. Thus, at present, there are a large number of substances and materials used as fillers and making it possible to obtain PCM with low shrinkage and shape stability of products, high mechanical properties and the necessary set of special properties. Due to fillers, PCM can compete with other materials such as glass, ceramics and even metal in most areas of human activity.
Бесплатно
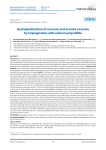
Hydrophobization of concrete and aerated concrete by impregnation with calcium polysulfide
Статья научная
Introduction. A method for protecting concrete and aerated concrete by treatment with a calcium polysulfide-based solution is considered. The solution penetrates into the pores of the materials and, after drying, forms a water-repellent nanoscale layer, protecting the material from water penetration. This ultra-thin layer is formed as a result of the destruction of calcium polysulfide molecules while drying the impregnating solution and gives the material hydrophobic properties. The paper presents research results of the properties and composition of the forming protective layer and its effect on water penetration into the materials. Materials and methods. In the article authors present data on water penetration into the studied concrete and aerated concrete samples, the size and composition of the hydrophobic agent using laser and X-ray diffraction, ultraviolet spectroscopy, as well as using visual research methods, including electron microscopy. Results. It has been revealed that the hydrophobic surface is formed from a mixture of sulfur and calcium carbonate. It is shown that concrete and aerated concrete impregnated with a calcium polysulfide-based solution acquires pronounced water-repellent properties, expressed in contact angles corresponding to superhydrophobic surfaces. The presence of sulfur was established by ultraviolet spectroscopy, and force microscopy showed the formation of nanocomposite particles from sulfur and calcium compounds. X-ray phase analysis showed that the protective layer deposited on the surface of the materials consists of sulfur nanoparticles (65%), as well as nanoparticles of calcium compounds – vaterite (21%) and calcite (13%). Surface treatment of concrete with a sprayer leads to a decrease in water absorption from 5.4% to 3.1%, and in the case of treatment by immersion to a value of 1.5%, while the use of preliminary vacuuming before immersion of the samples allows achieving a water absorption parameter of 0.9%. It is shown that impregnation with preliminary vacuuming leads to water absorption values of less than 1%, which indicates the practical water impermeability of samples of full-scale products (concrete curbs and pipes). Discussion. It is noted that during surface treatment of aerated concrete with a sprayer, a chemically resistant superhydrophobic layer in the form of a nanocomposite is being formed, which penetrates to a depth of 3–3.5 cm, reliably protecting the material from water and chemical penetration. Surface treatment is effective in cases where objects (facades, above-ground structural elements, etc.) are exposed to water in the form of rain. Treatment of concrete products by immersion and immersion treatment with vacuuming can be carried out in harsh cases of constant water exposure (underground utilities, tunnels, manholes). Conclusions. The limitation of water penetration, and in some cases the absence of water in the pores of building materials impregnated with calcium polysulfide, indicate the preservation of substance, since water is a carrier of substances that destroy concrete and aerated concrete. Accordingly, there is no destructive effect from freezing of water in the pores of such materials as a result of the formation of a nano-sized coating of sulfur particles. Comparison of the results for aerated concrete shows that it acquires superhydrophobic properties, which indicates its excellent modification and expands the possibilities of its use. The data observed for concrete products indicate that after treatment with a calcium polysulfide-based solution, they can be used under conditions of long-term and constant exposure to water.
Бесплатно
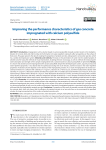
Improving the performance characteristics of gas concrete impregnated with calcium polysulfide
Статья научная
Introduction. Impregnation with a solution based on calcium polysulfide showed excellent results in the hydrophobization of concrete, brick and shell rock due to the formation of a water-repellent coating of sulfur nanoparticles on the surface of their pores. This paper presents the data of studying the properties of aerated concrete, widespread in construction practice, which has a widely developed pore system. Materials and methods. The data on the penetration of water into the studied samples of aerated concrete using the methods of visual examination, including electron microscopy, as well as methods for measuring the water absorption and strength of the samples impregnated with a solution based on calcium polysulfide are presented. Results. It is shown that aerated concrete impregnated with calcium polysulfide, despite the developed pore system, acquires pronounced water-repellent properties. It was found that the optimal processing time is 20 minutes, and the increase in the water-repellent properties of aerated concrete depends on the density of the impregnating solution. As a result of impregnation of aerated concrete by immersion in a solution with a density of 1.16 g/cm3, a decrease in 3.7 times occurs, and when treated with a solution with a density of 1.25 g/cm3, it decreases 6.8 times and becomes equal to 6%. For samples processed with the use of vacuum, in the case of processing a solution with a density of 1.16 g/cm3, water absorption decreases by 7.9 times, and when processing with a solution using vacuum, it decreases 19.8 times, while the compressive strength increases by 1.7 once. Samples of aerated concrete, treated with a polysulfide-based solution with a brush, showed that in this case, water absorption in the sprinkling mode decreases to values of 1.5–2.0%. Discussion. It is noted that during the surface treatment of aerated concrete, a chemically resistant, water-repellent layer 3–3.5 cm thick is formed, which reliably protects the material from the penetration of water and chemicals. The results of the performed experiments give reason to believe that on the surface of the pores of aerated concrete treated with a solution based on calcium polysulfide, as well as on the surface of the pores of previously investigated materials, a nanosized coating is formed of sulfur particles that hydrophobic aerated concrete. Conclusions. Comparison of the results for aerated concrete with excellent data for concrete, brick, shell rock shows that the efficiency for aerated concrete is no less and allows us to recommend the specified solution for long-term protection of the surface of aerated concrete walls
Бесплатно
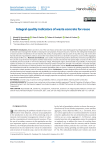
Integral quality indicators of waste concrete for reuse
Статья научная
Introduction. Waste concrete is one of the main heavy construction waste having good recycling prospects with regard to rational nature management related to reducing the consumption of natural resources. However, the widespread introduction of waste concrete is hindered on the one hand by the variety of compositions and structures of recycled scrap, and on the other hand by the lack of quantitative criteria to choose the most rational area of its use (a binder component, coarse and fine aggregate, finely dispersed filler, etc.). Materials and methods. Case studies of experimental powders obtained by mechanical grinding from the concrete scrap of internal wall panels and floor slabs (heavy concrete) and external wall panels (light concrete) of a five-storey residential panel house built in 1979 in the Obozersky village, Arkhangelsk region, demonstrated the possibility of choosing the optimal secondary use of waste concrete fractions featuring residual compressive strength. The indicators of residual strength, grindability and contraction of mineral powders were used as optimization criteria. Results and discussions. The applicability of the mathematical model for calculating the raw material grindability index is shown. A criterion for grinding equipment selection is proposed to obtain powders with an extended active surface. Conclusions. Powders obtained from the fraction of waste light concrete featuring low strength properties and grindability by mechanical grinding to a specific surface area comparable to that of Portland cement used and having a higher value of contraction can be rationally used as a composite binder component. Concrete scrap fractions featuring by higher grindability and strength properties are optimally suited for crushed aggregate preparation in the concrete composite production process.
Бесплатно
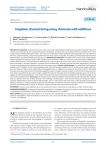
Irrigation channel lining using shotcrete with additives
Статья научная
Introduction. Shotcrete lining is the most economical and quite fully mechanized in production among all the known varieties of concrete linings. The construction practice of hydraulic structures has accumulated numerous examples of the use of a wide variety of building materials in lining – from stone to modern films made of synthetic resins. Despite the very active efforts to find more suitable materials, concrete lining will remain the main one for a long time. Accordingly, concrete lining requires further improvements, increasing durability and reducing cost. Methods and materials. The studies were carried out by the comparison method of laboratory tests of shotcrete with nanostructured surfactants additives. In the form of nanostructured additives, SCL (sulfite-cellulose liquor), NAR (neutralized air-retaining resin), cotton soap and bitumen were used in various consistency. The tests were conducted on strength properties, shrinkage, tension deformation, adhesion strength and water permeability. Structural changes in the properties were studied by electron-microscopic analysis. Results and discussion. It is established that the optimal proportion of SCL additive to the shotcrete gauged water, under the spraying condition, is 0.5% by the cement weight. NAR additive is not observed. When cotton soap additive with gauged water are added into the shotcrete, the water content in the placed shotcrete increases as the amount of the additive added increases, the optimal cement content in the shotcrete is observed when 0.3% cotton soap additive by the cement weight is added. The “rebound” decreases when the additive proportion grows. The 0.3% SCL additive by cement weight added in 1:4 dry mixture shotcrete increases its compression strength by 16%, bending strength by 1% and tension strength by 20%. Conclusion. All nanostructured surfactant additives increase the shotcrete shrinkage. The shotcrete with SCL additive shows the smallest increase in the shrinkage, and the largest – with bitumen emulsion. The additives used in shotcrete significantly increase its tension deformability, and in a wide range reduce the values of the shotcrete instantaneous elasticity modulus, i.e. enhance its plastic properties. The surfactants and bitumen emulsion reduce the adhesion strength between shotcrete and reinforcement, however, it remains at a higher level than that of conventional concretes.
Бесплатно
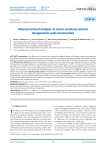
Microstructural analysis of strain-resistant cement designed for well construction
Статья научная
Introduction. The efficiency of oil and gas well construction depends largely on the stage of casing cementing and is completed by checking the quality of its fixing by various methods, most often by geophysical methods. The necessity of highquality cementing and ensuring the quality of technical conditions in the subsequent years of oil and gas well operation is the main task. Materials and methods. Microstructural features of cement slurries and cement stone were analyzed with advance methods. The essential technological properties were developed according to the requirements of GOST 1581-96 and API standards (API spec.10B). Class G cement (PCT-I-G) was used for all formulations. Polypropylene fiber and expanding additive СMA were used to increase impact resistance and to ensure tight contact with the confining surfaces of the obtained plugging stone. Microstructural analysis of the obtained cement stones and developed plugging mortars was carried out by X-ray diffraction (XRD) and scanning electron microscope (SEM). Results and discussion. The results of the study showed that the expanding additive in tandem with polypropylene fiber works effectively to ensure the integrity of the cement ring. Conclusion. Microstructural analysis of plugging stones showed a tight bond between polypropylene fiber and cement stone at a concentration of – 0.25%. The expanding additive is fully hydrated and the obtained cement stone has no expansion cracks at 7 days. The developed grouts with a water-cement ratio of 0.44 showed high compressive strength.
Бесплатно
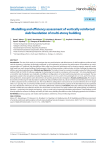
Статья научная
Introduction. The aim of this study is to investigate the structural behavior and effectiveness of slab foundations reinforced with vertical elements, a technique increasingly employed in civil engineering to improve the performance of foundations on weak, compressible soil. Traditional slab foundations often suffer from excessive settlement and low bearing capacity, especially under high loads from multi-storey buildings. Reinforcement of the soil base provides a viable solution to these challenges by improving stiffness and reducing deformation. Methods and Materials. The study is based on numerical modeling using the finite element method (FEM) in PLAXIS 3D software, applying the Hardening Soil model in accordance with Eurocode 7. A 9-storey building with a monolithic slab foundation was modeled, and different configurations of vertical reinforcing elements were analyzed. The key parameters varied in the simulations included the spacing (2×2 m, 3×3 m, and 5×5 m) and length (2.5 m, 5.5 m, and 9.5 m) of reinforcing elements. Soil properties were derived from site-specific geotechnical investigations. Results and Discussion. The analysis showed that reinforcing the slab foundation significantly reduced deformation (by a factor of three) and bending moments (by up to 60%) compared to the unreinforced case. The most efficient configuration was found to be concrete elements of 9.5 m length with 2×2 m spacing. The use of vertical reinforcement not only increased the bearing capacity of the foundation but also optimized the stress distribution within the soil mass, minimizing differential settlement. Conclusion. Vertically reinforced slab foundations provide a reliable and cost-effective solution for construction on weak soils. The study confirms that optimal design of reinforcing elements – particularly their length and spacing – plays a crucial role in improving foundation performance. These findings can be directly applied to enhance the design and safety of multi-storey building foundations under challenging geotechnical conditions.
Бесплатно
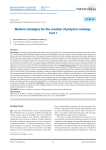
Modern strategies for the creation of polymer coatings. Part I
Статья научная
Introduction. Coatings on hard materials are widely used in many industries. Coating technologies help prevent or reduce corrosion, contamination and biofouling, chemical and structural degradation, and wear and tear of external surfaces due to exposure to the elements and natural environments. The range of materials used for functional coatings is quite wide: from organic polymers to hybrid composites and inorganic nanoparticles, depending on the desired properties and functionality of the final product. Despite the excellent anti-corrosion characteristics of non-polymer coatings, their usage causes environmental damage. Organic coatings are among the most widely used. Such compositions are applied in liquid form; organic solvents are one of the main components. Environmental concerns have encouraged the development of alternative technologies. The main areas for development are availability of raw materials and the cost of environmentally friendly coatings. Results and discussion. The review substantiates the relevance of research on the development of multifunctional polymer-based coatings. The market for polymer coatings is presented. Methods of surface protection, types of coatings formed, their main components, features of the formation of coatings, the influence of various factors on the formation of polymer coatings, including methods of preparation and pre-treatment of the protected surface are presented. Methods for preventing corrosion are discussed in detail, as well as the main directions in the development of anti-corrosion coatings based on various protective mechanisms. The characteristics of the main components of protective coatings are given. The issue of destruction of polymer coatings depending on the operating environment is considered in detail. The types of media, their influence and mechanisms of action on protected objects are considered. Factors and mechanisms of destruction of polymer coatings, methods for preventing degradation of coatings are listed. The latest technologies for the formation of protective polymer coatings are highlighted. Conclusion. Currently, coatings provide a wide range of quality indicators. An important characteristic of modern coatings is minimal negative impact on the environment, which requires an integrated approach to the design and production of coatings.
Бесплатно
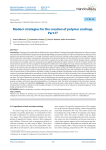
Modern strategies for the creation of polymer coatings. Part II
Статья научная
Introduction. Coatings on hard materials are widely used in many industries. Coating technologies help prevent or reduce corrosion, contamination and biofouling, chemical and structural degradation, and wear and tear of external surfaces due to exposure to the elements and natural environments. The range of materials used for functional coatings is wide enough: from organic polymers to hybrid composites and inorganic nanoparticles, depending on the desired properties and functionality of the final product. Despite the excellent anti-corrosion characteristics of non-polymer coatings, their usage causes environmental damage. Organic coatings are among the most widely used. Such compositions are applied in liquid form; organic solvents are one of the major components. Environmental concerns have encouraged the development of alternative technologies. The main areas for development are availability of raw materials and the cost of environmentally friendly coatings. Results and discussion. The review substantiates the relevance of research on the development of multifunctional polymer-based coatings. The market for polymer coatings is presented. Methods of surface protection, types of coatings formed, their main components, features of the formation of coatings, the influence of various factors on the formation of polymer coatings, including methods of preparation and pre-treatment of the protected surface are presented. Methods for preventing corrosion are discussed in detail, as well as the primary lines in the development of anti-corrosion coatings based on various protective mechanisms. The characteristics of the main components of protective coatings are given. The issue of destruction of polymer coatings depending on the operating environment is considered in detail. The types of media, their influence and mechanisms of action on protected objects are considered. Factors and mechanisms of destruction of polymer coatings, methods for preventing degradation of coatings are listed. The latest technologies for the formation of protective polymer coatings are highlighted. Conclusion. Currently, coatings provide a wide range of quality indicators. An important characteristic of modern coatings is minimal negative impact on the environment, which requires an integrated approach to the design and production of coatings.
Бесплатно