Статьи журнала - Siberian Aerospace Journal
Все статьи: 352
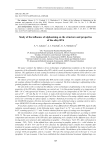
Study of the influence of alphanizing on the structure and properties of the alloy BT6
Статья научная
The paper considers the influence of two technologies of alphanizing (oxidation) on the structure and properties of the deformable titanium alloy BT6, which is used, in particular, in the aviation and space industries. The application of oxide coating by methods of chemical-thermal treatment (CTO) allows to compensate for the main drawback of the alloy – low wear resistance of the surface. The initial set of properties increases. The objects of research are titanium alloy BT6 and its oxide coatings. Two samples of the part with oxide coatings obtained by different technologies were compared. The first technology is alphanizing in finegrained graphite, the second one is alphanizing in a vacuum. The aim of the work is to find out the influence of two technologies of alphanizing on the structure and properties of the BT6 alloy. Alphanizing was carried out: 1) in fine-grained graphite at a temperature of 800 ± 10 ° C with exposure for 8 hours; 2) in an electric furnace at a temperature of 760–780 ° C in a vacuum of 10-1 – 10-3 mm Hg. for 1.5–2 hours. A study of the microstructure (light and electron microscopy) was performed. We used a microscope type Carl Zeiss Axio Observer A1m using a digital camera, adapter devices for converting an optical signal, a computer. Statistical processing was carried out according to the SIAMS700 program. Electron microscopic studies were performed using a scanning electron microscope (SEM) EVO 50 with an energy-dispersive microanalyzer INCA Energ 350. X-ray phase analysis was carried out using an X-ray diffractometer Shimadzu XRD7000, Japan (CuKa radiation, monochromator), in the following mode: range from 5 to 70 ° on a scale of 2θ, increments of 0.03°, scanning speed of 1.5 ° / min. Powders obtained from two types of coatings were investigated. The microhardness of the samples was measured on the DM8 microhardometer according to GOST 9450–76. The wear resistance of the alloy was assessed at a special laboratory installation. The phase composition and structure of the BT6 alloy after alphanizing were clarified. In the diffusion layer, the following points were detected: after alphanizing in graphite – TiO2 phases; Ti3O; TiN. After carbonation in vacuum – TiO2; Ti6O11. In the alphad layer, after processing in graphite, grains of α – solid solution, intermetallics Ti–Al-V, Ti–V and Ti–Al were detected; the alphanized layer contains more titanium after treatment in vacuum, and areas with 100% (at.) titanium have also been identified; the region of solid solution (α) and the intermetallics Ti–Al-V, Ti–V and Ti–Al are visible. The thickness of the oxidized layer is on average 103.6 μm (graphite), and in a vacuum – 66.8 μm. The average grain size in the layer is 17.2 μm (graphite); 6.0 μm (vacuum). It has been established that chemical-thermal treatment (alphanizing) contributes to a significant increase in microhardness in the diffusion layer. The hardness of HV580 (vacuum) and HV724 (graphite) was obtained on the surface. Alphanizing in graphite and in vacuum ensures the wear resistance of the product, but the best result is obtained after alphanizing in a vacuum. Both technologies improve the properties, but it is more profitable to carry out alphanizing in a vacuum, since in this case the process is carried out within 2 hours instead of 8 hours in graphite. Alphanizing (oxidation) provides wear resistance of the BT6 alloy, which contributes to the reliable operation of the product during operation.
Бесплатно
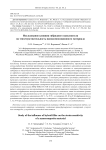
Study of the influence of hybrid filler on the strain sensitivity of a nanocomposite material
Статья научная
The reflector of spacecraft is in operation in the unfolded and folded position, thus an urgent task is to develop strain gauges that determine the position of the reflector. The paper presents a study of the influence of hybrid filler on the value of the strain resistance coefficient of a flexible strain-resistive element made of a nanocomposite material and describes the technological process of its manufacture using the vacuum infusion method. As hybrid filler, a composition containing an electrically conductive component (carbon nanotubes) and a solid component (silicon carbide), which promotes uniform distribution of the filler in the polymer matrix, were used. Using a rotational rheometer, the content of the carbon nanotubes (CNTs), at which the limiting level of viscosity for impregnation of glass fiber with a binder is achieved, was determined. The distribution features of the filler in the nanocomposite material were studied using a scanning electron microscope at the Krasnoyarsk Regional Centre for Collective Use of the Federal Research Centre KSC SB RAS. In the course of the work, the influence of the content of hybrid filler on the strain-resistive properties of the nanocomposite material was determined. The maximum values of the strain resistance coefficient were observed at the initial stage of the study (0.05 % tension): at 0.1 mm tension at a total length of 200 mm for the samples of a nanocomposite material with SiC hybrid filler of 1, 5 and 10 % and is 38, 40 and 40. The strain resistance coefficient of the nanocomposite material samples containing 1, 5 and 10 % SiC hybrid filler at maximum tensile (1 %) is approximately 19, 21 and 22 respectively.
Бесплатно
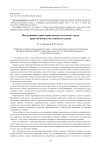
Study of the payload extraction trajectory heavy class carrier rocket
Статья научная
As the weight and complexity of the payload that needs to be launched into orbit increases, the relevance of rational trajectory selection to ensure maximum efficiency and minimum costs for delivering the payload to a given orbit increases. Rational choice of the trajectory of a heavy-class launch vehicle has a number of important practical applications. Firstly, it allows you to increase the payload capacity of the launch vehicle and reduce the cost of delivering payload to the target orbit. This is especially important in the context of the development of the space industry, when more and more companies and organizations are showing interest in launching their own satellites and other spacecraft in conditions of fierce economic competition. Choosing a rational trajectory for launching a payload into orbit will significantly reduce the cost of launches and make them available to a wider range of potential customers. Secondly, the choice of launch vehicle trajectory parameters is important for ensuring safety and minimizing risks during spacecraft launches. Thanks to the rational choice of trajectory, it is possible to reduce adverse impacts on the environment and eliminate the possibility of emergency situations associated with loss of control over the flight of the launch vehicle. Rational selection of launch vehicle trajectory parameters is a complex task that requires comprehensive research and consideration of various factors, such as aerodynamic parameters of the atmosphere, mass and characteristics of the payload (spacecraft), engine operating parameters, characteristics of the target orbit, features of the launch of the launch vehicle and many other factors. A more thorough and systematic study of the influence of these parameters will significantly improve the efficiency and reliability of launching spacecraft into orbit. Thus, the choice of rational parameters for the launch vehicle trajectory is a relevant and important topic for scientific research. Increasing the rocket's payload capacity, reducing the cost of delivering a spacecraft to a given orbit, and ensuring launch safety are tasks that depend on the chosen shape and parameters of the rocket's trajectory. Such research has important practical significance and can become the basis for the development of new technologies and methods in the space industry. The purpose of the study is to study and select rational parameters for the trajectory of a heavy-class launch vehicle when launching a payload. The main task is to determine the flight path parameters that will allow achieving maximum efficiency and accuracy in delivering the payload to a given orbit. To achieve the goal of the study, the analysis of various factors influencing the launch parameters of the spacecraft is required, such as structural and aerodynamic characteristics of the rocket, the influence of aerodynamic factors and the Earth’s gravitational field on the flight path. Taking these factors into account, numerical calculations were carried out on the basis of a system of differential equations of motion using a computer program created in the MAPLE software package. Based on the calculations, modeling of the shape and parameters of the launch vehicle flight path was carried out. Research results. During the study, the rational parameters of the trajectory of a heavy-class launch vehicle were selected. The calculations were carried out using numerical modeling of the parameters of payload launch trajectories, and the analysis of the resulting trajectories was carried out. Minimizing the rocket's flight time was identified as the main criterion for the rational choice of a trajectory, which allows increasing launch efficiency and saving energy resources. An increase in payload mass and minimization of fuel consumption were adopted as additional criteria. Conclusion. The procedure for choosing rational parameters for the trajectory of a heavy-class launch vehicle proposed in this work will improve the delivery accuracy and reliability of spacecraft launches at the stage of ballistic analysis when designing rockets. The results of the study have practical significance for the development of future heavy-lift launch vehicle missions and improving the efficiency of space launches.
Бесплатно
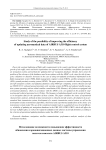
Статья научная
Due to the constant tightening of flight safety requirements in the country and abroad, with the constant growth of air traffic, more and more requirements are imposed on the reliability, non-failure operation of air navigation systems and methods for updating their air navigation databases. Besides, there arises the problem of the relevance of the databases used in accordance with the AIRAC cycle, since the risk of emer-gency situations or disasters increases in the case of using non-updated aeronautical information in the flight management system (FMS), flight management computer system (FMCS), satellite navigation system (SNS), ground proximity warning system (GPWS). The paper proposes to consider the issues of improving aircraft navigation systems and updating databases using FMS-type computing systems. Russian aircraft use FMCS-95-1V, onboard ground proximity early warning systems (GPWS) and onboard satellite naviga-tion systems operating with an orbital satellite constellation (GPS, Glonass). All of them are equipped with aeronautical databases, which, in accordance with the AIRAC cycle, are updated on the ground by engi-neering and technical personnel every 28 days. The frequency of updating depends on the receipt of chang-es in navigation data for the operation of these systems. The paper considers the issues of operational characteristics analysis, methods of data transmission to onboard aircraft systems, development of an aer-onautical data transmission system, development of a remote transmission control system, as well as the development of data transmission algorithms, theoretical and experimental justification of the choice of a transmission system model. The use of the considered complex leads to a qualitatively new level of efficien-cy, reliability of updating air navigation databases in the FMS, SNS, GPWS, FMCS, which will affect the increase in flight safety, as well as the regularity of flights in the absence of aircraft downtime according to the criterion of operational updating databases under the AIRAC cycle.
Бесплатно
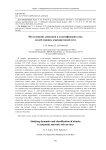
Studying dynamics and classification of attacks to corporate network web services
Статья научная
The article presents a study of the dynamics of attacks onto the web services using the classification of cyber threats by types due to the example of the corporate network of the Krasnoyarsk Scientific Center of the Siberian Branch of the Russian Academy of Sciences. The analysis is carried out on the basis of web services logs and it allows to solve urgent problems of ensuring the integrated security of web services, including identifying both existing and potential cybersecurity threats. The article demonstrates a review of the main approaches to the processing and analyzing logs. The authors describe the type and composition of data sources and provide a list of the software used. A feature of the study is a long observation period. The structure of the processing system is proposed and software tools for attack analysis and classification are implemented. The research shows that the use of classified samples allows to detect periodicity and reveal trends of certain types of attacks. Unclassified attacks have similar distribution parameters for different years, while in the case of classification, the distribution parameters have changed significantly, which makes it possible to track risks in automated intrusion prevention systems. A correlation matrix by type of attack is constructed. The analysis shows that most attack types have weak correlation, with the exception of the attacks “command injection”, “directory browsing”, “Java code injection”, which can be aggregated. The authors propose a heuristic method of risk comparison based on cyber threat classification. The method uses statistical parameters of sample distributions and permits to deal with different time intervals. The paper georeferences the IP addresses from which the attacks are carried out, builds attack profiles for different countries, and provides a list of countries with a stable attack profile. The conclusion indicates the features of the proposed method and outlines the prospects for its use in other areas.
Бесплатно
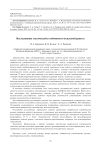
Studying static stability of a model rocket
Статья научная
Relevance. When designing flying models of rockets, one of the difficult tasks is to ensure the static stability of the rocket in flight along a given trajectory. Static stability refers to the ability of a model to return to an equilibrium position disturbed by external forces (wind, model asymmetry, etc.). In this case, the model must be stabilized in terms of the angle between the longitudinal axis of the model and the direction of flight (velocity vector), that is to maintain a zero angle of attack. The condition for ensuring the static stability of the rocket model is the location of its center of gravity ahead of the center of pressure. In this case, when the angle of attack is different from zero, the aerodynamic forces will create a stabilizing moment, which will return the model to a zero angle of attack. The purpose of the study is to develop and compare methods for determining the position of the center of pressure of a rocket and determining its static stability. The research considers a simplified method, an analytical calculation, a graphical method, and various practical approaches that can be used in rocket modeling. As research methods, an analytical approach, a graphical method and finite element modeling in the SolidWorks Flow Simulation program were used. In addition, a number of approximate calculation methods were considered. The study analyzes the capabilities of the considered methods for determining the static stability of a model rocket and the error of their application. To confirm the results of the calculation, a computer experiment was carried out in the form of blowing a finite element model of a rocket using the SolidWorks Flow Simulation program. The results of computer simulation confirmed the reliability of the proposed methods for determining the static stability of a model rocket. Research results. Simplified methods for determining the static stability of a rocket are the simplest and most reliable when designing model rockets. It is advisable to use it for launching demonstration rockets with an allowable misalignment error of 15% or more. Analytical methods are useful for designing sports models of rockets with high flight requirements, for example, for international competitions. Conclusion. The proposed method for ensuring the static stability of a model rocket makes it possible to simplify the design process of both demonstration and sports models of rockets for reliable demonstration launches.
Бесплатно
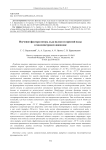
Studying the factor of ice of icing field loss from fresh water in the millimeter range
Статья научная
This research aimed at measuring the microwave radiation attenuation in an artificially formed icing field on the ice covering a freshwater lake within the millimeter range. The measurements were made using microwave radiometry at frequencies of 22, 34, 90, and 125 GHz with a cyclic change in the ambient temperature within the range from –19 to –31 C. A special technique is used, which makes it possible to determine the microwave radiation attenuation in it from the increments of radio brightness temperature between ice cover and without icing field. In the proposed method, the loss factor is found under the condition that attenuation in ice is determined by electromagnetic losses in the medium. The measurements were carried out on the ice cover of a fresh lake with a water salinity of about 100 mg/l. As a result of the study, it was found that the formation of radiation by ice is strongly influenced by scattering on the medium inhomogeneities. This conclusion was made based on comparing the calculations of the expected ice loss factor of icing field and the data obtained from measurements by the method used. The greatest difference in the loss factor (several tens of times) was found at frequencies of 90 and 125 GHz. It has been suggested that radiation scattering occurs on crystalline hydrates of salts and can be caused by increased electrical conductivity of thin water films on the crystal surface. This feature can arise, as it has been recently established, during the formation of ice 0 crystals in the medium. This ice is formed from deeply supercooled water at temperatures below –23 C. The observed effect is of interest for developing radar measurements of fresh natural ice at low temperatures and low concentrations in salts (about 100 mg/kg). Such ice can form from slightly salty water with a salt content of up to several grams per liter or when water with a salinity of ~ 100 mg/l freezes in a confined space. The results obtained are of interest for microwave aerospace determination of the ice areas with its structural disturbances, through which the water of the reservoir can penetrate to the ice surface with subsequent freezing. At the same time, radars can be effective at icing field temperatures below –20 °C, when liquid inclusions almost completely freeze out. For the temperature range above the eutectic point, where liquid inclusions appear, passive radiometric measurements can be effective.
Бесплатно
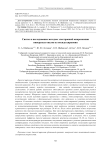
Synthesis and study by electron microsco-py of inverse opals from zirconium oxide
Статья научная
Zirconia has a high dielectric constant and high thermal stability. There are many methods for the syn-thesis of nanocrystalline materials from zirconium dioxide. These include hydrothermal synthesis, gas-phase chemical reactions, cryochemical synthesis, plasma chemistry methods - these methods are expen-sive and complex. In this work, we propose a relatively simple method for controlling the growth of zirco-nia nanocrystals by synthesis in polymer templates (template synthesis of inverse opals). Inverse opals have unique physical and chemical properties, so they can be widely used in optics, optoelectronics, biological research, catalysis, functional ceramics, which is also relevant in the rocket and space industry. As a start-ing material, we used a water-alcohol solution of zirconium oxychloride, with which we impregnated tem-plates of monodisperse submicron spherical particles of polymethyl methacrylate. After impregnation of these templates, the solution solidified in a limited pore space of 20–40 nm. After that, we annealed the result-ing templates to remove the polymer matrix. In this case, structures consisting of zirconium dioxide nano-crystals were formed. Using the methods of scanning and transmission electron microscopy, we assessed the morphology of the obtained materials, and showed that under conditions of limited diffusion, zirconia forms crystals with a size of 10–30 nm. Also, depending on the calcination temperature, materials with dif-ferent crystalline modifications are obtained. As a result, we have shown that water-alcoholic solutions of zirconium oxychloride are a convenient means for obtaining nanocrystalline materials, including inverse opals from zirconium dioxide, by template synthesis.
Бесплатно
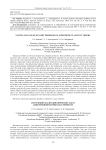
System analysis of dynamic problems of anisotropic plasticity theory
Статья научная
Dynamic problems are the least studied area of plasticity theory. These problems arise in various fields of engineering and science, but the complexity of the original differential equations do not allow to develop accurate solutions and correctly solve numerical boundary value problems. This is even more typical of dynamic equations of anisotropic plasticity. Anisotropy reduces the group of symmetries allowed by the equations, and therefore narrows the number of invariant solutions. One-dimensional dynamic plasticity problems are well studied, but two-dimensional problems cause insurmountable mathematical difficulties due to the nonlinearity of the basic equations, even in the isotropic case. The study of the symmetries of the plasticity equations allowed us to find some exact solutions. The most known solution was found by B. D. Annin, who described the unsteady compression of a plastic layer made of isotropic material by rigid plates. Annin's solution is linear in two spatial variables, however, it includes arbitrary functions of time. Symmetries are also used in the proposed work. Point symmetries are first calculated for dynamic plasticity equations in the anisotropic case and are presented in the paper. The Lie algebra generated by the found symmetries appeared to be infinite-dimensional. This circumstance made it possible to apply the method of constructing new classes of nonstationary solutions. Symmetry can transform the exact solution of stationary dynamic equations in non-stationary solutions. The framed solutions include arbitrary functions and arbitrary constants. The outline of the article is as follows: according to the method of Lie group of point symmetries allowed by the equations of anisotropic plasticity is calculated. Two classes of new stationary invariant solutions are framed. These stationary solutions, by means of transformations generated by point symmetries, are transformed into new non-stationary solutions. In conclusion, a new selfsimilar solution of unsteady equations of anisotropic plasticity is framed; Annin's solution is generalized for the anisotropic case. The framed solutions can be used to describe the compression of plastic material between rigid plates, as well as to test programs, designed to solve anisotropic plastic problems.
Бесплатно
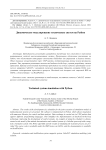
Technical system simulation with Python
Статья научная
The results of the development of a scheduler for the joint execution of simulation models of multicomponent systems are presented. The software is implemented in Python, which allows integration with numerous libraries for control and data analysis. Data exchange is carried out via UDP packets that support different programming languages. This simplifies the implementation of hardware-in-the-loop technology, improving the development of control systems. An example of using the scheduler is demon-strated on the model of the attitude determination and condtrol system of a CubeSat spacecraft with a magnetic orientation system. The B-Dot algorithm and the results of simulating the transient process are provided. The source code is available under the BSD license on GitFlic, and the documentation is available on ReadTheDocs.
Бесплатно
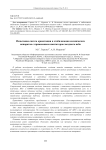
Testing of spacecraft orientation and stabilization systems using starry sky simulators
Статья научная
The paper investigates the need to create a method of simulating the starry sky for testing spacecraft and conducting tests of orientation and stabilization systems in laboratory conditions. Modern space exploration and, as a consequence, the complexity of technical requirements for flight support facilities are constantly increasing, respectively, the requirements for ensuring the accuracy of determining the position and orientation of the spacecraft are increasing. The history of the development of astroorientation devices and, in particular, stellar sensors is given. The modern stage of development of stellar sensors came with the advent of matrix radiation receivers: charged coupled device (CCD) and complementary metal-oxide semiconductor (CMOS) video matrices. Such stellar sensors are no longer tied to individual, predefined stars, but determine their orientation from images of groups of stars visible in the field of view of the device. Examples are given for their field of application, namely, determining the orientation of the sensor, pointing some device mounted on a spacecraft, and others. Modern requirements for astrogation are given. The basic principles of ground-based testing of the spacecraft orientation and stabilization system using starry sky simulators are considered. This is a stage of development and autonomous tests on a hardware and software stand of semi-natural modeling. To date, the ISS JSC enterprise has a complex modeling stand for conducting these types of spacecraft tests, using methods of both mathematical and semi-natural modeling, which includes various simulators of the starry sky. The development of these simulators has a long history, a comparative table of previously used simulators is given. The structures of both past and modern simulators of the starry sky are shown. The conclusions state the need to create a method that will simulate the rotation of the spacecraft at speeds up to 15–30 °/s. This method will allow testing the orientation and stabilization system of modern spacecraft.
Бесплатно
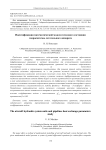
The aircraft hydraulic system units and pipelines heat exchange parameters study
Статья научная
The paper offers a method of mathematical modelling of aircraft hydraulic system thermal state. The given mathematical model presents a system of partial differential equations for carbon-fiber composite thermal insulation together with ordinary differential equations for hydraulic system components that describe their heat exchange with the ambient air and close-located surfaces. To solve the direct thermal state problem for hydraulic system components, i. e., to solve a stiff ordinary differential equation system, a Rosenbrock-type second order approximation numerical scheme for non-autonomous systems was applied. A solution of a partial differential equation system in Monte-Carlo method based on a probabilistic representation of the solution as a functional expectation of the diffusion process was also used. The inverse problem of the hydraulic system elements’ thermal state was solved applying a composition of the steepest descent method, Newton method and quasi-Newton method of Broydon-Fletcher-Goldfarb-Shanno. A mathematical model of the thermal state of a hydraulic system unit operating in an unpressurized aircraft compartment has been also developed, and the confidence intervals of each of the required model coefficients have been estimated using 2 1 α χ distribution at confidence probability = 0.95.
Бесплатно
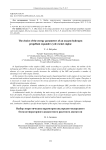
The choice of the energy parameters of an oxygen-hydrogen propellant expander cycle rocket engine
Статья научная
In liquid-propellant rocket engines (LRE), made according to a gas-free scheme, the turbine of the turbopump unit (TPU) is driven by heated fuel in the coolant system of the combustion chamber (CC). The absence of a gas generator greatly increases the reliability of the LRE and provides a number of advantages over other engine schemes. At the moment, the existing oxygen-hydrogen gasless liquid-propellant rocket engines do not meet mod-ern tactical and technical requirements for the level of thrust and pressure in the (CC) engine. Therefore, it is necessary to study ways to increase the energy parameters of the liquid-propellant rocket engine and identify promising engine schemes. This article proposes schematic solutions for an oxygen-hydrogen LRE, provides an analysis of the influence of various factors on the power parameters of the engine, as well as recommendations for the design of gasless LRE. A mathematical model for calculating the main energy and geometric parameters of the engine has been developed. Prospective pneumohydraulic schemes of an oxygen-hydrogen gasless liquid-propellant rocket engine are proposed, depending on the tactical and technical requirements.
Бесплатно
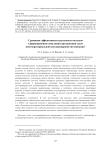
Статья научная
Dynamic multi-objective optimization problems are challenging and currently not-well understood class of optimization problems but this class is of great practical value. In such problems, the objective functions, their parameters and restrictions imposed on the search space can change over time. This fact means that solutions of the problem change too. When changes appear in the problem, an optimization algorithm needs to adapt to the changes in such a way that the convergence rate is sufficiently high. The work is devoted to the comparison of the different approaches to formation of a new population when changes in the dynamic multi-objective optimization problem appear: using solution, which obtained in the previous step; using a random generating of the population; partial using solutions which obtained in the previous step. In the first part of the article the classification of the changes in the problems is provided; the currently existing approaches to solving the problems based on evolutionary algorithms are considered. During the research NSGA-2 and SPEA2 algorithms are used to solving the dynamic optimization problems, the benchmark problems set is used to the comparison of the approaches. Obtained results being processed by Mann–Whitney U-test. It was obtained that changes rate in the problem affect the efficiency of the application of the solutions obtained in the previous step of new population the forming.
Бесплатно
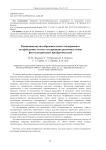
Статья научная
The article proposes the concept of an experiment for conducting flight testing of various samples of photo voltaic converters. The purpose of the experiment is to study the behavior of new types of solar cells in outer space. The research will be carried out by testing samples on board the spacecraft. The experiment will be carried out by a device that collects data on the electrical properties of solar cells. The information re-ceived will be presented in the form of a voltage characteristic. During the experiment, its dependence on external parameters will also be studied. In particular, the correlation of the current-voltage characteristic from the values of temperature and illumination of solar cells will be investigated. Based on the data ob-tained, the efficiency of photo voltaic converters will be determined. Their degradation as a result of expo-sure to cosmic ionizing radiation will also be studied. The authors are tasked with designing and develop-ing an experimental installation that will be a payload module of a small CubeSat-class spacecraft. Based on the results of the work, the appearance of the flight testing experiment was developed, the re-quirements for the payload module were determined and a project for its creation was proposed. At this stage, the circuit design and software implementation of the module itself are under development. In the course of the work, the main requirements that this module provides to the main systems of the spacecraft were also formulated. To carry out the mission of the experiment, it is planned to integrate the payload module on the plat-form of the ReshUCube-2 form factor 3U. This satellite will be equipped with equipment enabling techno-logical experiments.
Бесплатно
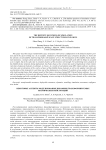
The definite questions of simulation of transformable space structures dynamics
Статья научная
This paper describes large transformable space structures with various configuration in the folded transport position and in the open working one. As an example, simulation of transformable space structures dynamics is shown for the antenna circuit foldable load-bearing frame with diameter of 5 m. For investigation of the foldable frame deployment dynamics, a design scheme presented by a system of rigid bodies connected with each other by hinges is accepted as it is simple, but at the same time it considers features of the structure well enough. For performing stress analysis of the foldable frame elements during deployment, the frame shape at the certain time point of deployment, when relative velocities of adjacent elements are ultimate, is chosen. As a results of calculation using MSC.Adams software, positions, velocities and accelerations of the centres of mass of the foldable frame elements as well as the angular velocities and accelerations of the elements for each time step of the deployment are obtained. To perform stress analysis of the foldable load-bearing frame, finite element model of the frame is developed using MSC.Patran/Nastran software. As a results of investigation of stressed and deformed states of antenna circuit foldable frame elements both without taking into account damping and with consideration of damping, stresses arising in the foldable frame elements at the certain time points during deployment are found.
Бесплатно
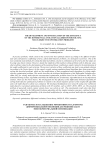
Статья научная
In practice problems, which consist in the search of the best (optimal) solution according to the different irredundant and contradictory (conflicting) criteria, called multi-objective problems, are of frequent occurrence. One of the most commonly used methods for solving this kind of problems consists in combination of all criteria into the single one by using some linear relation. However, despite the simplicity of this method, solving problems with its help may cause other problems related to the determination of the mentioned linear combination, namely related to the determination of the weight coefficients for each criterion. The incorrect selection of these coefficients may lead to non-optimal solutions (according to the Pareto theory). In this regard, recently various population-based algorithms have been proposed for solving the described problems, which are the modifications of these population-based algorithms for solving singleobjective optimization problems. This article describes the developed modifications of the Differential Evolution algorithm (DE) for solving multi-objective unconstrained optimization problems based on the well-known NSGA (Nondominated Sorting Genetic Algorithm) and MOEA/D (Multiobjective Evolutionary Algorithm Based on Decomposition) schemes, which use the Pareto theory. The investigation into the efficiency of the Differential Evolution algorithm for solving multi-objective optimization problems in relation to the chosen mutation operator of the original DE algorithm and to the multi-objective scheme was conducted. The developed modifications were tested by using some well-known multi-objective real-valued optimization problems with 30 variables, such as ZDT1, ZDT2, ZDT3, etc. The practical problem of spacecraft control contour variant choice was solved as well. The experimental results show that better results were achieved by the Differential Evolution algorithm with the simplest mutation operators combined with the NSGA scheme. Thus, the applicability of the described modification for solving practical multi-objective optimization problems was demonstrated.
Бесплатно
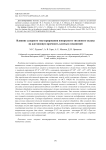
Статья научная
The paper examines issues related to the influence of laser texturing of the surface of a titanium alloy on the characteristics of the titanium-carbon fiber adhesive joint. Using an ytterbium pulsed fiber laser, textures with a linear structure (0°–0° and 90°–90°) and a mesh structure (0°–90°, ±30°, ±45°, ±60°) were created on the surface of a titanium alloy. The surface roughness values in two perpendicular directions were determined, and microsections were made, which can be used to characterize the surface morphology of the titanium alloy. To determine the adhesive strength of the joint, samples with the same surface texture were glued together. The samples were glued together according to OST 1-90281–86. Bonding was carried out within 24 hours after laser surface treatment. Before gluing, the treated surface was cleaned with isopropyl alcohol. Adhesive joint area S = 300 mm2. Three-component adhesive VK-9 based on epoxy and polyamide resin was used as an adhesive. Laser surface treatment of titanium alloys increases the strength of the adhesive joint by more than 70 % relative to the untreated surface. This may indicate that the main mechanisms for increasing the strength of an adhesive joint are an increase in the contact area between the surface and the adhesive, and chemical modification that activates the surface. The processing texture has a lesser effect on the adhesive strength, provided that the specific surface energy of the laser processing is the same. When laser processing, you should pay great attention to the choice of surface texture, because certain textures can give an increase in strength by 20–30 %. If the type of load in the truss load elements is known, then it is better to use linear textures directed perpendicular to the direction of the load (for shear – texture 0°–0°; for torsion – texture 90°–90°). For mixed loads, it is better to use mesh structures ±30°, ±45°, ±60°, which resist loads in two directions.
Бесплатно
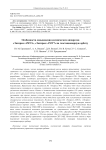
The feature of raising the “Express-AMU3” and “Express-AMU7” satellites into geostationary orbit
Статья научная
At present, in order to increase the launch mass, raising satellites into geostationary orbit by their own propulsion subsystem is widely used. Oly the JSC “Academician M. F. Reshetnev “Information Satellite Systems” applied such a scheme for several satellites of their own design - "Express-AM5", "Express-AM6", "Express-80" and "Express-103". Along with this, some diversity of approaches to the implementa-tion of this operation can be noted. In particular, the orbit raising of the above satellites was carried out using the onboard propulsion subsystem based on SPT-100 plasma thrusters. The operation was carried out by one or two thrusters. The use of two thrusters of the "Express-80" and"Express-103" satellites was due to the desire to keep within a reasonable amount of no more than six months with a significant increase in the output mass. Nevertheless, the duration of the orbit raising of about 150 days, which took place dur-ing the raising of satellite data, is also excessively long. It is evidemnt that it can be reduced, other things being equal, only by increasing the available thrust of the thrusters. This can be achieved both by increas-ing the thrust of individual units, and by increasing the number of simultaneously used thrusters. Therefore, for the new Express-AMU3 and Express-AMU7 satellites (with dimensions similar to the Express-80 and Express-103 satellites), for which a paired launch was also assumed, both of these methods were used. For orbit raising, two SPT-100V thrusters and, additionally, an SPT-140D type thruster were used. The total thrust of a cluster of thrusters made it possible to count on a significant reduction in the duration of orbit raising in comparison with the Express-80 and Express-103 satellites. The SPT-140 thruster developed by JSC "Experimental Design Bureau FAKEL" was used in Russia for the first time. For its power supply, the CCS-140D control and conversion device was specially created at the JSC "Design Bureau Polyus". The use of a combination of three thrusters made it possible to significantly reduce the duration of the opera-tion of raising into geostationary orbit.
Бесплатно