Вестник Южно-Уральского государственного университета. Серия: Металлургия @vestnik-susu-metallurgy
Статьи журнала - Вестник Южно-Уральского государственного университета. Серия: Металлургия
Все статьи: 885
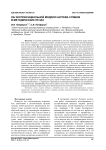
Об экспоненциальной модели нагрева слябов в методических печах
Статья научная
Введение. В условиях повышения требований к качеству нагрева металла перед прокаткой задача создания и совершенствования алгоритмического обеспечения автоматизированных систем управления технологическим процессом (АСУ ТП) методических печей является вполне актуальной. Цель исследования: рассмотреть задачу физической обусловленности и параметрической настройки так называемой экспоненциальной модели, часто применяемой для описания нагрева слябов в методических печах прокатного производства. Выясняется вопрос о том, насколько экспоненциальная модель соответствует физике процесса нагрева, какая точность описания при этом может быть достигнута. Материалы и методы. Производится сравнение как структур моделей - физической модели на основе уравнения теплопроводности и экспоненциальной модели, так и результатов расчета среднемассовой температуры металла по этим моделям. Результаты. Показано, что экспоненциальная модель в точности соответствует физике процесса нагрева только для термически тонких тел. Получено дифференциальное уравнение для ошибки расчета среднемассовой температуры термически массивных тел. При этом анализируются три режима нагрева: при постоянной температуре рабочего пространства и при линейном и экспоненциальном росте этой температуры. Приведено решение уравнения для ошибки расчета при нагреве при постоянной температуре рабочего пространства. Установлено, что экспоненциальная модель удовлетворительно описывает процесс, как правило, только для режима нагрева при постоянной температуре рабочего пространства. Найдено рациональное значение настраиваемого параметра экспоненциальной модели. Указывается достаточно простая схема перехода от параметров модели, ядром которой является дифференциальное уравнение теплопроводности, к параметрам упрощенной экспоненциальной модели для среднемассовой температуры. Заключение. Результаты работы могут быть использованы при разработке и совершенствовании алгоритмического обеспечения АСУ ТП методических печей.
Бесплатно
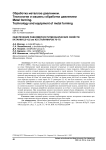
Обеспечение равномерности механических свойств катанки 5,5-6,5 мм из стали марок 70-75
Статья научная
В 2019 году была проведена модернизация линии воздушного охлаждения стана 170 ПАО «ММК». Она была направлена на получение сорбитизированной катанки непосредственно на стане. Применение такой продукции позволяет отказаться от одной промежуточной операции термической обработки в процессе производства проволоки, а также повысить стабильность механических свойств готовой проволоки, производимой из такой катанки. Учитывая особенности укладки катанки на линии воздушного охлаждения за прокатным станом, со стороны метизных предприятий предъявляются следующие требования к равномерности механических свойств получаемой катанки: не более 40 Н/мм2 по длине витка, 50 Н/мм2 по длине мотка, 60 Н/мм2 по плавке. При анализе образцов проката из стали марок 70-75 диаметром 5,5-6,5 мм было выявлено, что полное соблюдение требований метизных предприятий на действующих прокатных станах затруднено. По заказу ПАО «ММК» в рамках научных исследований по освоению технологии производства катанки на линии воздушного охлаждения была разработана математическая модель, адекватность которой была доказана с помощью разработки режимов прокатки на ее базе с последующей оценкой полученной продукции. При дальнейшем анализе полученного проката было обнаружено, что произведенная по новым режимам продукция в большей степени отвечает требованиям по неравномерности механических свойств по длине витка, мотка и партии.
Бесплатно
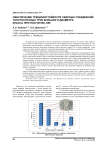
Статья научная
Из практики эксплуатации и опыта механических испытаний известно, что металл зоны термического влияния (ЗТВ) сварного соединения более чем основной металл подвержен разрушению. В ходе проведения многочисленных испытаний по оценке статической трещиностойкости установлено, что наименьшими вязкими свойствами обладают область крупного зерна ЗТВ и линия сплавления. Такое снижение вязких свойств сварных соединений прямошовных труб большого диаметра (ТБД) приводит к отбраковке продукции и серьезным экономическим последствиям. С целью выявления причин такого поведения металла в ЗТВ было выполнено моделирование термических циклов сварки на образцах из сталей класса прочности К65 с помощью комплекса Gleeble 3800. В ходе выполнения работы была установлена взаимосвязь между сформированной микроструктурой в ЗТВ и вязкими свойствами сварных соединений высокопрочных труб. Самым неблагоприятным типом микроструктуры в области крупного зерна ЗТВ является глобулярный бейнит. Выявлено негативное влияние ванадия и кремния на вязкие свойства сварных соединений высокопрочных труб большого диаметра. Так же были установлены причины снижения вязких свойств литого металла сварных швов. Сильное снижение вязких свойств металла шва происходит при выделении феррита по границам первичных дендритов. По результатам исследований был разработан химический состав основного металла труб, и предложен способ повышения вязких свойства литого металла сварного шва за счет добавок титана и бора в сварочную ванну. Рекомендации были применены при производстве опытной партии труб для проекта «Сила Сибири». Результаты механических испытаний показали высокие значения вязких свойства полученных сварных соединений.
Бесплатно
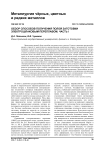
Обзор способов получения полой заготовки электрошлаковым переплавом. Часть I
Статья научная
Представлен краткий обзор способов получения полых слитков. В связи с развитием ресурсодобывающих отраслей и энергетического машиностроения возобновился интерес к возможностям электрошлаковых технологий в вопросах повышения качества полой заготовки. Проблема повышения эксплуатационных свойств полых заготовок и снижения их себестоимости является весьма актуальной и требует своего дальнейшего разрешения. Ведь формирование полости методом горячей деформации при производстве полых заготовок замкнутой формы это вынужденное решение, которое использовали металлурги из-за низкого качества литья. Поэтому необходимо получать литые полые заготовки, которые по качеству не уступали бы горячедеформированным. Эта задача успешно решается технологиями на основе электрошлакового переплава. Применение электрошлакового переплава (ЭШП) для производства полых слитков реализовано в Институте электросварки им. Е.О. Патона НАН Украины еще в 70-х гг XX в. Электрошлаковый переплав является одним из прогрессивных способов улучшения структуры и физико-химических свойств металла посредством управления процессами кристаллизации. Показана целесообразность применения полых слитков электрошлакового переплава для изготовления оборудования, используемого в ресурсодобывающих отраслях и энергетическом машиностроении. Представлены достоинства и недостатки основных видов ЭШП, таких как с подвижным дорном, неподвижным многоразовым дорном, с подвижными кристаллизаторами и заготовкой, центробежное электрошлаковое литье, жидкая штамповка в электрошлаковом литье, электрошлаковая подпитка, ЭШП с вытягиванием.
Бесплатно
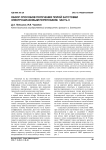
Обзор способов получения полой заготовки электрошлаковым переплавом. Часть II
Статья научная
В представленном обзоре рассмотрены состояние, возможности и ограничения технологии электрошлаковой прошивки. Рассмотрены особенности процесса формирования полой заготовки и способы внешнего воздействия на процесс плавления и кристаллизации металла, обеспечивающих высокое металлургическое качество полой заготовки. Промышленное освоение способа прошивки наталкивается на некоторые трудности, связанные со стойкостью технологической оснастки. Во-первых, максимальная длина полой заготовки, выплавляемой таким способом, ограничена жесткостью штока, сохраняющего с требуемой точностью расположение дорна относительно наружного кристаллизатора. Во-вторых, недостатком указанного способа является то, что из-за отсутствия специальных защитных мер часть дорна, расположенная над уровнем металлической ванны, подвергается значительному разрушению. Одна из причин этого явления - электроэрозия поверхности дорна при прохождении через него части рабочего тока при прямой схеме подключения электрод - слиток. Разрушение дорна происходит также вследствие попадания на него капель расплавленного металла, так как зона каплеобразования расположена в осевой части электрода непосредственно над дорном. Это, в свою очередь, определяет высокие тепловые нагрузки на головку дорна. Изготавливаемая из меди рабочая часть дорна подвержена сильному электроэрозионному износу и требует смены уже после нескольких плавок. Воспрепятствовать разрушению дорна можно применив внешнее воздействие на процессы каплеобразования, траекторию движения капли в шлаковой ванне и изменению места доставки электродного металла. Также при помощи внешнего воздействия можно изменить форму металлической ванны, достигнуть измельчения кристаллитов, избежать кристаллизационных дефектов, а также повысить рафинирующую способность и производительность процесса.
Бесплатно
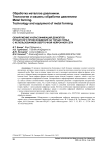
Статья научная
В процессе производства бесшовных труб большое внимание уделяют качеству продукции, которая, в свою очередь, складывается из качества заготовки, качества гильзы и качества черновой трубы. При этом на заднем торце гильз могут возникать различные дефекты формы, которые могут препятствовать внедрению оправки и последующей раскатке гильзы в непрерывном раскатном стане. Также дефекты формы на заднем торце гильзы («корона», «серьга», «шип» и др.) могут спровоцировать аварийный останов. Своевременное информирование вальцовщиков о типе торца гильзы сможет способствовать оперативному принятию решения о корректировке настроечных параметров прошивного стана, что, в свою очередь, приведет к недопущению появления продукции с критическими отклонениями по форме. Один из способов получения информации об объекте (торец трубы) - использование цифровых камер. Поэтому необходимо проанализировать современные возможности применения цифровых камер и способов цифровой обработки изображений с целью определения интересующих характеристик.
Бесплатно
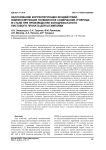
Статья научная
В практике металлургического производства бывают ситуации, когда плавка стали с химическим составом, предназначенным для выполнения одного заказа, переназначается на производство проката из другой марки стали. При формальном соответствии химического состава выплавленной стали требованиям к другой марке ключевые контрольные характеристики процесса, традиционно применяемые для новой марки стали, могут оказаться несоответствующими особенностям структурных и фазовых превращений в стали с реальным химическим составом. В таком случае, чтобы предотвратить выпуск несоответствующей продукции, необходимо выработать и применить оперативные корректирующие действия. Цель работы - выбор и обоснование оперативных корректирующих действий при производстве холоднокатаного листового проката классов качества CQ, DQ и DDQ из малоуглеродистой качественной стали с целью компенсации пониженного содержания углерода в плавках, назначенных на выполнение соответствующих заказов. Использовались методы микроскопии для изучения структуры и фазового состава стали с содержанием углерода 0,008-0,04 % в горячекатаном и холоднокатаном состояниях. Стандартизованными методами испытаний на растяжение получены данные о механических свойствах горячекатаного и холоднокатаного проката. По результатам испытаний построены достоверные множественные аппроксимации влияния контрольных характеристик технологии на свойства холоднокатаного проката, которые в дальнейшем применялись в ходе оптимизации толщины подката для холодной прокатки как компенсирующего воздействия при колебаниях содержания углерода в указанных выше пределах. Новизна работы заключается в выявлении и обосновании корректирующих воздействий для технологической системы, в которой холодная прокатка осуществляется на непрерывном четырехклетевом стане с рулонным питанием. Результаты работы состоят в определении значений температуры конца прокатки и приращения толщины подката как оперативных компенсирующих воздействий при назначении плавок стали с пониженным содержанием углерода на прокатку в технологическую систему, включающую непрерывный четырехклетевой стан с рулонным питанием. Практическая значимость работы состоит в предотвращении выхода несоответствующей продукции при использовании предлагаемого решения в производстве холоднокатаного проката классов качества CQ, DQ и DDQ толщиной 0,6-2,0 мм.
Бесплатно

Статья научная
Методами металлографии, сканирующей и просвечивающей электронной микроскопии исследована структура низкоуглеродистых сталей мартенситного класса ВКС-7 и ВКС-10, подвергнутых теплой прокатке либо осадке при температурах 600 и 700 °С (в α-состоянии). Рассмотрена роль растворения и выделения карбидных фаз, стока дислокаций на высокоугловые границы реек, полигонизации и рекристаллизации в процессе формирования фрагментированной структуры сталей при теплой деформации. Показано, что деформация прокаткой при 600 °С со степенью 40 % не приводит к созданию фрагментированной структуры, в мартенсите сохраняются рейки, поделенные на ячейки. При увеличении степени деформации до 60 % образуются отдельные фрагменты с высокоугловыми границами. Установлено, что доля фрагментированной структуры существенно возрастает при увеличении степени деформации до 80 %, одновременно происходит коалесценция субзерен близкой ориентации, приводящая к образованию крупных фрагментов α-фазы. Увеличение температуры прокатки до 700 °С и степени деформации до 80 % вызывает эффективную фрагментацию структуры стали ВКС-7, однако в более легированной стали ВКС-10 сохраняются признаки реечного строения. Показано, что изменение схемы деформации стали ВКС-7 с прокатки на всестороннюю осадку при 600 °С со степенью 50 % вызывает рекристаллизацию α-фазы по механизму in situ с образованием высокой доли ультрамелкозернистой структуры (размер зерен 0,2-2,5 мкм). В стали ВКС-10 с большим содержанием легирующих элементов подобные явления происходят при более высокой температуре теплой осадки, 700 °С.
Бесплатно
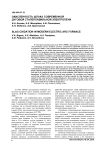
Окисленность шлака современной дуговой сталеплавильной электропечи
Статья научная
В электросталеплавильном цехе ОАО «ММК» продолжается освоение технологии выплавки стали в мощных дуговых электропечах ДСП-180, пущенных в эксплуатацию в 2006 г. Для установления зависимости содержания оксидов железа FeO и Fe2O3 шлака от его общей окисленности были проведены промышленные исследования. Это позволило описать зависимость отношения FeO/Fe2O3 от общей окисленности шлака. Выявлено отсутствие зависимости общей окисленности шлака от расхода вдуваемого углерода для вспенивания шлака. Анализ отходящих газов в тот же период плавки показал резкий скачок содержания оксидов углерода (особенно СО) и увеличение его температуры. Низкое усвоение вдуваемого углерода расплавом приводит к тому, что значительная его часть окисляется в газовой фазе.
Бесплатно
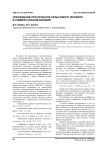
Опережение при прокатке рельсового профиля в универсальном калибре
Статья научная
Поставленная ранее вариационная задача о прокатке рельсов в универсальных калибрах реализована в системе MathCAD. Численная реализация позволила установить закономерности изменения опережения в зависимости от основных технологических параметров прокатки. Представлены зависимости коэффициента опережения от коэффициента обжатия шейки рельсового профиля, приведенного диаметра горизонтальных валков, приведенной толщины фланцев и условий трения на контактных поверхностях. Установленные закономерности позволили уточнить модель скоростного режима прокатки рельсов на современных рельсобалочных станах.
Бесплатно
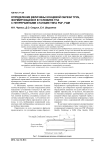
Статья научная
Проведено теоретическое исследование формирования концевой обрези раската на трубопрокатных агрегатах с непрерывными станами. Выявлено, что большинство из имеющихся формул адаптированы для расчета концевой обрези при раскатке черновой трубы в линии ТПА с использованием непрерывных станов двухвалкового типа с удерживаемой либо плавающей оправкой. Определено, что основными технологическими факторами, влияющими на формирование концевой обрези на участке горячего передела, являются наличие системы гидроутонения непрерывного стана, коэффициент вытяжки по горячему переделу, отношение наружного диаметра к толщине стенки раската (D/S), тоннаж (прокатная компания), использование различных систем калибров стана PQF. Из анализа замеров толщины стенки за извлекательно-калибровочным станом видно, что система гидроутонения труб выравнивает толщину стенки по телу раската, но при этом величина абсолютной разнотолщинности стенки на заднем конце значительно превосходит разнотолщинность стенки на переднем. На основании анализа промышленных данных получена степенная зависимость величины концевой обрези от безразмерного коэффициента, который включает в себя такие параметры как: коэффициенты вытяжки и наружные диаметры труб после непрерывного оправочного, извлекательно-калибровочного и редукционно-растяжного станов. С использованием данной зависимости, можно регламентировать величину концевой обрези труб с использованием калибра стана PQF 190 мм и 290 мм. Полученная формула имеет высокую сходимость результатов с практическими данными, а также не противоречит рекомендациям, приводимых в литературных источниках.
Бесплатно
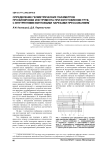
Статья научная
Представлена постановка задачи определения геометрических параметров профилировки прессового инструмента, в частности пресс-иглы, позволяющей изготавливать трубы с внутренними винтовыми нарезами прессованием. Учитывая кинематические условия процесса прессования, получены зависимости для определения параметров пресс-иглы, позволяющие проектировать профилировку рабочего инструмента при изготовлении требуемого сортамента труб с внутренними винтовыми нарезами.
Бесплатно
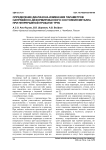
Статья научная
Процессы продольной горячей прокатки бесшовных труб на оправке и без оправки широко используются на современных трубопрокатных агрегатах. При анализе технологии производства труб необходимо учитывать множество факторов, поэтому для определения влияния каждого из них на качество готовых труб целесообразно использовать компьютерное моделирование. На сегодняшний день известно довольно много программ, позволяющих моделировать процессы горячей прокатки методом конечных элементов. Одним из обязательных условий получения достоверных результатов при моделировании является корректный расчёт величины сопротивления металла пластической деформации. В данной работе при помощи компьютерного моделирования были определены диапазоны, в которых изменяются основные параметры, определяющие величину сопротивления пластической деформации. В программе QForm была промоделирована прокатка трубы на плавающей оправке в первых четырёх клетях непрерывного двухвалкового стана. Получены максимальные значения для таких величин, как скорость и величина деформации в клети, а также диапазон изменения температуры металла.
Бесплатно

Определение количества потерь металла с отвальными шлаками при выплавке углеродистого феррохрома
Статья научная
Проведена магнитная сепарация отвальных шлаков производства углеродистого феррохрома. Приведены данные по составу магнитного продукта, а также по химическому составу металла и шлака, полученных после переплава магнитного продукта, содержащего хром. Установлена связь между степенью измельчения шлаков и выходом извлекаемого металла. Методом комбинирования решен вопрос о массе пробы, магнитная сепарация которой даст достоверную информацию о количестве содержащегося в шлаке металла. Построенные зависимости позволяют определить массу пробы и количество параллельных опытов для определения выхода целевого магнитного продукта с требуемой точностью.
Бесплатно
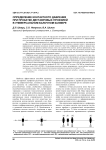
Определение контактного давления при прокатке двутавровых профилей в универсальном балочном калибре
Статья научная
Представлено решение задачи об определении контактных давлений и усилий прокатки в универсальном калибре на основе использования физических уравнений связи напряженного и деформированного состояния металла в очаге деформации. Для определения напряженного и деформированного состояния металла при прокатке двутаврового профиля в универсальном четырехвалковом калибре была поставлена и решена задача с применением вариационного принципа минимума полной мощности. При этом деформация шейки и фланцев рассматривалась как прокатка прямоугольных полос на гладкой бочке валков, причем принималось, что обжатие фланцев происходит только со стороны вертикального валка. По результатам решения такой задачи с использованием известных положений механики были определены компоненты тензора скорости деформации и интенсивность деформации сдвига. Разработан новый теоретический метод расчета контактных давлений и усилий прокатки при прокатке двутавровых профилей в универсальном балочном калибре. Достоверность метода подтверждена результатами экспериментальной проверки. Разработанный метод определения контактных давлений и сил прокатки реализован в виде программ расчетов на персональном компьютере с использованием вычислительного пакета Mathcad. С целью экспериментальной проверки этого метода проведены расчеты для условий прокатки двутавровых профилей № 35Б1, 40К2 и 45Б2 из стали 15ХСНД на универсальном балочном стане ОАО «НТМК». Полученные расчетные данные сравнивались с результатами экспериментальных исследований; среднестатистическая погрешность расчетов составляет 6,4 %.
Бесплатно
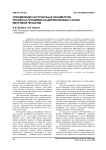
Определение настроечных параметров процесса прошивки на двухвалковых станах винтовой прокатки
Статья научная
Разработаны математические зависимости по описанию основных геометрических параметров очага деформации при винтовой прошивке на двухвалковых станах. Полученные выражения учитывают искажение очага деформации в любом поперечном сечении, вызванное разворотом валков прошивного стана на угол подачи, и могут применяться для математического описания двухвалковых станов винтовой прокатки с грибовидными и бочковидными валками, работающих на повышенных углах подачи. Для достаточно точного математического описания геометрических параметров очага деформации предложены зависимости, которые позволяют определить расстояния от оси прокатки до поверхности валков в любом поперечном сечении очага деформации. Расстояние от оси прокатки до поверхности валков определенно при допущении: изменение радиуса валка в его основной меридиональной плоскости незначительное. Сравнение полученных математических зависимостей с твердотельным моделированием, основанным на поверхностном моделировании с граничным представлением твердых тел и реализованном в САD программе КОМПАС-3D, показало хорошую сходимость и правомочность принятого допущения. На основе полученных выражений разработана методика по определению основных настроечных параметров процесса винтовой прошивки: расстояние между валками в пережиме валков; выдвижение оправки за пережим валков; обжатие перед носком оправки; расстояние от захвата заготовки валками до носка оправки. Разработанные математические зависимости пригодны также для разработки калибровок прокатного инструмента прошивных станов (оправок и валков) и для проведения анализа по схеме деформирования при процессе винтовой прошивки.
Бесплатно
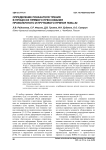
Статья научная
В любом процессе обработки металлов давлением имеет место внешнее трение на контакте инструмента и обрабатываемого материала. Под влиянием сил трения возрастает усилие деформации, разогревается и интенсивно изнашивается инструмент, увеличивается неравномерность деформации и, как следствие, возникает разнородность микроструктуры обрабатываемого металла, возникают растягивающие напряжения, которые иногда приводят к нарушению сплошности изделия. В настоящей работе исследуется влияние контактного трения на процесс прямого прессования прутков и проволоки из сплава ПОИн-52. С помощью математического моделирования исследовано влияние коэффициента трения на усилие в процессе прессования прутков Ø8,0 и 15,0 мм, а также проволоки Ø2,0 мм. Показано, что с увеличением коэффициента трения на преодоление силы трения скольжения на контактной поверхности обрабатываемого металла с контейнером и с матрицей тратится до 60 % усилия, необходимого для прессования исследуемого сплава. В ходе экспериментальных исследований показано, что применение смазочных материалов, а именно графитовой (графит - С) и молибденовой (дисульфид молибдена - MoS2) смазки, позволяет снизить коэффициент трения более чем в 10 раз. С определенной долей допущения можно говорить о том, что при прессовании припоя ПОИн-52 с использованием стального контейнера без применения смазки коэффициент трения равен 0,5, а при применении графитовой или молибденовой смазки коэффициент трения будет принимать значения, близкие к 0,05. С помощью результатов экспериментальных исследований путем подбора были определены показатели трения по законам Кулона, Зибеля и Леванова, которые могут быть применены для компьютерного моделирования в пакете Qform процесса прямого прессования припоя ПОИн-52 с использованием стального контейнера без применения смазки и с применением графитовой и молибденовой смазки. Учет достоверной величины показателя трения при компьютерном моделировании позволит существенно повысить точность расчетов.
Бесплатно
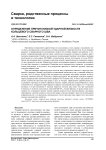
Определение причин низкой ударной вязкости кольцевого сварного шва
Статья научная
Причинами пониженной ударной вязкости околошовных зон в сварных соединениях могут быть неоднородность химического состава (ликвация) и перегрев металла. Если ликвация приводит к неравномерности механических свойств по сечению сварного соединения, то перегрев, сопровождающийся ростом зерна, значительно повышает склонность сварного шва к хрупкому разрушению. В работе исследовался штампосварной тройник: магистраль тройника изготовлена из стали марки 10Г2ФБЮ, удлинительное кольцо изготовлено из стали 09Г2С. Целью исследования было установить причины низкой ударной вязкости кольцевого сварного шва указанного изделия. Макроструктурные исследования сварного соединения показали, что шов был наложен со смещением. Имеющая место неравноосность приводит к смещению линии разрушения, в результате чего разрушение проходит в наиболее хрупкой структуре участков сварного шва. При исследовании микроструктуры металла шва установлено наличие в структуре видманштетт феррита. Данная структурная составляющая наблюдается как у внешней поверхности шва, так и в центре. Присутствие видманштетта оказывает негативное влияние на механические свойства металла. Поскольку микроструктурные исследования показали неравномерное распределение грубоигольчатого феррита по толщине шва, то было предложено увеличить количество проходов при сварке с трех до четырех. Проведенные сравнительные исследования структуры и свойств образцов опытных сварок показали целесообразность таких изменений. Так, измерения микротвердости сварных соединений после сварки в 3 и 4 прохода показали, что при наложении 3 валиков твердость металла шва ниже, чем при наложении 4 валиков, но не более допустимых значений 260 HV10. Таким образом, по результатам исследования по устранению причин низкой ударной вязкости были рекомендованы следующие мероприятия: строгий контроль технологии сварки участков сварного шва (для недопущения неравноосности) и установление минимального числа проходов при сварке (для получения нужных механических свойств).
Бесплатно