Technological processes and material science. Рубрика в журнале - Siberian Aerospace Journal
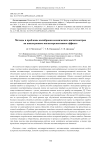
Статья научная
Instruments measuring the Earth's magnetic field are widely used in the space industry. Increasingly, loworbit spacecraft orientation and stabilization systems include magnetometers manufactured using magnetoresistive technology. This is justified by the low weight, size and consumption of such devices, which makes them ideal for use on small-sized spacecraft. However, the main problem of magnetoresistive magnetometers is the need to estimate possible measurement errors. The influence of errors significantly reduces the accuracy characteristics of the device. In order to solve the problem, researchers propose various methods for evaluating and eliminating the influence of errors on measurements [1–7]. Among the ways to eliminate errors in the readings of the device, constructive solutions are used, such as putting the device at a distance from the spacecraft using a retractable boom, in order to reduce the influence of interference on the device from the apparatus [2]. Such a solution is advisable for large spacecraft, where the presence of a retractable boom will not complicate the design and will not increase energy consumption. For small spacecraft, such a solution is not advisable, for this reason, when discussing small-sized spacecraft magnetometers, much attention is paid to calibration methods, mathematical evaluation and error correction, both in ground and in flight conditions. The objectives of the article include the formation of a general understanding of the causes of distortions in the readings of anisotropic magnetoresistive magnetometers, methods of their mathematical evaluation. A review of methods and equipment for ground calibration is carried out. The characteristics of the calibrated parameters of magnetometers are given and a mathematical model of measurement of the device is proposed, taking into account errors. The basic operations and equipment used in the calibration process are described. The results of the work can be useful in designing workplaces for calibrating magnetometers, as well as in conducting empirical research in the field of magnetometric sensors.
Бесплатно

Rigging material selection methodology for aircraft elements design
Статья научная
The development of modern materials and technologies for manufacturing structural elements of aircraft from polymer compositions requires justification for the choice of technological rigging. The physical and technical characteristics of the material, ensuring the required accuracy of rigging manufacturing, as well as economic feasibility are the main criteria for choosing the material of technological rigging. The main criteria for choosing a rigging material are the physical and technical characteristics of the material, ensuring the required accuracy rigging manufacturing, as well as economic feasibility. The choice of rigging material depends on the technology for manufacturing structural elements from polymer composite materials. The paper presents a methodology for selecting rigging material for manufacturing details using the vacuum infusion method. The methodic of rigging materials selection for aircraft constriction elements production from polymer composition by vacuum infusion is considered in the paper. The results of a comparative analysis of typical rigging materials used in production are presented. It is shown that the main criteria for a comparative analysis are: temperature, resistance to solvents, resistance to mechanical stress; maintainability; the value of the coefficient of linear thermal expansion; the stability of the geometry of the rigging and its tightness. The results of the comparative analysis showed that metals and carbon fiber are the most appropriate for the manufacture of rigging, when using high temperatures in the technological process. The paper presents an algorithm for choosing the rigging material for manufacturing the details from polymer composite materials. It is noted that in the manufacture of structural elements based on fiberglass and carbon fiber, the rigging material should be chosen the same as that of the detail. This allows, firstly, to ensure the same CLTE, what is important when hot detail formation, and, secondly, to eliminate the warping of the detail during its cooling on the rigging. However, achieving the specified accuracy of such rigging requires taking into account the processing of the rigging with a gelcoat after its manufacture. The paper presents an approach to quantifying the economic feasibility of the choice of rigging material. It is shown that only a combination of technical, technological and economic factors makes it possible to justify the expediency of the rigging material used for the specific production of aircraft structural elements.
Бесплатно
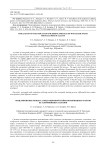
Simulation of the induction soldering process of waveguide paths from aluminum alloys
Статья научная
A system of waveguide paths is a complex structure of various elements with various geometries. Induction soldering based on the induction heating method is one of the promising methods for waveguides fabricating. Induction soldering of waveguide paths has a number of technological features: the melting temperature of the base material AD31 (695–663 0C) slightly differs from the melting temperature of St. AK12 solder (577–580 0C) at an average induction heating rate of 20–25 0C / sec; a wide variety of standard sizes of waveguide paths elements complicates the development and subsequent reproduction of technological parameters of the induction soldering process; zones of maximum heating of waveguide paths elements do not coincide with zones of soldering. Therefore, to solve the problems of controlling the waveguides soldering process, it is necessary to simulate this process. The paper deals with the problem of simulating the process of heating a waveguide during induction soldering. Requirements for the process model have been formed. The model is built on the basis of the differential heat conduction equation. The formed model requirements take into account the geometric parameters of waveguides, the physical parameters of materials, the initial and boundary conditions, as well as the uneven distribution of eddy current density in the waveguide. It is proposed to use the finite difference method for the numerical solution of the heat conduction equation. The process of calculating the temperature at the grid nodes is shown. The authors propose a two-stage solution. At the first stage, at an intermediate time step, the temperature at the grid nodes along the X axis is calculated. At the second stage, the temperature at the grid nodes along the Y axis is calculated. The numerical solution of the difference equations along the X and Y axes is carried out by the sweep method. An algorithm for the numerical solution of the heat conduction equation has been developed.
Бесплатно
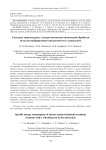
Статья научная
According to the specific energy consumption, the shaping processes are arranged in three energy levels. Electrophysical and electrochemical methods of metal processing are at the third level, where the specific energy consumption is more than 6·104 J/cm3. The analysis of the literature data showed the inconsistency of the specific costs of some authors. The specific energy consumption of electrical contact processing cannot be commensurate with the costs of electrochemical processing due to the different sizes of the particles removed from the surface of the workpiece. There are no literature data on the specific energy consumption of electro-contact-chemical treatment of metals with a vibrating instrument in the electrolyte, therefore, experiments have been carried out with the fixation of current, voltage and interelectrode gap oscillograms. The method of calculation of specific energy consumption according to the oscillograms of the process is given. The energy costs for vibration of the electrode-tool are calculated, which are an order of magnitude less for electro-contact-chemical treatment. When the vibration amplitude decreases or the voltage on the electrodes increases, the process in the interelectrode gap turns into dimensional arc processing. When electro-contact-chemical treatment of metals with a vibrating tool in water, the specific energy consumption is equal to (3.5–3.8) · 105 J/cm3, which corresponds to electrocontact treatment. It is assumed that the use of aqueous solutions of neutral salts will lead to a reduction in energy costs.
Бесплатно
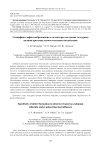
Статья научная
Active development of science-intensive technologies in the aerospace industry requires consideration of the operation of devices and instruments under extreme conditions; it is important to study the degradation of materials during rapid heating and cooling. On the basis of the theoretical and experimental work performed, the authors of the paper consider the degradation of cadmium telluride detectors caused by the development and evolution of a network of point defects resulting from pulsed exposure with a heat dose of about 1,000º С for no more than 10 s, simulating an extreme situation of a short circuit near the detector or direct heating by light pulses. The study showed that the crystalline material quickly degrades under such extreme conditions due to the rapid evolution of the defect network. The phenomenological model of the formation and distribution of defects during short-term exposure of the detector to thermal radiation has been improved. Electron microscopic studies of samples exposed to pulsed infrared radiation showed the development of a dense defect network, vacancy and interstitial defects, their clusters and other damage in all samples.
Бесплатно
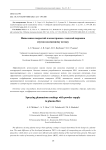
Spraying plasmatron coatings with powder supply to plasma flow
Статья научная
The efficiency of using plasma energy when applying coatings is largely determined by the design of a plasma-tron. The main difference of the developed plasmatron PM-1 is the supply of transporting gas with powder to the plaza flow, which allows us to ensure more efficient and uniform heating of the material being sprayed. This paper presents the results of measuring a material usage factor (MUF), which is an important and indicative characteristic of plasmatrons, showing their economy and productivity. The authors calculated the cost of electricity and con-ducted studies of the sprayed samples for thermal shock.
Бесплатно
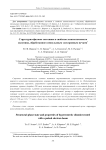
Structural-phase state and properties of hypereutectic silumin treated with a pulsed electron beam
Статья научная
Hypereutectic silumin composition are promising modern materials of wide application (mechanical engineering, aviation, instrumentation, medicine, etc.). Disadvantages of hypereutectic silumin, significantly limiting their scope of application, are pores and cavities, large (about 100 µm) inclusions of lamellar and needle-shaped second phases. As a result of the studies carried out in this work, the possibility of forming structural-phase states in the surface layer of silumin, the size and morphology of which can purposefully change in the range from tens of micrometers to tens of nanometers, is demonstrated. The irradiation modes that allow more than 5 times to increase the microhardness (15 J/cm2, 150 µs, 0.3 s–1, 5 imp.) and more than 3 times to increase the wear resistance (50 J/cm2, 150 µs, 0.3 s–1, 5 imp.) of silumin were revealed.
Бесплатно
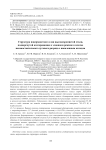
Статья научная
The purpose of this work is to reveal the patterns of formation of the structure of the surface layer of high-chromium steel subjected to nitriding in a low-pressure gas discharge plasma using a plasma genera-tor with a hot cathode "PINK". Heating of the samples to the nitriding temperature was carried out by the ionic component of the plasma, as well as by the electron and ionic components of the plasma (elion mode). The object of the study was heat-resistant corrosion-resistant steel of the austenitic class grade 20X23H18 (foreign analogue is AISI 310S). The relevance of research is due to the relatively low level of hardness and wear resistance of steels of this class. Nitriding of steel was carried out on the TRIO installation, retro-fitted with a switching unit for implementing the aelion (electronic and ionic) processing mode. It has been established that the thickness of the hardened layer is (55–60) μm and weakly depends on the method of nitriding, temperature (in the range of 793–873 K), and duration (3–5 hours) of the process. A nitriding regime has been revealed that makes it possible to form a surface layer with a microhardness of 13.7 GPa (ionic heating mode) and 10.8 GPa (elion heating mode). It has been revealed that the high strength and tribological properties of nitrided steel are due to the formation of a nanocrystalline structure in the surface layer, the main phases of which are iron nitrides Fe4N and chromium nitrides CrN. It is shown that heating the samples to the nitriding temperature in the aelion mode, which uses the electron and ion components of the plasma, leads to a significantly lower level of material roughness compared to the samples heated during nitriding by the ion component of the plasma.
Бесплатно
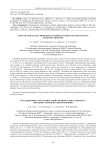
Study of structural properties of bismuth pyrostannate by Raman and IR spectroscopy
Статья научная
Chromium-substituted bismuth pyrostannates with a pyrochlore structure were synthesized by the solid-phase reaction method. The X-ray structural analysis performed at room temperature showed that the samples Bi2(Sn1-xCrx)2O7, x = 0; 0.05, 0.1 are single-phase and belong to the Pc monoclinic structure. Polymorphic transformations of the synthesized samples were studied by Raman and IR spectroscopy. IR spectra were obtained at the temperature range 110–525 K and frequencies 350–1100 cm–1. Raman spectra were measured at room temperature at frequencies of 100–3000 cm–1. Heterovalent substitution of Sn4+ for Cr3+ modifies the spectra of pure Bi2Sn2O7. The crystal structure of Bi2Sn2O7 consists of two oxygen sublattices: SnO6 and Bi2O'. Chromium ions substituted tin ions in the SnO6 oxygen octahedra, distorting the local structure in the vicinity of bismuth ions. Phonon modes are softening in the vicinity of phase transitions. А shift of the phase boundaries of polymorphic transitions is observed for Bi2(Sn1-хCrх)2O7, x = 0.05, 0.1. The frequencies of stretching vibration modes were determined from IR and Raman spectra. The substitution of chromium for tin ions resulted in the appearance of two new modes at frequencies of 581 and 822 cm–1 in the Raman spectra. The absence of an inversion center in the crystal structure of Bi2(Sn1-xCrx)2O7 is confirmed by Raman spectroscopy. IR spectra of chromium-substituted samples consist of complex lines, which decompose into 2 and 3 Lorentzian lines. The softening and broadening of optical absorption modes are associated with the electronic contribution. Impurity states of electrons form polarons.
Бесплатно
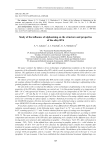
Study of the influence of alphanizing on the structure and properties of the alloy BT6
Статья научная
The paper considers the influence of two technologies of alphanizing (oxidation) on the structure and properties of the deformable titanium alloy BT6, which is used, in particular, in the aviation and space industries. The application of oxide coating by methods of chemical-thermal treatment (CTO) allows to compensate for the main drawback of the alloy – low wear resistance of the surface. The initial set of properties increases. The objects of research are titanium alloy BT6 and its oxide coatings. Two samples of the part with oxide coatings obtained by different technologies were compared. The first technology is alphanizing in finegrained graphite, the second one is alphanizing in a vacuum. The aim of the work is to find out the influence of two technologies of alphanizing on the structure and properties of the BT6 alloy. Alphanizing was carried out: 1) in fine-grained graphite at a temperature of 800 ± 10 ° C with exposure for 8 hours; 2) in an electric furnace at a temperature of 760–780 ° C in a vacuum of 10-1 – 10-3 mm Hg. for 1.5–2 hours. A study of the microstructure (light and electron microscopy) was performed. We used a microscope type Carl Zeiss Axio Observer A1m using a digital camera, adapter devices for converting an optical signal, a computer. Statistical processing was carried out according to the SIAMS700 program. Electron microscopic studies were performed using a scanning electron microscope (SEM) EVO 50 with an energy-dispersive microanalyzer INCA Energ 350. X-ray phase analysis was carried out using an X-ray diffractometer Shimadzu XRD7000, Japan (CuKa radiation, monochromator), in the following mode: range from 5 to 70 ° on a scale of 2θ, increments of 0.03°, scanning speed of 1.5 ° / min. Powders obtained from two types of coatings were investigated. The microhardness of the samples was measured on the DM8 microhardometer according to GOST 9450–76. The wear resistance of the alloy was assessed at a special laboratory installation. The phase composition and structure of the BT6 alloy after alphanizing were clarified. In the diffusion layer, the following points were detected: after alphanizing in graphite – TiO2 phases; Ti3O; TiN. After carbonation in vacuum – TiO2; Ti6O11. In the alphad layer, after processing in graphite, grains of α – solid solution, intermetallics Ti–Al-V, Ti–V and Ti–Al were detected; the alphanized layer contains more titanium after treatment in vacuum, and areas with 100% (at.) titanium have also been identified; the region of solid solution (α) and the intermetallics Ti–Al-V, Ti–V and Ti–Al are visible. The thickness of the oxidized layer is on average 103.6 μm (graphite), and in a vacuum – 66.8 μm. The average grain size in the layer is 17.2 μm (graphite); 6.0 μm (vacuum). It has been established that chemical-thermal treatment (alphanizing) contributes to a significant increase in microhardness in the diffusion layer. The hardness of HV580 (vacuum) and HV724 (graphite) was obtained on the surface. Alphanizing in graphite and in vacuum ensures the wear resistance of the product, but the best result is obtained after alphanizing in a vacuum. Both technologies improve the properties, but it is more profitable to carry out alphanizing in a vacuum, since in this case the process is carried out within 2 hours instead of 8 hours in graphite. Alphanizing (oxidation) provides wear resistance of the BT6 alloy, which contributes to the reliable operation of the product during operation.
Бесплатно
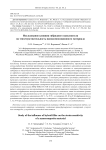
Study of the influence of hybrid filler on the strain sensitivity of a nanocomposite material
Статья научная
The reflector of spacecraft is in operation in the unfolded and folded position, thus an urgent task is to develop strain gauges that determine the position of the reflector. The paper presents a study of the influence of hybrid filler on the value of the strain resistance coefficient of a flexible strain-resistive element made of a nanocomposite material and describes the technological process of its manufacture using the vacuum infusion method. As hybrid filler, a composition containing an electrically conductive component (carbon nanotubes) and a solid component (silicon carbide), which promotes uniform distribution of the filler in the polymer matrix, were used. Using a rotational rheometer, the content of the carbon nanotubes (CNTs), at which the limiting level of viscosity for impregnation of glass fiber with a binder is achieved, was determined. The distribution features of the filler in the nanocomposite material were studied using a scanning electron microscope at the Krasnoyarsk Regional Centre for Collective Use of the Federal Research Centre KSC SB RAS. In the course of the work, the influence of the content of hybrid filler on the strain-resistive properties of the nanocomposite material was determined. The maximum values of the strain resistance coefficient were observed at the initial stage of the study (0.05 % tension): at 0.1 mm tension at a total length of 200 mm for the samples of a nanocomposite material with SiC hybrid filler of 1, 5 and 10 % and is 38, 40 and 40. The strain resistance coefficient of the nanocomposite material samples containing 1, 5 and 10 % SiC hybrid filler at maximum tensile (1 %) is approximately 19, 21 and 22 respectively.
Бесплатно
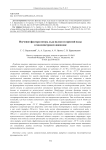
Studying the factor of ice of icing field loss from fresh water in the millimeter range
Статья научная
This research aimed at measuring the microwave radiation attenuation in an artificially formed icing field on the ice covering a freshwater lake within the millimeter range. The measurements were made using microwave radiometry at frequencies of 22, 34, 90, and 125 GHz with a cyclic change in the ambient temperature within the range from –19 to –31 C. A special technique is used, which makes it possible to determine the microwave radiation attenuation in it from the increments of radio brightness temperature between ice cover and without icing field. In the proposed method, the loss factor is found under the condition that attenuation in ice is determined by electromagnetic losses in the medium. The measurements were carried out on the ice cover of a fresh lake with a water salinity of about 100 mg/l. As a result of the study, it was found that the formation of radiation by ice is strongly influenced by scattering on the medium inhomogeneities. This conclusion was made based on comparing the calculations of the expected ice loss factor of icing field and the data obtained from measurements by the method used. The greatest difference in the loss factor (several tens of times) was found at frequencies of 90 and 125 GHz. It has been suggested that radiation scattering occurs on crystalline hydrates of salts and can be caused by increased electrical conductivity of thin water films on the crystal surface. This feature can arise, as it has been recently established, during the formation of ice 0 crystals in the medium. This ice is formed from deeply supercooled water at temperatures below –23 C. The observed effect is of interest for developing radar measurements of fresh natural ice at low temperatures and low concentrations in salts (about 100 mg/kg). Such ice can form from slightly salty water with a salt content of up to several grams per liter or when water with a salinity of ~ 100 mg/l freezes in a confined space. The results obtained are of interest for microwave aerospace determination of the ice areas with its structural disturbances, through which the water of the reservoir can penetrate to the ice surface with subsequent freezing. At the same time, radars can be effective at icing field temperatures below –20 °C, when liquid inclusions almost completely freeze out. For the temperature range above the eutectic point, where liquid inclusions appear, passive radiometric measurements can be effective.
Бесплатно
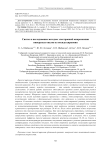
Synthesis and study by electron microsco-py of inverse opals from zirconium oxide
Статья научная
Zirconia has a high dielectric constant and high thermal stability. There are many methods for the syn-thesis of nanocrystalline materials from zirconium dioxide. These include hydrothermal synthesis, gas-phase chemical reactions, cryochemical synthesis, plasma chemistry methods - these methods are expen-sive and complex. In this work, we propose a relatively simple method for controlling the growth of zirco-nia nanocrystals by synthesis in polymer templates (template synthesis of inverse opals). Inverse opals have unique physical and chemical properties, so they can be widely used in optics, optoelectronics, biological research, catalysis, functional ceramics, which is also relevant in the rocket and space industry. As a start-ing material, we used a water-alcohol solution of zirconium oxychloride, with which we impregnated tem-plates of monodisperse submicron spherical particles of polymethyl methacrylate. After impregnation of these templates, the solution solidified in a limited pore space of 20–40 nm. After that, we annealed the result-ing templates to remove the polymer matrix. In this case, structures consisting of zirconium dioxide nano-crystals were formed. Using the methods of scanning and transmission electron microscopy, we assessed the morphology of the obtained materials, and showed that under conditions of limited diffusion, zirconia forms crystals with a size of 10–30 nm. Also, depending on the calcination temperature, materials with dif-ferent crystalline modifications are obtained. As a result, we have shown that water-alcoholic solutions of zirconium oxychloride are a convenient means for obtaining nanocrystalline materials, including inverse opals from zirconium dioxide, by template synthesis.
Бесплатно
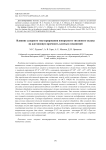
Статья научная
The paper examines issues related to the influence of laser texturing of the surface of a titanium alloy on the characteristics of the titanium-carbon fiber adhesive joint. Using an ytterbium pulsed fiber laser, textures with a linear structure (0°–0° and 90°–90°) and a mesh structure (0°–90°, ±30°, ±45°, ±60°) were created on the surface of a titanium alloy. The surface roughness values in two perpendicular directions were determined, and microsections were made, which can be used to characterize the surface morphology of the titanium alloy. To determine the adhesive strength of the joint, samples with the same surface texture were glued together. The samples were glued together according to OST 1-90281–86. Bonding was carried out within 24 hours after laser surface treatment. Before gluing, the treated surface was cleaned with isopropyl alcohol. Adhesive joint area S = 300 mm2. Three-component adhesive VK-9 based on epoxy and polyamide resin was used as an adhesive. Laser surface treatment of titanium alloys increases the strength of the adhesive joint by more than 70 % relative to the untreated surface. This may indicate that the main mechanisms for increasing the strength of an adhesive joint are an increase in the contact area between the surface and the adhesive, and chemical modification that activates the surface. The processing texture has a lesser effect on the adhesive strength, provided that the specific surface energy of the laser processing is the same. When laser processing, you should pay great attention to the choice of surface texture, because certain textures can give an increase in strength by 20–30 %. If the type of load in the truss load elements is known, then it is better to use linear textures directed perpendicular to the direction of the load (for shear – texture 0°–0°; for torsion – texture 90°–90°). For mixed loads, it is better to use mesh structures ±30°, ±45°, ±60°, which resist loads in two directions.
Бесплатно
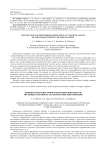
The influence of prefinishing operations at titanium alloys on the characteristics of MAO coatings
Статья научная
Improving the reliability, service life and operational safety of titanium alloy structures exposed to thermal, chemical and mechanical stresses can be achieved by applying various protective coatings. One of the effective methods of protecting such alloys is the formation on their surface of oxide coatings that are resistant to external factors. Of great interest from this point of view is the method of micro-arc oxidation (MAO), which allows one to obtain multifunctional ceramic-like oxide coatings with unique properties. Such coatings can be used to create a durable heat and electrical insulating layer on parts, protect surfaces from erosion in high-speed gas flows, corrosion in aggressive environments and wear by friction, to increase the surface emissivity, etc. This method is well established for the oxidation of aluminum alloys. Despite the fact that the mechanism of coating formation during MAO is the same for aluminum and titanium alloys, there are certain differences in the structure and characteristics of the resulting coating. For example, it is believed that during the MAO treatment of aluminum alloys, preliminary surface preparation is not required and the adhesive strength is comparable with the strength of the substrate material. However, when processing titanium alloys, we noted cases of a significant decrease in adhesive strength. One of the reasons may be the lack of preliminary surface preparation before coating. Therefore, studies aimed at studying the influence of the method of surface preparation and the resulting roughness on the characteristics of the applied coatings are relevant.
Бесплатно
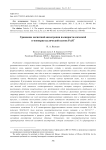
The magnetic anisotropy comparison of polycrystalline and single-crystal Fe3Si films
Статья научная
High-tech devices improvement requires development of technology and search for new materials from science. Currently, the development of the magnetism research field has reached a very broad knowledge, making it possible to create and study a variety of artificial ferromagnetic materials, which are already actively used in science and technology. The latest scientific knowledge shows that the same material in different states can exhibit different electrical and magnetic properties. Thus, thin magnetic films are actively used in modern devices. Physical processes in thin films proceed differently than in bulk materials. As a result, the film elements have characteristics that differ from those of bulk samples and make it possible to observe effects that are not characteristic of bulk samples. A film is a thin layer of a bound condensed substance, the thickness of which is compared with the distance of surface forces action; it is a thermodynamically stable or metastable part of a heterogeneous film-substrate system. Further researsh of film structures led to the creation and study of multilayer magnetic systems. In such structures, the presence of both various ferromagnetic materials layers and non-ferromagnetic interlayers is possible, and the multilayer systems properties can differ significantly from the properties of any system components. These materials also have many practical applications, including radio communications and geological exploration. In our experiment, ferromagnetic thin films of Fe3Si silicide were synthesized by molecular beam epitaxy with co-deposition of Fe and Si. A polycrystalline silicide film was obtained on a SiO2/Si(111) substrate, and a single-crystal film - on Si(111)7×7. The structure was investigated using the diffraction of reflected fast electrons directly during the growth process. The magnetic anisotropy of the obtained samples was studied applying the method of ferromagnetic resonance. It was found that the polycrystalline film is characterized by uniaxial magnetic anisotropy, which is 13.42 Oe and is formed as a result of “oblique” deposition, whereas the magnetic anisotropy for a single-crystal Fe3Si film is formed to a greater extent by internal magnetocrystalline forces.
Бесплатно
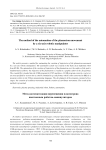
The method of the automation of the plasmotron movement by six-axis robotic manipulator
Статья научная
The article presents a method for automating the creation of trajectories of the plasmotron movement by a six-axis robotic manipulator. The automation system was created on the basis of an industrial robot from KUKA. The automation of the creation of trajectories of the plasmatron over the surface of the part is implemented as follows: the trajectory of the plasmatron is created in a graphic editor in the .dwg format. The created file is loaded into the CAM program for CNC machines. A CAM program converts a vector or an area specified by vectors into a control command in g-code format, which is then converted to KRL by a program written in the Python programming language. The development of the program consisted of two stages: the creation of rectilinear movements and the creation of curvilinear movements. The result of the method is presented.
Бесплатно
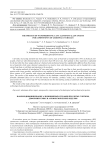
The process of nanomodifying cast aluminum alloy ingots for components of aerospace vehicles
Статья научная
Currently, increasing attention has been paid to such a class of materials as nanopowders (NP) of chemical compounds, which are ultra-thin formations of not more than 100 nm in size. Such attitude to these materials is explained by the fact that they have unique physical, chemical and mechanical properties significantly different from the properties of materials of the same chemical composition in a massive state, and these properties can be transferred to some extent from them or with their participation to the products. The existing methods of introducing NP into metal melts could not be used due to their special properties in comparison with coarse powders, and therefore a new method of their introduction into the melt was developed, excluding direct contact of NP particles with oxygen and unhindered penetration of particles into the melt through the oxide layer. The essence of the method was as follows. In the aluminum container filled up with aluminum particles or deformable aluminum alloys D1 or D16 and various NP (nitrides, carbides, oxides, etc.), and this composition was pressed into the rod, with its help NP was introduced into the melt during casting of aluminum ingots and deformable aluminum alloys. The results of the study showed that this excludes the appearance of cracks in the ingots, as well as improves their technological and mechanical properties.
Бесплатно
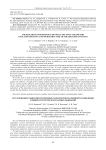
Статья научная
Today, protective coatings are applied to almost all parts and components of engineering products in order to ensure high performance properties of machines, with the lowest economic cost. The method of plasma spraying allows to apply heat-resistant coatings on a different kind of basis, in addition to a wide variety of materials. Therefore, rocket and space engineering is primarily interested in the method. In modern conditions of high rate of mechanical engineering development engineers must develop and put into operation products within the shortest possible period of time. As a rule, engineers select the modes of plasma spraying using the method of selecting the empirical relationship between the properties of the coatings and the values of the specified parameters of plasma spraying, which suggests conducting a huge number of experiments. That is why we see the need to find new methods for selecting the plasma spraying parameters, which are based on mathematical and analytical apparatus. We set the task to study and show the applicability and prospects of the proposed method. In the work we carried out the operations of spraying nichrome coating, at different values of the arc current. We studied the adhesive strength of the coatings obtained and their microstructure. We showed the relationship between the arc current and the adhesion of the coatings using their microstructure. These studies have made it possible to exclude a large number of experiments, which usually establish an empirical relationship between the values of the input parameters of the deposition process and the values of the characteristics of the coatings obtained. In the future, we assume that the database of such relationships will make it possible to fully use this method in engineering industries.
Бесплатно
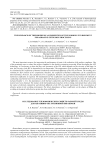
Статья научная
The most important resource for improving the performance of parts is the reduction of the surface roughness. One of the promising ways to reduce the surface roughness is the abrasive extrusion processing. When developing the AEP technology, it is necessary to know the flow rate (pressure) of the WE, which depends on the viscosity of the latter. In turn, the viscosity of the WE is determined by its temperature. The temperature of the working environment at AEP can be calculated if the coefficients of thermal conductivity and thermal diffusivity of the WE are known. The working environment for AEP consists of two components, therefore, the coefficient of thermal conductivity can be calculated by known formulas. However, the calculation error is significant, therefore, the experimental determination of the abovementioned coefficients is required. The installations for the coefficients research have been presented, the methods of conducting experiments have been developed. After mathematical processing of the experiments results by means of the AdvanceGrapher v. 2.11, the dependences of the thermal conductivity and thermal diffusivity on the abrasive concentration have been obtained. The studies of the thermophysical properties of the working environment have shown that the values of thermal conductivity and thermal diffusivity of the WE are mainly determined by the concentration of abrasive grains in the working environment. The direct dependence of these coefficients on the degree of filling the working environment with abrasive grains has been established.
Бесплатно